2022年11月30日星期三
Induction Melting Videos
Induction Melting Videos for melting copper,brass,copper wire,iron steel,etc.
Induction Preheat Welding Systems
Portable Post Weld Heating Treatment System With Induction
Main Application:
l Preheat: weld heat,coating, spraying, bending, fitting&unfitting heat
l Post-weld heat treatment: tank, boile, pipeline, steel sheet or other metal jobs
l InductionHeat: mold heating, shipboard, zinc bath, large& irregular metal parts
l Pipeline material heat: pipeline oil, pipeline gas, pipeline water, pipeline petrochemical and other pipeline material
Main Features:
* High speed: 70%
* Low tolerance
* Energy Saving
* High efficiency
* Accurate heating
* Simple operation
* Non-contact heating
* Environmental protection
* Hypothermia circumstance
* Air cooling is suitable for low-temperature environment
* Induction heating is more uniform than oil,gas,flame heating
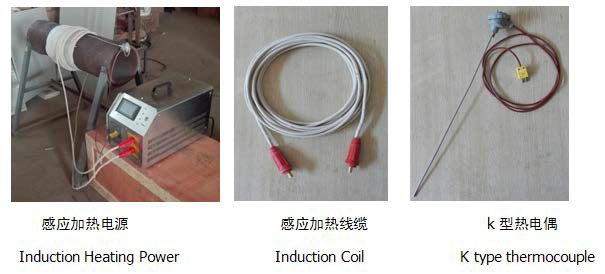
MYD-20KW | MYD-10KW | |
Input voltage | 3*380V, 50/60Hz, 4 Wires | |
Input Current | 1~30A | 1~15A |
Output Current | 0~300A | 0~200A |
Output Power | 1~20KW | 1~10KW, Max 15KW, 150% duty cycle |
Output Frequency | 5~30KHZ | |
Thermocouple | K type | |
Temperature system | Build in induction machine | |
Heating Temperature | Max800℃ | Max500℃ |
Size | 700 x 330 x 410 mm | 650 x 310 x 410 mm |
Weight | 32kg | 26 kg |
Induction Heating coil | ||
Length | 10~20 M | |
Diameter | 15 mm | |
Working temperature | -30~45℃ | |
Pipeline Size | OD: 50~500mm or equivalent |
induction fluid pipe heater
Induction Thermal Fluid Pipeline Heater
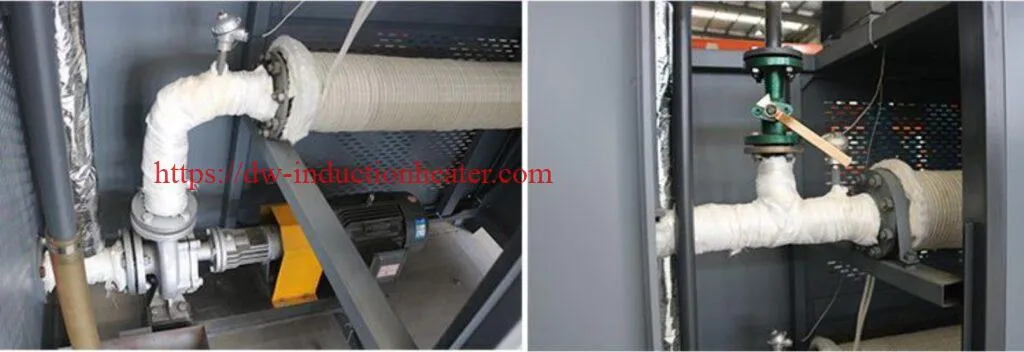
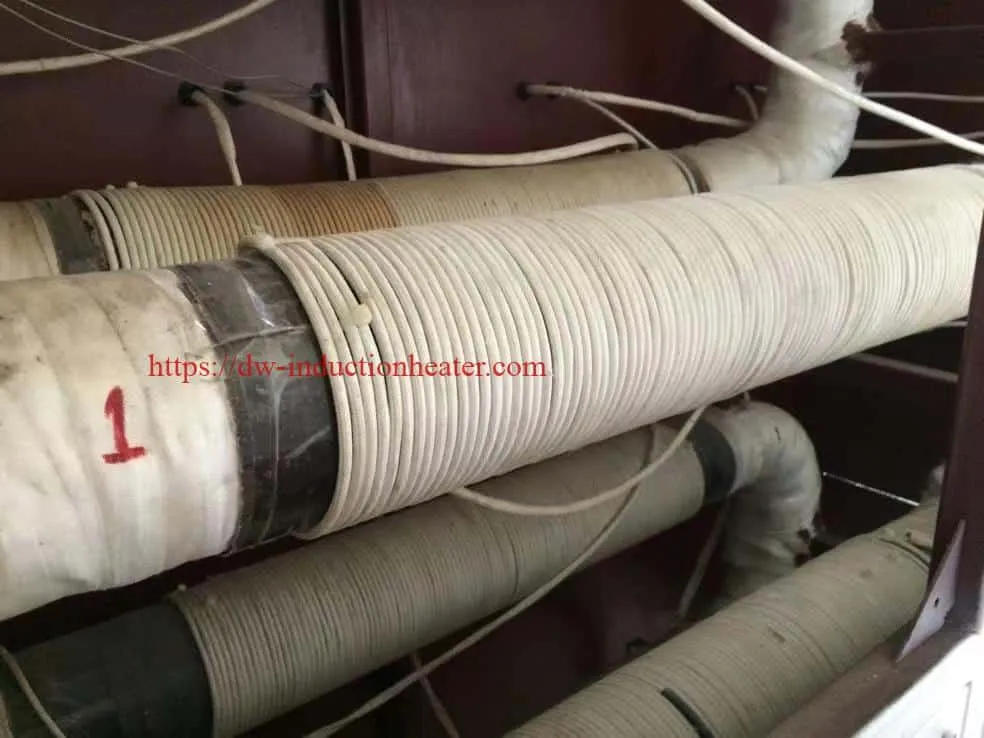
Heating method | Conditions | Power consumption |
Induction heating | Heating 10 liters of water up to 50ºC | 0.583kWh |
Resistance heating | Heating 10 liters of water up to 50ºC | 0.833kWh |
Items | Induction heating | Coal-fired heating | Gas-fired heating | Resistance heating |
Heating efficiency | 98% | 30-65% | 80% | Below 80% |
Pollutant emissions | No noise, no dust, no exhaust gas, no waste residue | Coal cinders, smoke, carbon dioxide, sulfur dioxide | Carbon dioxide, sulfur dioxide | Non |
Fouling (pipe wall) | Non-fouling | Fouling | Fouling | Fouling |
Water softener | Depending on the quality of fluid | Required | Required | Required |
Heating stability | Constant | Power is decreased by 8% yearly | Power is decreased by 8% yearly | Power is decreased by more than 20% yearly (high power consumption) |
Safety | Electricity and water separation, no electricity leakage, no radiation | Risk of carbon monoxide poisoning | Risk of carbon monoxide poisoning and exposure | Risk of electricity leakage, electric shock or fire |
Durability | With core design of heating, 30 years service life | 5 years | 5 to 8 years | Half to one year |
Diagram
Induction Heating Power Calculation
Required parameters of parts to be heated: specific heat capacity, weight, starting temperature and end temperature, heating time;
Calculation formula: specific heat capacity J/(kg*ºC)×temperature differenceºC×weight KG ÷ time S = power W
For example, to heat thermal oil of 1 ton from 20ºC to 200ºC within an hour, the power calculation is as follows:
Specific heat capacity: 2100J/(kg*ºC)
Temperature difference: 200ºC-20ºC=180ºC
Weight: 1ton=1000kg
Time: 1 hour=3600 seconds
i.e. 2100 J/ (kg*ºC)×(200ºC -20 ºC)×1000kg ÷3600s=105000W=105kW
Conclusion
The theoretical power is 105kW, but the actual power is commonly increased by 20% because of taking the heat loss into consideration, that is, the actual power is 120kW. Two sets of 60kW induction heating system as a combination are required.
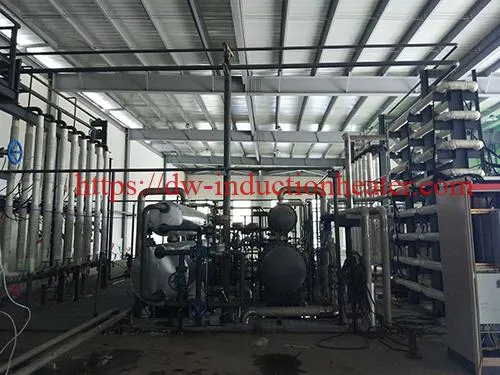
Induction Thermal Fluid Pipeline Heater
