2022年5月31日星期二
Induction Brazing Carbide
Induction Brazing Carbide File
Objective: Induction Brazing carbide rotary file assemblies with uniform concentricity in an aerospace application
Material • Carbide blank • High speed steel shank • Temperature indicating paint • Braze shim and black flux
Temperature 1400°F (760°C)
Frequency 550 kHz
Equipment: DW-UHF-4.5kw induction heating system, equipped with a remote heat station containing two 0.33 μF capacitors (total 0.66 μF) An induction heating coil designed and developed specifically for this application.
Process A multi-turn helical coil is used. The part is heated to determine the time required to reach the desired temperature and required heat pattern. It takes approximately 30 - 45 seconds to reach 1400°F (760°C) depending on the various part sizes. Flux is applied to the entire part. A braze shim is sandwiched between the steel shank and carbide. Induction heating power is applied until the braze flows. With proper fixturing, concentricity of the part can be achieved.
Results/Benefits • Repeatable, consistent precise heat.
induction hot forming and forging process
Induction Hot forming and Forging Process
Induction Hot forming is a process in the manufacture of industrial fasteners such as bolts, screws and rivets. Heat is used to soften the metal which is usually a sheet, bar, tube or wire and then pressure is used to alter the shape of the metal by performing any of the following operations: hot heading, blanking, punching, slotting, perforating, trimming, shearing or bending. Besides, billet heating is also a process best performed with induction hot forming.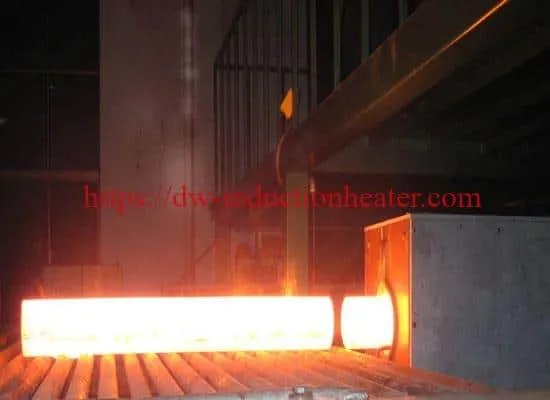
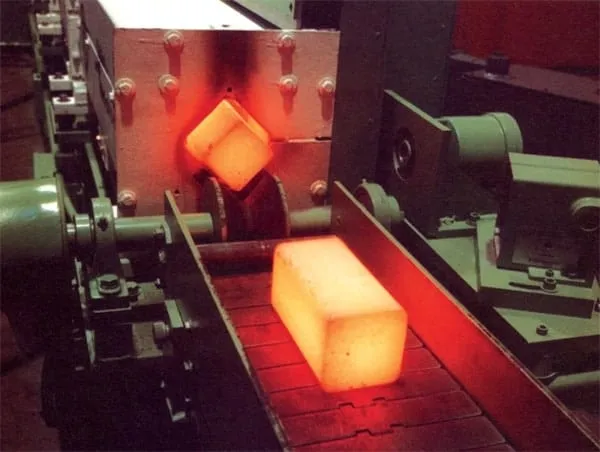
- Steel from 1100 to 1250 ºC
- Brass 750 ºC
- Aluminium 550ºC
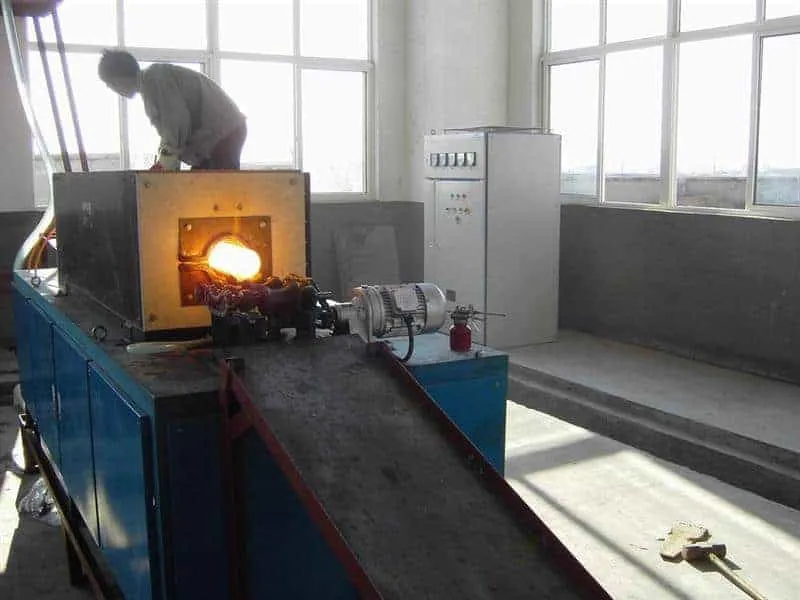
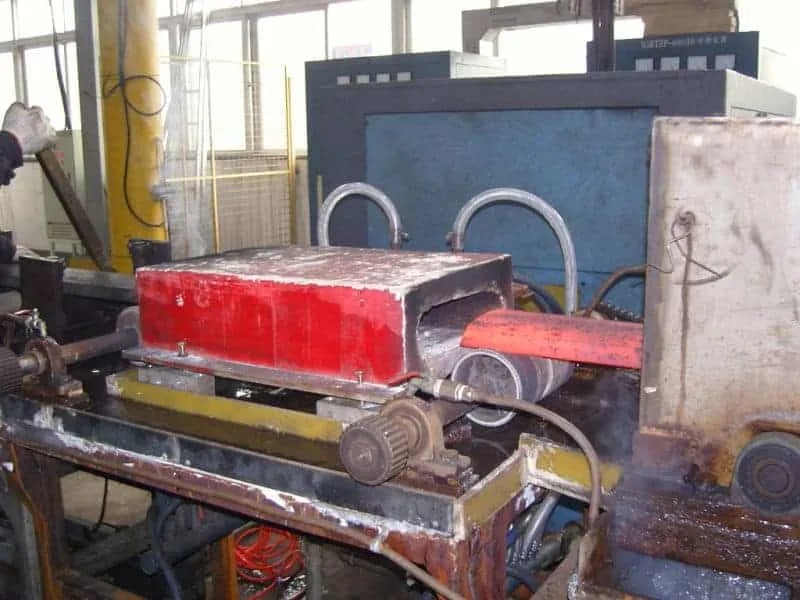
Induction heating advantages:
- Material and energy saving plus flexibility
- Greater quality
- Process control
- Much shorter heating times
- Less oxidise and the production of scale is very low
- Easy and accurate adjustment of the temperature to be applied
- No time needed for the furnace pre and maintenance heating (for example after or during the weekend when it takes more time)
- Automation and reduction of the labour required
- Heat can be directed to one specific point, which is highly important for parts with only one forming area
- Greater thermal efficiency
- Better working conditions as the only heat present in the air is that of the parts themselves

Induction Soldering Brass Tube-Pipe
Induction Soldering Brass Tube-Pipe-Tubing With RF Soldering Heating System
Objective: Soldering two brass tubes measuring 3/4" and 1/4" together for use as cellular phone antennas. The lengths of tubes range from four (4) feet to twelve (12) feet, and must be soldered along the axial side. The joint is to be made using 60/40 Tin Lead Solder and Kestor Rosin paste flux.
Material: Brass Tubes measuring 3/4" and 1/4" 60/40 Tin Lead Solder
Kestor Rosin Flux
Temperature: 3750F
Application: Through the use of the the DW-UHF-40KW output solid state induction power supply along with a unique five (5) turn 12" long channel coil, the following results were achieved:
3750 F was reached and the solder flowed after a heating period of 35 seconds.
A production rate of 24" per minute was determined to be adequate.
A quality solder fillet was observed after heating and cooling
Equipment: DW-UHF-40kW output solid state induction power supply including one (1) remote heat station containing two (2) capacitors, and a unique five (5) turn channel coil made from 3/16" copper tubing and measuring 1 1/4" by 12".
