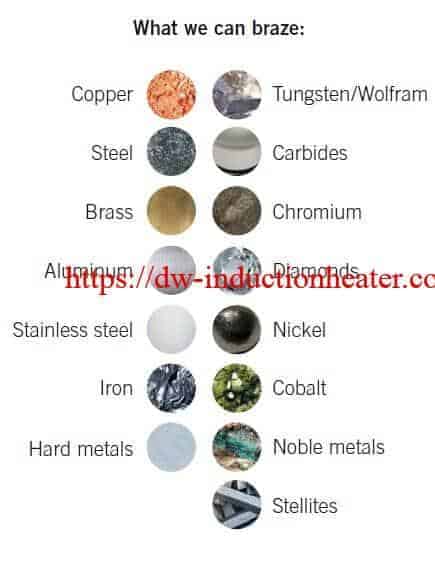
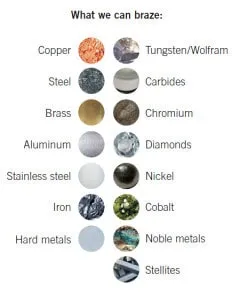
MYD-20KW | MYD-10KW | |
Input voltage | 3*380V, 50/60Hz, 4 Wires | |
Input Current | 1~30A | 1~15A |
Output Current | 0~300A | 0~200A |
Output Power | 1~20KW | 1~10KW, Max 15KW, 150% duty cycle |
Output Frequency | 5~30KHZ | |
Thermocouple | K type | |
Temperature system | Build in induction machine | |
Heating Temperature | Max800℃ | Max500℃ |
Size | 700 x 330 x 410 mm | 650 x 310 x 410 mm |
Weight | 32kg | 26 kg |
Induction Heating coil | ||
Length | 10~20 M | |
Diameter | 15 mm | |
Working temperature | -30~45℃ | |
Pipeline Size | OD: 50~500mm or equivalent |
Series |
Model |
Input power Max |
Input current Max |
Oscillate frequency |
Input Voltage |
Duty cycle |
|
M
.
F
. |
DW-MF-15 Induction Generator |
15KW |
23A |
1K-20KHZ
According to the application |
3*380V
380V±20% |
100% |
|
DW-MF-25 Induction Generator |
25KW |
36A |
|||||
DW-MF-35Induction Generator |
35KW |
51A |
|||||
DW-MF-45 Induction Generator |
45KW |
68A |
|||||
DW-MF-70 Induction Generator |
70KW |
105A |
|||||
DW-MF-90 Induction Generator |
90KW |
135A |
|||||
DW-MF-110 Induction Generator |
110KW |
170A |
|||||
DW-MF-160 Induction Generator |
160KW |
240A |
|||||
DW-MF-45 Induction Heating Rod Forging Furnace |
45KW |
68A |
1K-20KHZ |
3*380V
380V±20% |
100% |
||
DW-MF-70 Induction Heating Rod Forging Furnace |
70KW |
105A |
|||||
DW-MF-90 Induction Heating Rod Forging Furnace |
90KW |
135A |
|||||
DW-MF-110 Induction Heating Rod Forging Furnace |
110KW |
170A |
|||||
DW-MF-160 Induction Heating Rod Forging Furnace |
160KW |
240A |
|||||
DW-MF-15 Induction Melting Furnace |
15KW |
23A |
1K-20KHZ |
3*380V
380V±20% |
100% |
||
DW-MF-25 Induction Melting Furnace |
25KW |
36A |
|||||
DW-MF-35 Induction Melting Furnace |
35KW |
51A |
|||||
DW-MF-45 Induction Melting Furnace |
45KW |
68A |
|||||
DW-MF-70 Induction Melting Furnace |
70KW |
105A |
|||||
DW-MF-90 Induction Melting Furnace |
90KW |
135A |
|||||
DW-MF-110 Induction Melting Furnace |
110KW |
170A |
|||||
DW-MF-160 Induction Melting Furnace |
160KW |
240A |
|||||
DW-MF-110 Induction Hardening Equipment |
110KW |
170A |
1K-8KHZ |
3*380V
380V±20% |
100% |
||
DW-MF-160Induction Hardening Equipment |
160KW |
240A |
|||||
H
.
