Induction straightening deck and bulkhead heating solutions
Induction straightening deck and bulkhead heating solutions times by as much as 80 per cent compared to alternative methods. Induction straightening is better at preserving metallurgical properties. It’s also the safest, healthiest, most environmentally friendly straightening method available.
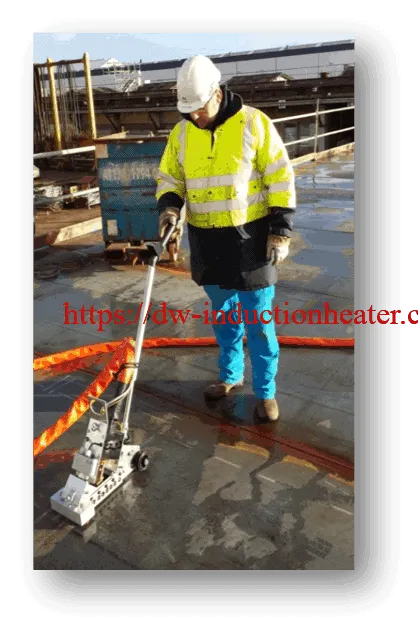
The traditional method used for this application is flame straightening. For this, a skilled operator is dedicated to provide heat in specific areas, following a heating pattern, which determines the reduction of distortion in the metal structure.
Currently this straightening process has high costs because it requires a large amount of skilled labour, high workplace hazards, contamination of work area and high energy consumption.
During the welding of plates to fixed structures, buckling stress is produced. In order to eliminate this distortion, different traditional deck and bulkhead straightening techniques are employed: welding of beads in non-visible areas, cutting and re-welding of plates, and stress relieving using flame heating. These techniques are big time consumers, costly and do not provide any added value. Improving the efficiency of this process is paramount.
The HLQ Induction Straightening Solution provides a simple, flexible, low-maintenance alternative to traditional deck and bulkhead straightening techniques. The quick, clean induction heating system rapidly generates heat with precision to relief the stress and straighten the plate.
Induction Portable Heating Design
The HLQ induction straightening heating System is housed in an all-in-one, portable container. The container is placed at a suppport beam; eyebolts are provided for easy movement.
Horizontal or Vertical Orientation
With just a tool change, the equipment can be used in either horizontal or vertical position. The system can be placed on both flat and tilted surfaces.
Low Maintenance
The HLQ
induction straightening heating System is designed for marine environments and meets both IP55 and AISI1316 requirements. The cabinet is made of stainless steel and the induction process requires no expendable materials.
Easy to Operate
System operators can master the three basic steps with just a few hours of training.
- Program selection based on plate thickness. The system handles steel plates with thickness of 4 to 20mm, and aluminum plates with thickness of 3 to 6 mm.
- Position the inductor on the heating tool, in horizontal or vertical orientation, at the desired location
- Press the start buttom to begin the program. The advanced induction technology generates the required amount of heat rapidly, without exceeding the Curie temperature.
What is induction straightening?
Induction straightening uses a coil to generate localized heat in pre-defined heating zones. As these zones cool, they contract, "pulling" the metal into a flatter condition.
Where is it used?
Induction heating is widely used to straighten ship decks and bulkheads. In the construction industry it straightens beams. Induction straightening is increas-ingly used in the manufacture and repair of locomotives, rolling stock and heavy goods vehicles.
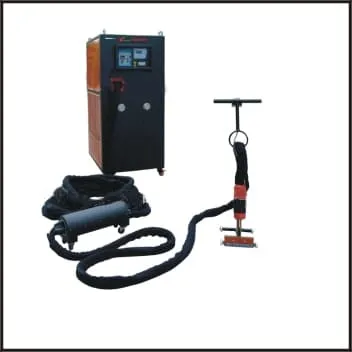
Induction straightening heating advantages
The replacement of flame straightening by the method of induction has the following advantages:
- Significant time reduction in the straightening operation
- Repeatability and heating quality
- Improved quality of working environment (no hazardous fumes)
- Improved safety for workers
- Energy and labor cost savings
Related industries are shipbuilding, railway and steel structures in construction among others.
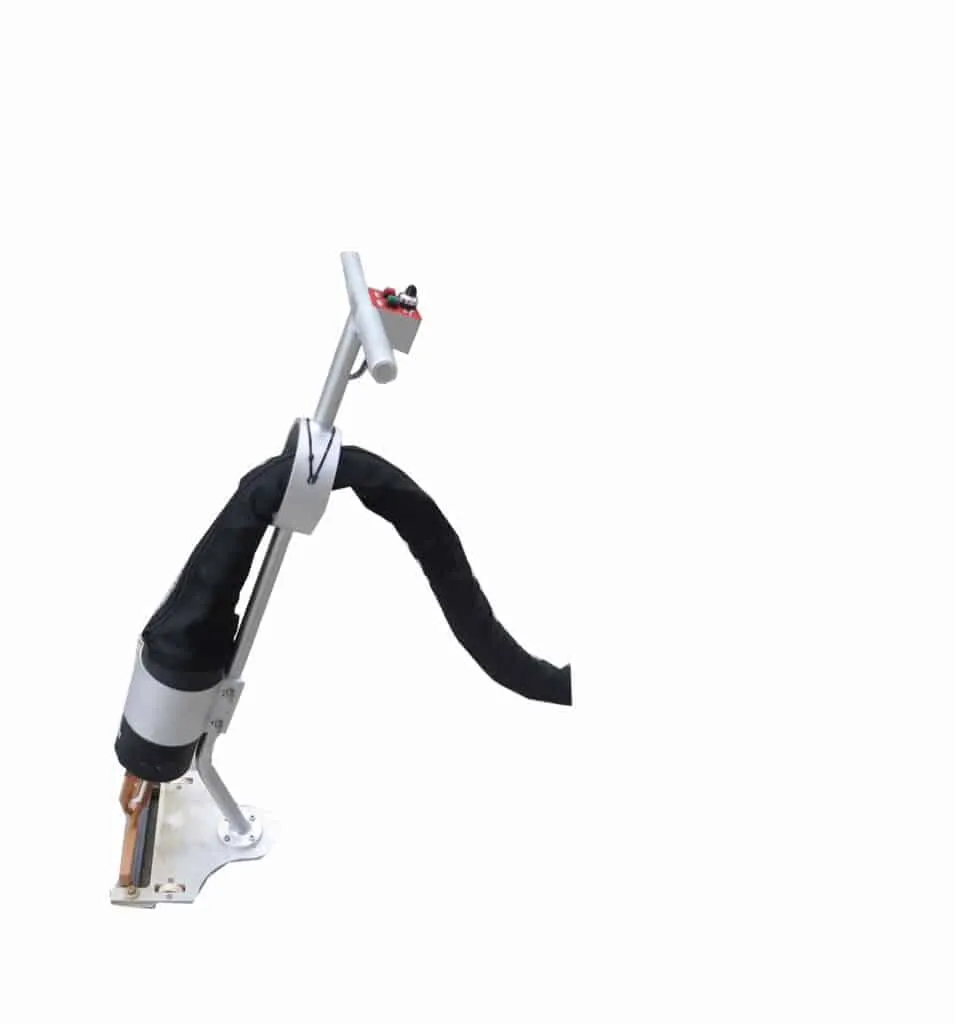