2023年1月31日星期二
Brazing Carbide-Steel Tool with Induction
Induction Brazing Copper Pipe Fittings
induction brazing stainless steel to steel
High frequency magnetic induction brazing stainless steel to steel process
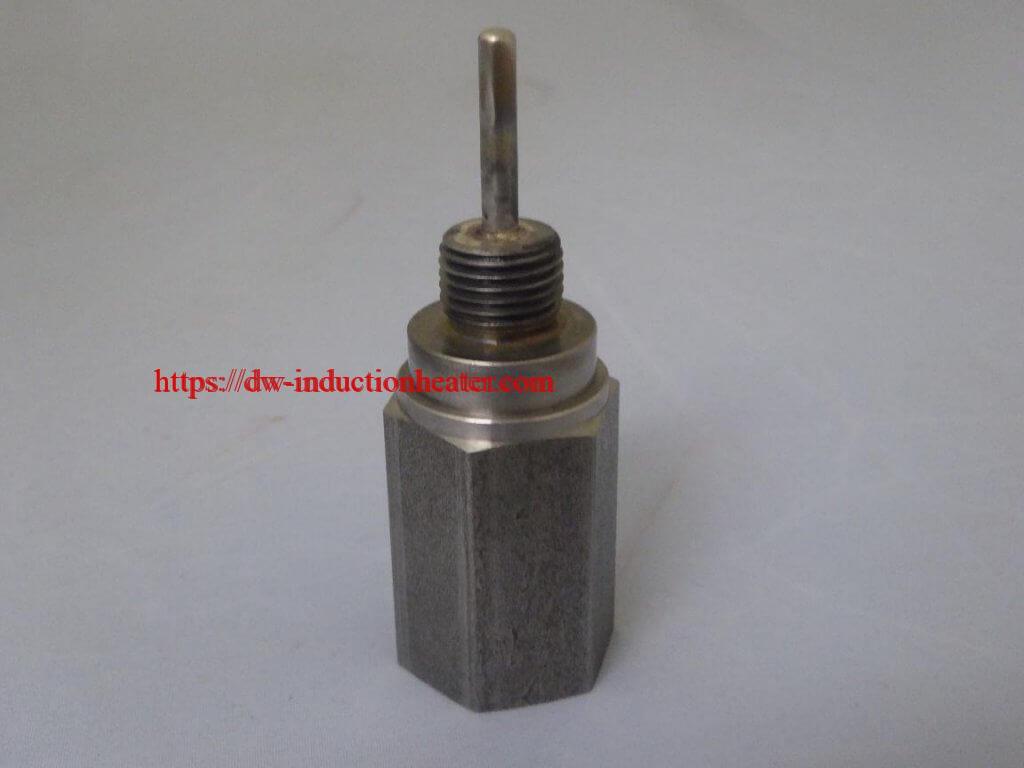


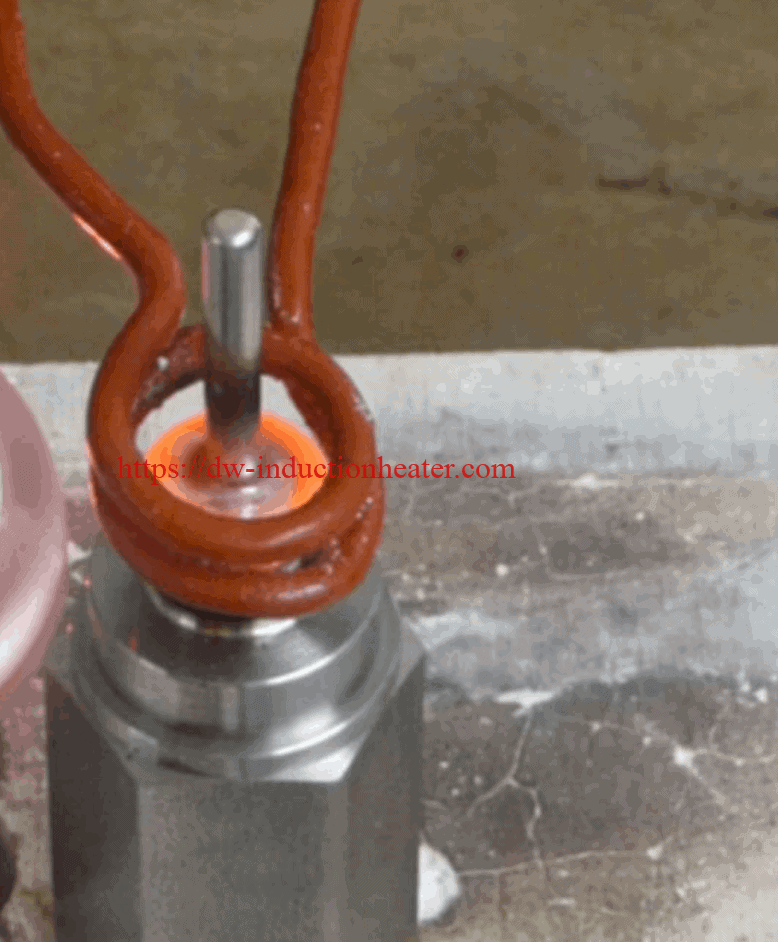
Induction inline wire heating process
Induction inline wire heating process
Objective Induction Heat several different inline wire diameters to 204°C (400°F) in 0.8 seconds with the same induction coil.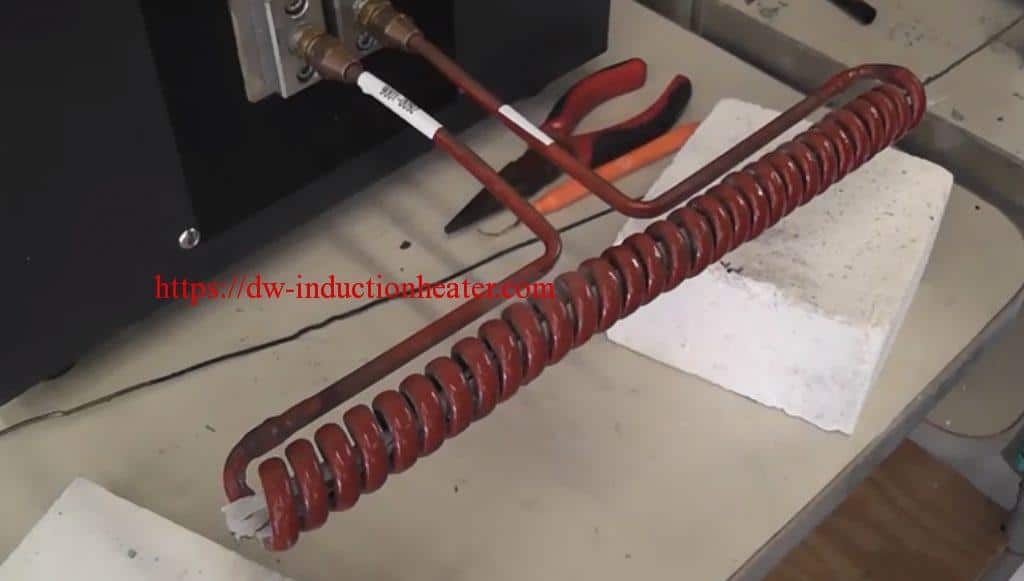
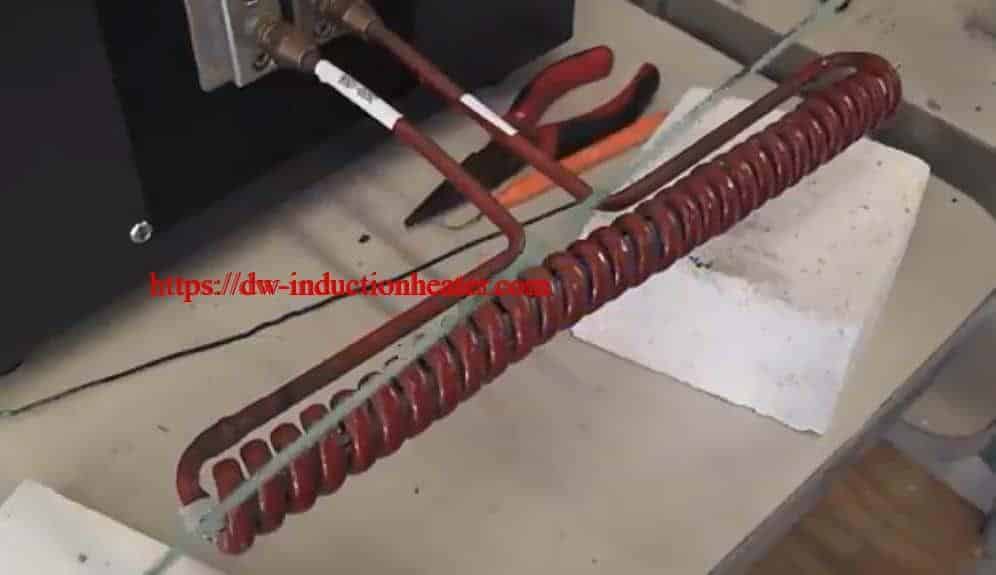
induction coating removal for removing paint
induction coating removal for removing paint
Induction coating removal principle
The induction disbonder works by the principle of induction. Heat is generated in the steel substrate and the bonding is broken. The coating is then removed entirely without disintegrating and completely free from contaminating agents, i.e. blast media.This obviously makes