2023年3月31日星期五
What Is Induction Heating Coil&Inductor?
induction hardening process
High Frequency Induction Hardening Process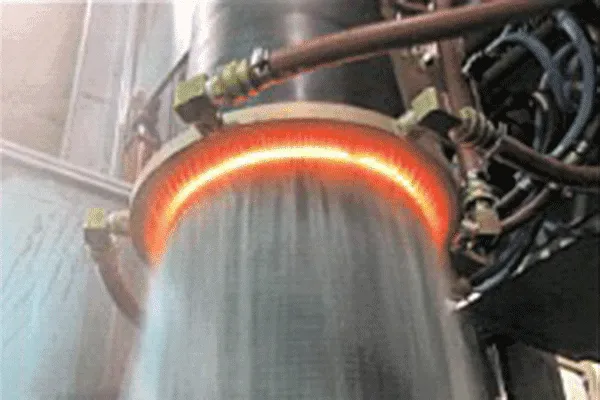
Induction hardening is used in particular for the hardening/quenching of bearing surfaces and shafts as well as intricately shaped parts where only a specific area needs to be heated.
Through the choice of the operating frequency of the induction heating system, the resulting depth of penetration is defined.
Additionally, it can be decided if the area is to be hardened in the air, with water or with a special hardening emulsion. Depending on the cooling medium, different degrees of hardness are achieved.
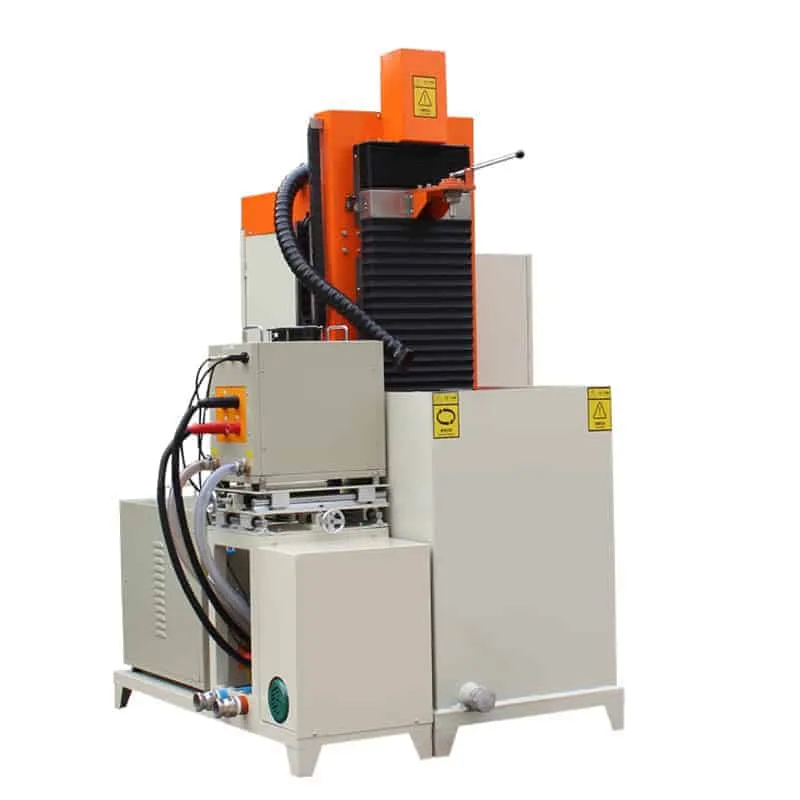
- Suitable for hardening and tempering of various workpieces, such as induction hardening of shafts, gears, guide rails, discs, pins, and other parts;
- It has the functions of continuous hardening, simultaneous hardening, segmented continuous hardening, and segmented simultaneous hardening;
- Use numerical control system or PLC and frequency conversion speed regulation system to realize workpiece positioning and scanning, and connect PLC and induction heating power supply to realize fully automated production.
- Vertical (hardening of shaft parts) + horizontal (hardening of gear ring parts)
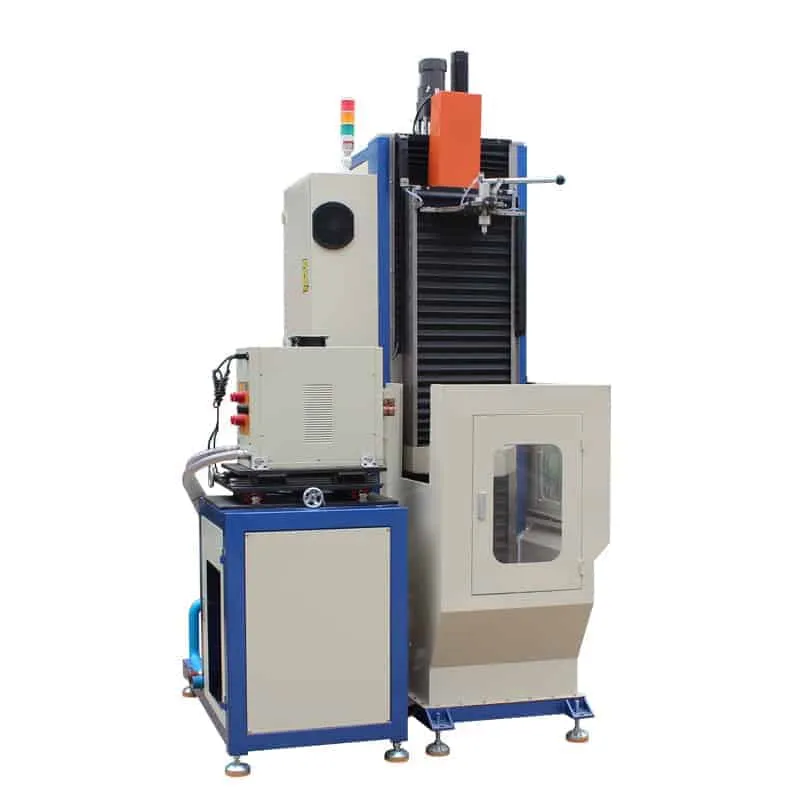
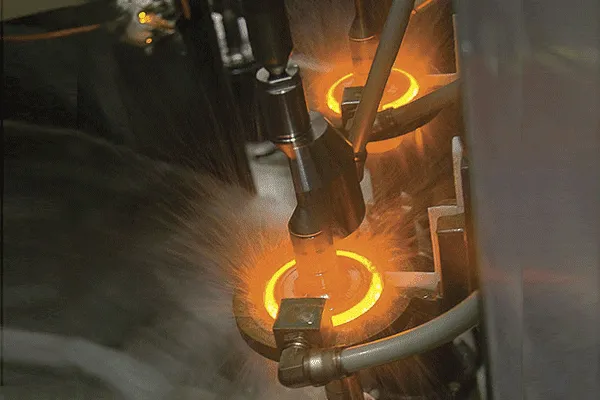
- This series hardening machine tool uses numberic control technology, has continuous, simultaneous, sectionally-continuous and sectionally-silultaneous quenching functions, it is mainly used for induction quenching of shafts, discs, pins and gears, and featured by high quenching precision. hardening machine tool used by connecting with medium frequency, superaudio frequency, high frequency and ultrahigh frequency induction heating machine.
- CNC quenching/hardening machine tool feature:
- CNC system:The high-frequency quenching machine CNC system can compile and store a variety of quenching process programs according to different workpiece requirements.
- HMI: programming type and human machine interface displays in English and Chinese.
- Control adjust: it can control the heating power to start, stop, parts heating and cooling time, rotation speed and movement speed.
- Lathe: adopt welded structure with good rust-proof functions.
- Top adjustment parts: adopt electric adjustment, to realize clamping of different length work piece.
- Work table system: adopt ball screw and servo motor to drive, driving light, high guide precision and accurate positioning.
- Main shaft rotation system: adopt variable frequency regulating to realize parts rotation speed continuous adjusted.
- Electric control part: the machine tool has power-loosing protection function, has high safety and reliability.
- Frame: made by thick steel plates, with window and sliding doors, prevent water splash, easy to load parts and monitor hardening process.
