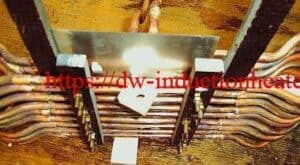

Series |
Model |
Input power Max |
Input current Max |
Oscillate frequency |
Input Voltage |
Duty cycle |
|
M
.
F
. |
DW-MF-15 Induction Generator |
15KW |
23A |
1K-20KHZ
According to the application |
3*380V
380V±20% |
100% |
|
DW-MF-25 Induction Generator |
25KW |
36A |
|||||
DW-MF-35Induction Generator |
35KW |
51A |
|||||
DW-MF-45 Induction Generator |
45KW |
68A |
|||||
DW-MF-70 Induction Generator |
70KW |
105A |
|||||
DW-MF-90 Induction Generator |
90KW |
135A |
|||||
DW-MF-110 Induction Generator |
110KW |
170A |
|||||
DW-MF-160 Induction Generator |
160KW |
240A |
|||||
DW-MF-45 Induction Heating Rod Forging Furnace |
45KW |
68A |
1K-20KHZ |
3*380V
380V±20% |
100% |
||
DW-MF-70 Induction Heating Rod Forging Furnace |
70KW |
105A |
|||||
DW-MF-90 Induction Heating Rod Forging Furnace |
90KW |
135A |
|||||
DW-MF-110 Induction Heating Rod Forging Furnace |
110KW |
170A |
|||||
DW-MF-160 Induction Heating Rod Forging Furnace |
160KW |
240A |
|||||
DW-MF-15 Induction Melting Furnace |
15KW |
23A |
1K-20KHZ |
3*380V
380V±20% |
100% |
||
DW-MF-25 Induction Melting Furnace |
25KW |
36A |
|||||
DW-MF-35 Induction Melting Furnace |
35KW |
51A |
|||||
DW-MF-45 Induction Melting Furnace |
45KW |
68A |
|||||
DW-MF-70 Induction Melting Furnace |
70KW |
105A |
|||||
DW-MF-90 Induction Melting Furnace |
90KW |
135A |
|||||
DW-MF-110 Induction Melting Furnace |
110KW |
170A |
|||||
DW-MF-160 Induction Melting Furnace |
160KW |
240A |
|||||
DW-MF-110 Induction Hardening Equipment |
110KW |
170A |
1K-8KHZ |
3*380V
380V±20% |
100% |
||
DW-MF-160Induction Hardening Equipment |
160KW |
240A |
|||||
H
.
F
. |
DW-HF-04 Series |
DW-HF-4KW-A |
4KVA |
15A |
100-250KHZ |
Single phase 220V |
80% |
DW-HF-15 Series |
DW-HF-15KW-A
DW-HF-15KW-B |
15KVA |
32A |
30-100KHZ |
Single phase 220V |
80% |
|
DW-HF-25 Series |
DW-HF-25KW-A
DW-HF-25KW-B |
25KVA |
23A |
20-80KHZ |
3*380V
380V±10% |
100% |
|
DW-HF-35 Series |
DW-HF-35KW-B |
35KVA |
51A |
||||
DW-HF-45 Series |
DW-HF-45KW-B |
45KVA |
68A |
||||
DW-HF-60 Series |
DW-HF-60KW-B |
60KVA |
105A |
||||
DW-HF-80 Series |
DW-HF-80KW-B |
80KVA |
130A |
||||
DW-HF-90 Series |
DW-HF-90KW-B |
90KVA |
160A |
||||
DW-HF-120 Series |
DW-HF-120KW-B |
120KVA |
200A |
||||
U
.
H
.
F
.
|
DW-UHF-3.2KW |
3.2KW |
13A |
1.1-2.0MHZ |
Single phase220V
±10% |
100% |
|
DW-UHF-4.5KW |
4.5KW |
20A |
|||||
DW-UHF-045T |
4.5KW |
20A |
|||||
DW-UHF-045L |
4.5KW |
20A |
|||||
DW-UHF-6.0KW |
6.0KW |
28A |
|||||
DW-UHF-06A |
6.0KW |
28A |
|||||
DW-UHF-6KW-B |
6.0KW |
28A |
|||||
DW-UHF-10KW |
10KW |
15A |
100-500KHZ |
3*380V
380V±10% |
100% |
||
DW-UHF-20KW |
20KW |
30A |
50-250KHZ |
||||
DW-UHF-30KW |
30KW |
45A |
50-200KHZ |
||||
DW-UHF-40KW |
40KW |
60A |
50-200KHZ |
||||
DW-UHF-60KW |
60KW |
90A |
50-150KHZ |
DW-MF-200 | DW-MF-250 | DW-MF-300 | DW-MF-400 | DW-MF-500 | DW-MF-600 | ||
Input Voltage | 3phases, 380V/410V/440V , 50/60Hz | ||||||
Max Input Current | 320A | 400A | 480A | 640A | 800A | 960A | |
Oscillating frequency | 0.5KHz^20KHz ( Oscillating frequency will be customized according to the size of heating parts) | ||||||
Duty Cycle Loading | 100%,24h continuously work | ||||||
Cooling Water Desires | 0.1MPa | ||||||
Dimension | Host | 1000X800X1500mm | 1500X800X2800mm | 850X1700X1900mm | |||
Extension | extension will be customized according to the material and size of heating parts | ||||||
Weight | 110kg | 150kg | 160kg | 170kg | 200kg | 220kg | |
Depend on the dimension of extension |