Energy savings at the induction drying grain with induction heating method
Annually Kazakhstan produces around 17-19 million tons of grain in clean weight,exports about 5 million tons of grain, and the average volume of domestic consumption reaches 9-11 million tons. Further development of the grain industry and promotion of grain export requires developing the infrastructure of storage, transportation and drying of grain, including the construction of new and reconstruction of the old grain silos, construction of port terminals and purchase of dry cargo vessels and grain carriers (Baum, 1983). There is a need to modernize the industry and the task requires a intensive efforts of the state and national grain producers.
Participants of Astana Kazakh Grain Forum V KAZGRAIN-2012 discussed the current state of grain market, trends and price expectations, as well as challenging issues in logistics and infrastructure. It was noted that 10 years ago Kazakhstan could not be considered as a grain exporter, while in current time the export issues are recognized as priority ones. And the production and drying of grain takes one of the leading places both in agroindustrial complex, and the economy as a whole.
Analysis of experience of many manufacturing enterprises in post-harvest grain processing proves that the primary task in ensuring the safety and quality of newly harvested seeds is their drying. Importance of grain drying increases in the humid zone: delay in drying or carrying out this operation with violation of technological regimes inevitably cause crop losses. According to the researches in 25-28% humidity of heap for three days the germination decreases by 20%. And the losses of dry matter makes 0.7-1% per day when a moisture of the grain heap is 37% (Ginzburg, 1973).
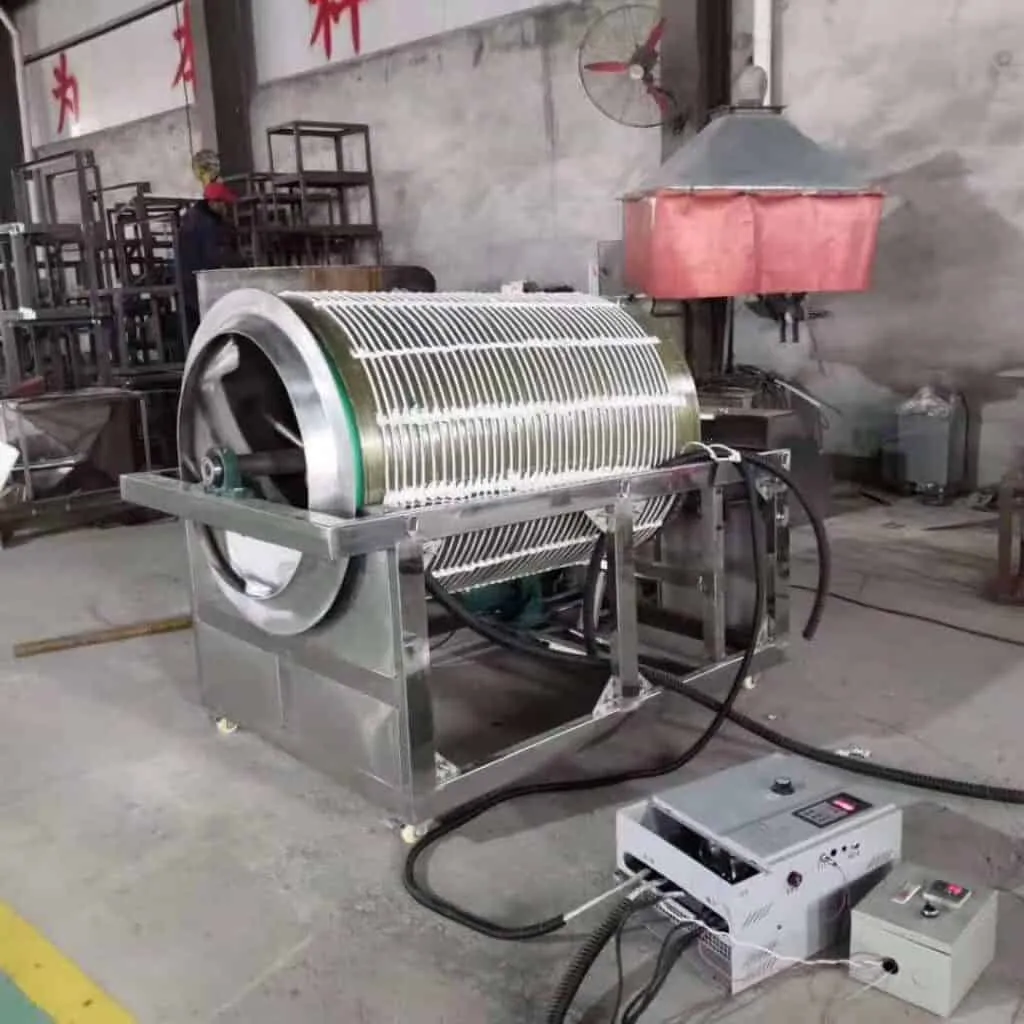
The important factors in efficient use of dryers in agriculture are provision of higher grain quality, increase of bandwidth of units, as well as lowering energy costs. Base for improving the effectiveness of existing dryers in agriculture is ensuring sufficient and stable removal of moisture from one cubic meter in cameras of grain dryers. One of the reason preventing for this is that the cooling units, built into the drying shaft, do not create optimal conditions for full grain cooling and thereby reduce the effective volume of the drying shaft and moisture removal from a cubic meter of the camera.
