Unveiling the Power of Induction Heating: A Revolution in Mill Liners Recycling
Introduction: The Quest for Sustainable Solutions
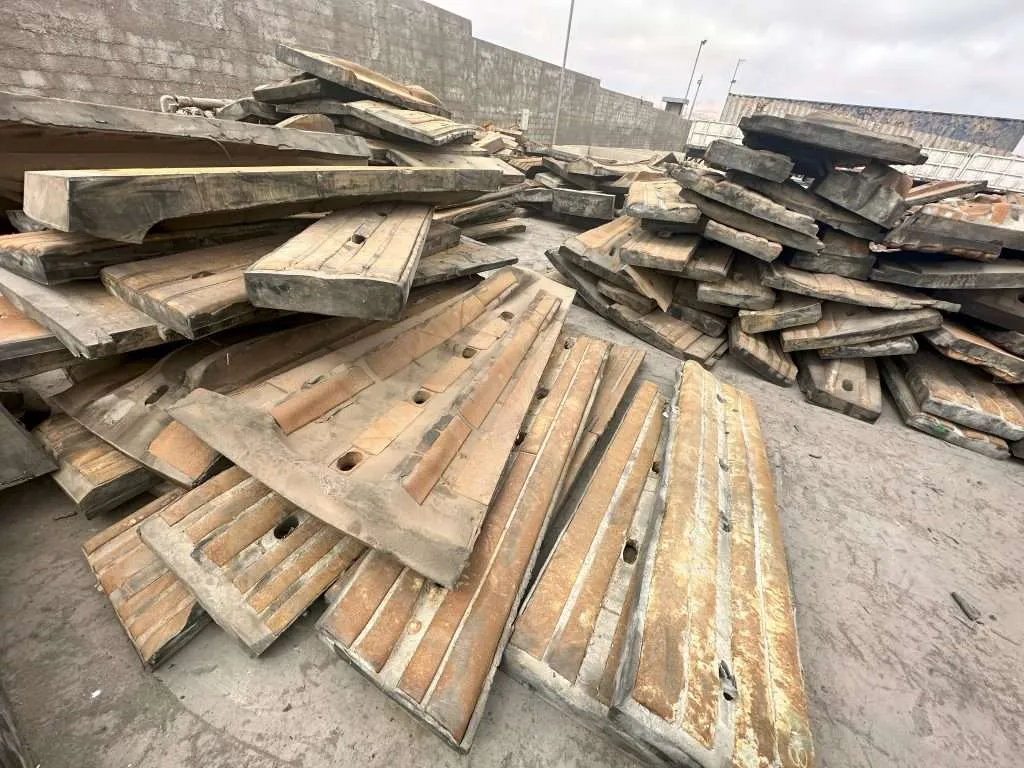
In the ever-evolving landscape of industrial recycling, the mining sector faces relentless pressure to adopt greener methods and reduce waste. Among the myriad of challenges is the efficient recycling of mill liners, a critical component comprised of steel plates and rubber. Traditionally, separating these materials for recycling has been a cumbersome and inefficient process. Enter induction heating—an innovative, eco-friendly technology revolutionizing how we separate and recover materials from mill liners.
Understanding Mill Liners: The Foundation
Before diving into the mechanics of induction heating, it's essential to grasp what mill linings are and their role in mining operations. Mill linings, designed to protect grinding mills from wear and tear, are typically made from a combination of steel plates for durability and rubber for impact resistance. As these liners wear out, the quest for effectively recycling them becomes paramount, posing both an environmental obligation and an economic opportunity.
Induction Heating: The Game-Changer
Induction heating operates on the principle of electromagnetic induction to generate heat directly in the steel plates of the mill linings without heating the rubber. This section outlines the process in detail, explaining how an alternating current passing through a coil generates an electromagnetic field that induces eddy currents and, consequently, heat in the conductive steel, leaving non-conductive materials unaffected.
Advantages of Induction Heating
- Efficiency and Speed: This method significantly quickens the separation process, allowing for rapid recovery and recycling.
- Environmental Impact: By eliminating the need for harsh chemicals and reducing landfill waste, induction heating offers a sustainable alternative.
- Cost-Effectiveness: The energy-efficient nature of induction heating reduces operational costs, presenting a win-win scenario for businesses.
- Enhanced Safety: The contactless nature of induction heating minimizes the risk of accidents, promoting a safer workplace environment.

The Process Detailed: From Theory to Application
The recycling of mill linings into steel plates and rubber through induction heating involves a series of intricately connected steps, underlying both theoretical principles and practical applications. This section outlines these steps, providing insights into the machinery, techniques, and nuances of the recycling process.
