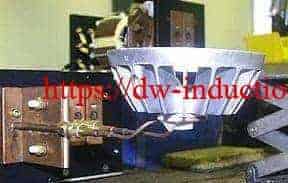
2022年9月30日星期五
Induction Soldering Aluminum Housing
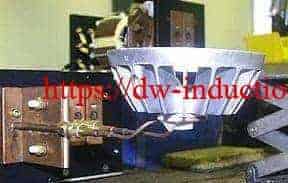
Aluminum Tubes Induction Brazing
The advantages of induction brazing of aluminum vs. torch or flame brazing
The low melting temperature of aluminum base metals coupled with the narrow temperature process window of the braze alloys used is a challenge when torch brazing. The lack of color change while heating aluminum does not provide braze operators any visual indication that the aluminum has reached the proper brazing temperature. Braze operators introduce a number of variables when torch brazing. Among these include torch settings and flame type; distance from torch to parts being brazed; location of flame relative to parts being joined; and more. Reasons to consider using induction heating when brazing aluminum include:- Quick, rapid heating
- Controlled, precise heat control
- Selective (localized) heat
- Production line adaptability and integration
- Improved fixture life and simplicity
- Repeatable, reliable brazed joints
- Improved safety
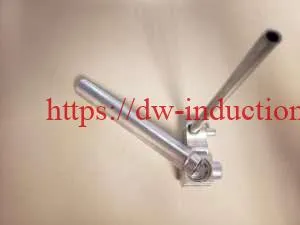
Why induction braze vs. torch braze aluminum components?
First, a little background on common aluminum alloys prevalent today and the common aluminum braze and solders used for joining. Brazing aluminum components is much more challenging than brazing copper components. Copper melts at 1980°F (1083°C) and it changes color as it is heated. Aluminum alloys often used in HVAC systems start to melt at approximately 1190°F (643°C) and do not provide any visual cues, such as color changes, as it heats.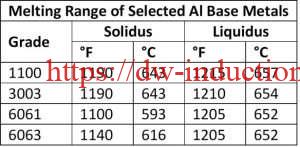
AWS A5.8 Classification | Nominal Chemical Composition | Solidus °F (°C) | Liquidus °F(°C) | Brazing Temperature |
BAISi-3 | 86% Al 10%Si 4%Cu | 970 (521) | 1085 (855) | 1085~1120 °F |
BAISI-4 | 88% aL 12%Si | 1070 (577) | 1080 (582) | 1080~1120 °F |
78 Zn 22%Al | 826 (441) | 905(471) | 905~950 °F | |
98% Zn 2%Al | 715(379) | 725(385) | 725~765 °F |
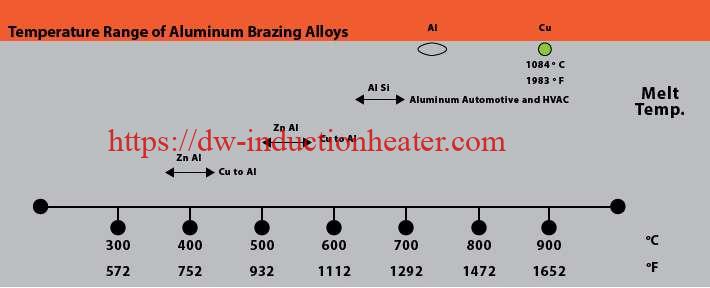
Induction Brazing Principle-Theory
Induction Brazing Technology
Induction Brazing Principle|Theory Brazing and soldering are processes of joining similar or dissimilar materials using a compatible a filler material. Filler metals include lead, tin, copper, silver, nickel and their alloys. Only the alloy melts and solidifies during these processes to join the work piece base materials. The filler metal is pulled into the joint by capillary action. Soldering processes are conducted below 840°F (450°C) while brazing applications are conducted at temperatures above 840°F (450°C) up to 2100°F (1150°C).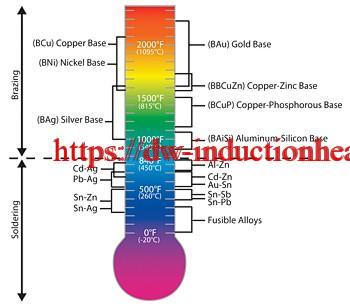

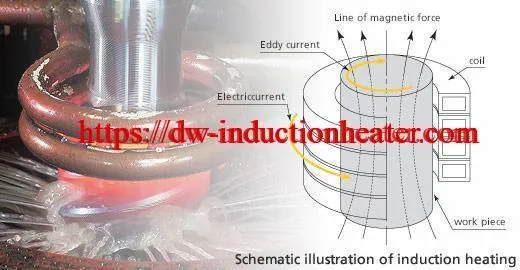
Induction Handheld Brazing Copper To Steel Tube
Induction Handheld Brazing Copper To Steel Tube
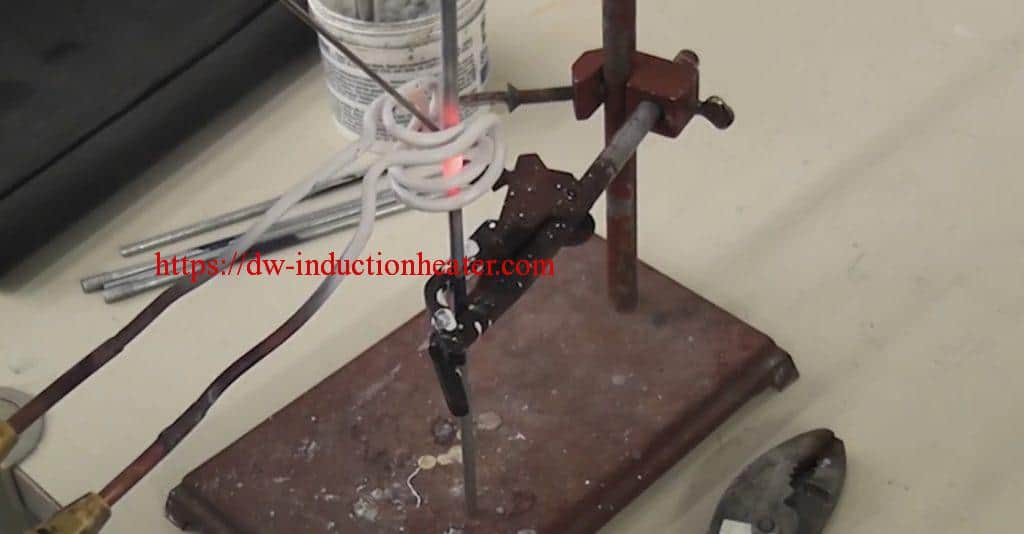
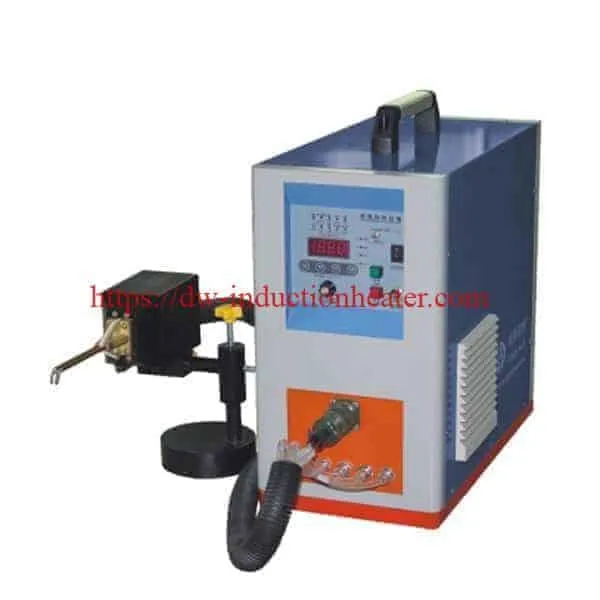
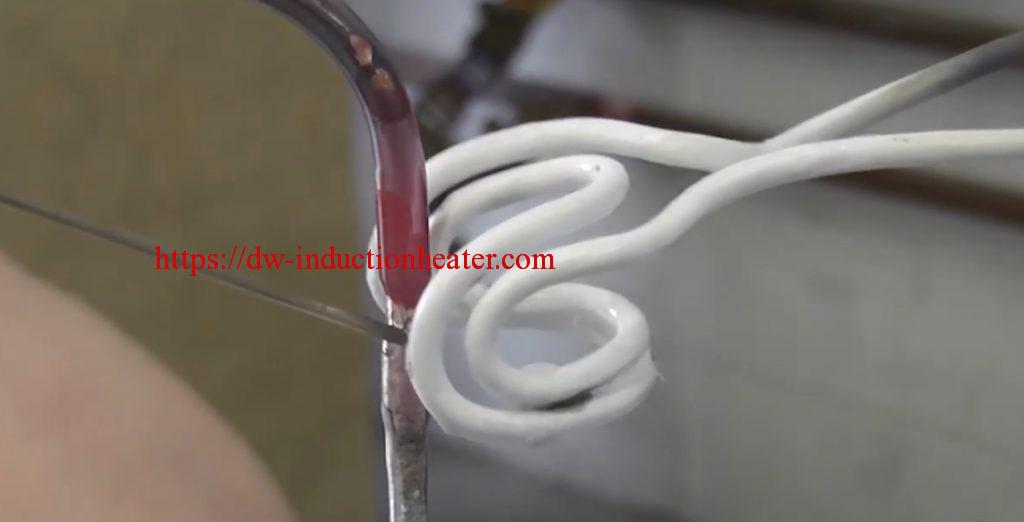

Induction Heating Solutions For Cancer Research
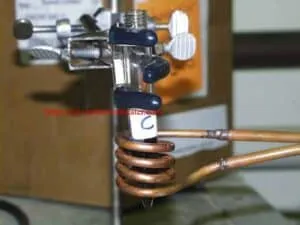

Induction Bending Pipe-Tube
Induction bending pipe
What is Induction Bending?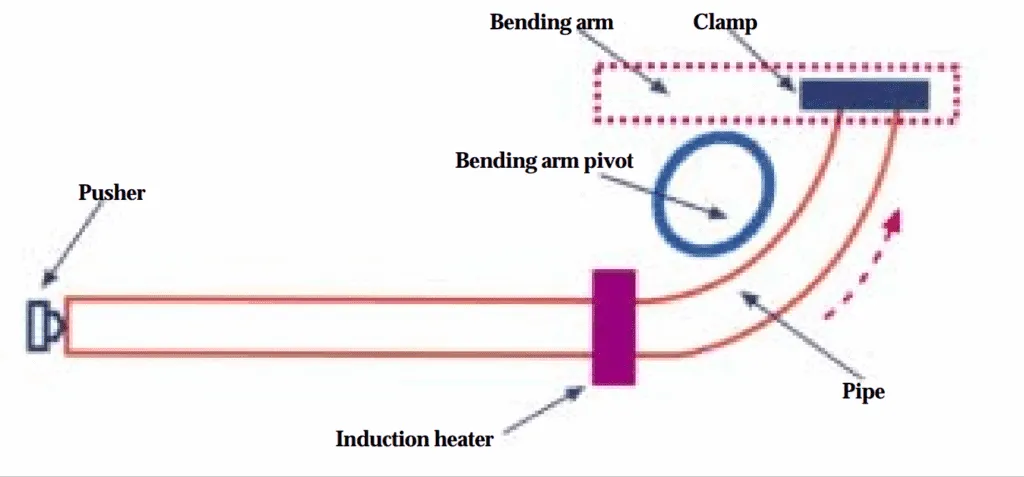

Benefits of Induction Bending:
- Large radii for smooth flow of fluid.
- Cost efficiency, straight material is less costly than standard components (e.g. elbows) and bends can be produced faster than standard components can be welded.
- Elbows can be replaced by larger radius bends where applicable and subsequently friction, wear and pump energy can be reduced.
- Induction bending reduces the number of welds in a system. It removes welds at the critical points (the tangents) and improves the ability to absorb pressure and stress.
- Induction bends are stronger than elbows with uniform wall thickness.
