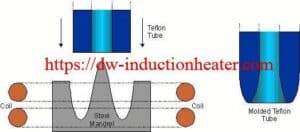
2022年8月31日星期三
Induction Heating Molding Catheter Tip
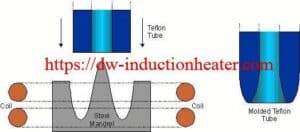
induction heating plastic extrusion
Brief Introduction of induction heating plastic extrusion:
Induction heating plastic extrusion is a one type of energy-saving heater. It has many advantages including significant energy-saving, fast heating up, high energy efficiency, low or zero maintenance etc. It can also lower environment temperature by generating much less heat. While installing the induction heater system, there will not involve any major changes to the electrical control system.
Where can induction heating plastic extrusion?
It is mainly applied to injection, extrusion; blow filming, wire drawing, granulating and recycling machines, etc. The product application includes film, sheet, profile, raw material etc. It can be used for heating the barrel, flange, die head, screw and other parts of the machines. It is excellent in energy-saving and cooling down work environment.
Induction heating is the process of heating an electrically conducting object (usually a metal) by electromagnetic induction, where eddy currents are generated within the metal and resistance leads to Joule heating of the metal. The induction coil itself does not get heated. The heat generating object is the heated object itself.
Why and how induction heating plastic extrusion can save energy?
Presently,most of the plastic machines are using the conventional resistance heating method, where the resistance wire is heated up and then transfer the heat to the barrel via heater cover.So only the heat close to the barrel surface can be transferred to the barrel and the heat close to outside heater cover is lost to the air which causes a rise in environment temperature. Induction heater is technology where high frequency magnetic fields which cause he be heated up bu electro-magnetic field(EMF)that are brushing against each other.When the barrel is heated up and heat is minimum,there is very high heat efficiency and minimum heat loss to the environment where energy saving could reach30-80%.Due to the fact that the induction coil is not producing any high heat and also there is no resistance wire that gets oxidized and causes the heater to burn out, the induction heater has a longer service life and also less maintenance.
What are the advantages of induction heating plastic extrusion?