Advantages of using the Induction Fluid Pipeline Heater: Precise control of the working temperature, low maintenance cost and the possibility to heat any type of fluid to any temperature and pressure are some of the advantages presented by the Inductive Electrothermal Induction Heating Generator (or Inductive Heater for fluids) manufactured by HLQ. Using the principle of magnetic induction heating, in the Inductive Heater for fluids heat is generated in the walls of a spiral of stainless steel tubes. The fluid that circulates through these tubes removes that heat, which is used in the process.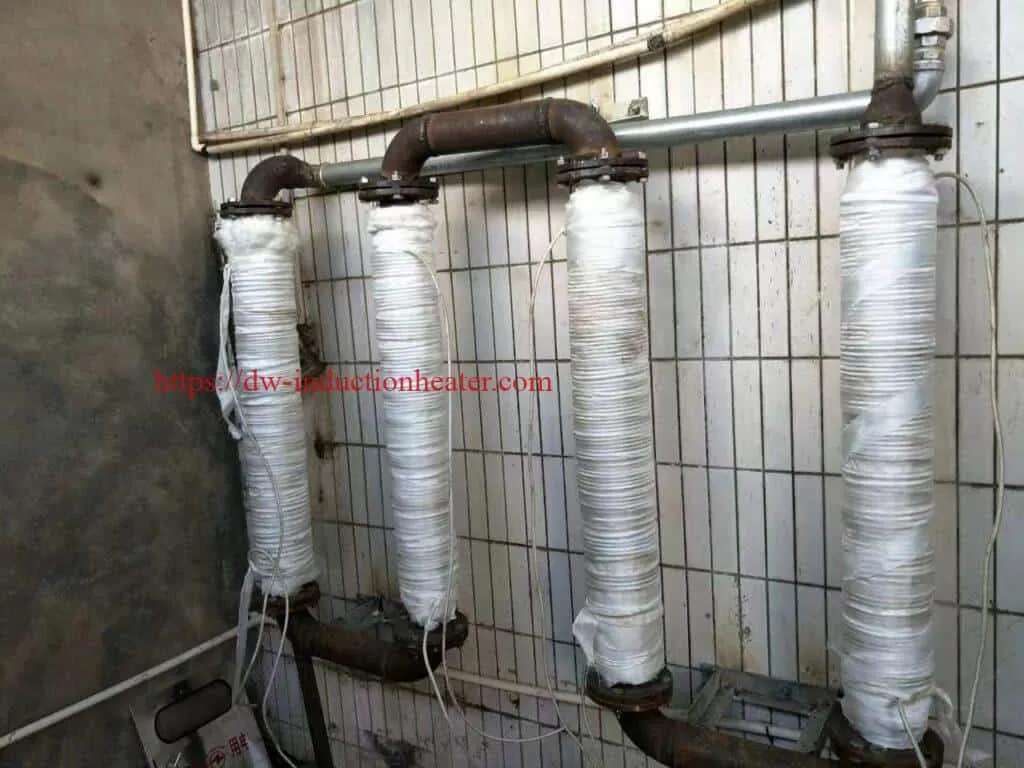
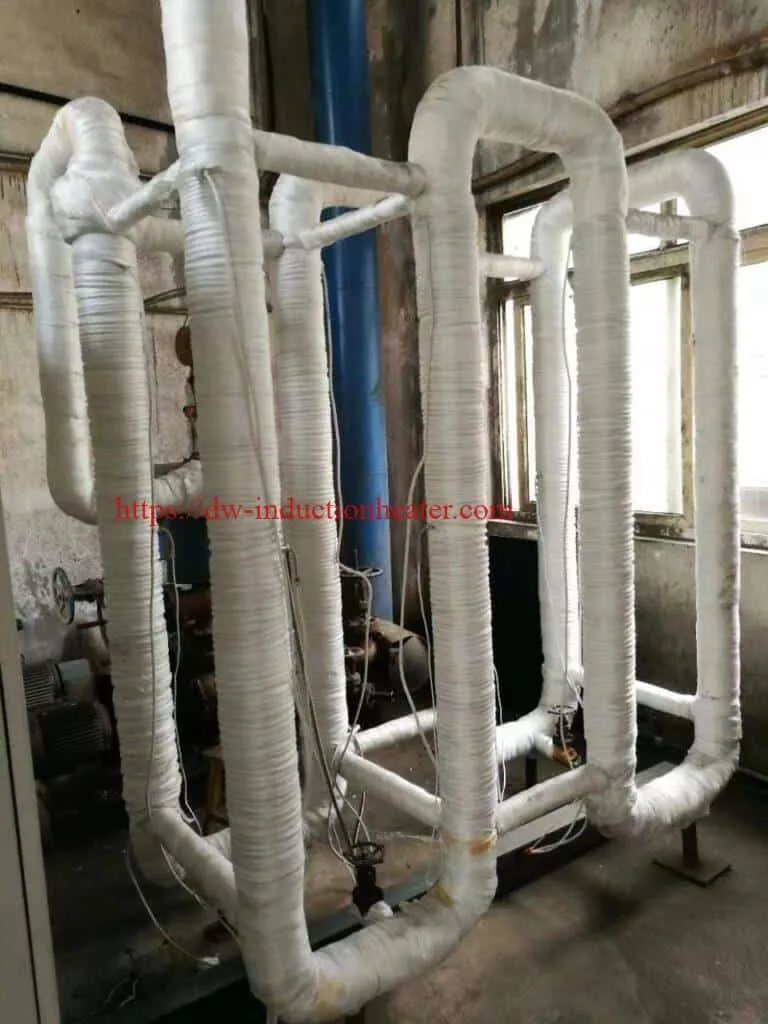
- System works dry and is naturally cooled.
- Precise control of the working temperature.
- Almost immediate availability of heat when energizing the Inductive Heater, due to its very low thermal inertia, eliminating the long heating periods necessary for other heating systems to reach the regime temperature.
- High efficiency with consequent energy savings.
- High power factor (0.96 to 0.99).
- Operation with high temperatures and pressures.
- Elimination of heat exchangers.
- Total operational security due to the physical separation between the heater and the electrical network.
- Maintenance cost practically non-existent.
- Modular installation.
- Quick responses to temperature variations (low thermal inertia).
- Wall temperature differential - extremely low fluid, avoiding any kind of cracking or degradation of the fluid.
- Accuracy and temperature uniformity throughout the fluid and quality of the process for maintaining a constant temperature.
- Elimination of all maintenance costs, installations and relative contracts when compared to steam boilers.
- Total security for the operator and the entire process.
- Gain space due to the compact construction of the Inductive Heater.
- Direct heating of the fluid without the use of a heat exchanger.
- Due to the working system, the heater is anti-pollutant.
- Exempt from generating residues in direct heating of the thermal fluid, due to minimal oxidation.
- In operation the inductive heater is completely noise free.
- Ease and low cost of installation.
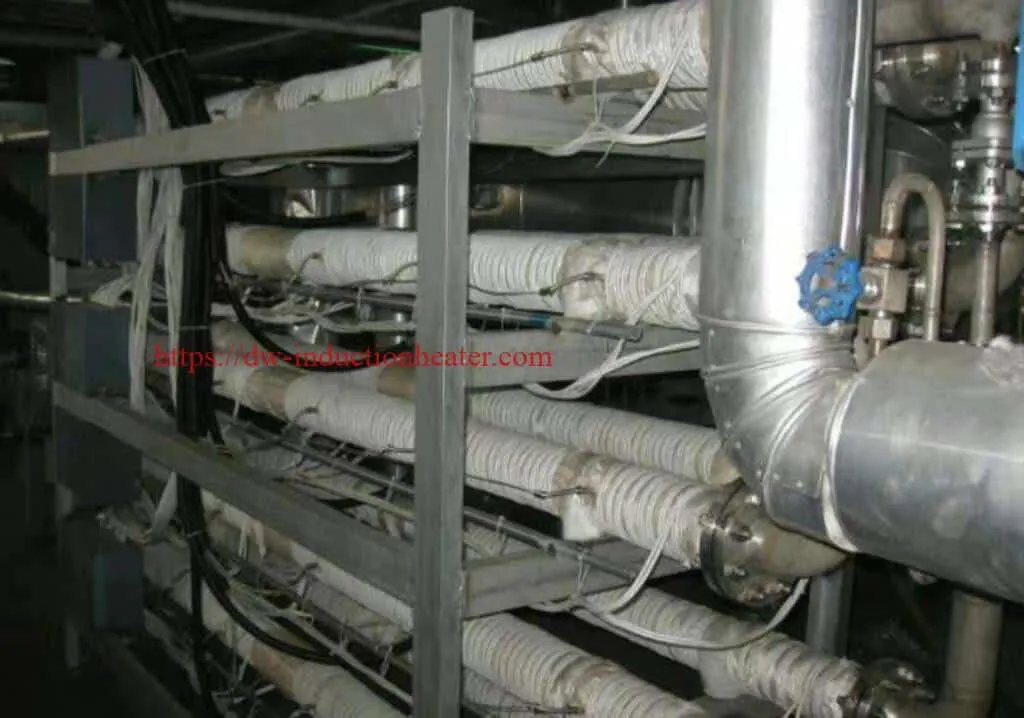
Induction Catheter Tipping Heating
High Frequency Induction Catheter Tipping Heating Applications
This induction catheter tipping heating application is often needed in the Medical Industry for the manufacturing of catheter tubes.
With induction catheter tipping, RF energy raises the temperature on the stainless steel or brass mold, without physically contacting the mold or using an open flame. The tip of the catheter is then formed by inserting the plastic tubing into the heated die or mold to form the rounded edges. The rounded end of the catheter tube allows the tube to be safely inserted into the human with minimal trauma to body tissue. The mold will also have a wire that inserts into the tubing to prevent the formation of blockages. The precise and accurate temperature control capabilities of induction are ideal for this type of precise medical application. The molds are usually fitted with a water-cooled jacket used to cool the heated mold back to a defined start temperature which enables the induction system to be driven by a set time/cycle zone.
Induction heating equipment for catheter tipping ensures a great degree of repeatability. The manufacturing process is fast and precise.
Catheter tipping typically requires low power. HLQ has several low power units that are ideal for catheter tipping and will recommend the right equipment based on the parts and unique application requirements.
Heating Catheter Tipping Die
Objective: To heat an aluminum catheter tipping die to above 2850F within 2 to 5 seconds for the forming of catheter material. Presently, heating is performed in 15 seconds with older induction equipment. The customer would like to use solid state induction heating equipment to reduce the heating times and develop a more efficient process.