- Less non-destructive testing of welds, such as X-ray examination will save cost.
- Stock of elbows and standard bends can be greatly reduced.
- Faster access to base materials. Straight pipes are more readily available than elbows or standard components and bends can almost always be produced cheaper and faster.
- A limited amount of tools is needed (no use of thorns or mandrels as required in cold bending).
- Induction bending is a clean process. No lubrication is needed for the process and water needed for the cooling is recycled.

ADVANTAGES OF USING INDUCTION BENDING
- Infinitely variable bend radius, offering optimum design flexibility.
- Superior quality in terms of ovality, wall thinning and surface finish.
- Avoids the need for components with an elbow, allowing cheaper, more readily available straight materials to be utilised.
- A stronger end product than elbows with a uniform wall thickness.
- Large radius bend capability reduces friction and wear.
- Surface quality of bent material is not relevant in terms of suitability for use.
- Quicker production times than the welding of separate components.
- No cutting, rounding-up, match boring, fitting or heat treating/welding of forged fittings.
- Pipe and other sections can be curved to smaller radii than with cold bending techniques.
- Material surface unaffected/unblemished by the process.
- Multiple bends possible on a single length of pipe.
- Reduced welding requirement with compound bends, improving finished pipework integrity.
- Welds avoided at critical points.
- Less need for non-destructive testing, driving costs further down.
- Faster and more energy efficient than traditional fire/hot slab bending methods.
- Process eliminates the need for sand filling, mandrels or formers.
- A clean, lubricant-free process.
- Bend specification changes are possible right up to the last minute before production.
- Reduced need for formal on-site inspection of welded joint integrity.
- Faster repair and maintenance lead times, due to relative ease of producing replacement induction-bent pipes or tubes.
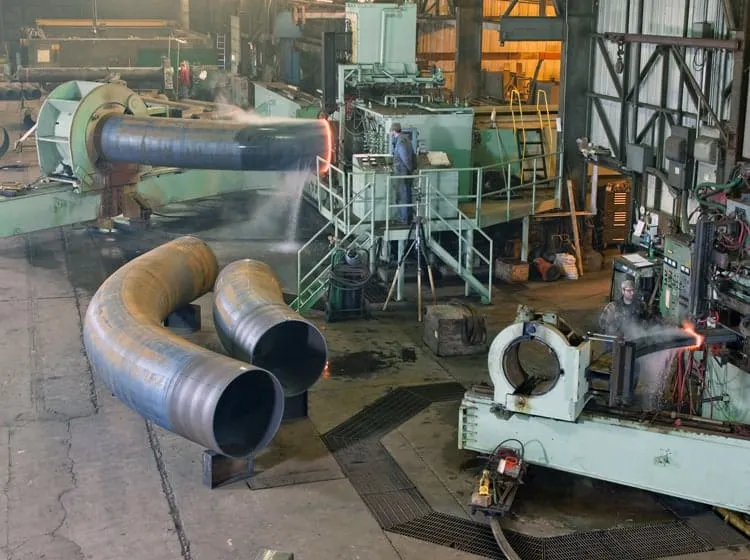
2022年9月29日星期四
Induction Brazing Machine
Series |
Model |
Input power Max |
Input current Max |
Oscillate frequency |
Input Voltage |
Duty cycle |
|
M
.
F
. |
DW-MF-15 Induction Generator |
15KW |
23A |
1K-20KHZ
According to the application |
3*380V
380V±20% |
100% |
|
DW-MF-25 Induction Generator |
25KW |
36A |
|||||
DW-MF-35Induction Generator |
35KW |
51A |
|||||
DW-MF-45 Induction Generator |
45KW |
68A |
|||||
DW-MF-70 Induction Generator |
70KW |
105A |
|||||
DW-MF-90 Induction Generator |
90KW |
135A |
|||||
DW-MF-110 Induction Generator |
110KW |
170A |
|||||
DW-MF-160 Induction Generator |
160KW |
240A |
|||||
DW-MF-45 Induction Heating Rod Forging Furnace |
45KW |
68A |
1K-20KHZ |
3*380V
380V±20% |
100% |
||
DW-MF-70 Induction Heating Rod Forging Furnace |
70KW |
105A |
|||||
DW-MF-90 Induction Heating Rod Forging Furnace |
90KW |
135A |
|||||
DW-MF-110 Induction Heating Rod Forging Furnace |
110KW |
170A |
|||||
DW-MF-160 Induction Heating Rod Forging Furnace |
160KW |
240A |
|||||
DW-MF-15 Induction Melting Furnace |
15KW |
23A |
1K-20KHZ |
3*380V
380V±20% |
100% |
||
DW-MF-25 Induction Melting Furnace |
25KW |
36A |
|||||
DW-MF-35 Induction Melting Furnace |
35KW |
51A |
|||||
DW-MF-45 Induction Melting Furnace |
45KW |
68A |
|||||
DW-MF-70 Induction Melting Furnace |
70KW |
105A |
|||||
DW-MF-90 Induction Melting Furnace |
90KW |
135A |
|||||
DW-MF-110 Induction Melting Furnace |
110KW |
170A |
|||||
DW-MF-160 Induction Melting Furnace |
160KW |
240A |
|||||
DW-MF-110 Induction Hardening Equipment |
110KW |
170A |
1K-8KHZ |
3*380V
380V±20% |
100% |
||
DW-MF-160Induction Hardening Equipment |
160KW |
240A |
|||||
H
.
