2023年8月31日星期四
Induction Brazing Brass Faucet
Induction Brazing Brass Faucet
Objective Brazing two joints on a brass bathroom faucet assembly
Material Brass bathroom fittings 1” OD, brazing rings, flux
Temperature 1148 ºF (620 ºC)
Frequency 90 kHz
Equipment • DW-UHF-30 kW induction heating system, equipped with a remote workhead containing eight 1.0 μF capacitors for a total of 8.0 μF
• An induction heating coil designed and developed specifically for this application.
Process A two turn C shaped coil is used to braze the faucet assembly.
The braze rings are placed at the joint, the parts assembled and fluxed. The first braze joint is heated for 30 seconds and the braze ring flows. The assembly is rotated & the second joint is heated for 30 seconds to flow the braze ring. The two brazes are completed in 60 seconds.
Results/Benefits Induction heating provides:
• Faster, repeatable and consistent results
• Localized heat produces neat and clean joints
• Hands-free heating that involves no operator skill for manufacturing
• Even distribution of heating
Aluminum Billet Heating Furnace
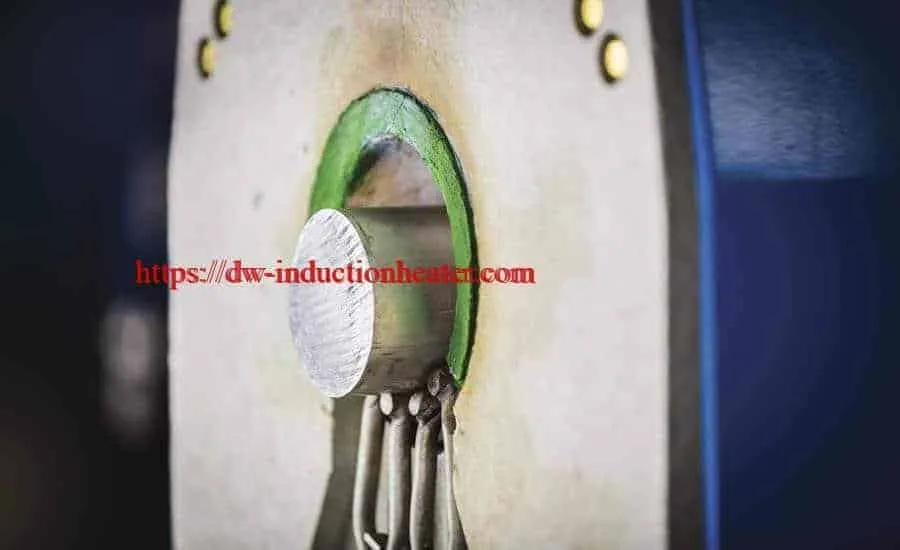
Continous Aluminum Billet Heating Furnace/Aluminium Alloys Billet Heater for the heating Aluminum Billets/Rods/Bars before the hot formging, extrusion, hot rolling and cutting,etc.
Induction Heating is a proven, reliable and efficient method of heating hot forming aluminum alloys. However, aluminum alloys have material properties that, if unaccounted for, can result in unexpected challenges. Understanding the unique facets of the induction heating of aluminum can be achieved by considering the properties that make aluminum alloys such advantageous materials. Given that aluminum and its alloys offer numerous advantages over many other metals, it is not surprising that inquiries about induction billet-heating equipment increasingly involve the heating of aluminum alloys. Many of these inquiries focus on how the induction heating of aluminum differs from the induction heating of other materials – typically steels – and how these differences affect heating quality, efficiency and productivity. Electromagnetic induction is well-suited for the heating of aluminum-alloy billets. However, there are some critical, yet easily overlooked, realities of aluminum billet heating that should be considered when designing, operating and maintaining this type of equipment. Fundamentally, the induction heating of aluminum alloys is no different than that of other common materials (e.g., carbon-steel and stainless steel alloys). It is ultimately material-property differences that set apart the induction heating of aluminum alloys from other metals. These material-property differences, if unaccounted for, can result in unexpected equipment performance and practical challenges. Because the users of most continuous induction billet-heating systems are familiar with the induction heating of steels and carbon-steel and stainless steel alloys, they provide a convenient point of reference in the consideration of the continuous heating of aluminum-alloy billets. HLQ Induction Equipment Co.,Ltd specializes in continous aluminum billet heating furnace/aluminium billet heater for heating aluminum billets/bars/rods before the hot formging, extrusion, hot rolling and cutting,etc.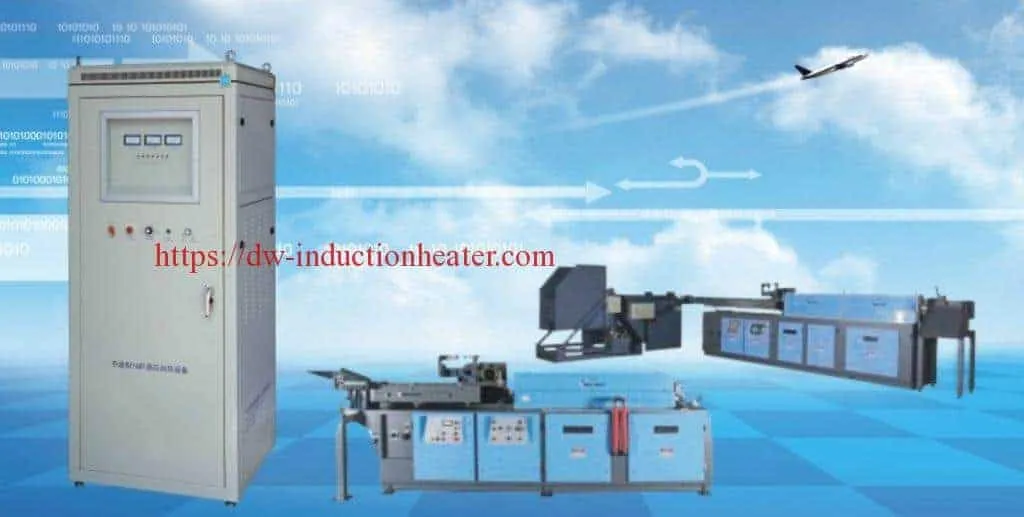

