2022年2月28日星期一
Induction Brazing & Soldering Principle
Induction Annealing Copper Tubes
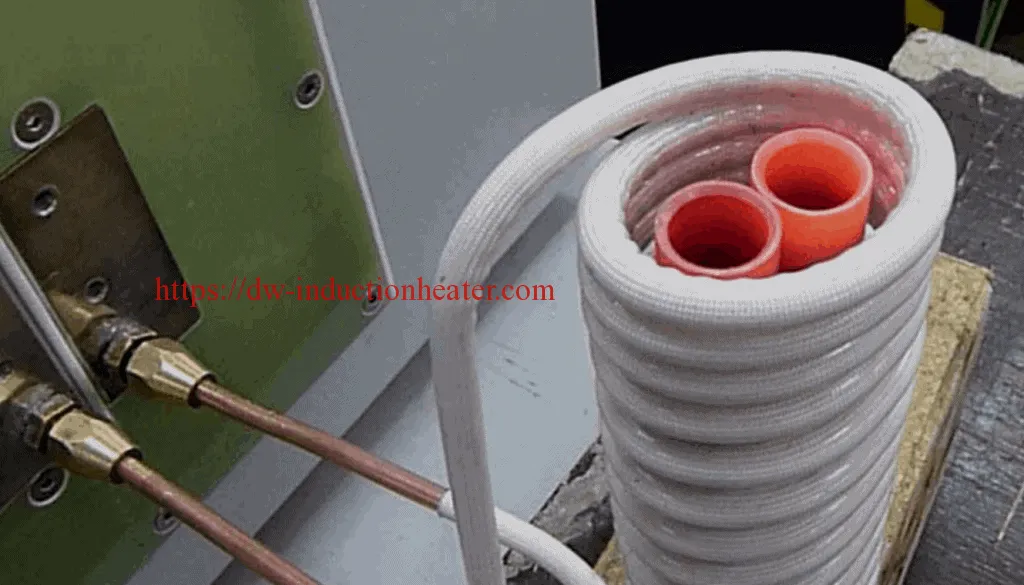
- The two copper tubes were placed together in the coil.
- Induction heating was applied for 5s.
- Improved process control for uniform induction heating to a desired temperature
- Power on demand and rapid, consistent heat cycles
- Technology without pollution, which is both clean and safe


Induction Heating Barrel for Plastic Extruder and Injection Molding Machine
Induction heating barrel offers greater energy savings, reliability, and faster response.
Spectacular energy savings, superior reliability and much faster response than conventional heater bands are some of the advantages offered by a newly developed induction heating system. The heating system uses electromagnetic induction - an old and well-known principle used to heat large industrial furnaces, special machines for injection moulding molten metal, thermoset molds, and some Japanese hot-runner nozzles. However, it is a relatively new concept for heating barrels of plastics extrusion and injection molding machines.
Where can induction heating barrel?
It is mainly applied to injection, extrusion; blow filming, wire drawing, granulating and recycling machines, etc. The product application includes film, sheet, profile, raw material etc. It can be used for heating the barrel, flange, die head, screw and other parts of the machines. It is excellent in energy-saving and cooling down work environment. Induction heating is the process of heating an electrically conducting object (usually a metal) by electromagnetic induction, where eddy currents are generated within the metal and resistance leads to Joule heating of the metal. The induction coil itself does not get heated. The heat generating object is the heated object itself.Why and how induction heating barrel can save energy?
Presently,most of the plastic machines are using the conventional resistance heating method, where the resistance wire is heated up and then transfer the heat to the barrel via heater cover.So only the heat close to the barrel surface can be transferred to the barrel and the heat close to outside heater cover is lost to the air which causes a rise in environment temperature. Induction heater is technology where high frequency magnetic fields which cause he be heated up bu electro-magnetic field(EMF)that are brushing against each other.When the barrel is heated up and heat is minimum,there is very high heat efficiency and minimum heat loss to the environment where energy saving could reach30-80%.Due to the fact that the induction coil is not producing any high heat and also there is no resistance wire that gets oxidized and causes the heater to burn out, the induction heater has a longer service life and also less maintenance.
What are the advantages of induction heating barrel?
- Energy efficiency 30%-85% Currently, plastic processing machinery mainly uses resistance heating elements which can produce a large amount of heat radiated to the surroundings. Induction heating is an ideal alternative to solve this issue. The surface temperature of induction heating coil ranges between 50ºC and 90ºC, the heat losses are significantly minimized, providing energy savings of 30%-85%. The energy saving effect is therefore more obvious when the induction heating system is used in high power heating equipment.
- Safety Using induction heating system enables the surface of the machine to be safe for touching, and that means it can avoid burn injuries which often occur in plastic machines that use resistance heating elements, providing a safe workplace for operators.
- Fast heating, high heating efficiency Compared to resistance heating whose energy conversion efficiency is approximately at 60%, the induction heating is over 98% efficient at converting electricity to heat.
- Lower workplace temperature, higher operation comfort After using induction heating system, the temperature of entire production workshop is lowered by more than 5 degrees.
- Long service life In contrast to resistance heating elements that have to long-lasting work at high temperature, the induction heating works at near ambient temperature, therefore efficiently prolonging the service life.
- Accurate temperature control, high product qualification rate The induction heating provides low or no thermal inertia, so that it will not cause the temperature overshoot. And the temperature can remain at set value of 0.5 degree difference.
What is the superiority of induction heating barrel for plastic extrusion compared with traditional heaters?
