The principle of induction steam boilers|
electromagnetic induction steam generators|induction heating steam boilers
This invention relates to an induction steram boiler|electromagnetic
induction steam generator which operates with a low-frequency alternating current electric power source. More specifically, this invention relates to an electromagnetic induction steam boiler which is compact and highly efficient being capable of continuous operation, intermittent operation and empty-heating operation.
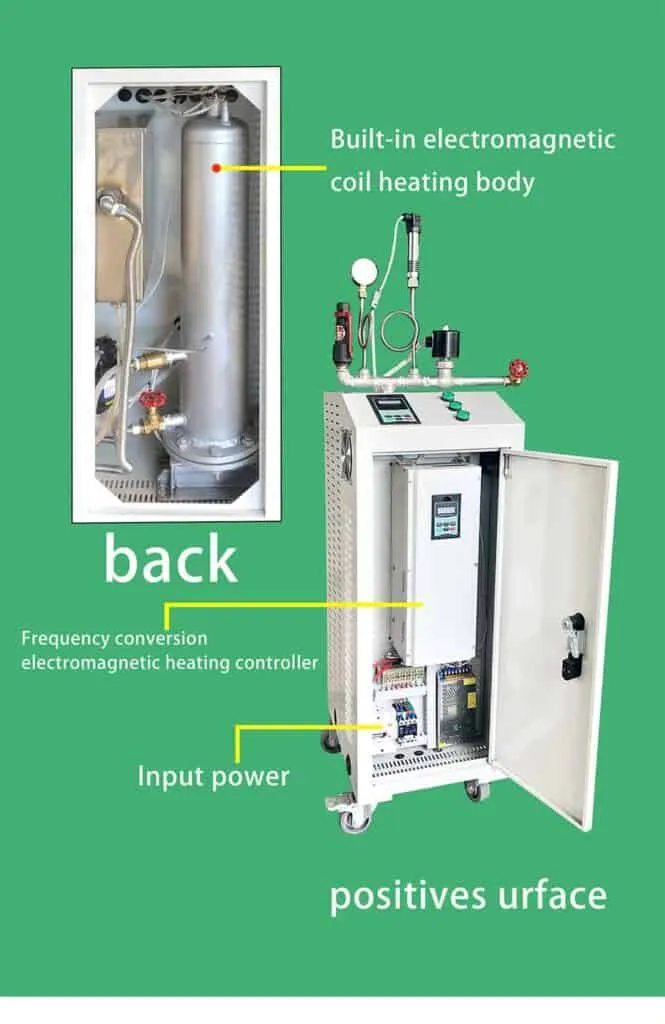
Steamers in current use, such as cooking steamers, convection ovens, cooking steam warmers, steamers for defrosting frozen food, steamers for processing tea leaves, steam baths for household use, steamers for cleaning, and steamers used in restaurants and hotels, are widely used as equipment for utilizing the steam they generate.Generally, fossil fuels (gas, petroleum, crude petroleum, coal and so forth) are burned as heat sources for large steamers in current use. This heating method, however, is not economical for compact steamers.
Relatively compact steamers in current use commonly employ electrical resistance heaters as a heat source. Such steamers obtain steam intermittently by spraying water on an iron plate which has been heated in advance with a heater or the heater's protecting tube from inside or beneath the plate.
Energy saving rate of electromagnetic induction steam boiler:
Because the iron container heats itself, the heat conversion rate is particularly high, which can reach more than 95%; the working principle of electromagnetic steam generator is that when some water enters the container, it will be heated into steam Drain, to ensure a fixed way of replenishing water, there will be continuous steam utilization.