Frequency: 385 kHz
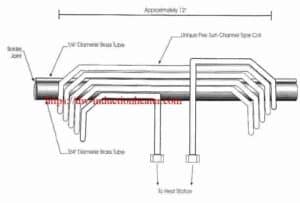
principle of electromagnetic induction heating
principle of electromagnetic induction heating
In 1831 Michael Faraday discovered Electromagnetic induction heating. The basic principle of induction heating is an applied form of Faraday’s discovery. The fact is that, AC current flowing through a circuit affects the magnetic movement of a secondary circuit located near it. The fluctuation of current inside the primary circuit provided the answer as to how themysterious current is generated in the neighboring secondary circuit. Faraday’sdiscovery led to the development of electric motors, generators, transformers, and wireless communications devices.Its application, however, has not been flawless. Heat loss, which occurs during the induction heating process, was amajor headache undermining the overall functionality of a system. Researchers sought to minimize heat loss by laminating the magnetic frames placed insidethe motor ortransformer. Heat loss, occurring in the process ofelectromagnetic induction, could be turned into productive heat energy in an electricheating system by applying this law.Many industries have benefited from this new breakthrough by implementing induction heating.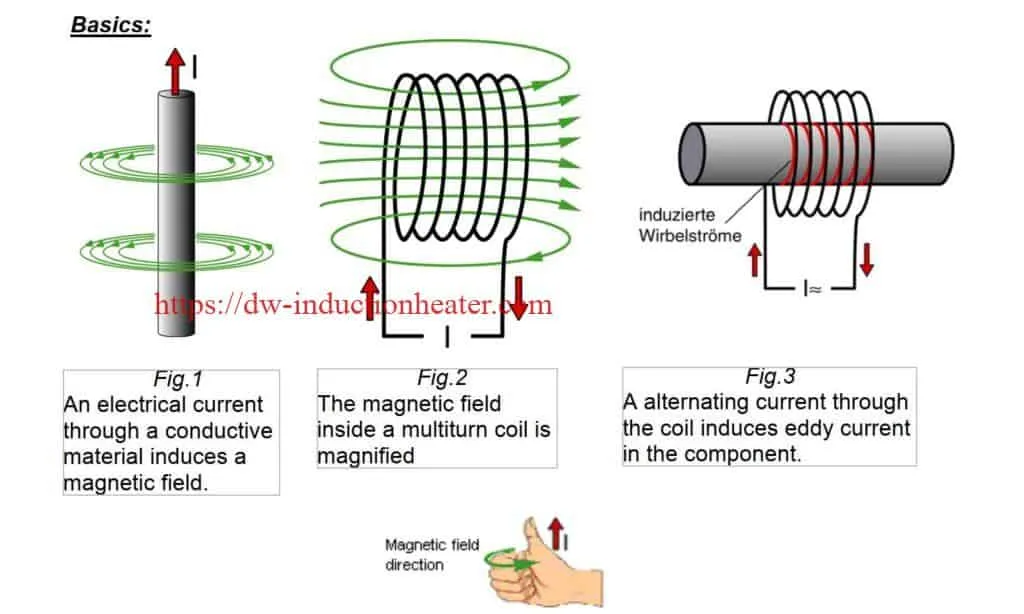
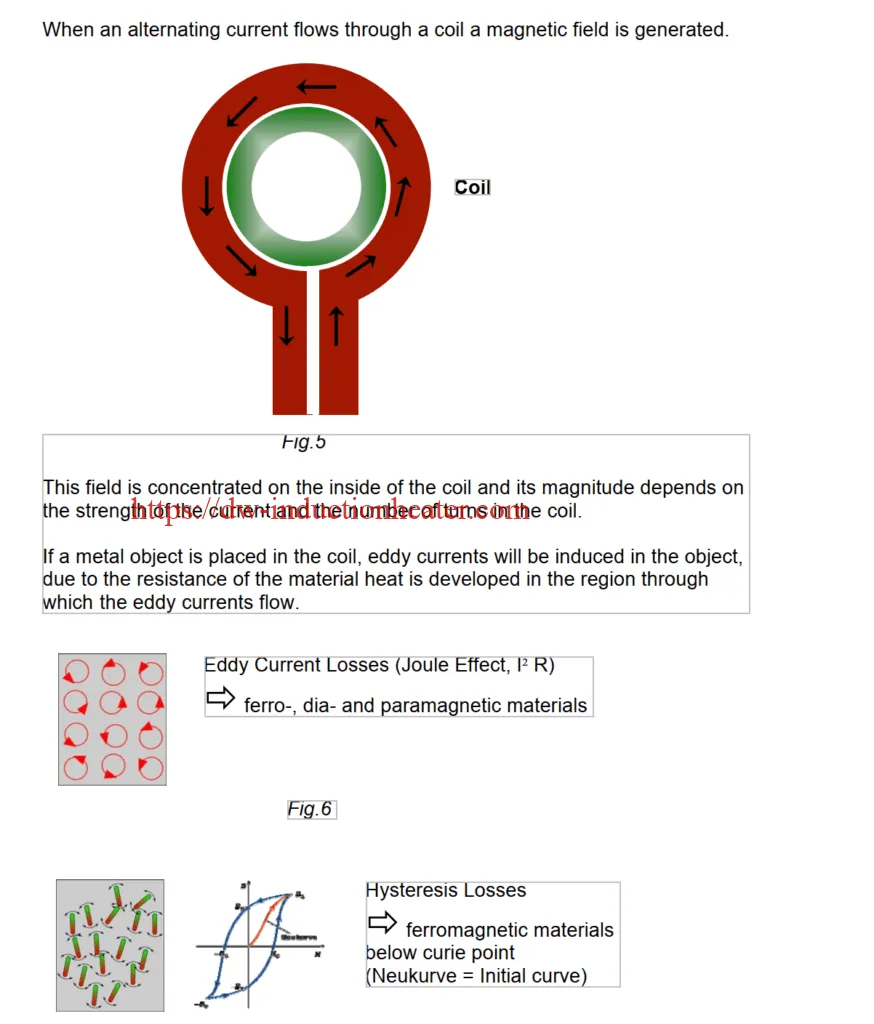
High frequency induction brazing steel tube to steel fitting
High frequency induction brazing steel tube to steel fitting
Objective
Handheld high frequency induction brazing of a steel tube to a steel fitting
Recommended Equipment
The recommended equipment for this application is the
DW-UHF-6KW-III handheld induction brazing heater heat station.
Soldering Steel To Brass With Induction Heater
Soldering Steel To Brass With Induction IGBT Soldering Heater
Objective Heat an assembly of small, gold-plated steel connectors to a brass block.
Material Approx. 1/8” (3.2mm) diameter gold-plated steel connectors, 1”(25.4mm) square x 1/4” thick brass block
Temperature 600°F(315.6ºC)
Frequency 240 kHz
Equipment • DW-UHF-6kW induction heating system equipped with a remote workhead.
• An induction heating coil designed and developed specifically for this application.
Process A two-turn helical coil is used to provide uniform heat to parts assembly. Solder paste and flux are applied to the joint area and power is applied for 20 seconds to solder the parts. Proper
fixturing is needed to hold the parts in position.
Results/Benefits Induction heating provides:
• Rapid, localized heating to specific regions of part
• Neat and clean joints
• Flameless processing
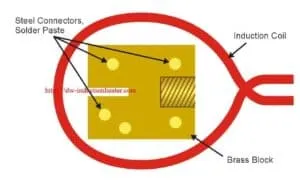
handheld induction brazing HVAC tubing
Handheld Induction Brazing HVAC Tubing
Refrigeration piping is always brazed as brazing makes a very solid leak-free joint that withstands high and low temperatures and pressures. When soldering refrigeration pipe it is best to use solder which has a composition of silver in it as the silver bounds with the copper and makes for an excellent leak free strong joint (capillary attraction).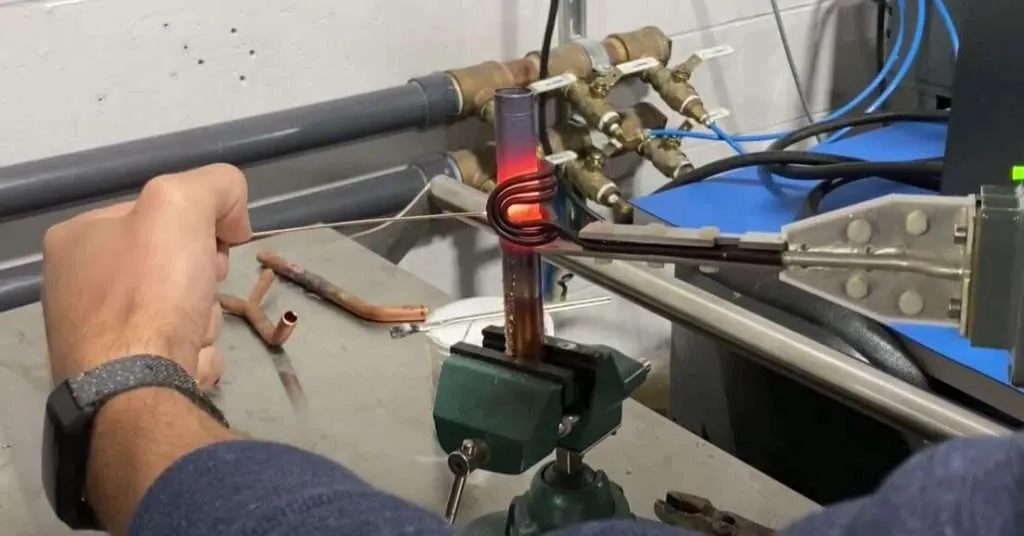
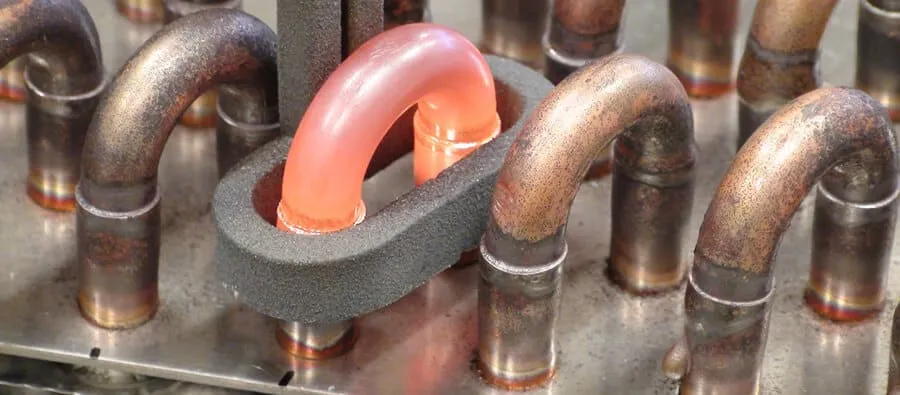
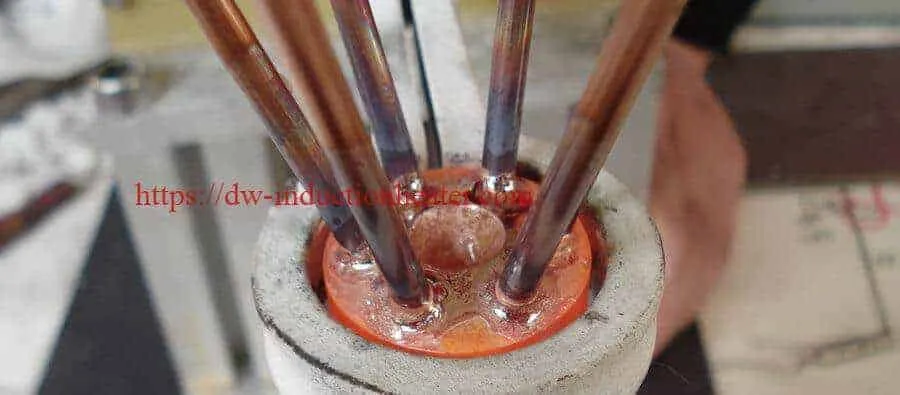

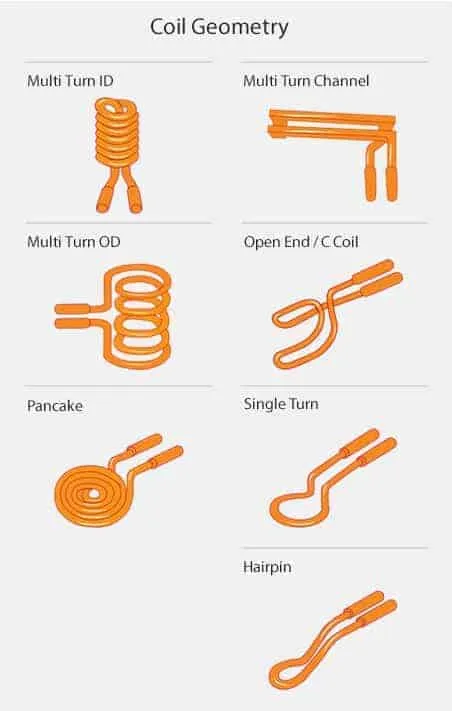
2022年5月30日星期一
Brazing Stainless Steel To Copper With Induction
Brazing Stainless Steel To Copper With Induction Heater
Objective Braze a stainless steel braided hose to copper elbows for a braided hose assembly.