Induction heater | Traditional heaters | |
Heating method | Induction heating is the process of heating an electrically conducting object (usually a metal) by electromagnetic induction, where eddy currents are generated within the metal and resistance leads to Joule heating of the metal. The induction coil itself does not get heated. The heat generating object is the heated object itself | Resistance wires get heated directly and heat is transferred by contact. |
heating up time | Quicker heating-up, higher efficiency | slower heating-up, lower efficiency |
Energy saving rate |
Save 30-80% energy rate,reduce working temperature |
Cannot save energy |
Installation | Easy to install | Easy to install |
Operation | Easy to operate | Easy to operate |
Maintenance |
Control box is easy to replace without turning off your machine |
Easy to replace but have to turning off your machine |
Temperature Control | Small thermal inertia and precise temperature control because the heater doesn’t get heated byitself. | Big thermal inertia, low accuracy in temperature control |
Product Quality | Higher product quality because of precise temperature control | Lower product quality |
Safety |
Outer sheath is safe to touch, lower surface temperature, no electric leakage. |
Temperature on outer sheath is much higher, easy to get burned. Electric leakage under wrong operation. |
Service life of heater | 2-4years | 1-2 years |
Service life of Barrel and Screw |
Longer usage life for barrel, screw etc. due to lower frequency of changing heaters. |
Shorter usage life for barrel, screw etc. |
Environment | Lower environment temperature; No noise | Much higher environment temperature and much noise |
Induction Heating Power Calculation
In the case of knowing the heating power of existing heating system, selecting an appropriate power according to load rate
- Load rate ≤ 60%, applicable power is 80% of the original power;
- Load rate between 60%-80%, select the original power;
- Load rate > 80%, applicable power is 120% of the original power;
When the heating power of existing heating system is unknown
- For injection molding machine, blown film machine and extrusion machine, the power should be calculated as 3W per cm2 according to the actual surface area of the cylinder (barrel);
- For dry cut pelletizing machine, the power should be calculated as 4W per cm2 according to the actual surface area of the cylinder (barrel);
- For wet cut pelletizing machine, the power should be calculated as 8W per cm2 according to the actual surface area of the cylinder (barrel);
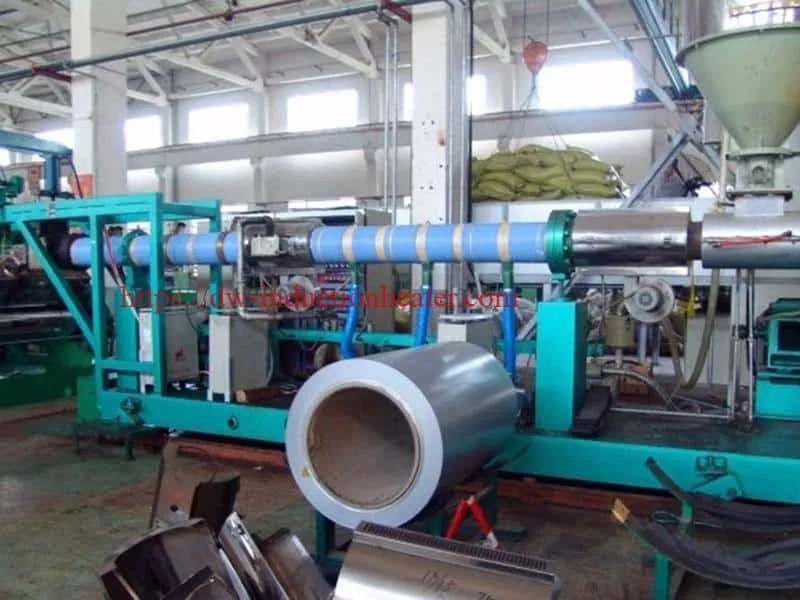
Induction Heating Barrel for Plastic Extruder and Injection Molding Machine
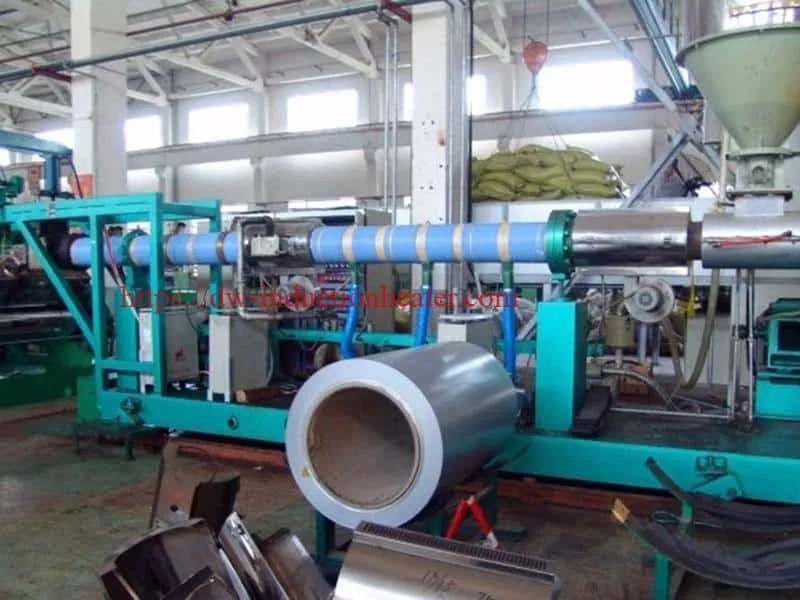
Induction heating barrel offers greater energy savings, reliability, and faster response.
Spectacular energy savings, superior reliability and much faster response than conventional heater bands are some of the advantages offered by a newly developed induction heating system. The heating system uses electromagnetic induction - an old and well-known principle used to heat large industrial furnaces, special machines for injection moulding molten metal, thermoset molds, and some Japanese hot-runner nozzles. However, it is a relatively new concept for heating barrels of plastics extrusion and injection molding machines.
Where can induction heating barrel?
It is mainly applied to injection, extrusion; blow filming, wire drawing, granulating and recycling machines, etc. The product application includes film, sheet, profile, raw material etc. It can be used for heating the barrel, flange, die head, screw and other parts of the machines. It is excellent in energy-saving and cooling down work environment. Induction heating is the process of heating an electrically conducting object (usually a metal) by electromagnetic induction, where eddy currents are generated within the metal and resistance leads to Joule heating of the metal. The induction coil itself does not get heated. The heat generating object is the heated object itself.Why and how induction heating barrel can save energy?
Presently,most of the plastic machines are using the conventional resistance heating method, where the resistance wire is heated up and then transfer the heat to the barrel via heater cover.So only the heat close to the barrel surface can be transferred to the barrel and the heat close to outside heater cover is lost to the air which causes a rise in environment temperature. Induction heater is technology where high frequency magnetic fields which cause he be heated up bu electro-magnetic field(EMF)that are brushing against each other.When the barrel is heated up and heat is minimum,there is very high heat efficiency and minimum heat loss to the environment where energy saving could reach30-80%.Due to the fact that the induction coil is not producing any high heat and also there is no resistance wire that gets oxidized and causes the heater to burn out, the induction heater has a longer service life and also less maintenance.