Material: Aluminum catheter tipping die measuring 3/8" OD and 2" long with a nonmagnetic sleeve over the heat zone. The catheter material was described as being similar to polyurethane plastic. Also, a 0.035" diameter steel wire
was inserted into the catheter tube to prevent collapsing.
Temperature: 5000F
Application: The DW-UHF-3kW solid state induction power supply was determined to most efficiently produce the following results:
--A heating time of 3.3 seconds to reach 5000F and form the catheter was achieved through the use of a two (2) over two (2) turn helical coil.
--A quality catheter was formed by pressing 1/2" of the polyurethane tube into the mold while retaining shape through the use of a 0.035" wire to prevent collapsing of the tube. Laboratory results show that a substantial time decrease was accomplished which will allow for a significant increase in production while not sacrificing quality.
Induction Heating Equipment: DW-UHF-3kWkW solid state induction power supply including a remote heat station containing one (1) capacitor totalling 1.2 µF.
Frequency: 287 kHz
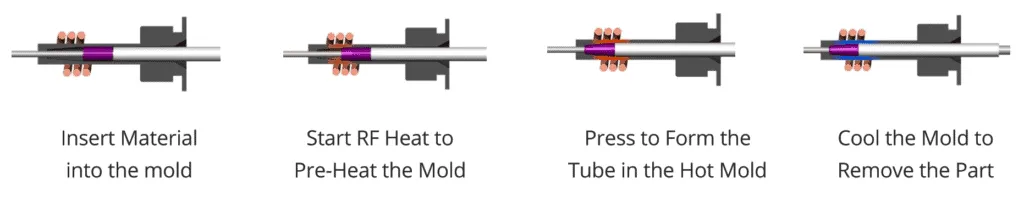
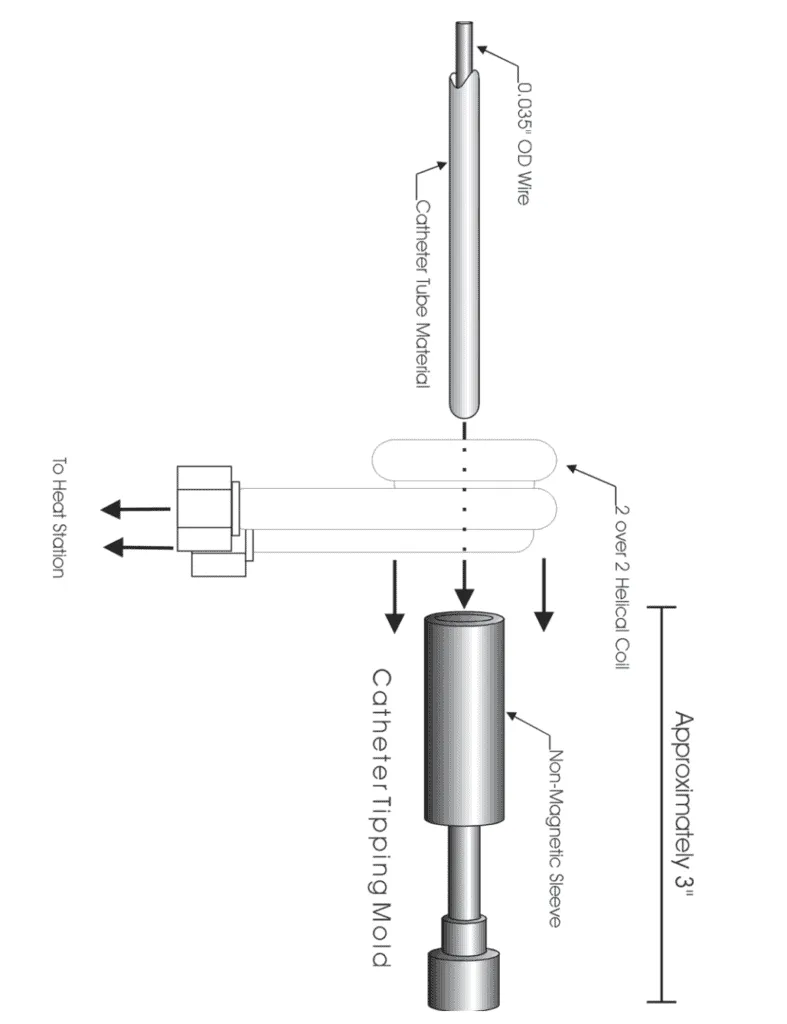
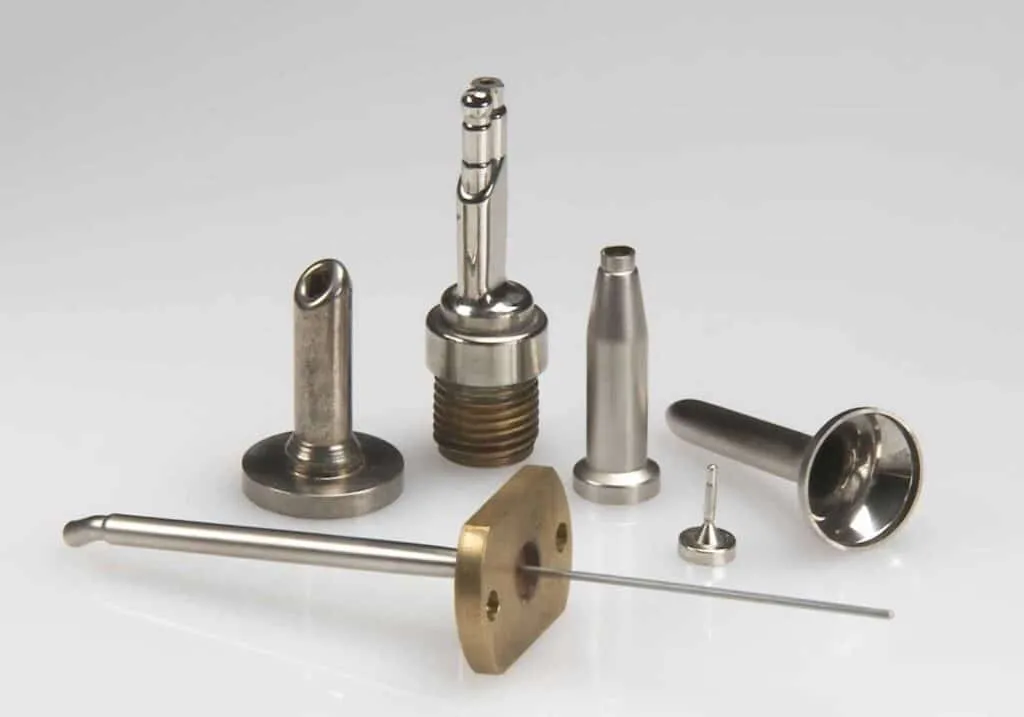
induction seam welder
Induction Seam Welder For Welding Tube and Pipe Solutions
What is induction welding?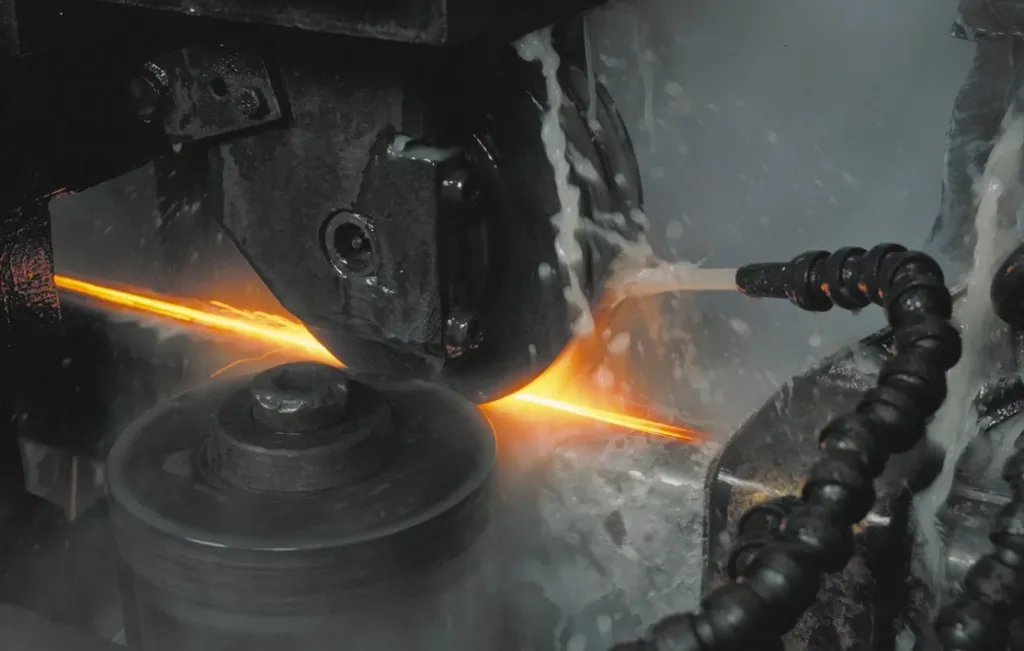
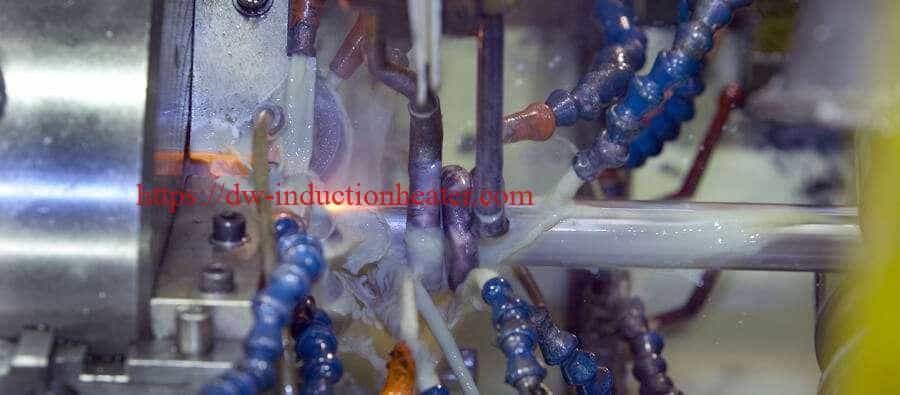
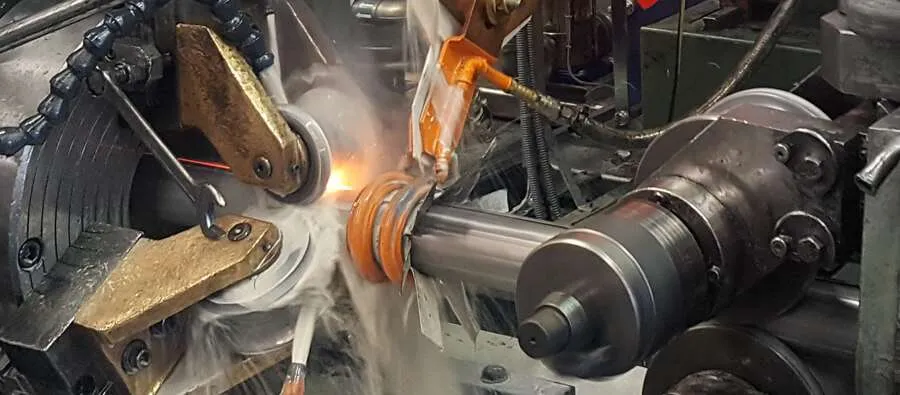
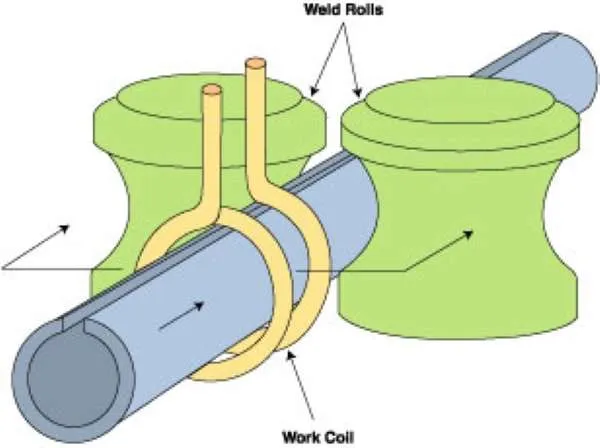
All Solid State (MOSFET) High Frequency Induction Seam Welder For Tube and Pipe | ||||||
Model | GPWP-60 | GPWP-100 | GPWP-150 | GPWP-200 | GPWP-250 | GPWP-300 |
Input power | 60KW | 100KW | 150KW | 200KW | 250KW | 300KW |
Input voltage | 3Phases,380/400/480V | |||||
DC Voltage | 0-250V | |||||
DC Current | 0-300A | 0-500A | 800A | 1000A | 1250A | 1500A |
Frequency | 200-500KHz | |||||
Output efficiency | 85%-95% | |||||
Power factor | Full load>0.88 | |||||
Cooling Water Pressure | >0.3MPa | |||||
Cooling Water Flow | >60L/min | >83L/min | >114L/min | >114L/min | >160L/min | >160L/min |
Inlet water temperature | <35°C |
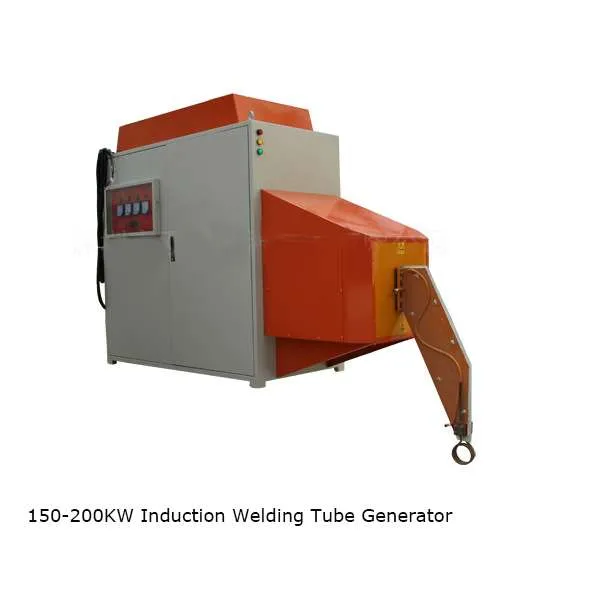
- Imported high-power resonant capacitors are used to obtain stable resonant frequency, effectively improve product quality, and realize the stability of the welded pipe process.
- Replace the traditional thyristor power adjustment technology with high-frequency chopping power adjustment technology to achieve microsecond level control, greatly realize the rapid adjustment and stability of the power output of the welding pipe process, the output ripple is extremely small, and the oscillation current is stable. The smoothness and straightness of the weld seam are guaranteed.
- Security. There is no high frequency and high voltage of 10,000 volts in the equipment, which can effectively avoid radiation, interference, discharge, ignition and other phenomena.
- It has a strong ability to resist network voltage fluctuations.
- It has a high power factor in the whole power range, which can effectively save energy.
- High efficiency and energy saving. The equipment adopts high-power soft switching technology from input to output, which minimizes power loss and obtains extremely high electrical efficiency, and has extremely high power factor in the full power range, effectively saving energy, which is different from traditional Compared with the tube type high frequency, it can save 30-40% of the energy saving effect.
- The equipment is miniaturized and integrated, which greatly saves the occupied space. The equipment does not need a step-down transformer, and does not need a power frequency large inductance for SCR adjustment. The small integrated structure brings convenience in installation, maintenance, transportation, and adjustment.
- The frequency range of 200-500KHZ realizes the welding of steel and stainless steel pipes.
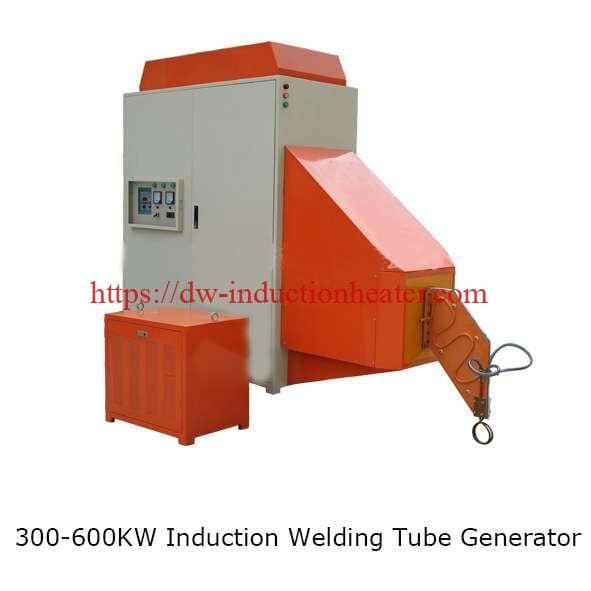
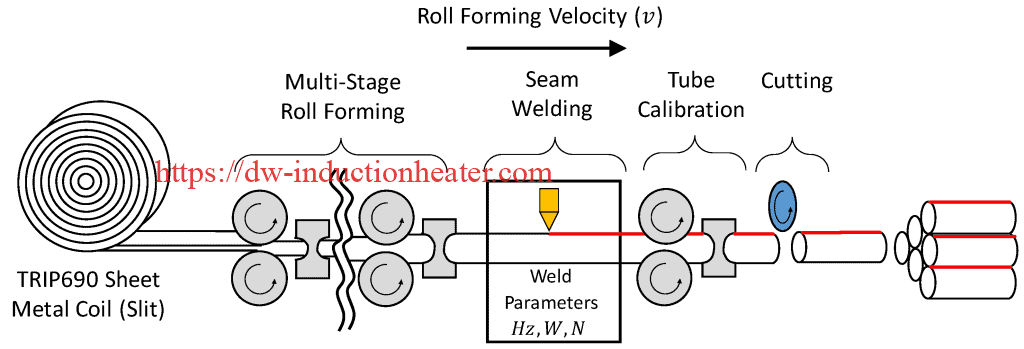

