Why Choose Induction Heating and what are its advantages
Why choose induction heating over convection, radiant, open flame or another heating method? Here's a short summary of the major advantages that modern solid state induction heating offers for lean manufacturing:
Optimized Consistency
Induction heating eliminates the inconsistencies and quality issues associated with open flame, torch heating and other methods. Once the system is properly calibrated and set up, there is no guess work or variation; the heating pattern is repeatable and consistent. With modern solid state systems, precise temperature control provides uniform results; power can be instantly turned on or shut off. With closed loop temperature control, advanced induction heating systems have the capability to measure the temperature of each individual part. Specific ramp up, hold and ramp down rates can be established & data can be recorded for each part that is run.
Maximized Productivity
Production rates can be maximized because induction works so quickly; heat is developed directly and instantly (>2000º F. in < 1 second) inside the part. Startup is virtually instantaneous; no warm up or cool down cycle is required. The induction heating process can be completed on the manufacturing floor, next to the cold or hot forming machine, instead of sending batches of parts to a remote furnace area or subcontractor. For example, a brazing or soldering process which previously required a time-consuming, off-line batch heating approach can now be replaced with a continuous, one-piece flow manufacturing system.
Improved Product Quality
With induction, the part to be heated never comes into direct contact with a flame or other heating element; the heat is induced within the part itself by alternating electrical current. As a result, product warpage, distortion and reject rates are minimized. For maximum product quality, the part can be isolated in an enclosed chamber with a vacuum, inert or reducing atmosphere to eliminate the effects of oxidation.
Extended Fixture Life
Induction heating rapidly delivers site-specific heat to very small areas of your part, without heating any surrounding parts. This extends the life of the fixturing and mechanical setup.
Environmentally Sound
Induction heating systems do not burn traditional fossil fuels; induction is a clean, non-polluting process which will help protect the environment. An induction system improves working conditions for your employees by eliminating smoke, waste heat, noxious emissions and loud noise. Heating is safe and efficient with no open flame to endanger the operator or obscure the process. Non-conductive materials are not affected and can be located in close proximity to the heating zone without damage.
Reduced Energy Consumption
Tired of increasing utility bills? This uniquely energy-efficient process converts up to 90% of the energy expended energy into useful heat; batch furnaces are generally only 45% energy-efficient. And since induction requires no warm-up or cool-down cycle, stand-by heat losses are reduced to a bare minimum. The repeatability and consistency of the induction process make it highly compatible with energy-efficient automated systems.
High frequency induction machines and
induction heating technology is currently the highest heating efficiency of the metallic materials, the fastest speed, and low power consumption of environmental protection. It has been widely used in various industries on the thermal processing of the metal material, heat treatment, hot assembly and welding, melting process. It can not only heating the workpiece as a whole, but also on the relevance of the workpiece local heating; deep through the heat of the workpiece can be realized, to focus only on its surface, the surface heating; not only the direct heating of the metal material, but also on non-metallic material indirect heating. And so on. Thus, induction heating technology is more widely used in all walks of life.
Local heating of the surface of the workpiece with the induced current heat treatment process. This heat treatment process commonly used in the surface hardening, but also can be used for partial annealing or tempering, and sometimes also used for the overall quenching and tempering. The early 1930s, the United States, the Soviet Union has applied to the induction heating method for surface hardening of parts. With industrial development, induction heating, heat treatment technology continue to improve, continue to expand the range of applications.
Basic principles: the workpiece into the inductor (coil), and when the sensors pass into the alternating current of a certain frequency, alternating magnetic field is generated around. The electromagnetic induction effect of the alternating magnetic field so that the induction current the workpiece generated within a closed ─ ─ vortex. Induced currents are very unevenly distributed in the cross section of the workpiece, a high current density of the workpiece surface, the inwardly gradually decreases, this phenomenon is called the skin effect. The high current density of the workpiece surface energy into thermal energy, so that the temperature of the surface layer is increased, i.e. the surface heating. The current frequency is higher, the current density of the workpiece surface and the internal differential is the greater, the heating layer is thinner. Rapid cooling, the temperature of the heating layer over the temperature of the critical point of steel surface hardening can be achieved.
Classification: according to the frequency of the alternating current, the induction heating and heat treatment is divided into UHF, HF, RF, MF, working frequency.
(1) ultra-high frequency induction heating treatment used in the current frequency up to 27 MHz, the heating layer is extremely thin, only about 0.15 mm, can be used for complex shapes such as circular saws and workpiece thin surface hardening.
② high-frequency induction heating heat treatment is usually used in current frequency of 200 to 300 kHz, the depth of the heating layer is 0.5 to 2 mm can be used for the gear, cylinder sleeve, cam, shaft and other parts of the surface quenching.
③The radio induction heating heat treatment with the current frequency of 20 to 30 kHz, with a super audio induced current small modulus gear heating, the heating layer roughly along the tooth profile distribution, the pure fire better performance.
4 MF (Medium Frequency) induction heating of the heat treatment using the current frequency is generally from 2.5 to 10 kHz, the depth of the heating layer is 2 to 8 mm, and more for large modulus gear, having a larger diameter shaft and cold roll the workpiece such as surface hardening.
⑤ power frequency induction heating heat treatment used in the current frequency of 50 to 60 Hz, the depth of the heating layer is 10 to 15 mm, can be used for the surface hardening of large workpieces.
