
Enhancing Efficiency and Control: Induction Heating Fluidized Bed Reactors
Introduction
Fluidized bed reactors are integral to many industrial processes due to their excellent heat and mass transfer properties. When combined with induction heating technology, these reactors achieve a new level of efficiency, control, and environmental sustainability. This article delves into the principles and advantages of induction heating fluidized bed reactors, their applications across various industries, and the challenges and future directions of this innovative technology.Principles of Fluidized Bed Reactors
Fluidized bed reactors operate by suspending solid particles in an upward flow of gas or liquid, creating a state that mimics fluid behavior. This fluidization enhances mixing and allows for uniform temperature distribution, making these reactors ideal for processes such as combustion, drying, and chemical reactions. Key components and principles include: 1. **Distributor Plate**: Ensures even distribution of the fluidizing medium to achieve consistent fluidization. 2. **Solid Particles**: Act as the medium for reactions, ranging from fine powders to larger granules. 3. **Fluidizing Medium**: Typically air, steam, or other gases, chosen based on process requirements. 4. **Enhanced Transfer Rates**: The fluidized state significantly improves heat and mass transfer rates within the reactor.Applications of Fluidized Beds
1. Chemical Reactions: Fluidized beds are widely used in catalytic cracking, gasification, and other chemical reactions where efficient mixing and temperature control are crucial for optimizing reaction rates and product yields.
2. Combustion: In fluidized bed combustion, fuels such as coal, biomass, or waste materials are burned more efficiently due to the enhanced mixing and heat transfer, resulting in lower emissions and better combustion control.
3. Drying: Fluidized bed dryers are used to remove moisture from solid particles, providing uniform drying conditions and preventing overheating or degradation of the material.
4. Coating and Granulation: Fluidized beds are used in the pharmaceutical and food industries for coating particles with protective or functional layers and for granulating powders into larger, more manageable particles.
5. Heat Treatment: Metal and ceramic particles can be uniformly heated or cooled in fluidized beds, ensuring consistent treatment and improving the quality of the final product.
Principles of Induction Heating
Induction heating generates heat within conductive materials through electromagnetic induction. An alternating current (AC) passes through a coil, creating a varying magnetic field that induces eddy currents in nearby conductive materials.Integration of Induction Heating with Fluidized Bed Reactors
Combining induction heating with fluidized bed reactors leverages the benefits of both technologies, resulting in superior process performance. Here’s how this integration enhances fluidized bed reactors: 1. **Uniform Heating**: Induction heating ensures direct and uniform heating of conductive particles, maintaining consistent temperatures throughout the reactor. 2. **Energy Efficiency**: Induction heating minimizes energy loss, reducing operational costs and improving sustainability. 3. **Environmental Impact**: Non-contact heating eliminates the need for combustion, lowering emissions of pollutants and greenhouse gases. 4. **Enhanced Process Control**: Precise control over heating parameters allows for optimization of reaction conditions, improving product quality and yield.Applications of Induction Heated Fluidized Bed Reactors
The integration of induction heating in fluidized bed reactors has broad applications across various industries: 1. **Chemical Processing**: Ideal for catalytic reactions and other processes requiring precise temperature control, such as methanation and Fischer-Tropsch synthesis. 2. **Material Processing**: Suitable for sintering, melting, and heat treatment of metals and ceramics, ensuring consistent material properties. 3. **Energy Production**: Enhances processes like biomass gasification and pyrolysis, maximizing energy output and efficiency. 4. **Environmental Remediation**: Effective for soil decontamination and waste treatment, offering rapid and uniform heating.Advantages of Induction Heated Fluidized Bed Reactors
1. **Improved Efficiency**: Enhanced heat transfer and mixing lead to higher reaction rates and yields. 2. **Cost Savings**: Reduced energy consumption and lower operational costs due to the efficiency of induction heating.
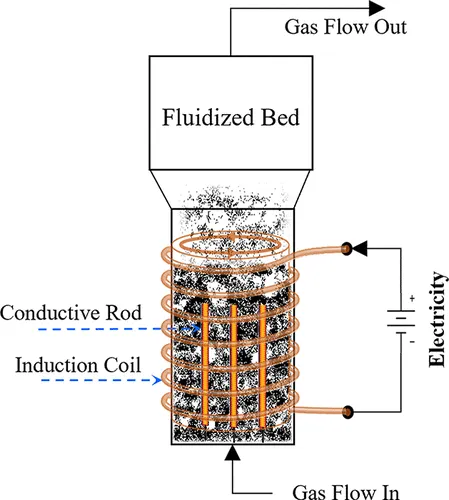
Challenges and Future Directions
Despite the numerous advantages, several challenges need to be addressed: 1. **Design Optimization**: Developing efficient induction coil and power supply designs to ensure uniform heating and minimize energy loss. 2. **Material Durability**: Ensuring the durability of reactor materials and particles subjected to continuous motion and heating. 3. **Scalability**: Expanding the technology for large-scale industrial applications while maintaining efficiency and control. Future research should focus on optimizing reactor designs, exploring new conductive materials and coatings, and expanding the range of applications. Collaboration between industry and academia will be crucial in overcoming these challenges and realizing the full potential of induction heated fluidized bed reactors.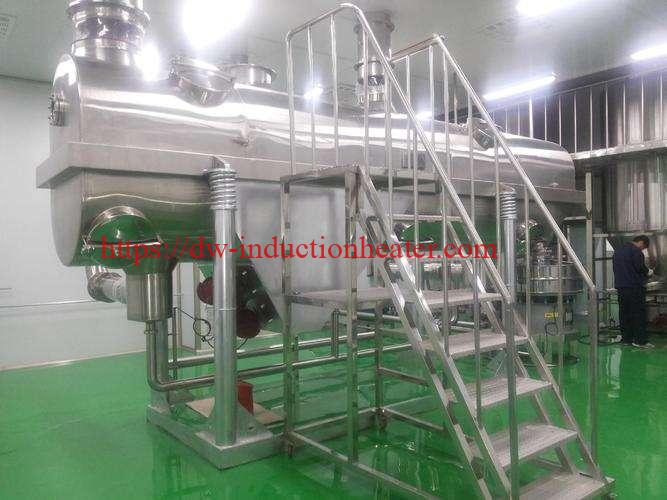