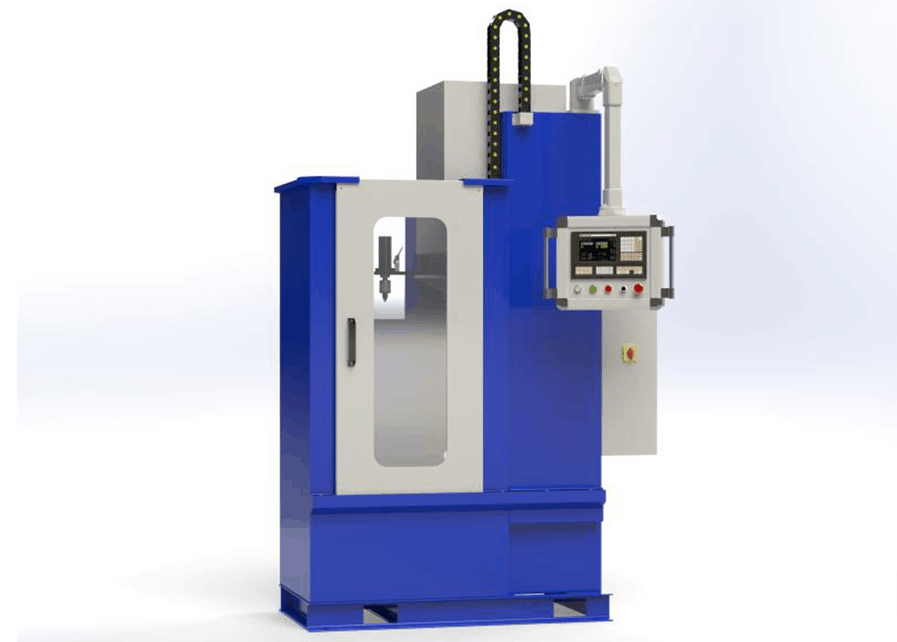
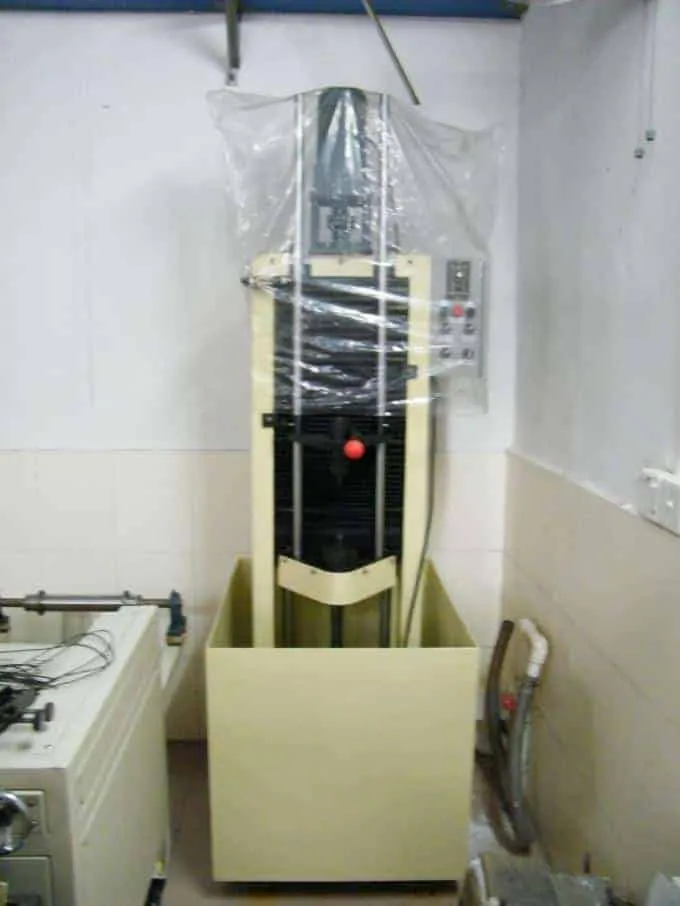
Model | SK-500 | SK-1000 | SK-1200 | SK-1500 |
Max heating length(mm) | 500 | 1000 | 1200 | 1500 |
Max heating diameter(mm) | 500 | 500 | 600 | 600 |
Max holding length(mm) | 600 | 1100 | 1300 | 1600 |
Max weight of workpiece(Kg) | 100 | 100 | 100 | 100 |
Workpiece rotation speed(r/min) | 0-300 | 0-300 | 0-300 | 0-300 |
workpiece moving speed(mm/min) | 6-3000 | 6-3000 | 6-3000 | 6-3000 |
Cooling method | Hydrojet cooling | Hydrojet cooling | Hydrojet cooling | Hydrojet cooling |
Input voltage | 3P 380V 50Hz | 3P 380V 50Hz | 3P 380V 50Hz | 3P 380V 50Hz |
Motor power | 1.1KW | 1.1KW | 1.2KW | 1.5KW |
Dimension LxWxH (mm) | 1600 x800 x2000 | 1600 x800 x2400 | 1900 x900 x2900 | 1900 x900 x3200 |
weight(Kg) | 800 | 900 | 1100 | 1200 |
Model | SK-2000 | SK-2500 | SK-3000 | SK-4000 |
Max heating length(mm) | 2000 | 2500 | 3000 | 4000 |
Max heating diameter(mm) | 600 | 600 | 600 | 600 |
Max holding length(mm) | 2000 | 2500 | 3000 | 4000 |
Max weight of workpiece(Kg) | 800 | 1000 | 1200 | 1500 |
workpiece rotation speed(r/min) | 0-300 | 0-300 | 0-300 | 0-300 |
workpiece moving speed(mm/min) | 6-3000 | 6-3000 | 6-3000 | 6-3000 |
Cooling method | Hydrojet cooling | Hydrojet cooling | Hydrojet cooling | Hydrojet cooling |
Input voltage | 3P 380V 50Hz | 3P 380V 50Hz | 3P 380V 50Hz | 3P 380V 50Hz |