Material Stainless steel braided hose 3/8” (9.5mm) OD, copper elbow 1/4” (6.3mm) OD, braze preform rings and black flux
Temperature 1400 ºF (760 ºC)
Frequency 300 kHz
Equipment • DW-UHF-6kW-III induction heating system, equipped with a remote workhead containing two 0.33μF capacitors for a total of 0.66μF
• An induction heating coil designed and developed specifically for this application.
Process: A two turn helical coil is used to heat the braided hose assembly. Braze rings are placed at the joint on the copper elbow and flux is applied to the entire surface of the assembly.
The assembly is placed in the heating coil and the braze flows within 30-45 seconds. This creates a liquid and gas tight braze between the copper and stainless steel braided hose.
Results/Benefits Induction heating provides:
• Liquid and gas-tight braze
• Energy efficient heat in a minimal amount of time
• Controllable braze flow through the use of braze rings
• Even distribution of heating
ultrasonic plastic welder for US plastic welding bonding Solutions
Ultrasonic plastic welder | ultrasonic welder | ultra sonic plastic welding machine with Automatic Frequency Chasing
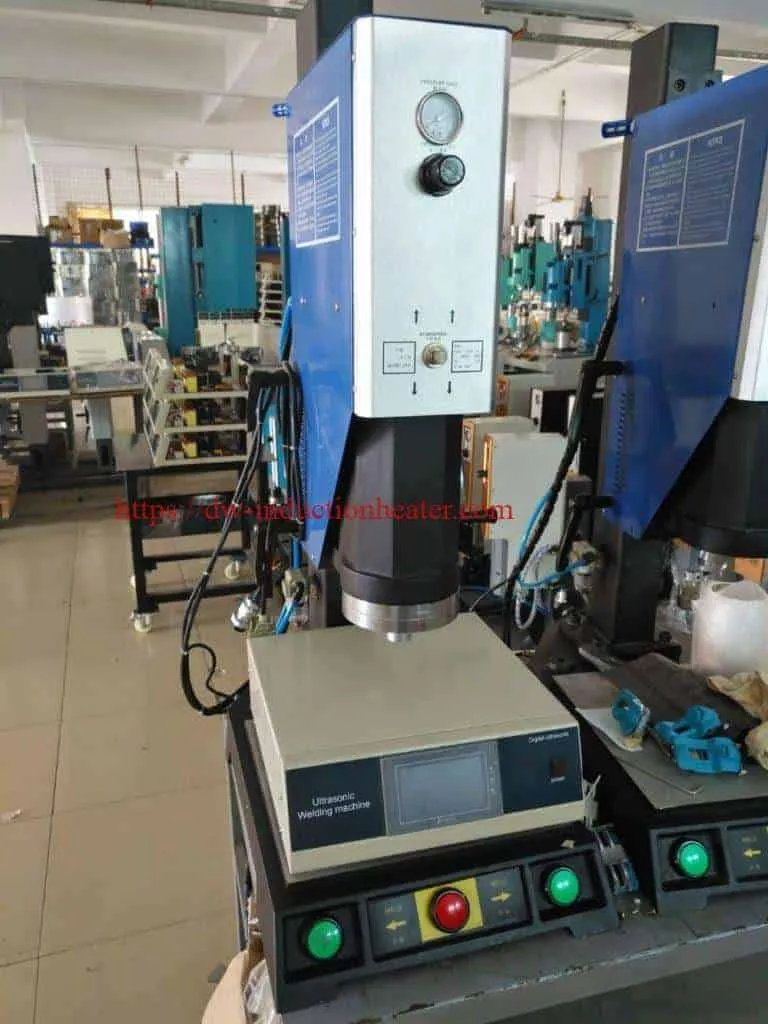

Model | 1520A | 1526A | 1532A | 1542A |
Frequency | 15KHz | |||
Power | 2000W | 2600W | 3200W | 4200W |
Voltage | 220V | |||
