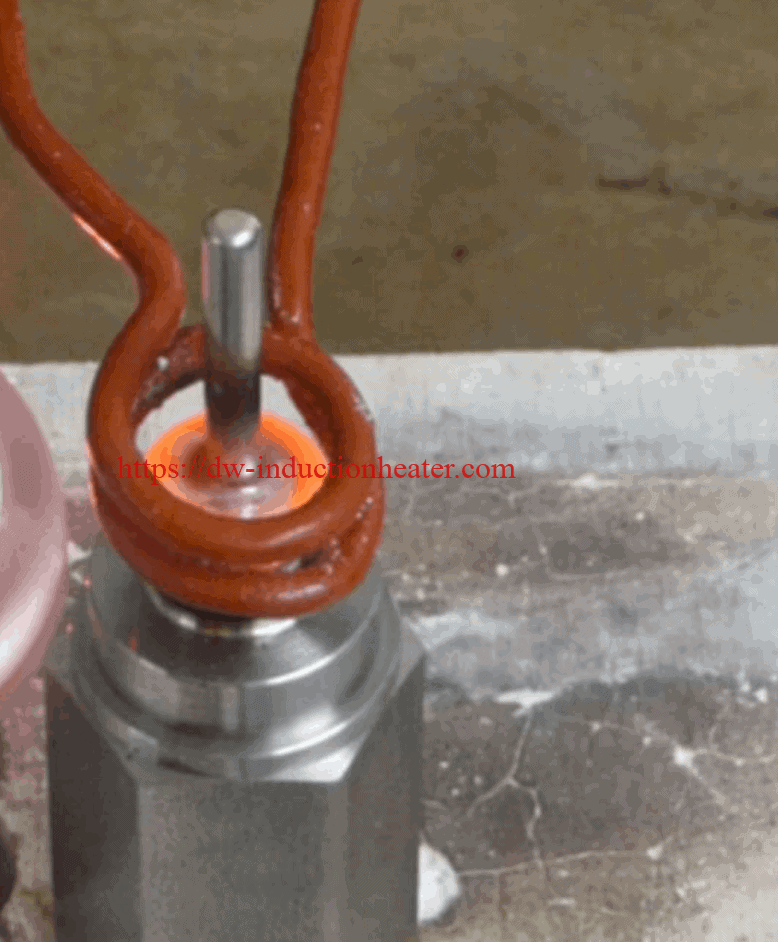
High frequency magnetic induction brazing stainless steel to steel process
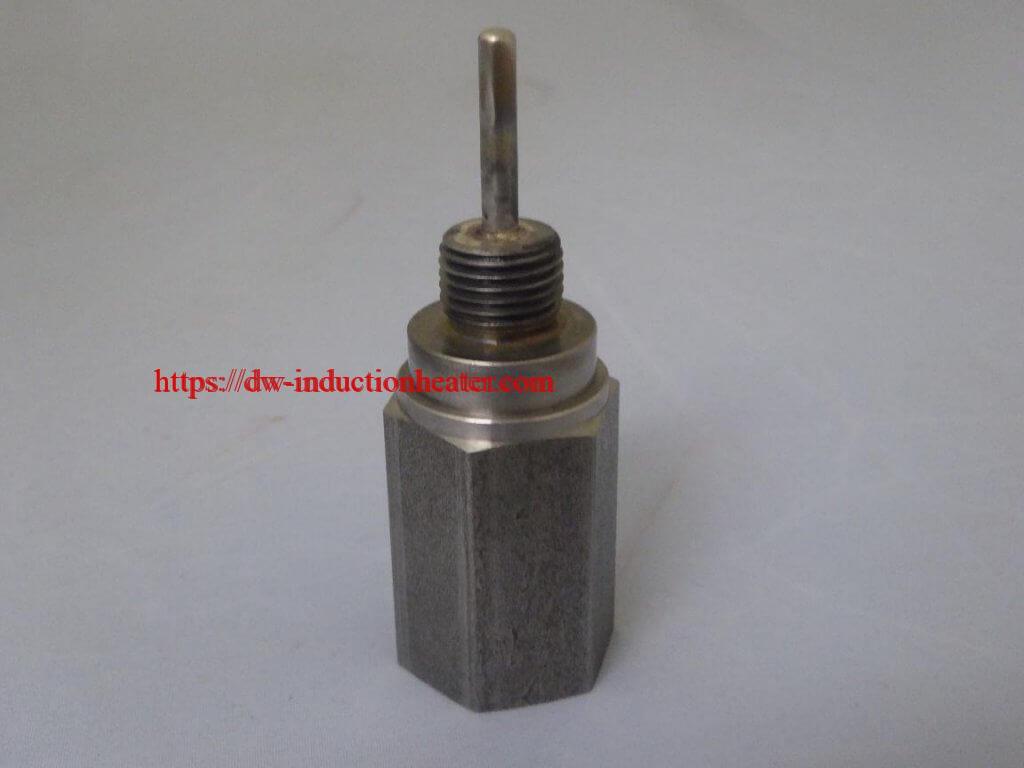