Motor power | 2KW | 2.2KW | 2.5KW | 3KW |
Dimension LxWxH (mm) | 1900 x900 x2400 | 1900 x900 x2900 | 1900 x900 x3400 | 1900 x900 x4300 |
weight(Kg) | 1200 | 1300 | 1400 | 1500 |
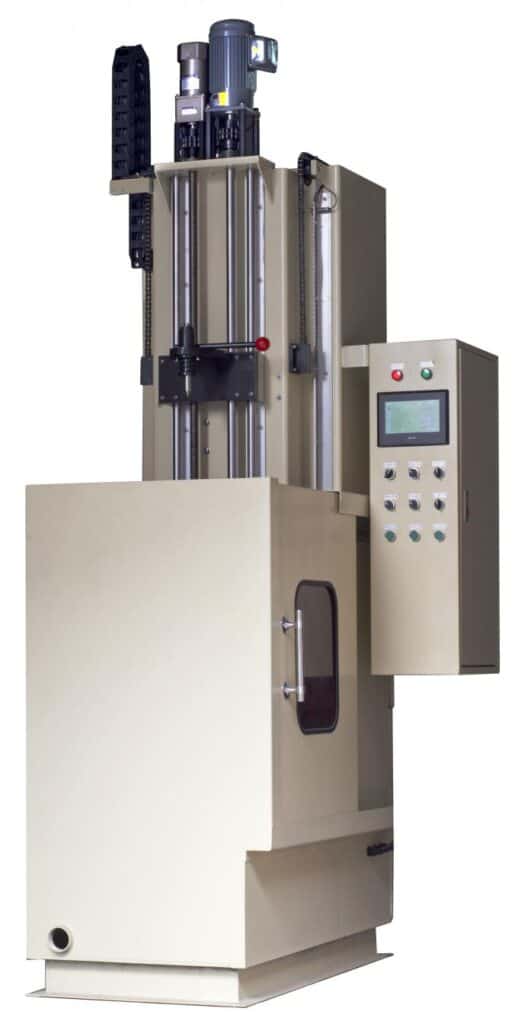
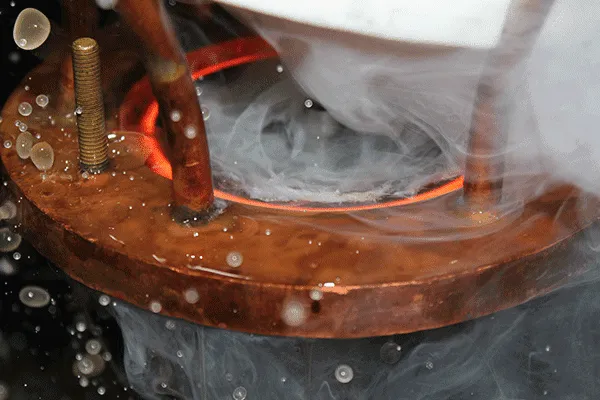

induction brazing and soldering technology
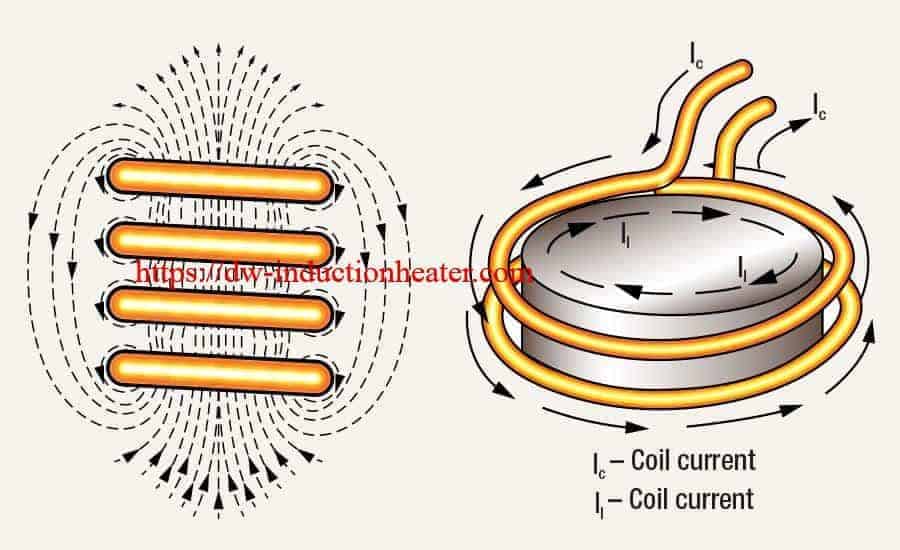
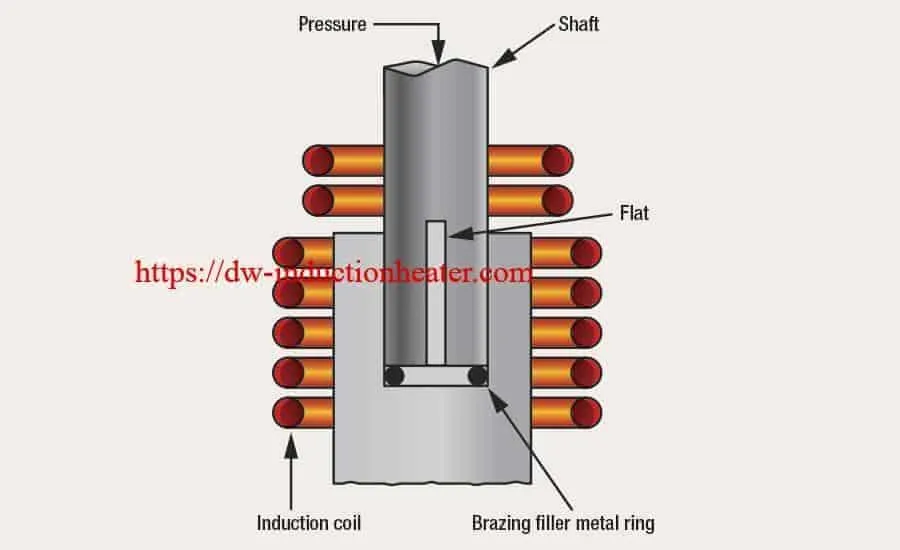
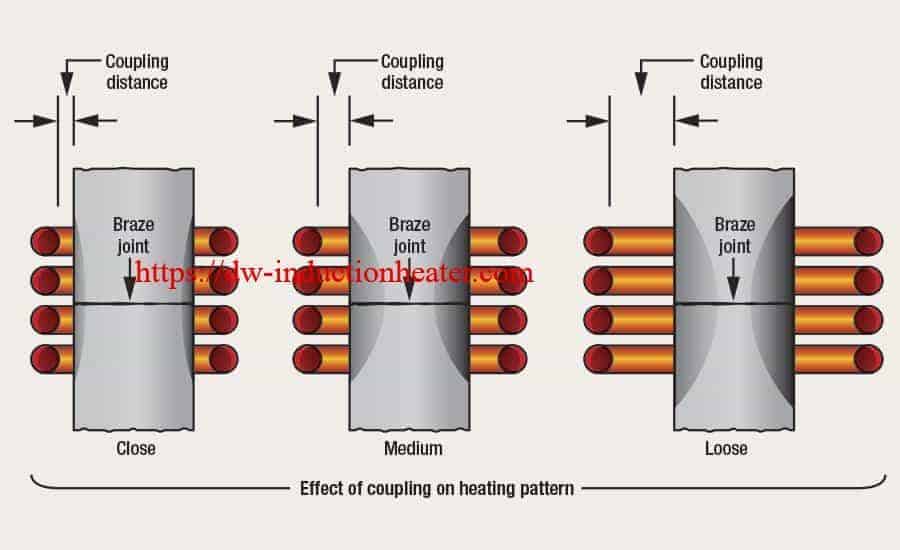


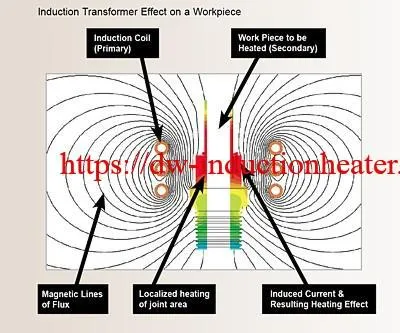
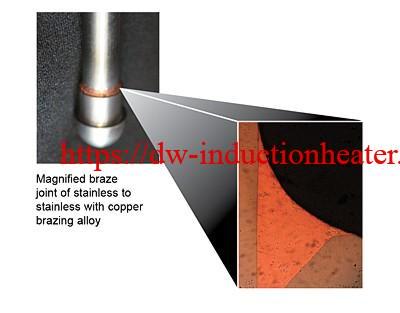

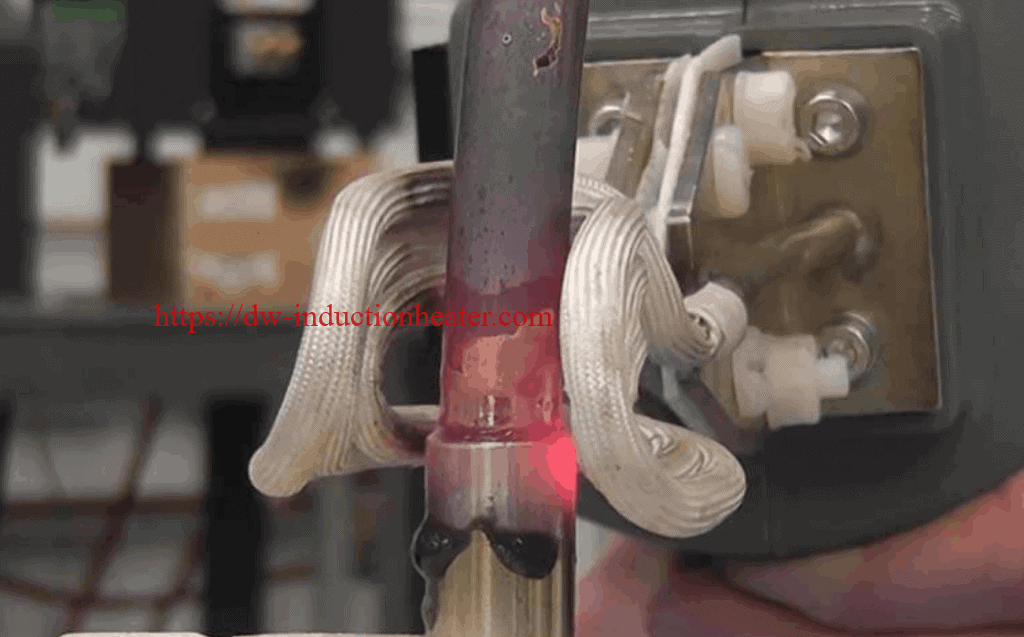
ultrasonic welding fabric machine for bonding nonwoven fabric
ultrasonic welding fabric machine| ultrasonic nonwoven fabric welder | ultra sonic nonwoven fabric welding equipment with Automatic Frequency Chasing
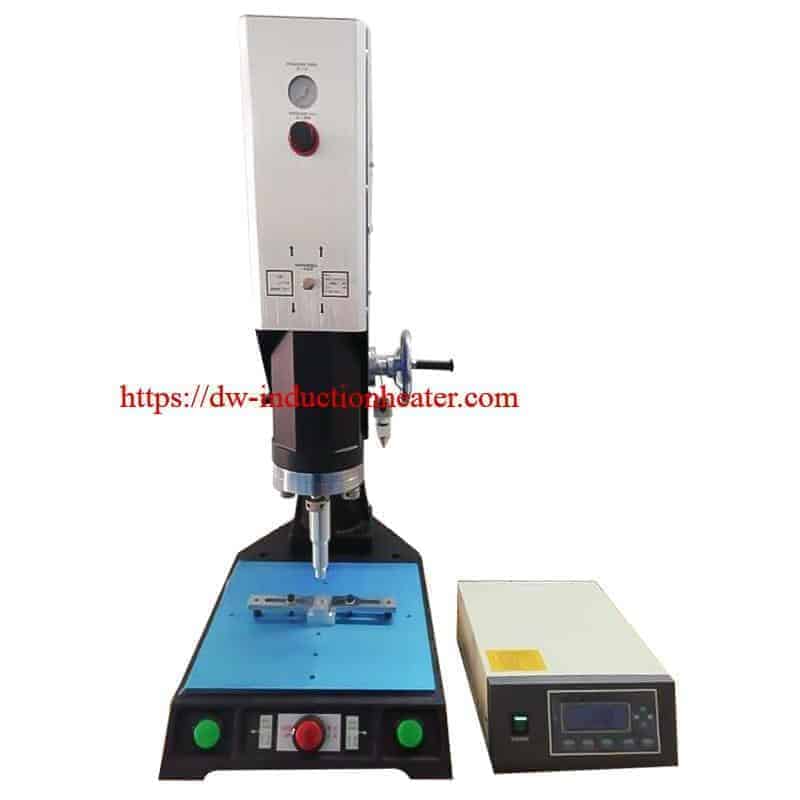
Main Functions:
1.According to the product requirements,drive mode can choose pneumatic, hydraulic or servo motor drive. 2. The welding temperature, heating time, cooling time, welding depth, pressure, transit time are adjustable parameters,etc 3.In accordance with the requirements of welding procedure, can choose semi-automatic or fully automatic mode; 4.Should be a variety of materials, can adjust the welding procedure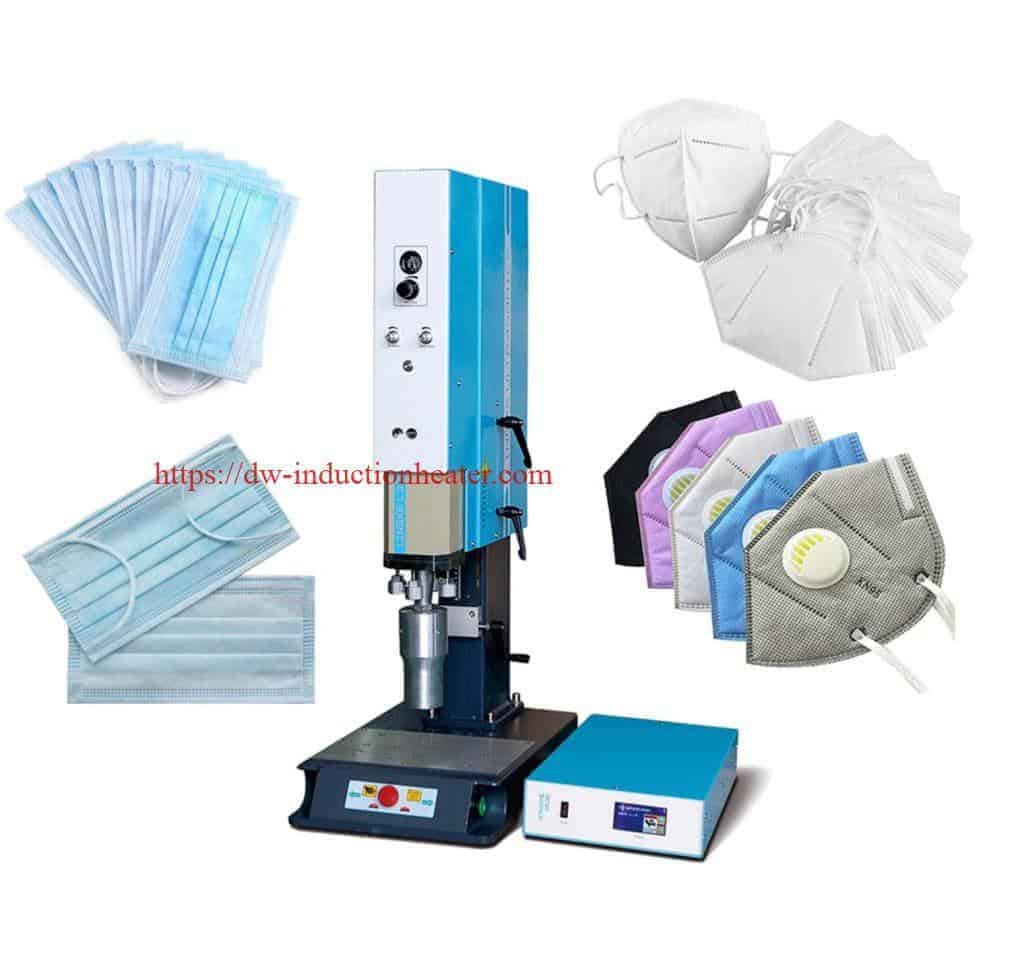
Model | 2015B | 2018B | 1522A | 1526A |
Frequency | 20KHZ | 15KHZ | ||
Power | 1500W | 1800W | 2200W | 2600W |
Max Stroke | 75-100mm | |||
