Induction Crankshaft Hardening: The Ultimate Guide to Durable Engines
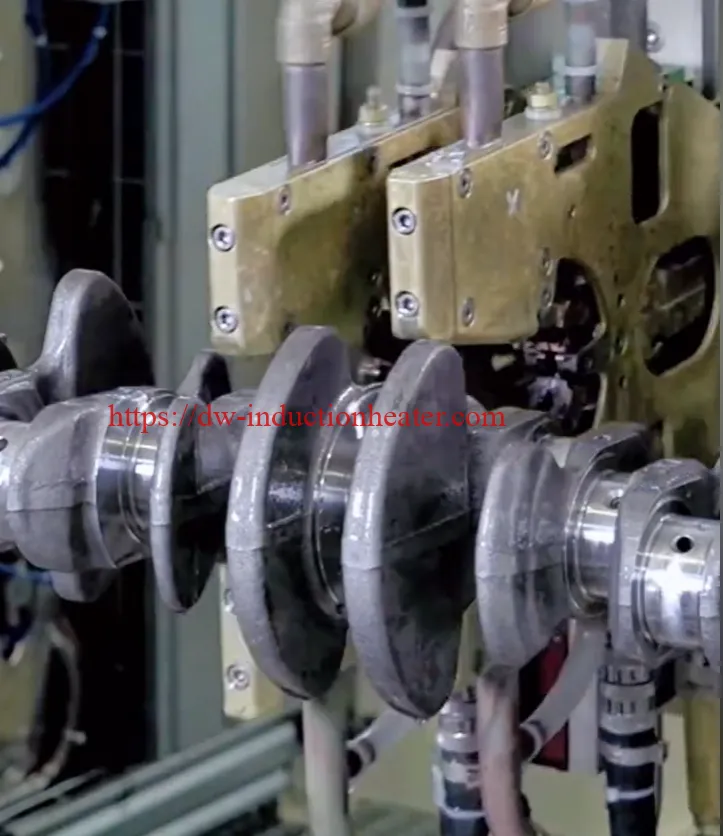
Crankshafts are the heart of internal combustion engines. They transfer motion from pistons to the drive shaft, powering your vehicle. As engines are subject to extreme stresses, ensuring the durability of the crankshaft is vital to the longevity of the engine.
Induction crankshaft hardening is a heat treatment process that can produce superior durability and strength in crankshafts, making them a popular choice among engine manufacturers. In this guide, we'll explain everything you need to know about induction crankshaft hardening and its benefits.
What is Induction Crankshaft Hardening?
Induction crankshaft hardening is a process used in the manufacturing of engines that can significantly improve engine performance. The process involves heating the crankshaft to a high temperature and then quenching it in a controlled manner. The result is a crankshaft that has a hard outer layer, which improves wear resistance and reduces the risk of damage to the engine. This process is typically used in racing engines, where reliability and performance are essential. Induction crankshaft hardening is also becoming more common in high-performance street engines, due to the significant benefits it can provide. The process is performed using a specialized induction heating system, which applies heat to the crankshaft in a controlled and precise manner. With the increased durability and performance benefits that come with induction crankshaft hardening, it's no wonder that it is becoming a popular choice for engine manufacturers and high-performance engine builders alike.
Benefits of Induction Crankshaft Hardening
Induction crankshaft hardening is a process that can bring numerous benefits to engine performance. The primary benefit of induction crankshaft hardening is that it greatly increases the durability and strength of the crankshaft. Induction crankshaft hardening offers several benefits, including:
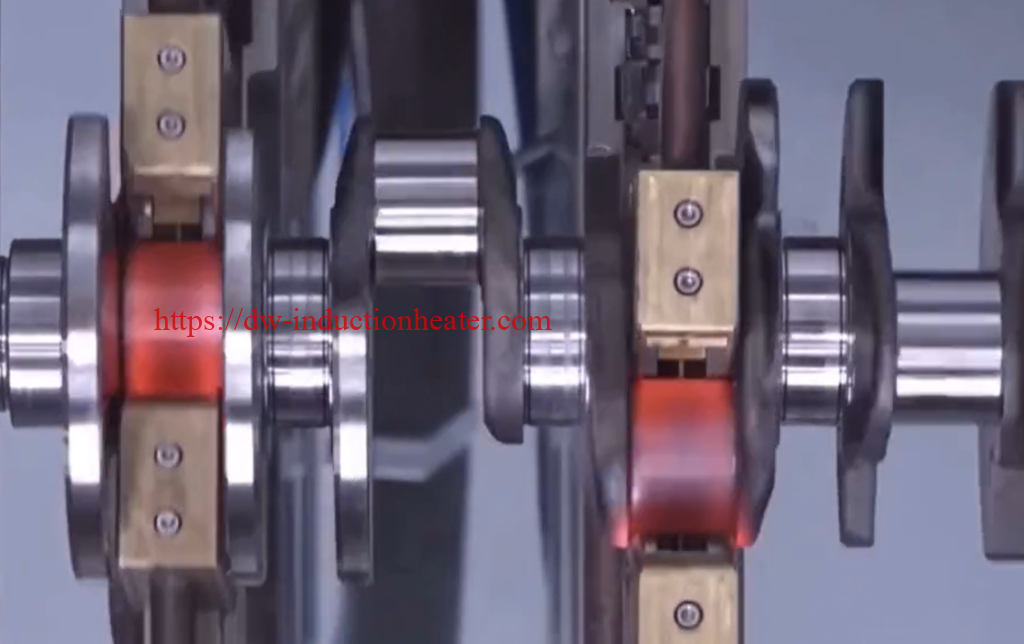
1. Increased durability and wear resistance: Induction hardening produces a hardened shell on the surface layer of the crankshaft. The hardened shell can resist wear and scratches, providing long-lasting durability.