Brazing Carbide Tool Tips With Induction
Brazing Carbide Tool Tips With Induction
Objective: Attaching carbide cutters to a steel meat cutter impeller
Material carbide blocks; steel shank fitting
Temperature 1400 °F (760 °C)
Frequency 300 kHz
Equipment DW-UHF-30KW induction heating systems including: Induction heating coil Workhead: two-cap 1.0μF (Total 0.5 μF) Process The entire part is placed in a five-turn helical coil, the power is applied until the part is heated to the required temperature and a uniform heat pattern is achieved. The coil allows for easy fixturing and uniformity of heating between the carbide and the steel shank for a premium braze joint.
Results/Benefits
Precision: Due to the size of the induction coil, the process allows for precise placement of the carbides on the steel shanks
Economy: Power is consumed only during the heat cycle
Repeatability: joint quality is maintained in this repeatable process
Induction Soldering Coaxial Cable
Objective
Induction Soldering coaxial cable to connector ring and pin in two steps in under 5 seconds by reaching a temperature of 500°F (260°C) with induction heating.


Process:
Results/Benefits:
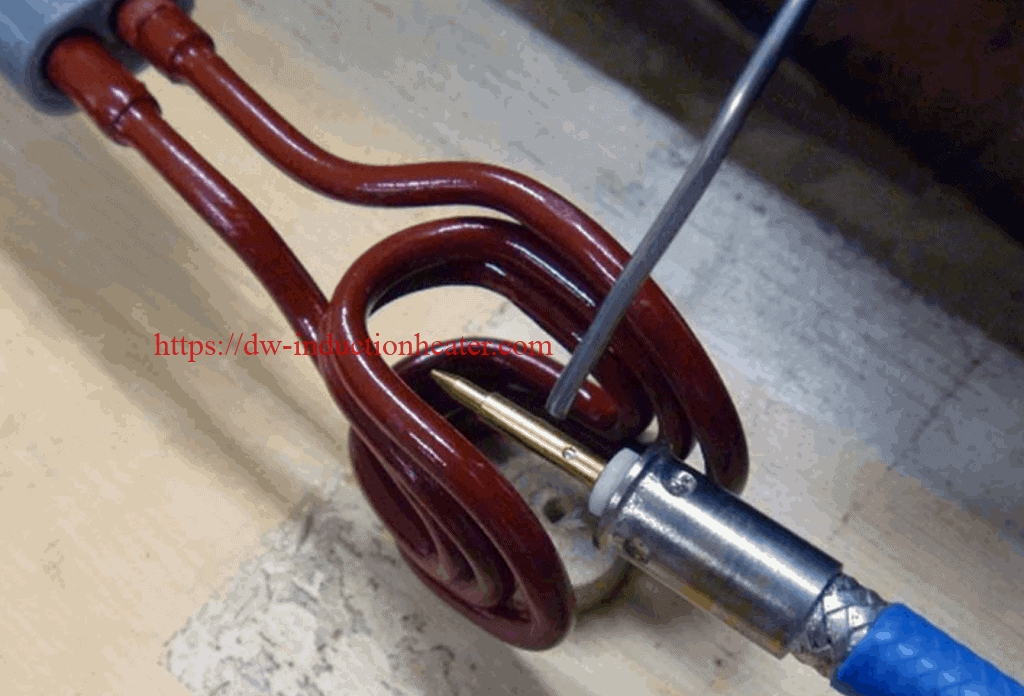


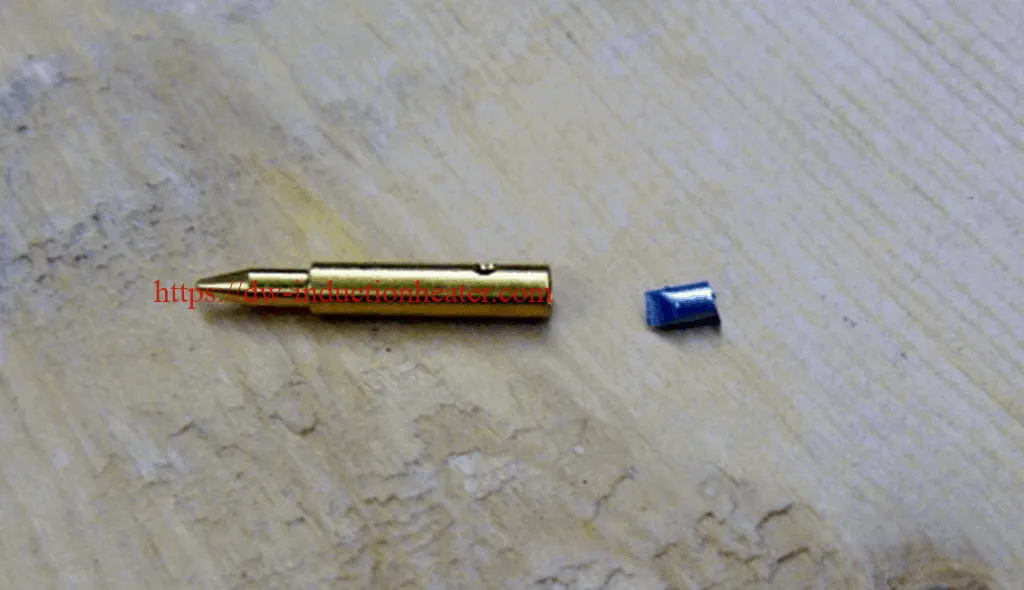
- The coaxial cable and connector were placed vertically inside the coil.
- Induction heating was applied for 3 seconds, at which point the part is hot enough for soldering.
- The induction soldering wire was fed between the cable braid and connector.
- Solder wire was inserted into the center pin, and the center pin was placed in the coil.
- The cable with connector was placed above the pin.
- Induction heat was applied for 1.5 seconds, after which the part was hot enough for soldering.
- The center conductor was inserted into the pin.
- The assembly was inspected to ensure that the soldering was successful.