Product Description
Industrial quality high pressure induction steamist boiler pure steam generator from china manufacturers
1) LCD Full-Automatically Intelligent Electronic Control System
2) High-quality Core Component——
Electromagnetic induction heater
3) High-quality Components and Parts——Famous Brand Delixi Electrical Appliance
4) Multiple Safety Interlock Protection
5) Scientific Design and Attractive Appearance
6) Easy and Rapid Installation
7) Magnetic induction coil heat up boiling water Generate steam - Is Much More Eco-Friendly and Economical
8) Wide Application Range
Item content / model |
Rated power
(KW) |
Rated steam temperature
(℃) |
Rated current
(A)
|
Rated steam pressure
(mpa)
|
Evaporation
(kg/h) |
Thermal efficiency
(%)
|
Input voltage
(V/HZ) |
Cross section of input power cord
(MM2)
|
Steam outlet diameter
|
Relief valve diameter |
Inlet diameter |
Drainage diameter |
Overall dimensions
(mm)
|
HLQ-10 |
10 |
165 |
15 |
0.7 |
14 |
97 |
380/50HZ |
2.5 |
DN20 |
DN20 |
DN15 |
DN15 |
450*750*1000 |
HLQ-20 |
20 |
165 |
30 |
0.7 |
28 |
97 |
380/50HZ |
6 |
DN20 |
DN20 |
DN15 |
DN15 |
450*750*1000 |
HLQ-30 |
30 |
165 |
45 |
0.7 |
40 |
97 |
380/50HZ |
10 |
DN20 |
DN20 |
DN15 |
DN15 |
650*950*1200 |
HLQ-40 |
40 |
165 |
60 |
0.7 |
55 |
97 |
380/50HZ |
16 |
DN20 |
DN20 |
DN15 |
DN15 |
780*950*1470 |
HLQ-50 |
50 |
165 |
75 |
0.7 |
70 |
97 |
380/50HZ |
25 |
DN20 |
DN20 |
DN15 |
DN15 |
780*950*1470 |
HLQ-60 |
60 |
165 |
90 |
0.7 |
85 |
97 |
380/50HZ |
25 |
DN20 |
DN20 |
DN15 |
DN15 |
780*950*1470 |
HLQ-80 |
80 |
165 |
120 |
0.7 |
110 |
97 |
380/50HZ |
35 |
DN25 |
DN20 |
DN15 |