What are the advantages of induction heating barrel?
- Energy efficiency 30%-85% Currently, plastic processing machinery mainly uses resistance heating elements which can produce a large amount of heat radiated to the surroundings. Induction heating is an ideal alternative to solve this issue. The surface temperature of induction heating coil ranges between 50ºC and 90ºC, the heat losses are significantly minimized, providing energy savings of 30%-85%. The energy saving effect is therefore more obvious when the induction heating system is used in high power heating equipment.
- Safety Using induction heating system enables the surface of the machine to be safe for touching, and that means it can avoid burn injuries which often occur in plastic machines that use resistance heating elements, providing a safe workplace for operators.
- Fast heating, high heating efficiency Compared to resistance heating whose energy conversion efficiency is approximately at 60%, the induction heating is over 98% efficient at converting electricity to heat.
- Lower workplace temperature, higher operation comfort After using induction heating system, the temperature of entire production workshop is lowered by more than 5 degrees.
- Long service life In contrast to resistance heating elements that have to long-lasting work at high temperature, the induction heating works at near ambient temperature, therefore efficiently prolonging the service life.
- Accurate temperature control, high product qualification rate The induction heating provides low or no thermal inertia, so that it will not cause the temperature overshoot. And the temperature can remain at set value of 0.5 degree difference.
What is the superiority of induction heating barrel for plastic extrusion compared with traditional heaters?
Induction heater | Traditional heaters | |
Heating method | Induction heating is the process of heating an electrically conducting object (usually a metal) by electromagnetic induction, where eddy currents are generated within the metal and resistance leads to Joule heating of the metal. The induction coil itself does not get heated. The heat generating object is the heated object itself | Resistance wires get heated directly and heat is transferred by contact. |
heating up time | Quicker heating-up, higher efficiency | slower heating-up, lower efficiency |
Energy saving rate |
Save 30-80% energy rate,reduce working temperature |
Cannot save energy |
Installation | Easy to install | Easy to install |
Operation | Easy to operate | Easy to operate |
Maintenance |
Control box is easy to replace without turning off your machine |
Easy to replace but have to turning off your machine |
Temperature Control | Small thermal inertia and precise temperature control because the heater doesn’t get heated byitself. | Big thermal inertia, low accuracy in temperature control |
Product Quality | Higher product quality because of precise temperature control | Lower product quality |
Safety |
Outer sheath is safe to touch, lower surface temperature, no electric leakage. |
Temperature on outer sheath is much higher, easy to get burned. Electric leakage under wrong operation. |
Service life of heater | 2-4years | 1-2 years |
Service life of Barrel and Screw |
Longer usage life for barrel, screw etc. due to lower frequency of changing heaters. |
Shorter usage life for barrel, screw etc. |
Environment | Lower environment temperature; No noise | Much higher environment temperature and much noise |
Induction Heating Power Calculation
In the case of knowing the heating power of existing heating system, selecting an appropriate power according to load rate
- Load rate ≤ 60%, applicable power is 80% of the original power;
- Load rate between 60%-80%, select the original power;
- Load rate > 80%, applicable power is 120% of the original power;
When the heating power of existing heating system is unknown
- For injection molding machine, blown film machine and extrusion machine, the power should be calculated as 3W per cm2 according to the actual surface area of the cylinder (barrel);
- For dry cut pelletizing machine, the power should be calculated as 4W per cm2 according to the actual surface area of the cylinder (barrel);
- For wet cut pelletizing machine, the power should be calculated as 8W per cm2 according to the actual surface area of the cylinder (barrel);
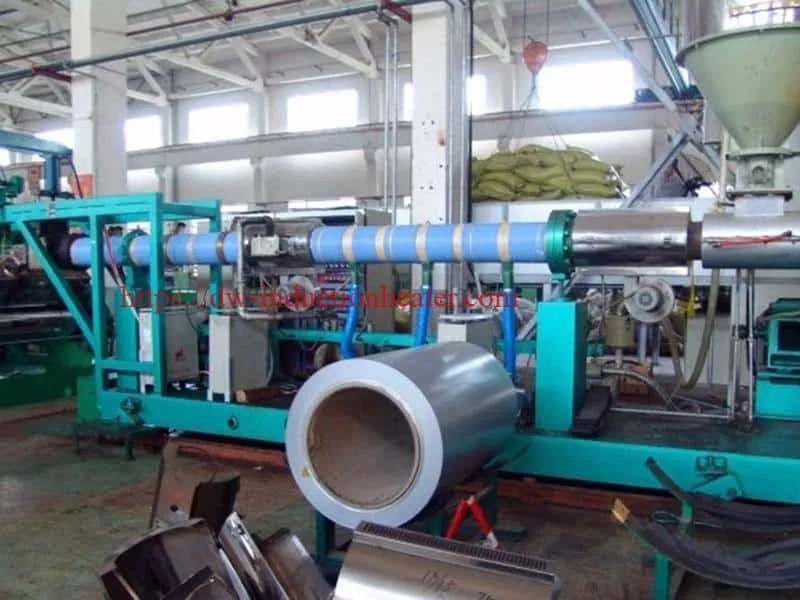
2022年2月27日星期日
Induction Brazing Aluminum Pipes
How to design induction heating coil
How to design induction heating coil
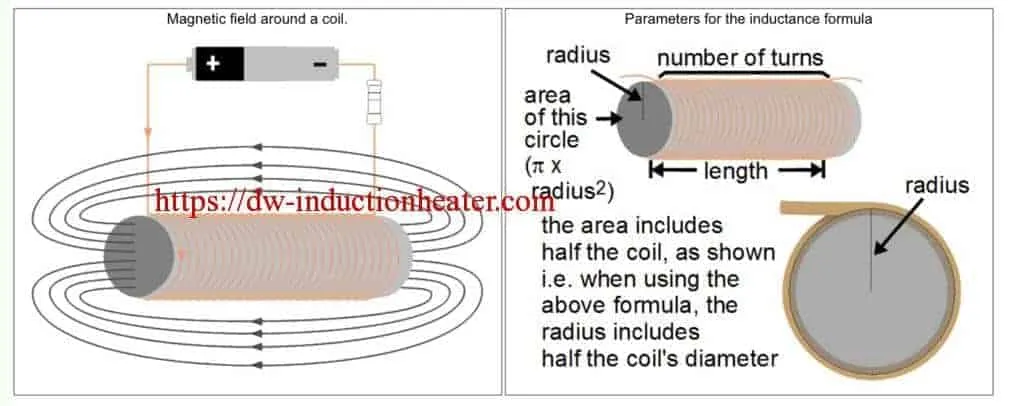
Coupling Efficiency
There is a proportional relationship between the amount of current flow and distance between the inductor and part. Placing the part close to the inductor increases the flow of current and the amount of heat induced in the part. This relationship is referred to as the coupling efficiency of the inductor.Basic Construction
Induction heating coil/Inductors are often made of copper tubing - a very good conductor of heat and electricity - with a diameter of 1/8" to 3/16"; larger copper coil assemblies are made for applications such as strip metal heating and pipe heating. Inductors are usually cooled by circulating water, and are most often custom-made to fit the shape and size of the part to be heated. So inductors can have single or multiple turns; have a helical, round or square shape; or be designed as internal (part inside inductor) or external (part adjacent to inductor).How Induction Heating Coils Work
