Why Choose Induction Heating and what are its advantages
Why choose induction heating over convection, radiant, open flame or another heating method? Here's a short summary of the major advantages that modern solid state induction heating offers for lean manufacturing:
Optimized Consistency
Induction heating eliminates the inconsistencies and quality issues associated with open flame, torch heating and other methods. Once the system is properly calibrated and set up, there is no guess work or variation; the heating pattern is repeatable and consistent. With modern solid state systems, precise temperature control provides uniform results; power can be instantly turned on or shut off. With closed loop temperature control, advanced induction heating systems have the capability to measure the temperature of each individual part. Specific ramp up, hold and ramp down rates can be established & data can be recorded for each part that is run.
Maximized Productivity
Production rates can be maximized because induction works so quickly; heat is developed directly and instantly (>2000º F. in < 1 second) inside the part. Startup is virtually instantaneous; no warm up or cool down cycle is required. The induction heating process can be completed on the manufacturing floor, next to the cold or hot forming machine, instead of sending batches of parts to a remote furnace area or subcontractor. For example, a brazing or soldering process which previously required a time-consuming, off-line batch heating approach can now be replaced with a continuous, one-piece flow manufacturing system.Improved Product Quality
With induction, the part to be heated never comes into direct contact with a flame or other heating element; the heat is induced within the part itself by alternating electrical current. As a result, product warpage, distortion and reject rates are minimized. For maximum product quality, the part can be isolated in an enclosed chamber with a vacuum, inert or reducing atmosphere to eliminate the effects of oxidation.Extended Fixture Life
Induction heating rapidly delivers site-specific heat to very small areas of your part, without heating any surrounding parts. This extends the life of the fixturing and mechanical setup.Environmentally Sound
Induction heating systems do not burn traditional fossil fuels; induction is a clean, non-polluting process which will help protect the environment. An induction system improves working conditions for your employees by eliminating smoke, waste heat, noxious emissions and loud noise. Heating is safe and efficient with no open flame to endanger the operator or obscure the process. Non-conductive materials are not affected and can be located in close proximity to the heating zone without damage.Reduced Energy Consumption
Tired of increasing utility bills? This uniquely energy-efficient process converts up to 90% of the energy expended energy into useful heat; batch furnaces are generally only 45% energy-efficient. And since induction requires no warm-up or cool-down cycle, stand-by heat losses are reduced to a bare minimum. The repeatability and consistency of the induction process make it highly compatible with energy-efficient automated systems.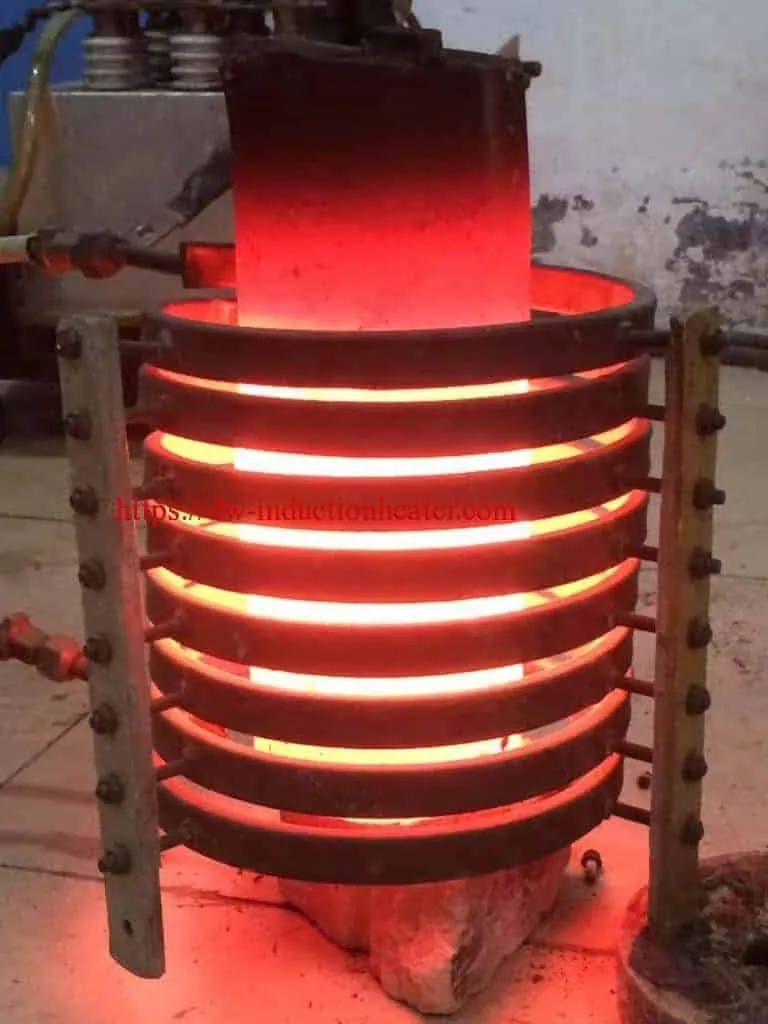