F
. |
DW-HF-04 Series |
DW-HF-4KW-A |
4KVA |
15A |
100-250KHZ |
Single phase 220V |
80% |
DW-HF-15 Series |
DW-HF-15KW-A
DW-HF-15KW-B |
15KVA |
32A |
30-100KHZ |
Single phase 220V |
80% |
|
DW-HF-25 Series |
DW-HF-25KW-A
DW-HF-25KW-B |
25KVA |
23A |
20-80KHZ |
3*380V
380V±10% |
100% |
|
DW-HF-35 Series |
DW-HF-35KW-B |
35KVA |
51A |
||||
DW-HF-45 Series |
DW-HF-45KW-B |
45KVA |
68A |
||||
DW-HF-60 Series |
DW-HF-60KW-B |
60KVA |
105A |
||||
DW-HF-80 Series |
DW-HF-80KW-B |
80KVA |
130A |
||||
DW-HF-90 Series |
DW-HF-90KW-B |
90KVA |
160A |
||||
DW-HF-120 Series |
DW-HF-120KW-B |
120KVA |
200A |
||||
U
.
H
.
F
.
|
DW-UHF-3.2KW |
3.2KW |
13A |
1.1-2.0MHZ |
Single phase220V
±10% |
100% |
|
DW-UHF-4.5KW |
4.5KW |
20A |
|||||
DW-UHF-045T |
4.5KW |
20A |
|||||
DW-UHF-045L |
4.5KW |
20A |
|||||
DW-UHF-6.0KW |
6.0KW |
28A |
|||||
DW-UHF-06A |
6.0KW |
28A |
|||||
DW-UHF-6KW-B |
6.0KW |
28A |
|||||
DW-UHF-10KW |
10KW |
15A |
100-500KHZ |
3*380V
380V±10% |
100% |
||
DW-UHF-20KW |
20KW |
30A |
50-250KHZ |
||||
DW-UHF-30KW |
30KW |
45A |
50-200KHZ |
||||
DW-UHF-40KW |
40KW |
60A |
50-200KHZ |
||||
DW-UHF-60KW |
60KW |
90A |
50-150KHZ |
induction Brazing copper rods to brass strips

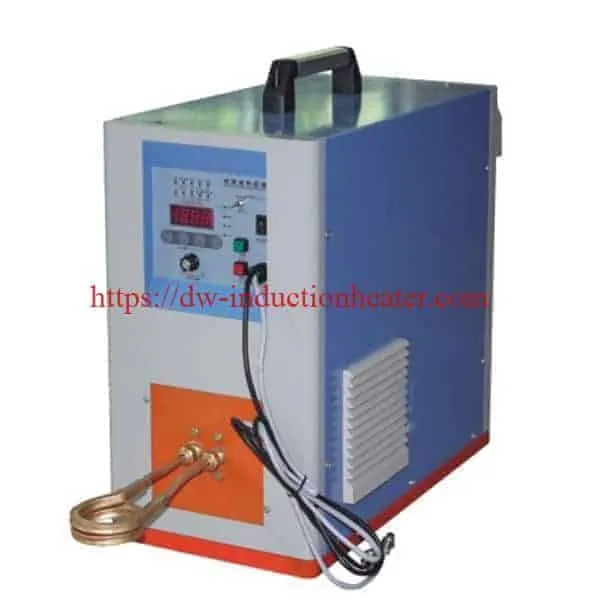
- induction brazing Strong durable joints
- Selective and precise heat zone, resulting in less part distortion and joint stress than welding
- Less oxidation
- Faster heating cycles
- More consistent results and suitability for large volume production, without the need for batch processing
- Safer than flame brazing
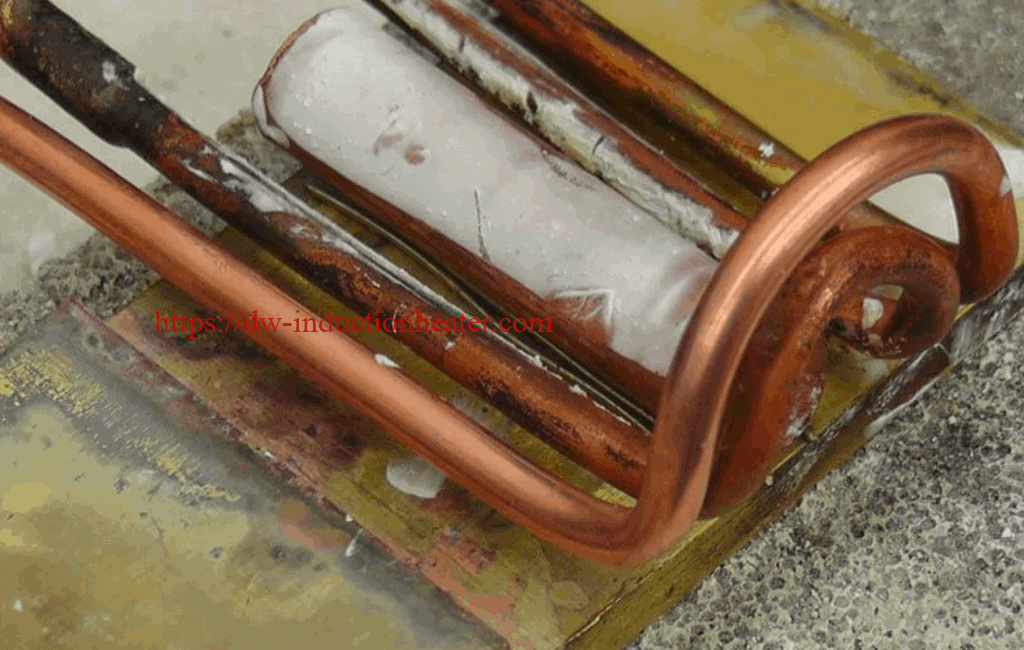
Handheld Induction Brazing HVAC Pipes of Heat Exchangers
Fast Handheld Induction Brazing HVAC Pipes System of Heat Exchangers

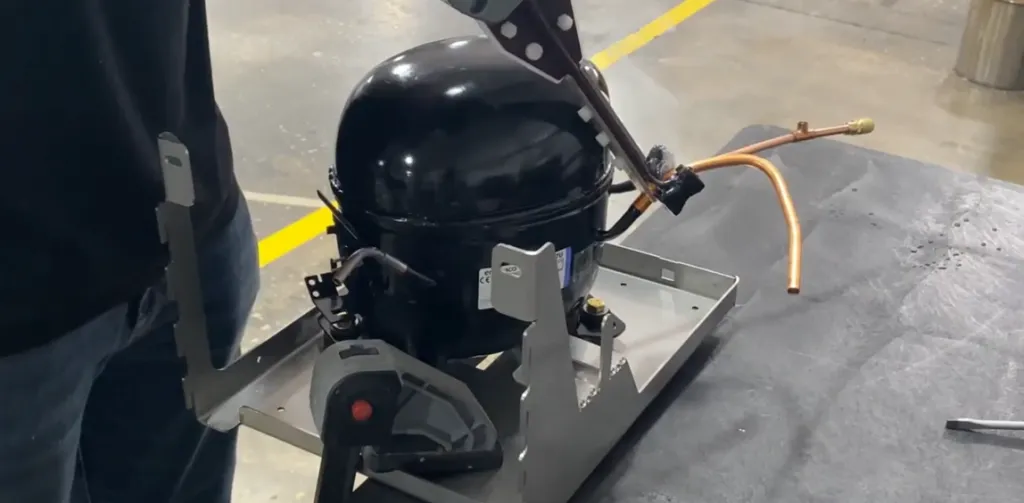
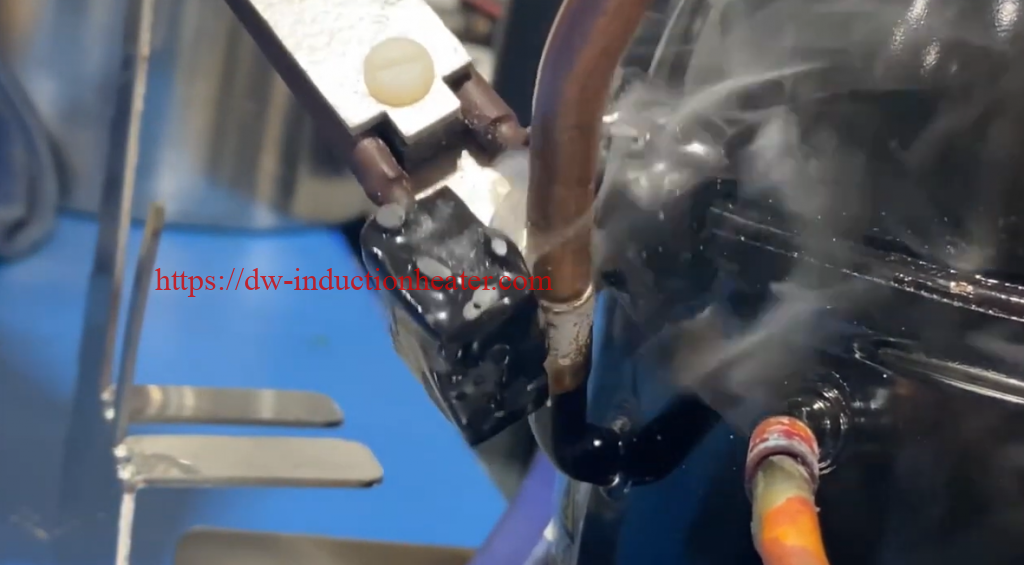
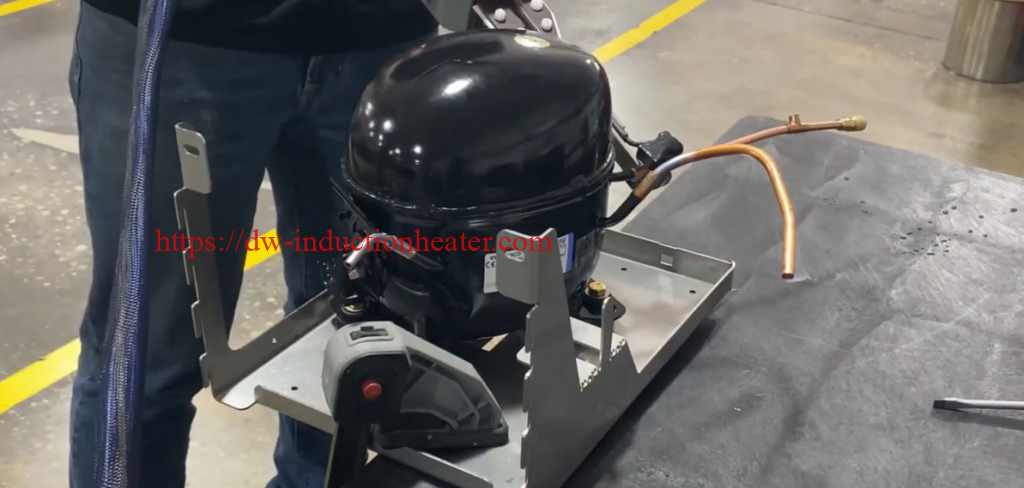
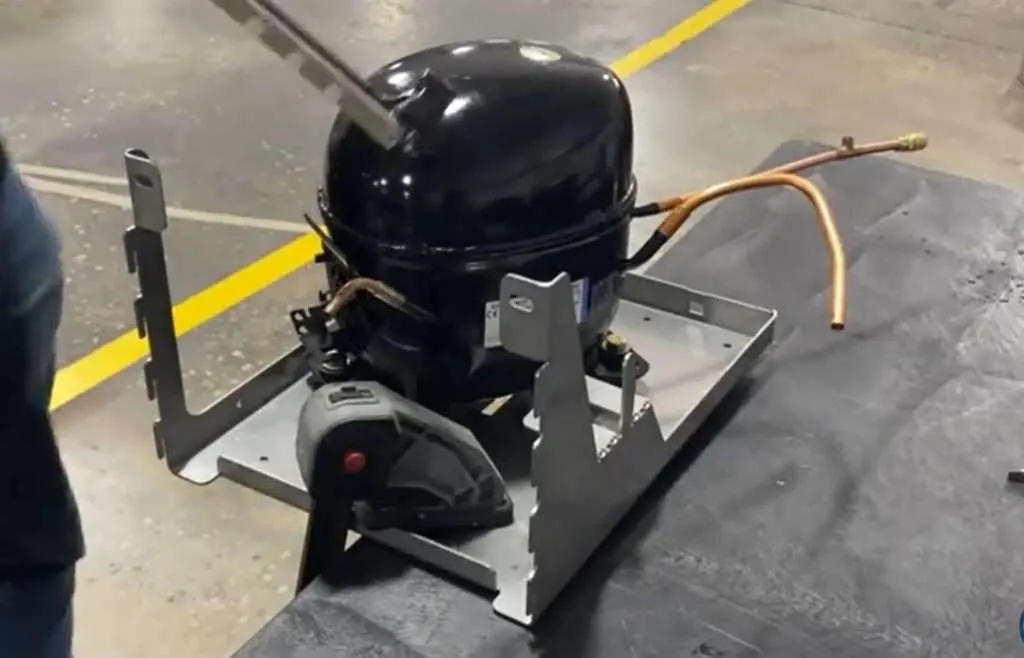
Induction Soldering Brass Rings