Characteristics and application: The main advantage of induction heating: ① having overall heating workpiece deformation is small, small power consumption. The ② pollution. ③ heating speed, the workpiece surface oxidation and decarbonization lighter. ④ surface hardened layer can be adjusted as needed, easy to control. (5) heating equipment can be installed in the mechanical processing production line, easy to realize mechanization and automation, easy to manage, and can reduce the transportation, saving manpower, improve production efficiency. ⑥ hardened layer martensite smaller, hardness, strength, toughness, are higher. ⑦ surface hardening of the workpiece surface greater compression internal stress, higher workpiece anti-fatigue breaking ability.
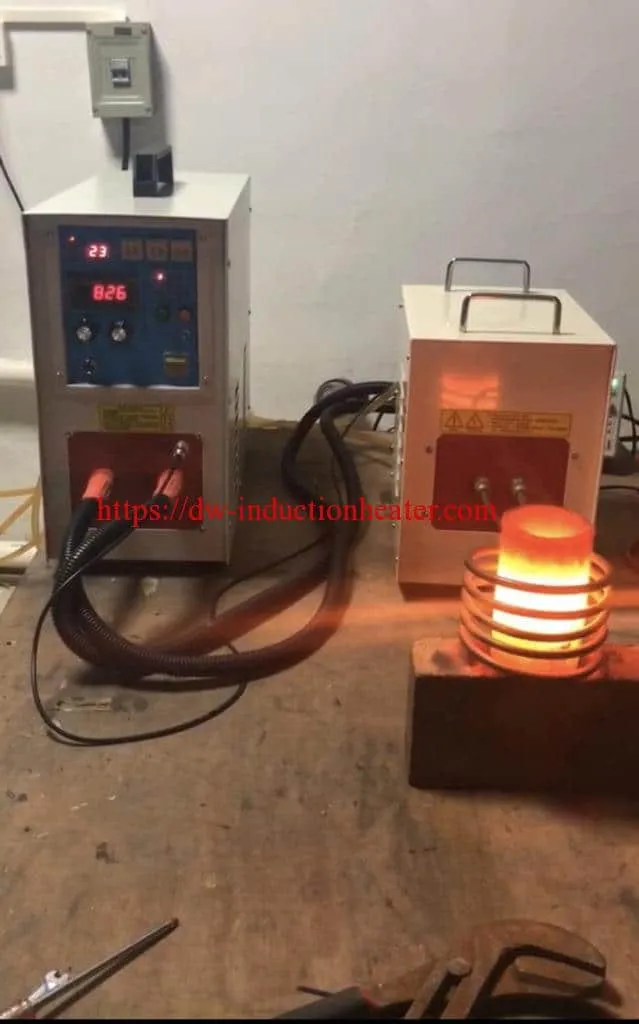
The
induction heating heat treatment also has some
drawbacks or
disadvantages. Compared with flame hardening, induction heating equipment is more complex, and adaptability to poor, difficult to guarantee the quality of some of the complex shape of the workpiece.
The induction heater is more complex, once the cost of inputs is relatively high, interchangeability and adaptability of the induction coil(inductor) is poor, can not be used for some complex shape of the workpiece.
But obviously,the advantages outweighed the disadvantages.
Therefore, the induction heating is a better choice of metalworking for replacing coal heating, oil heating, gas heating, electric cooker, electric oven heating and other heating methods.
Applications: Induction heating is widely used for the surface hardening of the gears, shafts, crankshafts, cams, rollers, etc. of the workpiece, the purpose is to improve the abrasion resistance and anti-fatigue breaking capability of these artifacts. Automobile rear axle using induction heating surface hardening, fatigue design load cycles increases by about 10 times more than the quenched and tempered. Induction heating surface hardening of the workpiece material is generally in the carbon steel. In order to meet the special needs of some of the workpiece has been developed for induction heating surface hardening dedicated low hardenability steel. High-carbon steel and cast iron workpiece can also be used induction heating surface hardening. The quenching medium commonly Water or polymer solution.
Equipment: Induction Heat Treatment Equipment power equipment, quenching machine and sensor. The main role of the power supply apparatus is suitable output frequency of the alternating current. The high-frequency current power supply tube high-frequency generator and two SCR inverter. IF current power supply generator sets. General power supply can only output a frequency current, some equipment can change the current frequency, directly with the 50 Hz power frequency current induction heating.
Selection: the depth of the induction heating device selection and the workpiece requires heating layer. Heating the deep layer of the workpiece, using the current low frequency power supply apparatus; the heating layer shallow workpiece, the current high frequency power supply apparatus should be used. Select other conditions of the power supply is the power of the device. Heating surface area increases, the electrical power required by the corresponding increase. When the heating surface area is too large, or when insufficient power supply, the method may be continuously heated, so that the relative movement of workpiece and the sensor, the front heating, behind cooling. But the best, or the entire heating surface heating. This can use the the workpiece core section waste heat so that the hardened surface layer tempering so that the process is simplified, and also saving energy.
The main role of the
induction heating machine is the workpiece positioning and necessary movement. It should also be accompanied by the quenching media device. Quenching machine can be divided into standard machine tools and special machine tools, the former applies to the general workpiece, which is suitable for mass production of complex workpieces.
Inductive heating of heat treatment, in order to ensure the quality of the heat treatment and to improve thermal efficiency, it is necessary according to the shape of the workpiece and requirements, design and manufacturing structure appropriate sensors. Common sensor heating the outer surface of the sensor, inner hole heating sensor plane heat sensor, universal heating sensor, a special type of heating sensor, a single type of heating sensors, the composite heated sensor, smelting furnace .