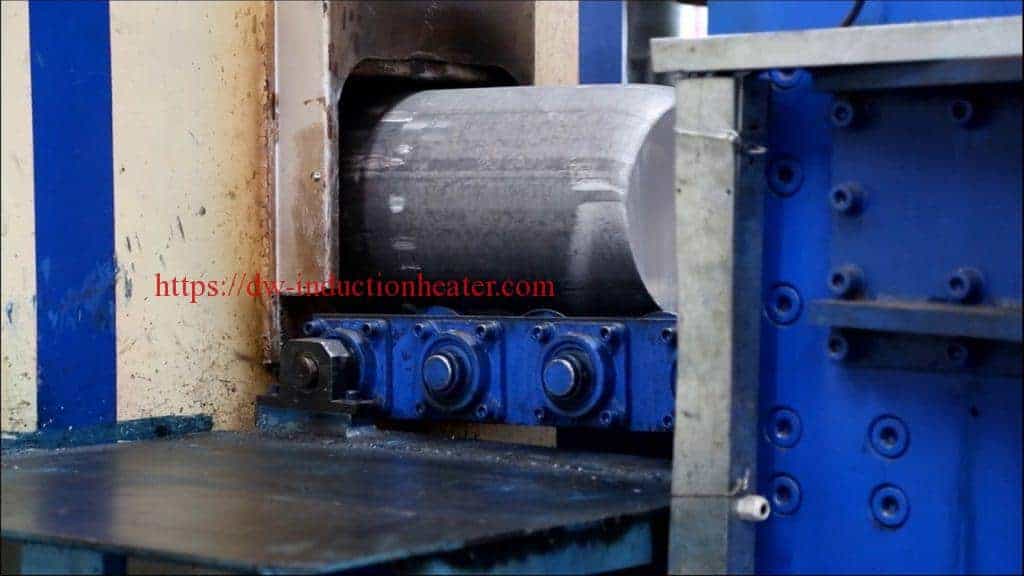
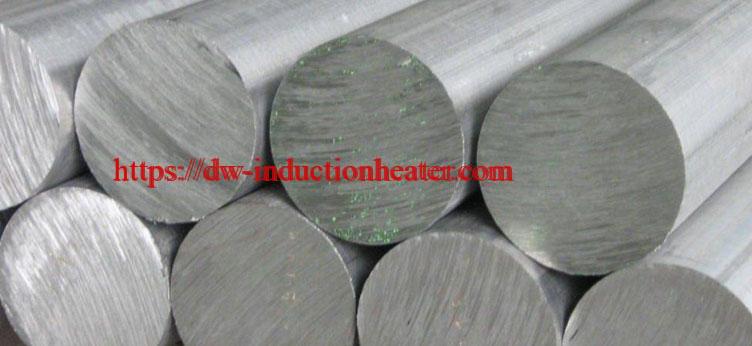
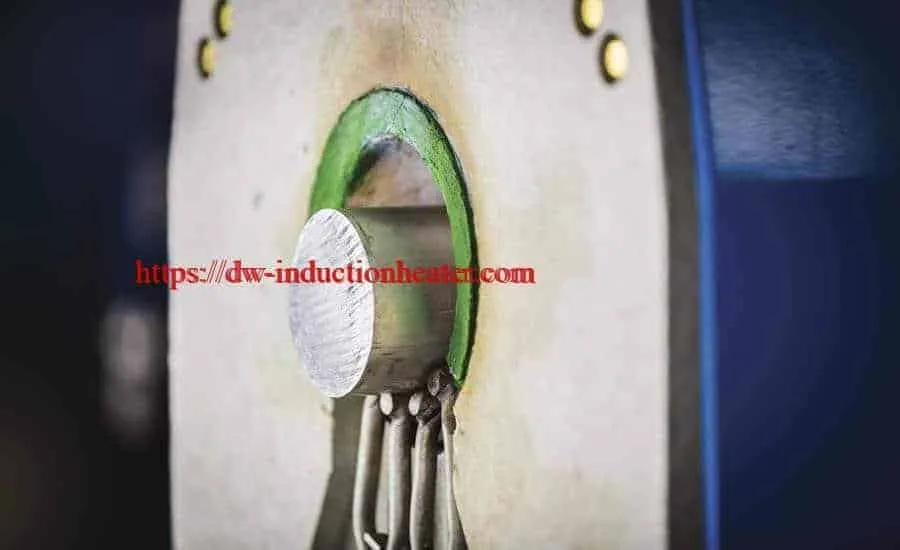
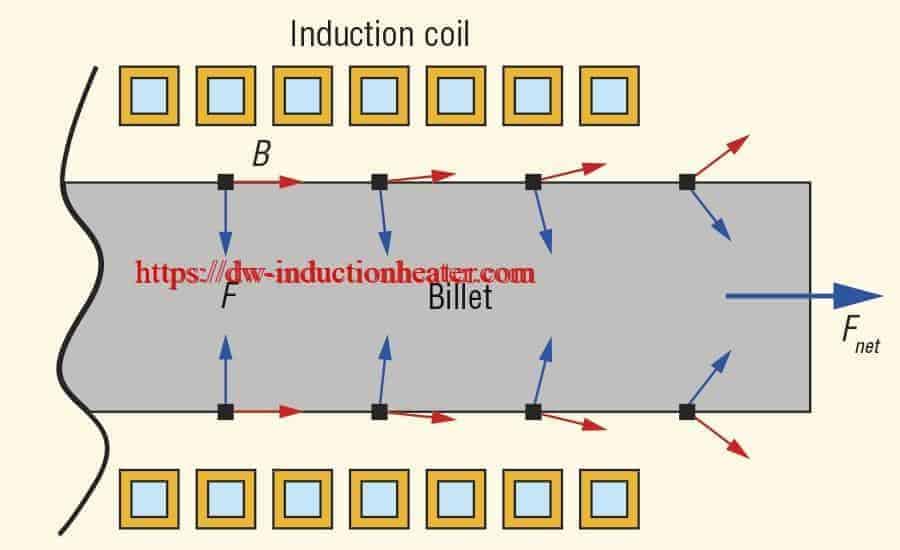
Induction Preheat Welding Systems
Portable Post Weld Heating Treatment System With Induction
Main Application:
l Preheat: weld heat,coating, spraying, bending, fitting&unfitting heat
l Post-weld heat treatment: tank, boile, pipeline, steel sheet or other metal jobs
l InductionHeat: mold heating, shipboard, zinc bath, large& irregular metal parts
l Pipeline material heat: pipeline oil, pipeline gas, pipeline water, pipeline petrochemical and other pipeline material
Main Features:
* High speed: 70%
* Low tolerance
* Energy Saving
* High efficiency
* Accurate heating
* Simple operation
* Non-contact heating
* Environmental protection
* Hypothermia circumstance
* Air cooling is suitable for low-temperature environment
* Induction heating is more uniform than oil,gas,flame heating
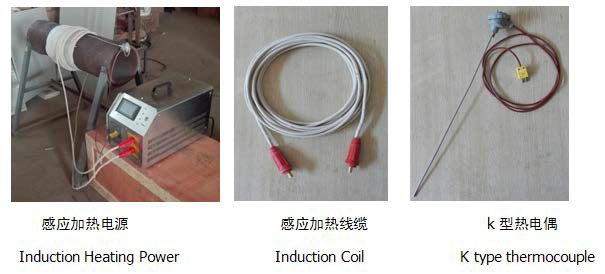
MYD-20KW | MYD-10KW | |
Input voltage | 3*380V, 50/60Hz, 4 Wires | |
Input Current | 1~30A | 1~15A |
Output Current | 0~300A | 0~200A |
Output Power | 1~20KW | 1~10KW, Max 15KW, 150% duty cycle |
Output Frequency | 5~30KHZ | |
Thermocouple | K type | |
Temperature system | Build in induction machine | |
Heating Temperature | Max800℃ | Max500℃ |
Size | 700 x 330 x 410 mm | 650 x 310 x 410 mm |
Weight | 32kg | 26 kg |
Induction Heating coil | ||
Length | 10~20 M | |
Diameter | 15 mm | |
Working temperature | -30~45℃ | |
Pipeline Size | OD: 50~500mm or equivalent |
2023年8月30日星期三
Induction Brazing Stainless Steel
Induction Brazing Stainless Steel
Objective
1st Application: Braze hub assembly to needle holder
2nd Application: Braze Large tube to ring joint
Material: 1st Application: Steel hub assembly and needle 0.1" dia(2.5mm) 2nd Application: Steel tube 1" OD (25.4 mm) and ring
Temperature 1400 ºF (760 ºC)
Frequency 325 kHz for brazing the needle 0.1" dia (2.5mm) 259 kHz for brazing ring to steel tube 1" OD (25.4 mm)
Equipment • DW-UHF-4.5KW induction heating system, equipped with a
remote workhead containing two .66 μF capacitors for a total of 1.32 μF
• Two induction heating coils, designed and developed specifically for this dual application.
Process 1st application: A two-turn helical coil is used to heat the hub assembly on the needle holder for 10 seconds. The coil concentrates the heat on the hub only, as the needle is magnetic and the hub material is non-magnetic. A small