DN15 |
680*1020*1780 |
HLQ-100 |
100 |
165 |
150 |
0.7 |
140 |
97 |
380/50HZ |
50 |
DN25 |
DN20 |
DN25 |
DN15 |
1150*1000*1730 |
HLQ-120 |
120 |
165 |
180 |
0.7 |
165 |
97 |
380/50HZ |
70 |
DN25 |
DN20 |
DN25 |
DN15 |
1150*1000*1730 |
HLQ-160 |
160 |
165 |
240 |
0.7 |
220 |
97 |
380/50HZ |
95 |
DN25 |
DN20 |
DN25 |
DN15 |
1150*1000*1880 |
HLQ-240 |
240 |
165 |
360 |
0.7 |
330 |
97 |
380/50HZ |
185 |
DN40 |
DN20 |
DN40 |
DN15 |
1470*940*2130 |
HLQ-320 |
320 |
165 |
480 |
0.7 |
450 |
97 |
380/50HZ |
300 |
DN50 |
DN20 |
DN50 |
DN15 |
1470*940*2130 |
HLQ-360 |
360 |
165 |
540 |
0.7 |
500 |
97 |
380/50HZ |
400 |
DN50 |
DN20 |
DN50 |
DN15 |
2500*940*2130 |
HLQ-480 |
480 |
165 |
720 |
0.7 |
670 |
97 |
380/50HZ |
600 |
DN50 |
DN20 |
DN50 |
DN15 |
3150*950*2130 |
HLQ-640 |
640 |
165 |
960 |
0.7 |
900 |
97 |
380/50HZ |
800 |
DN50 |
DN20 |
DN50 |
DN15 |
2500*950*2130 |
HLQ-720 |
720 |
165 |
1080 |
0.7 |
1000 |
97 |
380/50HZ |
900 |
DN50 |
DN20 |
DN50 |
DN15 |
3150*950*2130 |
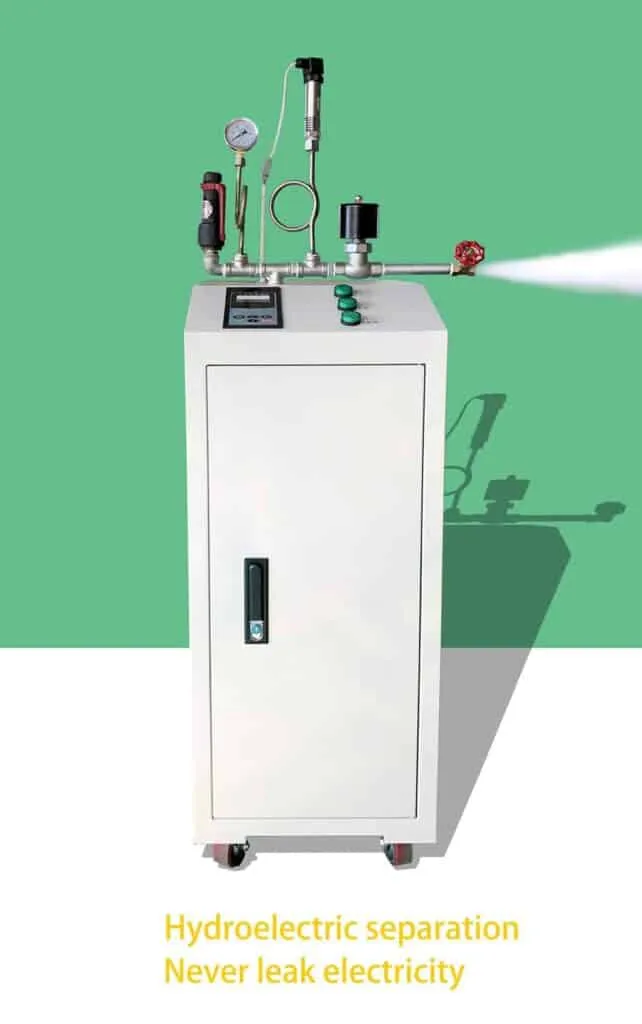
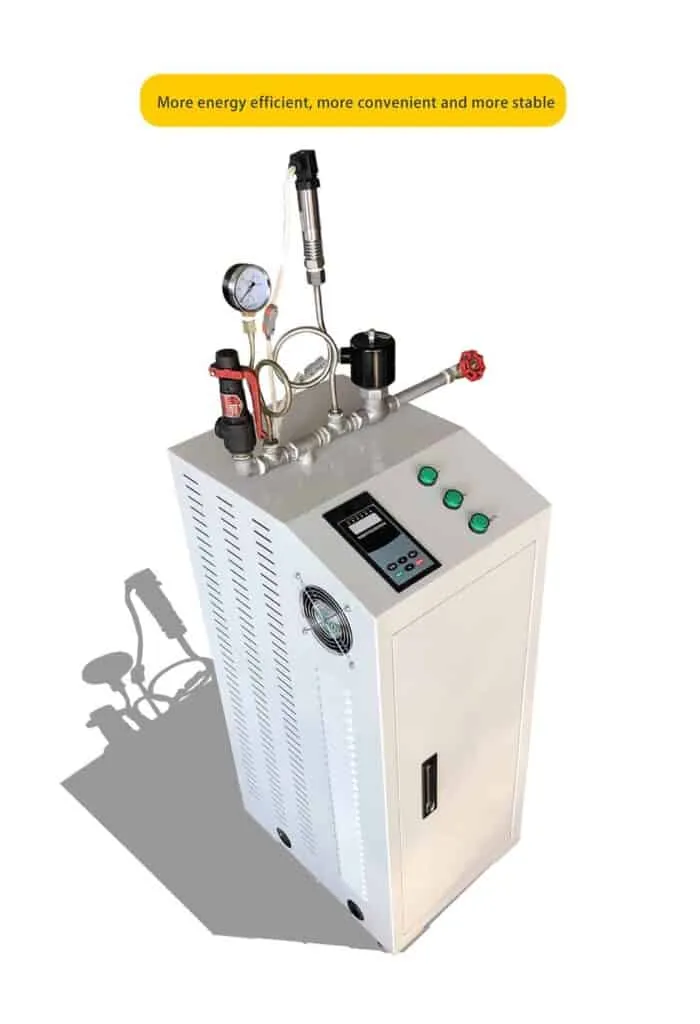
Advantages & Features of Electromagnetic Induction Heating System:
-Save electricity 30%~80%, especially for big power machine.
- No influence on working environment: high frequency heating system has heat energy utilization rate of 90%+.
- Heating fast, accurate temperature control
- Can work for a long time in harsh environments
- High frequency heating system make heating power bigger compare to traditional resistance wire heating.
- No unsafe factors compare to traditional heating: temperature on surface of material container about 50°C~80°C.