Capacity | 10-20 times/min | |||
Driving form | Pneumatic | |||
Stroke Length(Horn Journy) | 75mm | 100mm | ||
Output Time | 0.01-9.99S Adjustable | |||
Welding Area | Φ100 | Φ200 | Φ300 | Φ400 |
Electricity | AC | |||
Control mode | Numerical control | |||
Working air pressure | 1-7 Bar | |||
Weight | 90KG | 90KG | 90KG | 120KG |
Dimensions | 450*750*1100mm | 760*1000*1950mm |
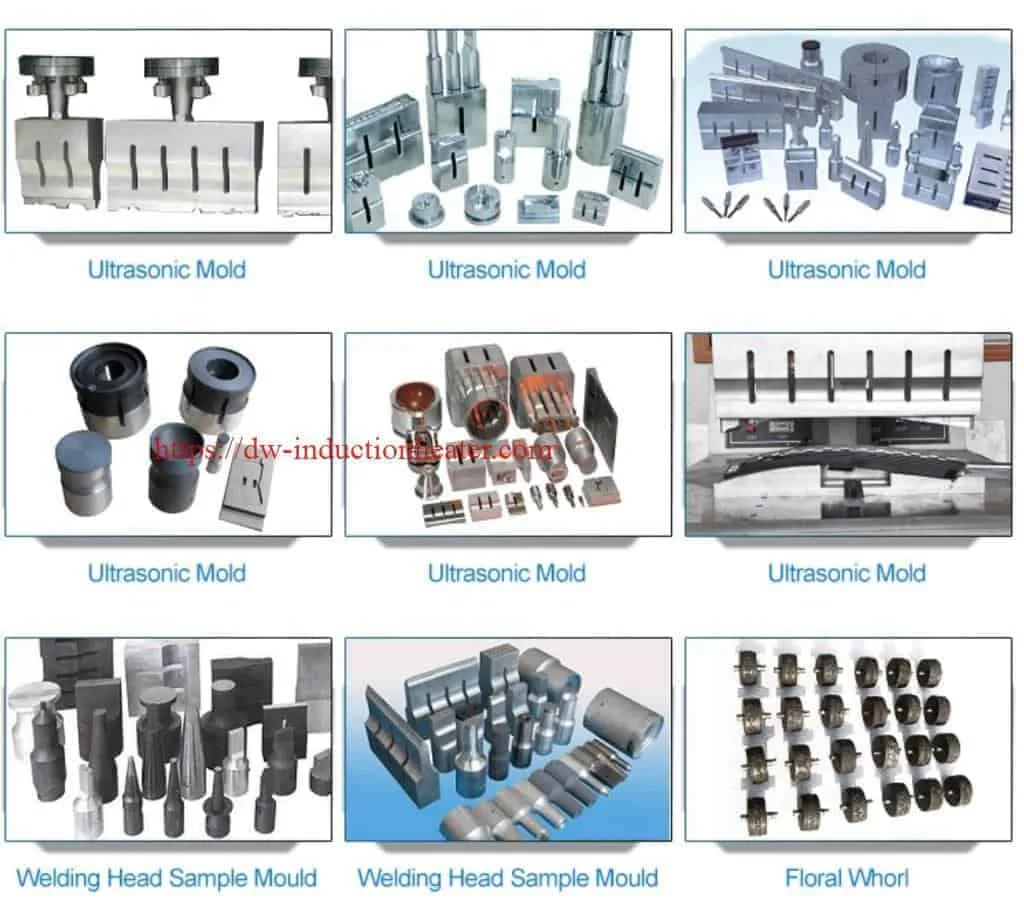
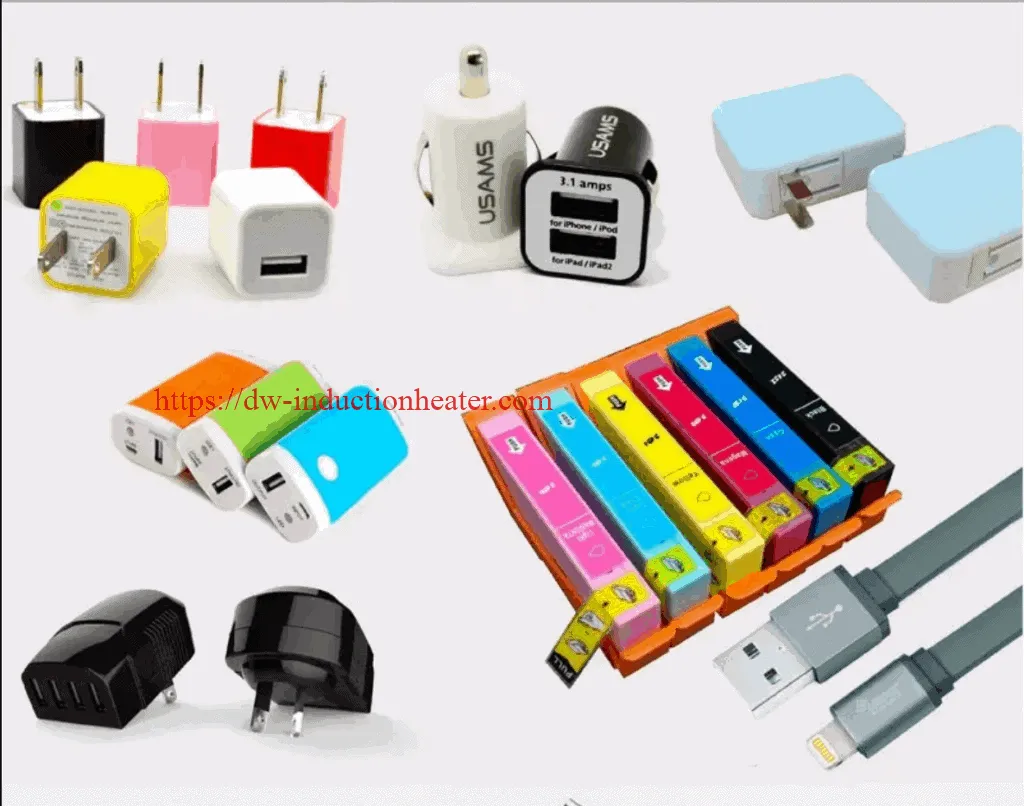

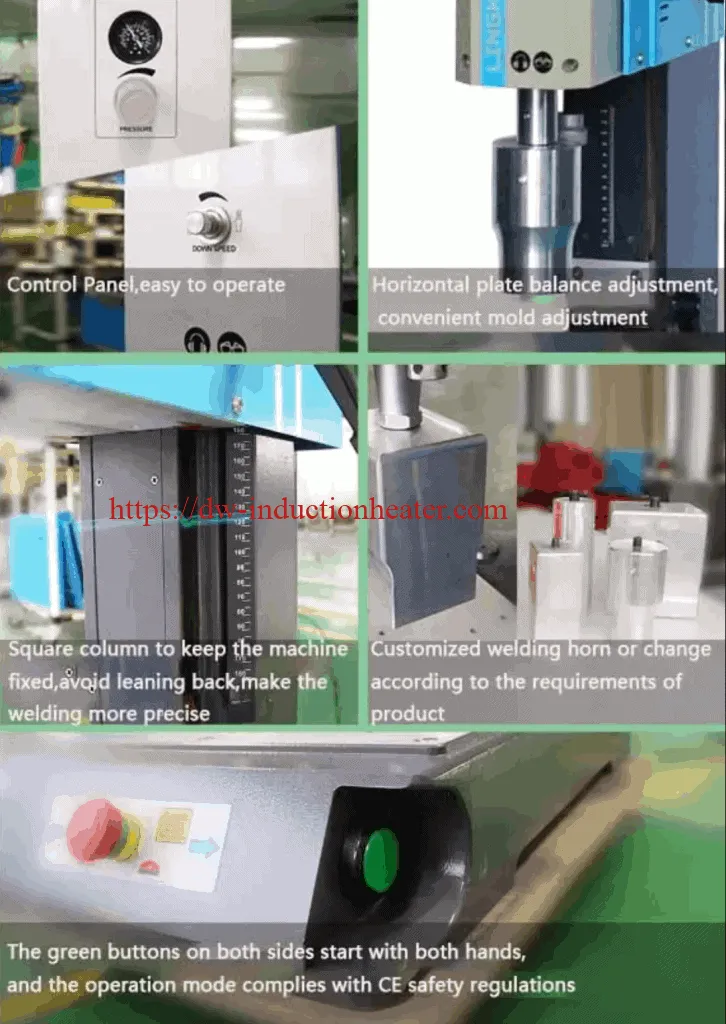
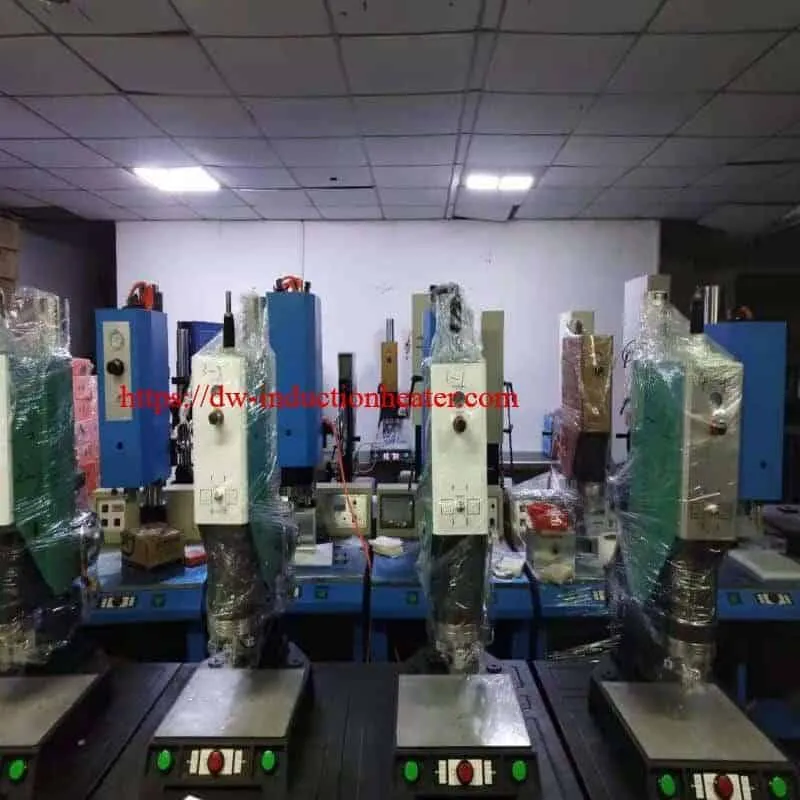

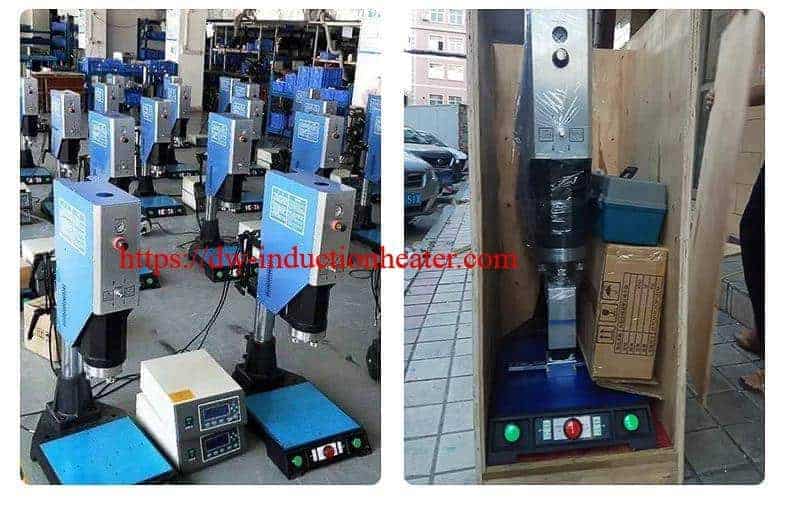
Induction Heating Wires For Hot Heading
Induction Heating Wires For Hot Heading With IGBT Induction Heating Units
Objective To heat multiple steel wires to 1350ºF (732ºC) for hot heading application
Material Steel wire 0.185” (4.4mm) OD
Temperature 1350 ºF (732ºC)
Frequency 141 kHz
Equipment • DW-UHF-6 kW induction heating system, equipped with a remote workhead containing one 0.66μF capacitor
• An induction heating coil designed and developed specifically for this application.
Process A two turn channel coil is used to heat 12 wires at a time to reach the required 130 parts per minute. The wires are placed 0.5” (12.7mm) on center. The top 0.3” (7.6mm) of the wires are
heated for 5 seconds to achieve the desired temperature.