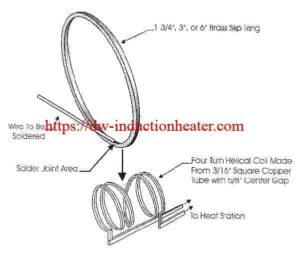
induction brazing steel tube to copper tube
High Frequency Induction Brazing Steel Tube to Copper Tube
Objective The goal is to braze a steel tube to a copper tube in 60 seconds using flux and brazing alloy.- The assembly section was pre-assembled and fluxed (B-1) then located in the two diameter coil with a single pre-formed alloy ring set at the interface area.
- Alloy flow and joint completed in 60 seconds.
- The material was cooled in water following the completion of induction brazing.
- The joint was then cross-sectioned to validate that the brazing process had produced a strong, high quality joint.
- Strong durable joints with induction heating
- Selective and precise heat zone, resulting in less part distortion and joint stress than welding
- Less oxidation
- Faster heating cycles
- More consistent results and suitability for large volume production, without the need for batch processing
- Safer than flame brazing
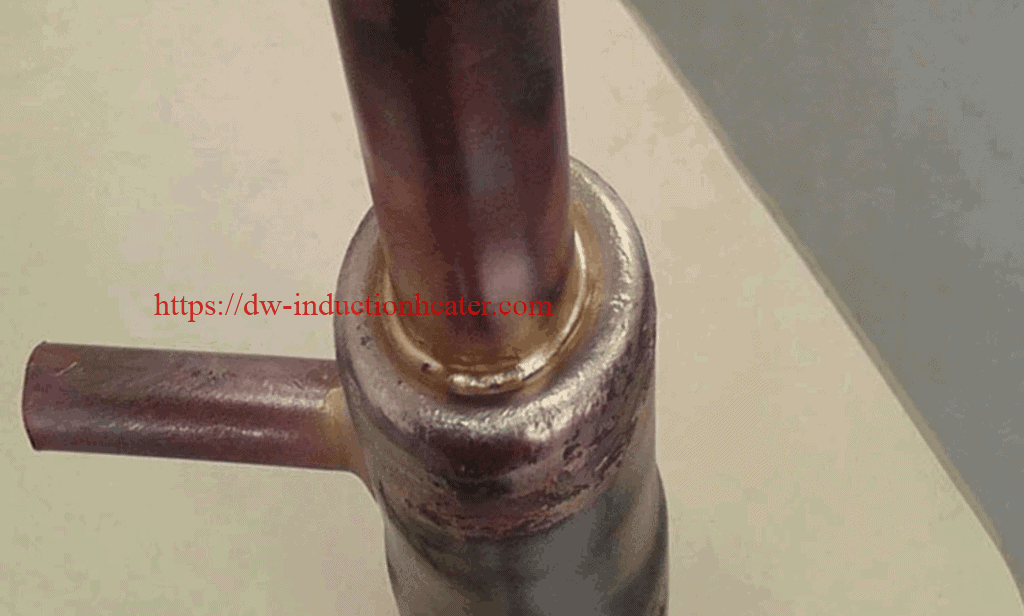
Ultrasonic Plastic Welding Machine For Bonding Thermoplastic Parts
Ultrasonic plastic welding machine | ultrasonic thermoplastic welder | ultra sonic plastic welding equipment with Automatic Frequency Chasing
Ultrasonic plastic welding is an industrial technique whereby high-frequency ultrasonic acoustic vibrations are locally applied to workpieces being held together under pressure to create a solid-state weld. It is commonly used for plastics and metals, and especially for joining dissimilar materials. In ultrasonic welding, there are no connective bolts, nails, soldering materials, or adhesives necessary to bind the materials together. When applied to metals, a notable characteristic of this method is that the temperature stays well below the melting point of the involved materials thus preventing any unwanted properties which may arise from high temperature exposure of the materials.