How efficiently and effectively a workpiece is heated is determined by the induction coil. Induction coils are water-cooled copper conductors created from copper tubing which is readily formed into the shape of the coil for the induction heating process. As water flows through them, induction heating coils themselves do not get hot. Work coils range in complexity from a coil that is precision machined from solid copper and brazed, to a simple solenoid- or helical-wound coil (made up of a number of turns of copper tube wound around a mandrel). By producing an alternating electromagnetic field due to the alternating current flowing in them, coils transfer energy from the power supply to the workpiece. The coil’s alternating electromagnetic field (EMF) creates an induced current (eddy current) in the workpiece, which generates heats due to I Squared R losses (core losses). The coil’s EMF strength correlates with the current in the workpiece. This transfer of energy is known as the eddy current effect or transformer effect.induction heating plastic granulator
Brief Introduction of induction heating plastic granulator/plastic extrusion:
Induction heating plastic granulator/plastic extrusion is a one type of energy-saving heater. It has many advantages including significant energy-saving, fast heating up, high energy efficiency, low or zero maintenance etc. It can also lower environment temperature by generating much less heat. While installing the induction heater system, there will not involve any major changes to the electrical control system.
Where can induction heating plastic granulator/plastic extrusion?
It is mainly applied to injection, extrusion; blow filming, wire drawing, granulating and recycling machines, etc. The product application includes film, sheet, profile, raw material etc. It can be used for heating the barrel, flange, die head, screw and other parts of the machines. It is excellent in energy-saving and cooling down work environment.
Induction heating is the process of heating an electrically conducting object (usually a metal) by electromagnetic induction, where eddy currents are generated within the metal and resistance leads to Joule heating of the metal. The induction coil itself does not get heated. The heat generating object is the heated object itself.
Why and how induction heating plastic granulator/plastic extrusion can save energy?
Presently,most of the plastic machines are using the conventional resistance heating method, where the resistance wire is heated up and then transfer the heat to the barrel via heater cover.So only the heat close to the barrel surface can be transferred to the barrel and the heat close to outside heater cover is lost to the air which causes a rise in environment temperature. Induction heater is technology where high frequency magnetic fields which cause he be heated up bu electro-magnetic field(EMF)that are brushing against each other.When the barrel is heated up and heat is minimum,there is very high heat efficiency and minimum heat loss to the environment where energy saving could reach30-80%.Due to the fact that the induction coil is not producing any high heat and also there is no resistance wire that gets oxidized and causes the heater to burn out, the induction heater has a longer service life and also less maintenance.
What are the advantages of induction heating plastic granulator/plastic extrusion?
- Energy efficiency 30%-85% Currently, plastic processing machinery mainly uses resistance heating elements which can produce a large amount of heat radiated to the surroundings. Induction heating is an ideal alternative to solve this issue. The surface temperature of induction heating coil ranges between 50ºC and 90ºC, the heat losses are significantly minimized, providing energy savings of 30%-85%. The energy saving effect is therefore more obvious when the induction heating system is used in high power heating equipment.
Safety Using induction heating system enables the surface of the machine to be safe for touching, and that means it can avoid burn injuries which often occur in plastic machines that use resistance heating elements, providing a safe workplace for operators.
- Fast heating, high heating efficiency Compared to resistance heating whose energy conversion efficiency is approximately at 60%, the induction heating is over 98% efficient at converting electricity to heat.
- Lower workplace temperature, higher operation comfort After using induction heating system, the temperature of entire production workshop is lowered by more than 5 degrees.
- Long service life In contrast to resistance heating elements that have to long-lasting work at high temperature, the induction heating works at near ambient temperature, therefore efficiently prolonging the service life.
- Accurate temperature control, high product qualification rate The induction heating provides low or no thermal inertia, so that it will not cause the temperature overshoot. And the temperature can remain at set value of 0.5 degree difference.
What is the superiority of induction heating plastic granulator/plastic extrusion compared with traditional heaters?