- Strong durable joints and faster heating cycles
- Selective and precise heat zone, resulting in less part distortion and joint stress
- Technology without pollution, which is both clean and safe
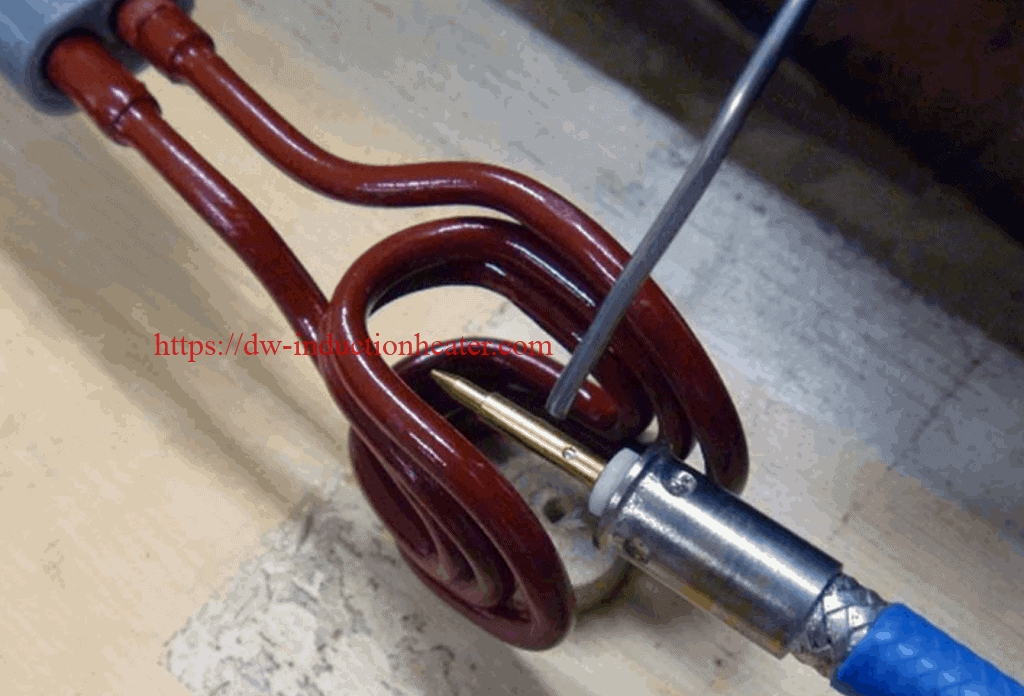


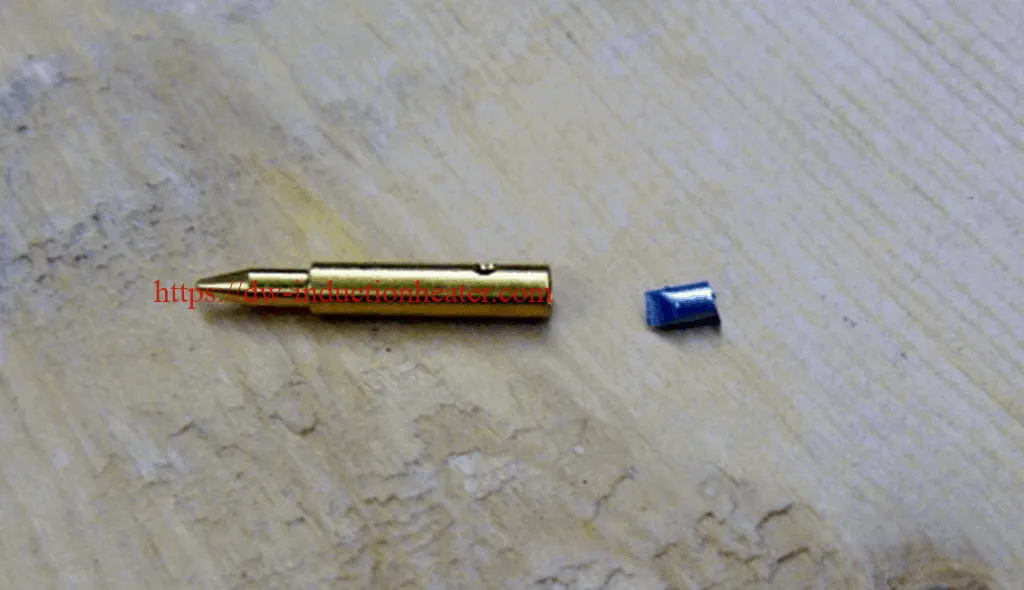

2022年11月29日星期二
Induction Brazing copper wire to copper cylinder
Equipment
20kw handheld induction brazing heater
Materials
Copper wire to Copper cylinder
Power: 12 kW
Temperature: 1600°F ( 871°C )
Time: 5 sec


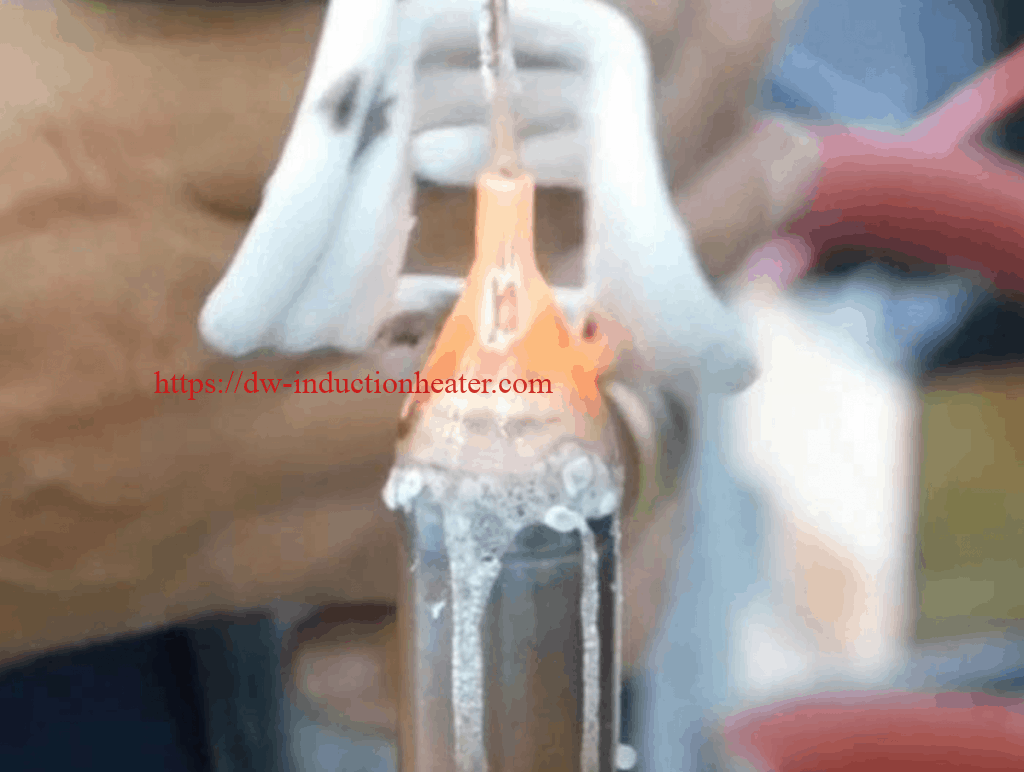
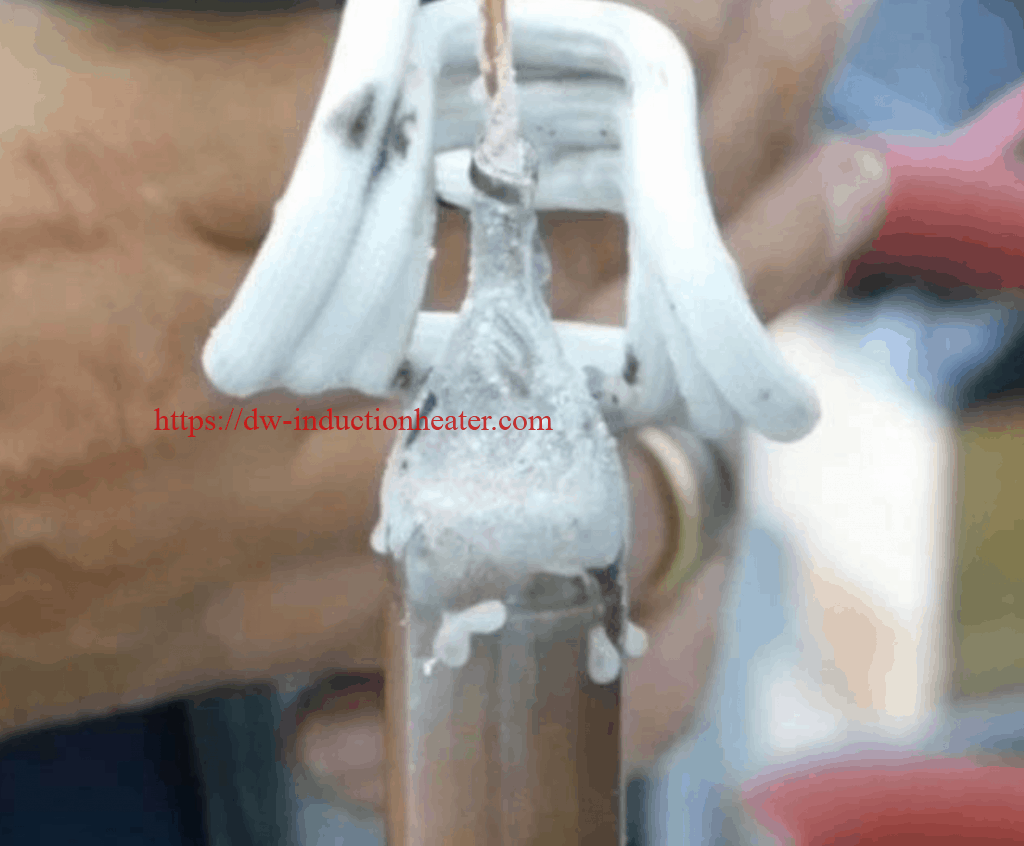
- Induction Brazing successfully in 5 seconds
- Precise control of the time and temperature
- Power on demand with rapid heat cycles
- Reduction in defects due to overheating
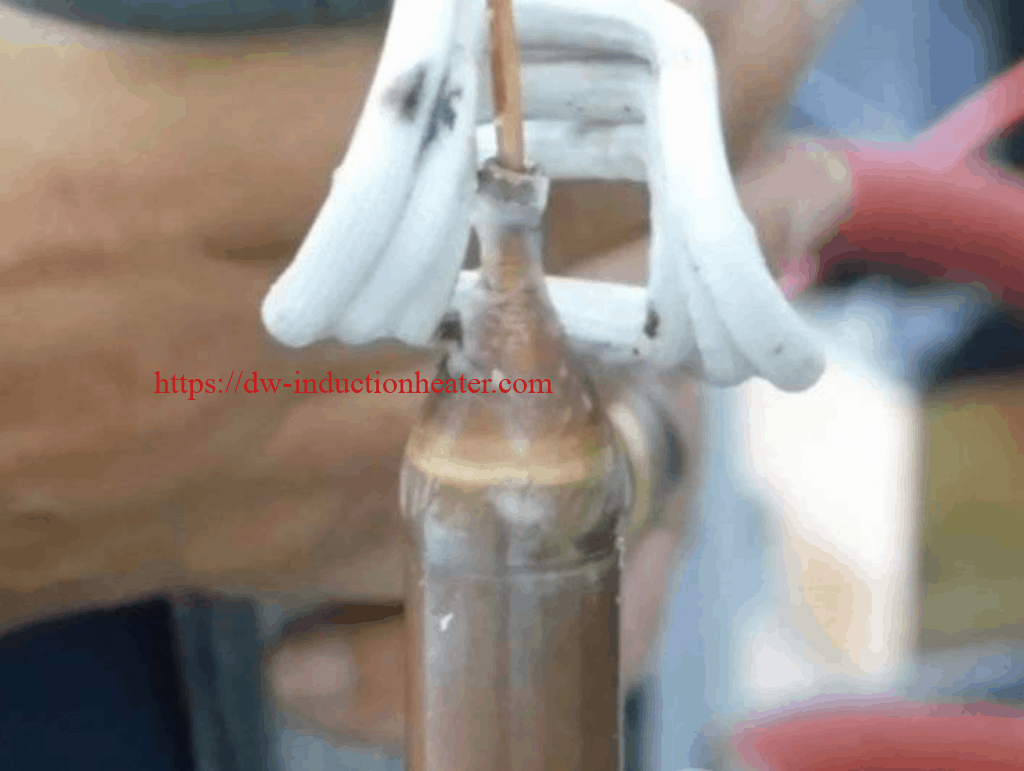

