
2024年6月30日星期日
What Is Induction Melting?

what is induction forging?

2024年6月29日星期六
Induction Brazing Aluminum Pipes

Brazing Aluminum to Copper Tubes with Induction
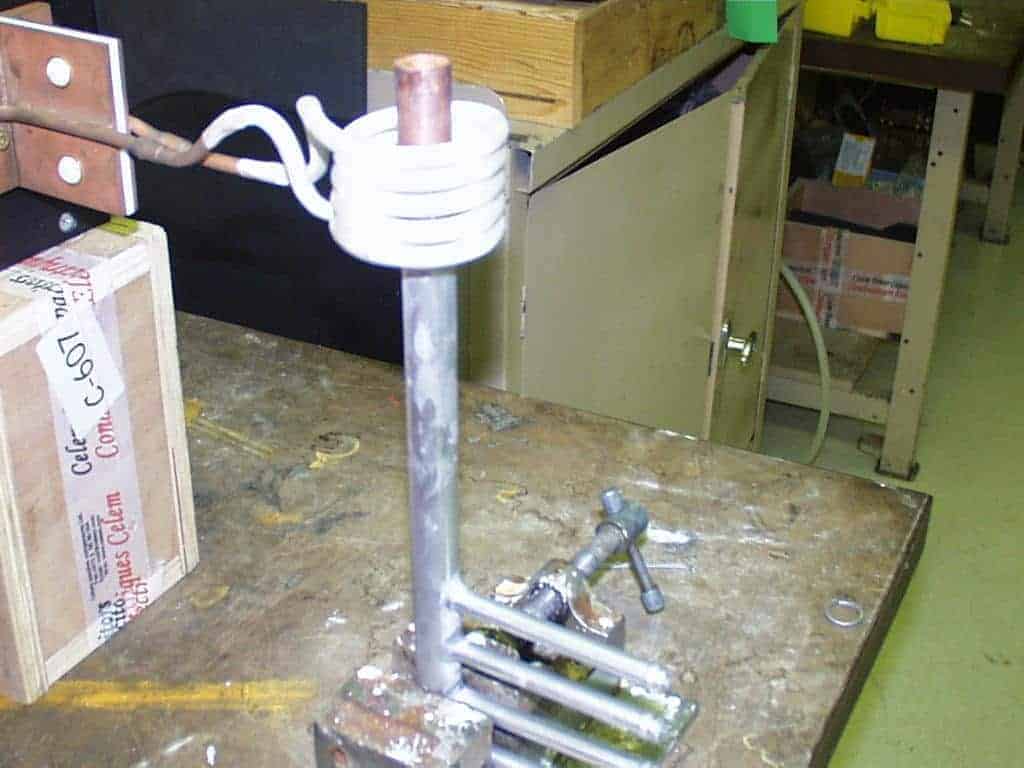
- Cu tubes (3/4"/19mm)
- Cu tubes (5/8"/15.8mm)
- AI tubes (3/8"/9.5mm)
- AI manifold (5/8"/15.8mm)
- AI manifold (3/4"/19mm)
- Lucas-Milhaupt Handy One alloy 30-832
- Braze wire
- A two-turn oval helical induction heating coil designed and developed specifically for the aluminum assembly
- A five-turn helical induction heating coil designed and developed specifically for brazing the Cu tubes to AI joint assembly
- The client wanted more precise and repeatable heating than a torch could deliver, which induction was able to achieve .
- Temperature control: Induction allows for superior temperature control when compared to other methods, including a torch, which the client desired
2024年6月28日星期五
Brazing Aluminum Pipes Assembly With Induction

- Speed: The recommended approach cut their heating time in half when compared to using a torch
- Part quality: Induction heating is a repeatable method with more consistency than a torch can generally deliver
- Safety: Induction heating is a clean, precise method that does not involve an open flame like a torch, which results in a safer work environment
Induction Aluminum Brazing Process

2024年6月27日星期四
What Is Induction Heating Coil&Inductor?