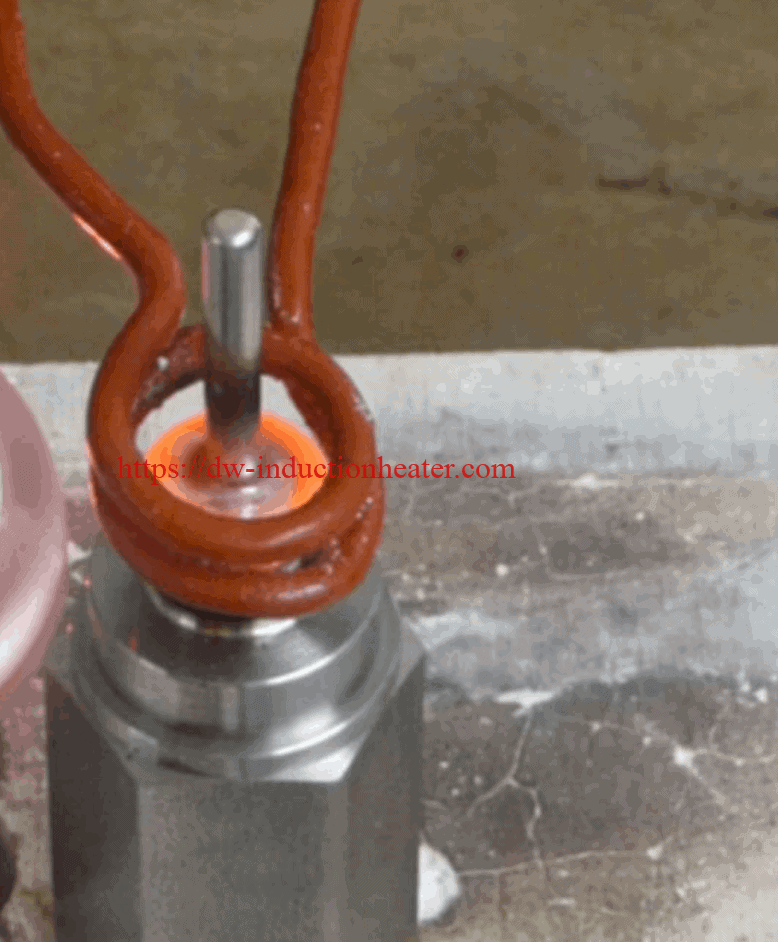
Series |
Model |
Input power Max |
Input current Max |
Oscillate frequency |
Input Voltage |
Duty cycle |
|
M
.