disposal and recycling of waste easier and cheaper. Even inside the pittings and cracks in the surface the coating is disbonded. The HLQ Induction heating works by fast transfer of energy to the steel substrate, as a result securing a controlled heating of the surface and fast removal of most types of coatings.What is induction coating removal?
The HLQ Induction coating removal system is a state-of-the-art induction heating tool that rapidly strips paint and tough, high-build coatings. It is a faster, cleaner and safer way to strip coatings.
What are the benefits?
Induction heating can outperform traditional paint-stripping methods. Abrasive blasting or disk grinding are generally more labour intensive and come with other issues such as the cost of enclosure or containment and collection of blast media, plus the filtration or separation of the coating materials for disposal. In many urban projects these are prime considerations and extremely costly to overcome. Whereas, when coatings are removed by induction, the only waste is the coating itself which in most cases can be swept or even vacuumed like any other workshop waste.
Safer working environment: The controlled, localized heat results in significantly reduced fumes and toxic dust.
Easy clean-up: The coating material mainly peels off in flakes rather than being pulverized.
Noiseless operation: Operators can work in public areas without creating a disturbance.
Mobile: The equipment is rugged and reliable but still light-weight and easy to move around worksites.
Reduced energy consumption: Fast, accurate and repeatable heat delivery makes the coating removal process extremely energy efficient.
Method flexibility: Spot heating, scanning, freehand and semi-automatic.
No limitations: The system can be used at flat surfaces, round contours, inside/outside corners, both sides of substrate, round rivets, etc.
Where is it used?
