Rotary Furnace For Aluminum Melting and Recycling
Ever wondered how your discarded soda cans transform into shiny new aluminum products? The magic happens in rotary furnaces used for
aluminum melting and recycling. In this article, we’ll dive deep into the workings of rotary furnaces, their role in aluminum recycling, and their environmental impact. By the end, you'll have a comprehensive understanding of how these industrial powerhouses contribute to sustainability and efficiency.
Basics of Rotary Furnaces
-What is a Rotary Furnace?
A rotary furnace is a hightemperature processing unit that is used for melting various metals, including aluminum. Its cylindrical shape rotates around a horizontal axis. Imagine a giant, rotating drum that's heated—this motion helps mix the material inside, ensuring even melting and processing.
-How Rotary Furnaces Work?
So, how does all this rotation help? The rotation ensures that the heat is evenly distributed and that the molten metal is thoroughly mixed. This uniform heating and mixing are critical when dealing with metals like aluminum, which need consistent melting temperatures to ensure quality. These furnaces can be either directfired, where the flame is in direct contact with the metal, or indirectfired, where heat is applied externally. Cool, right?
Aluminum Melting in Rotary Furnaces
-Melting Process Overview
Melting aluminum in a rotary furnace involves loading the aluminum scrap into the furnace, which is then heated to its melting point. The rotating action helps stir the molten metal, creating a homogenous liquid. Once the aluminum is fully melted, it's tapped out from the bottom of the furnace and cast into new forms. This whole process is efficient and significantly reduces energy consumption compared to other methods.
-Advantages of Rotary Furnaces for Melting Aluminum
The perks? For one, rotary furnaces are incredibly efficient. The uniform mixing ensures a highquality melt, which is essential when you're aiming for premium aluminum products. Plus, these furnaces can handle a variety of scrap, from cans to foils, making them versatile. They’re also more environmentally friendly because they reduce the amount of dross (waste material) during the melting process.
Aluminum Recycling and Rotary Furnaces
-Why Aluminum Recycling is Importan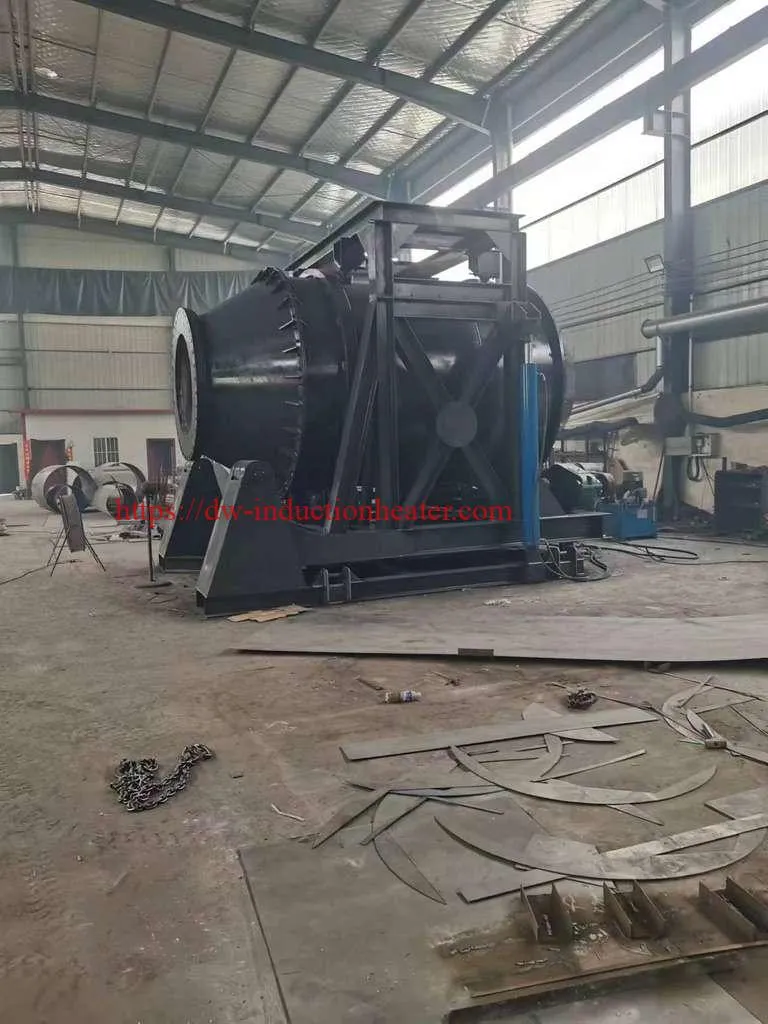
Recycling aluminum is a big deal. Not only does it save 95% of the energy compared to producing new aluminum from raw ore, but it also reduces landfill waste and cuts down on greenhouse gas emissions. Essentially, recycling is a winwin for both the economy and the environment.