Welding Time | 0.01-9.99sec | |||
Welding Area | φ100mm | φ120mm | φ150mm | φ200mm |
Dimensions | 450*750*1100mm | |||
Weight | 90KG |
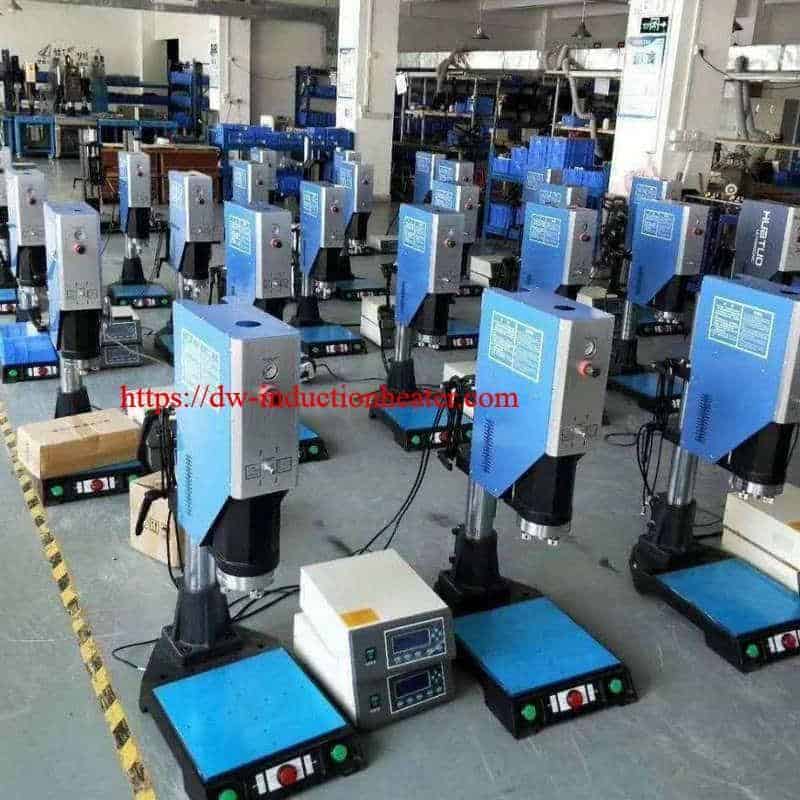
Application Industry | Application Products |
Automotive: | the car door welded baffle welding, automobile, car mats welding, automotive bumper repair welding, cotton insulation doors, seat wipers, engine cover, radiator cap spot, etc |
Consumer Products: | daily necessities, stationery, filter, folder and shell, pen stand, cosmetics box shell, the end of the toothpaste tube seal, mirror, insulated cup, lighter. |
Electronics: | recording, audio tape boxes and core wheel, disk enclosure, the board of mobile phone batteries and rectifier transformers, switches and sockets, remote control, |
Home appliances: | Balance ring, electronic clock, electric trumpeter hair dryer, steam iron water tank, |
Toy: | plastic toys, water guns, aquatic life video game, children dolls, plastic gifts, etc |
Film & Fabric: | Filters, Shower Curtains, Biodegradable Bag, Non-Woven Face Mark,..etc. |
Packaging: | Plastic pallet, Corrugated tray, hollow crate welding, zip lock welded, etc |
Medical: | Surgical Instruments,Testing Equipment,filters,I-V units,insulated trays..etc. |
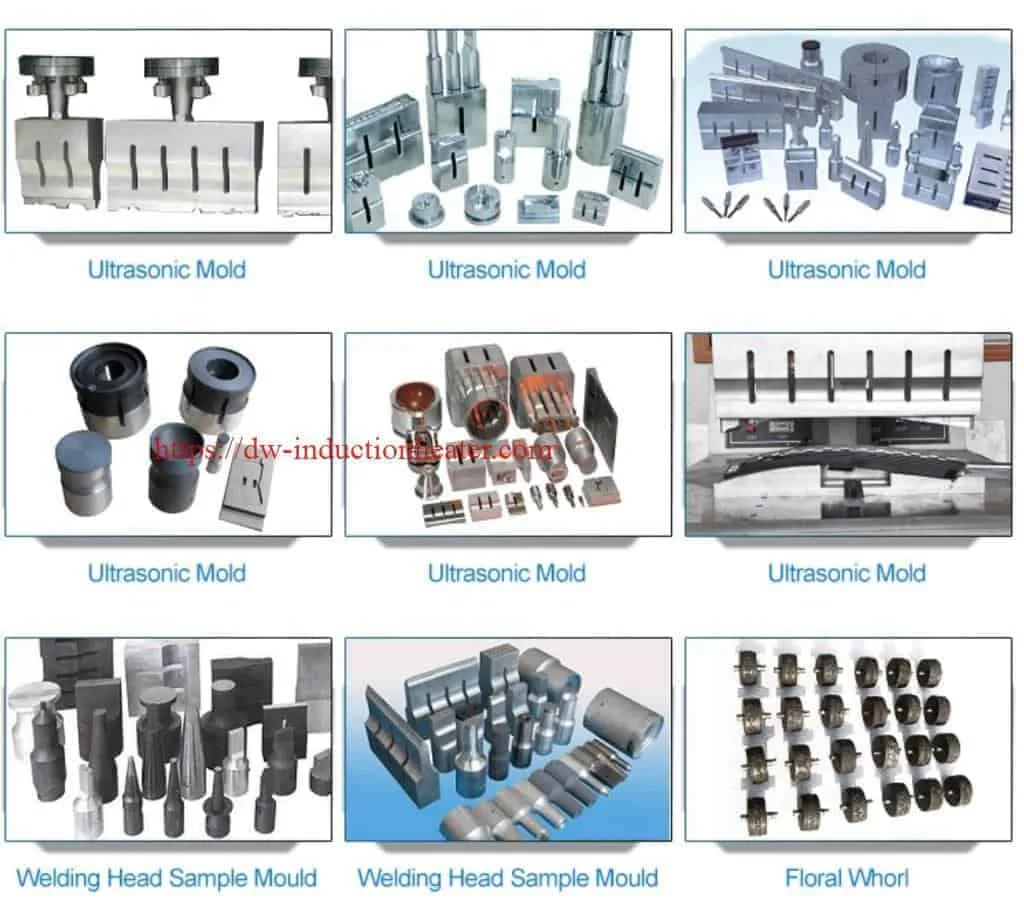
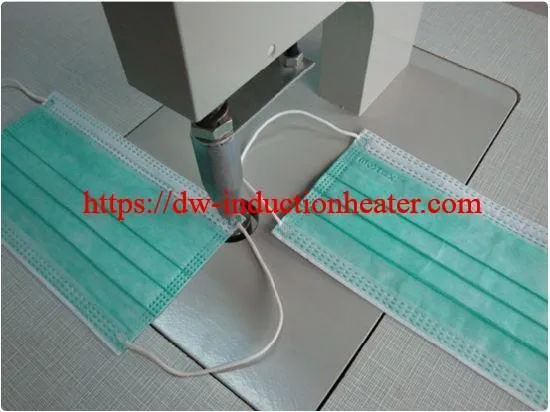
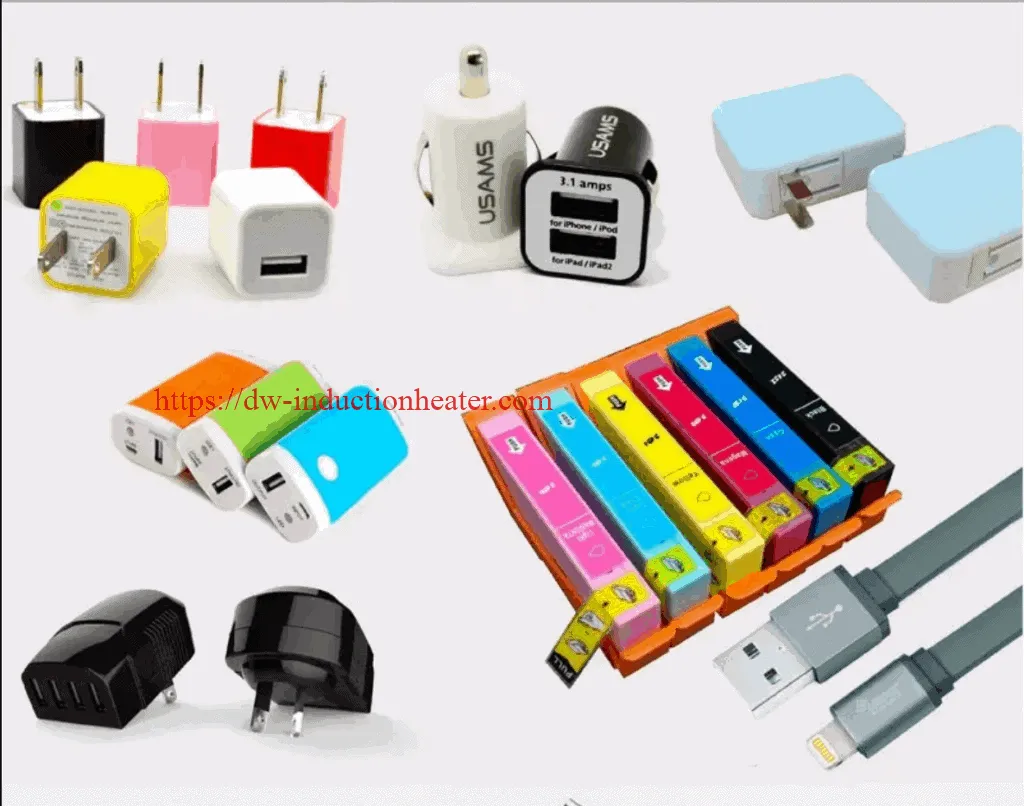