- Energy efficiency 30%-85% Currently, plastic processing machinery mainly uses resistance heating elements which can produce a large amount of heat radiated to the surroundings. Induction heating is an ideal alternative to solve this issue. The surface temperature of induction heating coil ranges between 50ºC and 90ºC, the heat losses are significantly minimized, providing energy savings of 30%-85%. The energy saving effect is therefore more obvious when the induction heating system is used in high power heating equipment.
- Safety Using induction heating system enables the surface of the machine to be safe for touching, and that means it can avoid burn injuries which often occur in plastic machines that use resistance heating elements, providing a safe workplace for operators.
- Fast heating, high heating efficiency Compared to resistance heating whose energy conversion efficiency is approximately at 60%, the induction heating is over 98% efficient at converting electricity to heat.
- Lower workplace temperature, higher operation comfort After using induction heating system, the temperature of entire production workshop is lowered by more than 5 degrees.
- Long service life In contrast to resistance heating elements that have to long-lasting work at high temperature, the induction heating works at near ambient temperature, therefore efficiently prolonging the service life.
- Accurate temperature control, high product qualification rate The induction heating provides low or no thermal inertia, so that it will not cause the temperature overshoot. And the temperature can remain at set value of 0.5 degree difference.
What is the superiority of induction heating for plastic extrusion compared with traditional heaters?
Induction heater | Traditional heaters | |
Heating method | Induction heating is the process of heating an electrically conducting object (usually a metal) by electromagnetic induction, where eddy currents are generated within the metal and resistance leads to Joule heating of the metal. The induction coil itself does not get heated. The heat generating object is the heated object itself | Resistance wires get heated directly and heat is transferred by contact. |
heating up time | Quicker heating-up, higher efficiency | slower heating-up, lower efficiency |
Energy saving rate |
Save 30-80% energy rate,reduce working temperature |
Cannot save energy |
Installation | Easy to install | Easy to install |
Operation | Easy to operate | Easy to operate |
Maintenance |
Control box is easy to replace without turning off your machine |
Easy to replace but have to turning off your machine |
Temperature Control | Small thermal inertia and precise temperature control because the heater doesn’t get heated byitself. | Big thermal inertia, low accuracy in temperature control |
Product Quality | Higher product quality because of precise temperature control | Lower product quality |
