In order to increase the efficiency and to reduce the thermal effect of metal heating, the induction brazing technology is proposed. Advantage of this technology consists mainly in exact location of heating supplied to the brazed joints. Based on the results of numerical simulation it was then possible to design the parameters necessary to achieve brazing temperatures in the desired time. The aim was to minimize this time to avoid an undesired thermal effect on the metals during metallurgical joining.The results of numerical simulation revealed that increasing the current frequency resulted in concentration of maximum temperatures in surface areas of joined metals. With increasing current, the reduction of time required for reaching the brazing temperature was observed.
The advantages of induction brazing of aluminum vs. torch or flame brazing
The low melting temperature of aluminum base metals coupled with the narrow temperature process window of the braze alloys used is a challenge when torch brazing. The lack of color change while heating aluminum does not provide braze operators any visual indication that the aluminum has reached the proper brazing temperature. Braze operators introduce a number of variables when torch brazing. Among these include torch settings and flame type; distance from torch to parts being brazed; location of flame relative to parts being joined; and more.
Reasons to consider using
induction heating when brazing aluminum include:
- Quick, rapid heating
- Controlled, precise heat control
- Selective (localized) heat
- Production line adaptability and integration
- Improved fixture life and simplicity
- Repeatable, reliable brazed joints
- Improved safety
Successful induction brazing of aluminum components is highly dependent on designing
induction heating coils to focus the electromagnetic heat energy into the areas to be brazed and to heat them uniformly so that the braze alloy melts and flows properly. Improperly designed induction coils can result in some areas being overheated and other areas not receiving enough heat energy resulting in an incomplete braze joint.
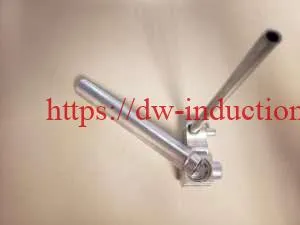
For a typical brazed aluminum tube joint, an operator installs an aluminum braze ring, often containing flux, on the aluminum tube and inserts this into another expanded tube or a block fitting. The parts are then placed into an induction coil and heated. In a normal process, the braze filler metals melt and flow into the joint interface due to capillary action.
Why induction braze vs. torch braze aluminum components?
First, a little background on common aluminum alloys prevalent today and the common aluminum braze and solders used for joining. Brazing aluminum components is much more challenging than brazing copper components. Copper melts at 1980°F (1083°C) and it changes color as it is heated. Aluminum alloys often used in HVAC systems start to melt at approximately 1190°F (643°C) and do not provide any visual cues, such as color changes, as it heats.
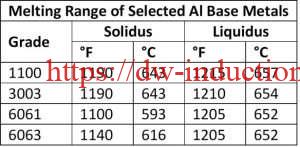
Very precise temperature control is required as the difference in the melting and brazing temperatures for aluminum, dependent upon the aluminum base metal, braze filler metal, and mass of the components to be brazed. For example, The temperature difference between solidus temperature of two common aluminum alloys, 3003 series aluminum, and 6061 series aluminum, and the liquid’s temperature of frequently used BAlSi-4 braze alloy is 20°F – a very narrow temperature process window, thus necessitating precise control. The selection of base alloys is extremely important with aluminum systems that are being brazed. The best practice is to braze at a temperature that is below the solidus temperature of the alloys the make up the components being brazed together.
AWS A5.8 Classification |
Nominal Chemical Composition |
Solidus °F (°C) |
Liquidus °F(°C) |
Brazing Temperature |
BAISi-3 |
86% Al 10%Si 4%Cu |
970 (521) |
1085 (855) |
1085~1120 °F |
BAISI-4 |
88% aL 12%Si |
1070 (577) |
1080 (582) |
1080~1120 °F |
|
78 Zn 22%Al |
826 (441) |
905(471) |
905~950 °F |
|
98% Zn 2%Al |
715(379) |
725(385) |
725~765 °F |
It should be noted that galvanic corrosion can occur between zinc-rich areas and aluminum. As noted in the galvanic chart in Figure 1, zinc is less noble and tends to be anodic compared to aluminum. The lower the potential difference, the lower the rate of corrosion. The potential difference between zinc and aluminum is minimal compared to the potential between aluminum and copper.
Another phenomenon when aluminum is brazed with a zinc alloy is pitting. Local cell or pitting corrosion can occur on any metal. Aluminum is normally protected by a hard, thin film that forms at the surface when they are exposed to oxygen (aluminum oxide) but when a flux removes this protective oxide layer, dissolution of the aluminum can occur. The longer the filler metal remains molten, the more severe the dissolution is.
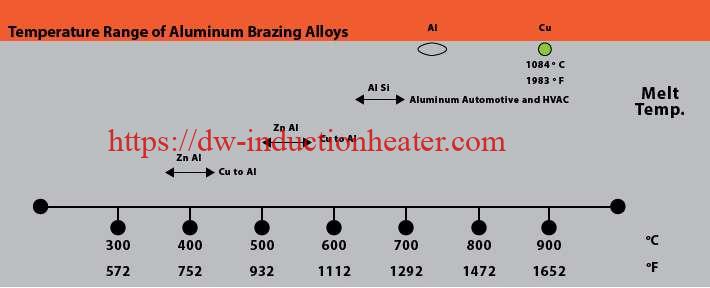
Aluminum forms a tough oxide layer during brazing, so the use of flux is essential. Fluxing aluminum components can be done separately prior to brazing or an aluminum brazing alloy containing flux can be incorporated into the brazing process. Depending upon the type of flux used (corrosive vs. non-corrosive), an additional step may be required if the flux residue must be removed after brazing. Consult with a braze and flux manufacturer to get recommendations on brazing alloy and flux based on the materials being joined and the expected brazing temperatures.
Aluminum Tubes Induction Brazing