2024年6月26日星期三
Brazing Carbide To Steel With Induction

Brazing Brass to Aluminum with Induction

2024年6月25日星期二
Brazing Carbide Tool Tips With Induction

Reducing Heavy Oil Viscosity and Enhancing Fluidity With Induction Heating
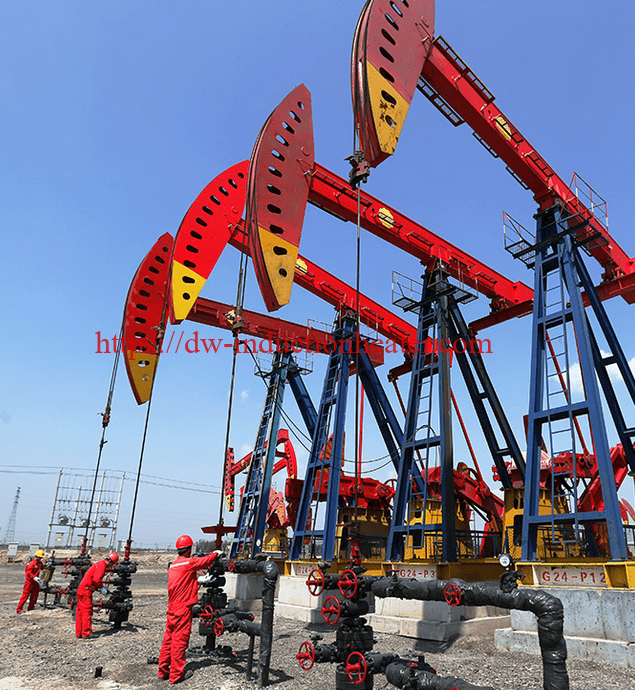
Electromagnetic Transformation: Reducing Heavy Oil Viscosity and Enhancing Fluidity With Induction Heating
-
Introduction
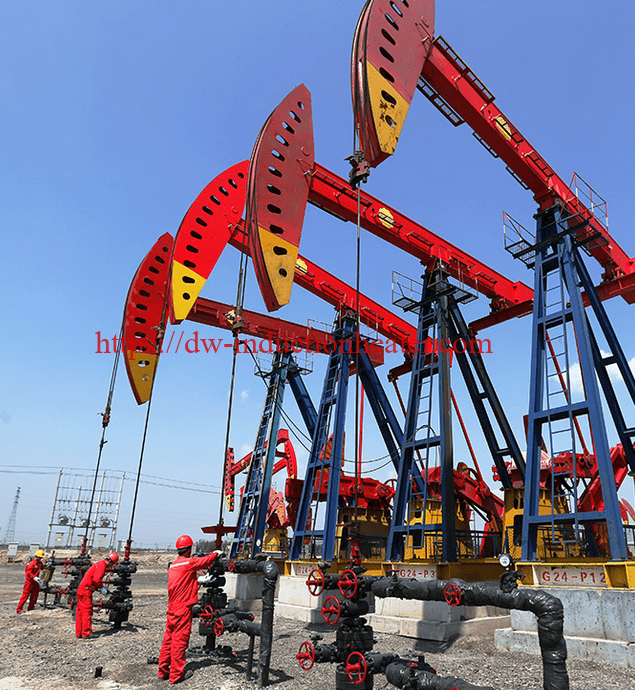
-
Fundamentals of Induction Heating
-
Challenges of Heavy Oil Viscosity
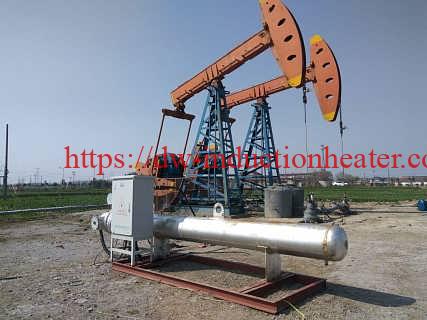
-
Mechanism of Viscosity Reduction through Induction Heating
Induction heating effectively reduces the viscosity of heavy oil through direct and localized heating, which increases the temperature of the oil and decreases its viscosity. The process involves the generation of heat through electromagnetic induction, which in turn influences the molecular dynamics and rheological properties of the oil. Induction Heating Process Placement of Induction Coils: The first step in the induction heating process involves the strategic placement of induction coils. These coils can be installed within the wellbore or around the pipeline carrying the heavy oil. The placement is crucial to ensure that the electromagnetic field generated by the coils effectively interacts with the oil to induce the desired heating effect. Generation of Eddy Currents: When alternating current (AC) flows through the induction coil, it creates a rapidly changing magnetic field around the coil. This alternating magnetic field penetrates the conductive material of the heavy oil. As a result, eddy currents are induced within the oil. These currents circulate within the oil and are responsible for generating heat due to electrical resistance. Heat Production: The heat generated by the eddy currents is a result of the Joule effect, where electrical energy is converted into thermal energy. As the eddy currents flow through the oil, they encounter resistance, which produces heat. This localized heating raises the temperature of the oil, effectively reducing its viscosity. Molecular Dynamics and Thermal Effects Increased Molecular Kinetic Energy: The heat produced by the induction process raises the kinetic energy of the oil molecules. As the temperature increases, the molecules gain more energy and move more freely. This increased molecular motion reduces the internal friction within the oil, making it less viscous. Weakening of Intermolecular Forces: Heavy oil contains large hydrocarbon molecules with strong intermolecular forces, such as van der Waals forces and hydrogen bonding, which contribute to its high viscosity. As the temperature rises, these intermolecular forces weaken, allowing the molecules to move past each other more easily. This reduction in intermolecular forces is a key factor in lowering the viscosity of the oil. Enhanced Fluidity: The combination of increased molecular kinetic energy and weakened intermolecular forces results in enhanced fluidity of the heavy oil. The oil becomes more mobile and easier to pump and transport through pipelines. This improved flow characteristic is essential for efficient extraction and transportation. Changes in Rheological Properties Viscosity Reduction: One of the most significant changes in the rheological properties of heavy oil due to induction heating is the reduction in viscosity. As the temperature of the oil increases, its viscosity decreases significantly. This change can be quantitatively measured using rheometers or viscometers, and the relationship between temperature and viscosity can be plotted to understand the effectiveness of the induction heating process.Improved Flow: The reduction in viscosity translates to improved flow characteristics of the heavy oil. Enhanced fluidity means that the oil can be more easily mobilized within the reservoir, leading to better extraction rates. In pipelines, the reduced viscosity minimizes frictional losses, allowing for smoother and more efficient transportation of the oil. By understanding the mechanism of viscosity reduction through induction heating, it becomes evident how this technology can revolutionize the extraction and transportation of heavy oil. The direct and localized heating provided by induction heating offers a highly efficient and controlled method to address the challenges posed by high-viscosity heavy oil, making it a valuable tool in the oil industry's efforts to optimize production and reduce operational costs.
-
Experimental Studies and Results
Results and Analysis:
- Temperature-Velocity Correlation: A clear correlation was observed between the increase in temperature and the decrease in viscosity. - Optimal Heating Parameters: Specific frequencies and power levels were identified as optimal for reducing viscosity without causing thermal degradation of the oil. - Case Studies: Field applications in locations such as Canada’s oil sands demonstrated practical effectiveness, with significant improvements in extraction rates and cost reductions.-
Advantages of Induction Heating for Heavy Oil
-
Applications in the Oil Industry
Induction heating offers several advantages in the oil industry, particularly in enhancing oil recovery processes, achieving practical successes in field applications, and integrating with existing extraction infrastructure. This section delves into how induction heating is being applied in various contexts to optimize oil extraction and transportation. Enhanced Oil Recovery (EOR) Techniques Enhanced Oil Recovery (EOR) methods are designed to increase the amount of crude oil that can be extracted from an oil field. Induction heating has shown significant promise in improving the efficiency and effectiveness of various EOR techniques. Steam-Assisted Gravity Drainage (SAGD): Steam-Assisted Gravity Drainage (SAGD) is a widely used EOR technique, particularly in the extraction of bitumen from oil sands. In SAGD, steam is injected into the reservoir to reduce the viscosity of the bitumen, allowing it to flow more easily to a production well. Induction heating can be used to preheat the reservoir, which enhances the efficiency of the SAGD process. By raising the initial temperature of the bitumen, induction heating reduces the amount of steam required, thereby lowering operational costs and improving overall energy efficiency. Additionally, preheating the reservoir with induction can shorten the startup time for the SAGD process, leading to faster production rates. Cyclic Steam Stimulation (CSS): Cyclic Steam Stimulation (CSS), also known as the "huff and puff" method, involves injecting steam into a well, allowing it to soak, and then producing the heated oil. The cyclic nature of CSS can benefit significantly from the integration of induction heating. By combining CSS with induction heating, the oil's mobility and extraction rates can be further enhanced. The heat generated by induction can be precisely controlled and applied where needed, ensuring uniform heating of the oil and reducing the thermal stress on the reservoir. This approach not only improves the efficiency of CSS but also extends the life of the wells and maximizes oil recovery. Field Applications and Success Stories The practical application of induction heating in the field has yielded impressive results, demonstrating its potential to revolutionize oil extraction processes. Canada’s Oil Sands: Canada’s oil sands are one of the largest reserves of bitumen, and the extraction of this heavy oil poses significant challenges due to its high viscosity. The successful deployment of induction heating in Canada’s oil sands has led to improved recovery rates and reduced costs. In pilot projects, induction heating has been used to preheat bitumen reservoirs, enhancing the effectiveness of traditional EOR techniques like SAGD and CSS. These projects have reported increased production rates, lower steam-to-oil ratios, and reduced greenhouse gas emissions. The success in Canada’s oil sands serves as a testament to the viability of induction heating in large-scale heavy oil extraction. Venezuela’s Orinoco Belt: The Orinoco Belt in Venezuela contains some of the most viscous heavy oil reserves in the world. Induction heating has been employed to enhance the extraction of this highly viscous oil, demonstrating significant benefits. Field applications in the Orinoco Belt have shown that induction heating can effectively reduce the viscosity of the heavy oil, making it more fluid and easier to extract. This has led to improved production rates and a more cost-effective extraction process. The ability to target specific areas of the reservoir with induction heating has also minimized environmental impact and reduced the need for extensive infrastructure modifications. Integration with Existing Extraction Processes One of the key advantages of induction heating is its compatibility with existing extraction processes and infrastructure, making it a versatile and scalable solution for the oil industry. Compatibility: Induction heating can be seamlessly integrated with existing extraction infrastructure, providing a straightforward addition to current operations. The technology can be implemented in both new and existing wells, allowing operators to enhance oil recovery without the need for significant modifications. The adaptability of induction heating systems means they can be tailored to fit various well configurations and reservoir conditions. This compatibility ensures that the benefits of induction heating can be realized with minimal disruption to ongoing operations. Scalability: The technology is scalable, making it suitable for both small and large-scale operations. Induction heating systems can be designed to meet the specific needs of different oil fields, from small pilot projects to extensive commercial operations. The scalability of induction heating allows for incremental implementation, enabling operators to start with smaller installations and expand as needed based on performance and results. This flexibility makes induction heating an attractive option for a wide range of applications, from enhancing production in mature fields to developing new heavy oil reserves. In summary, the applications of induction heating in the oil industry are vast and varied. By improving the efficiency of EOR techniques, achieving practical success in field applications, and seamlessly integrating with existing infrastructure, induction heating is poised to play a crucial role in the future of oil extraction. The technology’s ability to reduce viscosity, enhance fluidity, and optimize production processes offers significant economic and environmental benefits, making it a valuable tool for the industry.
-
Future Prospects and Innovations