F
. |
DW-HF-04 Series |
DW-HF-4KW-A |
4KVA |
15A |
100-250KHZ |
Single phase 220V |
80% |
DW-HF-15 Series |
DW-HF-15KW-A
DW-HF-15KW-B |
15KVA |
32A |
30-100KHZ |
Single phase 220V |
80% |
|
DW-HF-25 Series |
DW-HF-25KW-A
DW-HF-25KW-B |
25KVA |
23A |
20-80KHZ |
3*380V
380V±10% |
100% |
|
DW-HF-35 Series |
DW-HF-35KW-B |
35KVA |
51A |
||||
DW-HF-45 Series |
DW-HF-45KW-B |
45KVA |
68A |
||||
DW-HF-60 Series |
DW-HF-60KW-B |
60KVA |
105A |
||||
DW-HF-80 Series |
DW-HF-80KW-B |
80KVA |
130A |
||||
DW-HF-90 Series |
DW-HF-90KW-B |
90KVA |
160A |
||||
DW-HF-120 Series |
DW-HF-120KW-B |
120KVA |
200A |
||||
U
.
H
.
F
.
|
DW-UHF-3.2KW |
3.2KW |
13A |
1.1-2.0MHZ |
Single phase220V
±10% |
100% |
|
DW-UHF-4.5KW |
4.5KW |
20A |
|||||
DW-UHF-045T |
4.5KW |
20A |
|||||
DW-UHF-045L |
4.5KW |
20A |
|||||
DW-UHF-6.0KW |
6.0KW |
28A |
|||||
DW-UHF-06A |
6.0KW |
28A |
|||||
DW-UHF-6KW-B |
6.0KW |
28A |
|||||
DW-UHF-10KW |
10KW |
15A |
100-500KHZ |
3*380V
380V±10% |
100% |
||
DW-UHF-20KW |
20KW |
30A |
50-250KHZ |
||||
DW-UHF-30KW |
30KW |
45A |
50-200KHZ |
||||
DW-UHF-40KW |
40KW |
60A |
50-200KHZ |
||||
DW-UHF-60KW |
60KW |
90A |
50-150KHZ |
Magnetic Induction Heater is a process equipment which is used to melt,braze,forge,bond,heat treating,harden or soften metals or other conductive materials. For many modern manufacturing processes, Magnetic induction heating equipment offers an attractive combination of speed, consistency and control.The basic principles of magnetic induction heating have been understood and applied to manufacturing since the 1920s. During World War II, the technology developed rapidly to meet urgent wartime requirements for a fast, reliable process to harden metal engine parts. More recently, the focus on lean manufacturing techniques and emphasis on improved quality control have led to a rediscovery of induction technology, along with the development of precisely controlled, all solid state induction power supplies.
Magnetic Induction Heater relies on the unique characteristics of induction heating radio frequency (RF) energy - that portion of the electromagnetic spectrum below infrared and microwave energy. Since heat is transferred to the product via electromagnetic waves, the part never comes into direct contact with any flame, the inductor itself does not get hot, and there is no product contamination. When properly set up, the process becomes very repeatable and controllable.
Series |
Model |
Input power Max |
Input current Max |
Oscillate frequency |
Input Voltage |
Duty cycle |
|
M
.
F
. |
DW-MF-15 Induction Generator |
15KW |
23A |
1K-20KHZ
According to the application |
3*380V
380V±20% |
100% |
|
DW-MF-25 Induction Generator |
25KW |
36A |
|||||
DW-MF-35Induction Generator |
35KW |
51A |
|||||
DW-MF-45 Induction Generator |
45KW |
68A |
|||||
DW-MF-70 Induction Generator |
70KW |
105A |
|||||
DW-MF-90 Induction Generator |
90KW |
135A |
|||||
DW-MF-110 Induction Generator |
110KW |
170A |
|||||
DW-MF-160 Induction Generator |
160KW |
240A |
|||||
DW-MF-45 Induction Heating Rod Forging Furnace |
45KW |
68A |
1K-20KHZ |
3*380V
380V±20% |
100% |
||
DW-MF-70 Induction Heating Rod Forging Furnace |
70KW |
105A |
|||||
DW-MF-90 Induction Heating Rod Forging Furnace |
90KW |
135A |
|||||
DW-MF-110 Induction Heating Rod Forging Furnace |
110KW |
170A |
|||||
DW-MF-160 Induction Heating Rod Forging Furnace |
160KW |
240A |
|||||
DW-MF-15 Induction Melting Furnace |
15KW |
23A |
1K-20KHZ |
3*380V
380V±20% |
100% |
||
DW-MF-25 Induction Melting Furnace |
25KW |
36A |
|||||
DW-MF-35 Induction Melting Furnace |
35KW |
51A |
|||||
DW-MF-45 Induction Melting Furnace |
45KW |
68A |
|||||
DW-MF-70 Induction Melting Furnace |
70KW |
105A |
|||||
DW-MF-90 Induction Melting Furnace |
90KW |
135A |
|||||
DW-MF-110 Induction Melting Furnace |
110KW |
170A |
|||||
DW-MF-160 Induction Melting Furnace |
160KW |
240A |
|||||
DW-MF-110 Induction Hardening Equipment |
110KW |
170A |
1K-8KHZ |
3*380V
380V±20% |
100% |
||
DW-MF-160Induction Hardening Equipment |
160KW |
240A |
|||||
H
.