Induction coating removal is used in many industries, such as ships/marine, buildings, storage tanks, pipelines, bridges and offshore.
induction heating involves using alternating current and an induction coil to generate a powerful electro-magnetic field. When used properly, this field generates heat below a coating on a steel substrate, resulting in the coating de-bonding quickly and easily from the metal surface. At Alliance, we use this process to remove coatings from steel such as:
- Multiple coatings including epoxies, urethanes and others
- Lead paint
- Fire-retardant coatings (PFPs)
- Glued and vulcanized rubber as well as chlorinated rubber
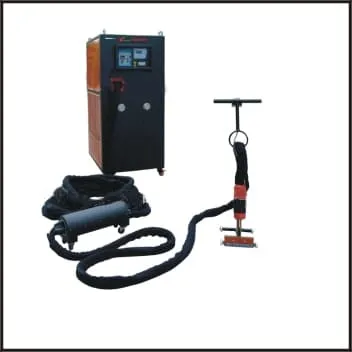
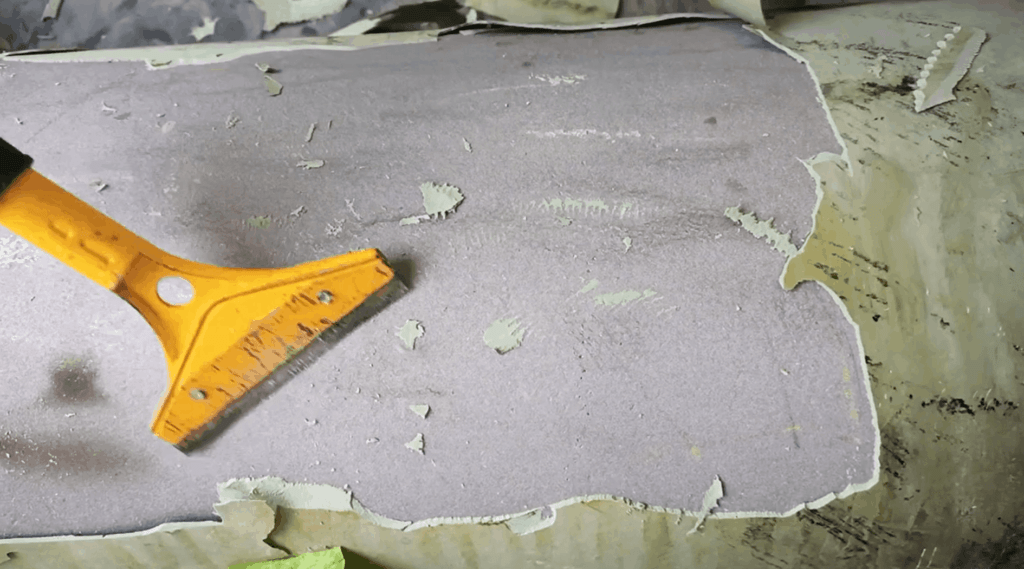

induction brazing stainless steel to steel
High frequency magnetic induction brazing stainless steel to steel process
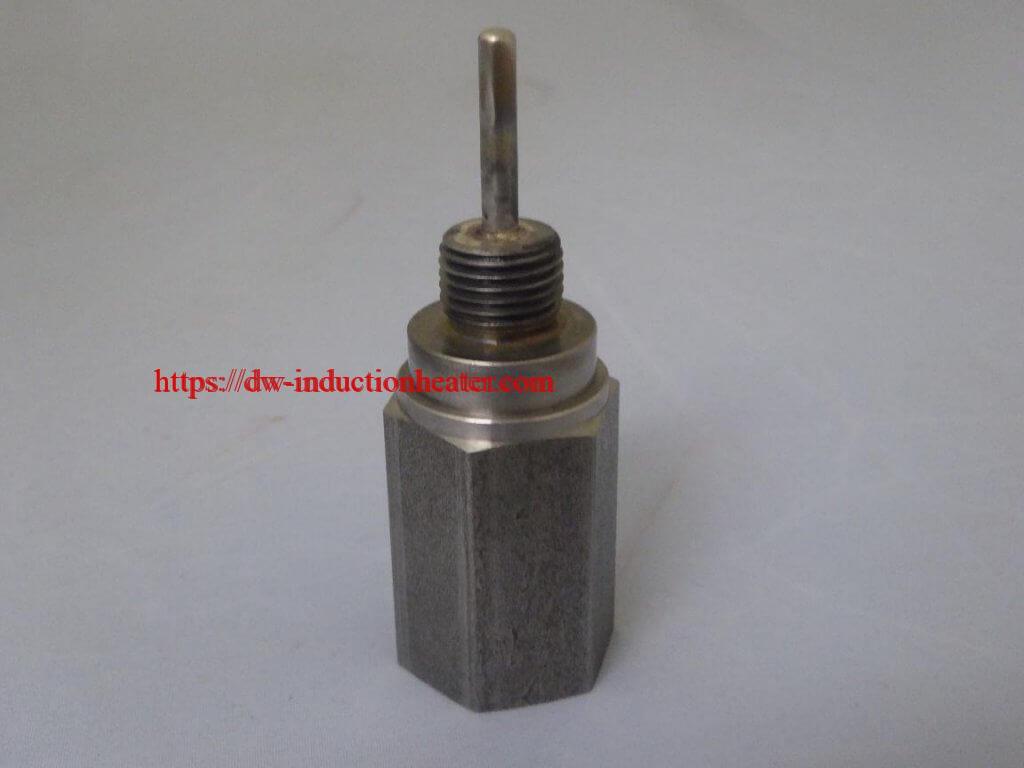


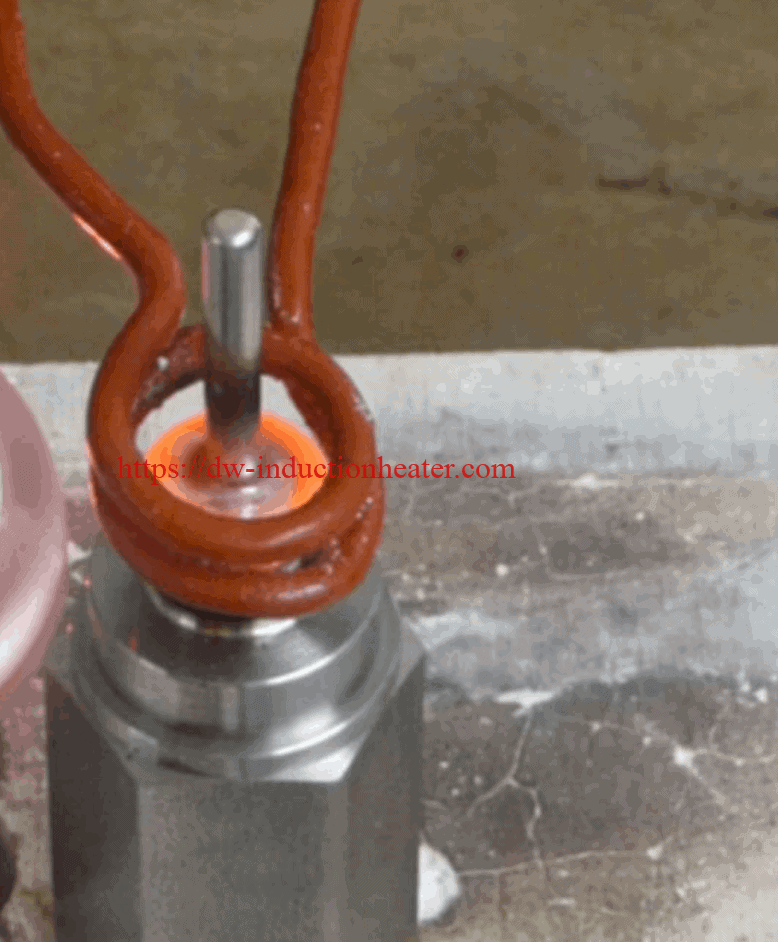
2023年1月30日星期一
Brazing Copper Bars with Induction
Brazing Carbide Tool Tips With Induction