-
Conclusion
Brazing Brass To Copper With Induction

Reducing Heavy Oil Viscosity and Enhancing Fluidity With Induction Heating
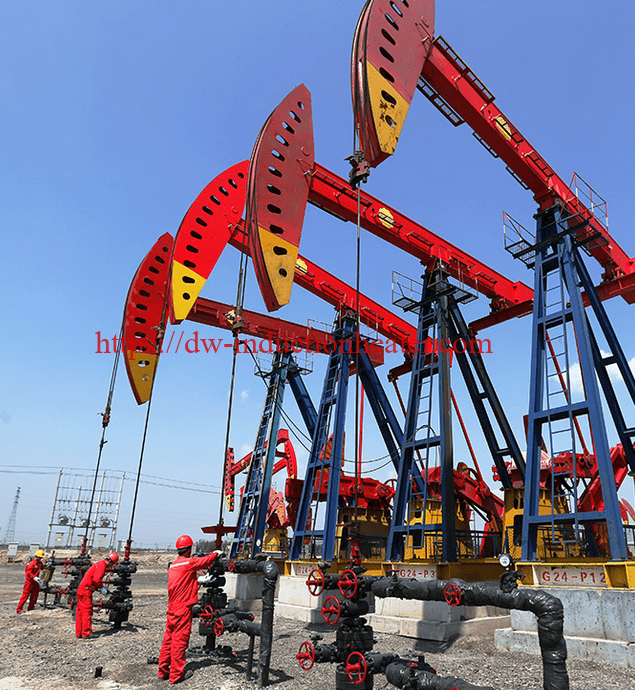
Electromagnetic Transformation: Reducing Heavy Oil Viscosity and Enhancing Fluidity With Induction Heating
-
Introduction
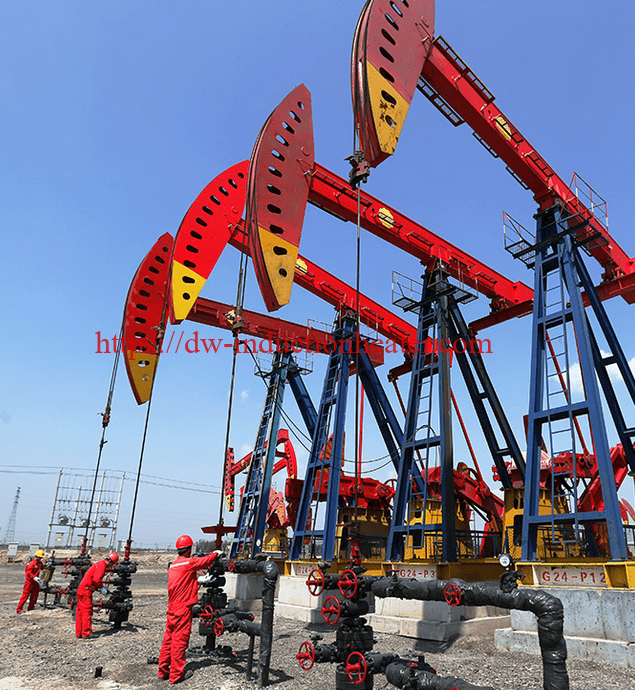
-
Fundamentals of Induction Heating
-
Challenges of Heavy Oil Viscosity
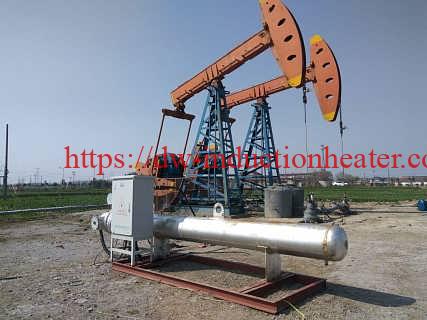
-
Mechanism of Viscosity Reduction through Induction Heating
Induction heating effectively reduces the viscosity of heavy oil through direct and localized heating, which increases the temperature of the oil and decreases its viscosity. The process involves the generation of heat through electromagnetic induction, which in turn influences the molecular dynamics and rheological properties of the oil. Induction Heating Process Placement of Induction Coils: The first step in the induction heating process involves the strategic placement of induction coils. These coils can be installed within the wellbore or around the pipeline carrying the heavy oil. The placement is crucial to ensure that the electromagnetic field generated by the coils effectively interacts with the oil to induce the desired heating effect. Generation of Eddy Currents: When alternating current (AC) flows through the induction coil, it creates a rapidly changing magnetic field around the coil. This alternating magnetic field penetrates the conductive material of the heavy oil. As a result, eddy currents are induced within the oil. These currents circulate within the oil and are responsible for generating heat due to electrical resistance. Heat Production: The heat generated by the eddy currents is a result of the Joule effect, where electrical energy is converted into thermal energy. As the eddy currents flow through the oil, they encounter resistance, which produces heat. This localized heating raises the temperature of the oil, effectively reducing its viscosity. Molecular Dynamics and Thermal Effects Increased Molecular Kinetic Energy: The heat produced by the induction process raises the kinetic energy of the oil molecules. As the temperature increases, the molecules gain more energy and move more freely. This increased molecular motion reduces the internal friction within the oil, making it less viscous. Weakening of Intermolecular Forces: Heavy oil contains large hydrocarbon molecules with strong intermolecular forces, such as van der Waals forces and hydrogen bonding, which contribute to its high viscosity. As the temperature rises, these intermolecular forces weaken, allowing the molecules to move past each other more easily. This reduction in intermolecular forces is a key factor in lowering the viscosity of the oil. Enhanced Fluidity: The combination of increased molecular kinetic energy and weakened intermolecular forces results in enhanced fluidity of the heavy oil. The oil becomes more mobile and easier to pump and transport through pipelines. This improved flow characteristic is essential for efficient extraction and transportation. Changes in Rheological Properties Viscosity Reduction: One of the most significant changes in the rheological properties of heavy oil due to induction heating is the reduction in viscosity. As the temperature of the oil increases, its viscosity decreases significantly. This change can be quantitatively measured using rheometers or viscometers, and the relationship between temperature and viscosity can be plotted to understand the effectiveness of the induction heating process.Improved Flow: The reduction in viscosity translates to improved flow characteristics of the heavy oil. Enhanced fluidity means that the oil can be more easily mobilized within the reservoir, leading to better extraction rates. In pipelines, the reduced viscosity minimizes frictional losses, allowing for smoother and more efficient transportation of the oil. By understanding the mechanism of viscosity reduction through induction heating, it becomes evident how this technology can revolutionize the extraction and transportation of heavy oil. The direct and localized heating provided by induction heating offers a highly efficient and controlled method to address the challenges posed by high-viscosity heavy oil, making it a valuable tool in the oil industry's efforts to optimize production and reduce operational costs.
-
Experimental Studies and Results
Results and Analysis:
- Temperature-Velocity Correlation: A clear correlation was observed between the increase in temperature and the decrease in viscosity. - Optimal Heating Parameters: Specific frequencies and power levels were identified as optimal for reducing viscosity without causing thermal degradation of the oil. - Case Studies: Field applications in locations such as Canada’s oil sands demonstrated practical effectiveness, with significant improvements in extraction rates and cost reductions.-
Advantages of Induction Heating for Heavy Oil
-
Applications in the Oil Industry
Induction heating offers several advantages in the oil industry, particularly in enhancing oil recovery processes, achieving practical successes in field applications, and integrating with existing extraction infrastructure. This section delves into how induction heating is being applied in various contexts to optimize oil extraction and transportation. Enhanced Oil Recovery (EOR) Techniques Enhanced Oil Recovery (EOR) methods are designed to increase the amount of crude oil that can be extracted from an oil field. Induction heating has shown significant promise in improving the efficiency and effectiveness of various EOR techniques. Steam-Assisted Gravity Drainage (SAGD): Steam-Assisted Gravity Drainage (SAGD) is a widely used EOR technique, particularly in the extraction of bitumen from oil sands. In SAGD, steam is injected into the reservoir to reduce the viscosity of the bitumen, allowing it to flow more easily to a production well. Induction heating can be used to preheat the reservoir, which enhances the efficiency of the SAGD process. By raising the initial temperature of the bitumen, induction heating reduces the amount of steam required, thereby lowering operational costs and improving overall energy efficiency. Additionally, preheating the reservoir with induction can shorten the startup time for the SAGD process, leading to faster production rates. Cyclic Steam Stimulation (CSS): Cyclic Steam Stimulation (CSS), also known as the "huff and puff" method, involves injecting steam into a well, allowing it to soak, and then producing the heated oil. The cyclic nature of CSS can benefit significantly from the integration of induction heating. By combining CSS with induction heating, the oil's mobility and extraction rates can be further enhanced. The heat generated by induction can be precisely controlled and applied where needed, ensuring uniform heating of the oil and reducing the thermal stress on the reservoir. This approach not only improves the efficiency of CSS but also extends the life of the wells and maximizes oil recovery. Field Applications and Success Stories The practical application of induction heating in the field has yielded impressive results, demonstrating its potential to revolutionize oil extraction processes. Canada’s Oil Sands: Canada’s oil sands are one of the largest reserves of bitumen, and the extraction of this heavy oil poses significant challenges due to its high viscosity. The successful deployment of induction heating in Canada’s oil sands has led to improved recovery rates and reduced costs. In pilot projects, induction heating has been used to preheat bitumen reservoirs, enhancing the effectiveness of traditional EOR techniques like SAGD and CSS. These projects have reported increased production rates, lower steam-to-oil ratios, and reduced greenhouse gas emissions. The success in Canada’s oil sands serves as a testament to the viability of induction heating in large-scale heavy oil extraction. Venezuela’s Orinoco Belt: The Orinoco Belt in Venezuela contains some of the most viscous heavy oil reserves in the world. Induction heating has been employed to enhance the extraction of this highly viscous oil, demonstrating significant benefits. Field applications in the Orinoco Belt have shown that induction heating can effectively reduce the viscosity of the heavy oil, making it more fluid and easier to extract. This has led to improved production rates and a more cost-effective extraction process. The ability to target specific areas of the reservoir with induction heating has also minimized environmental impact and reduced the need for extensive infrastructure modifications. Integration with Existing Extraction Processes One of the key advantages of induction heating is its compatibility with existing extraction processes and infrastructure, making it a versatile and scalable solution for the oil industry. Compatibility: Induction heating can be seamlessly integrated with existing extraction infrastructure, providing a straightforward addition to current operations. The technology can be implemented in both new and existing wells, allowing operators to enhance oil recovery without the need for significant modifications. The adaptability of induction heating systems means they can be tailored to fit various well configurations and reservoir conditions. This compatibility ensures that the benefits of induction heating can be realized with minimal disruption to ongoing operations. Scalability: The technology is scalable, making it suitable for both small and large-scale operations. Induction heating systems can be designed to meet the specific needs of different oil fields, from small pilot projects to extensive commercial operations. The scalability of induction heating allows for incremental implementation, enabling operators to start with smaller installations and expand as needed based on performance and results. This flexibility makes induction heating an attractive option for a wide range of applications, from enhancing production in mature fields to developing new heavy oil reserves. In summary, the applications of induction heating in the oil industry are vast and varied. By improving the efficiency of EOR techniques, achieving practical success in field applications, and seamlessly integrating with existing infrastructure, induction heating is poised to play a crucial role in the future of oil extraction. The technology’s ability to reduce viscosity, enhance fluidity, and optimize production processes offers significant economic and environmental benefits, making it a valuable tool for the industry.
-
Future Prospects and Innovations