induction brazing brass pipe to brass part
Objective
High Frequency Induction Brazing brass pipe to brass part and a brass tip in under one minute using induction.
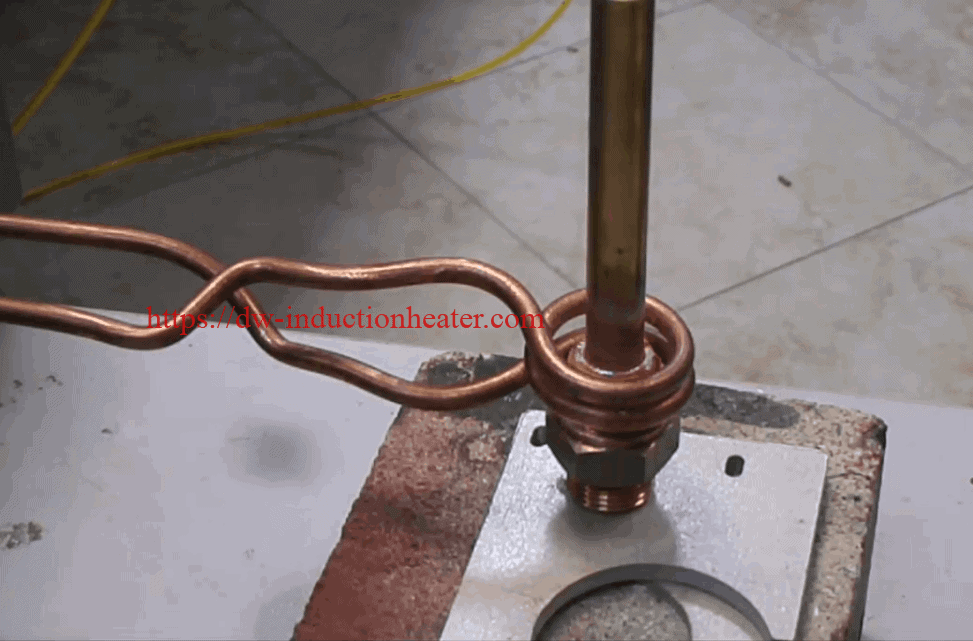
Equipment
DW-UHF-6KW-III handheld induction brazing machine
2 turns coil
Materials
• Wide brass part
• Brass pipe
• Silver-based brazing alloy, provided by customer
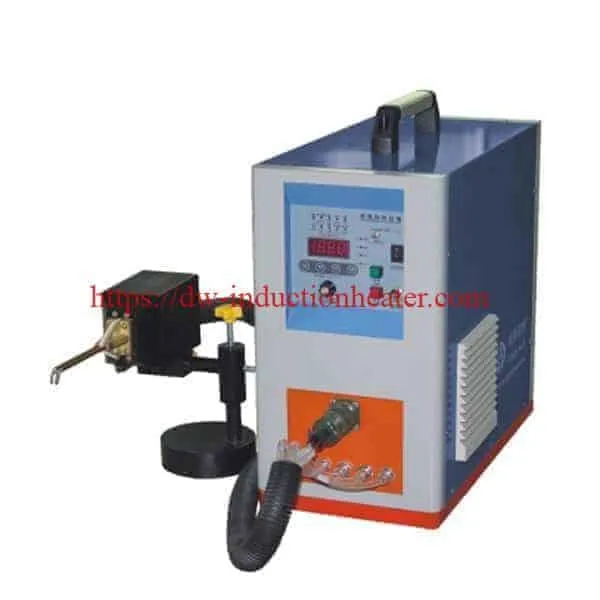
Test 2 – Pipe to tip:
Key Parameters
Power: 4.4 kW
Temperature: Approximately 1400° F (760° C)
Time: 17 sec
Process:
Test 1
Test 2
Results/Benefits:
Induction heating provides:
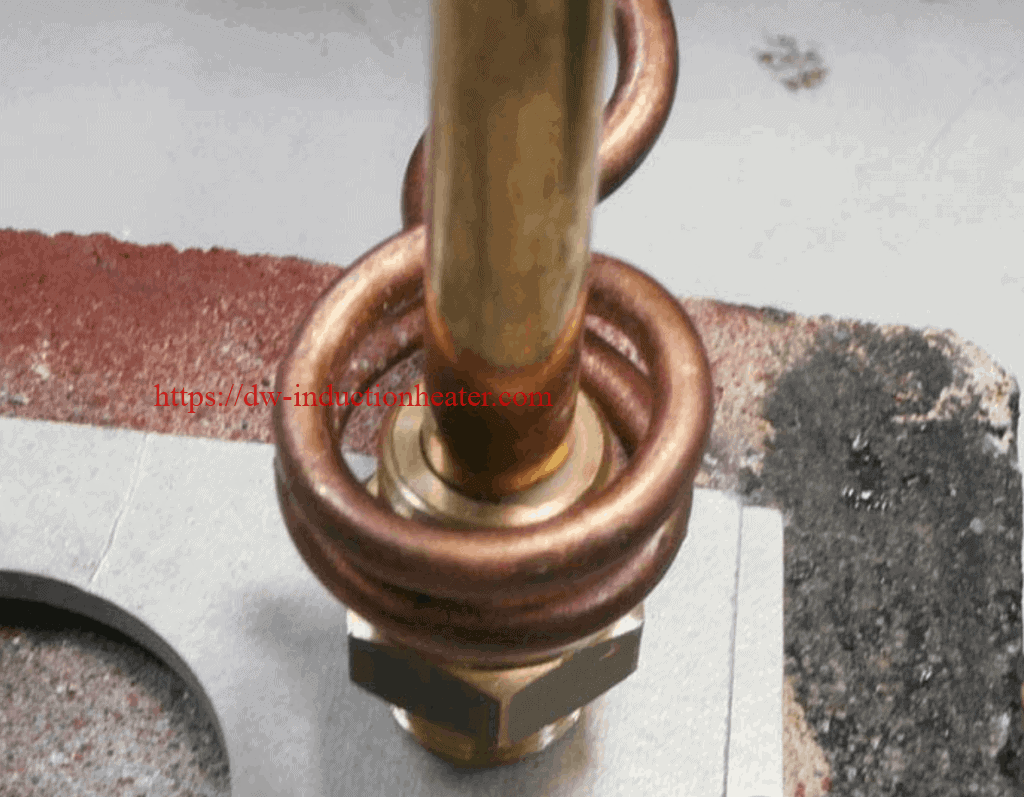
- The wide part and brass pipe are assembled and a brazing alloy ring is placed between them.
- The assembly is put inside the induction heating coil and induction heat is applied.
- The joint is completed in 38 seconds.
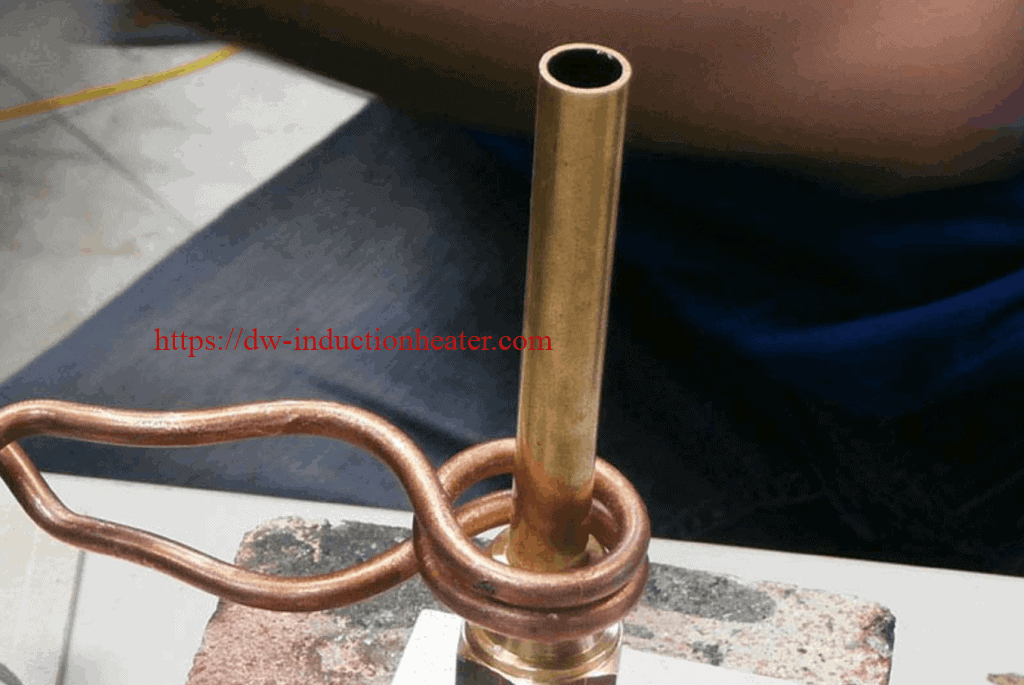
- The tip and pipe are assembled and a brazing alloy ring is placed between them.
- The assembly is put inside the coil and induction heat is applied.
- The joint is completed in 17 seconds.

