Tilting Rotary Furnace for Melting Zinc Alloy and Aluminum
The industrial foundry sector is an essential cog in the manufacturing machine, dealing heavily with metals such as zinc alloy and aluminum. Among the technological advancements improving efficiency and effectiveness in this field is the tilting rotary furnace. This article delves into the intricate workings, benefits, and future of these furnaces, with a special emphasis on their application in melting zinc alloys and aluminum.
What is a Tilting Rotary Furnace?
A
tilting rotary furnace is a type of furnace utilized in metallurgy for melting and recycling non-ferrous metals. Its design allows for the tilting of the furnace body, making the pouring of molten metal significantly safer and more efficient.
Basic Components
Furnace Body: The main structure, typically cylindrical, constructed from robust materials to withstand high temperatures and chemical reactions.
Burner System: Provides the necessary heat for melting operations, using industrial-grade gas or oil.
Tilting Mechanism: Often hydraulic or mechanical, this component facilitates the controlled pouring of molten metal.
Refractory Lining: High-temperature resistant lining that protects the furnace body and retains heat.
Control Systems: Automated control systems ensure precise temperature regulation and safety protocols.
Operating Principle
The furnace rotates during operation, ensuring homogeneity in the melt through continuous motion. This rotation, combined with the tilting feature, allows for efficient pouring and minimizes metal loss.
Advantages of Using Tilting Rotary Furnaces
The advent of tilting rotary furnaces brought multiple benefits to metal melting operations.
Versatility
These furnaces handle various materials, making them ideal for foundries that deal with multiple metal types.
Efficiency
Enhanced heat transfer and uniform mixing lead to shortened melting cycles and higher throughput.
Cost-Effectiveness
Reduced energy consumption and lower operating times translate into significant cost savings for foundries.
Application in Melting Zinc Alloy
Zinc alloys are crucial for die-casting, requiring precise melting techniques that tilting rotary furnaces aptly provide.
Material Properties
Zinc alloys have relatively low melting points and high casting precision requirements, which the furnace's controlled environment can ensure.
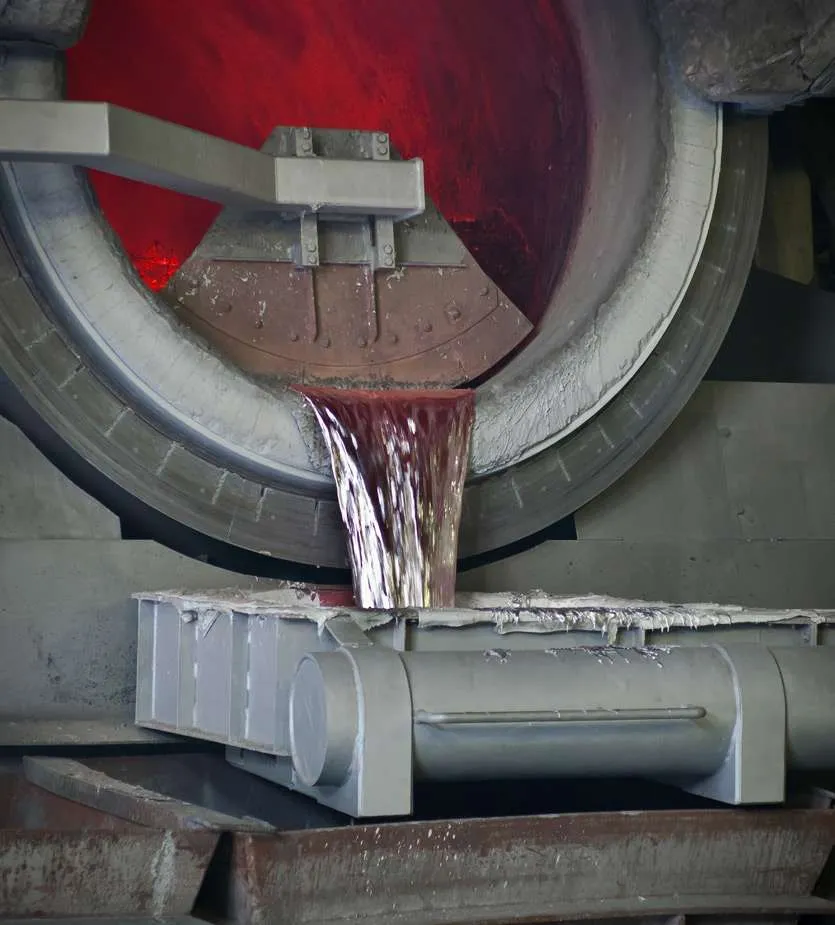
Temperature Control
Effective temperature management is vital for maintaining the material properties of zinc alloys.