Induction heater | Traditional heaters | |
Heating method | Induction heating is the process of heating an electrically conducting object (usually a metal) by electromagnetic induction, where eddy currents are generated within the metal and resistance leads to Joule heating of the metal. The induction coil itself does not get heated. The heat generating object is the heated object itself | Resistance wires get heated directly and heat is transferred by contact. |
heating up time | Quicker heating-up, higher efficiency | slower heating-up, lower efficiency |
Energy saving rate |
Save 30-80% energy rate,reduce working temperature |
Cannot save energy |
Installation | Easy to install | Easy to install |
Operation | Easy to operate | Easy to operate |
Maintenance |
Control box is easy to replace without turning off your machine |
Easy to replace but have to turning off your machine |
Temperature Control | Small thermal inertia and precise temperature control because the heater doesn’t get heated byitself. | Big thermal inertia, low accuracy in temperature control |
Product Quality | Higher product quality because of precise temperature control | Lower product quality |
Safety |
Outer sheath is safe to touch, lower surface temperature, no electric leakage. |
Temperature on outer sheath is much higher, easy to get burned. Electric leakage under wrong operation. |
Service life of heater | 2-4years | 1-2 years |
Service life of Barrel and Screw |
Longer usage life for barrel, screw etc. due to lower frequency of changing heaters. |
Shorter usage life for barrel, screw etc. |
Environment | Lower environment temperature; No noise | Much higher environment temperature and much noise |
Induction Heating Power Calculation
In the case of knowing the heating power of existing heating system, selecting an appropriate power according to load rate
- Load rate ≤ 60%, applicable power is 80% of the original power;
- Load rate between 60%-80%, select the original power;
- Load rate > 80%, applicable power is 120% of the original power;
When the heating power of existing heating system is unknown
- For injection molding machine, blown film machine and extrusion machine, the power should be calculated as 3W per cm2 according to the actual surface area of the cylinder (barrel);
- For dry cut pelletizing machine, the power should be calculated as 4W per cm2 according to the actual surface area of the cylinder (barrel);
- For wet cut pelletizing machine, the power should be calculated as 8W per cm2 according to the actual surface area of the cylinder (barrel);
Induction heating bearings machine PDF

induction heating plastic granulator
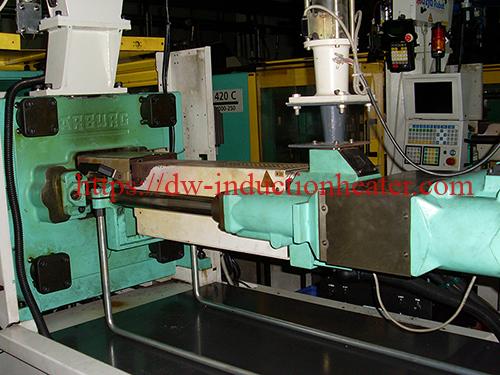
Brief Introduction of induction heating plastic granulator/plastic extrusion:
Induction heating plastic granulator/plastic extrusion is a one type of energy-saving heater. It has many advantages including significant energy-saving, fast heating up, high energy efficiency, low or zero maintenance etc. It can also lower environment temperature by generating much less heat. While installing the induction heater system, there will not involve any major changes to the electrical control system.
Where can induction heating plastic granulator/plastic extrusion?
It is mainly applied to injection, extrusion; blow filming, wire drawing, granulating and recycling machines, etc. The product application includes film, sheet, profile, raw material etc. It can be used for heating the barrel, flange, die head, screw and other parts of the machines. It is excellent in energy-saving and cooling down work environment.
Induction heating is the process of heating an electrically conducting object (usually a metal) by electromagnetic induction, where eddy currents are generated within the metal and resistance leads to Joule heating of the metal. The induction coil itself does not get heated. The heat generating object is the heated object itself.
Why and how induction heating plastic granulator/plastic extrusion can save energy?
Presently,most of the plastic machines are using the conventional resistance heating method, where the resistance wire is heated up and then transfer the heat to the barrel via heater cover.So only the heat close to the barrel surface can be transferred to the barrel and the heat close to outside heater cover is lost to the air which causes a rise in environment temperature. Induction heater is technology where high frequency magnetic fields which cause he be heated up bu electro-magnetic field(EMF)that are brushing against each other.When the barrel is heated up and heat is minimum,there is very high heat efficiency and minimum heat loss to the environment where energy saving could reach30-80%.Due to the fact that the induction coil is not producing any high heat and also there is no resistance wire that gets oxidized and causes the heater to burn out, the induction heater has a longer service life and also less maintenance.
What are the advantages of induction heating plastic granulator/plastic extrusion?
- Energy efficiency 30%-85% Currently, plastic processing machinery mainly uses resistance heating elements which can produce a large amount of heat radiated to the surroundings. Induction heating is an ideal alternative to solve this issue. The surface temperature of induction heating coil ranges between 50ºC and 90ºC, the heat losses are significantly minimized, providing energy savings of 30%-85%. The energy saving effect is therefore more obvious when the induction heating system is used in high power heating equipment.
Safety Using induction heating system enables the surface of the machine to be safe for touching, and that means it can avoid burn injuries which often occur in plastic machines that use resistance heating elements, providing a safe workplace for operators.
- Fast heating, high heating efficiency Compared to resistance heating whose energy conversion efficiency is approximately at 60%, the induction heating is over 98% efficient at converting electricity to heat.
- Lower workplace temperature, higher operation comfort After using induction heating system, the temperature of entire production workshop is lowered by more than 5 degrees.
- Long service life In contrast to resistance heating elements that have to long-lasting work at high temperature, the induction heating works at near ambient temperature, therefore efficiently prolonging the service life.
- Accurate temperature control, high product qualification rate The induction heating provides low or no thermal inertia, so that it will not cause the temperature overshoot. And the temperature can remain at set value of 0.5 degree difference.
What is the superiority of induction heating plastic granulator/plastic extrusion compared with traditional heaters?