Safety |
Outer sheath is safe to touch, lower surface temperature, no electric leakage. |
Temperature on outer sheath is much higher, easy to get burned. Electric leakage under wrong operation. |
Service life of heater | 2-4years | 1-2 years |
Service life of Barrel and Screw |
Longer usage life for barrel, screw etc. due to lower frequency of changing heaters. |
Shorter usage life for barrel, screw etc. |
Environment | Lower environment temperature; No noise | Much higher environment temperature and much noise |
Induction Heating Power Calculation
In the case of knowing the heating power of existing heating system, selecting an appropriate power according to load rate
- Load rate ≤ 60%, applicable power is 80% of the original power;
- Load rate between 60%-80%, select the original power;
- Load rate > 80%, applicable power is 120% of the original power;
When the heating power of existing heating system is unknown
- For injection molding machine, blown film machine and extrusion machine, the power should be calculated as 3W per cm2 according to the actual surface area of the cylinder (barrel);
- For dry cut pelletizing machine, the power should be calculated as 4W per cm2 according to the actual surface area of the cylinder (barrel);
- For wet cut pelletizing machine, the power should be calculated as 8W per cm2 according to the actual surface area of the cylinder (barrel);
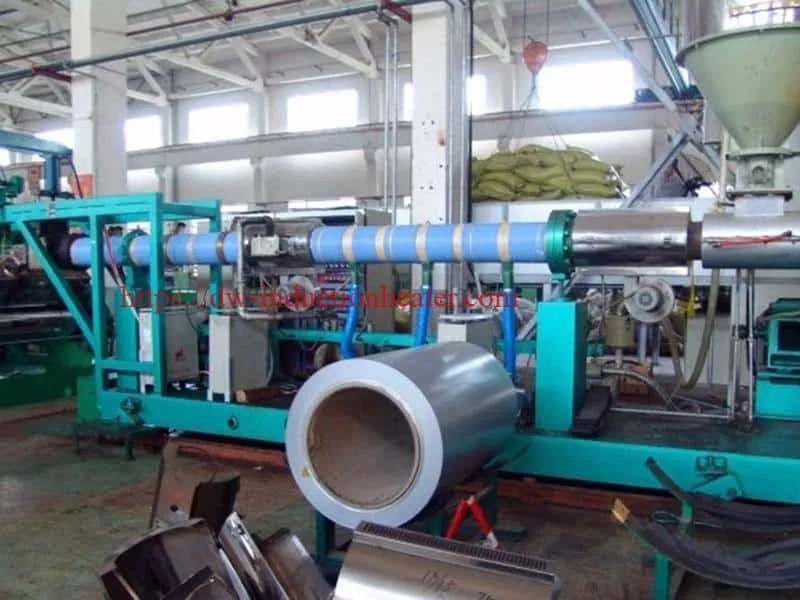
Induction Heating Aluminum Catheter Tipping
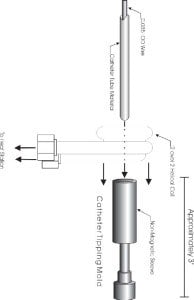
Induction Brazing Carbide Onto Steel Part
Induction Brazing Carbide Onto Steel Part
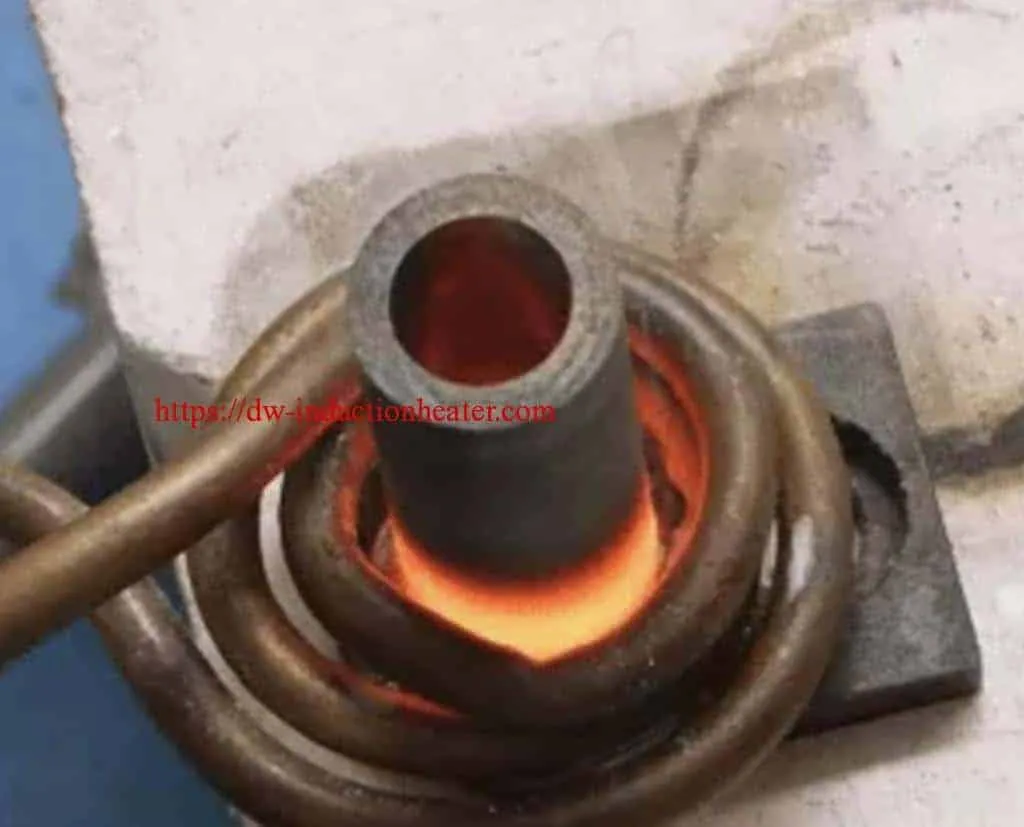
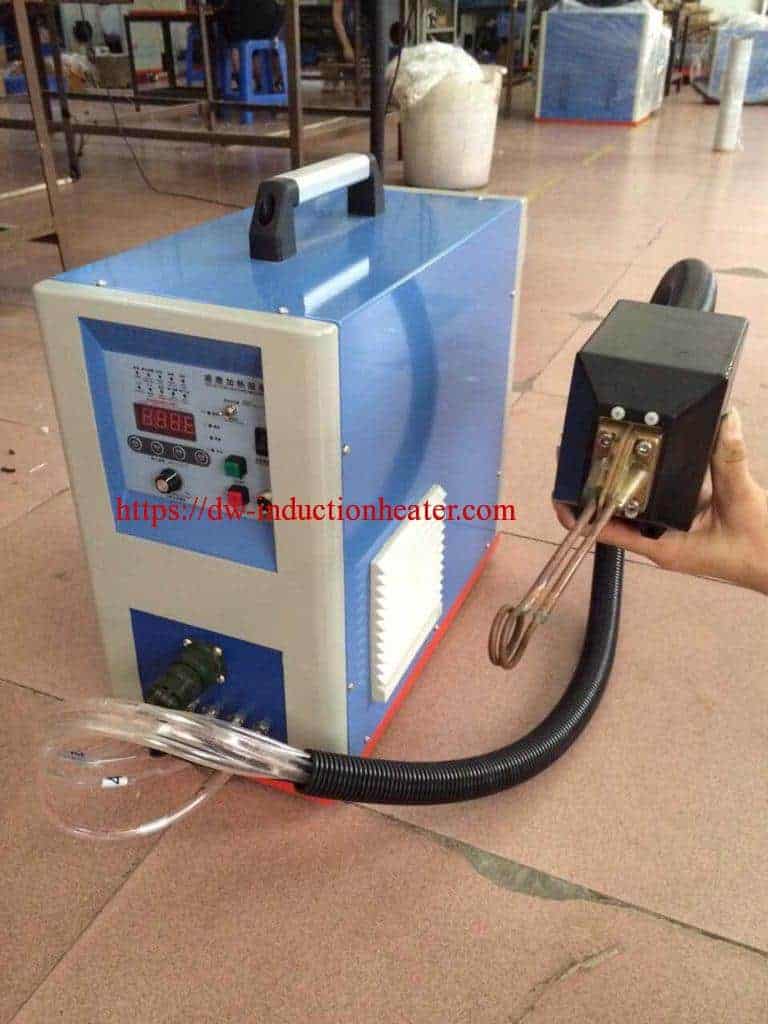
- To demonstrate elimination of “hand feeding” the alloy, we formed the alloy into a ring to tightly fit over the center post tube. This method provides a uniform amount for each cycle, resulting in uniform joints and wetting.
- The custom made coil was then placed over the steel piece, where is was set for 14 seconds to heat the alloy.
- The alloy was heated at approximately 1500°F (815)°C
- The whole piece is left alone and cooled with ambient air
induction preheating before welding steel pipe

Induction Preheating Before Welding Steel Pipe
This induction heating application shows the preheating of steel pipe before welding with 30kW air-cooled induction power supply and air-cooled coil. Inductively preheating of the pipe section to be welded ensures faster welding time and a better quality of the welding joint.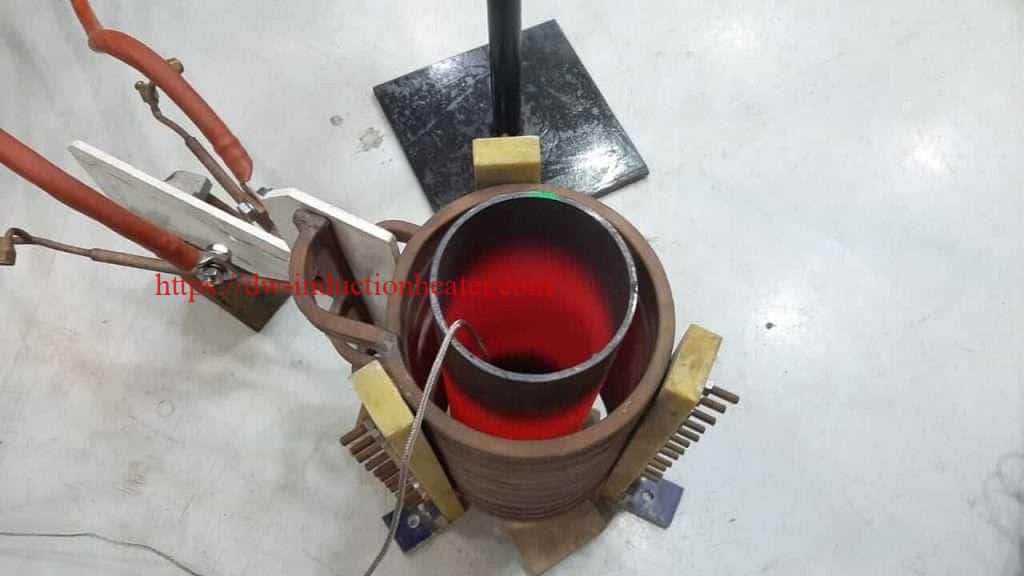


Induction Wire and Cable Heating
What is induction wire and cable heating?