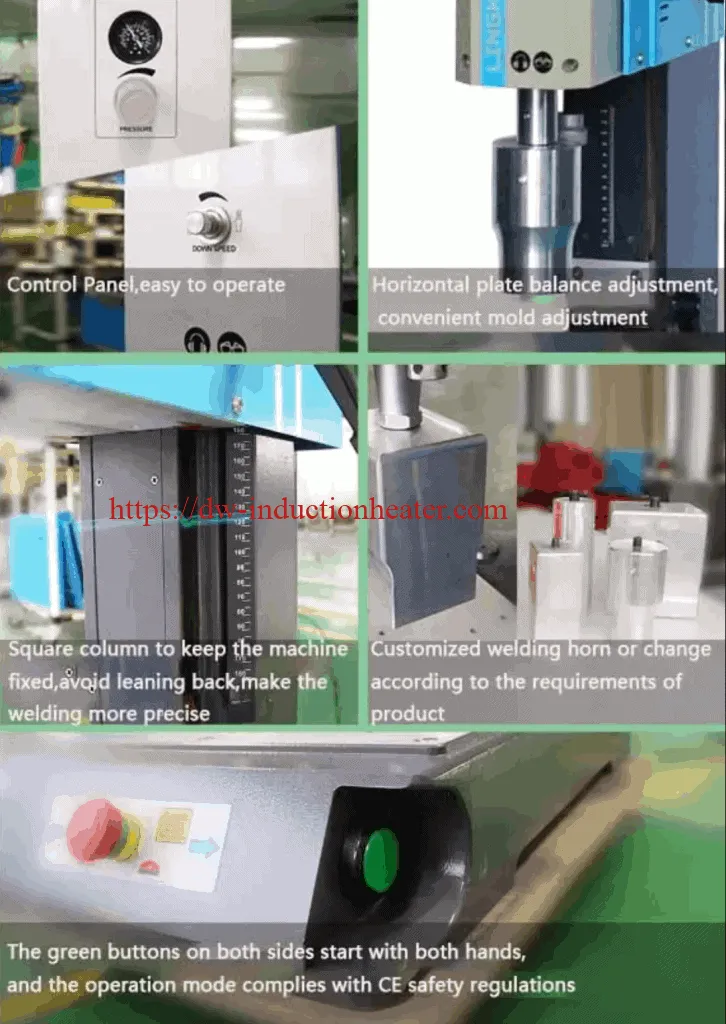

Shrink Fit Steel Gear onto Shaft
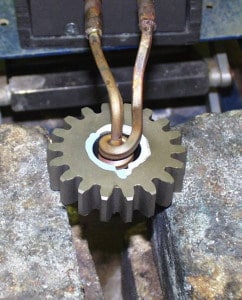
Induction Soldering Brass To Copper
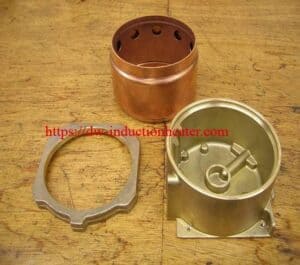

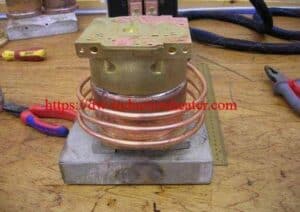
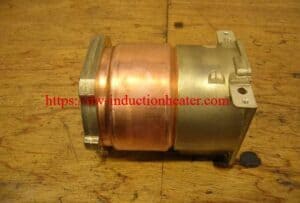
2023年3月30日星期四
Aluminum Can Recycling Furnace with induction heating
The top 200^1200kg Induction Heating Aluminuim Can Recycling Furnace for recycling and melting aluminum scraps,ingots,cans and dross material.
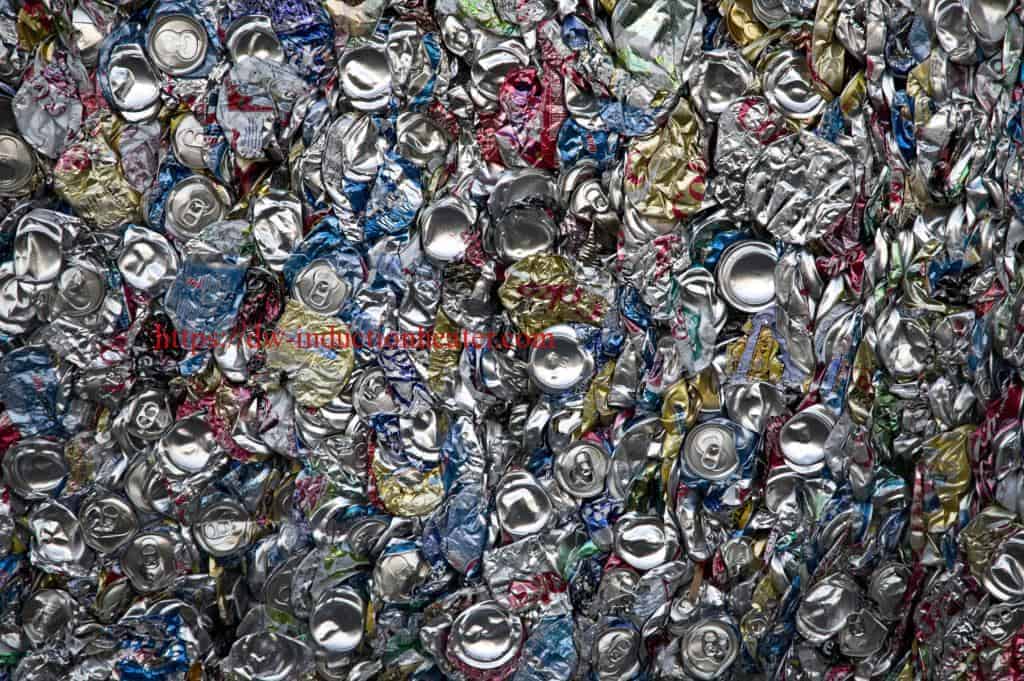
- An Induction Aluminum scraps/ingots/cans recycling furnace operator will place aluminum parts or aluminum ingot/scrap as a charge in the induction melting aluminum recycling furnace and start the furnace to begin the melting process. Adding more aluminum charge this process is advisable as molten aluminum transmits the heat better.
- When temperature of the aluminum reaches 1220.66°F it turns to liquid. Any residue from the coating and paint from the cans will float on the surface. This byproduct is called dross and can be skimmed by a steel ladle. This needs to cool before it can be disposed off safely.
- Next, the crucible (furnace) will pour out pure aluminum. Usually, Hydraulic tilting mechanism provided to pour large quantities of liquid metals.
- Finally, with care, the molten aluminum will be poured into mould to cool down and then slide out for use.