2. Improved fatigue strength: The hardened layer makes the crankshaft more resistant to fatigue, which can help prevent engine failures.
3. Better performance: Induction hardening improves the surface quality of the crankshaft, reducing friction and increasing engine performance.
4. Cost-effective: Induction hardening is a cost-effective heat treatment process compared to other methods, saving manufacturers money while producing high-quality crankshafts.
This is important because the crankshaft is the backbone of the engine, and it is responsible for transferring the power from the engine to the drive train. A stronger crankshaft means that the engine can handle more power and torque, which can result in better performance. Instead of using more expensive materials to create stronger crankshafts, induction hardening can be used to strengthen existing crankshafts. This can reduce the cost of manufacturing engines, making them more accessible to consumers. Overall, the benefits of induction crankshaft hardening are clear. By increasing durability, wear resistance, efficiency, and cost-effectiveness, this process can greatly enhance engine performance and longevity.
How Induction Crankshaft Hardening Can Boost Engine Performance
Induction crankshaft hardening is a process used in the automotive industry to increase the performance of engines. This process involves heating the crankshaft to a high temperature and then rapidly cooling it to create a hardened surface.
Induction hardening is a popular method because it is a cost-effective way of hardening crankshafts without the need for additional materials or treatments. When an engine is running, the crankshaft is subjected to a lot of stress and pressure. As a result, the crankshaft can wear down over time, leading to reduced engine performance. By hardening the crankshaft, the engine's performance can be improved. A hardened crankshaft can withstand more stress and pressure, allowing it to perform better. Induction crankshaft hardening can also improve the engine's fuel efficiency.
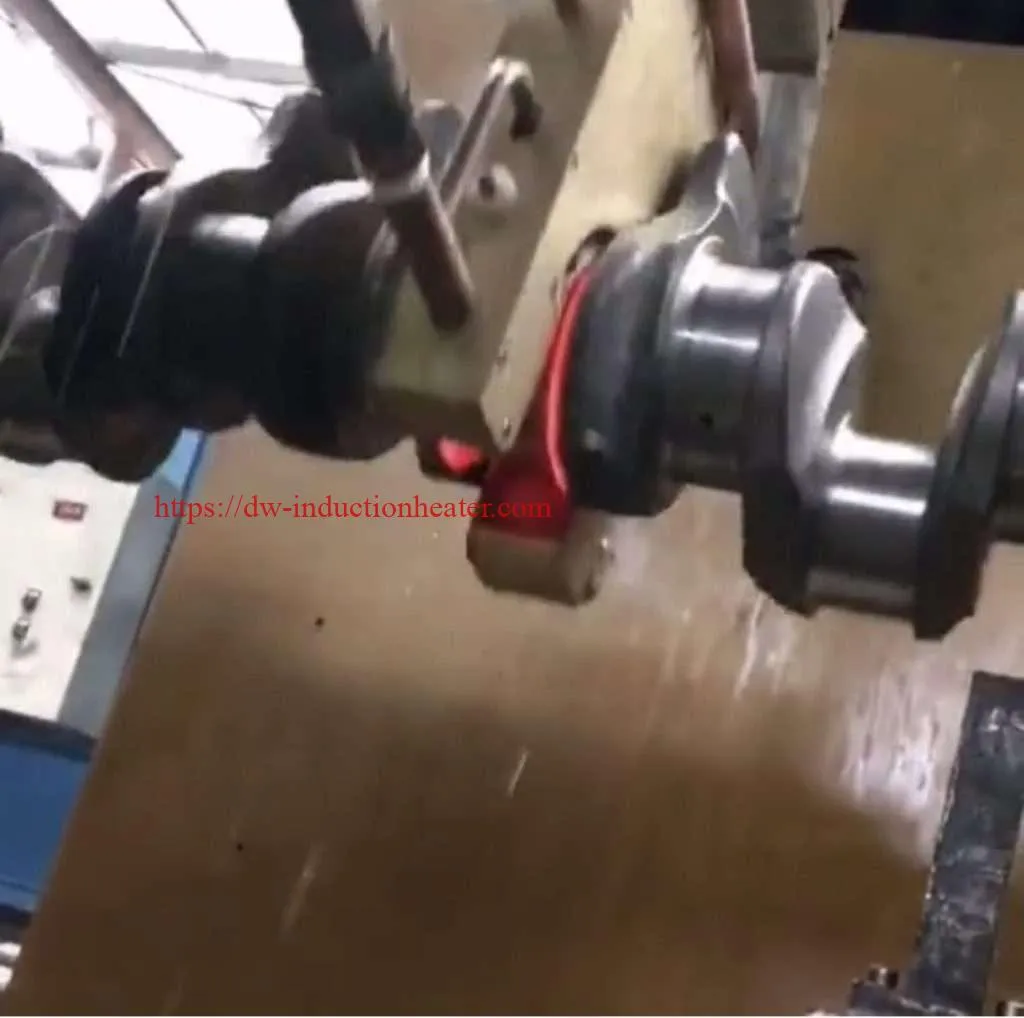