HLQ Induction offers solutions for many applications from structural ferrous and non-ferrous wires, copper and aluminium cable and conductors to fibre optic production. The applications are very wide ranging including, but not limited to, forming, forging, heat treatment, galvanizing, coating, drawing etc. at temperatures from 10’s of degrees to in excess of 1,500 degrees.
What are the advantages of induction wire and cable heating?
The systems can be employed as your total heating solution or as a booster to improve the productivity of an existing furnace by acting as a preheater. Our induction heating solutions are renowned for their compactness, productivity and efficiency. Whilst we supply a range of solutions, most are optimised to meet your specific requirements.Where is induction wire and cable heating used?
Typical applications include: -Drying post cleaning or removing water or solvent from coatings -Curing of liquid or powder based coatings. Providing a superior bond strength and surface finish -Diffusion of metallic coating -Pre heating for extrusion of polymer and metallic coatings -Heat treatment including: stress relieving, tempering, annealing, bright annealing, hardening, patenting etc. -Pre-heating for hot-forming or forging, especially important for specification alloys. The unrivalled accuracy, control and efficiency of induction heating makes it ideal for many key tasks in the manufacture and processing of wire and cable products. Objective Heat several different wire diameters to 204°C (400°F) in 0.8 seconds with the same induction coil. Equipment: DW-UHF-6KW-III induction heater Process Steps: 1. Clean and apply 204°C (400°F) Tempilaq over the length of the wire. 2. Apply induction heat for 0.8 seconds. Results and Conclusions: All wires exceeded 204°C (400°F) over full length of coil. Further development testing will be required to optimize the equipment for the application for the fastest rates available. Tuning and optimization of the equipment would need to be done with a continuous wire feed in the unit. Based on the results, a 6kW induction heating power supply can be used, and further development testing would guarantee the desired rates. A 10kW induction heating power supply will recommended. The additional power will make the tuning and development testing easier for the end user and leave additional power for production rates to be easily increased in the future.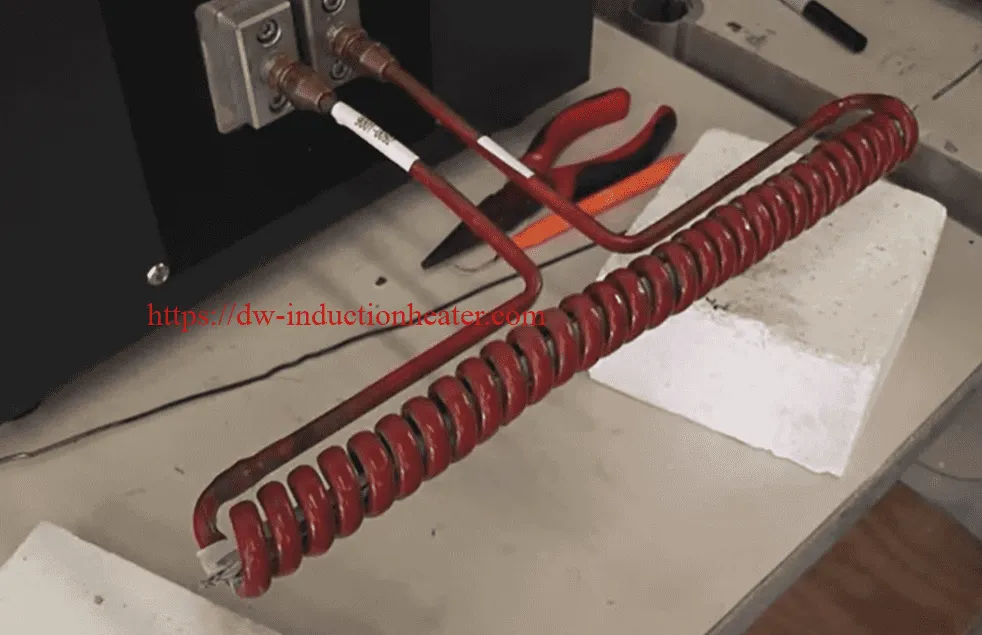
High Frequency Brazing Stainless Steel Fittings
High Frequency Brazing Stainless Steel Fittings
Objective High Frequency Brazing stainless steel fittings to corogated (SS) hoses. The hoses are with sizes ID 1.575in (40mm) and ID 2.99in (76 mm). The customer has never used induction heating before and is not familiar with the induction process. The goal of this test is to prove the strength of the joints.