- Strong durable joints
- Selective and precise heat zone, resulting in less part distortion and joint stress than welding
- Less oxidation
- Faster heating cycles
- More consistent results and suitability for large volume production, without the need for batch processing
- Safer process than flame brazing
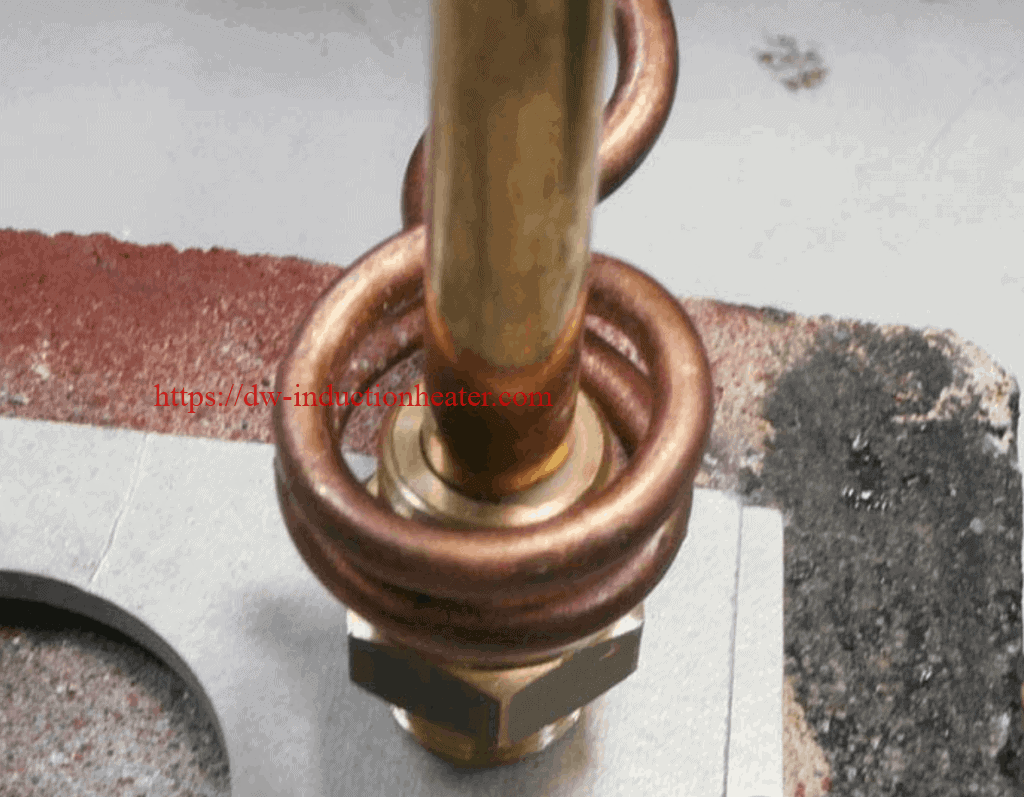
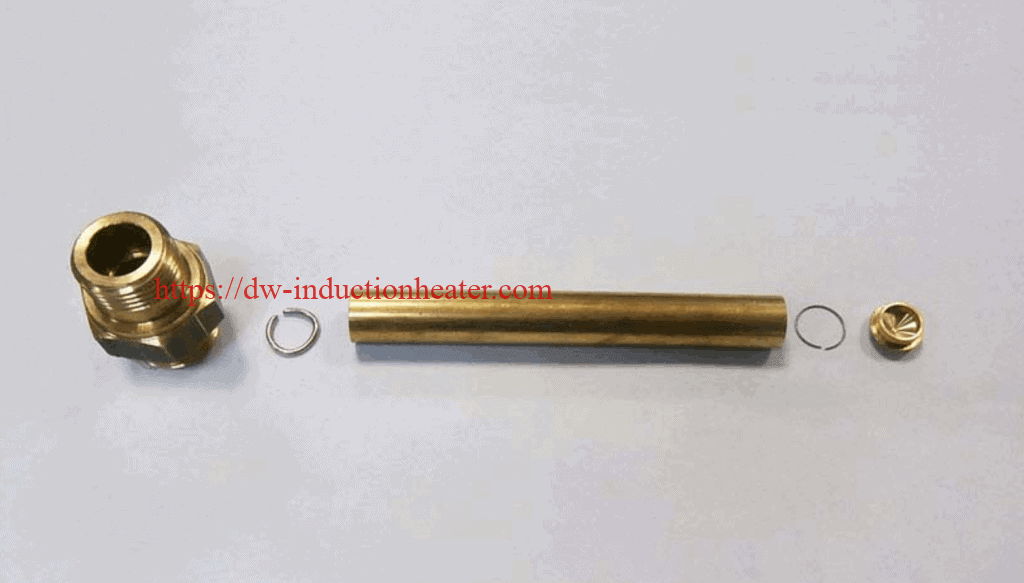
Induction Hot Plate
High Frequency Induction Hot Plate with a Tin Coating for Flow-Melting
Objective Heat a carbon steel plate coated with tin to 450 ºF (232 ºC) for flow-melting
Material 7.9” (200mm) x 4.7” (120mm) steel plates with a tin layer of 100 to 1000nm thickness, temperature sensing paint, water for quenching
Temperature 450 ºF (232 ºC)
Frequency 350 kHz
Equipment • DW-UHF-20kW induction heating system, equipped with a remote workhead containing two 0.5μF capacitors for a total of 0.25μF
• An induction heating coil designed and developed specifically for this application.
Process A nine turn “Dog Bone” style coil is used for the flow-melting process. The tin coated carbon steel plate is placed in the coil for 1.34 seconds to uniformly reflow the tin coating. The plate is then quenched in cool water to retain sufficient free tin at the surface.
Results/Benefits Induction heating provides:
• Uniform heating
• Rapid focused heat
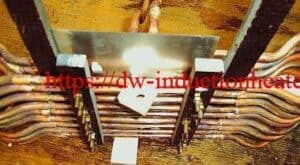

Brazing Aluminum Tubing to Aluminum Parts
Objective
The objective of the application test is induction brazing aluminum tubing to aluminum parts in less than 15 seconds. We have aluminum tubing and an aluminum “receiver”. The brazing alloy is an alloy ring, and has a flow temperature of 1030°F (554°C).
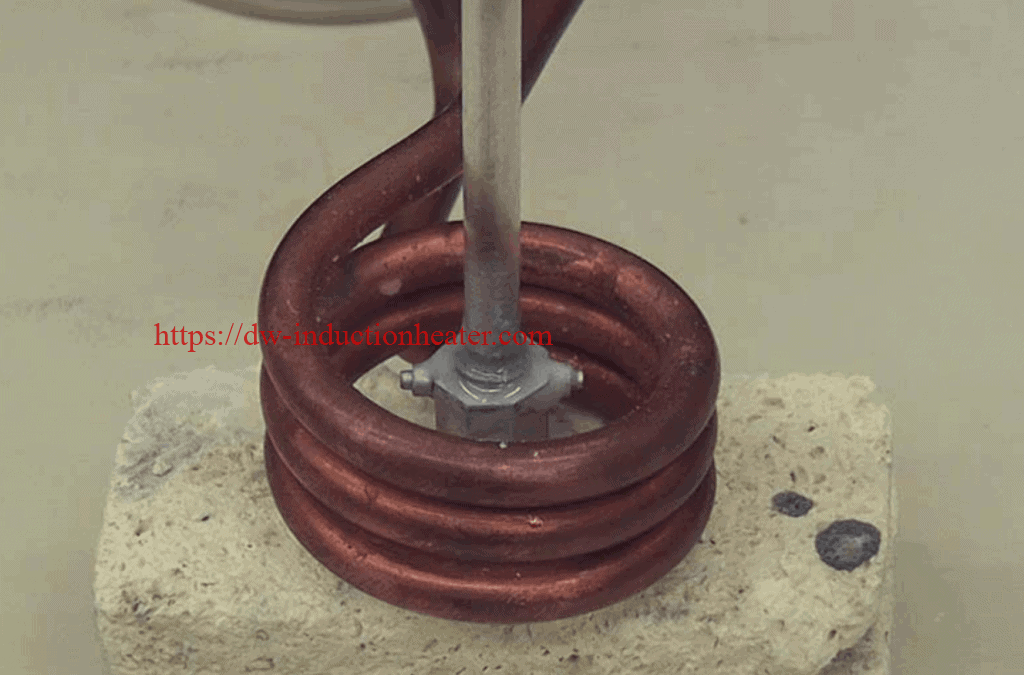
Equipment
DW-HF-15kw induction heating machine
[caption id="attachment_97" align="alignnone" width="267"]
induction heating machine HF-15[/caption]
Induction heating coil
Materials
• Aluminum tube: 0.167” (4.242mm) OD, 0.108” (2.743mm) ID
• Aluminum component: ID .1675” (4.255mm), depth .288” (7.315mm),
chamfer at top area is 0.2375” (6.033mm) ID max
• Braze alloy in the form of two-turn alloy ring
• Flux
Key Parameters
Temperature: 1030°F (554°C)
Power: 5 kW
Time: 14 seconds
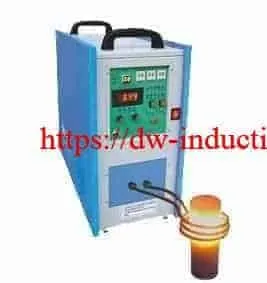

Process:
Results/Benefits:
The 5 kW induction heating system requested by the customer, will meet the customer’s time requirements for induction brazing.

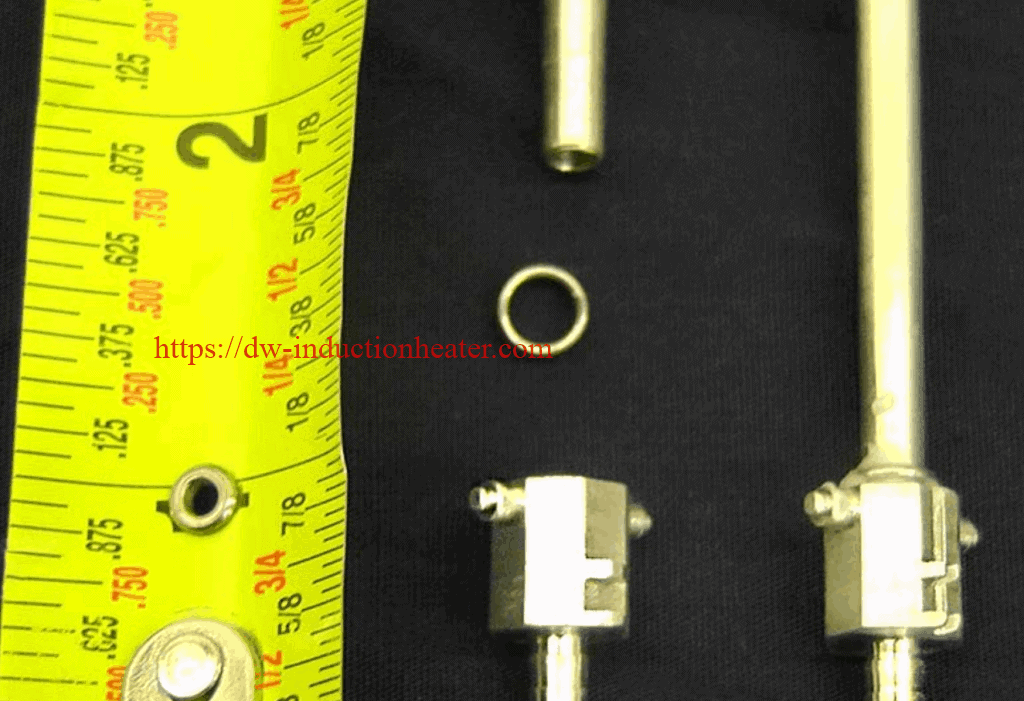
- The Aluminum component and tube were assembled together with the alloy ring. Flux was added.
- The part was positioned in the induction coil.
- Several tests were conducted with different cycle times to confirm the heating time for a good braze.
- At 15 seconds the assembly melted.
- At 14 seconds, we had success for brazing aluminum to aluminum, and a good quality braze joint was achieved.