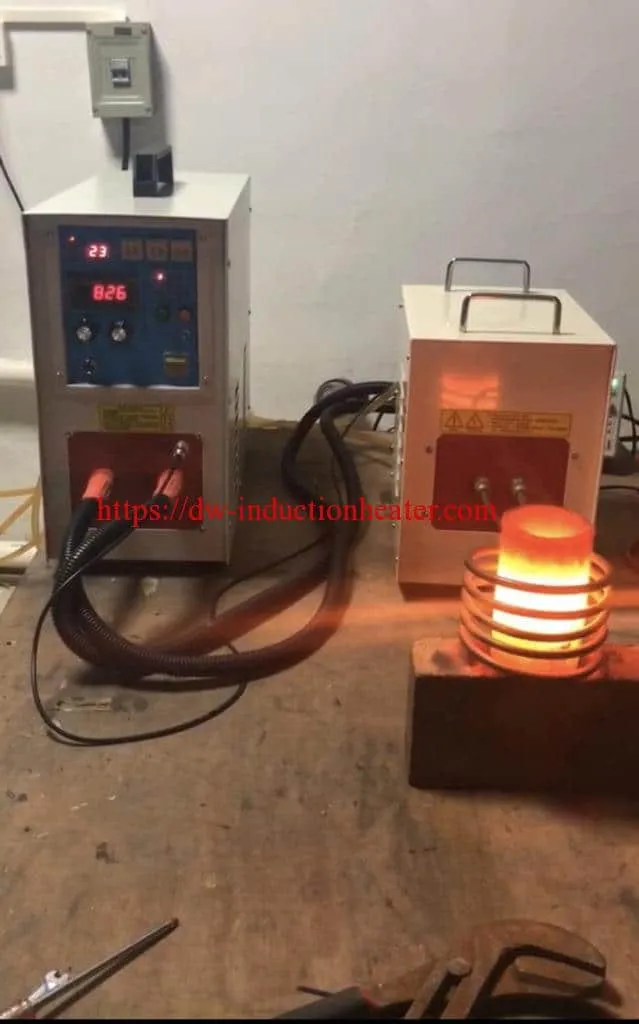
Applications: Induction heating is widely used for the surface hardening of the gears, shafts, crankshafts, cams, rollers, etc. of the workpiece, the purpose is to improve the abrasion resistance and anti-fatigue breaking capability of these artifacts. Automobile rear axle using induction heating surface hardening, fatigue design load cycles increases by about 10 times more than the quenched and tempered. Induction heating surface hardening of the workpiece material is generally in the carbon steel. In order to meet the special needs of some of the workpiece has been developed for induction heating surface hardening dedicated low hardenability steel. High-carbon steel and cast iron workpiece can also be used induction heating surface hardening. The quenching medium commonly Water or polymer solution. Equipment: Induction Heat Treatment Equipment power equipment, quenching machine and sensor. The main role of the power supply apparatus is suitable output frequency of the alternating current. The high-frequency current power supply tube high-frequency generator and two SCR inverter. IF current power supply generator sets. General power supply can only output a frequency current, some equipment can change the current frequency, directly with the 50 Hz power frequency current induction heating. Selection: the depth of the induction heating device selection and the workpiece requires heating layer. Heating the deep layer of the workpiece, using the current low frequency power supply apparatus; the heating layer shallow workpiece, the current high frequency power supply apparatus should be used. Select other conditions of the power supply is the power of the device. Heating surface area increases, the electrical power required by the corresponding increase. When the heating surface area is too large, or when insufficient power supply, the method may be continuously heated, so that the relative movement of workpiece and the sensor, the front heating, behind cooling. But the best, or the entire heating surface heating. This can use the the workpiece core section waste heat so that the hardened surface layer tempering so that the process is simplified, and also saving energy. The main role of the induction heating machine is the workpiece positioning and necessary movement. It should also be accompanied by the quenching media device. Quenching machine can be divided into standard machine tools and special machine tools, the former applies to the general workpiece, which is suitable for mass production of complex workpieces. Inductive heating of heat treatment, in order to ensure the quality of the heat treatment and to improve thermal efficiency, it is necessary according to the shape of the workpiece and requirements, design and manufacturing structure appropriate sensors. Common sensor heating the outer surface of the sensor, inner hole heating sensor plane heat sensor, universal heating sensor, a special type of heating sensor, a single type of heating sensors, the composite heated sensor, smelting furnace .