- Hose and fittings are prepared with borax flux paste in the surface area.
- Brazing rod is prepared in form of a ring fitting around the diameter of the joint.
- The hose and the fittings are placed into the coil.
- Induction heating is applied to the area until the braze is completed.
- Power supply DW-UHF-10KW induction brazing machine meets the requirements for this process.
- For better performance for bigger diameter joints, we recommend power supply DW-UHF-10KW induction brazing heater.A special custom coil can be designed as well.
- For the tests, static induction was used (see video), but flexible leads and coil or our DW-UHF series are also recommended.
- Strong durable joints
- Selective and precise heat zone, resulting in less part distortion and joint stress
- Less oxidation
- Faster heating cycles
- More consistent results and suitability for large volume production, without the need for batch processing
- Safer than flame brazing
2022年8月30日星期二
portable ultrasonic mask welding machine for welding medical mask KN95 earloop
Portable ultrasonic mask welding machine-portable mask ultrasonic welder for bonding KN95 face earloop and nonwoven fabric and mask.
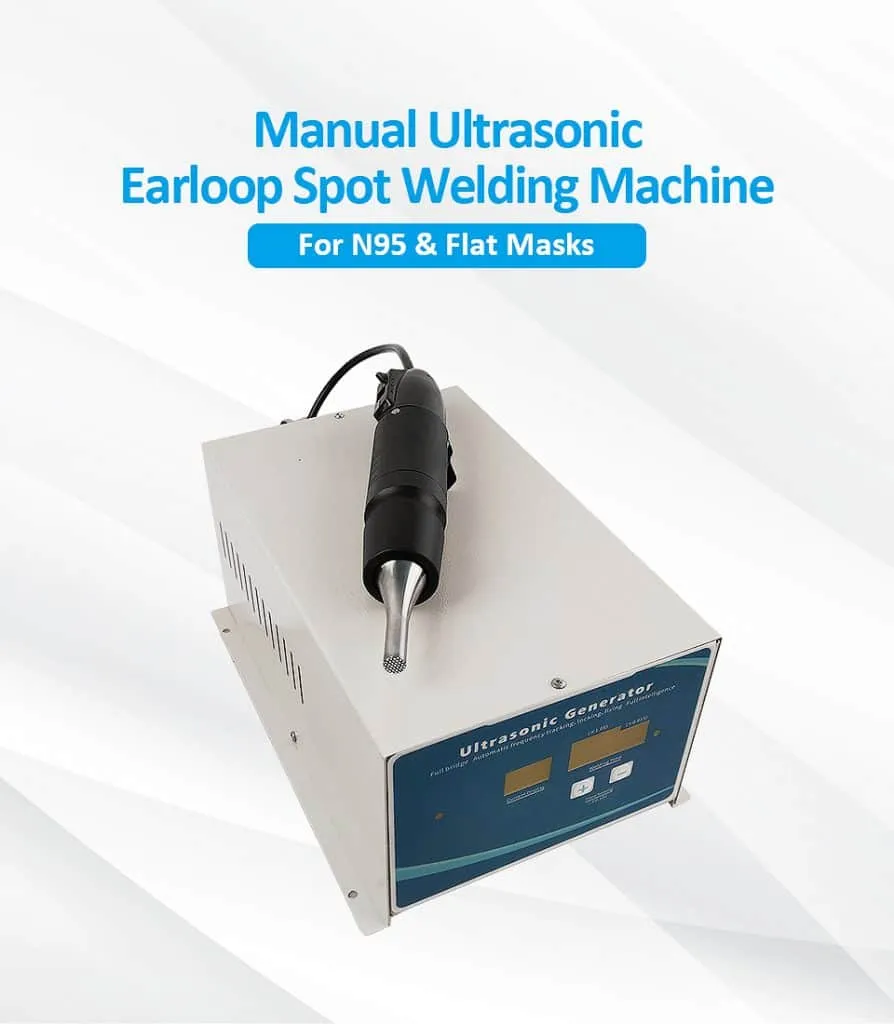
800W 28KHz portable mask portable ultrasonic mask welding machine for KN95& Mask Ear Loop Spot Welding ,Ultrasonic Face Mask Welding Machine Manually Used Device With Welding Head Transducer Generator.