Type | Input Power | Melting Capacity | Max Temperature | ||
steel, stainless steel | copper, gold, silver (scrap, Slag) | aluminum, aluminum alloy, Aluminum scrap, Aluminum slag, pop can | 1800℃ | ||
SMJD-463 | 60 KW | 200 KG | 500 KG | 200 KG | |
SMJD-480 | 60 KW | 150 KG | 500 KG | 150 KG | |
SMJD-580 | 80 KW | 200 KG | 600 KG | 200 KG | |
SMJD-600 | 60 KW | 230 KG | 560 KG | 230 KG | |
SMJD-900 | 120 KW | 300 KG | 900 KG | 300 KG | |
SMJD-905 | 80 KW | 300 KG | 900 KG | 300 KG | |
SMJD-1250 | 80 KW | 400 KG | 1200 KG | 400 KG | |
SMJD-1250 | 120 KW | 450 KG | 1350 KG | 450 KG | |
SMJD-1500 | 120 KW | 500 KG | 1500 KG | 500 KG | |
SMJD-1550 | 120 KW | 520 KG | 1560 KG | 520 KG | |
SMJD-1700 | 160KW | 600 KG | 1700 KG | 600 KG | |
SMJD-2300 | 160KW | 800 KG | 2000 KG | 800 KG | |
SMJD-3100 | 200KW | 1200 KG | 3000 KG | 1200 KG |
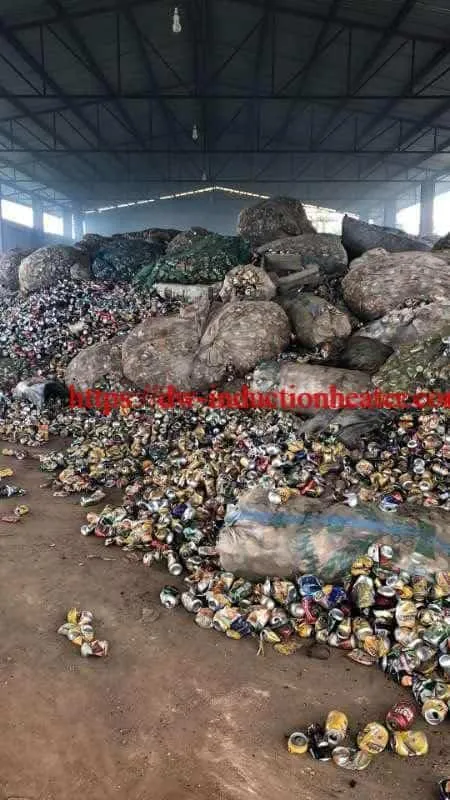
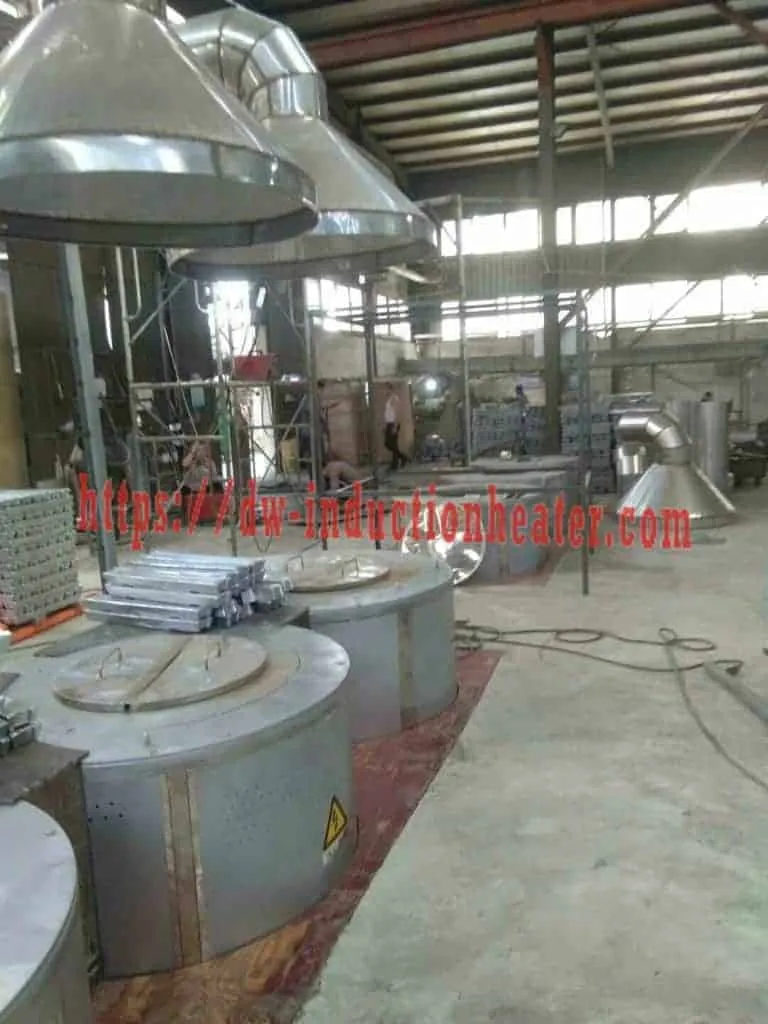
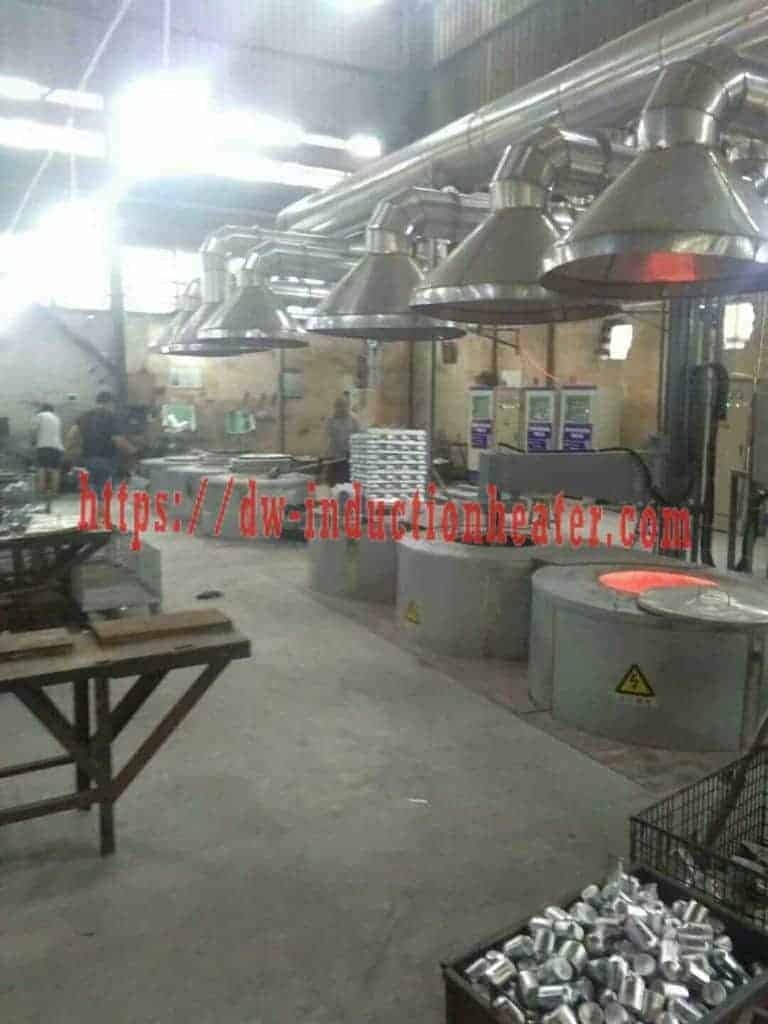
Induction Brazing Aluminum Pipes
handbook of induction heating eddy current
PDF handbook of induction heating eddy current
Both induction heating and eddy current testing work with coils, generators, ac-current and ac-voltage, frequencies, field strength and induction law. Contrary to heating of the test parts, the eddy current test does not want to heat the parts at all but wants to examine them for their metallurgical microstructure, thus for their mechanical features like hardness, case depth or alloy. The eddy current test does not provide absolute values (e.g. "56 HRC" or "2.6 mm case depth"). The eddy current test does detect fine differences in micro-structure with high sensitivity. In the production line, within a fraction of a second, a non-destructive 100 % test for • hardness • case depth • hardness run out, hardness pattern • tensile strength • carbon content • soft spots • surface decarburisation is completed, and thus quick corrective reactions to any variance from the specified structure can be realized. With a suitable mechanical part handling arrangement, the transport from the hardening station to the test station takes only a few seconds. Faulty parts, caused by a damaged inductor, a jammed quench nozzle or an unknown reason are immediately detected, providing an enormous savings in time and costs! [caption id="attachment_7309" align="alignright" width="1024"]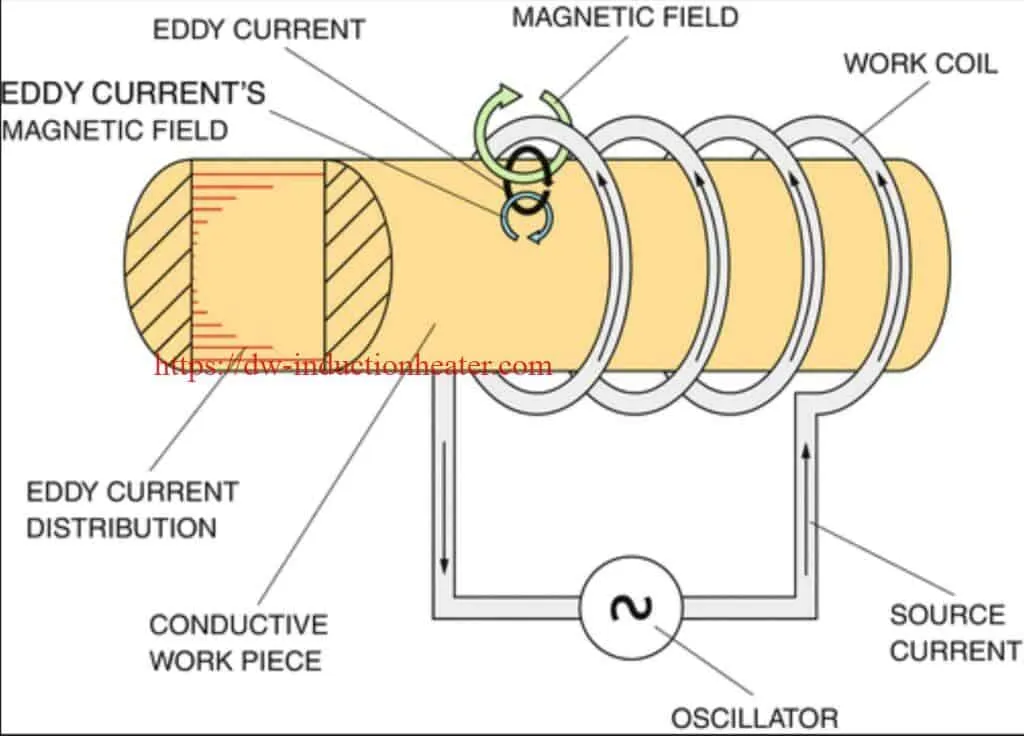
induction coating removal for removing paint
induction coating removal for removing paint
Induction coating removal principle
The induction disbonder works by the principle of induction. Heat is generated in the steel substrate and the bonding is broken. The coating is then removed entirely without disintegrating and completely free from contaminating agents, i.e. blast media.This obviously makes disposal and recycling of waste easier and cheaper. Even inside the pittings and cracks in the surface the coating is disbonded. The HLQ Induction heating works by fast transfer of energy to the steel substrate, as a result securing a controlled heating of the surface and fast removal of most types of coatings.What is induction coating removal?
The HLQ Induction coating removal system is a state-of-the-art induction heating tool that rapidly strips paint and tough, high-build coatings. It is a faster, cleaner and safer way to strip coatings.
What are the benefits?
Induction heating can outperform traditional paint-stripping methods. Abrasive blasting or disk grinding are generally more labour intensive and come with other issues such as the cost of enclosure or containment and collection of blast media, plus the filtration or separation of the coating materials for disposal. In many urban projects these are prime considerations and extremely costly to overcome. Whereas, when coatings are removed by induction, the only waste is the coating itself which in most cases can be swept or even vacuumed like any other workshop waste.
Safer working environment: The controlled, localized heat results in significantly reduced fumes and toxic dust.
Easy clean-up: The coating material mainly peels off in flakes rather than being pulverized.
Noiseless operation: Operators can work in public areas without creating a disturbance.
Mobile: The equipment is rugged and reliable but still light-weight and easy to move around worksites.