F
. |
DW-MF-15 Induction Generator |
15KW |
23A |
1K-20KHZ
According to the application |
3*380V
380V±20% |
100% |
|
DW-MF-25 Induction Generator |
25KW |
36A |
|||||
DW-MF-35Induction Generator |
35KW |
51A |
|||||
DW-MF-45 Induction Generator |
45KW |
68A |
|||||
DW-MF-70 Induction Generator |
70KW |
105A |
|||||
DW-MF-90 Induction Generator |
90KW |
135A |
|||||
DW-MF-110 Induction Generator |
110KW |
170A |
|||||
DW-MF-160 Induction Generator |
160KW |
240A |
|||||
DW-MF-45 Induction Heating Rod Forging Furnace |
45KW |
68A |
1K-20KHZ |
3*380V
380V±20% |
100% |
||
DW-MF-70 Induction Heating Rod Forging Furnace |
70KW |
105A |
|||||
DW-MF-90 Induction Heating Rod Forging Furnace |
90KW |
135A |
|||||
DW-MF-110 Induction Heating Rod Forging Furnace |
110KW |
170A |
|||||
DW-MF-160 Induction Heating Rod Forging Furnace |
160KW |
240A |
|||||
DW-MF-15 Induction Melting Furnace |
15KW |
23A |
1K-20KHZ |
3*380V
380V±20% |
100% |
||
DW-MF-25 Induction Melting Furnace |
25KW |
36A |
|||||
DW-MF-35 Induction Melting Furnace |
35KW |
51A |
|||||
DW-MF-45 Induction Melting Furnace |
45KW |
68A |
|||||
DW-MF-70 Induction Melting Furnace |
70KW |
105A |
|||||
DW-MF-90 Induction Melting Furnace |
90KW |
135A |
|||||
DW-MF-110 Induction Melting Furnace |
110KW |
170A |
|||||
DW-MF-160 Induction Melting Furnace |
160KW |
240A |
|||||
DW-MF-110 Induction Hardening Equipment |
110KW |
170A |
1K-8KHZ |
3*380V
380V±20% |
100% |
||
DW-MF-160Induction Hardening Equipment |
160KW |
240A |
|||||
H
.
F
. |
DW-HF-04 Series |
DW-HF-4KW-A |
4KVA |
15A |
100-250KHZ |
Single phase 220V |
80% |
DW-HF-15 Series |
DW-HF-15KW-A
DW-HF-15KW-B |
15KVA |
32A |
30-100KHZ |
Single phase 220V |
80% |
|
DW-HF-25 Series |
DW-HF-25KW-A
DW-HF-25KW-B |
25KVA |
23A |
20-80KHZ |
3*380V
380V±10% |
100% |
|
DW-HF-35 Series |
DW-HF-35KW-B |
35KVA |
51A |
||||
DW-HF-45 Series |
DW-HF-45KW-B |
45KVA |
68A |
||||
DW-HF-60 Series |
DW-HF-60KW-B |
60KVA |
105A |
||||
DW-HF-80 Series |
DW-HF-80KW-B |
80KVA |
130A |
||||
DW-HF-90 Series |
DW-HF-90KW-B |
90KVA |
160A |
||||
DW-HF-120 Series |
DW-HF-120KW-B |
120KVA |
200A |
||||
U
.
H
.
F
.
|
DW-UHF-3.2KW |
3.2KW |
13A |
1.1-2.0MHZ |
Single phase220V
±10% |
100% |
|
DW-UHF-4.5KW |
4.5KW |
20A |
|||||
DW-UHF-045T |
4.5KW |
20A |
|||||
DW-UHF-045L |
4.5KW |
20A |
|||||
DW-UHF-6.0KW |
6.0KW |
28A |
|||||
DW-UHF-06A |
6.0KW |
28A |
|||||
DW-UHF-6KW-B |
6.0KW |
28A |
|||||
DW-UHF-10KW |
10KW |
15A |
100-500KHZ |
3*380V
380V±10% |
100% |
||
DW-UHF-20KW |
20KW |
30A |
50-250KHZ |
||||
DW-UHF-30KW |
30KW |
45A |
50-200KHZ |
||||
DW-UHF-40KW |
40KW |
60A |
50-200KHZ |
||||
DW-UHF-60KW |
60KW |
90A |
50-150KHZ |
Induction brazing brass studs to copper pipes
The Client:
A manufacturer of coils for industrial heating applications.
Equipment:
DW-UHF-40KW Induction Brazing Systems – two modules.