Homogeneous Melting
The rotary action guarantees uniform heat distribution, a critical factor for high-quality zinc alloy melts.
Application in Melting Aluminum
Aluminum melting presents distinct challenges that these furnaces efficiently manage.
Aluminum Characteristics
Aluminum has a distinct melting point and is prone to oxidation, requiring careful control within the furnace.
Reducing Oxidation
The controlled atmosphere in the tilting rotary furnace minimizes oxygen exposure, thus reducing oxidation and ensuring the integrity of the aluminum melt.
Energy Savings
The efficient design and operation of these furnaces lead to substantial energy savings, crucial in large-scale aluminum processing.
Choosing the Right Furnace for Your Foundry
Selecting an appropriate furnace is critical for optimal foundry operations.
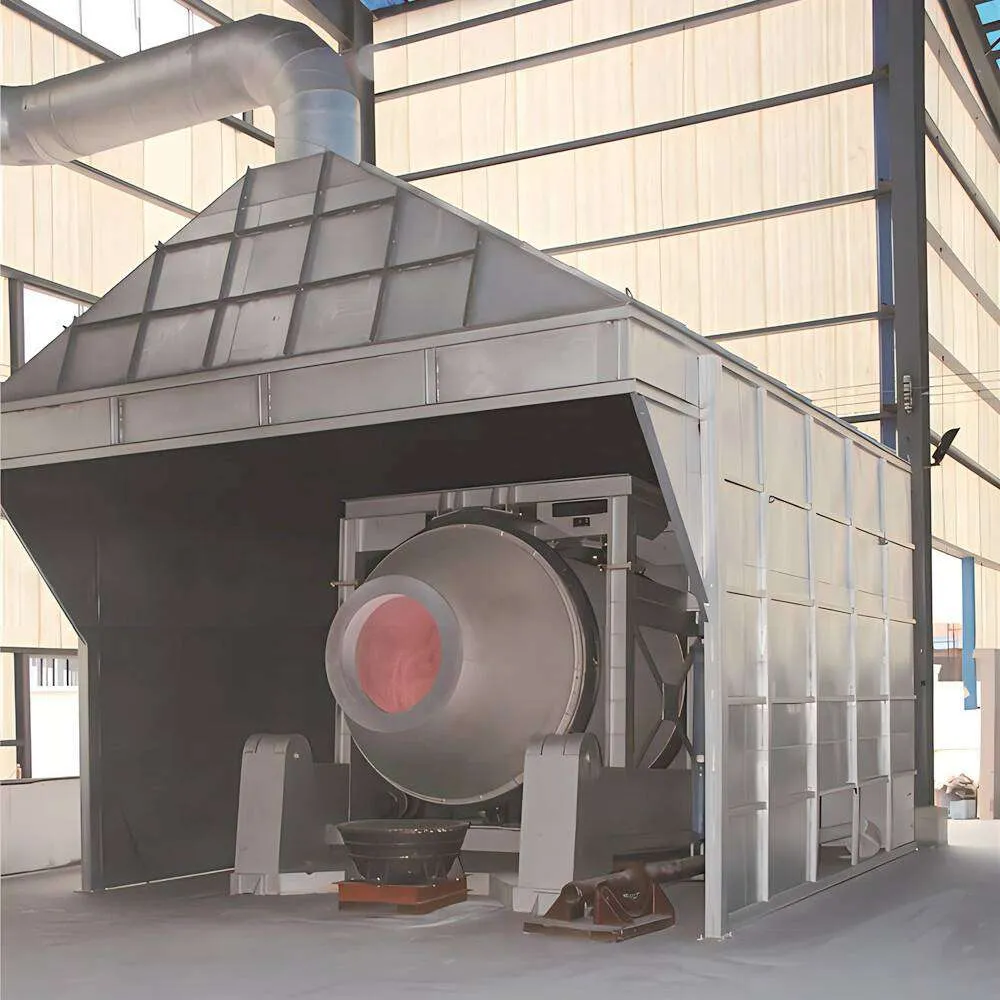
Capacity and Scale
Foundries must match furnace capacity with their production needs to avoid bottlenecks and ensure efficient workflows.