A hardened crankshaft reduces the amount of friction in the engine, which means that the engine can run more efficiently. This is because the engine doesn't have to work as hard to produce the same amount of power. Another benefit of induction crankshaft hardening is that it can increase the lifespan of the engine. As the crankshaft is one of the most critical components in an engine, hardening it can help to prevent premature failure. This means that the engine can last longer, and the vehicle owner can save money on repairs and replacements. Overall, induction crankshaft hardening is an excellent way to boost engine performance, improve fuel efficiency, and increase the lifespan of the engine. If you are looking for a way to get the most out of your vehicle, consider having your engine's crankshaft hardened through the process of induction hardening.
Why Choose Induction Crankshaft Hardening?
Induction crankshaft hardening is an ideal method for ensuring the durability of crankshafts, especially in high-performance engines. Induction hardening can produce high-quality crankshafts with precise depth and consistent hardness throughout the surface layer. Moreover, the heat input can be controlled easily, allowing manufacturers to adjust the hardening process according to the specific requirements of the crankshaft.
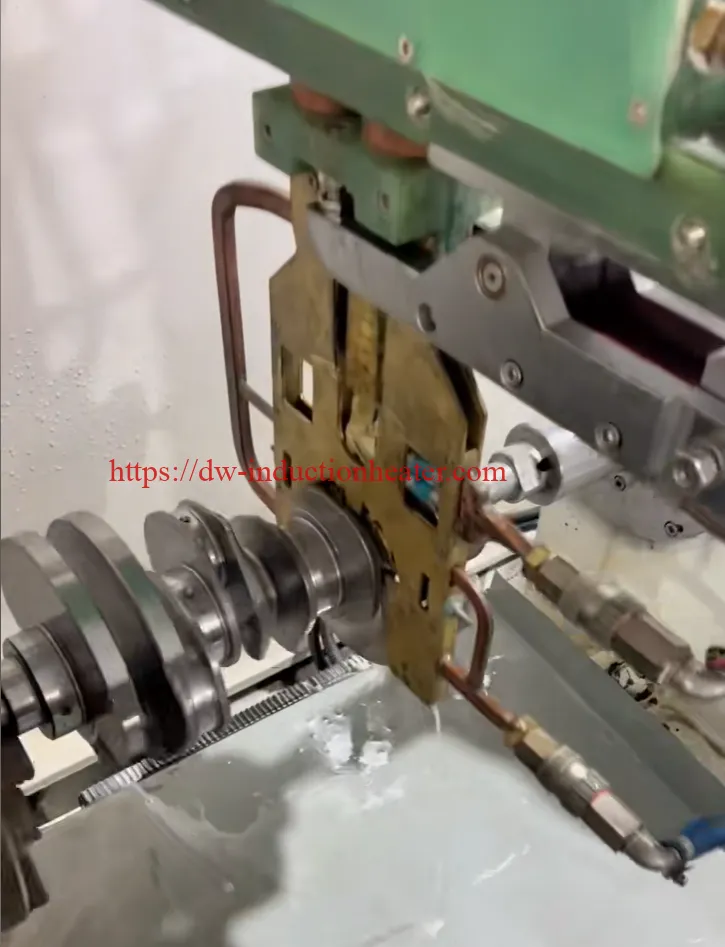
Induction crankshaft hardening is also eco-friendly. The process requires less energy, reducing the carbon footprint and improving sustainability.
Conclusion.
induction crankshaft hardening is a process that can significantly improve the performance of your engine. It allows for stronger, more durable crankshafts that can handle higher levels of stress and pressure. With the ability to withstand higher RPMs and temperatures, your engine can deliver more power and better performance. Additionally, the induction hardening process is environmentally friendly and cost-effective, making it an ideal choice for those looking to upgrade their engines without breaking the bank. So if you're looking to take your engine's performance to the next level, consider incorporating induction crankshaft hardening into your engine rebuilding process. It can be a game-changer for your vehicle's performance and longevity.