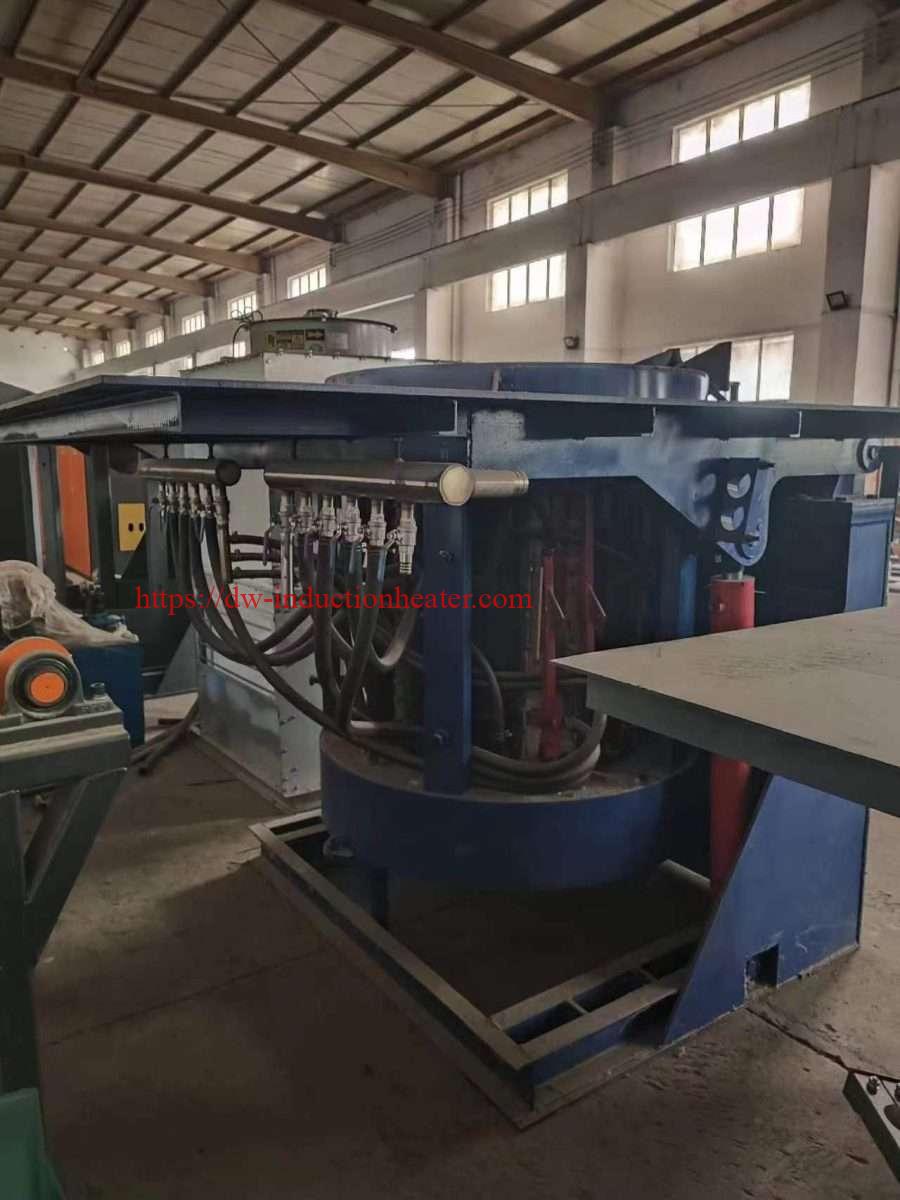
Casting Iron Melting Induction Furnace: Revolutionizing the Foundry Industry
A casting iron melting induction furnace, also known as an induction melting furnace, is a type of equipment used for melting iron and other metals using the principle of electromagnetic induction. It is commonly used in foundries, metalworking industries, and other applications where precise control over the melting process is required.
The foundry industry plays a vital role in the manufacturing sector by providing essential components for various industries, such as automotive, aerospace, and construction. One of the crucial processes in foundries is melting iron, which is a fundamental step in the production of cast iron components. Over the years, advancements in technology have revolutionized the way iron is melted, with the induction furnace emerging as a game-changer. This article aims to provide an in-depth analysis of the casting iron melting induction furnace, its working principle, benefits, and its impact on the foundry industry.