diameter braze wire is used to supply sufficient amount of braze creating a strong aesthetically pleasing bond. 2nd application: A three-turn helical coil is used for brazing the large tube to the ring joint for 3-5 minutes. A braze ring is
used to supply sufficient amount of braze to create an aesthetically pleasing bond.
Results/Benefits Induction heating provides:
• Even distribution of heating, provides even flow of braze alloy for an aesthetically pleasing bond
• System flexibility allows for the same unit to be used for two different applications which is a cost saving.
Billet Heating Furnace with Induction Heating

24h Continous Billet Heating Furnace with induction for the heating of copper/aluminum/iron steel billets before hot forming
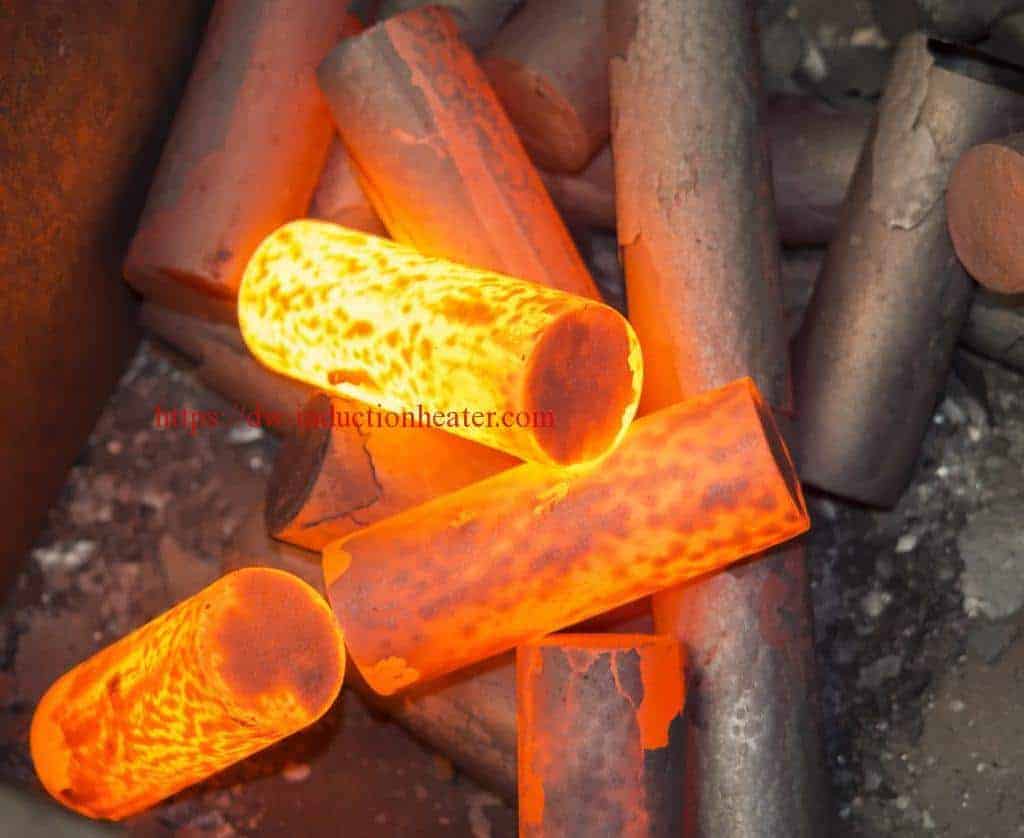
Features | Detail | |
1 | Heating fast and stable | saving 20%- 30% electric energy than traditional way; High efficiency and low energy consumption |
2 | Small in size | Easy to install, operate and repair |
3 | Safe and reliable | No high voltage, very safe to your workers. |
4 | A cooling circulation system | Able to operate continuously 24 hours |
5 | complete self-protect function | many types of alarm lamps: over-current, over-voltage, over hot, water shortage etc. These lamps can control and protect machine. |
6 | Environmental protection | Almost no oxide layer, produced no exhaust, no waste-water |
7 | IGBT Type | Avoid the interruption of unrelated electric net; Ensure the long-life of the machine. |
DW-MF-200 | DW-MF-250 | DW-MF-300 | DW-MF-400 | DW-MF-500 | DW-MF-600 | ||
Input Voltage | 3phases, 380V/410V/440V , 50/60Hz | ||||||
Max Input Current | 320A | 400A | 480A | 640A | 800A | 960A | |
Oscillating frequency | 0.5KHz^20KHz ( Oscillating frequency will be customized according to the size of heating parts) | ||||||
Duty Cycle Loading | 100%,24h continuously work | ||||||
Cooling Water Desires | 0.1MPa | ||||||
Dimension | Host | 1000X800X1500mm | 1500X800X2800mm | 850X1700X1900mm | |||
Extension | extension will be customized according to the material and size of heating parts | ||||||
Weight | 110kg | 150kg | 160kg | 170kg | 200kg | 220kg | |
Depend on the dimension of extension |

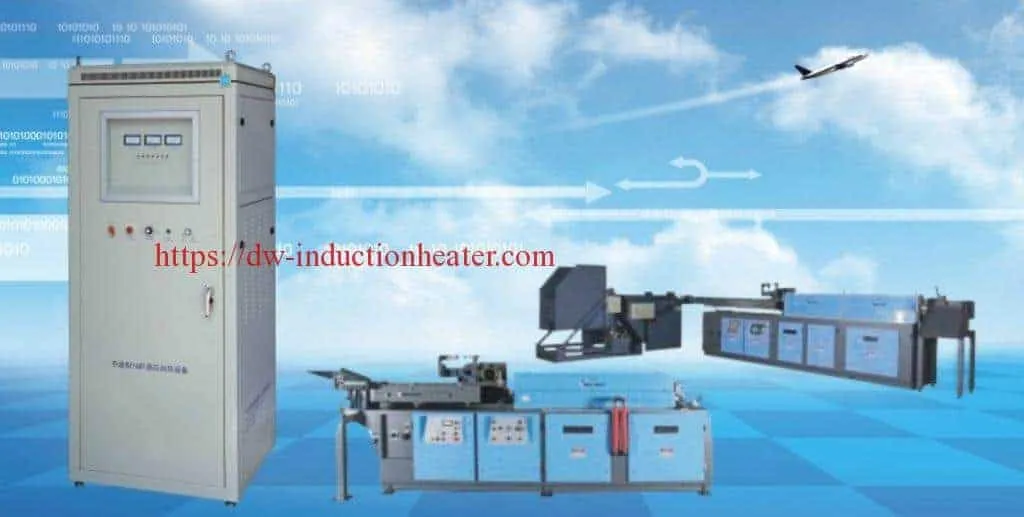
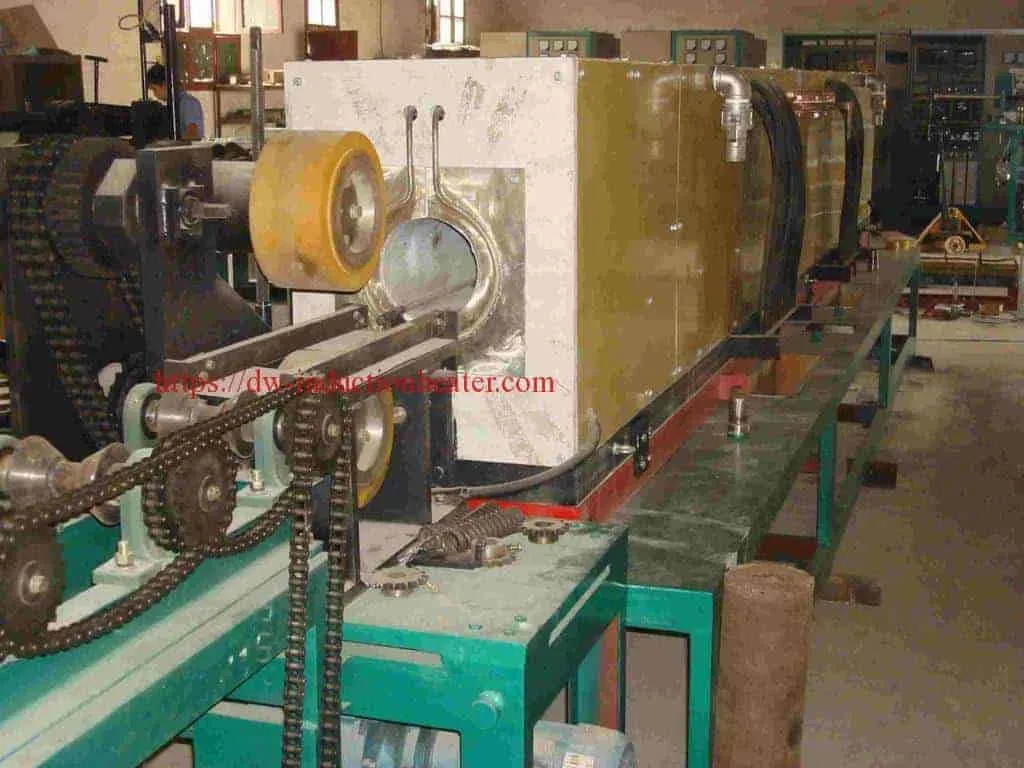
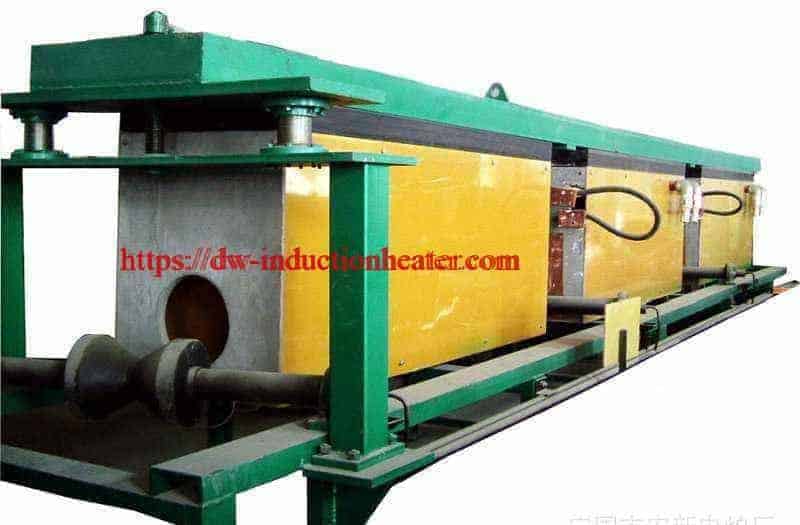
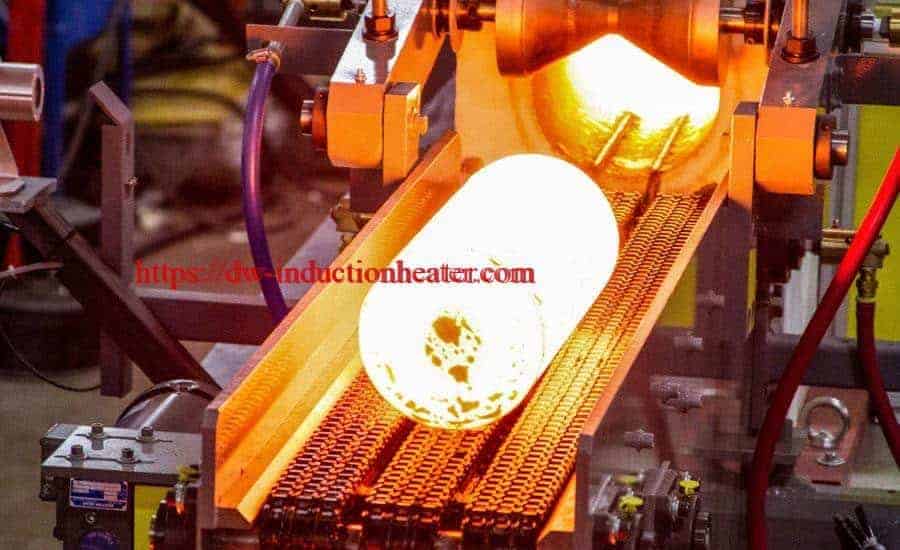
induction brazing steel carbide cap to shaft
Objective
High Frequency Induction brazing steel carbide cap to shaft. Customer currently uses a torch process, but would like to change to induction brazing in order to reduce scrap and rework and improve the quality of the braze.
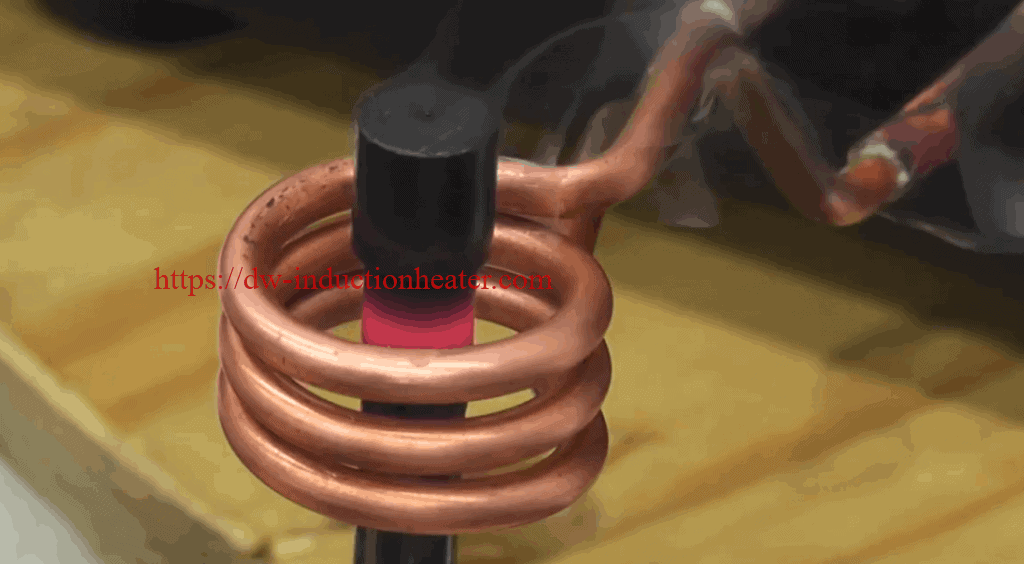
Equipment
DW-UHF-6kw-III handheld induction brazing heater
Materials
• Carbon steel
• magnetic carbide caps
• Alloy – EZ Flo 3 paste
• Test 1: Shaft Diameter: 0.5” (12.7 mm)
• Test 2: Shaft Diameter: 0.375” (9.525mm)
• Test 3: Shaft Diameter: 0.312” (7.925mm)
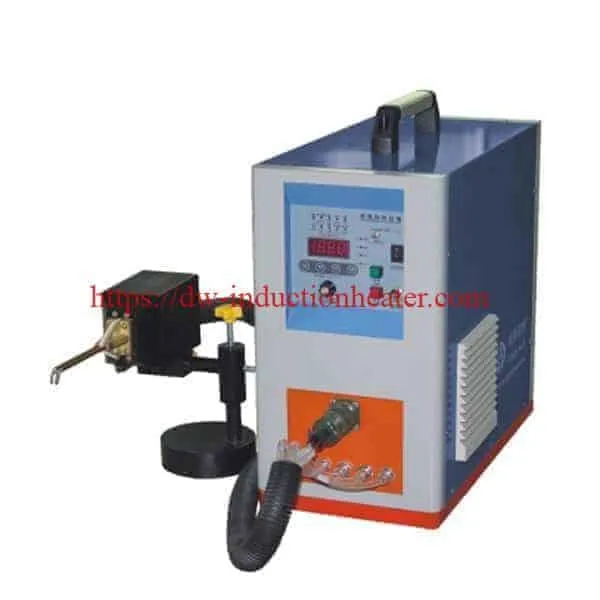
Process:
- Paste alloy was applied to the cone shape top of each steel shaft.