Face Mask Ultrasonic Welding Machine
For N95 Face Mask & Disposable Mask
Transducer Frequency: 28KHz
Transducer Material: Magnalium
Welding Head Material:Titanium Alloy
Working Voltage: AC220V±10%(50-60HZ)
Working Frequency: 28KHz
Working Power: 800W
Whole set includes:
1) 28KHz Ultrasonic generator
2) Plastic body
3) 28KHz Ultrasonic transducer
4) Welding head
[wpforms id="3947"]
Induction Brazing Carbide To Steel
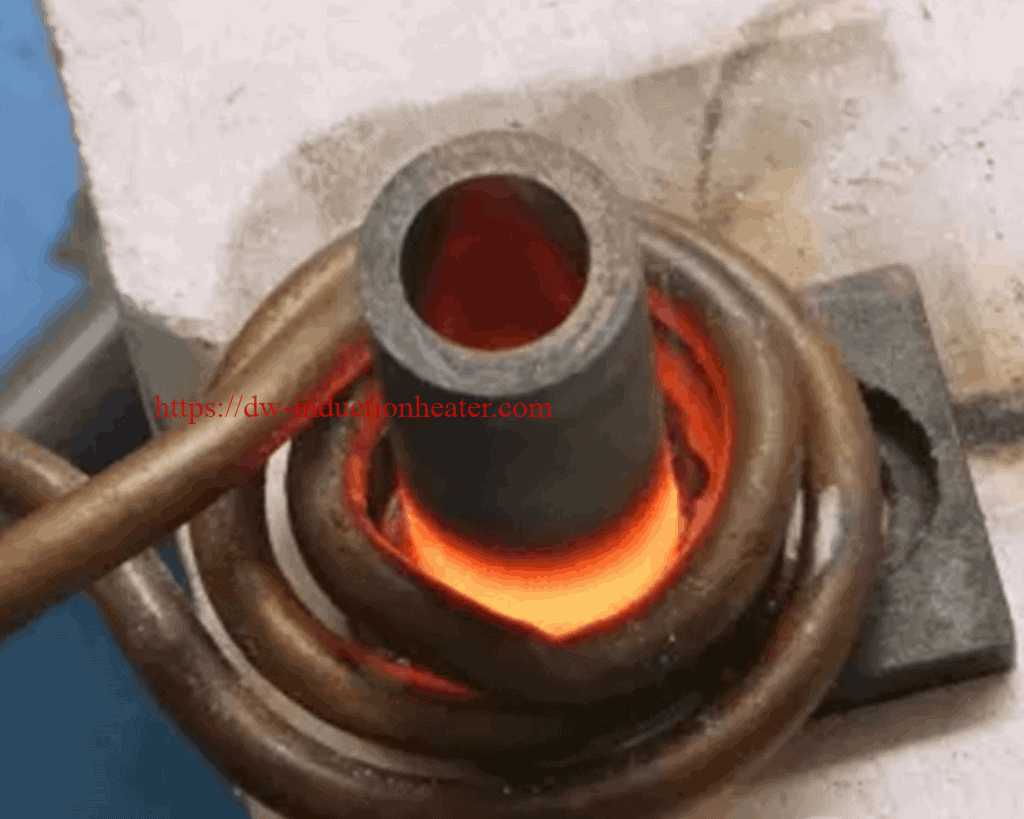


- To demonstrate elimination of “hand feeding” the alloy, we formed the alloy into a ring to tightly fit over the center post tube. This method provides a uniform amount for each cycle, resulting in uniform joints and wetting.
- The custom made coil was then placed over the steel piece, where is was set for 10 seconds to heat the alloy.
- The alloy was heated at approximately 1500°F (815)°C
- The whole piece is left alone and cooled with ambient air
- Induction Brazing was successful all in under 15 seconds with 8kW
- High quality and repeatability of the brazed joints
- Increased productivity
- Rings will need to be developed for specific joints to prevent the use of too much alloy
- Precise control of the time and temperature

Induction Curing Heating of Organic Coating
Induction Curing Heating of Organic Coating
Induction Heating is used to cure organic coating such as paint on metallic substrates by generating heat with in the subtract .By this mean curing occurs from within minimizing the tendency for formation of coating defects . A typical is application is drying of paint on sheet metal. Induction heating of metal parts to adhesive induction curing temperatures is utilized in a many automotive processes, such as the use of thermosetting adhesives to produce clutch plates, brake shoes and auto bumper components. Shafts are typically bonded to the squirrel cage rotors in the manufacture of small motors. In copying machines, plastic components are adhesively bonded to aluminum rotors; a thermoplastic glue is used to hold foam rollers on metal shafts. Once the rollers wear out, the shaft is heated and the foam replaced. Modern induction heating can solve many of these problems. Heating with induction provides reliable, repeatable, non-contact and energy-efficient heat in a minimal amount of time, so that the curing process can be completed with minimal energy and time. Improved temperature ramping cycles can be achieved with computer control of the solid state power supply. To eliminate extra steps for loading and unloading ovens, induction heat stations can be incorporated into a production line. Finally, induction heating can be performed in extremely clean environments, vacuum conditions or special atmospheres, allowing for unique curing solutions. Although induction heating is normally used with metals or other conductive materials, plastics and other non-conductive materials can often be heated very effectively by using a conductive metal susceptor to transfer the heat. Typical RF power supplies for induction curing applications range from 4 to 60kW, depending on the parts and application requirements.induction coating removal for removing paint
induction coating removal for removing paint
Induction coating removal principle
The induction disbonder works by the principle of induction. Heat is generated in the steel substrate and the bonding is broken. The coating is then removed entirely without disintegrating and completely free from contaminating agents, i.e. blast media.This obviously makes disposal and recycling of waste easier and cheaper. Even inside the pittings and cracks in the surface the coating is disbonded. The HLQ Induction heating works by fast transfer of energy to the steel substrate, as a result securing a controlled heating of the surface and fast removal of most types of coatings.What is induction coating removal?