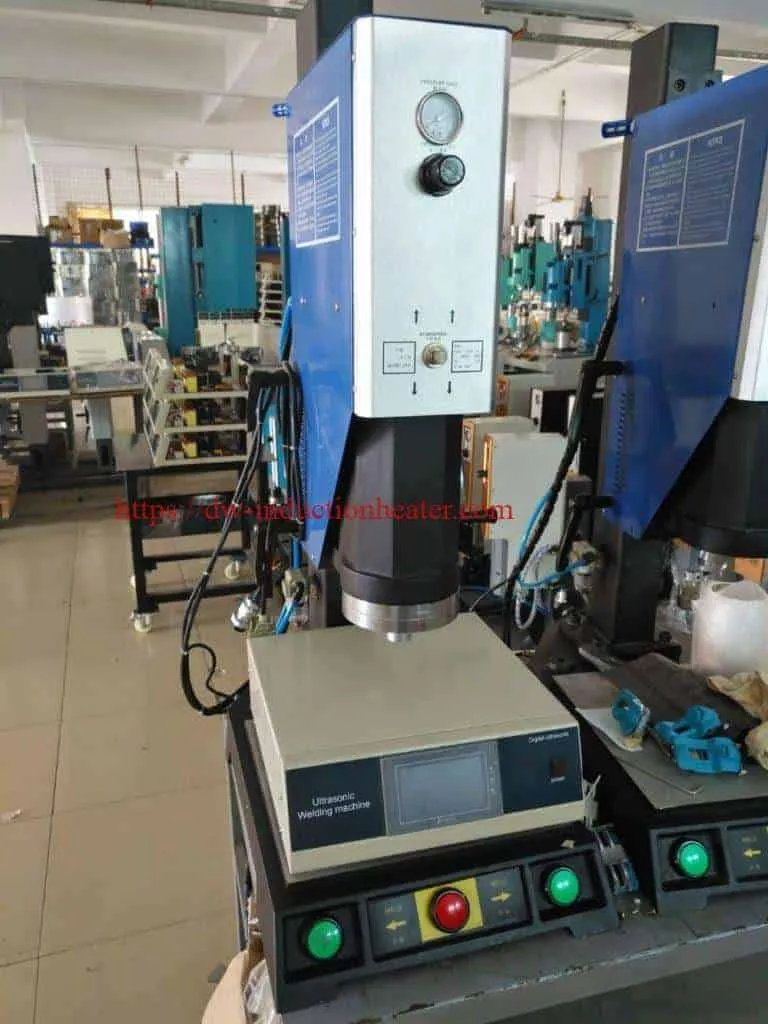
Model | 1520A | 1526A | 1532A | 1542A |
Frequency | 15KHz | |||
Power | 2000W | 2600W | 3200W | 4200W |
Voltage | 220V | |||
Capacity | 10-20 times/min | |||
Driving form | Pneumatic | |||
Stroke Length(Horn Journy) | 75mm | 100mm | ||
Output Time | 0.01-9.99S Adjustable | |||
Welding Area | Φ100 | Φ200 | Φ300 | Φ400 |
Electricity | AC | |||
Control mode | Numerical control | |||
Working air pressure | 1-7 Bar | |||
Weight | 90KG | 90KG | 90KG | 120KG |
Dimensions | 450*750*1100mm | 760*1000*1950mm |
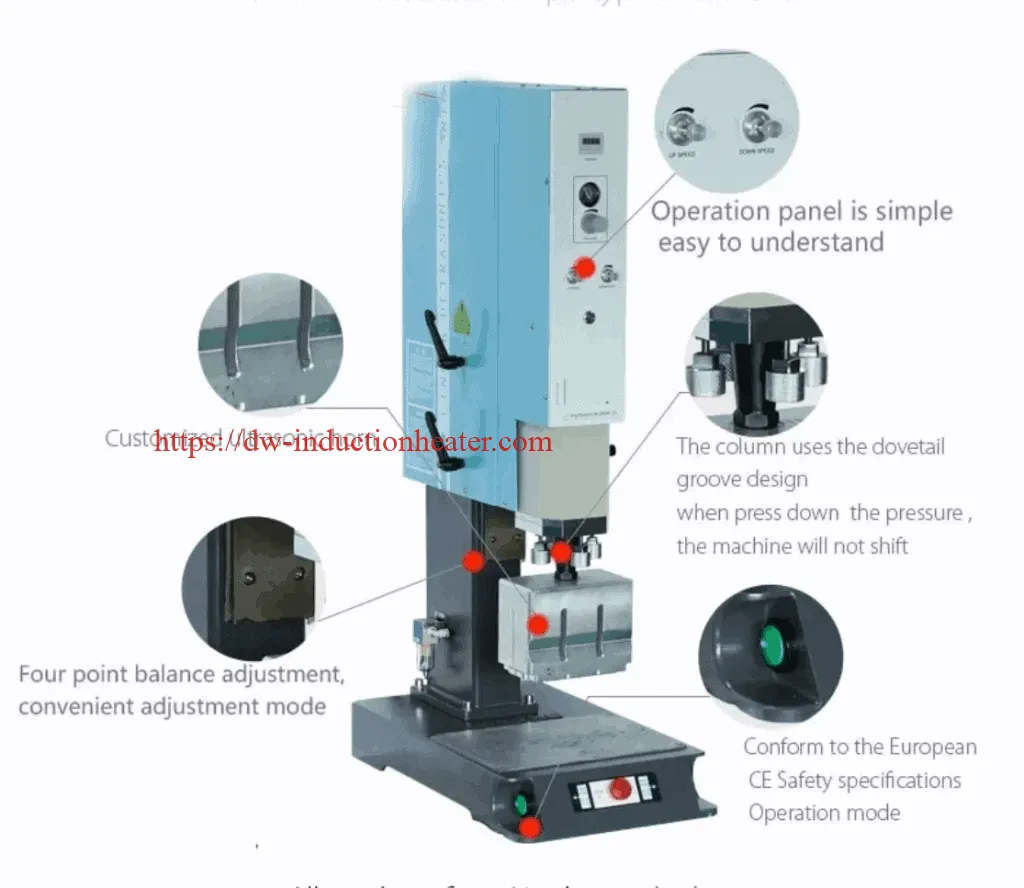
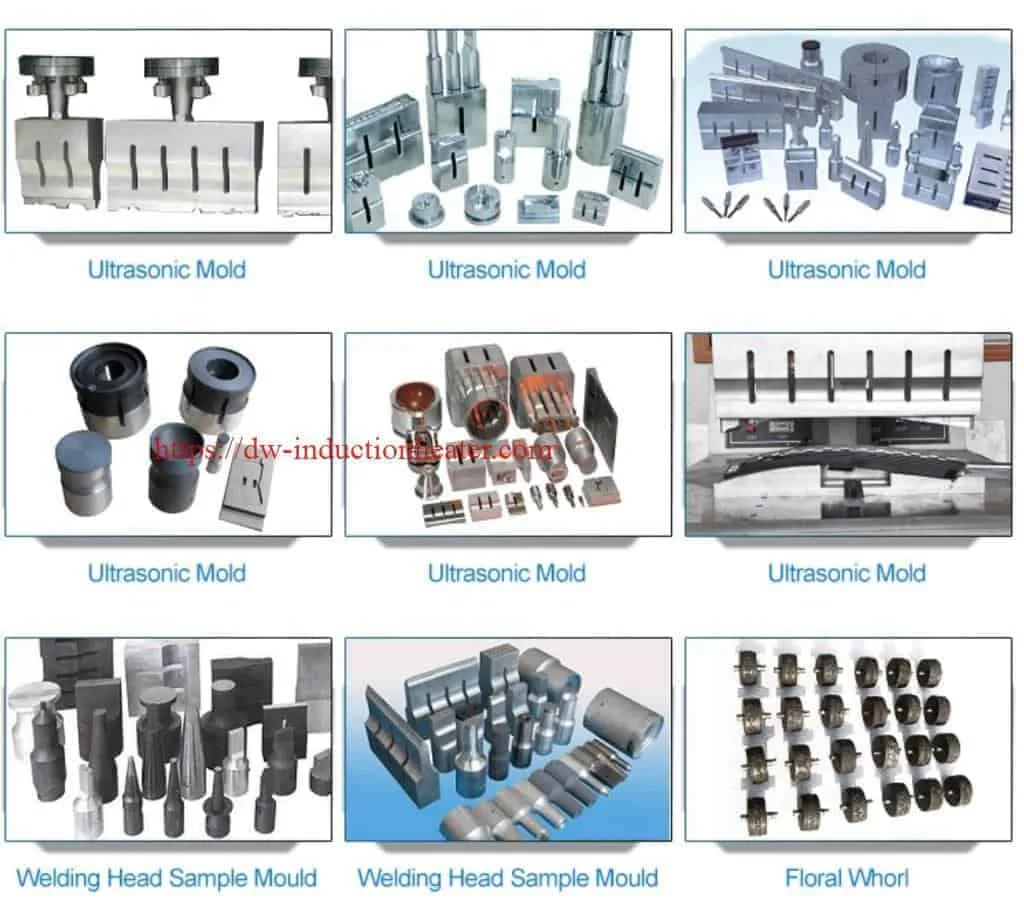
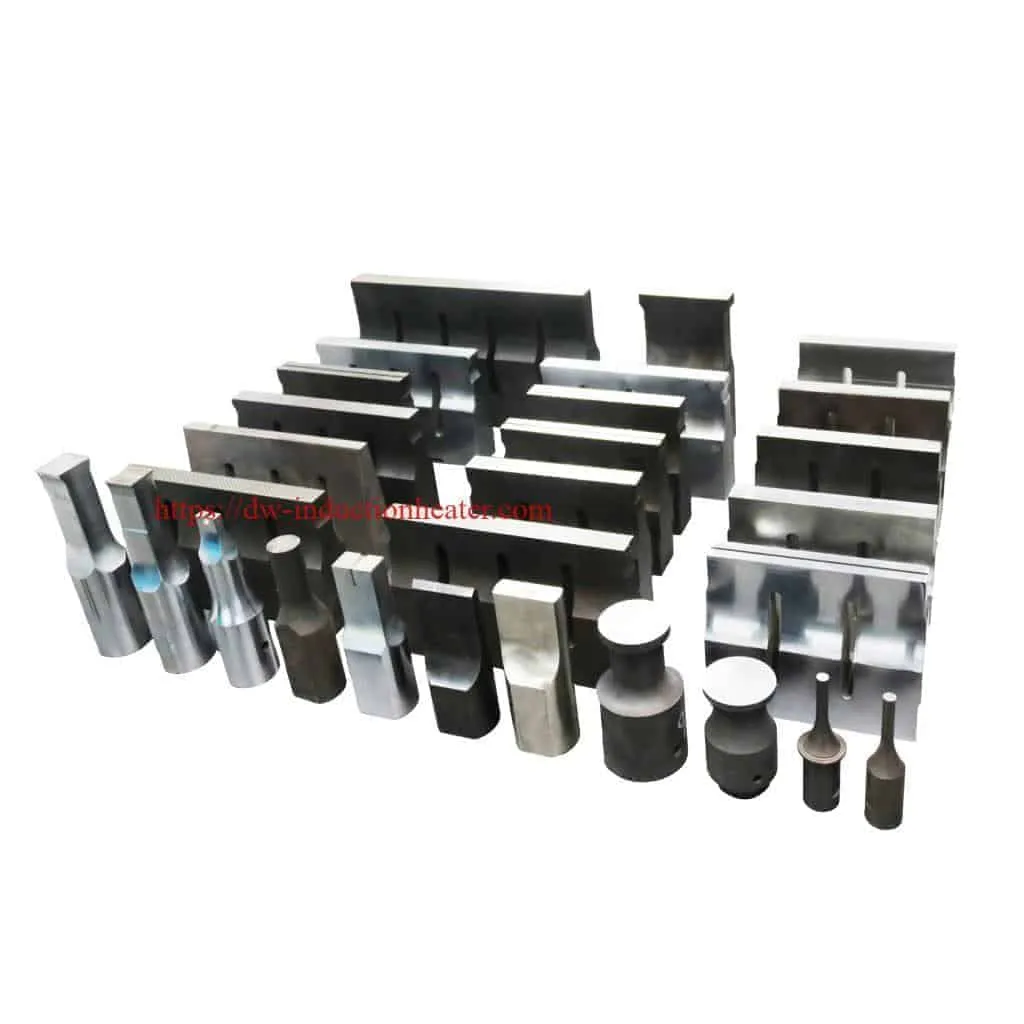
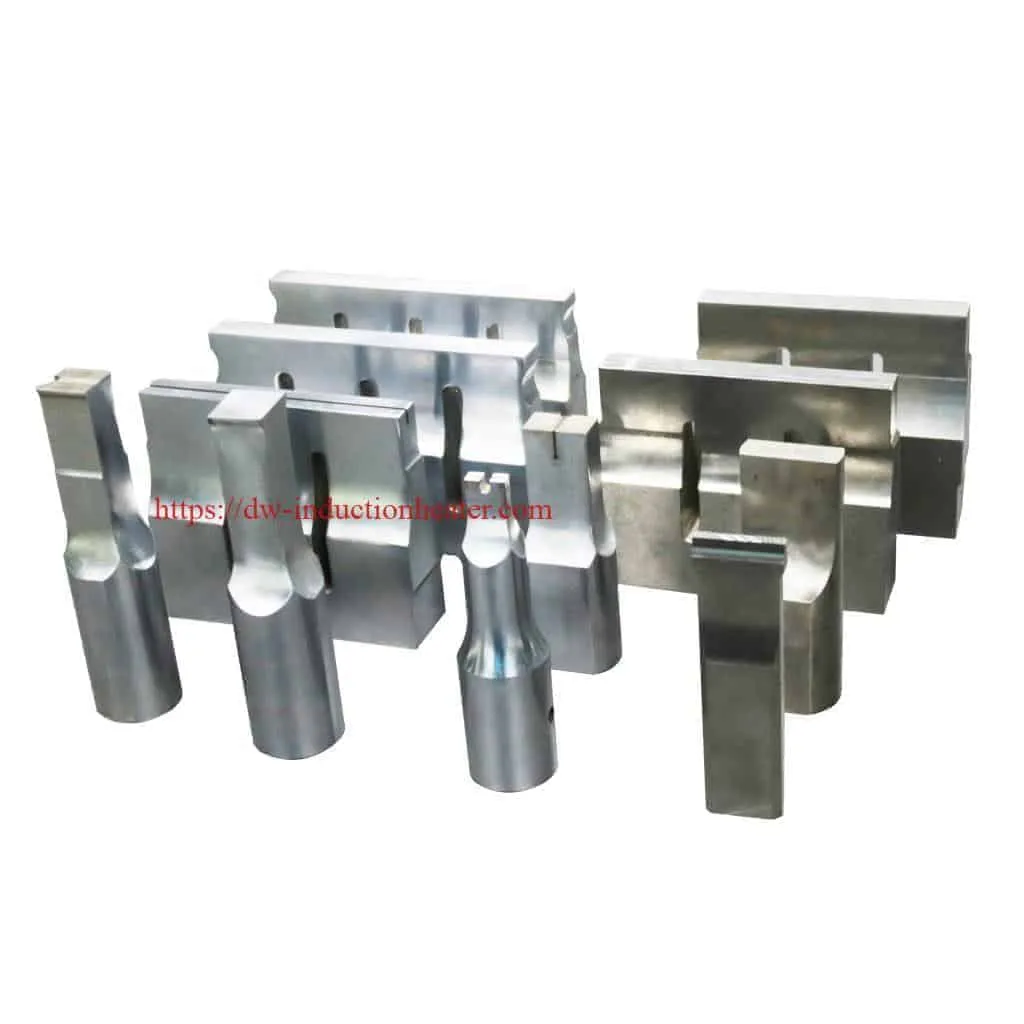
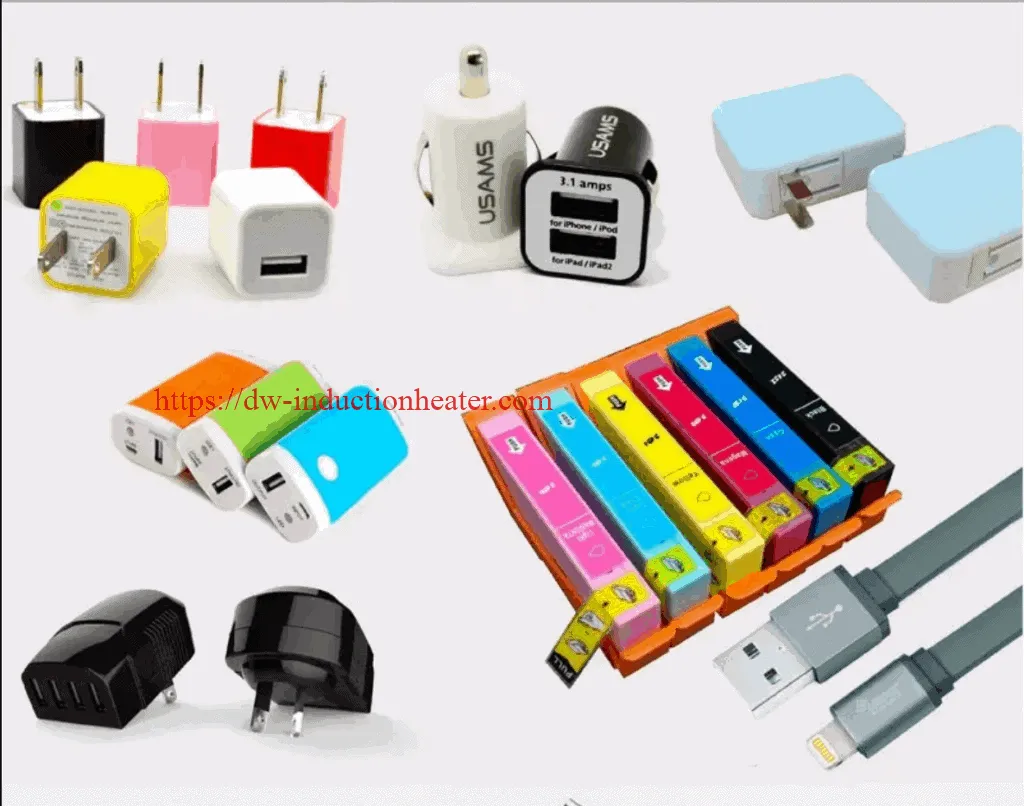

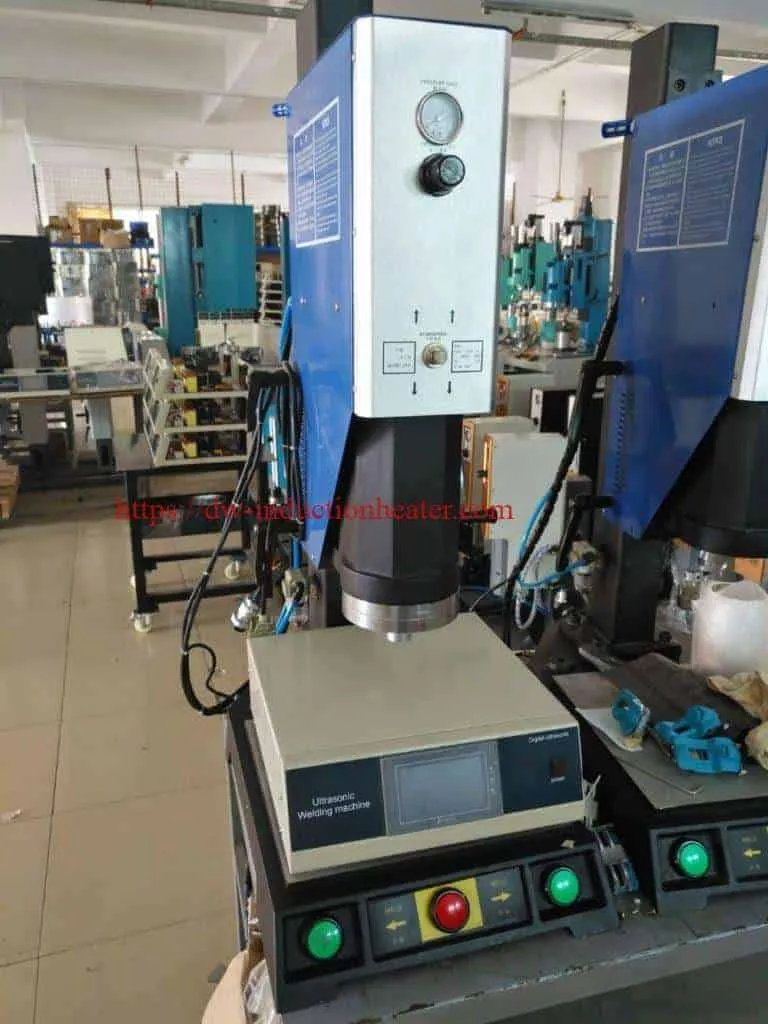
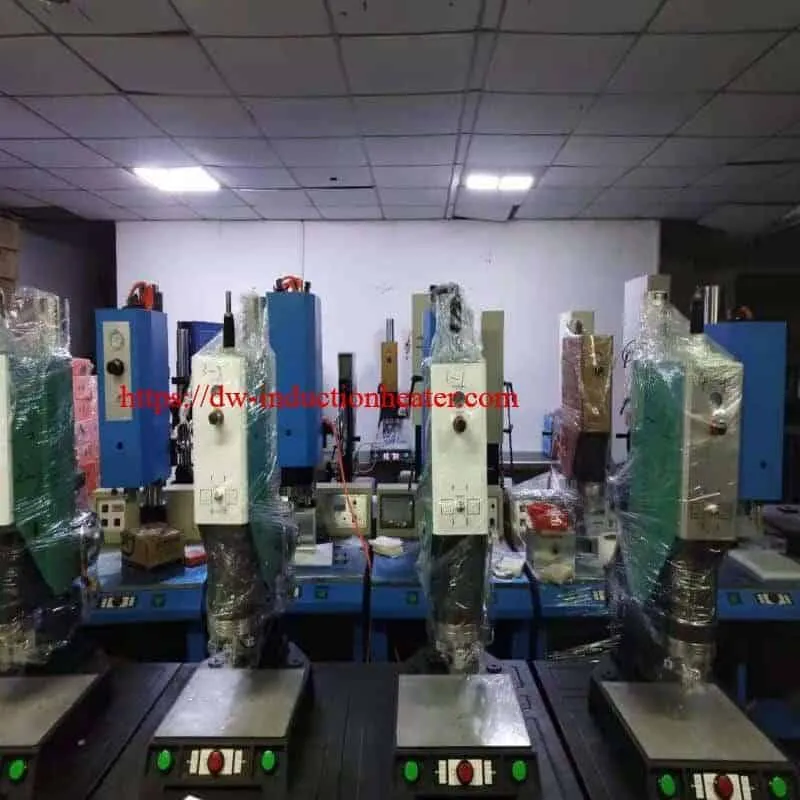

2022年9月28日星期三