-
Conclusion
2024年6月24日星期一
Brazing Copper to Brass Pipe With Induction

Brazing Brass Pipe With Induction

2024年6月23日星期日
Brazing Carbide-Steel Tool with Induction

Wax and Hydrate Prevention in Oil and Gas Pipelines with Induction Heatin

Ensuring Flow Assurance: Induction Heating for Wax and Hydrate Prevention in Oil and Gas Pipelines
Flow assurance is paramount in the oil and gas industry, where the uninterrupted transportation of hydrocarbons through pipelines is essential for operational efficiency and profitability. One of the significant challenges to flow assurance is the formation of wax and hydrates, which can obstruct pipelines and disrupt production. In addressing this challenge, induction heating has emerged as a highly effective and innovative solution.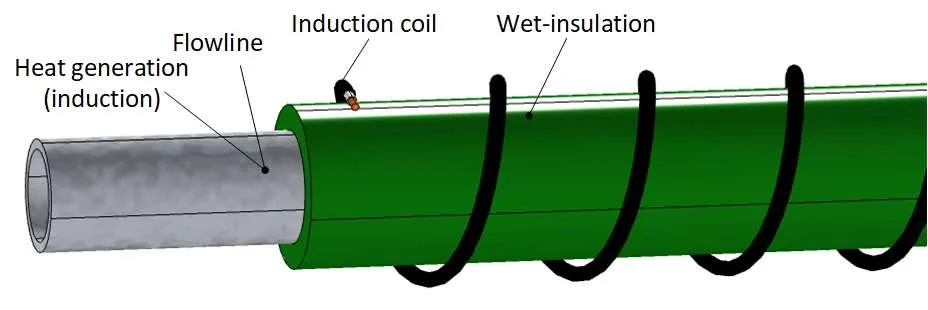
Understanding the Problem: Wax and Hydrate Formation
Wax and hydrates are natural by-products found in crude oil and natural gas. When transported through pipelines, the temperature of the hydrocarbons can drop below certain thresholds, causing these substances to solidify and adhere to pipeline walls. This buildup gradually restricts flow, leading to reduced throughput and potentially costly operational disruptions.The Role of Induction Heating
Induction heating technology utilizes electromagnetic induction to generate heat directly within pipeline walls or at critical points where wax and hydrates are likely to form. Unlike traditional methods that involve heating fluids externally or using chemical additives, induction heating offers several distinct advantages: 1. **Precision Heating:** Induction heating allows for precise control over temperature profiles, ensuring that pipeline temperatures remain above the wax appearance temperature (WAT) and hydrate formation temperature thresholds. This targeted approach minimizes energy consumption and maximizes efficiency. 2. **Continuous Monitoring and Control:** Advanced monitoring systems continuously assess pipeline conditions and adjust induction heating parameters in real-time. This proactive management prevents temperature fluctuations that could promote wax and hydrate deposition. 3. **Environmental Sustainability:** Induction heating is inherently cleaner and more environmentally friendly compared to methods involving combustion or chemical treatments. It reduces emissions and minimizes the use of chemicals, aligning with global sustainability goals.Practical Applications and Benefits
In practice, induction heating systems are strategically deployed along pipelines, particularly in subsea or cold climate regions where temperatures can drop significantly. Key applications include: - **Subsea Pipelines:** Induction heating protects pipelines operating in deepwater environments where temperatures are conducive to wax and hydrate formation. - **Arctic and Cold Climate Operations:** Essential for pipelines in regions experiencing extreme cold, where maintaining temperatures above critical thresholds is challenging yet crucial for uninterrupted flow.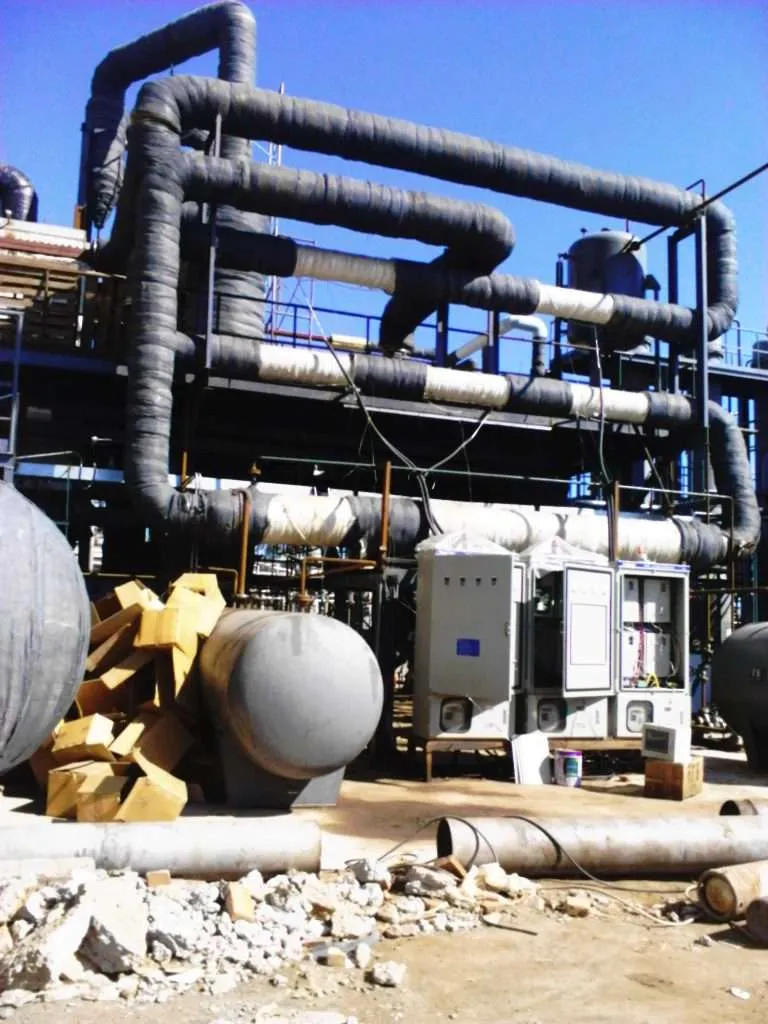
Case Studies and Success Stories
Several oil and gas companies have successfully implemented induction heating for wax and hydrate prevention, achieving notable improvements in operational reliability and cost-effectiveness. For instance, in offshore fields where subsea pipelines are subjected to cold seawater temperatures, induction heating has significantly reduced the frequency of pipeline blockages and maintenance shutdowns. #### Future Directions and Innovations As technology advances, ongoing research and development are focused on enhancing the efficiency and scalability of induction heating systems. Innovations include improved coil designs for better heat distribution, enhanced monitoring capabilities for predictive maintenance, and integration with smart pipeline management systems.Here are the detailed steps involved in using induction heating for wax and hydrate prevention:
### 1. Understanding the Problem Wax and hydrates are natural components found in crude oil and natural gas. When these fluids are transported through pipelines, especially in subsea or cold climate environments, their temperature can drop below critical thresholds. This causes wax to solidify and hydrates to form crystals, leading to the accumulation of deposits along pipeline walls. Over time, these deposits can restrict flow, reduce throughput, and necessitate costly maintenance interventions. ### 2. Designing the Induction Heating System #### a. System Components: - **Induction Coils:** Custom-designed coils are wrapped around the pipeline at strategic locations susceptible to wax and hydrate formation. These coils generate electromagnetic fields. - **Power Supply:** Provides the electrical energy necessary to create the electromagnetic fields in the coils. - **Control and Monitoring System:** Includes sensors and controllers to monitor pipeline temperature, adjust heating parameters, and ensure precise control over the induction heating process. #### b. Coil Configuration: - **Placement:** Coils are positioned along the pipeline where temperature management is critical, such as near wellheads, onshore/offshore risers, or subsea pipeline sections. - **Size and Shape:** Coils are tailored to fit the diameter and length of the pipeline, ensuring uniform heat distribution and efficient energy transfer. ### 3. Operational Steps #### a. Heating Strategy: - **Startup and Warm-Up:** The induction heating system is activated as soon as hydrocarbons start flowing through the pipeline. During startup, the system gradually increases heat to bring the pipeline temperature above the wax appearance temperature (WAT) and hydrate formation temperature. - **Continuous Heating:** Once operational, the system maintains a consistent pipeline temperature by continuously adjusting the power supplied to the coils based on real-time temperature readings from sensors. #### b. Monitoring and Control: - **Temperature Monitoring:** Sensors installed along the pipeline monitor the temperature at multiple points. This data is fed back to the control system, which ensures that the pipeline temperature remains within the optimal range to prevent wax and hydrate deposition. - **Adjustments and Optimization:** The control system dynamically adjusts heating parameters, such as coil power and frequency, to respond to changes in external conditions (e.g., ambient temperature variations) and internal pipeline conditions (e.g., flow rate fluctuations).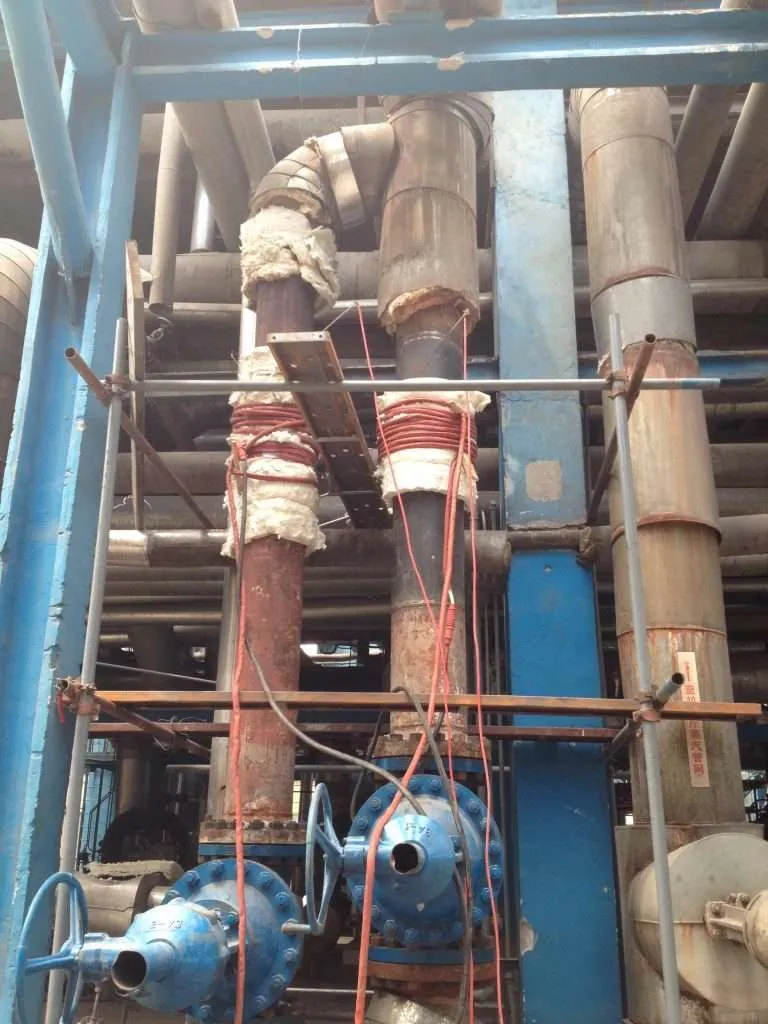
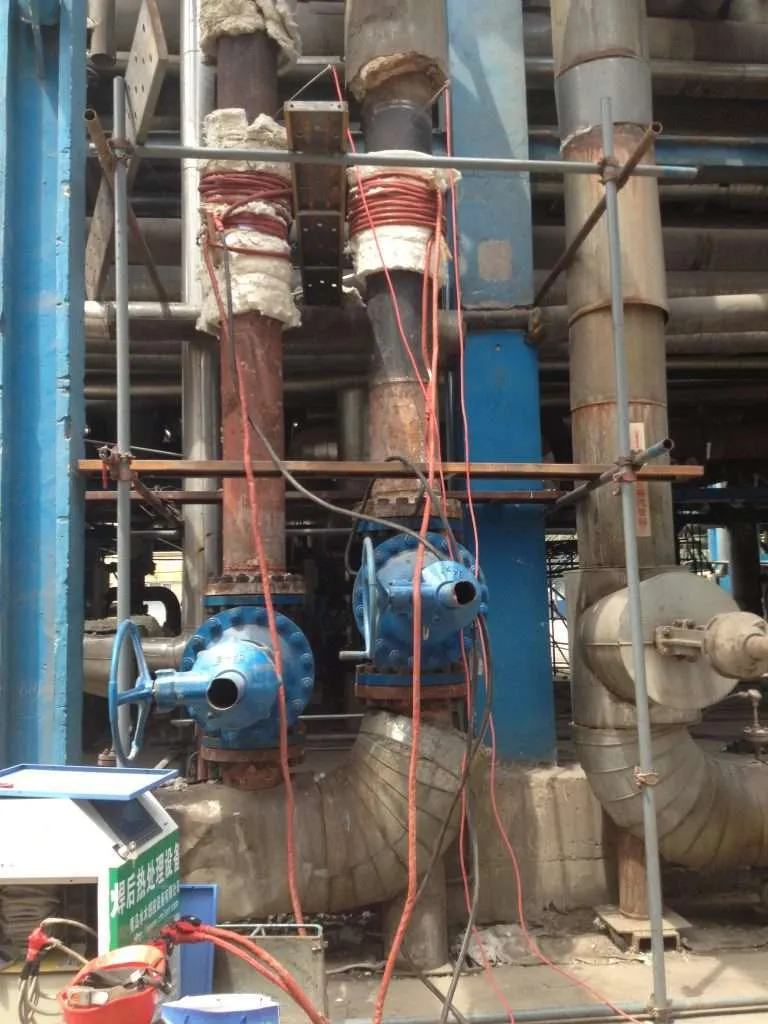
Conclusion
Induction heating for wax and hydrate prevention represents a technological breakthrough in ensuring flow assurance in oil and gas pipelines. By effectively managing pipeline temperatures above critical thresholds, this method mitigates operational risks, reduces maintenance costs, and supports sustainable energy practices. As industry demands for efficiency and reliability grow, investments in advanced induction heating technologies are poised to play a pivotal role in enhancing pipeline integrity and optimizing hydrocarbon transportation worldwide. Induction heating represents a transformative approach to ensuring flow assurance in oil and gas pipelines by effectively preventing wax and hydrate formation. Its precision heating capabilities, coupled with environmental benefits and operational efficiencies, make it a preferred choice for industry leaders seeking reliable and sustainable solutions. As the demand for energy continues to grow, investments in technologies like induction heating are pivotal in ensuring the safe and efficient transportation of hydrocarbons while mitigating environmental impacts. Embracing these innovations not only safeguards pipeline integrity but also reinforces the industry's commitment to responsible resource management and operational excellence. https://dw-inductionheater.com/wax-and-hydrate-prevention-in-oil-and-gas-pipelines-with-induction-heatin.html?feed_id=251109&_unique_id=66789d8020e53Wax and Hydrate Prevention in Oil and Gas Pipelines with Induction Heatin