Reduced energy consumption: Fast, accurate and repeatable heat delivery makes the coating removal process extremely energy efficient.
Method flexibility: Spot heating, scanning, freehand and semi-automatic.
No limitations: The system can be used at flat surfaces, round contours, inside/outside corners, both sides of substrate, round rivets, etc.
Where is it used?
Induction coating removal is used in many industries, such as ships/marine, buildings, storage tanks, pipelines, bridges and offshore.
induction heating involves using alternating current and an induction coil to generate a powerful electro-magnetic field. When used properly, this field generates heat below a coating on a steel substrate, resulting in the coating de-bonding quickly and easily from the metal surface. At Alliance, we use this process to remove coatings from steel such as:
- Multiple coatings including epoxies, urethanes and others
- Lead paint
- Fire-retardant coatings (PFPs)
- Glued and vulcanized rubber as well as chlorinated rubber
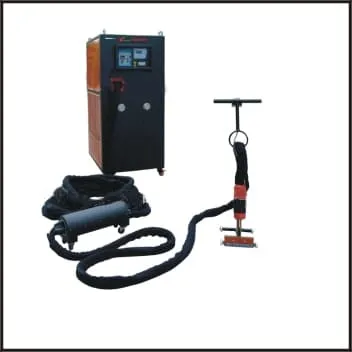
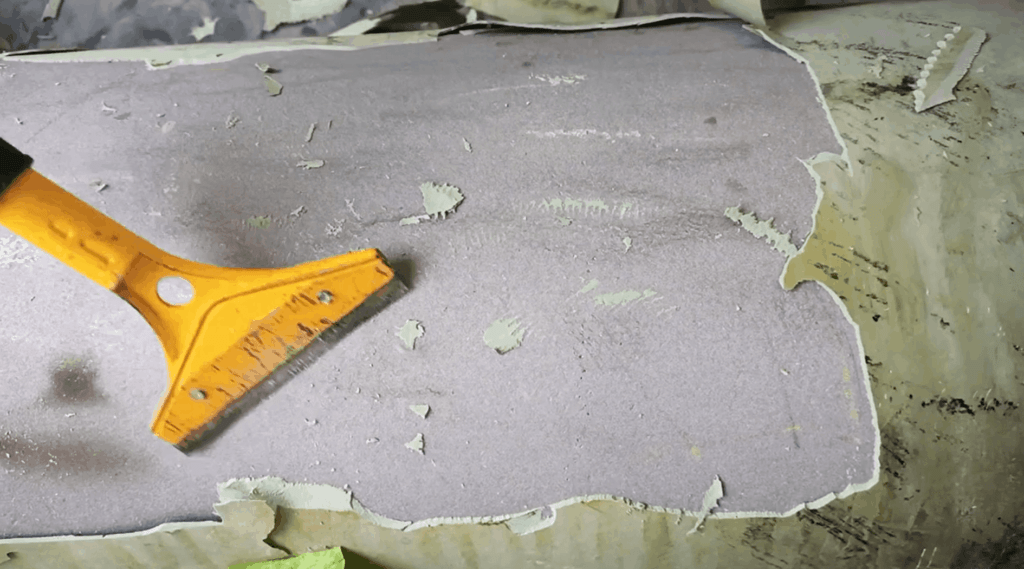

Induction Hardening Steel Part with High Frequency Hardening Machine
Induction Hardening Steel Part with High Frequency Hardening Machine

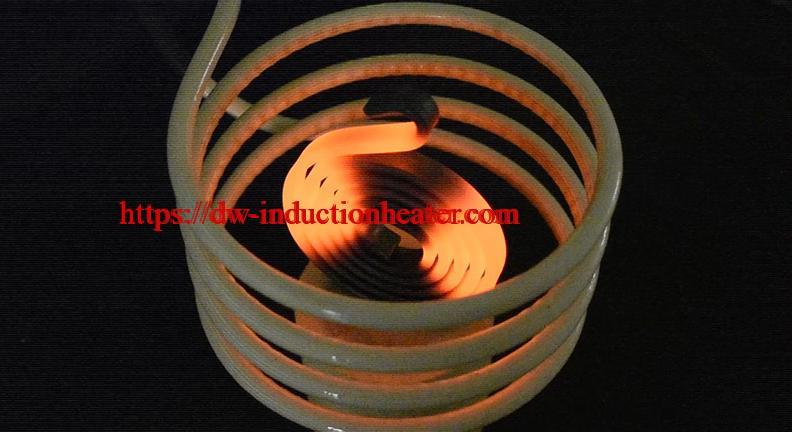
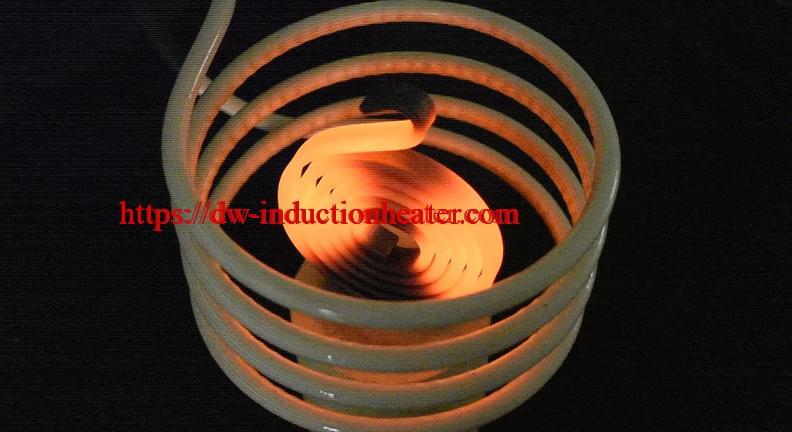
Aluminum Billet Heating Furnace
Continous Aluminum Billet Heating Furnace/Aluminium Alloys Billet Heater for the heating Aluminum Billets/Rods/Bars before the hot formging, extrusion, hot rolling and cutting,etc.
Induction Heating is a proven, reliable and efficient method of heating hot forming aluminum alloys. However, aluminum alloys have material properties that, if unaccounted for, can result in unexpected challenges. Understanding the unique facets of the induction heating of aluminum can be achieved by considering the properties that make aluminum alloys such advantageous materials. Given that aluminum and its alloys offer numerous advantages over many other metals, it is not surprising that inquiries about induction billet-heating equipment increasingly involve the heating of aluminum alloys. Many of these inquiries focus on how the induction heating of aluminum differs from the induction heating of other materials – typically steels – and how these differences affect heating quality, efficiency and productivity. Electromagnetic induction is well-suited for the heating of aluminum-alloy billets. However, there are some critical, yet easily overlooked, realities of aluminum billet heating that should be considered when designing, operating and maintaining this type of equipment. Fundamentally, the induction heating of aluminum alloys is no different than that of other common materials (e.g., carbon-steel and stainless steel alloys). It is ultimately material-property differences that set apart the induction heating of aluminum alloys from other metals. These material-property differences, if unaccounted for, can result in unexpected equipment performance and practical challenges. Because the users of most continuous induction billet-heating systems are familiar with the induction heating of steels and carbon-steel and stainless steel alloys, they provide a convenient point of reference in the consideration of the continuous heating of aluminum-alloy billets. HLQ Induction Equipment Co.,Ltd specializes in continous aluminum billet heating furnace/aluminium billet heater for heating aluminum billets/bars/rods before the hot formging, extrusion, hot rolling and cutting,etc.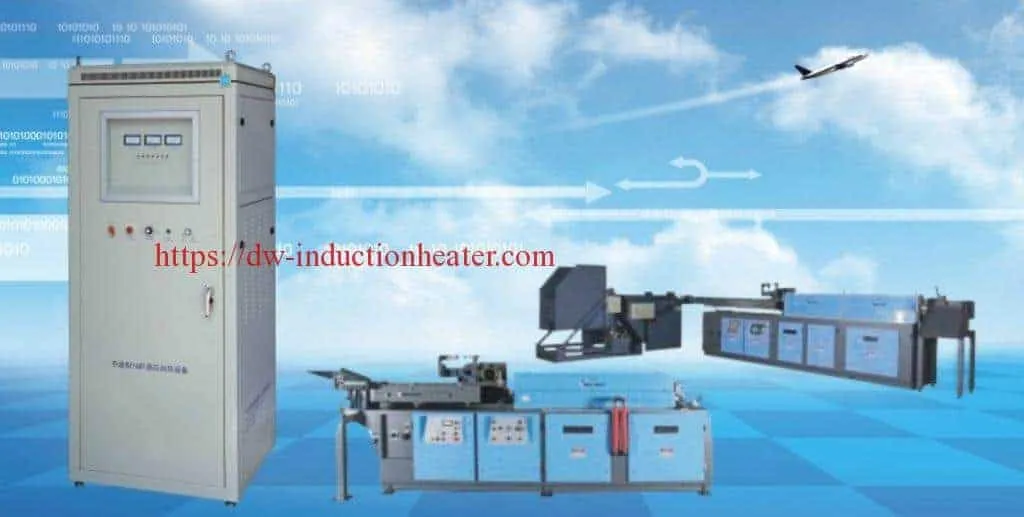

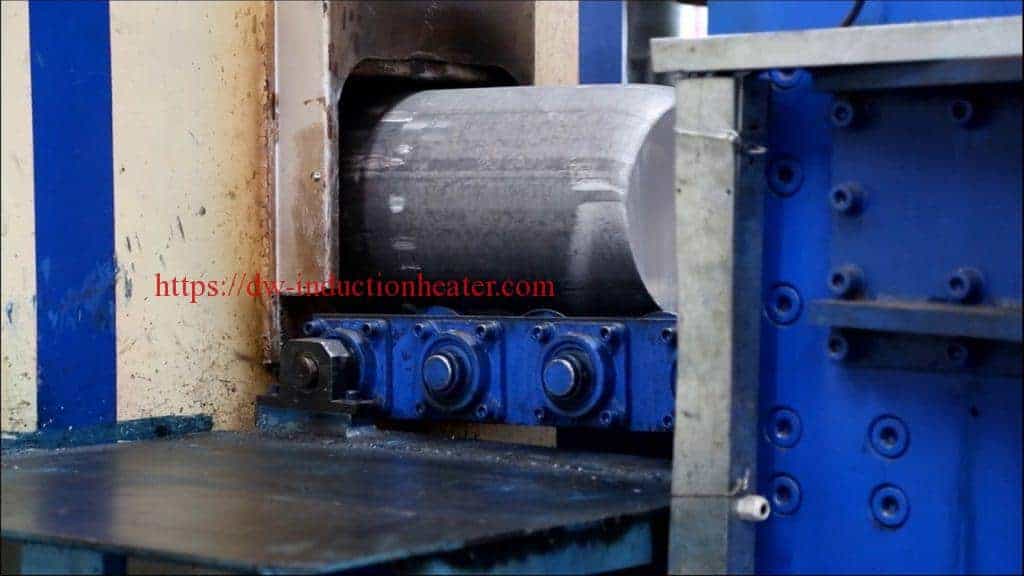
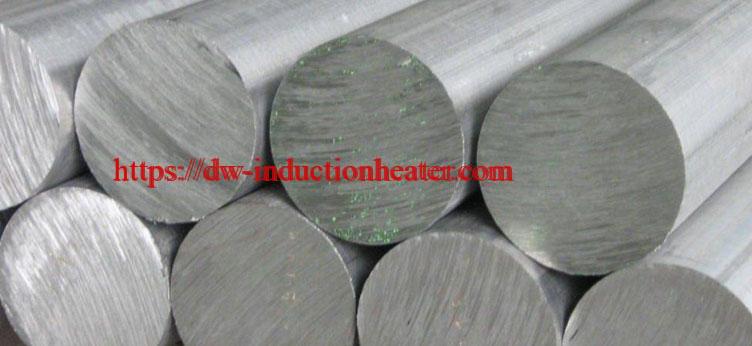
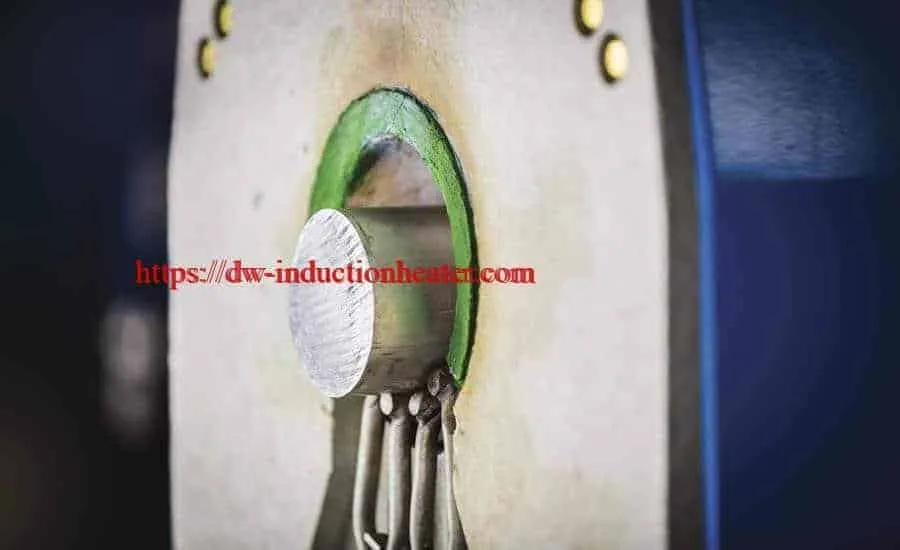
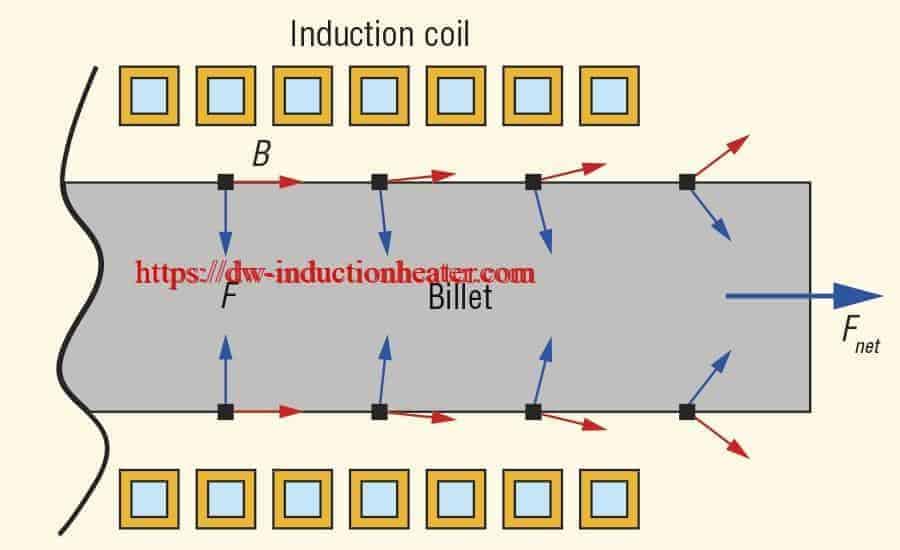
关注者
博客归档
-
▼
2023
(1696)
-
▼
三月
(191)
- What Is Induction Heating Coil&Inductor?
- induction hardening process
- induction brazing and soldering technology
- ultrasonic welding fabric machine for bonding nonw...
- Shrink Fit Steel Gear onto Shaft
- Induction Soldering Brass To Copper
- Aluminum Can Recycling Furnace with induction heating
- Induction Brazing Aluminum Pipes
- handbook of induction heating eddy current
- induction coating removal for removing paint
