5 Essential FAQs on Induction Hardening for Maximizing Durability
Induction hardening is a heat treatment process that improves the mechanical properties of a metal piece, particularly its hardness and strength.
Here are five frequently asked questions about induction hardening:
- What is induction hardening, and how does it work?Induction hardening is a process where a metal part is heated by electromagnetic induction to a temperature within or above its transformation range and then immediately quenched. The rapid heating is produced by circulating high-frequency electrical currents induced by a magnetic field around the metal part. Quenching, usually done by water, polymer, or air blast, rapidly cools down the metal, causing a transformation in its microstructure, which increases hardness and wear resistance.
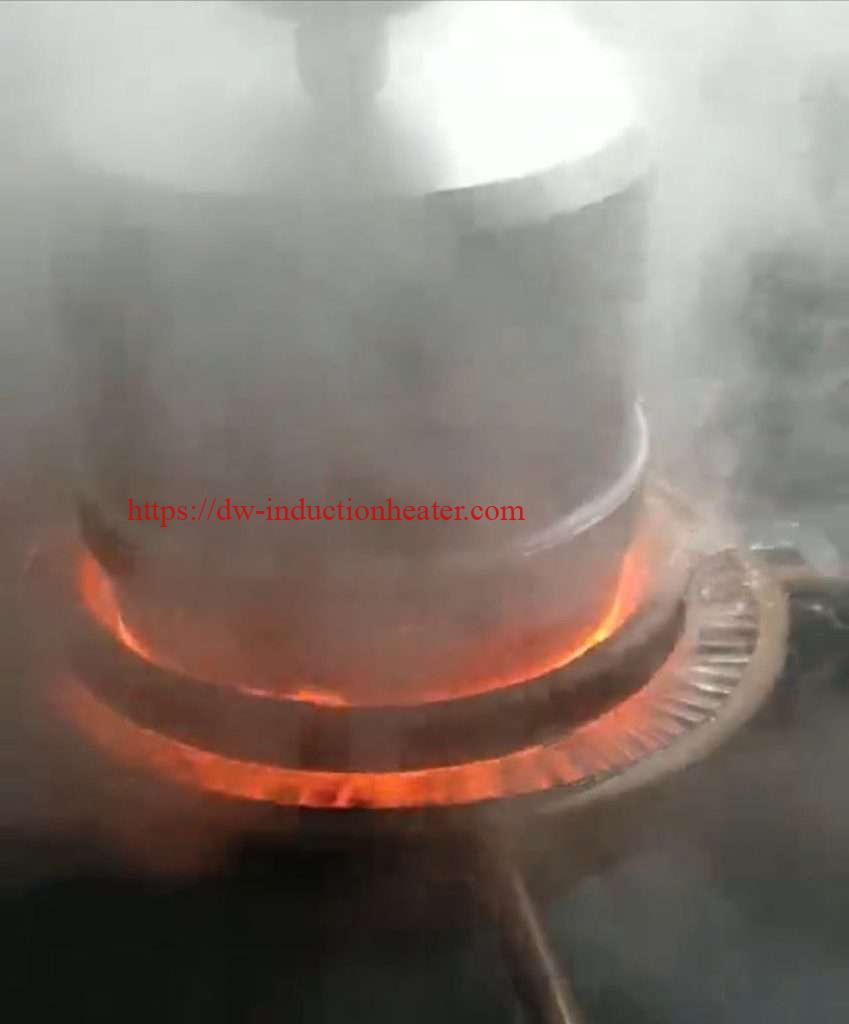
- What kinds of materials are suitable for induction hardening?The process is most commonly applied to medium-carbon and alloy steels that have a carbon content high enough to allow for the formation of martensite upon quenching. Ductile iron can also be induction hardened, as well as other grade steels with appropriate carbon and alloy content. Materials that cannot form martensite when quenched, such as low-carbon steels, are generally not suitable for induction hardening.
