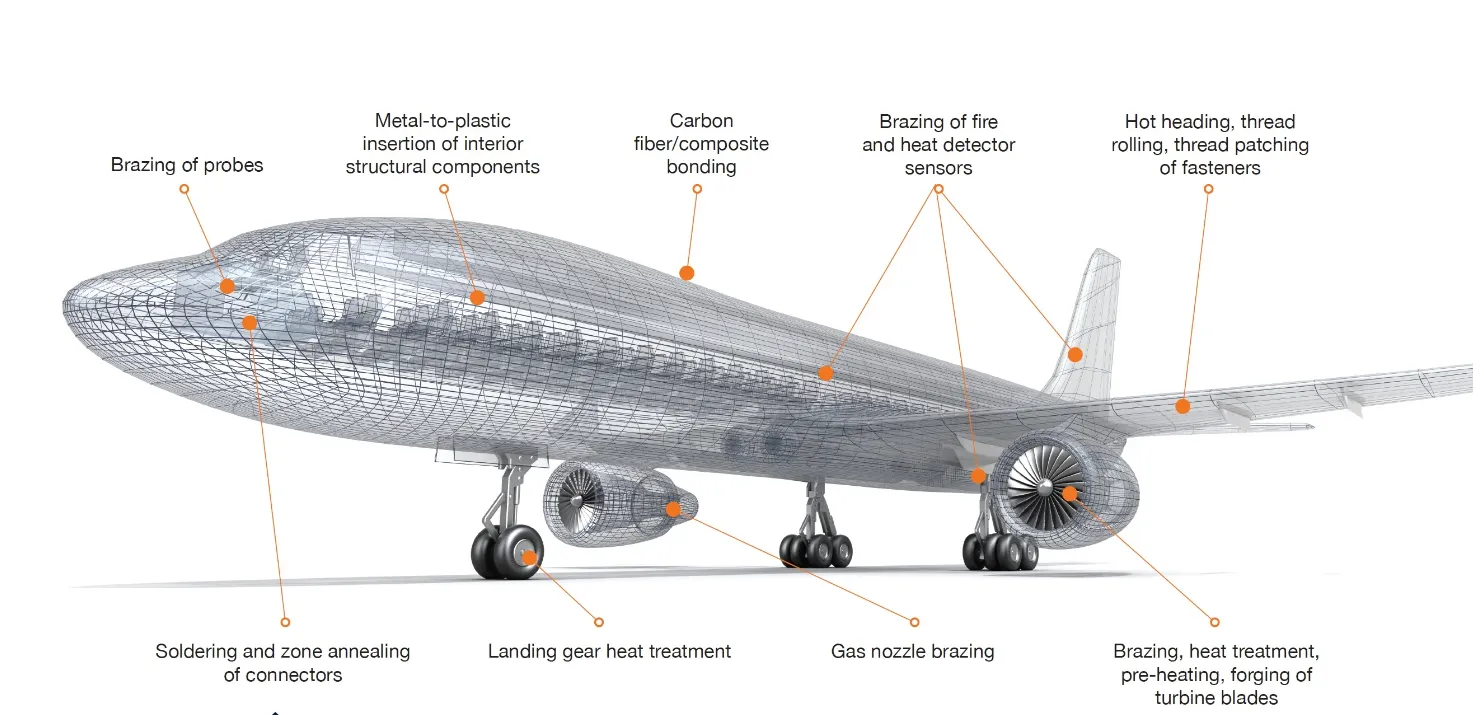
The aerospace industry is known for its stringent requirements in terms of safety, reliability, and performance. To meet these demands, various advanced technologies are employed throughout the manufacturing process. One such technology is induction quenching, which plays a crucial role in enhancing the durability and strength of aerospace components. This article aims to explore the applications of induction quenching in the aerospace industry, highlighting its benefits and significance.
