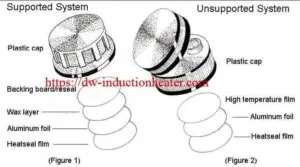
2022年3月7日星期一
Heating Aluminum Foil For Cap Sealing
Induction Heating Aluminum Foil For Cap Sealing with IGBT inductive heater
Objective An induction heater is used to heat a polymer laminated aluminum foil in 0.5 to 2.0 seconds. The heat produced in the aluminum foil melts the polymer that bonds to the neck of a plastic container.
Material Aluminum foil, polyethylene, polypropylene, polyvinylchloride, polystyrene, polyethylene terephthalate, styrene acrylonitrile
Temperature 300 - 400 (ºF), 149 - 204 (ºC)
Frequency 50 to 200 kHz
Equipment DAWEI solid-state induction power supplies operating between 1 & 10 kW at frequencies of 50- 200 kHz. These units operate with remote sealing heads which allows the main power cabinet of the equipment to be located away from the immediate production area. Distances of up to 100 meters are possible. The microprocessor is used to control
and protect the system and ensures that the optimal operating frequency is maintained at all times and that each container
receives the same amount of heat energy from cycle to cycle.
Process Two different types of aluminum foil laminates are available for this application. The first assembly includes backing
board/reseal, a wax layer, aluminum foil, and a heatseal film for supported systems (Figure 1). The second assembly includes a high temperature film, aluminum foil, and a heatseal film for unsupported systems (Figure 2). The procedure is to fit the foil membrane into the cap and to fit the cap to the container after the product is filled.
Results For the aluminum foil assembly as shown in Figure 1, heat induced in the metallic foil by the induction coil almost
instantaneously melts the polymer coating and the neck of the container forming a hermetic seal between the heat seal film
and the rim of the container. The heat also melts the wax between the aluminum foil and the back board. The wax is
absorbed into the back board. This results in an air tight bond between the aluminum foil/membrane and the rim of the
container, the back board is released and remains in the cap.
Process (cont’d) In the case of unsupported membranes in Figure 2, one side of the aluminum foil is coated with a heat sealable polymer film and this face that will be in contact with and sealed to the container. The other side of the foil that will be in contact with the cap has a higher melting-point film that prevents adhesion of the aluminum to the cap allowing the end user to unscrew the cap. Unsupported membranes are typically used where the end user pierces the tamper evident membrane prior to dispensing the product. The aluminum foil acts as a vapor barrier preserving the freshness of the product and prevents it from drying.
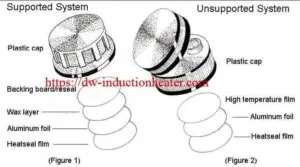
关注者
博客归档
-
▼
2022
(1729)
-
▼
三月
(100)
- Brazing stainless steel with induction
- Induction Soldering Stainless Steel Tubes to Brass...
- Electromagnetic Induction Heating Steam Generators
- Induction Aluminum Brazing Process
- Electromagnetic Induction Heating Steam Generators
- Induction Heating Steel Mold
- Induction Soldering Brass Tube-Pipe
- Brazing Copper to Brass Pipe With Induction
- induction surface hardening steel screws
- Induction Catheter Tipping Heating
- Induction Preheating Welding Steel Pipe
- induction brazing automotive copper heating exchan...
- Brazing Aluminum Pipes Assembly With Induction
- What is induction hardening?
- Induction Heating Wires For Hot Heading
- Shrink Fitting Assemble Connecting Rods
- Induction Preheating Welding Steel Pipe
- Induction Annealing Copper Tubes
- Induction Brazing Heating Exchanger Copper Pipes
- Brazing Joining Copper Connectors With Induction
- Brazing Copper Bars with Induction
- Induction Drying Grain with Induction Heating method
- Brazing Brass Pipe With Induction
- induction heating reactor tank-vessels
- induction soldering fiber optic cable
- Magnetic Induction Heating Boiler
- Brazing carbide shaft with induction
- Brazing carbide shaft with induction
- Induction Hardening and tempering
- Induction Soldering Coaxial Cable
- Induction Soldering Copper Pipes to PCB Board
- Induction Annealing Aluminum
- induction hot forming and forging process
- Ultrasonic Plastic Welding Machine For Bonding The...
- induction heating graphite susceptor
- Brazing Copper Tube to Brass Fitting With Induction
- Induction Curing Heating of Organic Coating
- Induction forging and induction hot forming
- induction curing
- Brazing Carbide-Steel Tool with Induction
- Induction Brazing Heating Exchanger Copper Pipes
- Research and Design on IGBT Induction Heating Powe...
- Brazing Aluminum Tubes with Induction Heating
- Induction Brazing Carbide Onto Steel Part
- Induction Soldering Copper Wire Connectors
- Induction Soldering Stainless Steel To Wire
- Annealing Saw Blades with Induction
- Brazing Carbide Tips To Steel With Induction
- induction Brazing copper rods to brass strips
- Aluminum Scrap Melting Recycling Induction Furnace
- Induction Soldering Coaxial Cable to Connector Ring
- induction heating for drying food processing industry
- Induction Brazing Copper To Copper Parts
- Induction Heating Bolts
- Small High Frequency Induction Melting Furnace
- induction heating stainless steel wire cable
- how does induction heating work?
- Induction Hardening and tempering
- Brazing Golf Ball With Induction
- how does induction heating work?
- Brazing Stainless Steel To Copper With Induction
- Induction Heat Treating Surface Process
- Brazing Brass Fittings With Induction
- Induction Tempering Spring
- Induction Heating Aluminum Catheter Tipping
- induction heating nanoparticle solution
- What Is Induction Heating?
- Brazing Carbide Tool Tips With Induction
- Brazing Stainless Steel To Copper With Induction
- Induction Fluid Pipeline heating system
- Billet Heating Furnace with Induction Heating
- Small High Frequency Induction Melting Furnace
- Brazing Brass Pipe With Induction
- Induction Soldering Brass To Copper
- Brazing Aluminum Pipes Assembly With Induction
- Induction Soldering Brass Tube-Pipe
- Heating Aluminum Foil For Cap Sealing
- how does induction heating work?
- induction heating stress relieving
- Induction Brazing Aluminum to Aluminum Tube
- Soldering Steel To Brass With Induction Heater
- Brazing Steel To Steel Pipe With Induction
- Induction Susceptor Heating
- Induction Brazing Copper T Pipe With Induction Hea...
- Shrink Fitting Assemble Connecting Rods
- Magnetic Induction Heater Manufacturer
- Induction Aluminum Brazing with Computer Assisted
- Induction Hot Plate
- Billet Heating Furnace with Induction Heating
- induction heating for surface quenching of steel
- induction heating steel cable for cutting
- Electromagnetic Induction Heater
- Electromagnetic Induction Heater
- Induction Brazing Copper Assembly
- Brazing Joining Copper Connectors With Induction
- Induction Brazing Steel Wire
- Induction Heating Magnetic Iron Oxide
- Induction Soldering Steel Cover
- Induction Heating Chemical Reactor
- Induction Annealing Aluminum PIpe
-
▼
三月
(100)
我的简介

- HLQ induction heating machine
- HLQ induction heating machine manufacturer provides the service of induction brazing,melting,hot forming,hardening surface,annealing,shrink fitting,PWHT,etc.