Ensuring Flow Assurance: Induction Heating for Wax and Hydrate Prevention in Oil and Gas Pipelines
Flow assurance is paramount in the oil and gas industry, where the uninterrupted transportation of hydrocarbons through pipelines is essential for operational efficiency and profitability. One of the significant challenges to flow assurance is the formation of wax and hydrates, which can obstruct pipelines and disrupt production. In addressing this challenge, induction heating has emerged as a highly effective and innovative solution.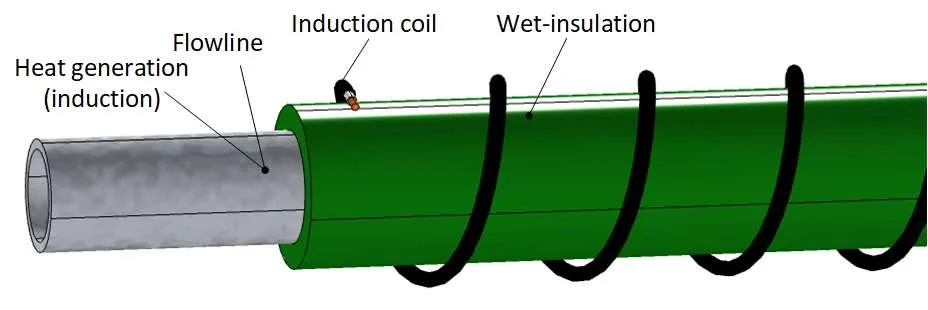
Understanding the Problem: Wax and Hydrate Formation
Wax and hydrates are natural by-products found in crude oil and natural gas. When transported through pipelines, the temperature of the hydrocarbons can drop below certain thresholds, causing these substances to solidify and adhere to pipeline walls. This buildup gradually restricts flow, leading to reduced throughput and potentially costly operational disruptions.The Role of Induction Heating
Induction heating technology utilizes electromagnetic induction to generate heat directly within pipeline walls or at critical points where wax and hydrates are likely to form. Unlike traditional methods that involve heating fluids externally or using chemical additives, induction heating offers several distinct advantages: 1. **Precision Heating:** Induction heating allows for precise control over temperature profiles, ensuring that pipeline temperatures remain above the wax appearance temperature (WAT) and hydrate formation temperature thresholds. This targeted approach minimizes energy consumption and maximizes efficiency. 2. **Continuous Monitoring and Control:** Advanced monitoring systems continuously assess pipeline conditions and adjust induction heating parameters in real-time. This proactive management prevents temperature fluctuations that could promote wax and hydrate deposition. 3. **Environmental Sustainability:** Induction heating is inherently cleaner and more environmentally friendly compared to methods involving combustion or chemical treatments. It reduces emissions and minimizes the use of chemicals, aligning with global sustainability goals.Practical Applications and Benefits
In practice, induction heating systems are strategically deployed along pipelines, particularly in subsea or cold climate regions where temperatures can drop significantly. Key applications include: - **Subsea Pipelines:** Induction heating protects pipelines operating in deepwater environments where temperatures are conducive to wax and hydrate formation. - **Arctic and Cold Climate Operations:** Essential for pipelines in regions experiencing extreme cold, where maintaining temperatures above critical thresholds is challenging yet crucial for uninterrupted flow.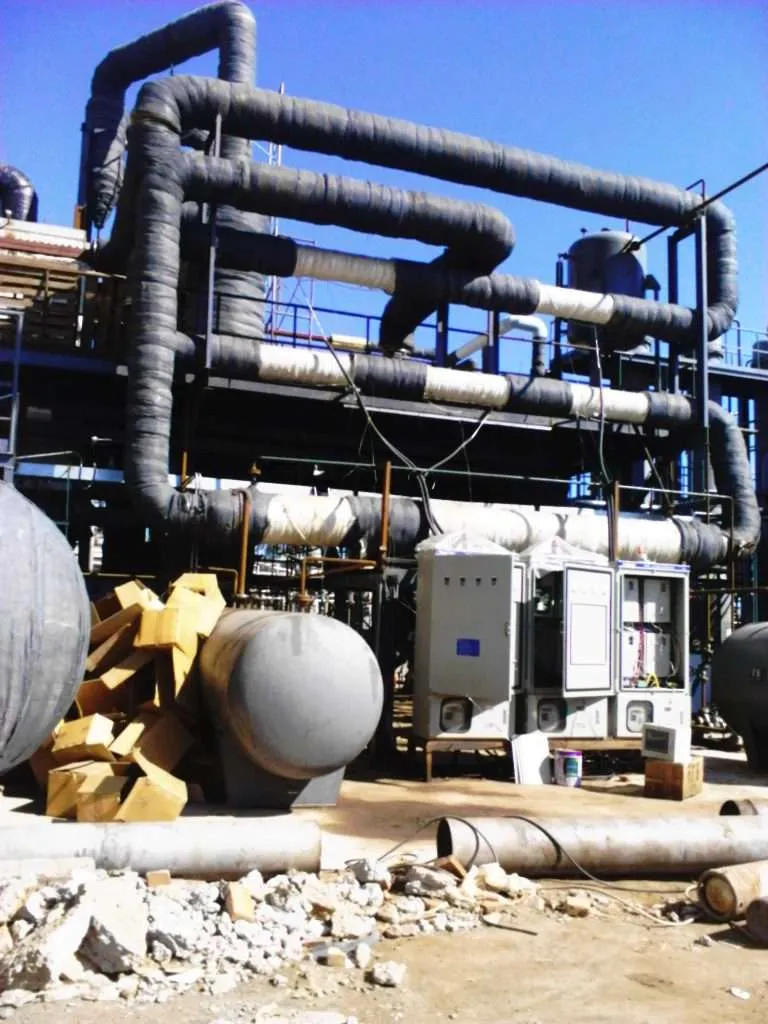
Case Studies and Success Stories
Several oil and gas companies have successfully implemented induction heating for wax and hydrate prevention, achieving notable improvements in operational reliability and cost-effectiveness. For instance, in offshore fields where subsea pipelines are subjected to cold seawater temperatures, induction heating has significantly reduced the frequency of pipeline blockages and maintenance shutdowns. #### Future Directions and Innovations As technology advances, ongoing research and development are focused on enhancing the efficiency and scalability of induction heating systems. Innovations include improved coil designs for better heat distribution, enhanced monitoring capabilities for predictive maintenance, and integration with smart pipeline management systems.Here are the detailed steps involved in using induction heating for wax and hydrate prevention:
### 1. Understanding the Problem Wax and hydrates are natural components found in crude oil and natural gas. When these fluids are transported through pipelines, especially in subsea or cold climate environments, their temperature can drop below critical thresholds. This causes wax to solidify and hydrates to form crystals, leading to the accumulation of deposits along pipeline walls. Over time, these deposits can restrict flow, reduce throughput, and necessitate costly maintenance interventions. ### 2. Designing the Induction Heating System #### a. System Components: - **Induction Coils:** Custom-designed coils are wrapped around the pipeline at strategic locations susceptible to wax and hydrate formation. These coils generate electromagnetic fields. - **Power Supply:** Provides the electrical energy necessary to create the electromagnetic fields in the coils. - **Control and Monitoring System:** Includes sensors and controllers to monitor pipeline temperature, adjust heating parameters, and ensure precise control over the induction heating process. #### b. Coil Configuration: - **Placement:** Coils are positioned along the pipeline where temperature management is critical, such as near wellheads, onshore/offshore risers, or subsea pipeline sections. - **Size and Shape:** Coils are tailored to fit the diameter and length of the pipeline, ensuring uniform heat distribution and efficient energy transfer. ### 3. Operational Steps #### a. Heating Strategy: - **Startup and Warm-Up:** The induction heating system is activated as soon as hydrocarbons start flowing through the pipeline. During startup, the system gradually increases heat to bring the pipeline temperature above the wax appearance temperature (WAT) and hydrate formation temperature. - **Continuous Heating:** Once operational, the system maintains a consistent pipeline temperature by continuously adjusting the power supplied to the coils based on real-time temperature readings from sensors. #### b. Monitoring and Control: - **Temperature Monitoring:** Sensors installed along the pipeline monitor the temperature at multiple points. This data is fed back to the control system, which ensures that the pipeline temperature remains within the optimal range to prevent wax and hydrate deposition. - **Adjustments and Optimization:** The control system dynamically adjusts heating parameters, such as coil power and frequency, to respond to changes in external conditions (e.g., ambient temperature variations) and internal pipeline conditions (e.g., flow rate fluctuations).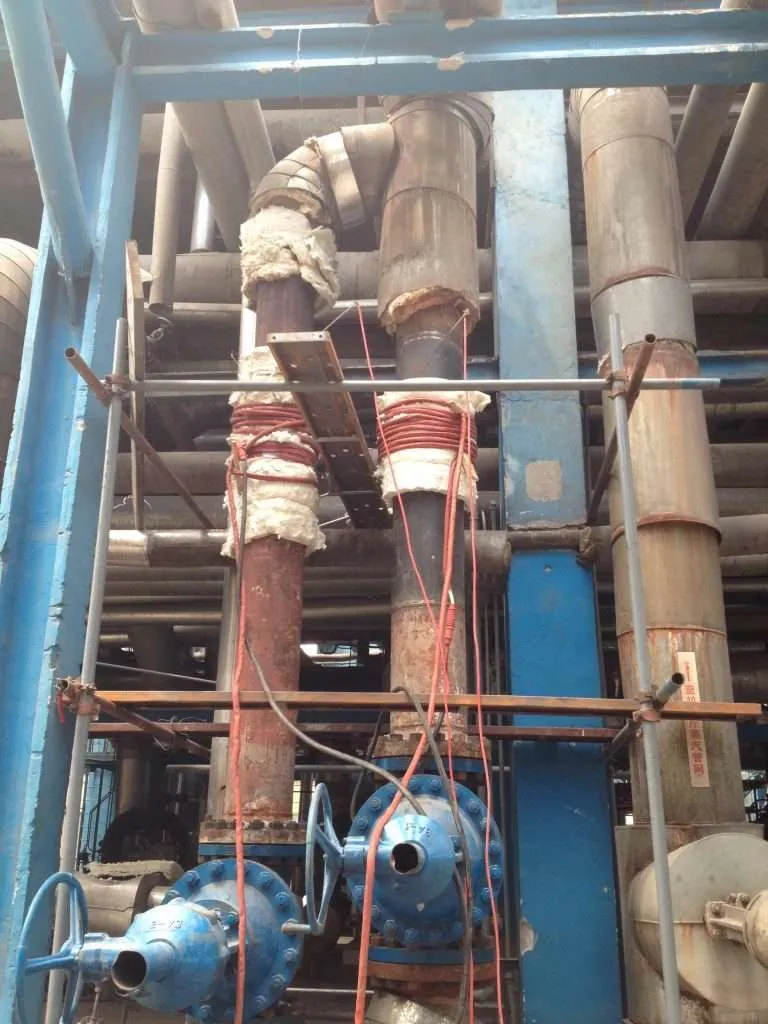
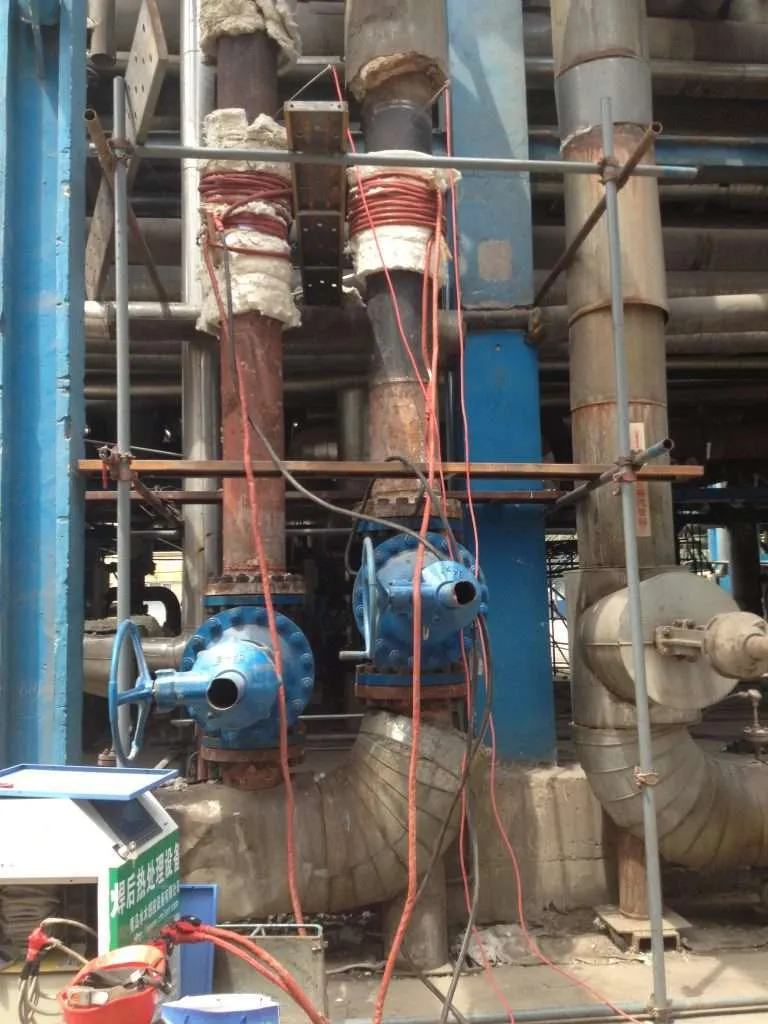
Conclusion
Induction heating for wax and hydrate prevention represents a technological breakthrough in ensuring flow assurance in oil and gas pipelines. By effectively managing pipeline temperatures above critical thresholds, this method mitigates operational risks, reduces maintenance costs, and supports sustainable energy practices. As industry demands for efficiency and reliability grow, investments in advanced induction heating technologies are poised to play a pivotal role in enhancing pipeline integrity and optimizing hydrocarbon transportation worldwide. Induction heating represents a transformative approach to ensuring flow assurance in oil and gas pipelines by effectively preventing wax and hydrate formation. Its precision heating capabilities, coupled with environmental benefits and operational efficiencies, make it a preferred choice for industry leaders seeking reliable and sustainable solutions. As the demand for energy continues to grow, investments in technologies like induction heating are pivotal in ensuring the safe and efficient transportation of hydrocarbons while mitigating environmental impacts. Embracing these innovations not only safeguards pipeline integrity but also reinforces the industry's commitment to responsible resource management and operational excellence. https://dw-inductionheater.com/wax-and-hydrate-prevention-in-oil-and-gas-pipelines-with-induction-heatin.html?feed_id=251061&_unique_id=667819f17b6afBrazing Steel To Steel Pipe With Induction