Induction Brazing & Soldering Principle
Induction Soldering Wire of Co-axial
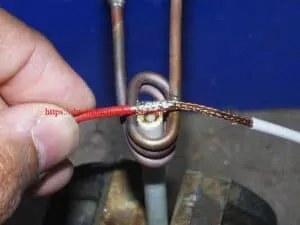
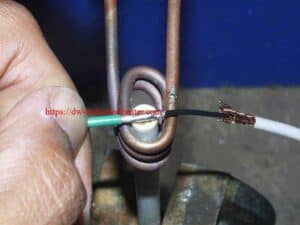
Induction Shrink Fit Aluminum Shaft
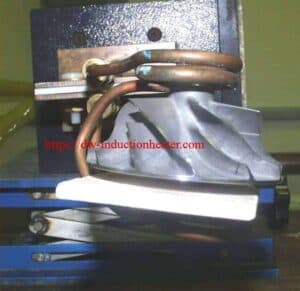
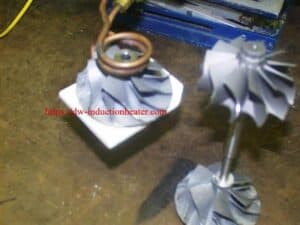
PDF of Induction Heating Principle and Applicatons
Induction Heating Principle and Applications PDF download for Research
Electromagnetic induction, simply induction, is a heating technique for electrical conductive materials (metals). Induction heating is frequently applied in several thermal processes such as the melting and the heating of metals. Induction heating has the important characteristic that the heat is generated in the material to be heated itself. Because of this, induction has a number of intrinsic trumps, such as a very quickheated itself. Because of this, induction has a number of