- The cap was set on top and rotated to distribute the paste alloy.
- Each assembly was positioned in the coil and heated.
- Preliminary heat tests were conducted using tempilaq paint to estimate the heat cycle to 1450 degrees F.
- Precise control of the time and temperature resulting in improved quality and consistent result
- Power on demand with rapid heat cycles
- Repeatable process, not operator dependent
- Safe induction heating with no open flames
- Energy efficient heating

2023年8月29日星期二
Induction Soldering Cable to Metallic Plate
Objective
The purpose of this test is to demonstrate the induction soldering cable to metallic plate process.
Recommended Equipment
The recommended equipment for this test is the DW-UHF-6kw-I handheld induction heater.
Results and Conclusions:
The results were satisfactory at 14 seconds. The complete process can be achieved in less than 5 seconds by increasing the frequency from under 200 kHz to over 300 kHz, as well as by increasing the induction heating power


Induction Brazing Principle-Theory

Induction Brazing Technology
Induction Brazing Principle|Theory Brazing and soldering are processes of joining similar or dissimilar materials using a compatible a filler material. Filler metals include lead, tin, copper, silver, nickel and their alloys. Only the alloy melts and solidifies during these processes to join the work piece base materials. The filler metal is pulled into the joint by capillary action. Soldering processes are conducted below 840°F (450°C) while brazing applications are conducted at temperatures above 840°F (450°C) up to 2100°F (1150°C).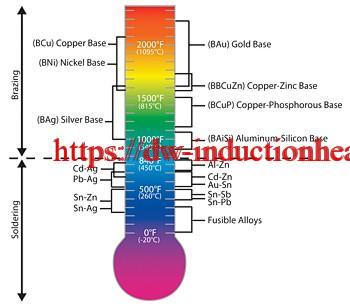

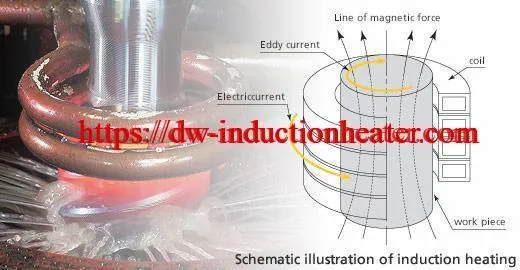
2023年8月28日星期一
aluminum scrap melting induction furnace

The top 200^2000kg aluminum scrap melting induction furnace for casting and melting aluminium scraps,ingots,cans and dross material.
Operation Steps:- An Aluminium melting induction furnace operator will place aluminum parts or aluminum ingot/scrap as a charge in the induction melting aluminum recycling furnace and start the furnace to begin the melting process. Adding more aluminum charge this process is advisable as molten aluminum transmits the heat better.
