Plastic Injection Molding with Induction Heating Machine
Plastic Injection molding with
induction heating requires pre-heating of the molds to a higher temperature, to ensure the proper flow or curing of the injection-molded material. Typical heating methods used in the industry are steam or resistive heating, but they are messy, inefficient, and unreliable. Induction heating is a clean, fast and energy-efficient alternative which has been widely used in recent years to replace steam, gas or resistive heating of molds and dies.
What is Injection Moulding?
Plastic injection moulding with induction heating is the process of melting plastic pellets (thermosetting/ thermoplastic polymers) that once malleable enough, are injected at pressure into a mould cavity, which fills and solidifies to produce the final product.
How Does Plastic Injection Moulding Work?
The plastic injection moulding process at Protolabs is a standard process involving an aluminium mould. Aluminium transfers heat much more efficiently than steel, so does not require cooling channels - which means the time we save on cooling can be applied to monitoring fill pressure, cosmetic concerns and producing a quality part.
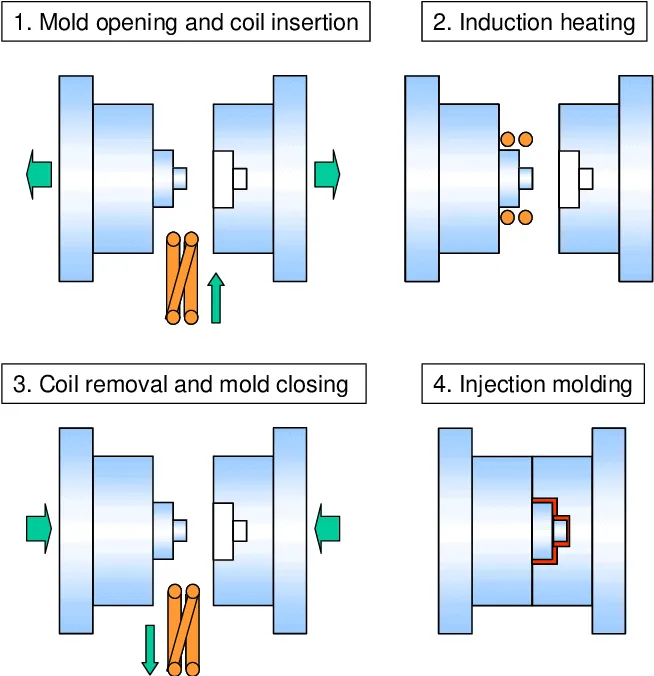
Resin pellets are loaded into a barrel where they will eventually be melted, compressed, and injected into the mould’s runner system. Hot resin is shot into the mould cavity through the gates and the part is moulded. Ejector pins facilitate removal of the part from the mould where it falls into a loading bin. When the run is complete, parts (or the initial sample run) are boxed and shipped shortly thereafter.
How Induction Heating is used in Dies & Molds Industry?
- Induction Preheating of tools and molds for plastic injection molding
- Heating of molding tools for curing of rubber product and automobile tires
- Die induction heating for catheter tipping and medical products manufacturing
- Die and platen heating for metal stamping and forming
- Induction Preheating of casting molds in the metal casting industry
- Induction Heat treating and hardening of stamping and punching tools and dies
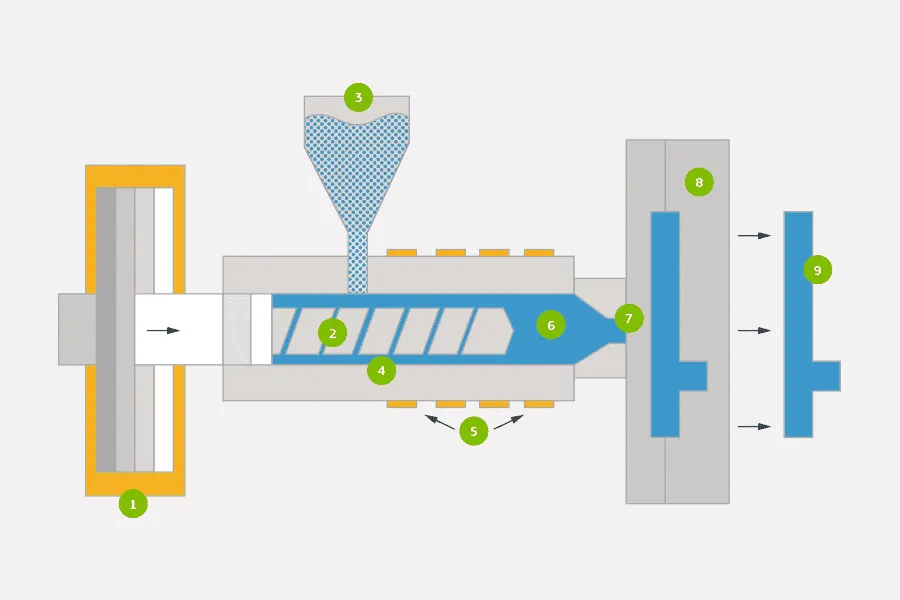
Plastic Injection Molding with Induction Heating