intrinsic trumps, such as a very quick response and a good efficiency. Induction heating also allows heating very locally. Tare extremely high because of the high power density..... [caption id="attachment_5482" align="alignnone" width="1024"]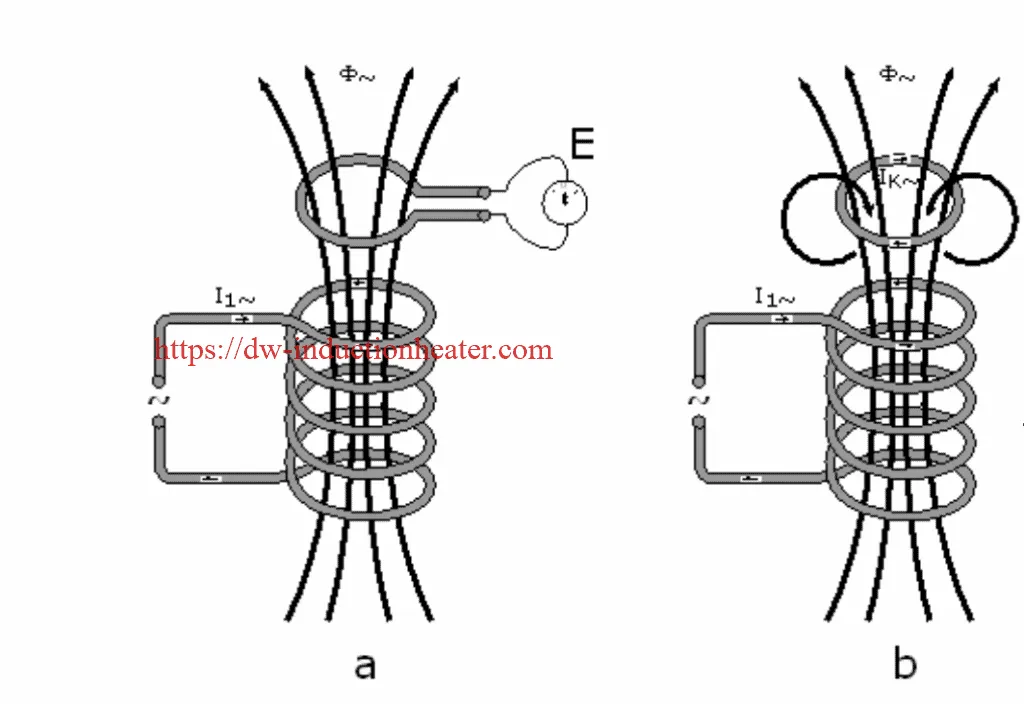
induction preheating copper rod for hot forging
Induction preheating copper rod for hot forging
In order to want to improve safety and productivity, and reduce energy costs, by using induction instead of resistive heating. To maximize productivity, they want to be able to heat 3 brass rods at a time to 780° C within 25 seconds. For this application test, we are only heating one rod, so our goal is to heat the single rod to 780° C within 25 seconds with less than 45 kW of power. This will ensure that when heating 3 rods, that the 110 kW system will meet the production requirements.