Induction heater | Traditional heaters | |
Heating method | Induction heating is the process of heating an electrically conducting object (usually a metal) by electromagnetic induction, where eddy currents are generated within the metal and resistance leads to Joule heating of the metal. The induction coil itself does not get heated. The heat generating object is the heated object itself | Resistance wires get heated directly and heat is transferred by contact. |
heating up time | Quicker heating-up, higher efficiency | slower heating-up, lower efficiency |
Energy saving rate |
Save 30-80% energy rate,reduce working temperature |
Cannot save energy |
Installation | Easy to install | Easy to install |
Operation | Easy to operate | Easy to operate |
Maintenance |
Control box is easy to replace without turning off your machine |
Easy to replace but have to turning off your machine |
Temperature Control | Small thermal inertia and precise temperature control because the heater doesn’t get heated byitself. | Big thermal inertia, low accuracy in temperature control |
Product Quality | Higher product quality because of precise temperature control | Lower product quality |
Safety |
Outer sheath is safe to touch, lower surface temperature, no electric leakage. |
Temperature on outer sheath is much higher, easy to get burned. Electric leakage under wrong operation. |
Service life of heater | 2-4years | 1-2 years |
Service life of Barrel and Screw |
Longer usage life for barrel, screw etc. due to lower frequency of changing heaters. |
Shorter usage life for barrel, screw etc. |
Environment | Lower environment temperature; No noise | Much higher environment temperature and much noise |
Induction Heating Power Calculation
In the case of knowing the heating power of existing heating system, selecting an appropriate power according to load rate
- Load rate ≤ 60%, applicable power is 80% of the original power;
- Load rate between 60%-80%, select the original power;
- Load rate > 80%, applicable power is 120% of the original power;
When the heating power of existing heating system is unknown
- For injection molding machine, blown film machine and extrusion machine, the power should be calculated as 3W per cm2 according to the actual surface area of the cylinder (barrel);
- For dry cut pelletizing machine, the power should be calculated as 4W per cm2 according to the actual surface area of the cylinder (barrel);
- For wet cut pelletizing machine, the power should be calculated as 8W per cm2 according to the actual surface area of the cylinder (barrel);
induction heating plastic granulator
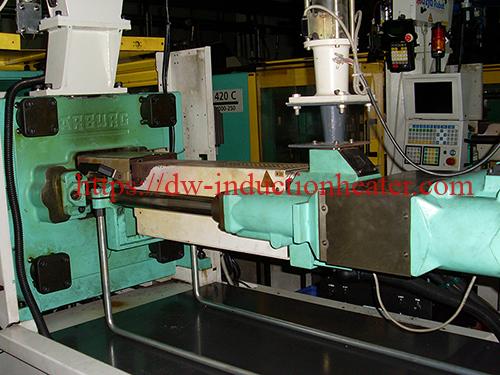
Brief Introduction of induction heating plastic granulator/plastic extrusion:
Induction heating plastic granulator/plastic extrusion is a one type of energy-saving heater. It has many advantages including significant energy-saving, fast heating up, high energy efficiency, low or zero maintenance etc. It can also lower environment temperature by generating much less heat. While installing the induction heater system, there will not involve any major changes to the electrical control system.
Where can induction heating plastic granulator/plastic extrusion?
It is mainly applied to injection, extrusion; blow filming, wire drawing, granulating and recycling machines, etc. The product application includes film, sheet, profile, raw material etc. It can be used for heating the barrel, flange, die head, screw and other parts of the machines. It is excellent in energy-saving and cooling down work environment.
Induction heating is the process of heating an electrically conducting object (usually a metal) by electromagnetic induction, where eddy currents are generated within the metal and resistance leads to Joule heating of the metal. The induction coil itself does not get heated. The heat generating object is the heated object itself.
Why and how induction heating plastic granulator/plastic extrusion can save energy?
Presently,most of the plastic machines are using the conventional resistance heating method, where the resistance wire is heated up and then transfer the heat to the barrel via heater cover.So only the heat close to the barrel surface can be transferred to the barrel and the heat close to outside heater cover is lost to the air which causes a rise in environment temperature. Induction heater is technology where high frequency magnetic fields which cause he be heated up bu electro-magnetic field(EMF)that are brushing against each other.When the barrel is heated up and heat is minimum,there is very high heat efficiency and minimum heat loss to the environment where energy saving could reach30-80%.Due to the fact that the induction coil is not producing any high heat and also there is no resistance wire that gets oxidized and causes the heater to burn out, the induction heater has a longer service life and also less maintenance.
What are the advantages of induction heating plastic granulator/plastic extrusion?
- Energy efficiency 30%-85% Currently, plastic processing machinery mainly uses resistance heating elements which can produce a large amount of heat radiated to the surroundings. Induction heating is an ideal alternative to solve this issue. The surface temperature of induction heating coil ranges between 50ºC and 90ºC, the heat losses are significantly minimized, providing energy savings of 30%-85%. The energy saving effect is therefore more obvious when the induction heating system is used in high power heating equipment.
Safety Using induction heating system enables the surface of the machine to be safe for touching, and that means it can avoid burn injuries which often occur in plastic machines that use resistance heating elements, providing a safe workplace for operators.
- Fast heating, high heating efficiency Compared to resistance heating whose energy conversion efficiency is approximately at 60%, the induction heating is over 98% efficient at converting electricity to heat.
- Lower workplace temperature, higher operation comfort After using induction heating system, the temperature of entire production workshop is lowered by more than 5 degrees.
- Long service life In contrast to resistance heating elements that have to long-lasting work at high temperature, the induction heating works at near ambient temperature, therefore efficiently prolonging the service life.
- Accurate temperature control, high product qualification rate The induction heating provides low or no thermal inertia, so that it will not cause the temperature overshoot. And the temperature can remain at set value of 0.5 degree difference.
What is the superiority of induction heating plastic granulator/plastic extrusion compared with traditional heaters?