- Historical Background of Iron Melting
Before delving into the specifics of the induction furnace, it is essential to understand the historical background of iron melting. The process of melting iron dates back thousands of years, with ancient civilizations using primitive furnaces fueled by charcoal. These traditional furnaces were time-consuming, labor-intensive, and energy-inefficient. However, they laid the foundation for the development of more sophisticated melting techniques.
- Introduction to the Induction Furnace
The
induction furnace, which emerged in the late 19th century, revolutionized the foundry industry. Unlike traditional furnaces, which rely on direct combustion of fuel, the induction furnace utilizes electromagnetic induction to generate heat. It consists of a crucible surrounded by a copper coil, which induces an alternating magnetic field when an electric current passes through it. This magnetic field creates eddy currents within the conductive material, leading to resistive heating and ultimately melting the iron.
- Working Principle of the Induction Furnace
The working principle of the induction furnace involves three main components: the power supply, the crucible, and the coil. The power supply provides an alternating current, typically at high frequencies, to the coil. The coil, made of copper or other conductive materials, surrounds the crucible, which contains the iron to be melted. When the current flows through the coil, it generates a magnetic field, which induces eddy currents within the conductive material of the crucible. These eddy currents produce resistive heat, rapidly increasing the temperature and melting the iron.
- Types of Induction Furnaces
There are several types of induction furnaces used in the foundry industry, each catering to specific melting requirements. These include coreless induction furnaces, channel induction furnaces, and crucible induction furnaces. Coreless induction furnaces are widely used for melting iron due to their efficiency and ability to handle large volumes. Channel induction furnaces are suitable for continuous melting and pouring processes. Crucible induction furnaces, on the other hand, are ideal for small-scale foundries or specialized applications.
- Benefits of Induction Furnaces
The adoption of induction furnaces in the foundry industry has brought numerous benefits, making it the preferred choice for melting iron.
5.1 Energy Efficiency
Induction furnaces are highly energy-efficient compared to traditional furnaces. The absence of direct combustion reduces heat loss, resulting in lower energy consumption and reduced greenhouse gas emissions. Additionally, the rapid melting process of induction furnaces minimizes the time required for each melt, further enhancing energy efficiency.
5.2 Precision and Control
Induction furnaces offer precise control over temperature and melting parameters, ensuring consistent quality and repeatability in the production process. The ability to monitor and adjust parameters in real-time allows foundries to optimize melting conditions for specific iron grades or component requirements.
5.3 Safety and Environmental Considerations
Induction furnaces provide a safer working environment for foundry workers compared to traditional furnaces. The absence of open flames and reduced emissions of harmful gases, such as carbon monoxide, improves air quality and reduces the risk of accidents. Additionally, the closed system of induction furnaces minimizes the release of pollutants into the atmosphere, promoting environmental sustainability.
5.4 Versatility and Adaptability
Induction furnaces offer versatility in terms of melting various iron grades, including gray iron, ductile iron, and steel. The ability to melt different alloys and adjust melting parameters makes induction furnaces suitable for a wide range of foundry applications. Furthermore, induction furnaces can be easily integrated into existing foundry operations, allowing for seamless adaptation and improved productivity.
- Impact on the Foundry Industry
The introduction of induction furnaces has had a significant impact on the foundry industry, transforming the way iron is melted and cast. The efficiency, precision, and adaptability of induction furnaces have led to improved productivity, reduced costs, and enhanced product quality. Foundries that have embraced induction furnaces have gained a competitive edge, attracting new customers and expanding their market share. Moreover, the environmental benefits of induction furnaces align with sustainable manufacturing practices, positioning foundries as responsible contributors to the global economy.
Conclusion
The
casting iron induction furnace has revolutionized the foundry industry, offering numerous advantages over traditional melting methods. Its energy efficiency, precision, safety, and adaptability have transformed the way iron is melted, leading to improved productivity and product quality. The induction furnace's impact on the foundry industry is undeniable, with foundries worldwide embracing this technology to stay ahead in a competitive market. As advancements continue, the induction furnace is poised to further shape the future of iron melting in the foundry industry.
https://dw-inductionheater.com/product/casting-rion-melting-induction-furnace?feed_id=220931&_unique_id=64c4d045e1e4f