- What are the main advantages of induction hardening?Induction hardening has several advantages, including:
- Speed: It is a rapid process compared to conventional furnaces.
- Selectivity: Specific areas of a component can be selectively hardened without affecting the entire part.
- Consistency: Controlled heating and quenching ensure consistent hardness and mechanical properties.
- Energy efficiency: Less energy is wasted heating the entire part or a large furnace space.
- Integration: Induction systems can be integrated into manufacturing lines for inline processing.
- What are the typical applications of induction hardening?Induction hardening is used in a wide range of applications where improved wear resistance and strength are desirable. Common applications include:
- Gears and sprockets
- Shafts
- Spindles
- Bearings and bearing races
- Camshafts
- Crankshafts
- Fasteners
- Tooling and die components
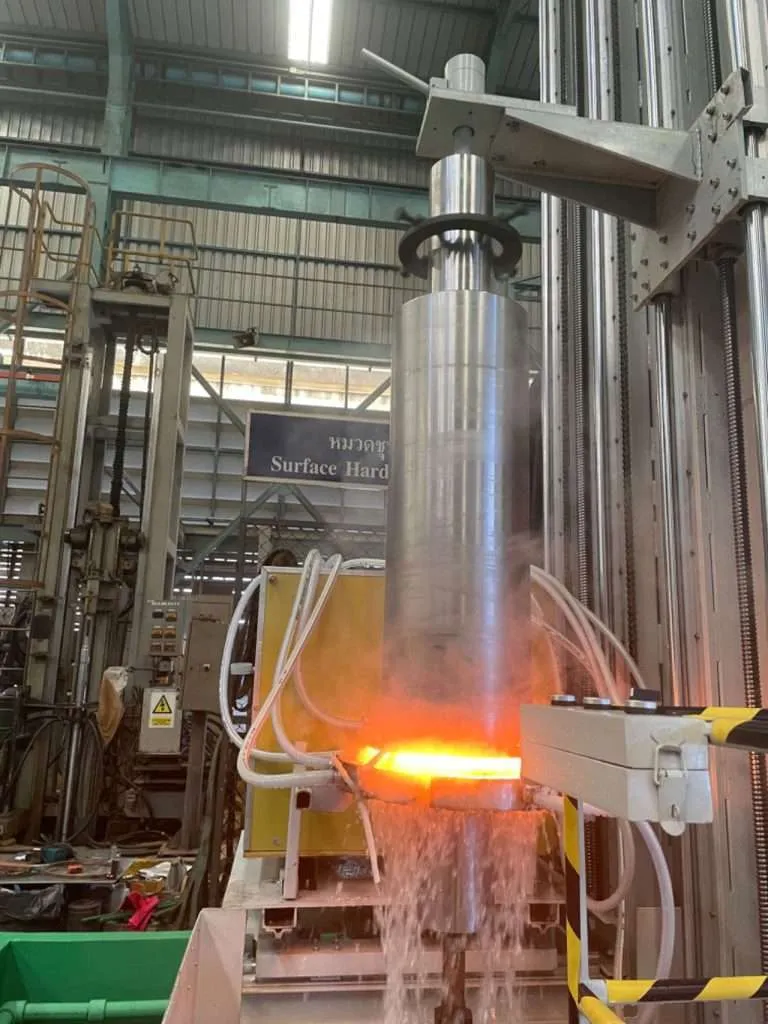
- How does induction hardening compare to other hardening methods?Compared to other hardening methods like case hardening or flame hardening, induction hardening offers more precise control over the hardened zone and depth. It is also faster and more energy-efficient than furnace hardening. However, it requires more initial investment in terms of equipment cost. Unlike case hardening, induction hardening does not involve the introduction of carbon or other elements into the surface layer of the metal part. Therefore, it is not suitable for materials that are not already predisposed to hardening through the heat-treat process.
https://dw-inductionheater.com/5-essential-faqs-on-induction-hardening-for-maximizing-durability.html?feed_id=240923&_unique_id=66168d1821e31