Induction heater | Traditional heaters | |
Heating method | Induction heating is the process of heating an electrically conducting object (usually a metal) by electromagnetic induction, where eddy currents are generated within the metal and resistance leads to Joule heating of the metal. The induction coil itself does not get heated. The heat generating object is the heated object itself | Resistance wires get heated directly and heat is transferred by contact. |
heating up time | Quicker heating-up, higher efficiency | slower heating-up, lower efficiency |
Energy saving rate |
Save 30-80% energy rate,reduce working temperature |
Cannot save energy |
Installation | Easy to install | Easy to install |
Operation | Easy to operate | Easy to operate |
Maintenance |
Control box is easy to replace without turning off your machine |
Easy to replace but have to turning off your machine |
Temperature Control | Small thermal inertia and precise temperature control because the heater doesn’t get heated byitself. | Big thermal inertia, low accuracy in temperature control |
Product Quality | Higher product quality because of precise temperature control | Lower product quality |
Safety |
Outer sheath is safe to touch, lower surface temperature, no electric leakage. |
Temperature on outer sheath is much higher, easy to get burned. Electric leakage under wrong operation. |
Service life of heater | 2-4years | 1-2 years |
Service life of Barrel and Screw |
Longer usage life for barrel, screw etc. due to lower frequency of changing heaters. |
Shorter usage life for barrel, screw etc. |
Environment | Lower environment temperature; No noise | Much higher environment temperature and much noise |
Induction Heating Power Calculation
In the case of knowing the heating power of existing heating system, selecting an appropriate power according to load rate
- Load rate ≤ 60%, applicable power is 80% of the original power;
- Load rate between 60%-80%, select the original power;
- Load rate > 80%, applicable power is 120% of the original power;
When the heating power of existing heating system is unknown
- For injection molding machine, blown film machine and extrusion machine, the power should be calculated as 3W per cm2 according to the actual surface area of the cylinder (barrel);
- For dry cut pelletizing machine, the power should be calculated as 4W per cm2 according to the actual surface area of the cylinder (barrel);
- For wet cut pelletizing machine, the power should be calculated as 8W per cm2 according to the actual surface area of the cylinder (barrel);
2022年2月26日星期六
induction brazing carbide tip onto steel head teeth
high frequency induction brazing carbide tip onto steel head teeth process
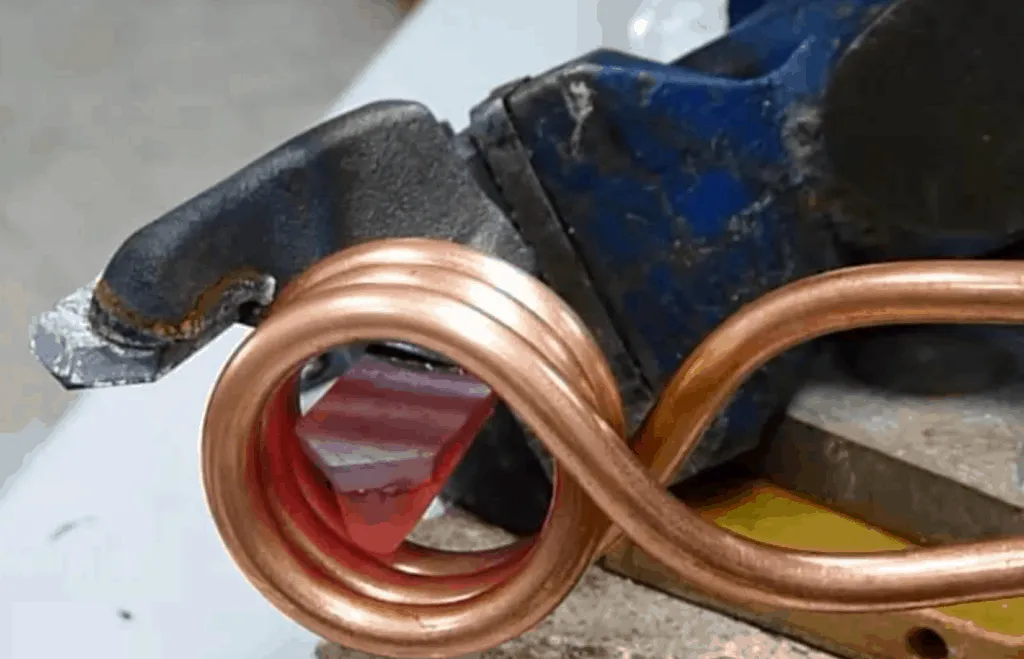

- Brazing paste is put on the tool
- The steel working head teeth are attached.
- The assembly is positioned in the three-turn coil.
- The assembly is heated.
- The joint is completed in 6 seconds.
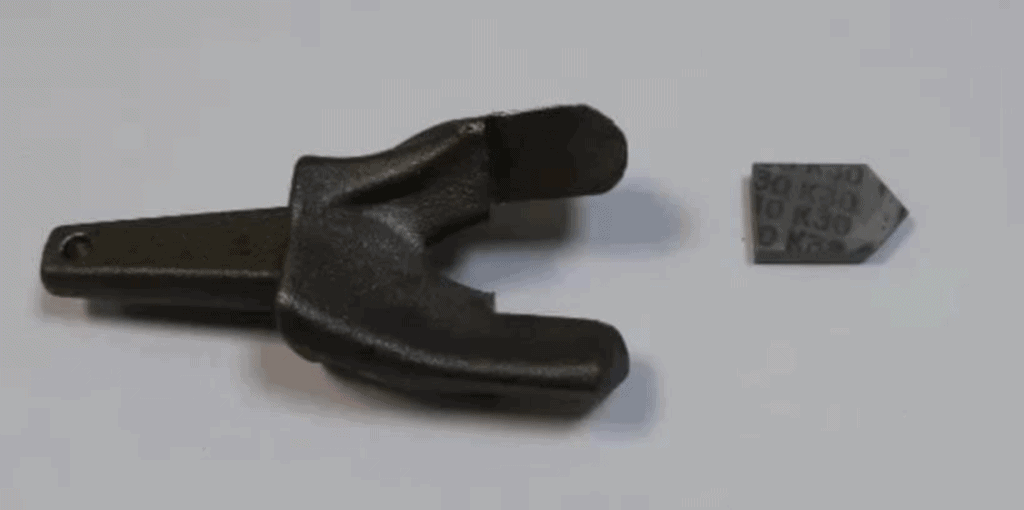
- Strong durable joints
- Selective and precise heat zone, resulting in less part distortion and joint stress than welding
- Less oxidation
- Faster heating cycles
- More consistent results and suitability for large volume production
- Safer than flame brazing
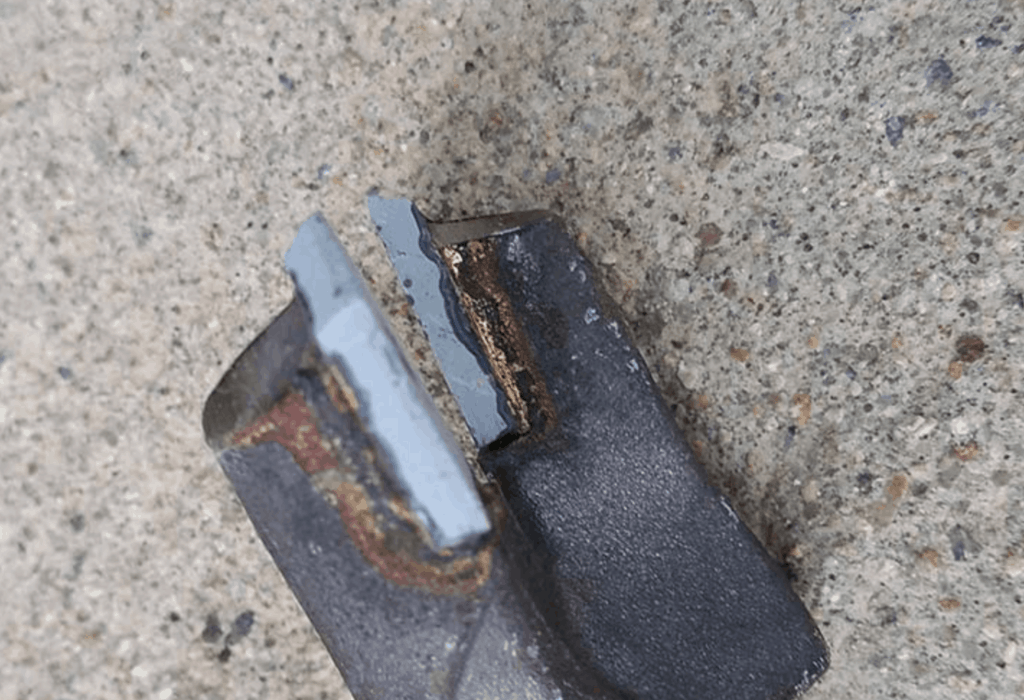
关注者
博客归档
-
▼
2022
(1729)
-
▼
二月
(98)
- Induction Brazing & Soldering Principle
- Induction Annealing Copper Tubes
- Induction Heating Barrel for Plastic Extruder and ...
- Induction Soldering Process Video
- Induction Heating Barrel for Plastic Extruder and ...
- Induction Brazing Aluminum Pipes
- How to design induction heating coil
- induction heating plastic granulator
- Induction heating bearings machine PDF
- induction heating plastic granulator