-Role of Rotary Furnaces in Recycling
Rotary furnaces are the unsung heroes in the aluminum recycling process. They efficiently melt down aluminum scrap and convert it into reusable material. Because of their design, rotary furnaces can process a large amount of scrap quickly and efficiently, which is crucial in keeping up with the high demand for recycled aluminum.
Efficiency and Environmental Impact
Efficiency is key. Rotary furnaces not only speed up the recycling process but also use less fuel and produce fewer emissions compared to traditional furnaces. This efficiency translates into a smaller carbon footprint and less environmental degradation. Plus, improved automation and control systems mean less human error and better overall performance.
Types of Rotary Furnaces
DirectFired Rotary Furnaces
Directfired rotary furnaces have the flame directly touching the metal. This method is quick and efficient but requires careful control to avoid overheating. It’s like cooking on a stovetop—direct heat for fast results but needs constant attention.
IndirectFired Rotary Furnaces
In contrast, indirectfired furnaces use an external heat source. The metal doesn’t come into direct contact with the flame, resulting in a slower but more controlled melting process. Think of it as an ovenbaked approach—steady heat for even cooking, er, melting.
Planning for a Rotary Furnace Setup
Installation Considerations
Planning to set up a rotary furnace? First, consider the location. You’ll need a space that can handle the furnace's size and provide adequate ventilation. Then, think about electrical and fuel supply. Ensuring you have the necessary utilities set up can save a lot of headaches down the line.
Safety Measures
Safety is nonnegotiable. Make sure to have proper training for operators and install safety measures like emergency shutoff systems and regular maintenance schedules. Think of it as wearing a seatbelt—essential for protection in case something goes wrong.
Operating a Rotary Furnace
-Operational Tips
Smooth operation comes down to routine. Regularly check the furnace's temperature controls and ensure proper loading and unloading techniques. It's like maintaining a car—keep an eye on the little things, and the big things will run smoothly.
-Common Challenges and Solutions
Every system has its hiccups. With rotary furnaces, common issues include irregular heating and mechanical wear. The solution? Regular maintenance and timely repairs. Being proactive can prevent small problems from becoming big ones.
Maintenance of Rotary Furnaces
-Routine Maintenance Tasks
Routine checks are your best friend. Inspect the furnace lining, monitor temperature gauges, and keep the rotating parts welllubricated. Regular cleaning to remove buildup can also extend the furnace's lifespan.
-Troubleshooting Common Issues
Facing issues? For uneven heating, check the burners and ensure they are functioning correctly. For mechanical wear, look into the bearings and rotating parts—they often need timely replacements to avoid more significant issues.
Future of Rotary Furnaces in Aluminum Recycling
-Technological Advancements
The future looks bright! Innovations like advanced control systems and automated processes are set to make rotary furnaces even more efficient and userfriendly. Imagine furnaces that can selfdiagnose issues and adjust operations for optimal performance—it’s not far off.
-Trends to Watch
Keep an eye on trends like ecofriendly designs and smart technology integration. Enhanced recycling capabilities and reduced emissions are the industry's next big things, ensuring a sustainable future for aluminum recycling.
Conclusion
The next time you recycle an aluminum can, picture the incredible journey it takes through a rotary furnace. These machines are at the forefront of metal recycling, making significant contributions to environmental sustainability and industrial efficiency. With advancements on the horizon, the role of rotary furnaces is only going to become more pivotal. So, keep recycling and appreciate the technology that makes it all possible!
FAQs
- What is a rotary furnace used for in aluminum recycling?
A
rotary furnace melts down aluminum scrap for recycling. Its rotating action ensures even melting and superior efficiency.
- How does a rotary furnace differ from a traditional furnace?
A rotary furnace rotates, ensuring uniform heat distribution and mixing, which is more efficient than the static design of traditional furnaces.
- Are rotary furnaces environmentally friendly?
Yes, they are. They use less fuel, produce fewer emissions, and help recycle aluminum, significantly reducing environmental impact.
- What are common issues faced when operating rotary furnaces?
Typical problems include irregular heating and mechanical wear. Regular maintenance can mitigate these issues.
- What advancements are expected in the future for rotary furnaces?
Future advancements include better automation, ecofriendly designs, and smart technology for improved efficiency and lower emissions.
https://dw-inductionheater.com/product/rotary-furnace-for-aluminum-melting-and-recycling?feed_id=253885&_unique_id=669b8e1c1dc2d