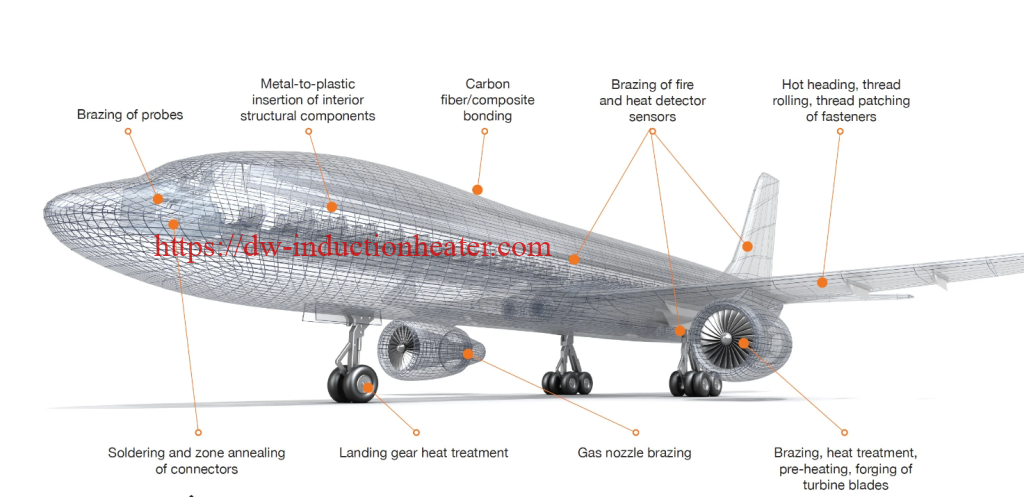
1.1 Definition and Principles
Induction quenching is a heat treatment process used to harden the surface of metal components by rapidly heating them using electromagnetic induction and then quenching them in a cooling medium, such as water or oil. The process involves the use of an induction coil that generates a high-frequency alternating current, which creates a magnetic field that induces eddy currents in the workpiece, causing it to heat up.
The principles behind induction quenching are based on the concept of selective heating, where only the surface layer of the component is heated while maintaining the core at a lower temperature. This allows for controlled hardening of the surface without affecting the overall properties of the component.
1.2 Process Overview
The induction quenching process typically involves several steps:
1) Preheating: The component is preheated to a specific temperature to ensure uniform heating during the quenching process.
2) Heating: The component is placed within an induction coil, and an alternating current is passed through it, generating eddy currents that heat up the surface layer.
3) Quenching: After reaching the desired temperature, the component is rapidly cooled by immersing it in a cooling medium, such as water or oil, to achieve rapid transformation and hardening of the surface layer.
4) Tempering: In some cases, after quenching, the component may undergo tempering to reduce internal stresses and improve toughness.
1.3 Advantages over Conventional Quenching Methods
Induction quenching offers several advantages over conventional quenching methods:
- Faster heating: Induction heating allows for rapid and localized heating of specific areas, reducing overall processing time compared to conventional methods.
- Selective hardening: The ability to control heating patterns enables selective hardening of specific areas while leaving other parts unaffected.
- Reduced distortion: Induction quenching minimizes distortion due to localized heating and cooling, resulting in improved dimensional stability.
- Improved repeatability: The use of automated systems ensures consistent results from batch to batch.
- Energy efficiency: Induction heating consumes less energy compared to other methods due to its localized nature.
2. Importance of Induction Quenching in Aerospace
2.1 Enhancing Component Durability
In aerospace applications, where components are subjected to extreme operating conditions such as high temperatures, pressures, and vibrations, durability is crucial for ensuring safe and reliable operation. Induction quenching plays a vital role in enhancing component durability by increasing their resistance to wear, fatigue, and corrosion.
By selectively hardening critical areas such as turbine blades or landing gear components using induction quenching techniques, their lifespan can be significantly extended under harsh operating conditions.
2.2 Improving Mechanical Properties
Induction quenching also improves mechanical properties such as hardness and strength by transforming the microstructure of metal components through rapid cooling after heating.
By carefully controlling the heating parameters during induction quenching processes like tempering or martempering, desired mechanical properties can be achieved for different aerospace applications.
2.3 Ensuring Consistency and Precision
Aerospace components require strict adherence to specifications due to their critical nature in ensuring flight safety. Induction quenching provides consistent results with high precision due to its automated nature and ability to control heat distribution accurately.
This ensures that each component undergoes uniform heat treatment with minimal variation from batch to batch or part-to-part within a batch.
3. Applications of Induction Quenching in Aerospace
3.1 Engine Components
Induction quenching is widely used in the aerospace industry for various engine components due to its ability to provide high strength and wear resistance.
3.1.1 Turbine Blades
Turbine blades are subjected to high temperatures and extreme conditions, making them prone to wear and fatigue. Induction quenching can be used to harden the leading edges and airfoil surfaces of turbine blades, improving their resistance to erosion and extending their service life.
3.1.2 Compressor Disks
Compressor disks are critical components in jet engines that require high strength and fatigue resistance. Induction quenching can be used to selectively harden the teeth and root areas of compressor disks, ensuring their durability under high rotational speeds and loads.