Soldering Steel To Brass With Induction Heater
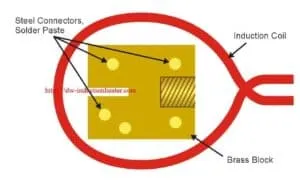
induction Brazing copper rods to brass strips

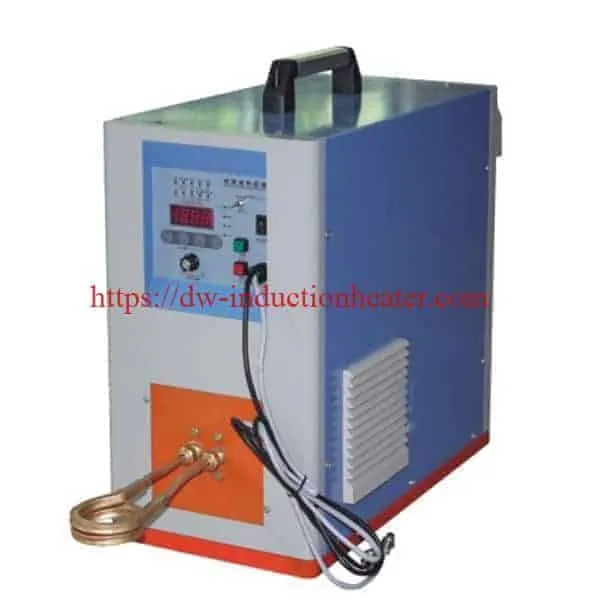
- induction brazing Strong durable joints
- Selective and precise heat zone, resulting in less part distortion and joint stress than welding
- Less oxidation
- Faster heating cycles
- More consistent results and suitability for large volume production, without the need for batch processing
- Safer than flame brazing
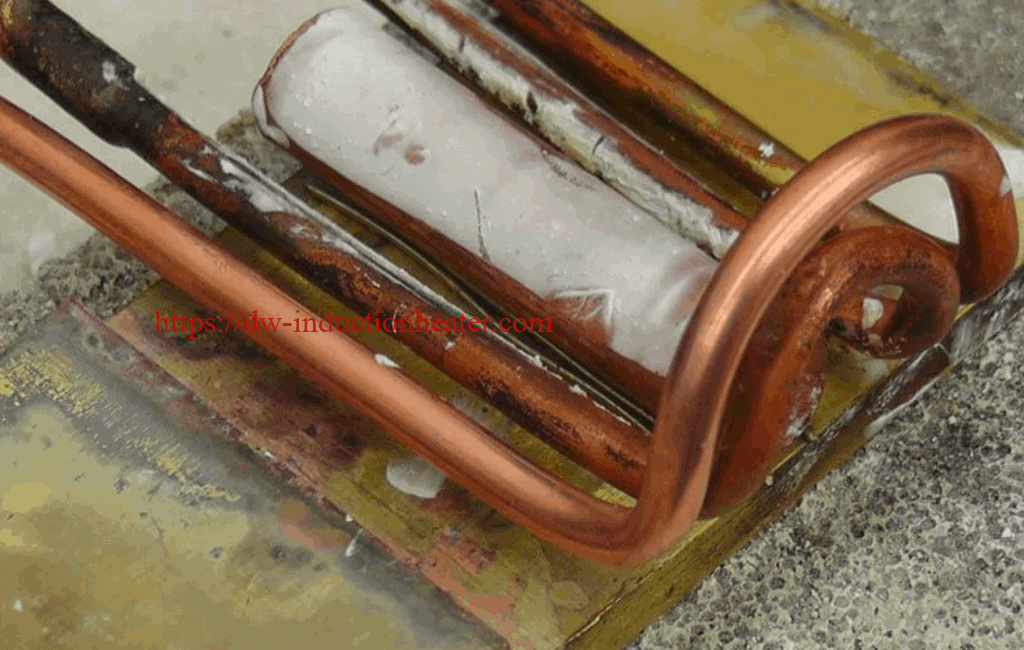
RF Soldering Circuit Board
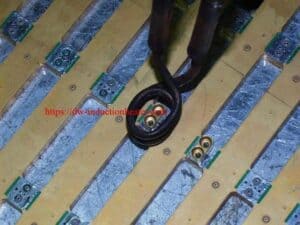
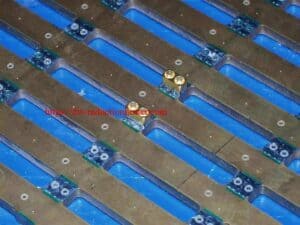
2023年1月29日星期日
Induction Heating Steel Mold
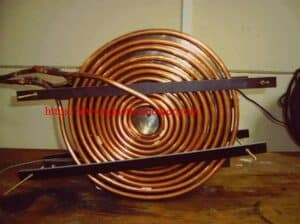
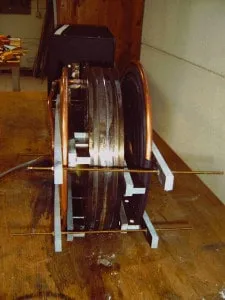
Induction inline wire heating process
Induction inline wire heating process
Objective Induction Heat several different inline wire diameters to 204°C (400°F) in 0.8 seconds with the same induction coil.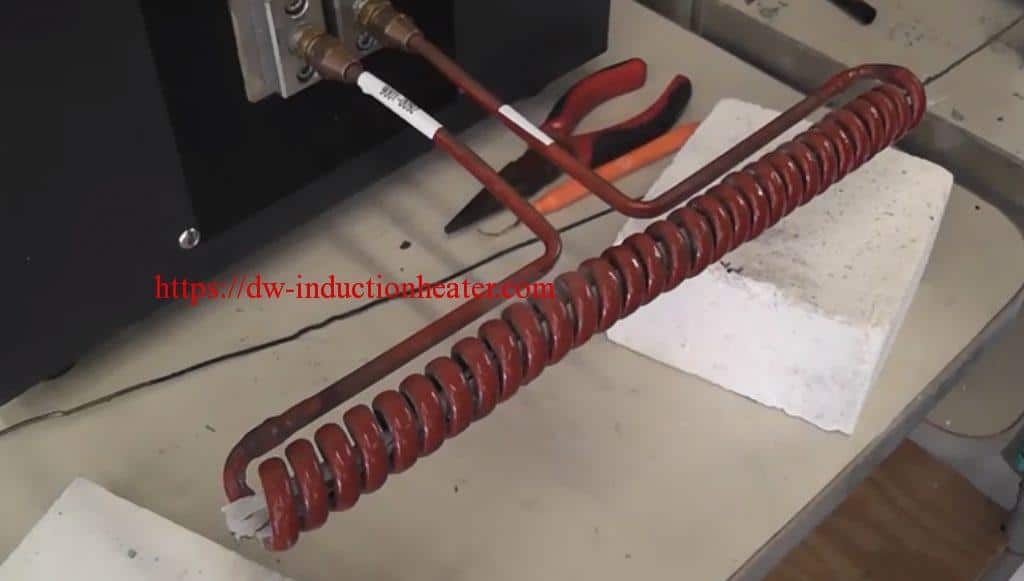