Initial Preparation of Mill Liners
Before the start of the induction heating process, mill linings undergo an initial preparation phase. This stage involves cleaning the linings to remove any debris, such as residual ore or dirt, which could potentially interfere with the heating process. Additionally, the linings are inspected, and any non-metallic attachments, which might not be affected by induction heating, are manually removed.
Induction Heating Process
The crux of the separation process lies in the application of induction heating. Specialized induction heating equipment is used, comprising an induction coil through which a high-frequency alternating current is passed. This coil is positioned close to, but not touching, the steel part of the mill lining. As the electrical current flows through the coil, it creates a rapidly changing magnetic field that penetrates the steel.
The magnetic field induces eddy currents within the steel plates, and because of the electrical resistance of the steel, these currents generate heat, increasing the temperature of the steel rapidly. Meanwhile, the rubber remains cooler due to its non-conductive nature, leading to a differential in temperature between the steel and rubber components.
Separation Techniques
Upon reaching a specific temperature, the adhesive that binds the steel and rubber weakens, allowing for separation. The process may involve mechanical intervention to peel away the now-loosened rubber from the steel. In some advanced setups, automated systems are in place to handle this part of the process, enhancing efficiency and reducing manual labor requirements.
Recovery and Recycling Pathways
Following separation, the steel plates and rubber are directed towards their respective recycling pathways. The steel, now free of rubber, is typically melted down and repurposed for various applications. The recovered rubber undergoes a grinding process, transforming it into crumb rubber, which finds usage in creating new rubber products, asphalt modifiers, or in sports and playground surfaces.
Innovations and Technological Advances
The field of induction heating has witnessed significant innovations that have refined the separation and recovery processes, leading to increased efficiency, reduced energy consumption, and broader applicability.
Improvements in Coil Design
One of the key advancements has been in the design of
induction coils. Modern coils are designed for higher efficiency, capable of focusing the magnetic field more precisely on the steel parts. This focus minimizes energy wastage and ensures that heat is generated more uniformly across the steel surface, improving the overall effectiveness of the separation process.
Energy Efficiency
Energy efficiency in induction heating systems has seen remarkable improvements through the incorporation of advanced power supplies and control systems. These systems optimize the energy input based on the load, ensuring that only the required amount of energy is used at any given time. Additionally, some systems are now capable of recovering and reusing energy from the process, further enhancing efficiency.
Automation
Automation has been a significant focus area, with sophisticated control systems now capable of monitoring and adjusting the heating process in real time. These systems use sensors to detect temperatures and adjust the power output accordingly, ensuring optimal conditions for separation are maintained throughout the operation. Automation not only boosts efficiency but also reduces dependency on skilled operators, making the technology more accessible.
Ongoing Research
Ongoing research in the field aims to further refine the induction heating process. Studies are exploring the applicability of this technology to different types of mill liners, including those with varying compositions or designs. Efforts are also directed toward enhancing the scalability of the process, making it feasible for operations of different sizes and capacities.
Researchers are investigating the ecological impact of the process, seeking ways to reduce any potential environmental footprint. The goal is to make induction heating an even more sustainable option for recycling mill linings.
By leveraging these technological advancements, the process of separating and recovering mill linings into steel plates and rubber not only becomes more efficient and sustainable but also unlocks new possibilities for recycling and material recovery within the mining industry and beyond. These innovations mark a significant stride toward a more sustainable future, one where waste is minimized, and resources are maximally utilized.
Case Studies: Success Stories Around the Globe
Illustrating the real-world impact of induction heating, this segment presents case studies from mining operations around the world. These success stories not only highlight the environmental and economic benefits of adopting induction heating for mill lining recycling but also shed light on the challenges faced and overcome by various companies during implementation.
Challenges and Considerations
Despite its advantages, the adoption of
induction heating for mill lining recycling is not without challenges. This section discusses potential obstacles such as the high initial investment in technology, the requirement for skilled operators, and the intricacies of integrating this method into existing recycling operations. Additionally, it addresses considerations for optimizing the process for different types of mill linings and operational scales.
Future Directions: The Path Forward
Looking to the horizon, this part explores the future potential of induction heating in mill lining recycling and beyond. It examines on-going innovations, the expanding applications of induction heating in recycling other materials, and the role of policy and industry standards in fostering sustainable practices. The discussion emphasizes a holistic outlook on how continued advancements could further enhance the efficiency, accessibility, and environmental benefits of
induction heating.
Conclusion: A Call to Action
The final section serves as a rallying cry for the mining industry and recycling sectors to embrace induction heating as a fundamental component of their sustainability strategies. It underscores the urgency of adopting eco-friendly technologies to mitigate environmental impact and advocates for collaborative efforts among stakeholders to drive widespread adoption and continuous improvement of such innovative solutions.
https://dw-inductionheater.com/how-induction-heating-separates-and-recovers-mill-liners-into-steel-plates-and-rubber.html?feed_id=248145&_unique_id=665b0b729386c