3.1.3 Shafts and Gears
Shafts and gears in aerospace engines also benefit from induction quenching. By selectively hardening the contact surfaces, these components can withstand the high torque, bending, and sliding forces they experience during operation.
3.2 Landing Gear Components
Landing gear components are subjected to heavy loads during takeoff, landing, and taxiing operations. Induction quenching is commonly used to enhance the strength and wear resistance of these components.
3.2.1 Axles and Shafts
Axles and shafts in landing gear systems can be induction hardened to improve their load-carrying capacity and resistance against fatigue failure.
3.2.2 Wheel Hubs
Wheel hubs are critical for supporting the weight of an aircraft during landing operations. Induction quenching can be applied to increase their hardness, reducing wear and extending their lifespan.
3.2.3 Brackets and Mounts
Brackets and mounts play a crucial role in securing various landing gear components together. Induction quenching can improve their strength, preventing deformation or failure under heavy loads.
3.3 Structural Components
Induction quenching is also utilized for strengthening structural components in aerospace applications.
3.4 Fasteners and Connectors
Fasteners such as bolts, screws, rivets, and connectors are essential for joining different parts of an aircraft together securely. Induction quenching can enhance their mechanical properties, ensuring reliable connections under extreme conditions.
4.Techniques Used in Induction Quenching
4 . 1 Single Shot Induction Hardening
Single shot induction hardening is a common technique used in aerospace applications where specific areas need to be hardened quickly with minimal distortion or heat affected zone (HAZ). In this technique, a single coil is used to heat the desired area rapidly before it is cooled using a spray or immersion quenching process.
4 . 2 Scanning Induction Hardening
Scanning induction hardening involves moving an induction coil over the surface of a component while applying heat locally through electromagnetic induction followed by rapid cooling using a spray or immersion method. This technique allows for precise control over the hardened area while minimizing distortion.
4 . 3 Dual Frequency Induction Hardening
Dual frequency induction hardening involves using two different frequencies simultaneously or sequentially during the heating process to achieve desired hardness profiles on complex-shaped components with varying cross-sections or thicknesses.
4 . 4 Surface Hardening
Surface hardening techniques involve selectively heating only the surface layer of a component while maintaining its core properties intact through techniques such as flame hardening or laser surface hardening.
5. Advancements in Induction Quenching Technology
Induction quenching is a heat treatment process that involves heating a metal component using electromagnetic induction and then rapidly cooling it to increase its hardness and strength. This process has been widely used in various industries, including the aerospace industry, due to its ability to provide precise and controlled heat treatment.
In recent years, there have been significant advancements in induction quenching technology that have further improved the efficiency and effectiveness of the process. This section will discuss some of these advancements.
5.1 Simulation Techniques for Process Optimization
Simulation techniques have become an essential tool for optimizing induction quenching processes. These techniques involve creating computer models that simulate the heating and cooling behavior of the metal component during the quenching process. By using these simulations, engineers can optimize various parameters such as power density, frequency, and quenching medium to achieve desired hardness profiles and minimize distortion.
These simulations also allow for virtual prototyping, which reduces the need for physical prototypes and testing. This not only saves time and cost but also enables engineers to explore different design options before manufacturing.
5.2 Intelligent Control Systems
Intelligent control systems have been developed to enhance the precision and repeatability of induction quenching processes. These systems use advanced algorithms and sensors to monitor and control various parameters such as power input, temperature distribution, and cooling rate.
By continuously adjusting these parameters in real-time based on feedback from sensors, intelligent control systems can ensure consistent heat treatment results even with variations in material properties or component geometry. This improves process reliability and reduces scrap rates.
5.3 Integration with Robotics
The integration of induction quenching technology with robotics has enabled automation of the heat treatment process. Robotic systems can handle complex geometries with high precision, ensuring uniform heating and cooling throughout the component.
Robotic integration also allows for increased productivity by reducing cycle times and enabling continuous operation without human intervention. Additionally, it improves worker safety by eliminating manual handling of hot components.
5.4 Non-Destructive Testing Techniques
Non-destructive testing (NDT) techniques have been developed to assess the quality of induction-quenched components without causing any damage or alteration to them. These techniques include methods such as ultrasonic testing, eddy current testing, magnetic particle inspection, etc.
By using NDT techniques, manufacturers can detect defects such as cracks or voids that may have occurred during the quenching process or due to material properties. This ensures that only components meeting quality standards are used in aerospace applications where reliability is critical.