2024年6月22日星期六
Induction Brazing Carbide to Steel

Brazing Copper Bars with Induction

2024年6月21日星期五
Induction Brazing Stainless Steel

Induction Brazing & Soldering Principle

2024年6月20日星期四
Brazing Carbide To Steel Shank

2024年6月19日星期三
Brazing Automotive Parts With Induction

Brazing Automotive Parts With Induction

Induction Brazing Aluminum Automotive
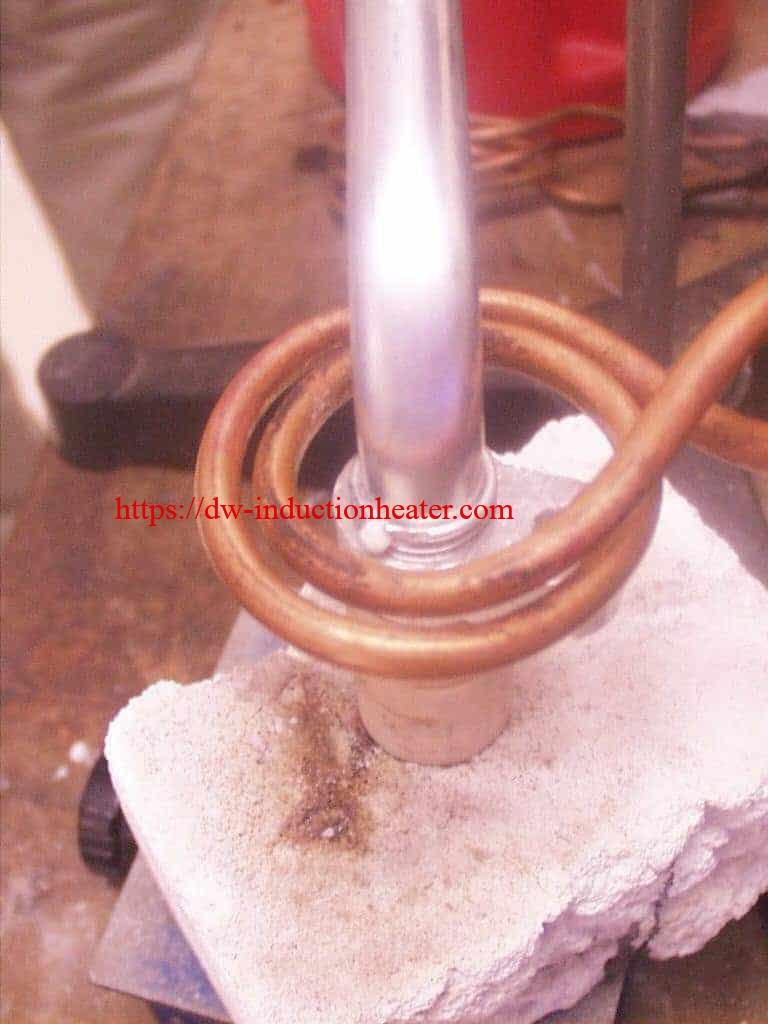
rail hardening system and scanner for induction quenching solutions