- When temperature of the aluminum reaches 1220.66°F it turns to liquid. Any residue from the coating and paint from the cans will float on the surface. This byproduct is called dross and can be skimmed by a steel ladle. This needs to cool before it can be disposed off safely.
- Next, the crucible (furnace) will pour out pure aluminum. Usually, Hydraulic tilting mechanism provided to pour large quantities of liquid metals.
- Finally, with care, the molten aluminum will be poured into mould to cool down and then slide out for use.
Type | Input Power | Melting Capacity | Max Temperature | ||
steel, stainless steel | copper, gold, silver (scrap, Slag) | aluminum, aluminum alloy, Aluminum scrap, Aluminum slag, pop can | 1800℃ | ||
SMJD-463 | 60 KW | 200 KG | 500 KG | 200 KG | |
SMJD-480 | 60 KW | 150 KG | 500 KG | 150 KG | |
SMJD-580 | 80 KW | 200 KG | 600 KG | 200 KG | |
SMJD-600 | 60 KW | 230 KG | 560 KG | 230 KG | |
SMJD-900 | 120 KW | 300 KG | 900 KG | 300 KG | |
SMJD-905 | 80 KW | 300 KG | 900 KG | 300 KG | |
SMJD-1250 | 80 KW | 400 KG | 1200 KG | 400 KG | |
SMJD-1250 | 120 KW | 450 KG | 1350 KG | 450 KG | |
SMJD-1500 | 120 KW | 500 KG | 1500 KG | 500 KG | |
SMJD-1550 | 120 KW | 520 KG | 1560 KG | 520 KG | |
SMJD-1700 | 160KW | 600 KG | 1700 KG | 600 KG | |
SMJD-2300 | 160KW | 800 KG | 2000 KG | 800 KG | |
SMJD-3100 | 200KW | 1200 KG | 3000 KG | 1200 KG |
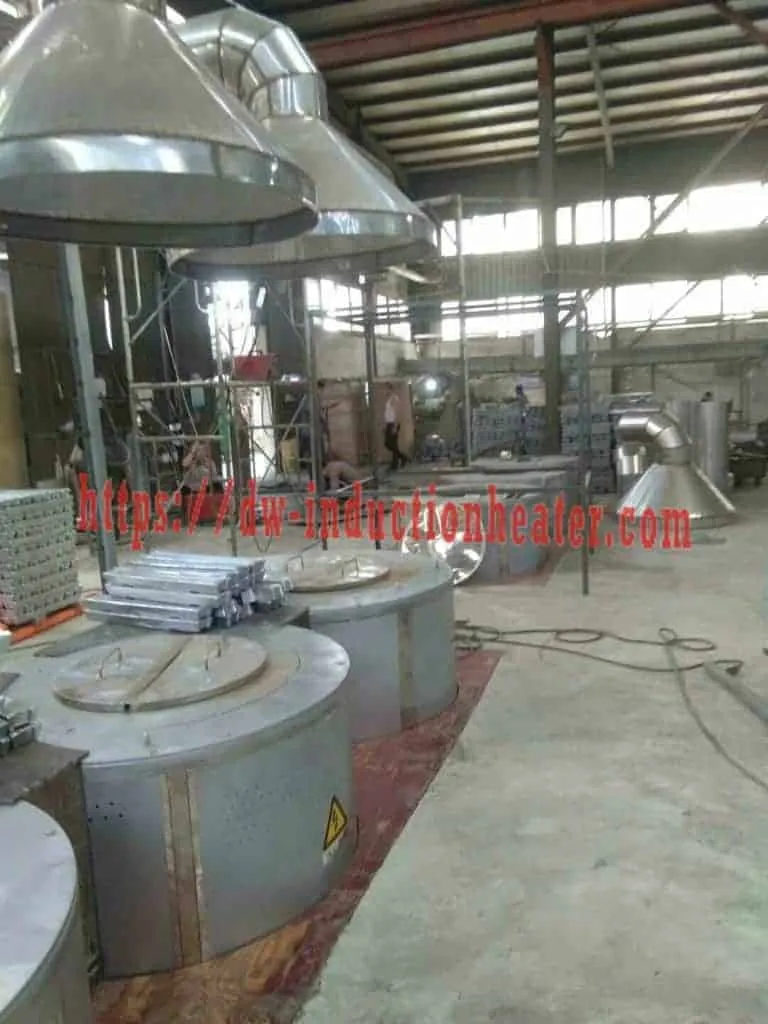
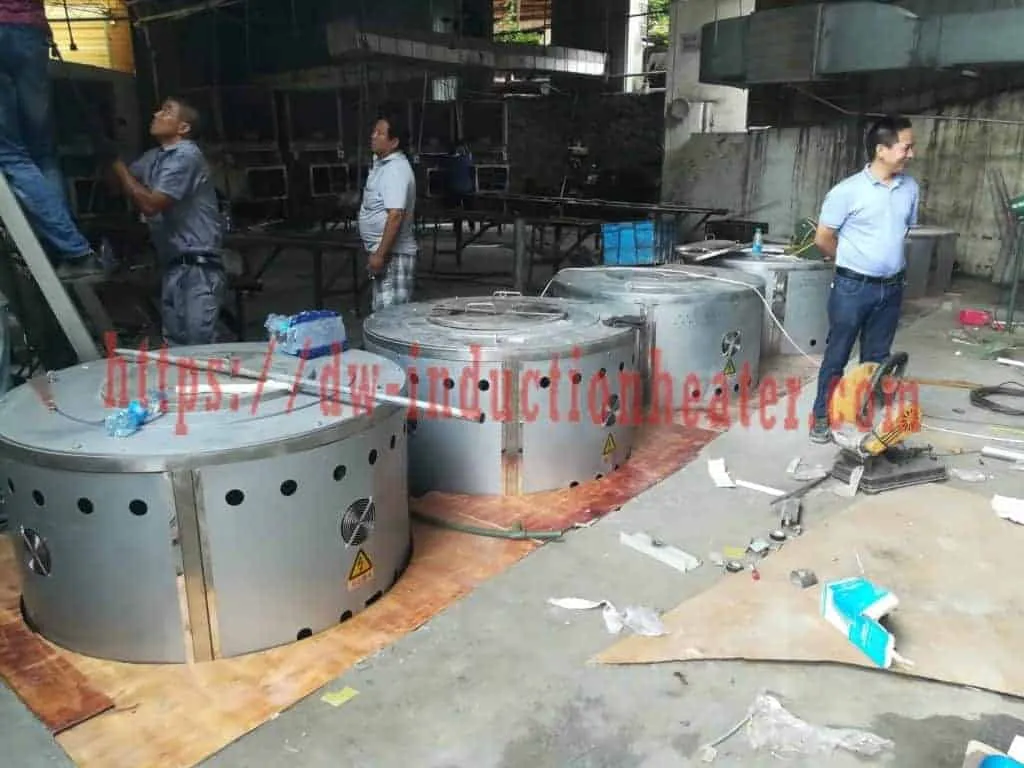
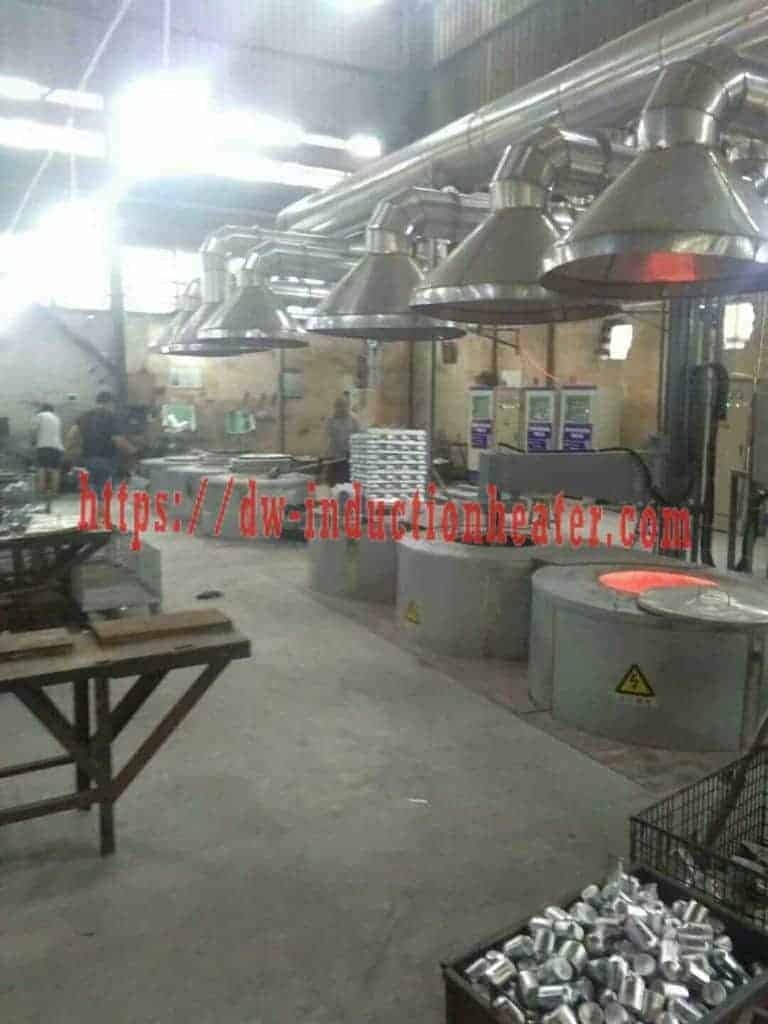
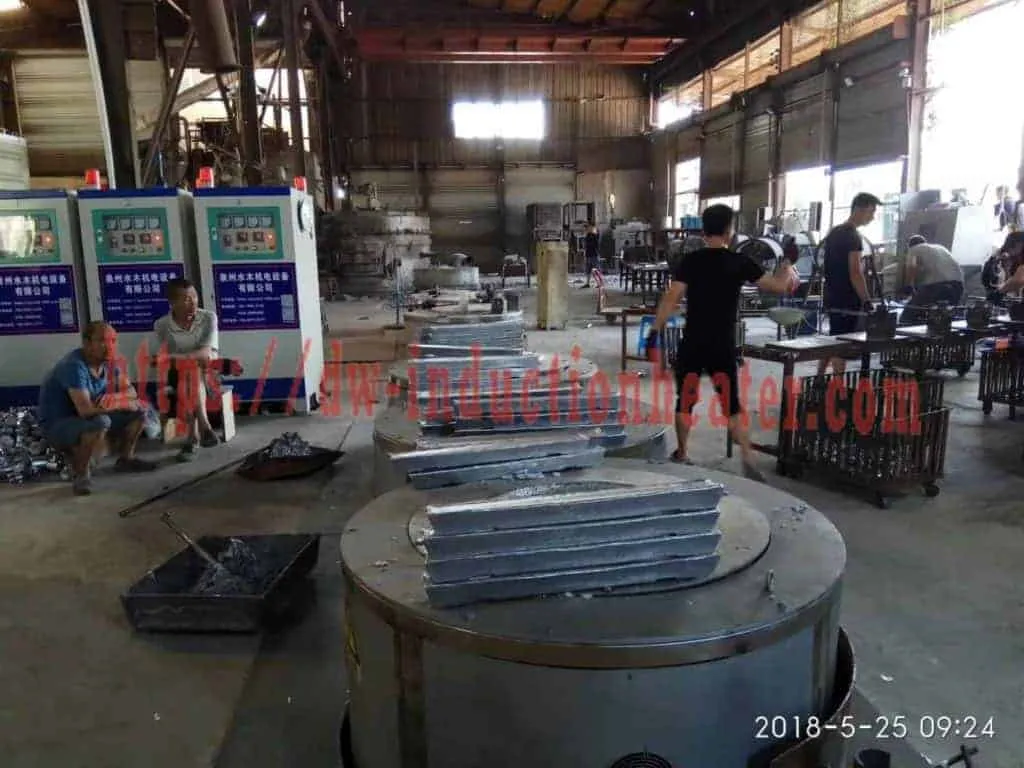
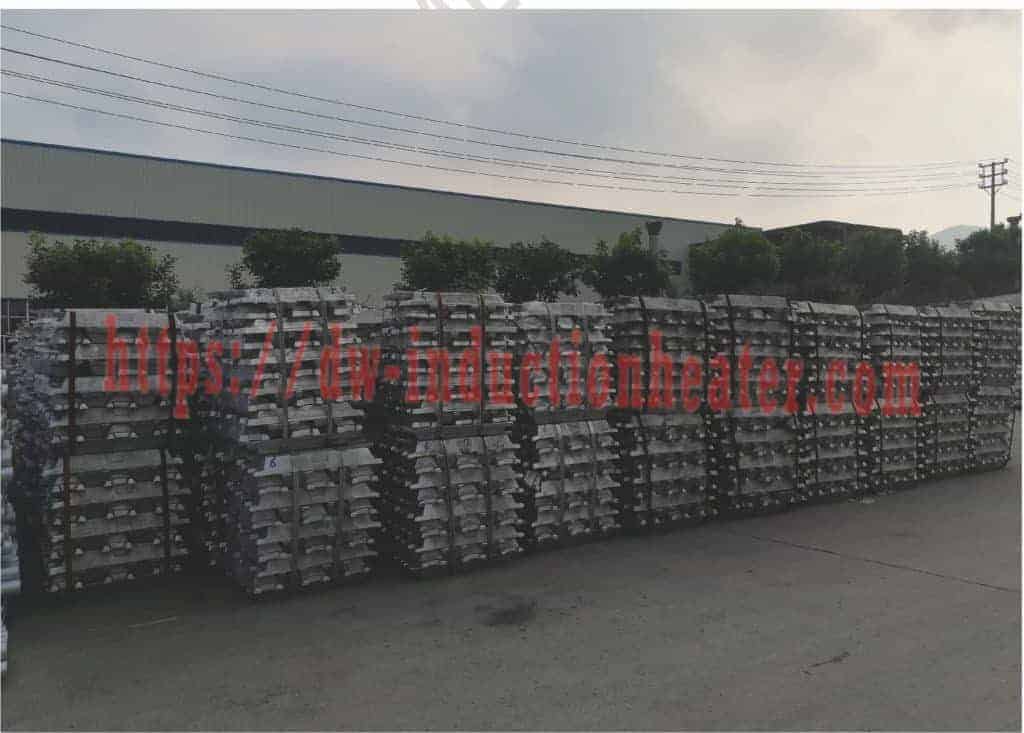
Induction Brazing Steel Tips
Induction Brazing Steel Tips with Hihg Frequency Heating System
Objective To heat a steel tip and shank assembly to 1300°F (704°C) within 3 seconds for brazing with induction heating instead of torch brazing.
Material 0.1” (2.54mm) diameter steel tip & shank, 0.07” (1.78mm) diameter braze ring
Temperature 1300°F (704°C)
Frequency 800kHz
Equipment DW-UHF-4.5kW induction heating system, remote heat station containing one 1.2 microfarad capacitor.
Process A two turn helical coil is used to braze the dental parts. The braze ring is placed at the joint area of the steel tip and shank. Black flux is applied to the joint area. RF power is applied for 3 seconds to heat the parts to the established target temperature and the braze paste flows evenly and consistantly.