Results/Benefits Induction heating provides:
• Hands-free heating that involves no operator skill for manufacturing
• Elimination of springback effect
• Extended die life
• Better grain flow and microstructure
• Even distribution of heating
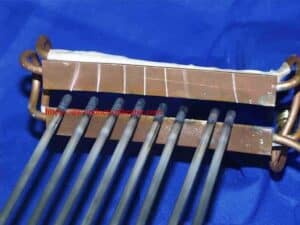
ultrasonic welding fabric machine for bonding nonwoven fabric
ultrasonic welding fabric machine| ultrasonic nonwoven fabric welder | ultra sonic nonwoven fabric welding equipment with Automatic Frequency Chasing
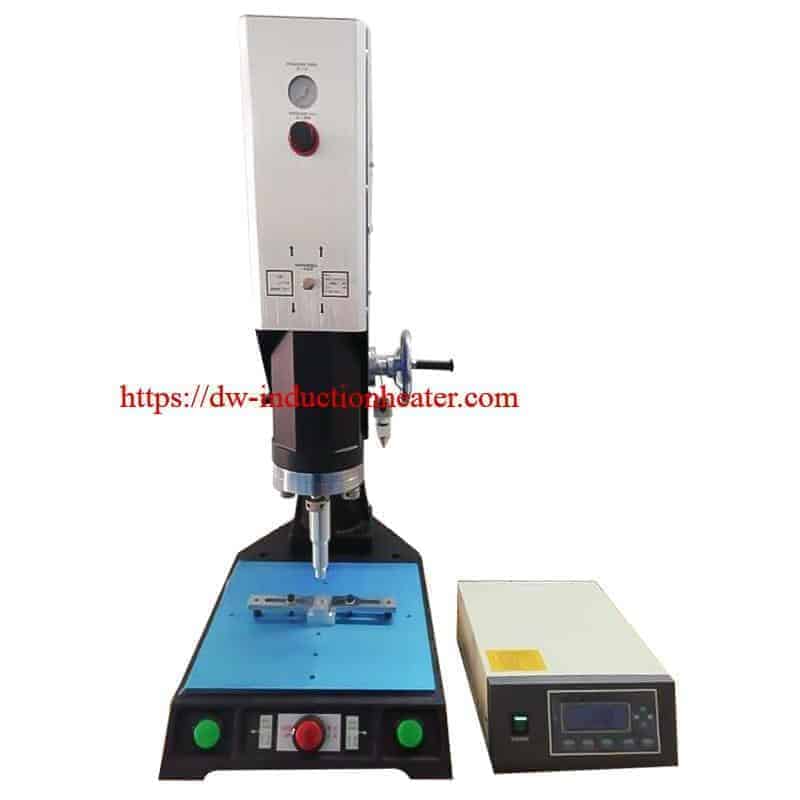
Main Functions:
1.According to the product requirements,drive mode can choose pneumatic, hydraulic or servo motor drive. 2. The welding temperature, heating time, cooling time, welding depth, pressure, transit time are adjustable parameters,etc 3.In accordance with the requirements of welding procedure, can choose semi-automatic or fully automatic mode; 4.Should be a variety of materials, can adjust the welding procedure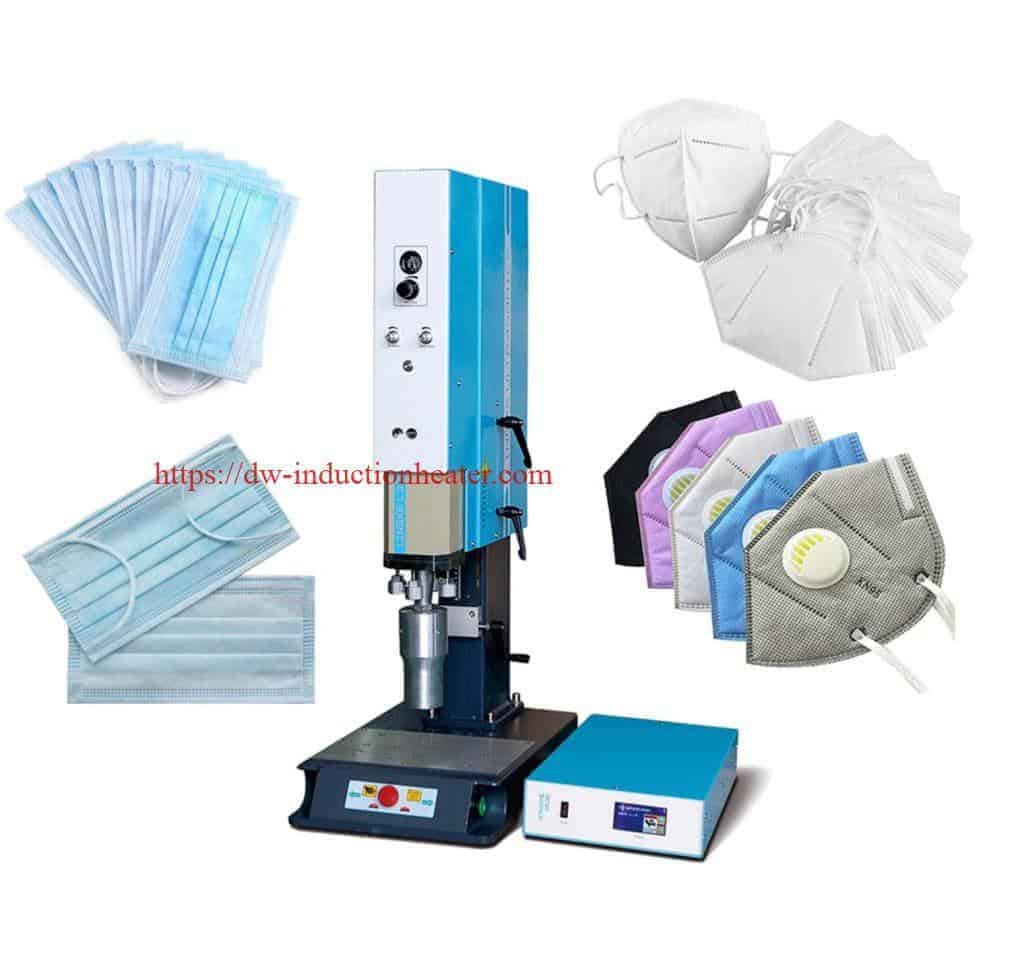
Model | 2015B | 2018B | 1522A | 1526A |
Frequency | 20KHZ | 15KHZ | ||
Power | 1500W | 1800W | 2200W | 2600W |
Max Stroke | 75-100mm | |||
Welding Time | 0.01-9.99sec | |||
Welding Area | φ100mm | φ120mm | φ150mm | φ200mm |
Dimensions | 450*750*1100mm | |||
Weight | 90KG |
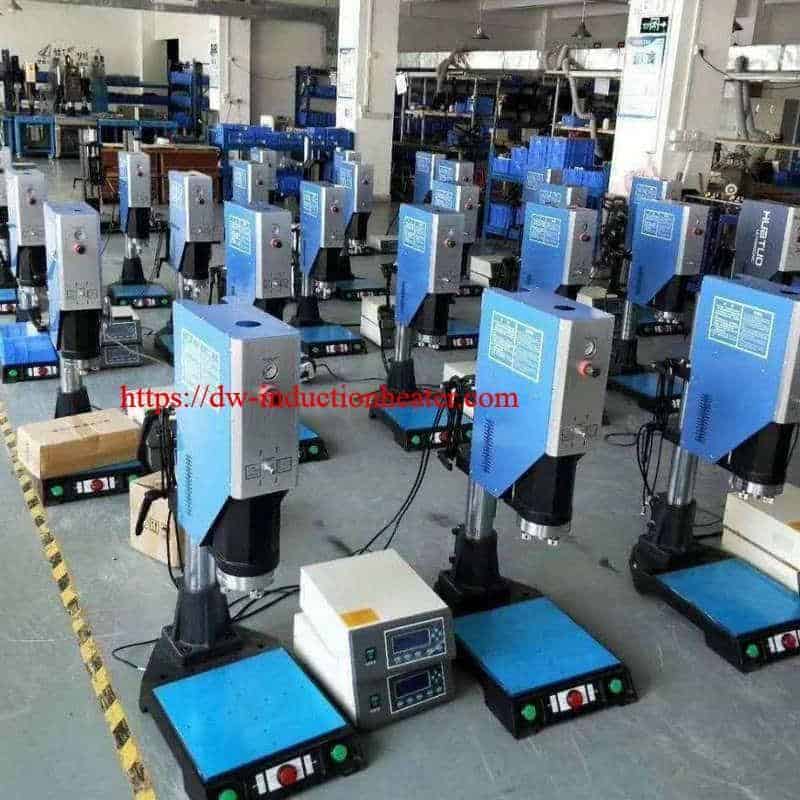
Application Industry | Application Products |