The Evolution and Impact of Rail Hardening Systems and Scanners on Modern Railways
In the industrial landscape, the evolution of metallurgical processes and the adoption of advanced machining technologies have been pivotal in enhancing the operational efficacy and longevity of crucial components. Among the myriad of innovations, the development and application of CNC (Computer Numerical Control) induction rail hardening systems stand out as a cornerstone in the advancement of railway infrastructure. This essay delves into the intricacies of this technology, exploring its principles, components, benefits, challenges, and the ongoing research aimed at refining and optimizing the process.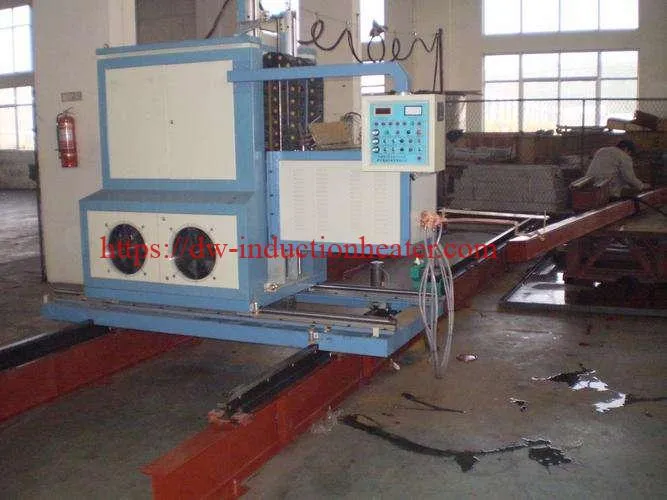
The Principle of Induction Rail Hardening
At the heart of CNC induction rail hardening technology lies the principle of electromagnetic induction, a process that has revolutionized the way steel rails are hardened. This method involves the heating of steel rails to the austenitizing temperature, followed by a rapid cooling or quenching phase. The transformation induced by this thermal cycling alters the microstructure of the steel, significantly enhancing its hardness and, consequently, its durability and wear resistance. The precise control afforded by CNC technology makes it possible to achieve consistent and optimal hardening results, tailored to the specific requirements of different rail profiles and compositions.Key Components of CNC Induction Rail Hardening Machines
The efficacy of CNC induction rail hardening scanners can be attributed to their sophisticated components, which include induction coils for precise heating, quenching systems for controlled cooling, and advanced control systems. These control systems are the linchpins of the machinery, enabling real-time monitoring and adjustment of the hardening process. This level of precision ensures that the rails undergo uniform hardening, thereby maintaining their dimensional accuracy and structural integrity.Benefits of CNC Induction Rail Hardening
The transition to CNC induction rail hardening offers a plethora of benefits over traditional furnace heating methods. Firstly, the process is markedly more energy efficient, reducing the carbon footprint associated with rail manufacturing and maintenance. Furthermore, the enhanced durability and wear resistance of the rails translate to lower maintenance costs and longer service lives, contributing to the cost-effectiveness and sustainability of railway infrastructure. Additionally, CNC induction rail hardening machines are inherently more flexible, capable of accommodating a wide range of rail profiles and compositions with minimal adjustments.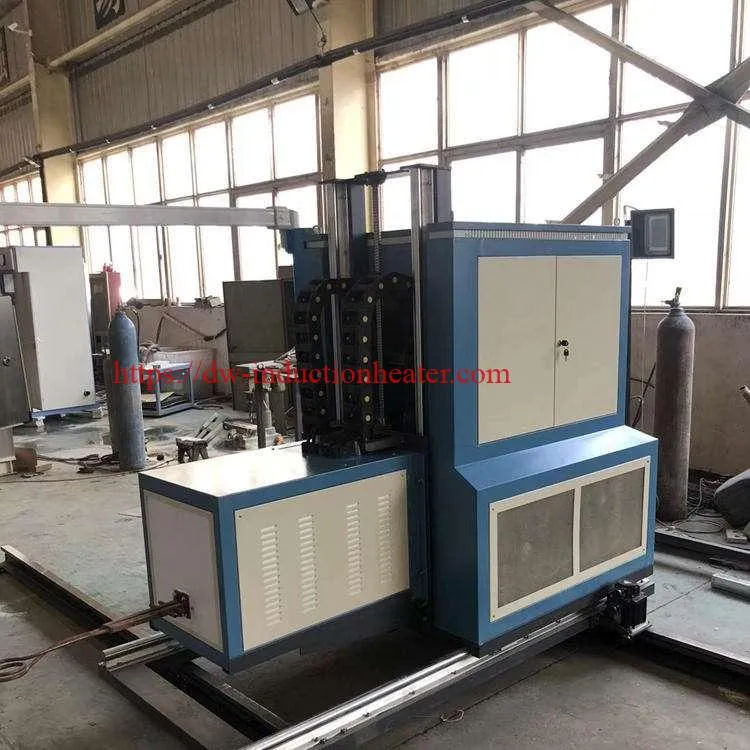
Challenges and Solutions
Despite its advantages, the induction rail hardening process is not without its challenges. One of the primary concerns is ensuring the compatibility of the material, as only certain steel compositions are amenable to this hardening technique. Moreover, the complexity of the machinery necessitates a high degree of expertise in operation and maintenance. However, ongoing research and development efforts are directed towards overcoming these hurdles. Innovations in machine design and control algorithms are expanding the scope of compatible materials and simplifying the operational demands of the technology.The Future Direction of CNC Induction Rail Hardening Technology
The future of CNC induction rail hardening is replete with possibilities. Research is ongoing to further enhance the energy efficiency and environmental compatibility of the process. Efforts are also underway to broaden the range of materials that can be effectively hardened, encompassing a wider variety of steel grades and compositions. Moreover, advancements in CNC technology and control systems promise to render the process even more precise and adaptable, thereby extending the benefits of induction rail hardening to a broader array of railway applications.Product Details:
Work-piece length ≤10000mm Working table level travelling distance ≤11000mm Transformer travelling distacne ≤800mm continuously adjustable Quenching travelling speed 2 ~20mm/s continuously adjustable Main Usage Used for all kinds of guide rail type work-piece induction quenching & induction tempering Feature Adopting two -axial association digital control system to control transformer and working table respectively, to make sure the transform positioning accurately. Adopting advance digital tracking tech, it can program and save different kinds of treatment procedure to meet different requirements.
The applications of CNC Induction Rail Hardening Machines include:
- Enhancing the durability and wear resistance of railway tracks, leading to reduced maintenance costs and improved safety.
- Improving energy efficiency and promoting environmental sustainability in rail manufacturing and maintenance.
- Accommodating a diverse range of rail profiles and steel compositions, making the technology versatile across different railway applications.
- Ensuring dimensional accuracy and structural integrity of rails, thus enhancing the safety and reliability of railway infrastructure.
- Supporting ongoing research and development efforts to expand material compatibility, enhance energy efficiency, and reduce environmental impacts, contributing to the advancement of railway infrastructure.
Conclusion
CNC induction rail hardening systems and solutions represent a significant leap forward in railway infrastructure technology. By merging the principles of electromagnetic induction with the precision of CNC control, this technology offers a means to significantly enhance the durability, efficiency, and environmental sustainability of steel rails. While challenges remain, the ongoing research and development efforts are paving the way for a future where railways are more durable, cost-effective, and compatible with the imperatives of environmental stewardship. In this evolving industrial narrative, CNC induction rail hardening stands as a testament to the transformative power of innovation, embodying the relentless pursuit of excellence in the realm of material science and machining technology.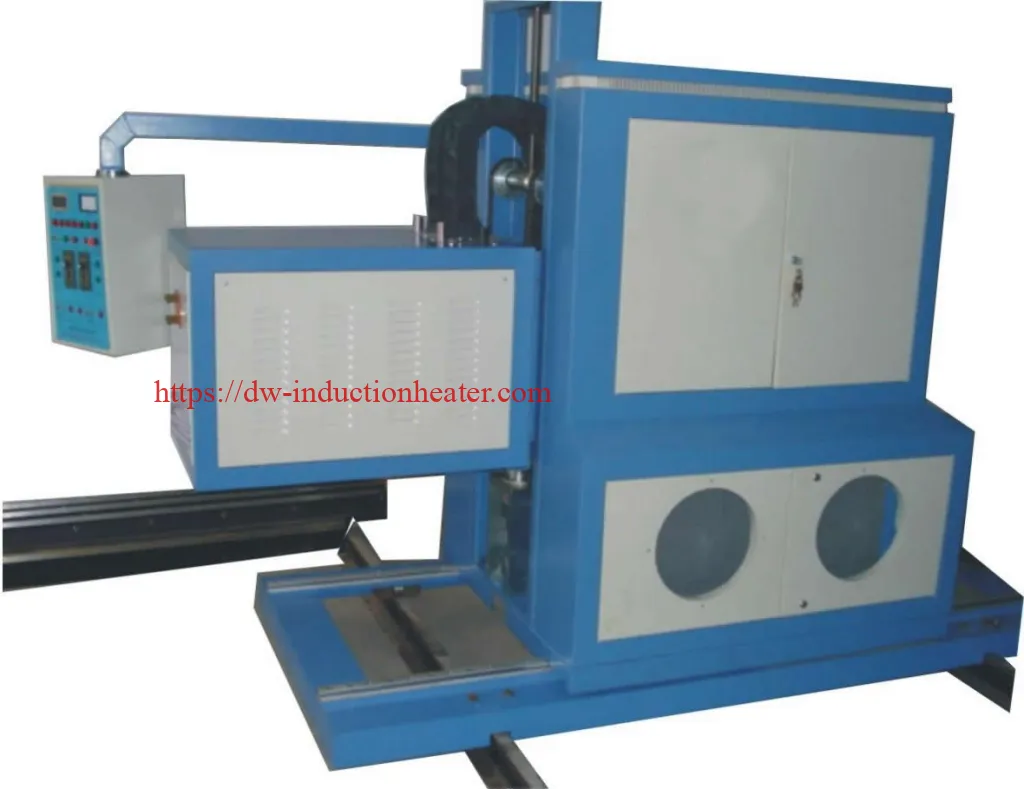
订阅:
博文 (Atom)
关注者
博客归档
-
▼
2024
(838)
-
▼
六月
(64)
- What Is Induction Melting?
- what is induction forging?
- Induction Brazing Aluminum Pipes
- Brazing Aluminum to Copper Tubes with Induction
- Brazing Aluminum Pipes Assembly With Induction
- Induction Aluminum Brazing Process
- What Is Induction Heating Coil&Inductor?
- Brazing Carbide To Steel With Induction
- Brazing Brass to Aluminum with Induction
- Brazing Carbide Tool Tips With Induction
- Reducing Heavy Oil Viscosity and Enhancing Fluidit...
- Brazing Brass To Copper With Induction
- Reducing Heavy Oil Viscosity and Enhancing Fluidit...
- Brazing Copper to Brass Pipe With Induction
- Brazing Brass Pipe With Induction
- Brazing Carbide-Steel Tool with Induction
- Wax and Hydrate Prevention in Oil and Gas Pipeline...
- Wax and Hydrate Prevention in Oil and Gas Pipeline...
- Brazing Steel To Steel Pipe With Induction
- Induction Brazing Carbide to Steel
- Brazing Copper Bars with Induction
- Induction Brazing Stainless Steel
- Induction Brazing & Soldering Principle
- Brazing Carbide To Steel Shank
- Brazing Automotive Parts With Induction
- Brazing Automotive Parts With Induction
- Induction Brazing Aluminum Automotive
- rail hardening system and scanner for induction qu...
- Brazing Golf Ball With Induction
- Brazing Joining Copper Connectors With Induction
- Induction Brazing Stainless Steel
- Brazing Stainless Steel To Copper With Induction
- Brazing Stainless Steel To Copper With Induction
- Brazing Silver To Copper With Induction
- Brazing Wire to Copper Bar With Induction
- Brazing Carbide Tips To Steel With Induction
- Hydrogen Atmosphere Brazing Tube To Copper With In...
- Induction Melting Videos
- Induction Brazing Steel To Carbide Plate
- Induction Brazing Brass Faucet
- Induction Brazing Copper Assembly
- Induction Brazing Steel Wire
- Induction Brazing Steel Tips
- Technology of Induction Forming Steel Plate
- Induction Soldering Process Video
- Induction Annealing Steel Wire
- Induction Annealing Stainless Steel Tubes
- Induction Annealing Aluminum
- Induction annealing copper wires
- Induction Annealing Aluminum PIpe
- Induction Heating Valve Head
- Induction Hardening Inner
- Induction Tempering Spring
- induction sealing glass
- induction heating steel cable for cutting
- induction heating steel casting
- Induction Heating Automotive Motor
- Induction Heating Sintering Copper Powder
- Induction Preheating Welding Steel Pipe
- Induction Heating Solutions For Cancer Research
- Induction Heating Bolts
- How induction heating separates and recovers mill ...
- Induction Heating Steel Pipe To Remove plastic coa...
- How induction heating separates and recovers mill ...
-
▼
六月
(64)
我的简介

- HLQ induction heating machine
- HLQ induction heating machine manufacturer provides the service of induction brazing,melting,hot forming,hardening surface,annealing,shrink fitting,PWHT,etc.