Since the 2010 production of wheat demonstrates a stable growth trend: crop area has increased by 17%, yield has increased by 25%, and total yield - by 52%. In the 1th January in 2012 Kazakhstan had 258 silos with a storage capacity 14 771.3 thousand tons and elevators with storage capacity 14 127.8 thousand tons. Increase of yield and gross harvest requires improving drying technology to avoid crop losses and maintain grain quality.
The most perspective method for grain drying and removing moisture is the
induction heating method which remains little studied and rarely used in practice due to considerable imperfections in technologies of frequency convertors manufacturing. Though the
induction heating equipment production is currently developing and use of it grain drying practice becomes more preferable compared to traditional heating methods (Zhidko, 1982).
At present time induction heating is used for surface hardening of steel products, through heating for plastic deformation (forging, stamping, pressing, etc.), metal melting, heat treatment (annealing, tempering, normalizing, quenching), welding, welding, soldering, metals. Indirect induction heating is used for heating of technological equipment (pipelines, tanks, etc.), heating of liquids, drying of coats and materials (e.g., wood). The most important parameter of induction heating installations is frequency. For each process (surface hardening, through heating) there is an optimal frequency range, providing the best technological and economic performance. Frequencies from 50Hz to 5 MHz are used for induction heating.
Advantages of induction heating include the following:
- Transmission of electrical energy directly into the heating body allows implementing direct heating of materials, thereby the heating rate is
- Transmission of electrical energy directly into the heating body does not require contact devices. This is useful for automated line
- When a heating material is a dielectric, e.g. grain, then the power is evenly distributed throughout volume of the heating material. Consequently, this induction method provides fast heating of
- Induction heating in most cases can increase productivity and improve working conditions. Induction device can be regarded as a kind of transformer, when the primary winding (inductor) is connected to the AC power source, and the heating material serves as the secondary

Reduction of cost of the entire installation requires development and implementation of simple in design induction heaters.
The main difference between induction heating from traditional methods of drying lies in volumetric heating. The heat penetrates into the product (material) not from the surface; it is formed in the whole volume at once, this process allows drying grain effectively with low energy consumption. Even distribution of moisture occurs in a dried material during the heating induction process. Induction does not assume heat transfer from heater to a material. While using other methods of drying requires heating the air, then transfer the heat from the hot air to material. At each stage - air heating, its transportation, and heat transfer to products - the heat losses are unavoidable.
Nowadays enterprises in Kazakhstan practically do not use induction heaters as they are very expensive. Old lamp models of
induction heating machines are outdated and they are not manufactured.
Grain drying by induction heating. Drying in the falling layer
We suggest the induction heating method of grain drying (Figure 1) where the grain material passes, driven by gravity power, through the drying shaft. At the top of the dryer grain is loaded by bucket conveyors or other transport devices; then grain gets into drying tower. In the camera of drying tower the inductor, connected to frequency converter, creates electromagnetic field (flux) of high frequency.
Drying in falling layer. Falling layer represents highly discharged gravitational moving grain stream, partially offset by upward flow of gas (aerodynamic braking). The true concentration of grain increases in the course of the movement.
Drying in suspended layer. The suspended state of grain is achieved in the raising stream of gas when increasing speed of power supply. In the process the whole surface of grain is involved to heat and moisture exchange with the gas. The time of stay of grain in the pneumo tube does not exceed few seconds; temperature of drying agent makes 350-400 °C. However, the reduction of moisture amounts to a fraction percent. Therefore, the apparatus with weighted layers of grain are used not as separate dryer, but as an element of multi-chamber combined dryer.
Conclusion
Today agricultural firms and elevators are equipped mostly by the direct flow shaft dryers. These dryers suggest considerable unevenness in heating and drying of grain, which in turn causes substantial thermal drying costs. The main reason here is the imperfection in supplying the drying agent and atmospheric air to dehydrating layers of grain.
An important condition for quality work of grain dryers is an efficient cooling of dried grain. According to plan the cooling devices of grain dryers are designed so that the temperature of the grain at the output should not exceed the atmospheric air temperature by more than 10°C. However, in practice this value reaches more than 12°C when the air temperature is higher than 15°C. Also modern grain dryers provide considerable unevenness in cooling of the individual layers of grain. In the discussed context applying of induction heating drying can be the more suitable way in terms of productivity, quality and cost efficiency.
References
Baum, A., 1983. Grain drying [in Russian], Moscow: Kolos
Ginzburg, A., 1973. Essentials of theory and technology in drying of foodstuffs [in Russian], Moscow: Food industry
Zhidko, V., 1982. Grain drying and grain dryers [in Russian], Moscow: Kolos