Automotive: | the car door welded baffle welding, automobile, car mats welding, automotive bumper repair welding, cotton insulation doors, seat wipers, engine cover, radiator cap spot, etc |
Consumer Products: | daily necessities, stationery, filter, folder and shell, pen stand, cosmetics box shell, the end of the toothpaste tube seal, mirror, insulated cup, lighter. |
Electronics: | recording, audio tape boxes and core wheel, disk enclosure, the board of mobile phone batteries and rectifier transformers, switches and sockets, remote control, |
Home appliances: | Balance ring, electronic clock, electric trumpeter hair dryer, steam iron water tank, |
Toy: | plastic toys, water guns, aquatic life video game, children dolls, plastic gifts, etc |
Film & Fabric: | Filters, Shower Curtains, Biodegradable Bag, Non-Woven Face Mark,..etc. |
Packaging: | Plastic pallet, Corrugated tray, hollow crate welding, zip lock welded, etc |
Medical: | Surgical Instruments,Testing Equipment,filters,I-V units,insulated trays..etc. |
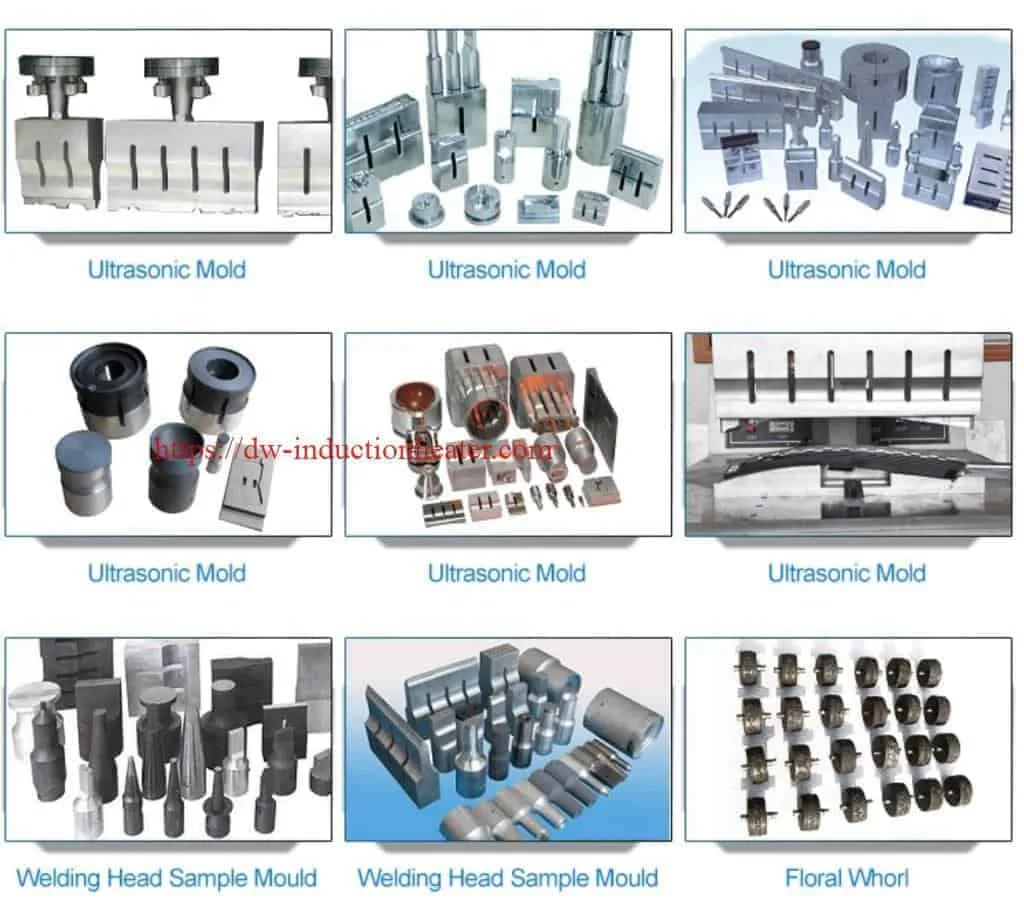
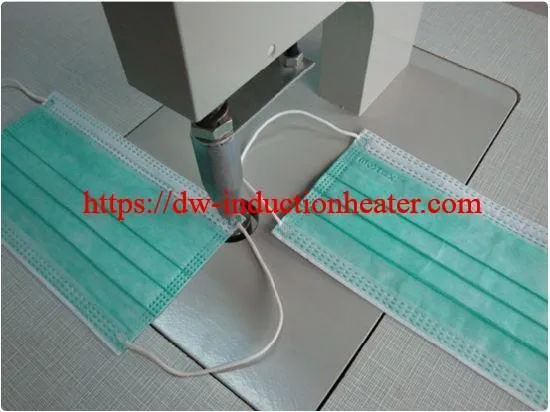
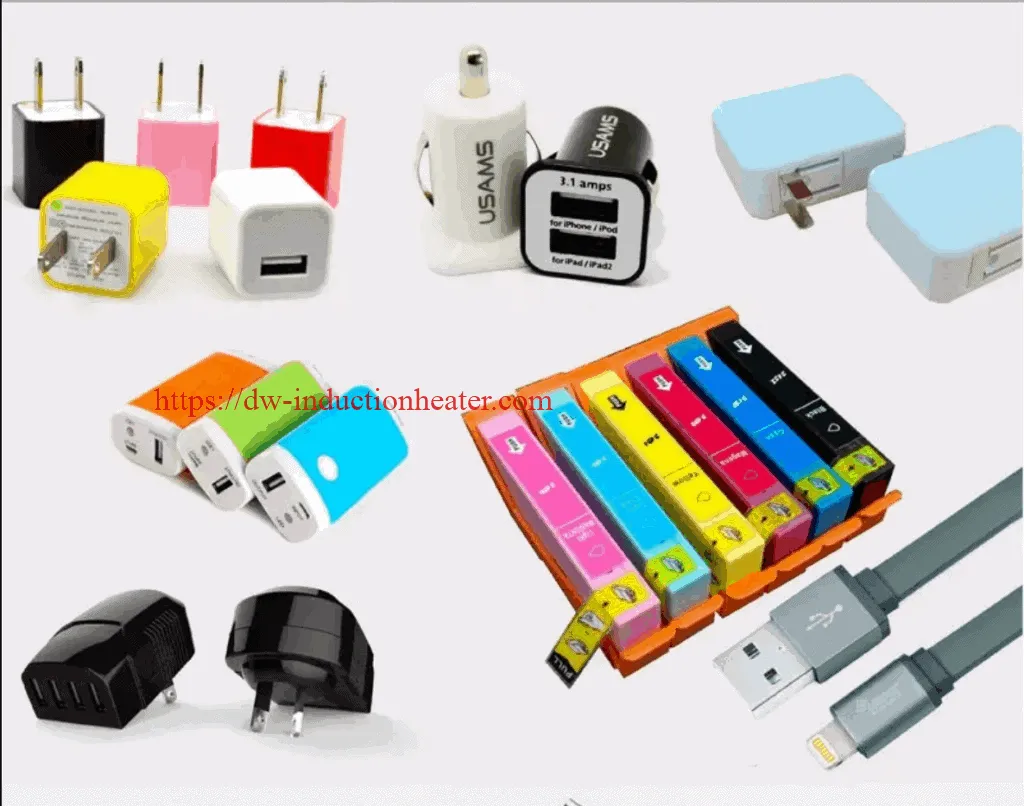

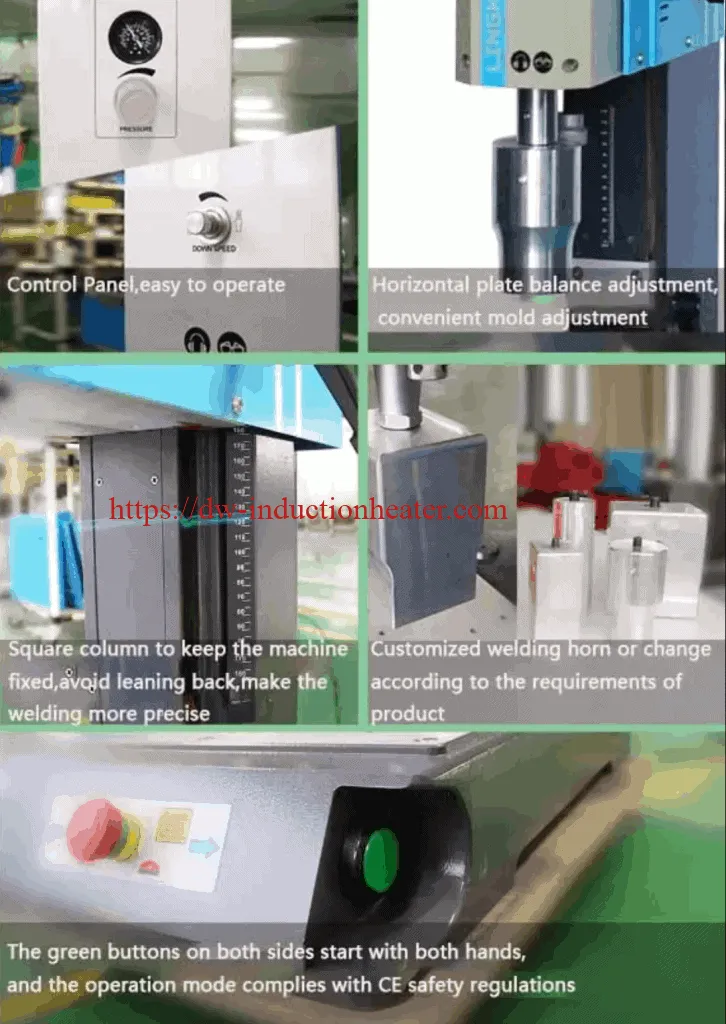

Induction Billets Heater Video
Induction Billets Heater Video
[embed]https://youtu.be/TuTzgyUYXe8[/embed]Induction Soldering Coaxial Cable
Objective
Induction Soldering coaxial cable to connector ring and pin in two steps in under 5 seconds by reaching a temperature of 500°F (260°C) with induction heating.