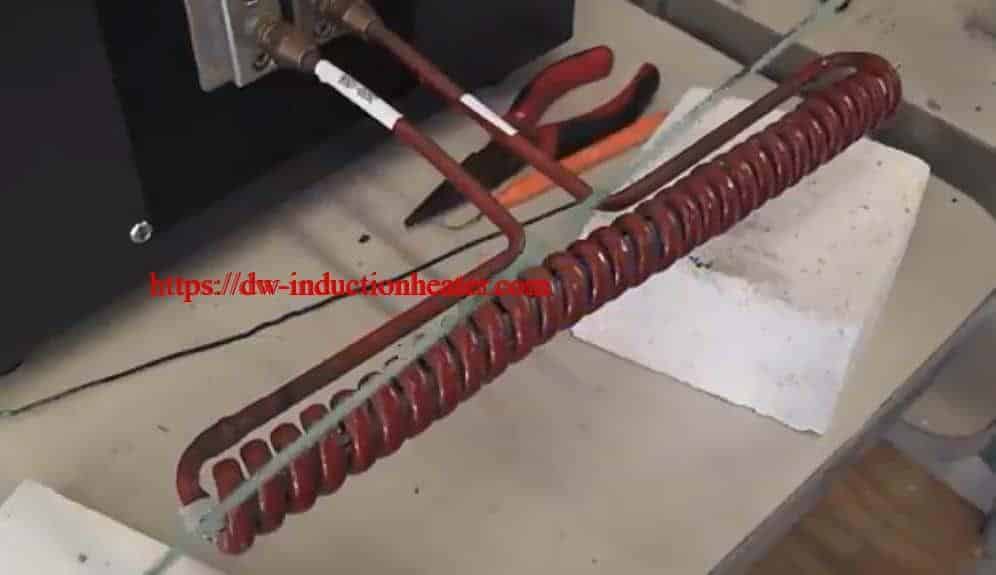
Induction Soldering Circuit Board
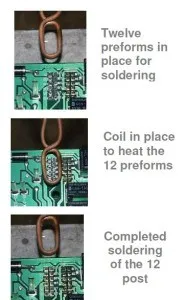
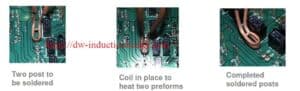
Induction Brazing Heating Exchanger Copper Pipes
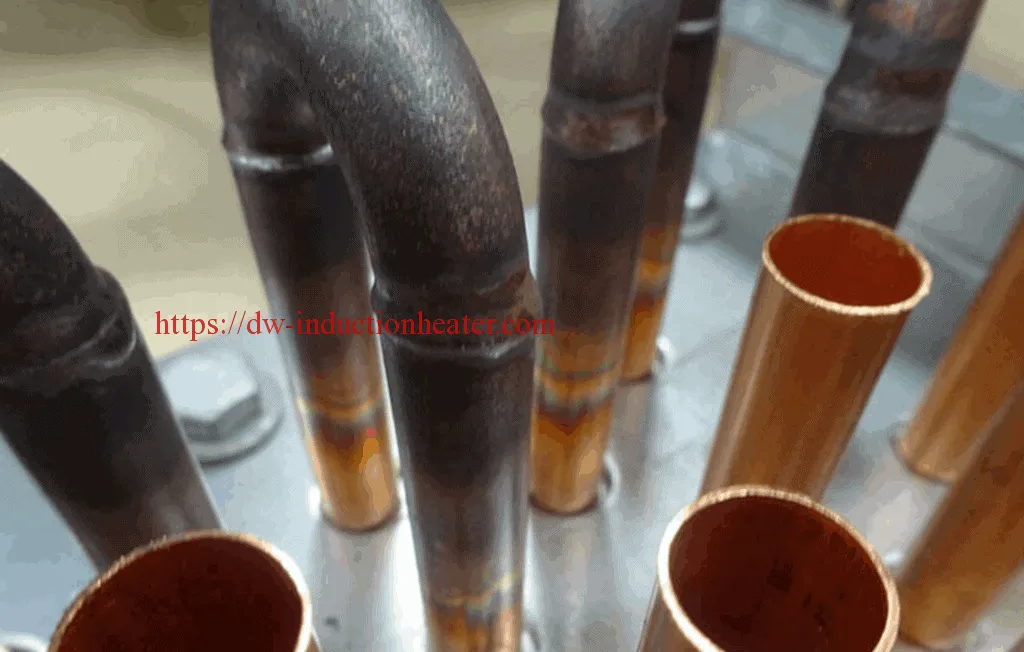
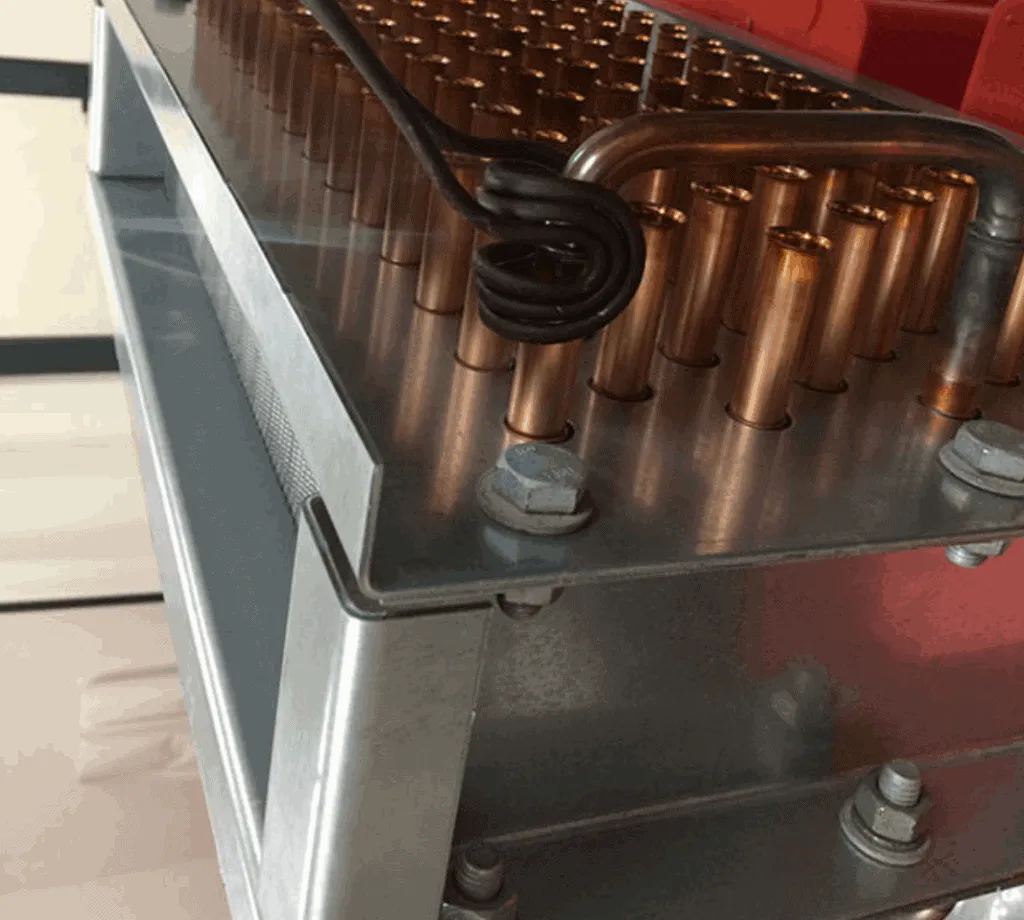
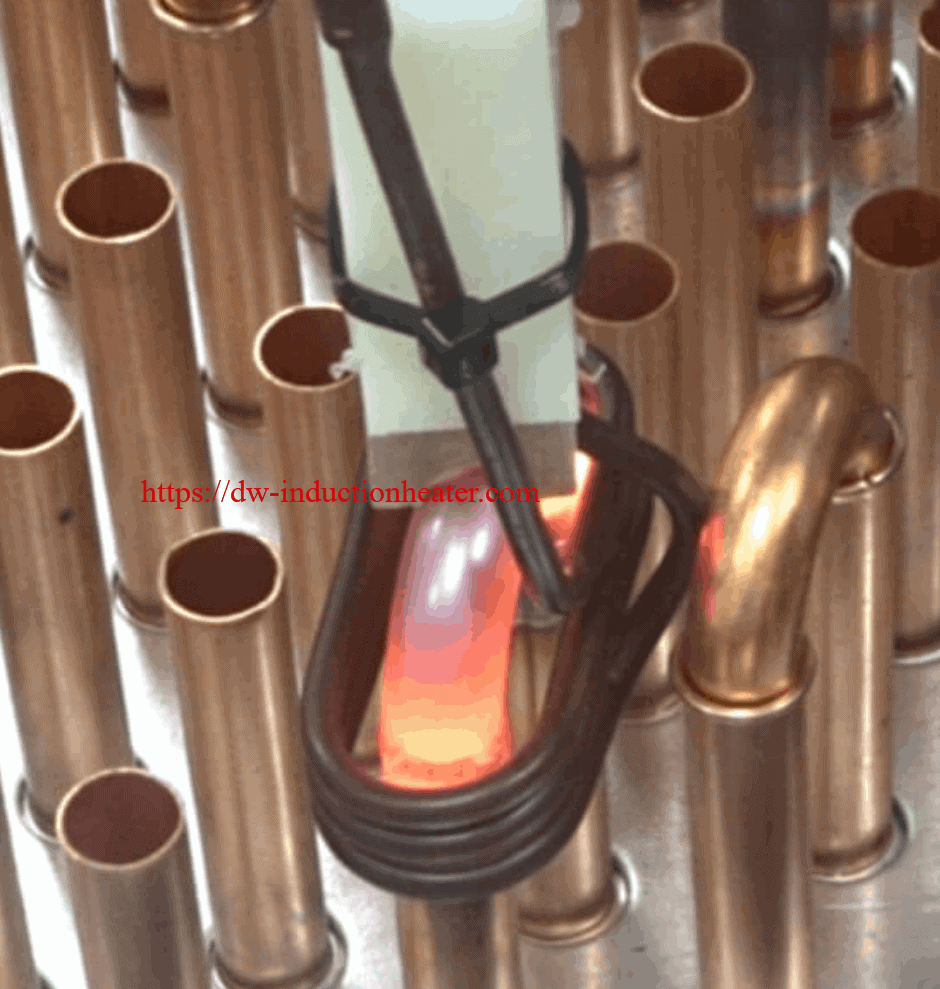
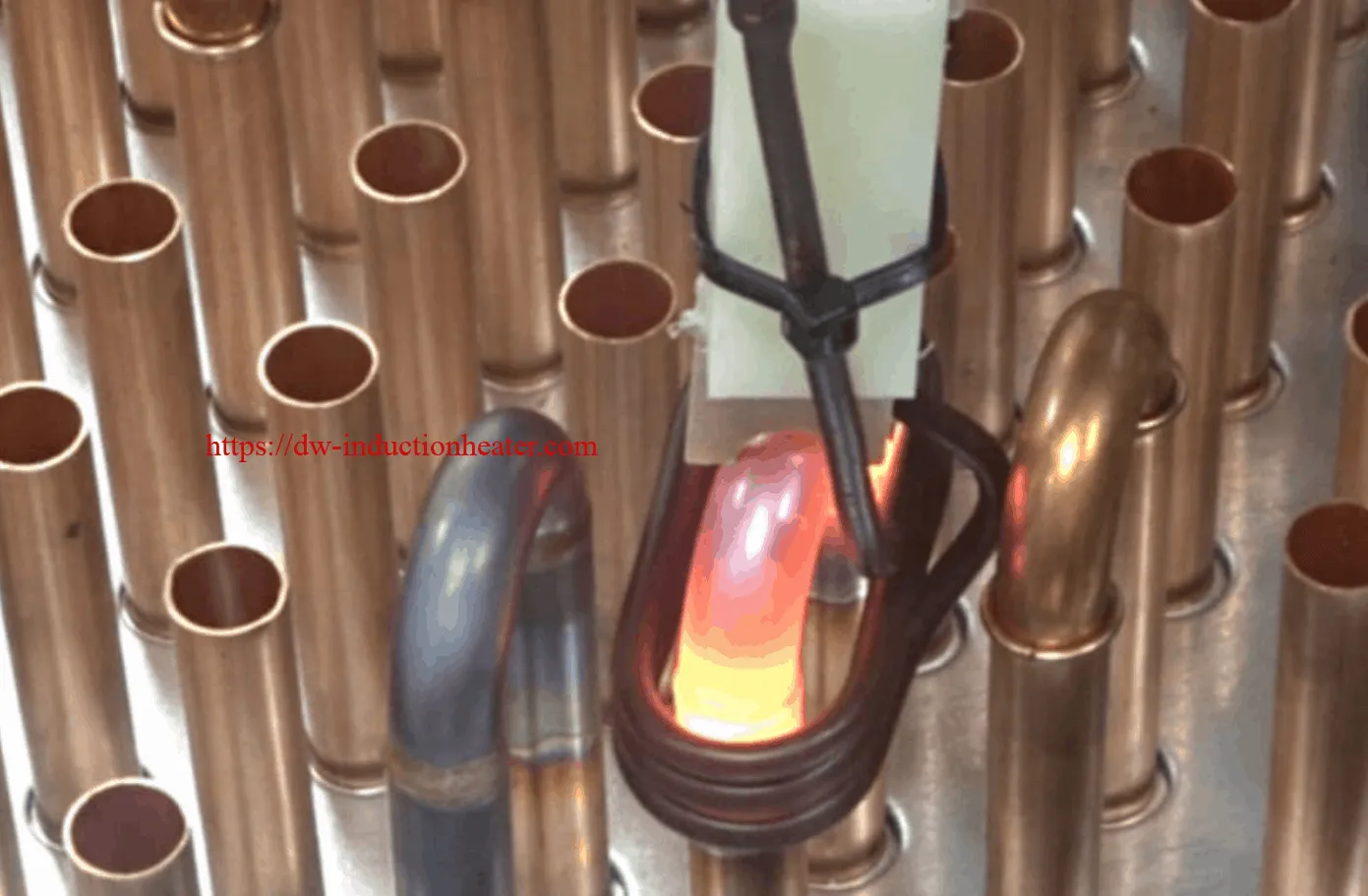
- Safe heating with no open flame
- Precise control over time and temperature resulting in improved quality and consistent result
- A repeatable process, not operator dependent
- Energy efficient induction heating
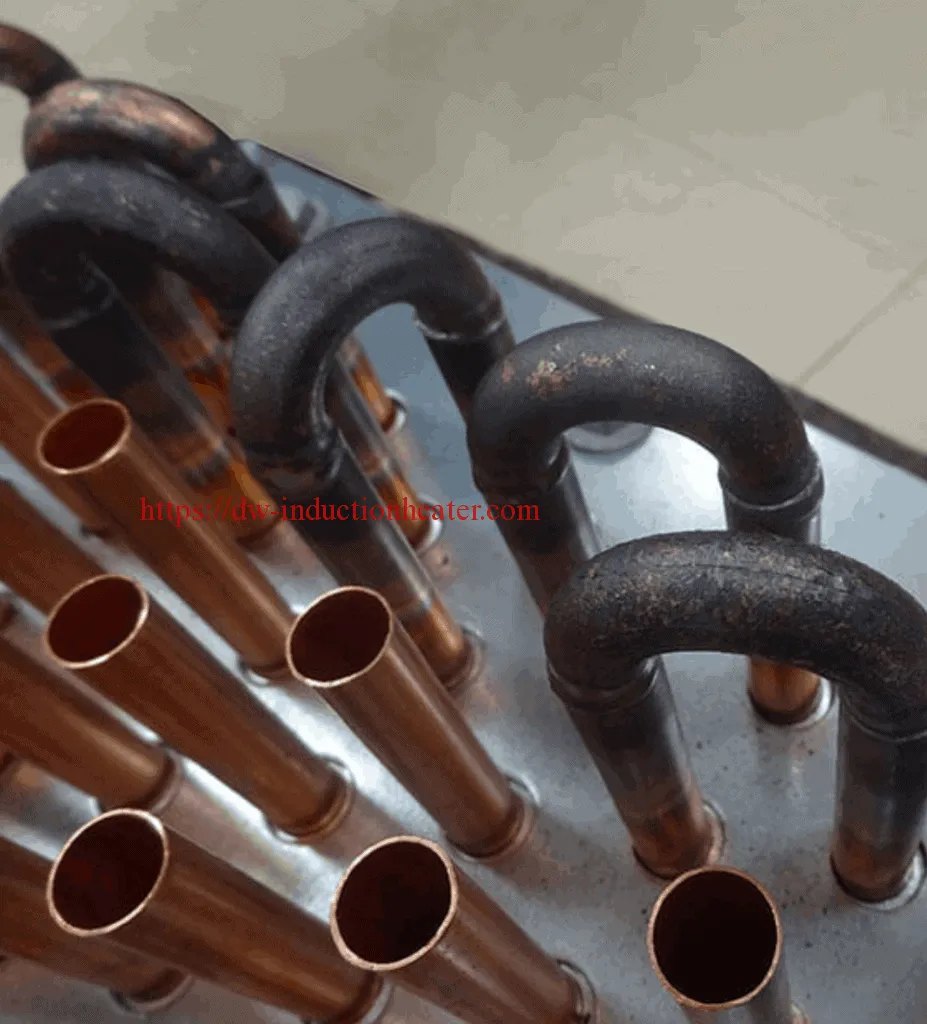
Technology of Induction Forming Steel Plate
induction heating diffusion pump with electromagnetic heater
induction heating diffusion pump with electromagnetic heater
Induction Heating diffusion pump-Vacuum coating diffusion pump electromagnetic induction heater instead of resistance heating plate can save how much electricity?