- induction heating plastic granulator
- induction brazing carbide tip onto steel head teeth
- Induction Brazing Carbide
- Induction Heating Injection Molding Machinery
- induction heating steel casting
- induction heating steel casting
- Induction Heating Plastic Extrusion
- induction heating plastic extrusion
- induction brazing automotive copper heating exchan...
- induction brazing automotive copper heating exchan...
- Brazing Copper Tube with Induction
- Induction Brazing Aluminum Tube T Joints
- Induction straightening deck and bulkhead heating ...
- Induction Soldering Wire To Aluminum Lug
- Induction Soldering Wires Onto Connection
- Shrink Fit Steel Gear onto Shaft
- Induction Brazing Steel Wire
- Induction annealing stainless steel wire
- Induction Preheating Steel Tubes
- Induction Soldering Brass Corner Joint
- Induction Soldering Coaxial Cable
- Induction Heating Automotive Motor
- Induction Melting Videos
- Why Choose Induction Heating and what are its adva...
- induction surface hardening steel screws
- High Frequency Brazing Stainless Steel Fittings
- ultrasonic welding equipment | ultrasonic plastic ...
- induction water boiler
- Brazing carbide shaft with induction
- Small High Frequency Induction Melting Furnace
- Shrink Fittting Part Removal application with Indu...
- Induction Soldering Wires Onto Connection
- Induction Soldering Cables to Terminals
- Induction Brazing Stainless Steel Tubing Joints
- Induction Brazing Carbide Onto Steel Part
- Application of induction aluminum melting furnace
- Induction Boiler
- Induction Heating Steel Part For Hot Heading
- Induction heating of aluminium billets
- Induction Brazing Carbide
- Induction Heating Steel Pipe To Remove plastic coa...
- Induction Brazing Carbide
- Induction Brazing Stainless Steel
- High Frequency Induction Brazing Copper Wire
- Brazing Automotive Parts With Induction
- Induction Brazing Carbide Onto Steel Part
- Brazing carbide shaft with induction
- Induction Heating Valve Head
- What Is Induction Heating?
- ultrasonic welding fabric machine for bonding nonw...
- induction preheating copper rod for hot forging
- Induction Annealing Aluminum
- induction heating stainless steel wire cable
- Induction Annealing Copper Wire
- induction heating for surface quenching of steel
- ELECTRIC INDUCTION FURNACE
- Induction Soldering Copper Pipes to PCB Board
- Induction Preheating Hot Rod Heading
- Plastic Injection Molding with Induction Heating
- Induction Brazing Carbide Onto Steel Part
- Induction Annealing Copper Tubes
- Induction hardening steel screw threads
- induction heating steel cable for cutting
- Induction Heating Valve Head
- Request a Quote
- Brazing Brass to Aluminum with Induction
- Induction Aluminum Brazing Process
- Induction Brazing Stainless Steel
- induction heating system technology PDF
- Induction Aluminum Brazing Process
- Induction Brazing Stainless Steel
- Induction Heating Steel Part For Hot Heading
- Brazing Carbide To Steel With Induction
- Brazing Automotive Parts With Induction
- Induction Brazing Copper Assembly
- Induction Soldering Copper Pipes to PCB Board
- Ultrasonic Welding Machine | Ultrasonic plastic We...
- Induction annealing copper wires
- Induction Brazing Basics
- Induction Billets Heater Video
- Brazing Copper to Brass Pipe With Induction
- What Is Induction Melting?
- Induction Brazing Steel Wire
- induction heating nanoparticle solution
- Induction Soldering Copper Pipes to PCB Board
- Induction Soldering Cable to Metallic Plate
- Aluminium Scraps Recycling Melting and Process
- induction curing
-
▼
二月
(98)
我的简介

- HLQ induction heating machine
- HLQ induction heating machine manufacturer provides the service of induction brazing,melting,hot forming,hardening surface,annealing,shrink fitting,PWHT,etc.