Process:
Results/Benefits:
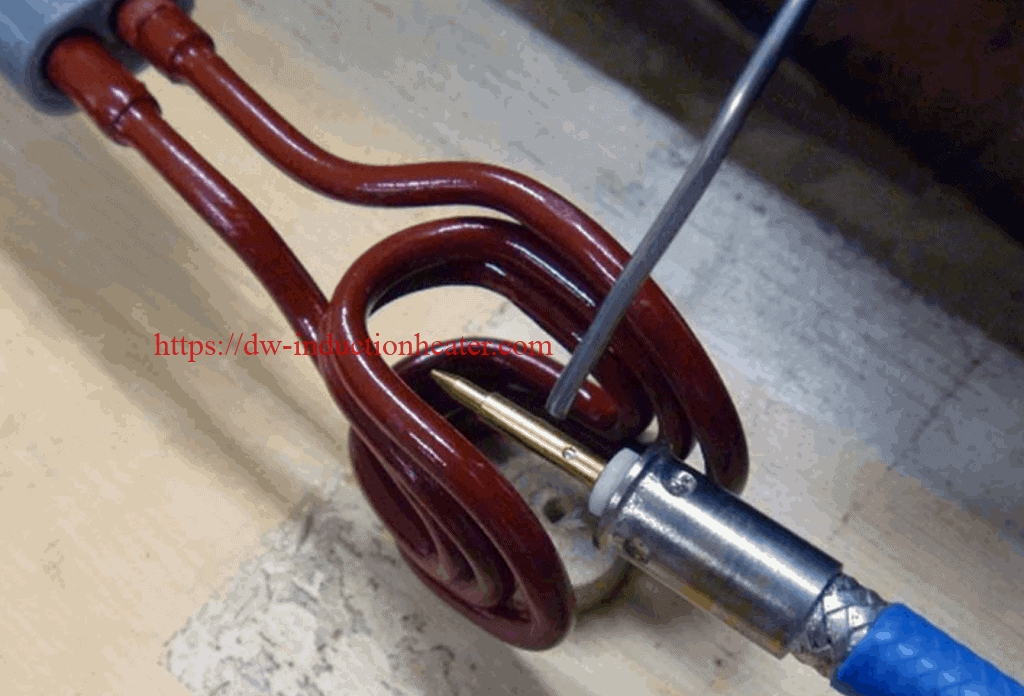


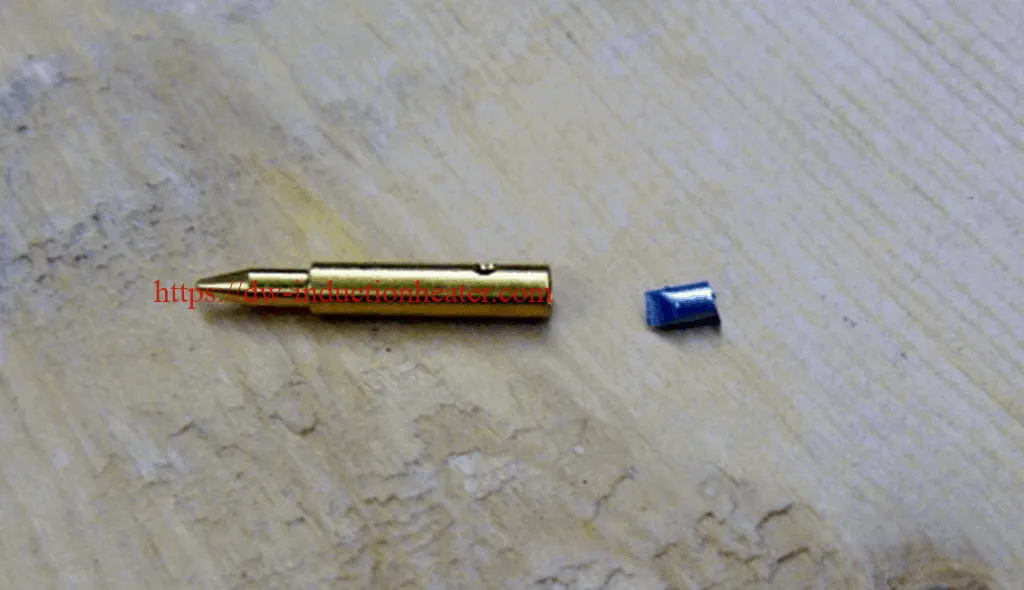
- The coaxial cable and connector were placed vertically inside the coil.
- Induction heating was applied for 3 seconds, at which point the part is hot enough for soldering.
- The induction soldering wire was fed between the cable braid and connector.
- Solder wire was inserted into the center pin, and the center pin was placed in the coil.
- The cable with connector was placed above the pin.
- Induction heat was applied for 1.5 seconds, after which the part was hot enough for soldering.
- The center conductor was inserted into the pin.
- The assembly was inspected to ensure that the soldering was successful.

- Strong durable joints and faster heating cycles
- Selective and precise heat zone, resulting in less part distortion and joint stress
- Technology without pollution, which is both clean and safe
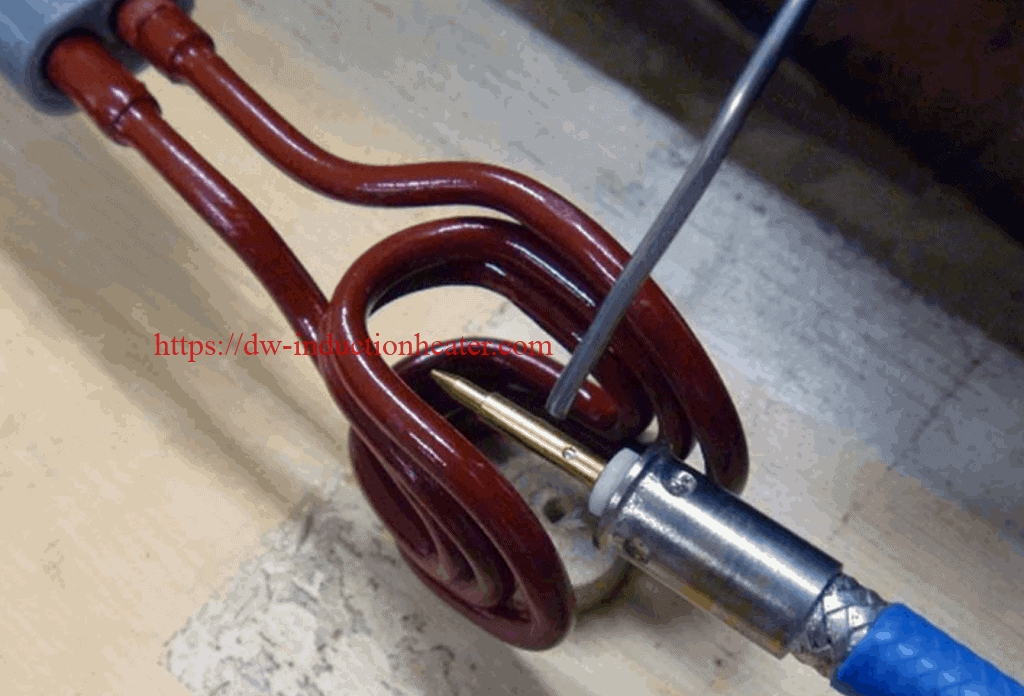


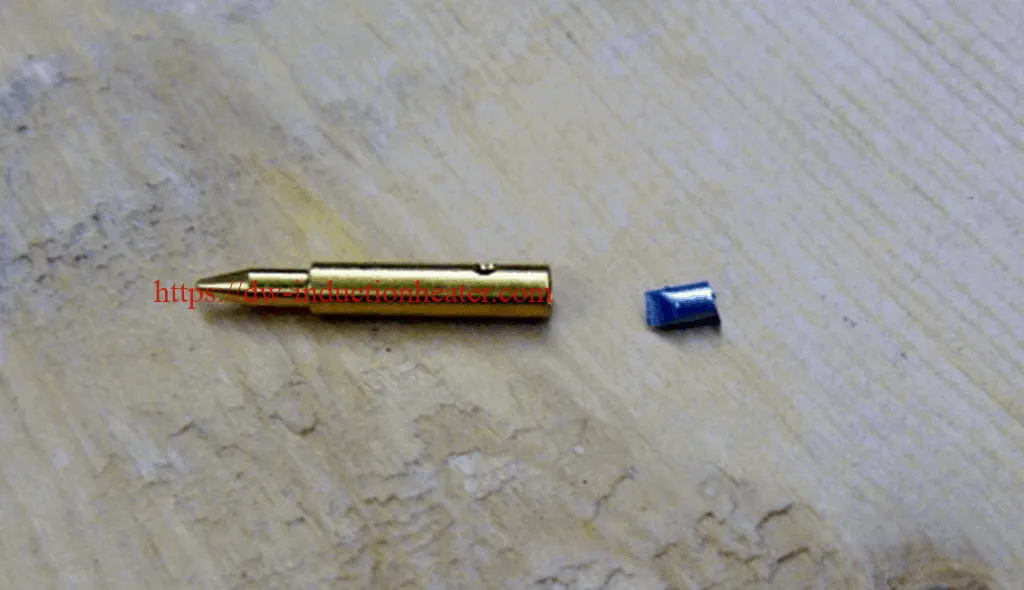

2022年5月29日星期日
Induction Soldering Copper Wires
Induction Soldering Copper Wires With IGBT High Frequency Heating Units
Objective Soldering two copper wires to pre-installed turrets on a copper buss bar
Material Solder dipped copper/nickel buss bar, 2 tinned stranded copper wires, brazing stick
Temperature 446 ºF (230 ºC)
Frequency 230 kHz
Equipment • DW-UHF-6kW induction heating system, equipped with a remote workhead containing one 1.2μF capacitor.
• An induction heating coil designed and developed specifically for this application.
Process A four turn split helical coil is used to solder the buss bar assembly. The 2 copper wires are applied to the turrets and power is applied for 30 seconds. The brazing stick is fed by hand to the heated parts and the braze flows evenly, creating the joint.