6.Challenges and Limitations
Despite advancements in induction quenching technology, there are still several challenges and limitations that need to be addressed for its widespread adoption in the aerospace industry.
6.1 Material Selection Challenges
Different materials require different heat treatment parameters for optimal results. The aerospace industry uses a wide range of materials with varying compositions and properties. Therefore, selecting appropriate heat treatment parameters for each material can be challenging.
Engineers need to consider factors such as material composition, microstructure requirements, desired hardness profiles, etc., while designing induction quenching processes for aerospace components.
6.2 Distortion Control Issues
Induction quenching processes can induce distortion in metal components due to non-uniform heating or cooling rates. This distortion can result in dimensional inaccuracies, warping, or even cracking of the components.
One common cause of distortion in induction quenching is non-uniform heating. Induction heating relies on electromagnetic fields to generate heat in the metal component. However, the distribution of heat within the component may not be uniform, leading to uneven expansion and contraction during the quenching process. This can cause bending or twisting of the component.
Another factor that contributes to distortion is non-uniform cooling rates. Quenching involves rapidly cooling the heated metal component to harden it. However, if the cooling rate is not consistent throughout the component, different areas may experience varying levels of contraction, leading to distortion.
To mitigate distortion issues, several strategies can be employed. One approach is to optimize the design of the induction coil and its positioning relative to the component. This can help ensure more uniform heating and minimize temperature gradients within the part.
Controlling the quenching process is also crucial for reducing distortion. The selection of an appropriate quenchant and its application method can significantly impact cooling rates and minimize distortion. Additionally, using fixtures or jigs during quenching can help constrain movement and prevent warping or bending.
Post-quenching processes such as tempering or stress relieving can also be employed to reduce residual stresses that contribute to distortion. These processes involve controlled heating and cooling cycles that help stabilize the metal structure and relieve internal stresses.
Induction quenching is a heat treatment process that involves rapidly heating a metal component using electromagnetic induction and then rapidly cooling it to increase its hardness and strength. This process has been widely used in the aerospace industry for many years, and its future prospects look promising due to advancements in material science, integration with additive manufacturing processes, and enhanced process monitoring techniques.
7.Future Prospects of Induction Quenching in Aerospace Industry
7.1 Advancements in Material Science:
Material science plays a crucial role in the aerospace industry as it constantly seeks to develop new materials with improved properties. Induction quenching can benefit from these advancements by utilizing new materials that are more resistant to high temperatures and have better mechanical properties. For example, the development of advanced alloys such as nickel-based superalloys or titanium alloys can enhance the performance of components subjected to induction quenching. These materials offer higher strength, better corrosion resistance, and improved fatigue properties, making them ideal for aerospace applications.
7.2 Integration with Additive Manufacturing Processes:
Additive manufacturing, also known as 3D printing, has gained significant attention in recent years due to its ability to produce complex geometries with high precision. The integration of induction quenching with additive manufacturing processes opens up new possibilities for the aerospace industry. By selectively heating specific areas of a 3D printed component using induction quenching, it is possible to locally modify the material's microstructure and improve its mechanical properties. This combination allows for the production of lightweight components with tailored properties, reducing weight and increasing fuel efficiency in aircraft.
7.3 Enhanced Process Monitoring Techniques:
Process monitoring is essential for ensuring consistent quality and reliability in induction quenching operations. Advancements in sensor technology and data analysis techniques have enabled more accurate monitoring of key parameters during the heat treatment process. Real-time monitoring of temperature gradients, cooling rates, and phase transformations can help optimize the induction quenching process parameters for specific aerospace components. Additionally, advanced non-destructive testing methods such as thermography or acoustic emission can be integrated into the process monitoring system to detect any defects or anomalies that may occur during induction quenching.
Conclusion
Induction quenching has emerged as a critical technology within the aerospace industry due to its ability to enhance component durability, improve mechanical properties, ensure consistency, and precision during manufacturing processes.
As advancements continue to be made in this field, it is expected that induction quenching will play an even more significant role in meeting the evolving demands of the aerospace industry.
By leveraging simulation techniques, intelligent control systems, integration with robotics, and non-destructive testing techniques, manufacturers can overcome challenges associated with material selection, distortion control issues, and energy consumption.
With future prospects including advancements in material science, integration with additive manufacturing processes, and enhanced process monitoring techniques; induction quenching is poised to revolutionize the aerospace industry by enabling the production of safer, more reliable aircraft components.
https://dw-inductionheater.com/induction-quenching-applications-in-the-aerospace-industry.html?feed_id=231987&_unique_id=659fa814e166d