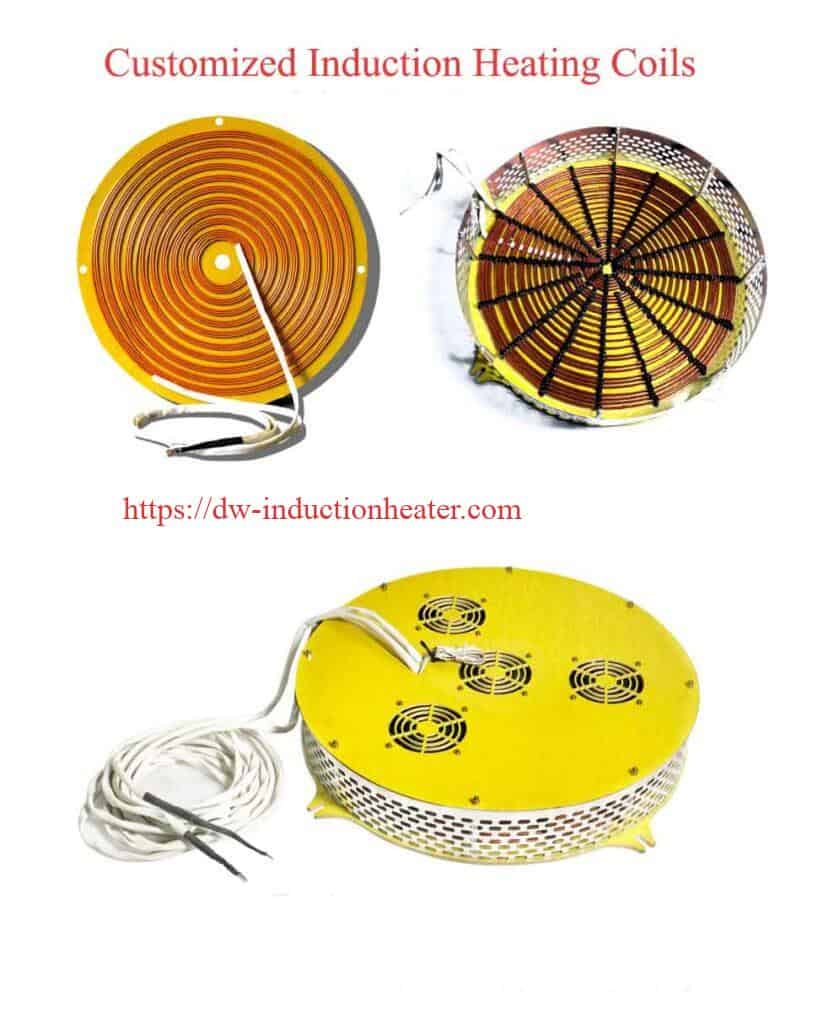

Advantages of diffusion pump electromagnetic induction heating over resistance wire heating:
(1) high efficiency and energy saving, saving more than 30% electricity than resistance wire heating.
(2) fast heating speed and even heating.
(3) stable operation and accurate temperature control
(4) easy operation and long service life
At room temperature, it takes 70-90 minutes for a traditional 15kw resistance wire for a diffusion pump with a diameter of 830mm to rise to 230 degrees and can no longer be heated up, while the 15kw electromagnetic heating coil only takes 35-40 minutes to raise the temperature to 230 degrees , greatly shorten the preheating time, improve the production efficiency, and save a lot of power. When the equipment is shut down, when the resistance wire heating method is used, because the electric furnace has residual heat, the cooling pump will work for a long time before it can stop, and the coil used for electromagnetic heating has no heat. After the equipment is shut down, it can be quickly Stop the cooling pump. This also saves the power consumption of the cooling pump. It can be seen that electromagnetic heating saves at least 30%-60% energy than traditional resistance wire heating. Electromagnetic induction heating evaporation coating can greatly improve the evaporation rate, and the evaporation temperature is stable, which can avoid the splash phenomenon of the coating material, the film will not have the effect of pinholes, greatly improve the qualification rate of the product, and the purity requirements of the coating material are also higher than the resistance. The requirements of the furnace are lower. The high-purity material required by the resistance furnace (electric furnace wire) must reach 99.99% purity, while the electromagnetic heating evaporation only needs to reach 99.9%. From every point, it can be seen that the electromagnetic heating evaporation technology has reduced Coating production cost.
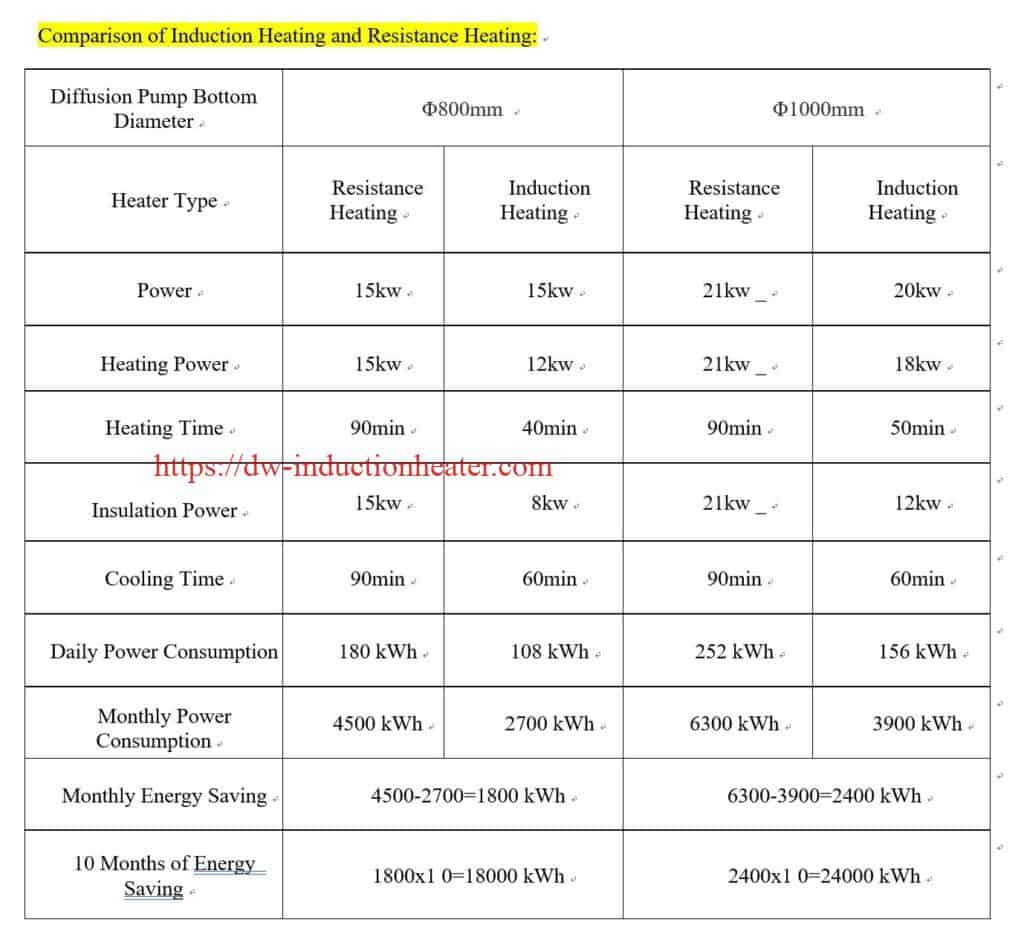
Induction heating machine is widely used in heat transfer forging, quenching, tempering, annealing, quenching and other heat treatment industries, as well as preheating, hot charging and other industries.