Results/Benefits Induction heating provides:
• Reduced solder time
• Even distribution of heating
• Joint to joint consistency
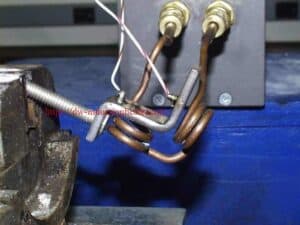
Induction Hot Forming Steel Pipe
Induction Hot Forming Steel Pipe
Objective : To heat a magnetic steel pipe to the targeted temperature to enable pipe induction bending; the objective is to create u-bends in pipes for boiler systems Material: Steel pipes (2.5”/64 mm OD bent steel pipe) Temperature: 2010 °F (1099 °C) Frequency: 8.8 kHz Equipment : DW-MF-250 kW, 5-15 kHz induction heating power supply with a remote workhead containing eight 6.63 μF capacitors for a total of 53 μF. - A single position six-turn channel induction heating coil designed and developed for this application Process: The steel pipe was placed inside the induction coil, and it heated to temperature within 120 seconds with an DW-MF- 250kW/10 kHz induction heating system.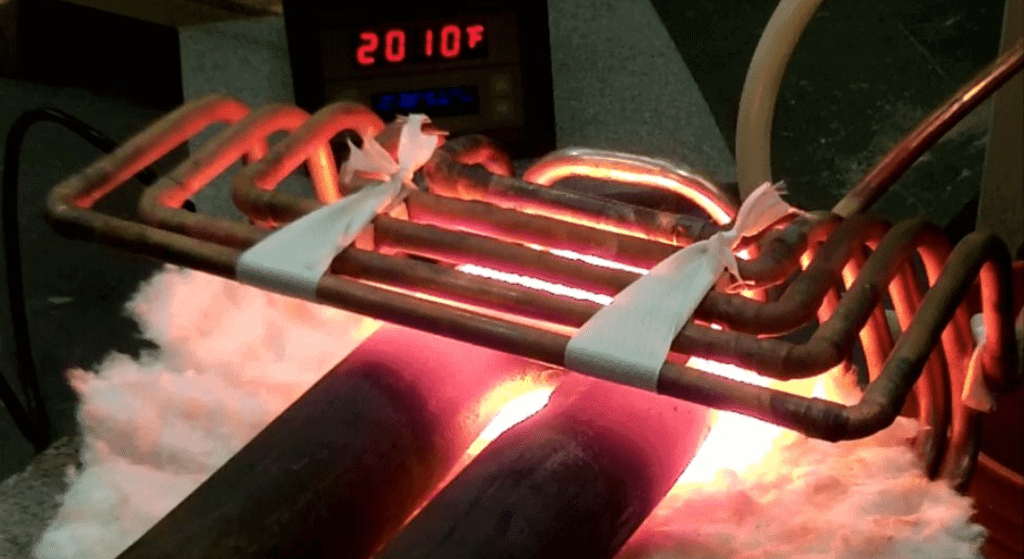
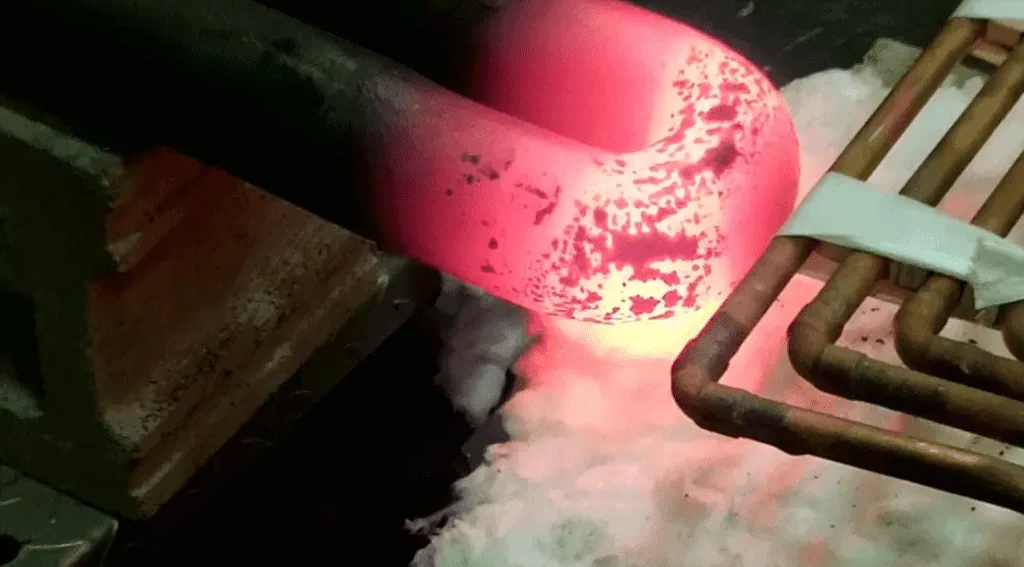
订阅:
博文 (Atom)
关注者
博客归档
-
▼
2022
(1729)
-
▼
五月
(167)
- Induction Brazing Carbide
- induction hot forming and forging process
- Induction Soldering Brass Tube-Pipe
- principle of electromagnetic induction heating
- High frequency induction brazing steel tube to ste...
- Soldering Steel To Brass With Induction Heater
- handheld induction brazing HVAC tubing
- Brazing Stainless Steel To Copper With Induction
- ultrasonic plastic welder for US plastic welding b...
- Induction Heating Wires For Hot Heading
- ultrasonic welding fabric machine for bonding nonw...
- Induction Billets Heater Video
- Induction Soldering Coaxial Cable
- Induction Soldering Copper Wires
- Induction Hot Forming Steel Pipe
- Handheld Induction Brazing Copper Tubing and Fitting
- induction brazing brass pipe to brass part
- Brazing Brass To Copper With Induction
- Application of Induction Heating In Food
- Induction Heating Plasma
- Induction Brazing Aluminum to Aluminum Tube
- Induction Annealing Brass Bullet Shells
- Induction Soldering Process Video
- Induction Soldering Steel Parts
- Induction Heating Basic
- Technology of Induction Forming Steel Plate
- induction brazing stainless steel to copper
- Induction Soldering magnetic steel pins
- Brazing Brass Pipe With Induction
- Induction Brazing Steel Tips
- induction heating for surface quenching of steel
- Induction Brazing Copper To Copper Parts
- Induction Brazing Carbide To Stainless Steel
- Brazing Brass To Copper With Induction
- Induction Soldering Brass Connector
- What Is Induction Heating?
- Induction annealing stainless steel wire
- Handheld Brazing Stainless Steel Tube
- Brazing Copper Assemblies With Induction
- Brazing stainless steel with induction
- Induction Soldering Wire To Aluminum Lug
- induction coating removal for removing paint
- induction heating stainless steel insertion applic...
- Brazing Carbide To Steel With Induction
- induction heating stainless steel insertion applic...
- Induction Soldering Steel Parts
- induction heating steel casting
- Brazing Carbide-Steel Tool with Induction
- What is induction bonding?
- Technology of Induction Forming Steel Plate
- induction brazing steel carbide cap to shaft
- induction coating removal for removing paint
- Induction Catheter Tipping Heating
- Induction Brazing Copper to Stainless Steel Process
- Small High Frequency Induction Melting Furnace
- Induction Brazing Carbide To Stainless Steel
- Brazing carbide shaft with induction
- induction fluid pipe heater
- What is induction bonding?
- Induction Brazing Stainless Steel Tubing Joints
- Induction Heat Staking for Spring Wire and Nylon P...
- Induction Wire and Cable Heating
- Handheld Brazing Stainless Steel Tube
- Induction Brazing Aluminum Tube T Joints
- Aluminum Scrap Melting Recycling Induction Furnace
- induction brazing steel carbide cap to shaft
- Inductioin Shrink Fitting Aluminum Pulley
- What is induction bonding?
- Induction Heat Treating Surface Process
- Induction Annealing Copper Tubes
- Induction brazing aluminum pipes
- Induction Soldering Cable to Metallic Plate
- High frequency induction brazing steel tube to ste...
- Brazing Aluminum Pipes Assembly With Induction
- Induction Soldering Brass Heating Exchanger
- Why Choose Induction Heating and what are its adva...
- High Frequency Induction Brazing Diamond Inserts
- Soldering Antenna Wire With Induction
- Induction Bar End Heating Furnace
- High Frequency Welding
- Brazing Carbide-Steel Tool with Induction
- Brazing Thin Copper Tube With Induction
- Heating Shrink Fitting Camshaft Gear
- RF Soldering Circuit Board
- Induction Brazing Heating Exchanger Copper Pipes
- induction heating graphite susceptor
- Induction Catheter Tipping Heating
- Induction Aluminum Brazing Process
- induction Brazing copper rods to brass strips
- Induction Heating Solutions For Cancer Research
- Induction Soldering Aluminum Housing
- Induction Preheating Hot Heading
- Induction Brazing Stainless Steel Tubing Joints
- Why Choose Induction Heating and what are its adva...
- Induction Brazing Steel Wire
- induction heating for drying food processing industry
- Induction Annealing Aluminum
- Induction Heating Steel Pipe To Remove plastic coa...
- Why choose Induction Brazing?
- Induction Annealing Copper Wire
-
▼
五月
(167)
我的简介

- HLQ induction heating machine
- HLQ induction heating machine manufacturer provides the service of induction brazing,melting,hot forming,hardening surface,annealing,shrink fitting,PWHT,etc.