Results/Benefits Induction heating provides:
• Fast, accurate, repeatable heat
• Ability to heat very small areas within precise production tolerances
• Better joint quality, reduced oxidation
• Increased production rates and reduced labor costs
Aluminum Scrap Melting Recycling Induction Furnace
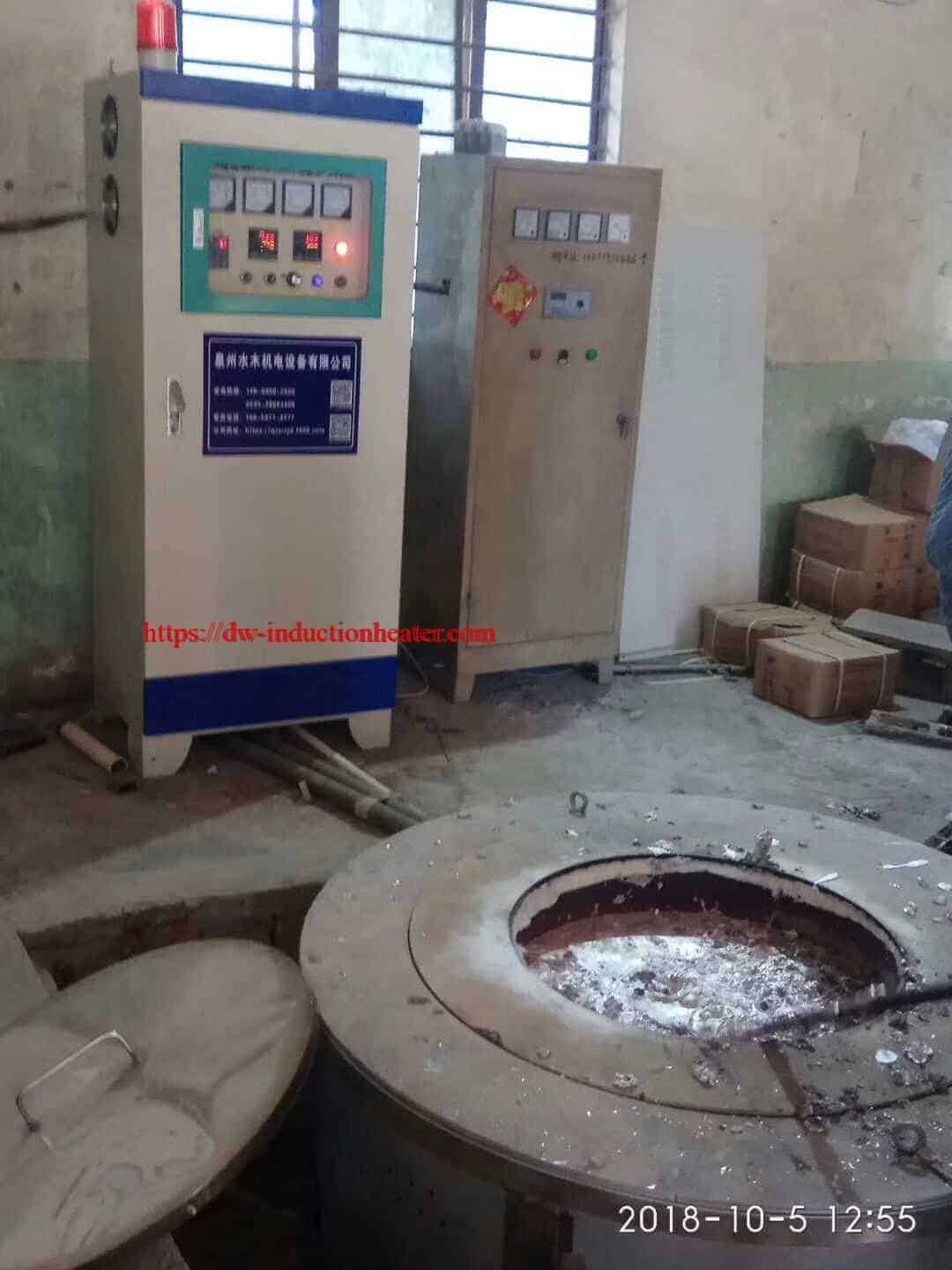
The top 200^1500kg Induction Aluminum Scrap Melting Recycling Induction Furnace for recycling and melting aluminum scraps,ingots,cans and dross material.
Operation Steps:- An Aluminum scraps/ingots/cans recycling furnace operator will place aluminum parts or aluminum ingot/scrap as a charge in the induction melting aluminum recycling furnace and start the furnace to begin the melting process. Adding more aluminum charge this process is advisable as molten aluminum transmits the heat better.
- When temperature of the aluminum reaches 1220.66°F it turns to liquid. Any residue from the coating and paint from the cans will float on the surface. This byproduct is called dross and can be skimmed by a steel ladle. This needs to cool before it can be disposed off safely.
- Next, the crucible (furnace) will pour out pure aluminum. Usually, Hydraulic tilting mechanism provided to pour large quantities of liquid metals.
- Finally, with care, the molten aluminum will be poured into mould to cool down and then slide out for use.
Type | Input Power | Melting Capacity | Max Temperature | ||
steel, stainless steel | copper, gold, silver (scrap, Slag) | aluminum, aluminum alloy, Aluminum scrap, Aluminum slag, pop can | 1800℃ | ||
SMJD-463 | 60 KW | 200 KG | 500 KG | 200 KG | |
SMJD-480 | 60 KW | 150 KG | 500 KG | 150 KG | |
SMJD-580 | 80 KW | 200 KG | 600 KG | 200 KG | |
SMJD-600 | 60 KW | 230 KG | 560 KG | 230 KG | |
SMJD-900 | 120 KW | 300 KG | 900 KG | 300 KG | |
SMJD-905 | 80 KW | 300 KG | 900 KG | 300 KG | |
SMJD-1250 | 80 KW | 400 KG | 1200 KG | 400 KG | |
SMJD-1250 | 120 KW | 450 KG | 1350 KG | 450 KG | |
SMJD-1500 | 120 KW | 500 KG | 1500 KG | 500 KG | |
SMJD-1550 | 120 KW | 520 KG | 1560 KG | 520 KG | |
SMJD-1700 | 160KW | 600 KG | 1700 KG | 600 KG | |
SMJD-2300 | 160KW | 800 KG | 2000 KG | 800 KG | |
SMJD-3100 | 200KW | 1200 KG | 3000 KG | 1200 KG |
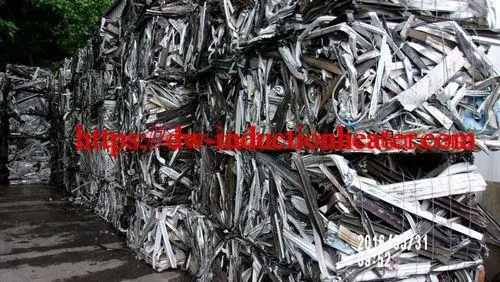
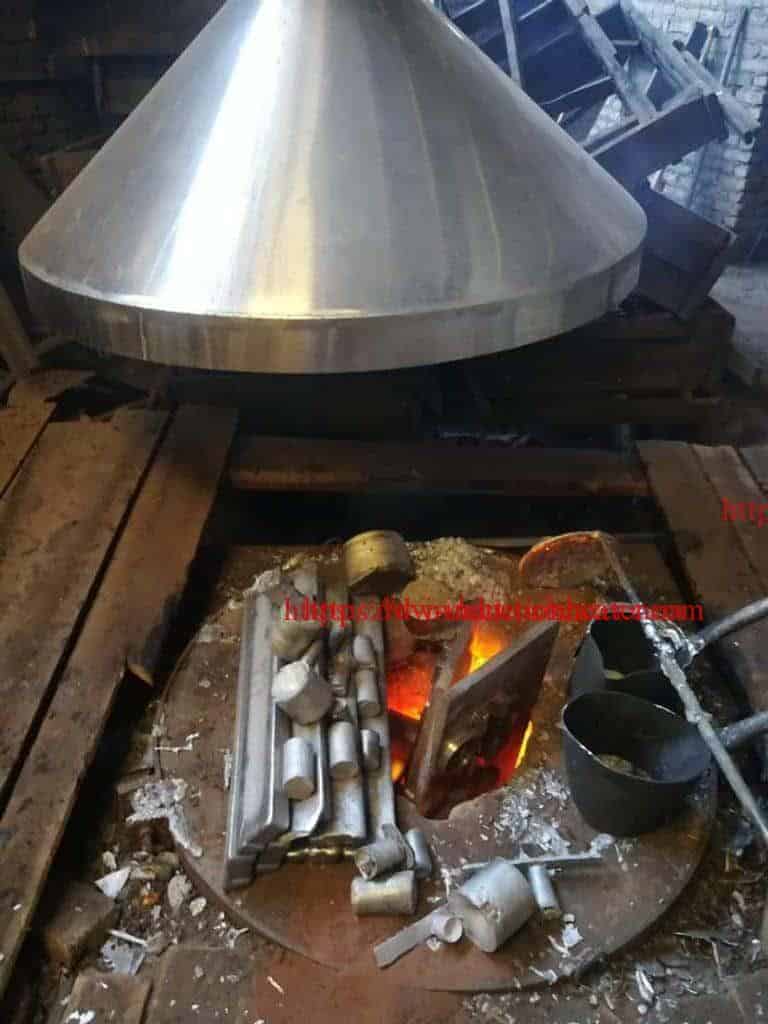
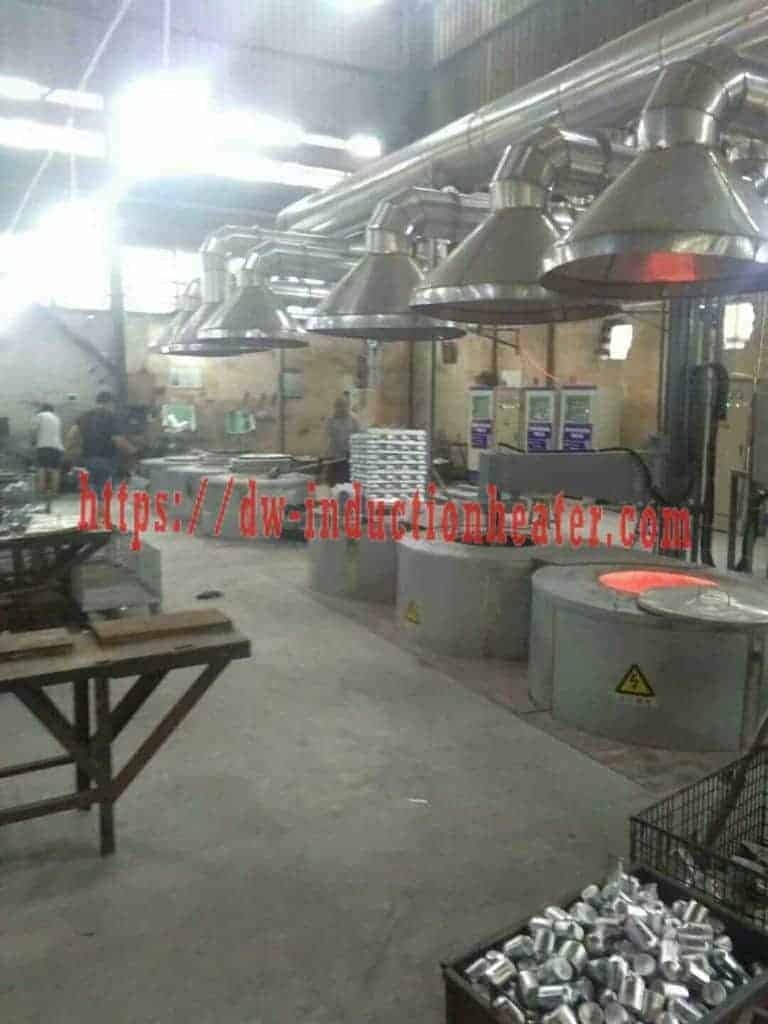
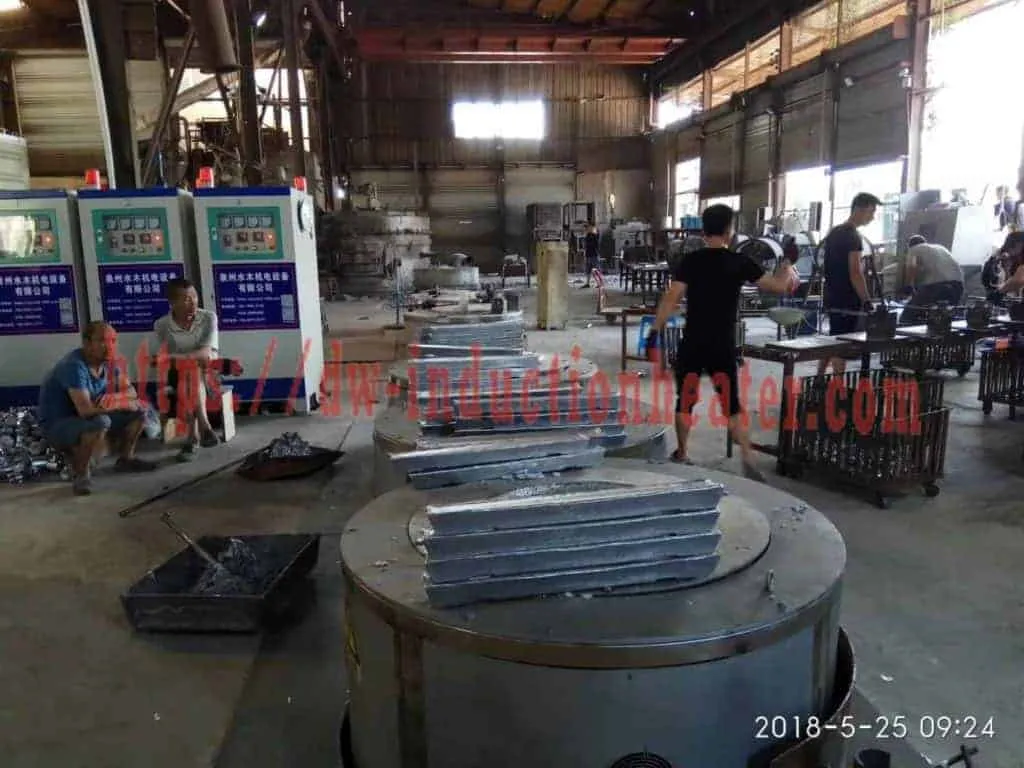
Induction Brazing Carbide Tipping on Cutting Steel Tool
Induction Brazing Carbide Tipping on Cutting Steel Tool Applications
Objective : A leading manufacturer of CBN and PCD cutting tools wants to increase their productivity by focusing heat on a very small area in order to decrease heat loss and improve a carbide tipping process.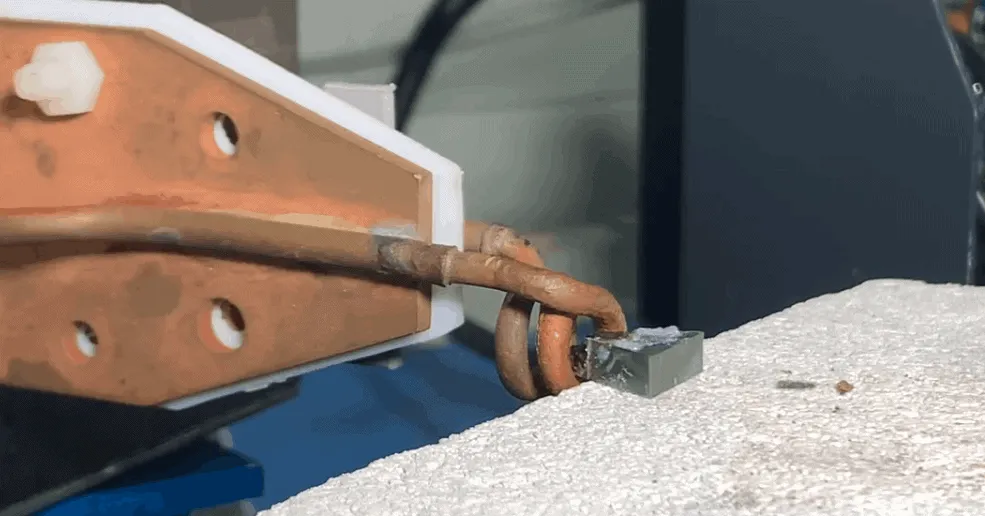