- Precise control of the time and temperature
- Power on demand with rapid heat cycles
- Repeatable process, not operator dependent
- Safe induction heating with no open flames
- Energy efficient heating

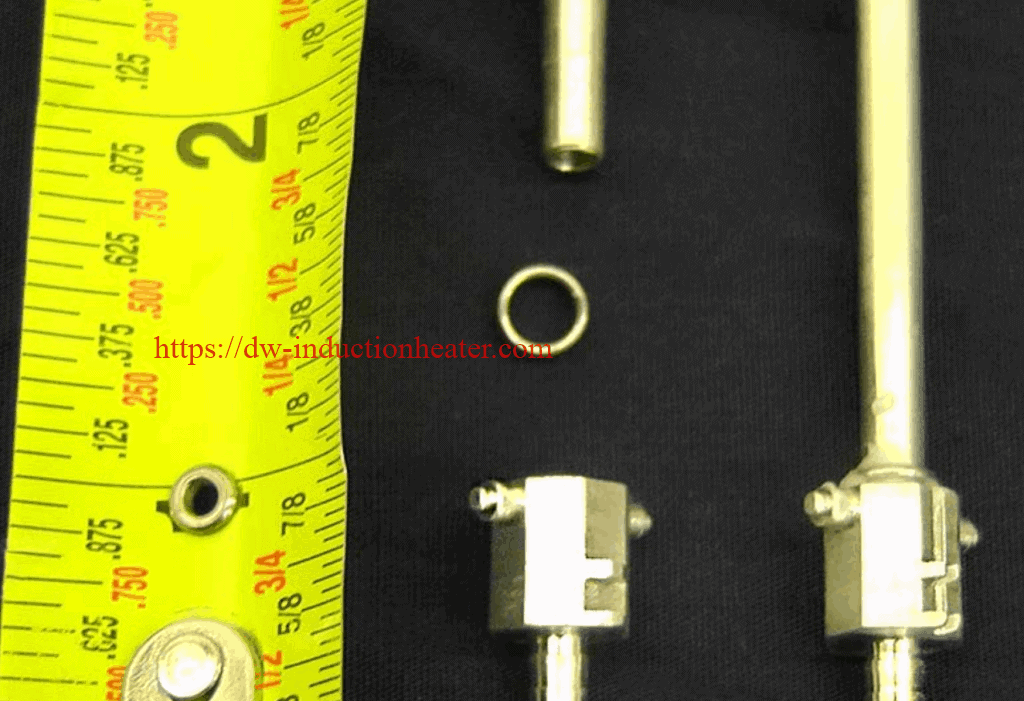
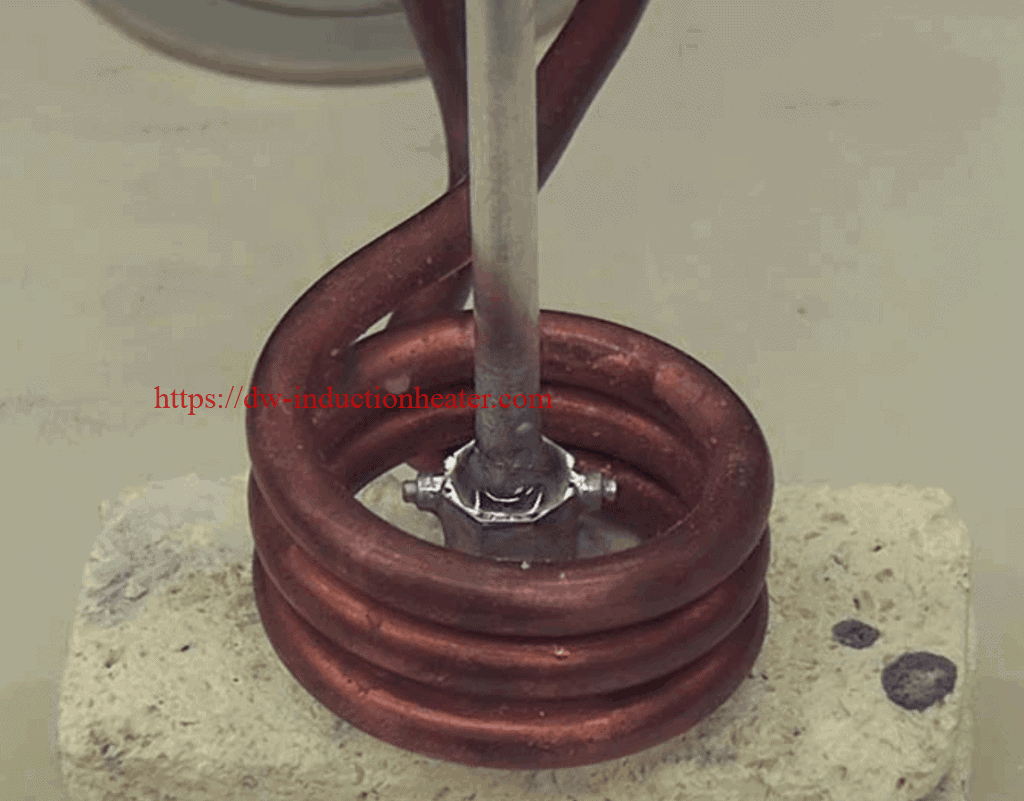
订阅:
博文 (Atom)
关注者
博客归档
-
▼
2022
(1729)
-
▼
十一月
(184)
- Induction Melting Videos
- Induction Preheat Welding Systems
- induction fluid pipe heater
- Induction Catheter Tipping Heating
- induction seam welder
- Brazing Carbide Tool Tips With Induction
- Induction Soldering Coaxial Cable
- Induction Brazing copper wire to copper cylinder
- induction brazing brass pipe to brass part
- Induction Hot Plate
- Brazing Aluminum Tubing to Aluminum Parts
- Brazing Eyeglass Frames With Induction
- KN95 mask ultrasonic mask welder for nonwoven fabr...
- high frequency induction seam welder
- Brazing Thin Copper Tube With Induction
- high frequency induction seam welder
- Induction Soldering Circuit Board
- Induction forging and induction hot forming
- Induction Heating Plasma
- induction heating nanoparticle solution
- Induction Brazing Brass Studs to Copper Pipes
- Why choose Induction Brazing?
- Induction Soldering Brass Corner Joint
- Induction Seam Welding For Tube and Pipe
- induction heating stainless steel wire cable
- Induction Soldering Coaxial Cable to Connector Ring
- High Frequency Induction Welding Tube and Pipe Sol...
- Tilting Crucible Melting Induction Furnace
- Brazing copper tube to brass fitting
- Brazing Copper to Brass Pipe With Induction
- Soldering Steel To Brass With Induction Heater
- Research and Design on IGBT Induction Heating Powe...
- Magnetic Induction Heating Boiler
- induction heating steel cable for cutting
- Induction Drying Grain with Induction Heating method
- Induction Heating Steel Part For Hot Heading
- induction fluid pipe heater
- induction hardening steel handheld stamps
- Induction heating of cylindrical nonmagnetic ingots
- Induction Brazing Aluminum Tube T Joints
- Induction Brazing copper wire to copper cylinder
- induction hardening process
- induction heating for surface quenching of steel
- Induction Heating Molding Catheter Tip
- Automatic Induction Forging Video
- Induction inline wire heating process
- Induction Drying Grain with Induction Heating method
- induction curing
- Induction Soldering Coaxial Cable
- How to design induction heating coil
- Induction Hardening Surface Process
- Induction Soldering Wires Onto Connection
- Induction Brazing Carbide Tipping of Medical Tools
- Heating Shrink Fitting Camshaft Gear
- Induction Wire and Cable Heating
- Induction Bending Pipe-Tube
- induction heating steel cable for cutting
- Handheld Brazing Stainless Steel Tube
- induction preheating copper rod for hot forging
- Induction Wire and Cable Heating
- Brazing Copper Bars with Induction
- induction heating for surface quenching of steel
- Induction Brazing Carbide Tipping on Cutting Steel...
- Induction Brazing Aluminum Automotive
- Induction Wire and Cable Heating
- ultrasonic welding fabric machine for bonding nonw...
- Induction Soldering Wire To Aluminum Lug
- Research and Design on IGBT Induction Heating Powe...
- Induction Susceptor Heating
- Induction Brazing Copper Tube For Refrigeration
- Tilting Crucible Melting Induction Furnace
- Induction Soldering Brass to Steel Plate
- How Induction Heating works?
- Induction inline wire heating process
- Induction Brazing Carbide Tipping on Cutting Steel...
- Induction Hot Forming Steel Pipe
- Induction Soldering Wire of Co-axial
- Induction Soldering Copper Tap
- What is induction welding?
- High Speed Heating by Induction Heating System
- Melting Aluminum Tilting Crucible Induction Furnace
- What Is Induction Heating?
- induction preheating before welding steel pipe
- induction brazing copper and brass rods
- PDF of Induction Heating Principle and Applicatons
- Induction Billets Heater Video
- Brazing Carbide Tool Tips With Induction
- Induction Wire Heating Process Applications
- Induction Shrink Fitting For Inserts
- Induction Soldering Steel Parts
- Brazing Silver To Copper With Induction
- High Frequency Induction Brazing Diamond Inserts
- Why choose Induction Brazing?
- Induction Brazing Carbide to Steel
- What is induction welding?
- Brazing stainless steel with induction
- RF Soldering Circuit Board
- Induction Soldering magnetic steel pins
- Technology of Induction Forming Steel Plate
- Brazing Silver To Copper With Induction
-
▼
十一月
(184)
我的简介

- HLQ induction heating machine
- HLQ induction heating machine manufacturer provides the service of induction brazing,melting,hot forming,hardening surface,annealing,shrink fitting,PWHT,etc.