F
. |
DW-HF-04 Series |
DW-HF-4KW-A |
4KVA |
15A |
100-250KHZ |
Single phase 220V |
80% |
DW-HF-15 Series |
DW-HF-15KW-A
DW-HF-15KW-B |
15KVA |
32A |
30-100KHZ |
Single phase 220V |
80% |
|
DW-HF-25 Series |
DW-HF-25KW-A
DW-HF-25KW-B |
25KVA |
23A |
20-80KHZ |
3*380V
380V±20% |
100% |
|
DW-HF-35 Series |
DW-HF-35KW-B |
35KVA |
51A |
||||
DW-HF-45 Series |
DW-HF-45KW-B |
45KVA |
68A |
||||
DW-HF-60 Series |
DW-HF-60KW-B |
60KVA |
105A |
||||
DW-HF-80 Series |
DW-HF-80KW-B |
80KVA |
130A |
||||
DW-HF-90 Series |
DW-HF-90KW-B |
90KVA |
160A |
||||
DW-HF-120 Series |
DW-HF-120KW-B |
120KVA |
200A |
||||
U
.
H
.
F
.
|
DW-UHF-3.2KW |
3.2KW |
13A |
1.1-2.0MHZ |
Single phase220V
±10% |
100% |
|
DW-UHF-4.5KW |
4.5KW |
20A |
|||||
DW-UHF-045T |
4.5KW |
20A |
|||||
DW-UHF-045L |
4.5KW |
20A |
|||||
DW-UHF-6KW-I |
6.0KW |
28A |
|||||
DW-UHF-6KW-II |
6.0KW |
28A |
|||||
DW-UHF-6KW-III |
6.0KW |
28A |
|||||
DW-UHF-10KW |
10KW |
15A |
100-500KHZ |
3*380V
380V±10% |
100% |
||
DW-UHF-20KW |
20KW |
30A |
50-250KHZ |
||||
DW-UHF-30KW |
30KW |
45A |
50-200KHZ |
||||
DW-UHF-40KW |
40KW |
60A |
50-200KHZ |
||||
DW-UHF-6, 0KW |
60KW |
90A |
50-150KHZ |
In order to want to improve safety and productivity, and reduce energy costs, by using induction instead of resistive heating. To maximize productivity, they want to be able to heat 3 brass rods at a time to 780° C within 25 seconds. For this application test, we are only heating one rod, so our goal is to heat the single rod to 780° C within 25 seconds with less than 45 kW of power. This will ensure that when heating 3 rods, that the 110 kW system will meet the production requirements.
Equipment DW-HF-70kW Induction Heating Power Supply, operating between 10-50 kHz
Materials • Brass rod • Custom coil, 10 turns, D=50mm, designed and manufactured by DaWei Induction Power Technologies for this specific application – capable to heat 3 rods at a heat cycle.
Key Parameters Temperature: 780° C Power: 70 kW Voltage: 380 – 480 V Time: 24 sec Frequency: 32 kHz
Process:
Results/Benefits:
Induction preheating provides:
Type | Input Power | Melting Capacity | Max Temperature | ||
steel, stainless steel | copper, gold, silver (scrap, Slag) | aluminum, aluminum alloy, Aluminum scrap, Aluminum slag, pop can | 1800℃ | ||
SMJD-463 | 60 KW | 200 KG | 500 KG | 200 KG | |
SMJD-480 | 60 KW | 150 KG | 500 KG | 150 KG | |
SMJD-580 | 80 KW | 200 KG | 600 KG | 200 KG | |
SMJD-600 | 60 KW | 230 KG | 560 KG | 230 KG | |
SMJD-900 | 120 KW | 300 KG | 900 KG | 300 KG | |
SMJD-905 | 80 KW | 300 KG | 900 KG | 300 KG | |
SMJD-1250 | 80 KW | 400 KG | 1200 KG | 400 KG | |
SMJD-1250 | 120 KW | 450 KG | 1350 KG | 450 KG | |
SMJD-1500 | 120 KW | 500 KG | 1500 KG | 500 KG | |
SMJD-1550 | 120 KW | 520 KG | 1560 KG | 520 KG | |
SMJD-1700 | 160KW | 600 KG | 1700 KG | 600 KG | |
SMJD-2300 | 160KW | 800 KG | 2000 KG | 800 KG | |
SMJD-3100 | 200KW | 1200 KG | 3000 KG | 1200 KG |