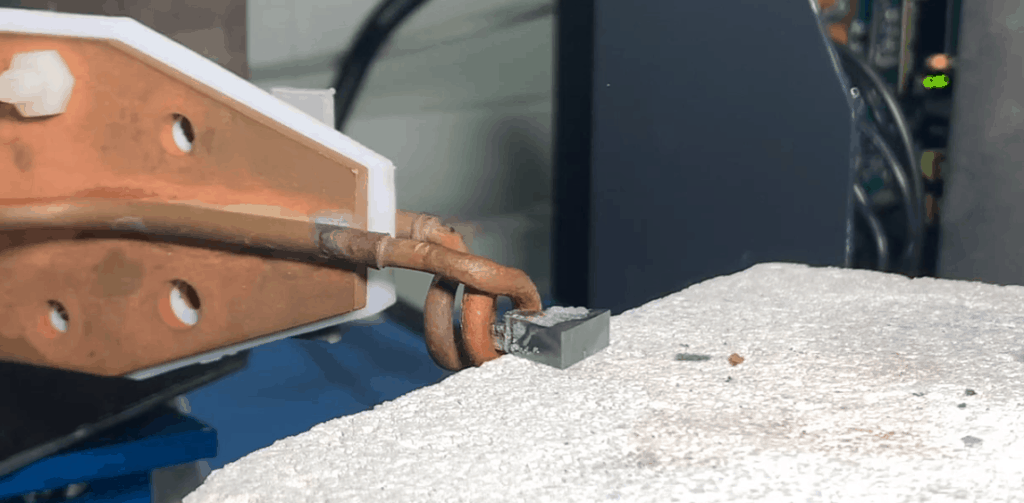
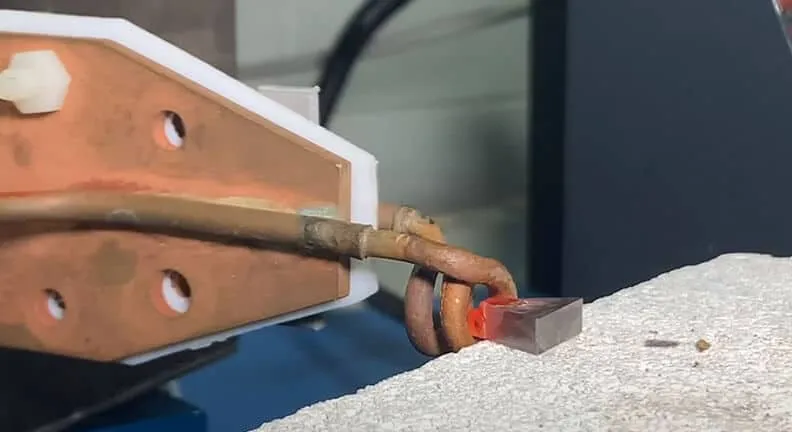
2023年8月27日星期日
induction hardening steel handheld stamps
induction hardening steel handheld stamps
Objective Induction hardening various size ends of handheld marking stamps. The area to be hardened is 3/4” (19mm) up the shank. Material : Steel stamps 1/4” (6.3mm), 3/8” (9.5mm), 1/2” (12.7mm) and 5/8” (15.8mm) square Temperature :1550 ºF (843 ºC) Frequency 99 kHz Equipment • DW-HF-45kW induction heating system, equipped with a remote workhead containing eight 1.0µF capacitors for a total of 2.0µF • An induction heating coil designed and developed specifically for this application.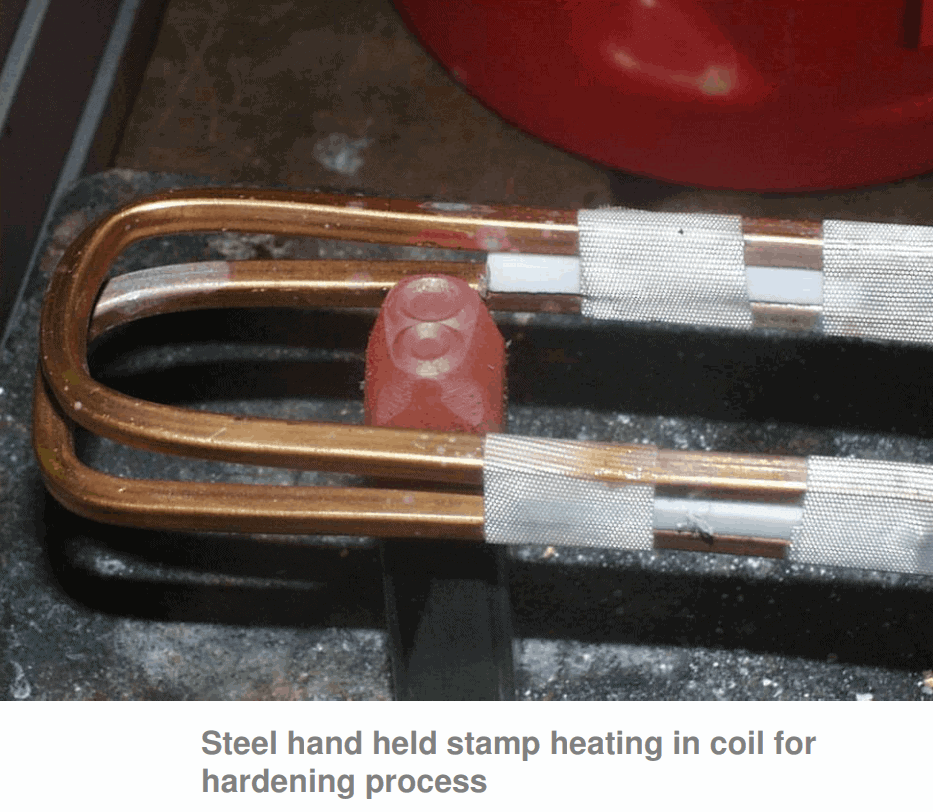
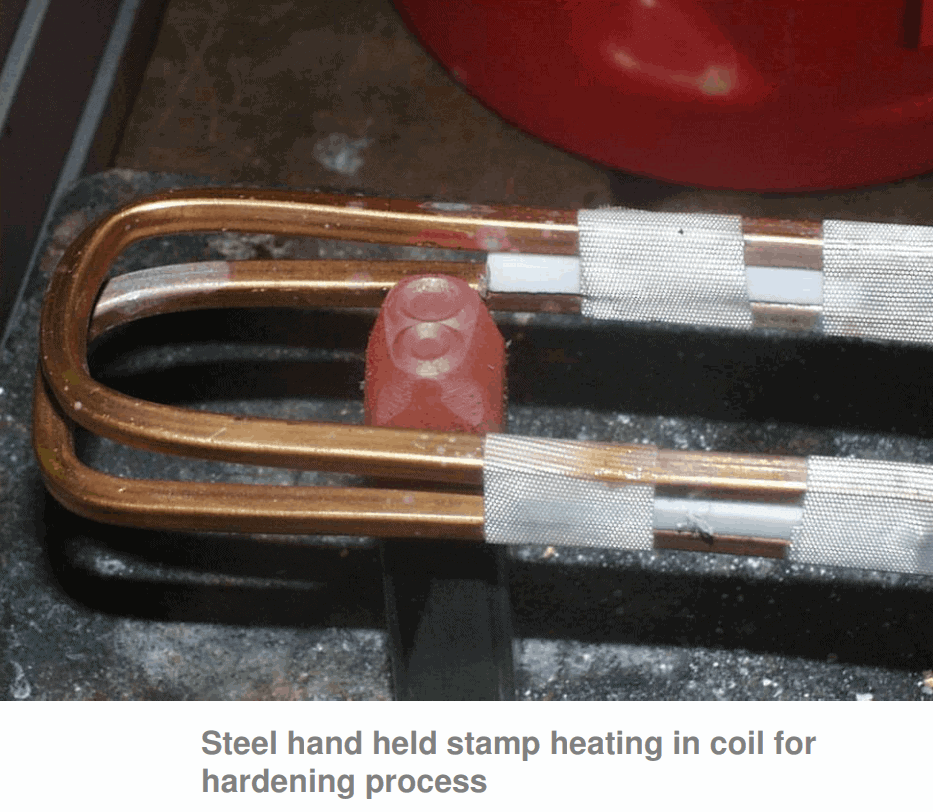
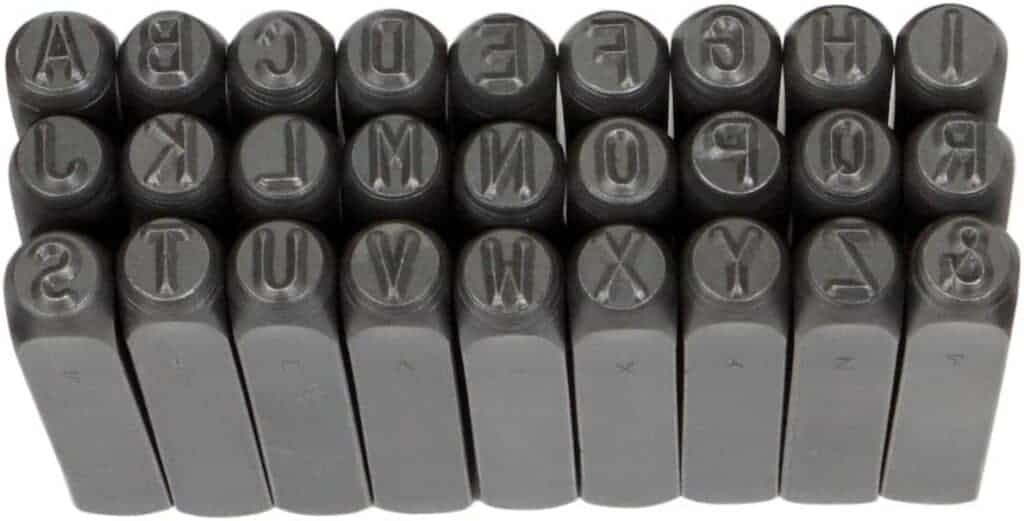
订阅:
博文 (Atom)
关注者
博客归档
-
▼
2023
(1696)
-
▼
八月
(129)
- Induction Brazing Brass Faucet
- Aluminum Billet Heating Furnace
- Induction Preheat Welding Systems
- Induction Brazing Stainless Steel
- Billet Heating Furnace with Induction Heating
- induction brazing steel carbide cap to shaft
- Induction Soldering Cable to Metallic Plate
- Induction Brazing Principle-Theory
- Induction Hardening Inner
- aluminum scrap melting induction furnace
- Induction Brazing Steel Tips
- Aluminum Scrap Melting Recycling Induction Furnace
- Induction Brazing Carbide Tipping on Cutting Steel...
- induction hardening steel handheld stamps
- Melting Aluminum Tilting Crucible Induction Furnace
- ultrasonic welding fabric machine for bonding nonw...
- Tilting Crucible Melting Induction Furnace
- Ultrasonic Plastic Welding Machine For Bonding The...
- Electromagnetic Induction Steam Generator
- Why Choose Induction Heating and what are its adva...
- Induction Hardening Surface Process
- How to design induction heating coil
- Induction annealing copper wires
- Induction Preheat Welding Systems
- Induction forging and induction hot forming
- Induction Soldering Wire To Aluminum Lug
- Magnetic Induction Heating Boiler
- portable ultrasonic mask welding machine for weldi...
- Induction Soldering Electrical Circuits
- Induction Heating Basic
- Induction Wire and Cable Heating
- Induction annealing stainless steel wire
- Induction Soldering Stainless Steel Tubes to Brass...
- Induction Heating Basic
- Induction Annealing Copper Tubes
- Brazing stainless steel with induction
- Induction Shrink Fitting Aluminum Pump Housing Part
- Induction Heating Steel Mold
- Soldering Steel To Brass With Induction Heater
- Induction Brazing Aluminum to Aluminum Tube
- Induction Brazing Copper Tube of Heat Exchanger
- How Induction Heating works?
- induction brazing stainless steel to steel
- Induction Brazing Carbide Onto Steel Part
- Small High Frequency Induction Melting Furnace