- Induction Hardening Steel Part with High Frequency...
- Aluminum Billet Heating Furnace
- Brazing Copper Tube to Brass Fitting With Induction
- Brazing Brass to Aluminum with Induction
- ultrasonic plastic welder for US plastic welding b...
- Advantages of Induction Heating
- Hydrogen Atmosphere Brazing Tube To Copper With In...
- Induction Preheating Before Welding For Stress Rel...
- Jointing Metal with Brazing and Welding
- induction sealing glass
- Brazing Copper Tube with Induction
- Shrink Fittting Part Removal application with Indu...
- Induction Brazing Carbide Tipping on Cutting Steel...
- induction soldering copper tubing to brass valves
- Induction Heating Ferroconcrete Dismantling Machine
- Induction Brazing Steel Tube
- electromagentic induction steam boiler with touch ...
- Induction Brazing Copper Pipe Fittings
- induction soldering fiber optic cable
- Induction Tempering Spring
- Induction Forging End of Bar and Rod for Copper an...
- Electromagnetic Induction Steam Generator
- Induction Forging End of Bar and Rod for Copper an...
- Induction Preheating Hot Heading
- evaporate water boiler with induction heating
- Induction Annealing Stainless Steel Tubes
- Automatic Induction Forging Video
- Induction Thermal Oil Heater-Thermal Fluid Heating...
- induction heating graphite susceptor
- Brazing Cutting Tool with Induction
- Shrink Fit Steel Gear onto Shaft
- Induction Furnace for melting copper brass and iro...
- RPR Induction Stripping-Induction Rust & Paint Coa...
- Induction Curing Heating of Organic Coating
- Induction Brazing Carbide Tipping on Cutting Steel...
- Induction Brazing Steel Pipe
- Induction Preheating Welding Steel Pipe
- refrigeration induction brazing refrigerator coppe...
- Research and Design on IGBT Induction Heating Powe...
- Induction Shrink Fitting Steel Tube
- Induction Brazing Steel To Carbide Plate
- Induction Heater is the Energy Saving heating Sour...
- Induction heating bearings machine PDF
- Induction Soldering Process Video
- Brazing Brass Pipe With Induction
- induction small copper tubing brazing connection j...
- ultrasonic welding fabric machine for bonding nonw...
- Hydrogen Atmosphere Brazing Tube To Copper With In...
- Induction Thermal Oil Heater-Thermal Fluid Heating...
- Induction Heating Bolts
- Brazing Carbide Tool Tips With Induction
- Induction Soldering Wires Onto Connection
- Hydrogen Atmosphere Brazing Tube To Copper With In...
- induction heating steel casting
- Brazing Copper Bars with Induction
- Induction Straightening For Deck and Bulkhead
- Induction Annealing Brass Bullet Shells
- Induction Aluminum Billet Rod Heating Furnace
- Handheld Brazing Stainless Steel Tube
- Induction Aluminum Billet Rod Heating Furnace
- Induction Shrink Fit Aluminum Shaft
- Induction Heating Automotive Motor
- What Is Induction Heating?
- Induction Heating Magnetic Iron Oxide
- Induction Hardening Surface Process
- Ultrasonic Welding Machine | Ultrasonic plastic We...
- Induction Heating PDF
- Induction Aluminum Brazing with Computer Assisted
- Aluminum Can Recycling Furnace with induction heating
- induction heating reactor tank-vessels
- Induction Soldering PCB Board with Copper Pipe
- Induction Heating Steel Pipe To Remove plastic coa...
- Induction Annealing Stainless Steel Tubes
- induction brazing stainless steel to copper
- Induction Brazing Carbide to Steel
- Induction Soldering Copper Wire Connectors
- Induction Annealing Copper Tubes
- Induction Heating Aluminum Pipe
- Induction Shrink Fitting Assemblies
- Brazing Aluminum Pipes Assembly With Induction
- Application of Induction Heating In Food
- Brazing Brass To Copper With Induction
- Brazing Copper Assemblies With Induction
- Induction Soldering Copper Tube
- Induction Heating Steel Mold
- induction heating reactor tank-vessels
- induction hardening process
- Induction heating bearings machine PDF
- What is induction hardening?
- Induction Brazing Carbide Tipping on Cutting Steel...
-
▼
三月
(191)
我的简介

- HLQ induction heating machine
- HLQ induction heating machine manufacturer provides the service of induction brazing,melting,hot forming,hardening surface,annealing,shrink fitting,PWHT,etc.