So what are the advantages of electromagnetic induction heating system that make it widely used in all walks of life?
Nowadays, many users are using this induction heater. Users use it because it has its own advantages.
Induction heating machine adopts electromagnetic induction heating process to directly heat the workpiece. It has the advantages of fast on-off speed and high working frequency.
- Energy saving and environmental protection. Now the state's control of air pollution is becoming more and more strict. This is the advantage of induction heating machine
- The use of induction heating machine can reduce the production cost.
- Induction heating machine has high technical content, so its energy efficiency is also very good.
- Induction heating machine can be used with very good performance and high efficiency.

2023年1月28日星期六
Induction Shrink Fitting Steel Tube
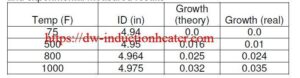

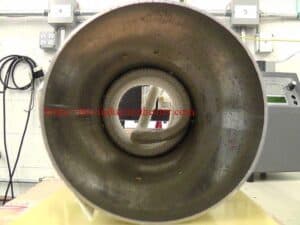
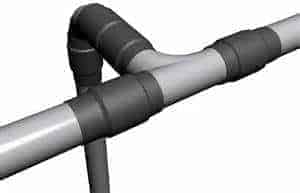
关注者
博客归档
-
▼
2023
(1696)
-
▼
一月
(174)
- Brazing Carbide-Steel Tool with Induction
- Induction Brazing Copper Pipe Fittings
- induction brazing stainless steel to steel
- Induction inline wire heating process
- induction coating removal for removing paint
- induction brazing stainless steel to steel
- Brazing Copper Bars with Induction
- Brazing Carbide Tool Tips With Induction
- Soldering Steel To Brass With Induction Heater
- induction Brazing copper rods to brass strips
- RF Soldering Circuit Board
- Induction Heating Steel Mold
- Induction inline wire heating process
- Induction Soldering Circuit Board
- Induction Brazing Heating Exchanger Copper Pipes
- Technology of Induction Forming Steel Plate
- induction heating diffusion pump with electromagne...
- Induction Shrink Fitting Steel Tube
- Induction Brazing Steel Parts to Tungsten Carbide ...
- Hydrogen Atmosphere Brazing Tube To Copper With In...
- Induction Heating Theory PDF
- Induction Annealing Copper Tubes
- Induction Billets Heater Video
- induction Brazing copper rods to brass strips
- induction sealing glass
- Induction Annealing Copper Tubes
- Induction Shrink Fitting Assemblies
- Brazing Copper Bars with Induction
- Induction Brazing Carbide Tipping of Medical Tools
- High Frequency Induction Cap Sealing
- induction brazing copper and brass rods
- Induction Soldering Stainless Steel Tubes to Brass...
- induction hardening steel handheld stamps
- induction coating removal for removing paint
- induction curing
- Induction Aluminum Brazing with Computer Assisted
- induction brazing automotive copper heating exchan...
- Induction Heating Bolts
- Induction Brazing Steel Pipe
- aluminum scrap melting induction furnace
- Induction Annealing Brass Bullet Shells
- Induction Heating Plastic Catheter Tube
- Induction stress relieving flat blanks
- Plastic Injection Molding with Induction Heating
- What is induction tempering?
- Induction Brazing Carbide Onto Steel Part
- Brazing Carbide To Steel Shank
- Melting Aluminum Tilting Crucible Induction Furnace
- Induction Heating Wires For Hot Heading
- Induction Heating Solutions For Cancer Research
- induction small copper tubing brazing connection j...
- Aluminum Billet Heating Furnace
- induction brazing steel carbide cap to shaft
- Induction Brazing Copper Tube For Refrigeration
- Induction Soldering Brass Tube-Pipe
- induction hardening steel handheld stamps
- Brazing Carbide To Steel With Induction
- Induction Heating Steel Mold
- Annealing Metal Stamp With Induction
- Induction Heating Steel Part For Hot Heading
- Induction brazing aluminum pipes
- steel plate-shovels hot forming with induction pre...
- Aluminum Scrap Melting Recycling Induction Furnace
- Induction Heating Solutions For Cancer Research
- Induction Heating Automotive Motor
- refrigeration induction brazing refrigerator coppe...
- Induction brazing aluminum pipes
- Induction Hardening Inner
- High Frequency Welding
- Brazing Copper Tube with Induction
- Induction Hot Forming Steel Pipe
- Induction Brazing Principle-Theory
- Induction Preheating Steel Tubes
- Brazing Brass To Copper With Induction
- high frequency induction soldering wire to connector
- How Induction Heating works?
- induction heating for surface quenching of steel
- induction brazing stainless steel to steel
- Induction Heating Sintering Copper Powder
- RPR Induction Pipeline Coating Removal
- Brazing Brass To Copper With Induction
- induction heating steel cable for cutting
- Induction Soldering Circuit Board
- induction brazing copper and brass rods
- Brazing Carbide-Steel Tool with Induction
- Induction Heating Coils Design and Basic PDF
- INDUCTION HEATING FOR SURFACE QUENCHING
- Induction Brazing Principle-Theory
- Brazing Eyeglass Frames With Induction
- Induction Soldering Aluminum Housing
- Induction Melting Furnace with Manual Tilting Device
- induction heating system technology PDF
- Induction hardening steel screw threads
- Induction Brazing Carbide to Steel
- induction preheating titanium billet for rolling
- brazing short circuit rings with induction heater
- Induction Soldering Copper Pipes to PCB Board
- Induction Soldering Brass Rings
- Induction Soldering Brass Tube-Pipe
- Induction Heating Stainless Steel
-
▼
一月
(174)
我的简介

- HLQ induction heating machine
- HLQ induction heating machine manufacturer provides the service of induction brazing,melting,hot forming,hardening surface,annealing,shrink fitting,PWHT,etc.