- Efficient and Versatile Induction Heating Coils fo...
- Small High Frequency Induction Melting Furnace
- handbook of induction heating eddy current
- Efficient and Versatile Induction Heating Coils fo...
- Efficient and Versatile Induction Heating Coils fo...
- Induction Soldering Brass Tube-Pipe
- RPR Induction Stripping-Induction Rust & Paint Coa...
- Heating Shrink Fitting Camshaft Gear
- Handheld Brazing Stainless Steel Tube
- induction brazing copper and brass rods
- High frequency induction brazing steel tube to ste...
- Handheld Induction Brazing Copper Tubing and Fitting
- induction brazing brass pipe to brass part
- Induction Brazing Copper Tube For Refrigeration
- Induction annealing stainless steel wire
- Brazing Stainless Steel To Copper With Induction
- Induction Brazing Aluminum Tube T Joints
- Induction Handheld Brazing Copper To Steel Tube
- Induction Soldering Process Video
- Induction Brazing Aluminum to Aluminum Tube
- induction brazing copper and brass rods
- High Frequency Brazing Stainless Steel Fittings
- Induction Hot Forming Steel Pipe
- Induction Brazing Heating Exchanger Copper Pipes
- Induction Brazing Steel Parts to Tungsten Carbide ...
- what is induction forging?
- High Frequency Induction Brazing Copper Wire
- Small High Frequency Induction Melting Furnace
- Induction Soldering Copper Wire Connectors
- Induction inline wire heating process
- Induction Soldering Brass Assembly
- induction heating stainless steel wire cable
- Brazing Carbide To Steel With Induction
- Induction Hardening Steel Part with High Frequency...
- Induction Brazing Carbide To Steel
- high frequency induction hardening camshafts process
- Aluminium Scraps Recycling Melting and Process
- Shrink Fittting Part Removal application with Indu...
- Why Choose Induction Heating and what are its adva...
- induction soldering copper tubing to brass valves
- Induction Soldering Wire To Aluminum Lug
- Induction Soldering Brass Corner Joint
- Induction Shrink Fit Aluminum Shaft
- Induction Soldering Copper Wire Connectors
- high frequency induction soldering wire to connector
- Brazing Automotive Parts With Induction
- Induction Soldering Copper Pipes to PCB Board
- Brazing Golf Ball With Induction
- Induction Soldering Stainless Steel Tubes to Brass...
- induction brazing steel tube to copper tube
- Brazing Aluminum to Copper Tubes with Induction
- Induction Soldering Wire To Aluminum Lug
- Brazing Joining Copper Connectors With Induction
- high frequency induction soldering wire to connector
- Induction Heating Steel Mold
-
▼
八月
(129)
我的简介

- HLQ induction heating machine
- HLQ induction heating machine manufacturer provides the service of induction brazing,melting,hot forming,hardening surface,annealing,shrink fitting,PWHT,etc.