Equipment DW-HF-70kW Induction Heating Power Supply, operating between 10-50 kHz
Materials • Brass rod • Custom coil, 10 turns, D=50mm, designed and manufactured by DaWei Induction Power Technologies for this specific application – capable to heat 3 rods at a heat cycle.
Key Parameters Temperature: 780° C Power: 70 kW Voltage: 380 – 480 V Time: 24 sec Frequency: 32 kHz
Process:
- The DW-HF series Power Supply was connected to the DW-HF-70kw Heat Station.
- The custom Coil was attached to the Heat Station.
- The Brass rods were placed inside the Coil.
- The Power Supply was turned on.
- The DW-HF series operating at 20 kW was able to successfully heat the single brass rod within 24 seconds, which was less than the 25 second time requirement established for the test. Three brass rods are expected then to heat within 25 seconds with approximately 60 kW of power (3 rods will be 3x the load and 3x the power). The 90 kW Induction system will therefore meet the customer’s requirements.
Results/Benefits:
Induction preheating provides:
- Faster heating cycles
- The process is safer than the flame heating
- Technology without pollution, clean and safe
induction preheating copper rod
high frequency induction preheating copper rod and connector for an epoxy curing application
induction preheating copper rod and connector for an epoxy curing application Objective: To preheat a portion of the copper rod and a rectangular connector to temperature prior to epoxy curing during a manufacturing process for electrical turnbuckles Material : Customer supplied plated copper rod (12” x 2” x 1”/305mm x 51mm x 102 mm) and connector Temperature :302 ºF (150 ºC) Frequency :25 kHz Induction Heating Equipment: -DW-HF-60kW 15-45 kHz induction heating system equipped with a remote workhead containing four 21 μF capacitors
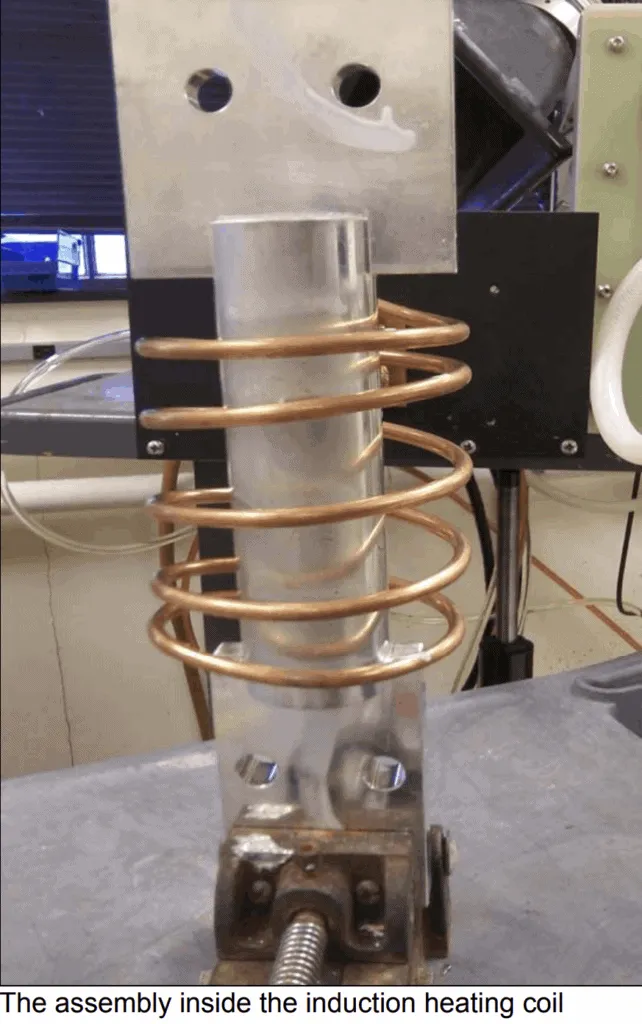
关注者
博客归档
-
▼
2022
(1729)
-
▼
九月
(177)
- Induction Soldering Aluminum Housing
- Aluminum Tubes Induction Brazing
- Induction Brazing Principle-Theory
- Induction Handheld Brazing Copper To Steel Tube
- Induction Heating Solutions For Cancer Research
- Induction Bending Pipe-Tube
- Induction Brazing Machine
- induction Brazing copper rods to brass strips
- Handheld Induction Brazing HVAC Pipes of Heat Exch...
- Induction Soldering Brass Rings
- induction brazing steel tube to copper tube
- Ultrasonic Plastic Welding Machine For Bonding The...
- Induction Brazing & Soldering Principle
- Induction Soldering Wire of Co-axial
- Induction Shrink Fit Aluminum Shaft
- PDF of Induction Heating Principle and Applicatons
- induction preheating copper rod for hot forging
- induction preheating copper rod
- PDF of Induction Heating Principle and Applicatons
- Induction Brazing Stainless Steel
- Induction forging and induction hot forming
- Brazing Brass To Copper With Induction
- Induction Fluid Pipeline heating system
- High Frequency Induction Brazing Copper Wire
- induction surface hardening steel screws
- High Speed Heating by Induction Heating System
- Induction Soldering Brass Heating Exchanger
- Induction Brazing Copper Tube For Refrigeration
- Induction Brazing Machine
- Induction Wire Heating Process Applications
- Induction Preheat Welding Systems
- induction preheating titanium billet for rolling
- Induction Hot Plate
- Induction Annealing Aluminum PIpe
- Induction Heating Solutions For Cancer Research
- Induction Melting Videos
- Induction Soldering Aluminum Housing
- RPR Induction Stripping-Induction Rust & Paint Coa...
- Induction Brazing Carbide To Steel
- Heating Aluminum Foil For Cap Sealing
- induction heating stainless steel wire cable
- Brazing Eyeglass Frames With Induction
- refrigeration induction brazing refrigerator coppe...
- High Frequency Induction Brazing Copper Wire
- Induction Heating Plasma
- Induction Heating Solutions For Cancer Research
- Induction Brazing Carbide To Stainless Steel
- Induction Soldering Wire To Aluminum Lug
- Induction annealing stainless steel wire
- Technology of Induction Forming Steel Plate
- Brazing Carbide Tool Tips With Induction
- Brazing Copper Tube to Brass Fitting With Induction
- Heating Aluminum Foil For Cap Sealing
- Annealing Saw Blades with Induction
- induction heating diffusion pump with electromagne...
- hot water boiler with induction heating
- Induction inline wire heating process
- portable ultrasonic mask welding machine for weldi...
- Induction Shrink Fit Aluminum Shaft
- Induction Preheating Hot Rod Heading
- Induction Brazing Carbide Onto Steel Part
- How to design induction heating coil
- RPR Induction Stripping-Induction Rust & Paint Coa...
- induction brazing steel tube to copper tube
- Induction Soldering Brass Rings
- induction hardening process
- Induction straightening deck and bulkhead heating ...
- Induction Shrink Fit Aluminum Shaft
- what is induction forging?
- Induction Soldering Cables to Terminals
- Applications and Advantages of Induction Heating S...
- Induction Brazing Steel Parts to Tungsten Carbide ...
- Induction Brazing Brass Studs to Copper Pipes
- What is induction bonding?
- induction preheating copper bars
- Induction Soldering Brass Rings
- What Is Induction Heating?
- Induction Curing Heating of Organic Coating
- induction soldering fiber optic cable
- Induction Heating Steel Part For Hot Heading
- Brazing Stainless Steel To Copper With Induction
- Inductioin Shrink Fitting Aluminum Pulley
- Induction Soldering Steel Cover
- How Induction Heating works?
- What is Induction Brazing?
- induction heating graphite susceptor
- Applications and Advantages of Induction Heating S...
- What Is Induction Heating?
- Handheld Brazing Stainless Steel Tube
- Induction Wire Heating Process Applications
- Induction stress relieving flat blanks
- Induction Heat Treating Surface Process
- Induction Soldering Stainless Steel To Wire
- Induction Soldering Circuit Board
- induction heating for drying food processing industry
- Brazing Carbide To Steel Shank
- Induction Heating Steel Mold
- induction brazing carbide tip onto steel head teeth
- induction curing
- Induction Brazing Heating Exchanger Copper Pipes
-
▼
九月
(177)
我的简介

- HLQ induction heating machine
- HLQ induction heating machine manufacturer provides the service of induction brazing,melting,hot forming,hardening surface,annealing,shrink fitting,PWHT,etc.