Technological Compatibility
Integration with existing systems and the ability to future-proof operations with modern technology is crucial.
Maintenance Requirements
Consideration of the ease and frequency of maintenance can significantly impact long-term operational costs and uptime.
Installation and Setup Process
Proper installation is essential for the safe and efficient operation of tilting rotary furnaces.
Site Preparation
Adequate space and foundational preparations are required to accommodate the furnace and its operations.
Electrical and Fuel Connections
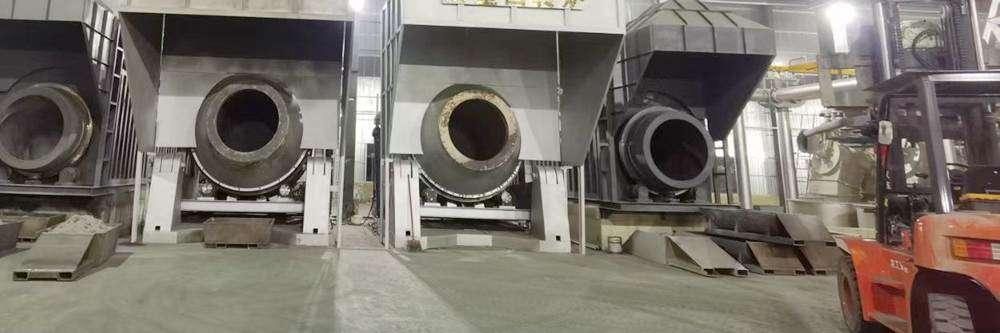
Ensuring reliable and safe connections to power and fuel sources is necessary for operational efficiency.
Operational Testing
Thorough testing post-installation guarantees that all systems function correctly and safely before full-scale operations commence.
Safety Measures and Compliance
Safety is a significant concern in high-temperature operations involving heavy machinery.
Operator Training
Comprehensive training programs for operators ensure safe and efficient furnace operations.
Regulatory Standards
Compliance with industry-specific safety and environmental regulations is mandatory to avoid legal repercussions and ensure worker safety.
Maintenance and Troubleshooting
Regular maintenance and prompt troubleshooting are vital for keeping the furnace in optimal condition.
Routine Maintenance
Scheduled inspections and servicing prevent breakdowns and extend the furnace's operational life.
Common Issues and Solutions
Understanding typical issues, such as refractory wear or burner inefficiencies, and their solutions can mitigate downtime and repair costs.
Future Trends in Rotary Furnace Technology
The landscape of rotary furnace technology continues to evolve with advancements aiming at increased efficiency and sustainability.
Automation
Incorporating advanced automation into furnace operations enhances precision, reduces manual labor, and improves safety.
Eco-Friendly Innovations
Developments in eco-friendly technologies, such as improved insulation materials and alternative energy sources, are making these furnaces greener.
Conclusion
Tilting rotary furnaces represent a significant advancement in the melting and recycling of non-ferrous metals, providing unparalleled efficiency, versatility, and cost savings. Their application in zinc alloy and aluminum melting showcases their adaptability and effectiveness, making them an indispensable tool in modern foundries.
FAQs
Key advantages of a tilting rotary furnace:
Enhanced efficiency, versatility in handling various metals, and cost-effectiveness stand out as primary benefits.
Capability to handle zinc alloy and aluminum
The furnace's design ensures precise temperature control and homogeneity, making it suitable for melting zinc alloys and aluminum.
Impact of operator training on efficiency
Proper training ensures that operators can manage the furnace safely, reducing downtime and operational errors.
Energy savings associated with these furnaces
Design improvements and high-efficiency components lead to significant reductions in energy consumption.
Ensuring compliance with regulatory standards
Strict adherence to regulatory standards through robust safety and operational protocols ensures legal compliance and safety.
https://dw-inductionheater.com/product/tilting-rotary-furnace-for-melting-zinc-alloy-and-aluminum?feed_id=253947&_unique_id=66a36b191e575