The HLQ Induction coating removal system is a state-of-the-art induction heating tool that rapidly strips paint and tough, high-build coatings. It is a faster, cleaner and safer way to strip coatings.
What are the benefits?
Induction heating can outperform traditional paint-stripping methods. Abrasive blasting or disk grinding are generally more labour intensive and come with other issues such as the cost of enclosure or containment and collection of blast media, plus the filtration or separation of the coating materials for disposal. In many urban projects these are prime considerations and extremely costly to overcome. Whereas, when coatings are removed by induction, the only waste is the coating itself which in most cases can be swept or even vacuumed like any other workshop waste.
Safer working environment: The controlled, localized heat results in significantly reduced fumes and toxic dust.
Easy clean-up: The coating material mainly peels off in flakes rather than being pulverized.
Noiseless operation: Operators can work in public areas without creating a disturbance.
Mobile: The equipment is rugged and reliable but still light-weight and easy to move around worksites.
Reduced energy consumption: Fast, accurate and repeatable heat delivery makes the coating removal process extremely energy efficient.
Method flexibility: Spot heating, scanning, freehand and semi-automatic.
No limitations: The system can be used at flat surfaces, round contours, inside/outside corners, both sides of substrate, round rivets, etc.
Where is it used?
Induction coating removal is used in many industries, such as ships/marine, buildings, storage tanks, pipelines, bridges and offshore.
induction heating involves using alternating current and an induction coil to generate a powerful electro-magnetic field. When used properly, this field generates heat below a coating on a steel substrate, resulting in the coating de-bonding quickly and easily from the metal surface. At Alliance, we use this process to remove coatings from steel such as:
- Multiple coatings including epoxies, urethanes and others
- Lead paint
- Fire-retardant coatings (PFPs)
- Glued and vulcanized rubber as well as chlorinated rubber
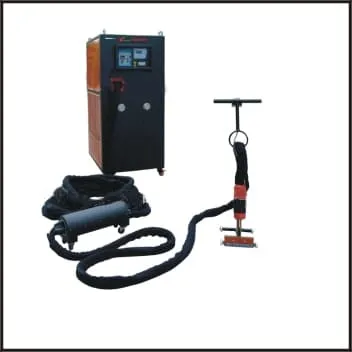
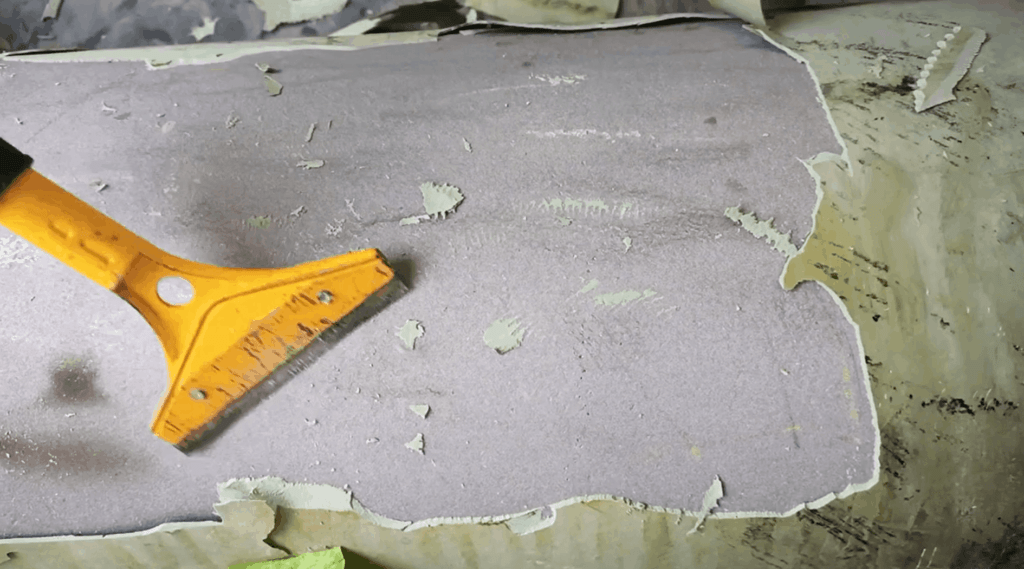

关注者
博客归档
-
▼
2022
(1729)
-
▼
八月
(178)
- Induction Heating Molding Catheter Tip
- induction heating plastic extrusion
- Induction Heating Aluminum Catheter Tipping
- Induction Brazing Carbide Onto Steel Part
- induction preheating before welding steel pipe
- Induction Wire and Cable Heating
- High Frequency Brazing Stainless Steel Fittings
- portable ultrasonic mask welding machine for weldi...