Features of Induction Steam Generator:
1) LCD Full-Automatically Intelligent Electronic Control System
2) High-quality Core Component——Electromagnetic induction heater
3) High-quality Components and Parts——Famous Brand Electrical Appliance
4) Multiple Safety Interlock Protection
5) Scientific Design and Attractive Appearance
6) Easy and Rapid Installation
7) Magnetic induction coil heat up boiling water Generate steam - Is Much More Eco-Friendly and Economical
8) Wide Application Range
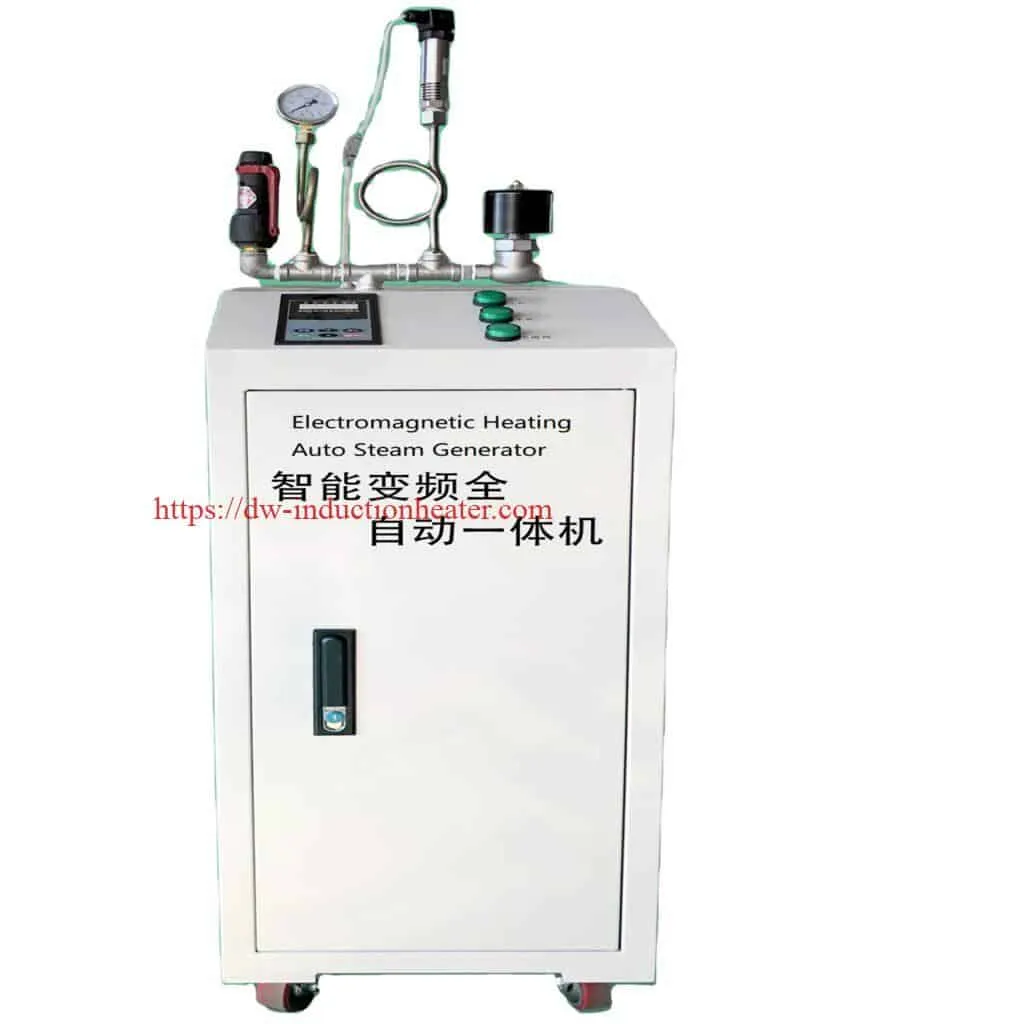
Applications of Electromagnetic Induction Heating Steam Generators
1, widely applied in food industry: like steam box, Dofu machine, sealing machine, sterilization tank, packing machine , coating machine and so on.
2, applications cases in biochemical industry: fermenter, reactor, sandwich pot, blender, Emulsifier and etc.
3, gradually be applied in washing industry like ironing table, washing machine dryer, drying and cleaning machine, washing machine and glue machine etc.
Comparison of Different Types of Steam Generators |
Steam Generator Type |
Gas Steam Generator |
Resistance Wire Steam Generator |
Coal Steam Generator |
Electromagnetic Heating Steam Generator |
Energy Used |
Gas by Fire |
Resistance Wire by Electricity |
Coal by Fire |
Electromagnetic Heating by Electricity |
Heat Exchange Rate |
85% |
88% |
75% |
96% |
Need Someone on Duty |
Yes |
No |
Yes |
No |
Temperature Control Accuracy |
±8℃ |
±6℃ |
±15℃ |
±3℃ |
Heating Speed |
Slow |
Quick |
Slow |
Very quick |
Working Environment |
A little pollution after fired |
Clean |
pollution |
Clean |
Production Risk Index |
Risk of gas leakage, complicated pipelines |
Risk of electricity leakage pipe inner wall easy be scaling |
Risk of high temperature, heavy pollution |
No risk of leakage, water & electricity separated completely |
Operational Performance |
Complicated |
Simple |
Complicated |
Simple |
Application of induction heating steam generators|induction heating steam boilers: