INDUCTION STRAIGHTENING Process For deck and bulkhead straightening
Our time-saving deck and bulkhead straightening solutions with
induction heating are found in the shipbuilding industry (deck straightening), construction industry (straightening of bridges) and trains/trucks industry (production and repair of locomotives, rolling stock and heavy goods vehicles).
What is induction straightening?
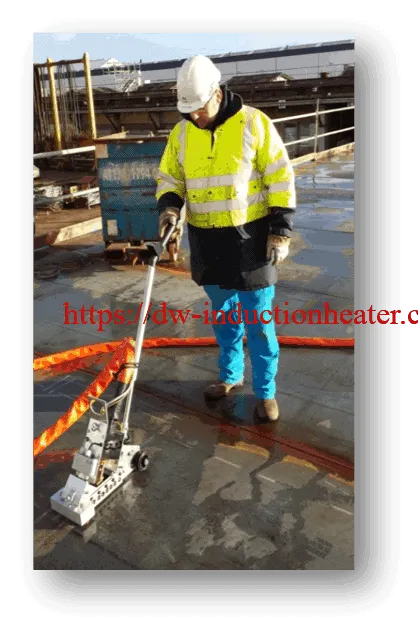
Induction straightening uses a coil to generate localized heat in pre-defined heating zones. As these zones cool, they contract, "pulling" the metal into a flatter condition.
What are the benefits of induction straightening?
Induction straightening is extremely fast. When straightening ship decks and bulkheads, our customers often report minimum 50% time savings compared to traditional methods. Without induction, straightening on a large vessel can easily consume tens of thousands of man-hours. The precision of induction also boosts productivity. For example, when straightening truck chassis, there is no need to remove heat-sensitive components. Induction is so precise it leaves adjacent materials unaffected.
Where is induction straightening used?
Induction heating is widely used to straighten ship decks and bulkheads. In the construction industry it straightens beams. Induction straightening is increas-ingly used in the manufacture and repair of locomotives, rolling stock and heavy goods vehicles.
Induction deck and bulkhead straightening
Induction heating cuts deck and bulkhead straightening times by as much as 80 per cent compared to alternative methods. Induction straightening is better at preserving metallurgical properties. It’s also the safest, healthiest, most environmentally friendly straightening method available.
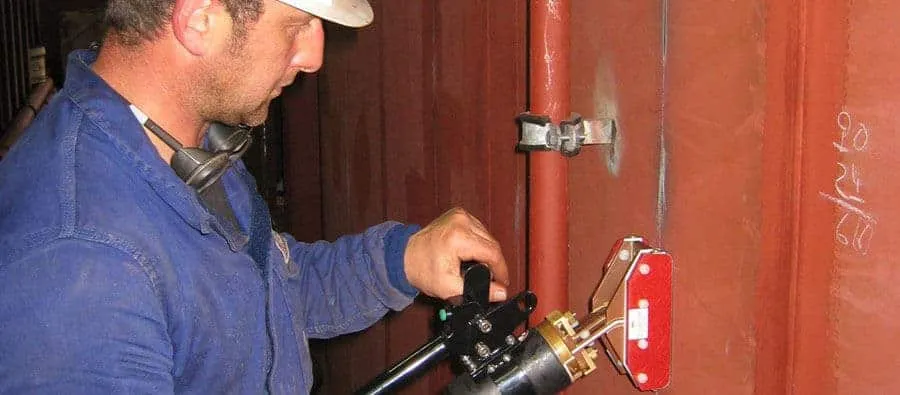
The principle of induction straightening system is that an inductor with an alternating current passing through generates an "induced current" in the steel plate, so that the current rapidly increases the temperature in the concentrated heating area, so that the material in the heating area expands vertically ; When the steel plate is cooled, the shrinkage of the material in the heating area is basically the same in all directions, resulting in lasting deformation, making the plate shortened and straightened, so as to achieve the leveling effect.
induction straightening through this system only needs to be heated near the ship's welding seam, which reduces the leveling workload, saves a lot of cooling water, ensures that other processes are carried out at the same time, and shortens the construction period; after leveling, the deformation can be permanently eliminated stress; the heat generated by leveling is concentrated in the small area covered by the inductor, reducing the damage to the paint layer; at the same time, no toxic gas is generated in the heating area, and there is less smoke when leveling the painted steel plate, no Noise can help improve the working environment of workers and improve work efficiency. In addition, the leveling system is simple to operate and, thanks to the maximum induction heating temperature set, does not overburn even if the operator makes mistakes.
At present, the shipbuilding industry usually uses the flame thermal leveling method for steel plate leveling, that is, directly heating the raised surface of the deformed area by "fire attack". When the steel plate cools, the heated side shrinks more than the unheated side, causing the material to expand in the vertical direction, thereby "straightening" the steel plate. This method has many disadvantages, such as long heating time, over-burning when leveling steel plates with large thickness, high requirements for operators, uneven leveling effect, and at the same time, a large number of Toxic gas and smoke consult, pollute the environment. Experiments show that compared with the traditional flame heat leveling process, the induction heat leveling process can reduce the leveling workload by up to 80%, and the energy saving and emission reduction effect is obvious, which greatly shortens the ship construction period and saves costs.
Straightening
When unwanted distortions in metal structures appear, their correction becomes necessary in many industrial processes. A solution in order to reduce the mentioned distortions is to apply heat on certain areas in these structures creating mechanical stresses in the material.
The traditional method used for this application is flame straightening. For this, a skilled operator is dedicated to provide heat in specific areas, following a heating pattern, which determines the reduction of distortion in the metal structure.
Currently this straightening process has high costs because it requires a large amount of skilled labor, high workplace hazards, contamination of work area and high energy consumption.
Induction heating advantages
The replacement of flame straightening by the method of induction has the following advantages:
-- Significant time reduction in the straightening operation
-- Repeatability and heating quality
-- Improved quality of working environment (no hazardous fumes)
-- Improved safety for workers
-- Energy and labor cost savings
Related industries are shipbuilding, railway and steel structures in construction among others.
Metal deformation is the major challenge in the metal processing industry, when they need to process a metal to desired shape. Here it comes the purpose of Magnetothermal Induction straightening Equipment, where the deformed metal can be restored when heating is applied to specific zone to remove stress within the metal. In induction straightening process where the metal is straightened or reformed to its original shape, there are case it is applied on solid metal or hollow metal surface to reshape to its original dimension. This method of straightening involves lesser manpower utilization than the conventional method of straightening methodology. Benefits of HLQ Induction based Induction straightening:
Better system efficiency.
Automated process control design
Faster heating and reduced cycle time.
Highest safety integrated within system.
Clean and environment friendly.
Efficient way of heating metal and its alloy.
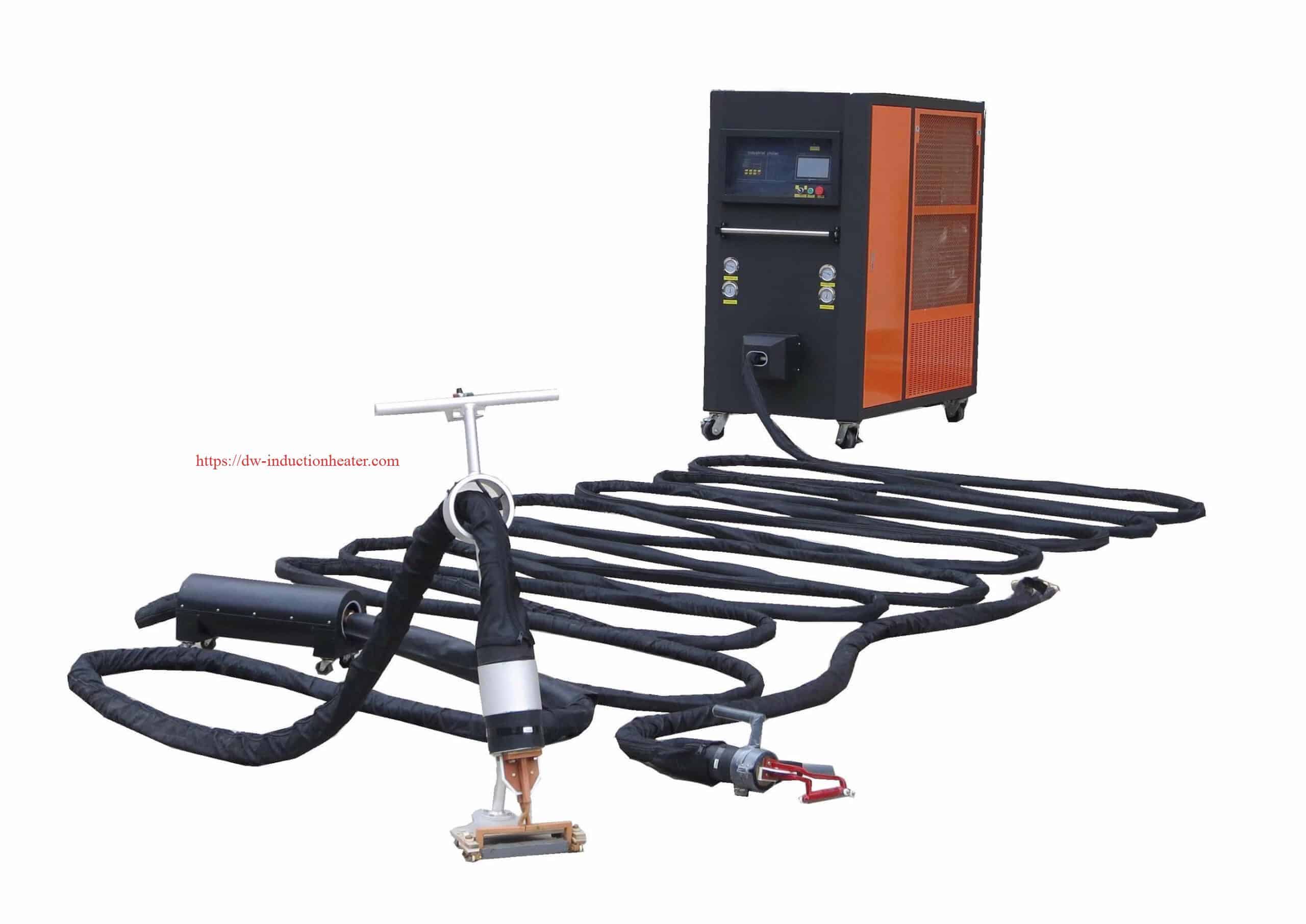
Ship building industry is demanding field where the customer expectation and requirement will be higher than the land navigation system. The domain knowledge on this particular sector will make the manufacturer to understand and produce product as per customer specific requirement and quality standard as expected.
HLQ Induction heating Machine supplies can really meet the standard as expected by the Railway. It is growing domain where only key technology based induction heating system with highest flexibility on user interface.
Heat treatment of Assembly parts.
Removing of rusted Fasteners.
Metal heating of structural parts.
Engine Assembly heating.
Critical metal forming as per dimension specification.
https://dw-inductionheater.com/induction-straightening-for-deck-and-bulkhead.html?feed_id=189949&_unique_id=641ad124de58a