- Induction Brazing Carbide To Steel
- Induction Curing Heating of Organic Coating
- Induction Hardening Inner
- induction coating removal for removing paint
- Brazing Copper Bars with Induction
- induction brazing stainless steel to steel
- induction heating plastic extrusion
- Brazing Aluminum to Copper Tubes with Induction
- Annealing Saw Blades with Induction
- Induction Heat Setting
- Brazing Aluminum Pipes Assembly With Induction
- Brazing Aluminum Tubes with Induction Heating
- Induction heating of aluminium billets
- Induction Wire and Cable Heating
- Induction Brazing Stainless Steel
- Induction Brazing Aluminum to Aluminum Tube
- Induction Soldering Cables to Terminals
- Induction Preheating Hot Heading
- Induction Shrink Fitting Carbide Ring
- Induction Soldering Electrical Circuits
- Brazing Automotive Parts With Induction
- Induction Preheating Hot Heading
- induction coating removal for removing paint
- INDUCTION HEATING FOR SURFACE QUENCHING
- induction heating thermal conductive oil system
- Induction Soldering Cables to Terminals
- RPR Induction Pipeline Coating Removal
- induction heating for surface quenching of steel
- Induction Brazing Steel Tube
- High Frequency Welding
- Brazing copper tube to brass fitting
- Induction Brazing T Shaped Copper Tubing Assemblies
- What is induction welding?
- How to design induction heating coil
- Induction heating of aluminium billets
- Induction Susceptor Heating
- Brazing Steel To Steel Pipe With Induction
- Pipeline Coating Process
- induction brazing stainless steel tubing process
- Induction Brazing Aluminum to Aluminum Tube
- Magnetic Induction Heater Manufacturer
- Induction Soldering Copper Pipes to PCB Board
- Research and Design on IGBT Induction Heating Powe...
- Induction Brazing Copper Assembly
- Application of induction aluminum melting furnace
- Induction Brazing Aluminum Tube T Joints
- Brazing Carbide to Steel Part With Induction Heating
- KN95 mask ultrasonic mask welder for nonwoven fabr...
- Induction Preheating Hot Heading
- Induction Heating Sintering Copper Powder
- Induction Soldering magnetic steel pins
- Induction Soldering Stainless Steel To Wire
- ultrasonic welding fabric machine for bonding nonw...
- High Frequency Welding
- Handheld Brazing Stainless Steel Tube
- Induction Brazing Machine
- Induction straightening deck and bulkhead heating ...
- Induction Catheter Tipping Heating
- Induction Brazing Carbide to Steel
- Induction Soldering Wires Onto Connection
- Induction Hardening and tempering
- Induction Wire Heating Process Applications
- induction heating reactor tank-vessels
- Induction Brazing Steel Tips
- high frequency induction hardening camshafts process
- Aluminum Scrap Melting Recycling Induction Furnace
- Induction Brazing Carbide
- Induction Fluid Pipeline heating system
- Induction annealing stainless steel wire
- Induction Heating Theory PDF
- Brazing stainless steel with induction
- Brazing Aluminum Tubes with Induction Heating
- RPR Induction Stripping-Induction Rust & Paint Coa...
- Induction Heating fundamentals PDF
- Induction Brazing Heating Exchanger Copper Pipes
- induction Brazing copper rods to brass strips
- Induction Brazing Copper Tube For Refrigeration
- High Speed Heating by Induction Heating System
- Induction Heat Setting
- Induction Heating Sintering Copper Powder
- Induction Annealing Copper Wire
- Induction Preheating Welding Steel Pipe
- Brazing Carbide Tool Tips With Induction
- Induction Shrink Fitting Assemblies
- Handheld Induction Brazing Copper Tubing and Fitting
- High Frequency Induction Cap Sealing
- induction sealing glass
- High Frequency Induction Brazing Copper Wire
- induction brazing stainless steel tubing process
- Jointing Metal with Brazing and Welding
- Induction Soldering Brass Assembly
- Induction Annealing Copper Tubes
-
▼
八月
(178)
我的简介

- HLQ induction heating machine
- HLQ induction heating machine manufacturer provides the service of induction brazing,melting,hot forming,hardening surface,annealing,shrink fitting,PWHT,etc.