CNC vertical induction quenching machines are becoming increasingly popular in the manufacturing industry due to their ability to quickly and efficiently heat-treat metal parts. These machines use induction heating technology to heat up metal parts to high temperatures, followed by a quenching process to rapidly cool the metal, resulting in a hardened surface. In this article, we will dive deeper into the features, benefits, and applications of
CNC vertical induction quenching machines.
What is CNC Vertical Induction Quenching Machine?
CNC vertical induction quenching machine is a type of machine used in the heat treatment process. It is designed to harden various metals and alloys using electromagnetic induction, which requires the use of a high-frequency electric current to generate heat.

The
CNC vertical induction quenching machine is constructed with an induction coil that surrounds the workpiece, and the coil is powered by an induction generator, which creates the high-frequency current. This current flows through the coil, which induces an electric current in the workpiece, generating heat that is used to harden the metal.
Features of CNC Vertical Induction Quenching Machines:
1. Precision Control: CNC vertical induction quenching machines are equipped with advanced control systems that allow for precise temperature and heating time control. This ensures that the metal parts are heated and cooled uniformly, resulting in consistent hardness levels across all parts.
2. Automated Processes: CNC vertical induction quenching machines are fully automated, which means that they can be programmed to perform a sequence of heating and cooling processes without human intervention. This not only saves time but also reduces the risk of errors.
3. High Efficiency: CNC vertical induction quenching machines use induction heating, which is a highly efficient heating method. This means that the machines consume less energy compared to other heating methods, resulting in cost savings for the manufacturer.
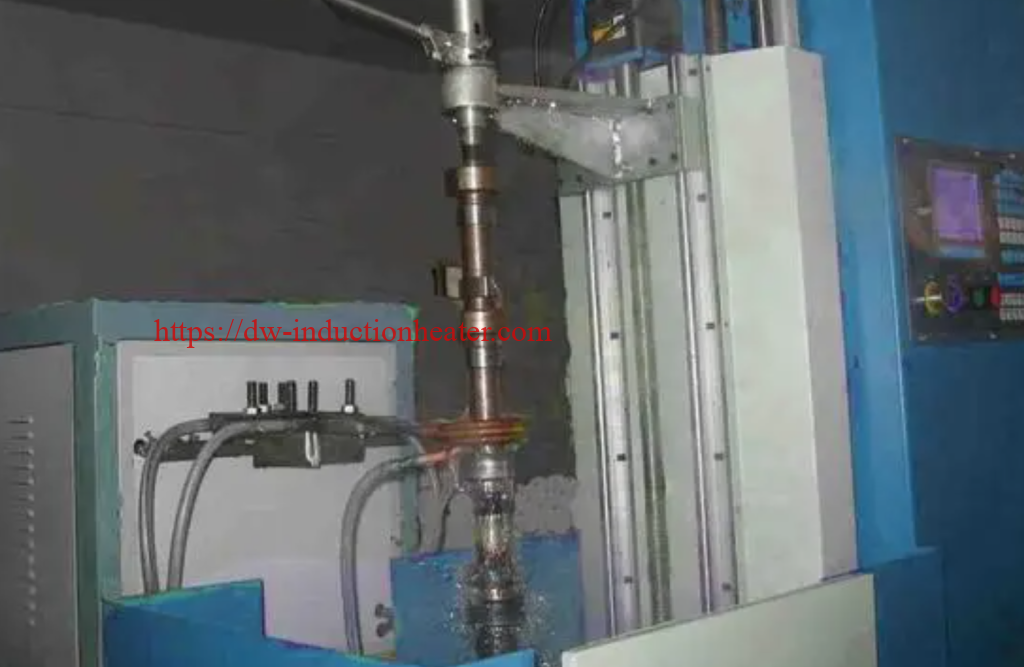
4. Compact Design: CNC vertical induction quenching machines have a compact design, which means that they occupy less floor space compared to other heat-treating equipment. This makes them ideal for small manufacturing facilities with limited space.
Benefits of CNC Vertical Induction Quenching Machines:
1. Improved Product Quality: CNC vertical induction quenching machines produce parts with consistent hardness levels, which translates into improved product quality. This is especially important for manufacturers who produce critical components that require high precision and reliability.
2. Reduced Manufacturing Time: CNC vertical induction quenching machines are faster than other heat-treating equipment, which means that they can process more parts in less time. This results in increased productivity and shorter lead times.
3. Lower Operating Costs: CNC vertical induction quenching machines consume less energy compared to other heating methods, resulting in lower operating costs. This is especially important for manufacturers who are looking to reduce their energy consumption and carbon footprint.
4. Increased Flexibility: CNC vertical induction quenching machines can be programmed to perform a variety of heating and cooling processes, making them ideal for a wide range of applications. This means that manufacturers can use the same machine to heat-treat different types of parts, resulting in increased flexibility.
Applications of CNC Vertical Induction Quenching Machines:
1. Automotive Industry: CNC vertical induction quenching machines are widely used in the automotive industry to heat-treat various components such as gears, shafts, and springs. These components require high precision and reliability, making CNC vertical induction quenching machines an ideal choice.
2. Aerospace Industry: The aerospace industry also uses CNC vertical induction quenching machines to heat-treat critical components such as turbine blades, engine parts, and landing gear. These components require high precision and reliability, making CNC vertical induction quenching machines an ideal choice.
3. Medical Industry: CNC vertical induction quenching machines are also used in the medical industry to heat-treat various surgical instruments and implants. These components require high precision and reliability, making CNC vertical induction quenching machines an ideal choice.
The Ultimate Guide to CNC Vertical Induction Hardening Machine
CNC Vertical induction hardening machine is an essential tool in the manufacturing industry that is used to harden roller shafts. The process of induction hardening is the most efficient way to strengthen the surface of metal parts, including roller shafts. It provides improved wear resistance, durability, and better performance of the finished product.
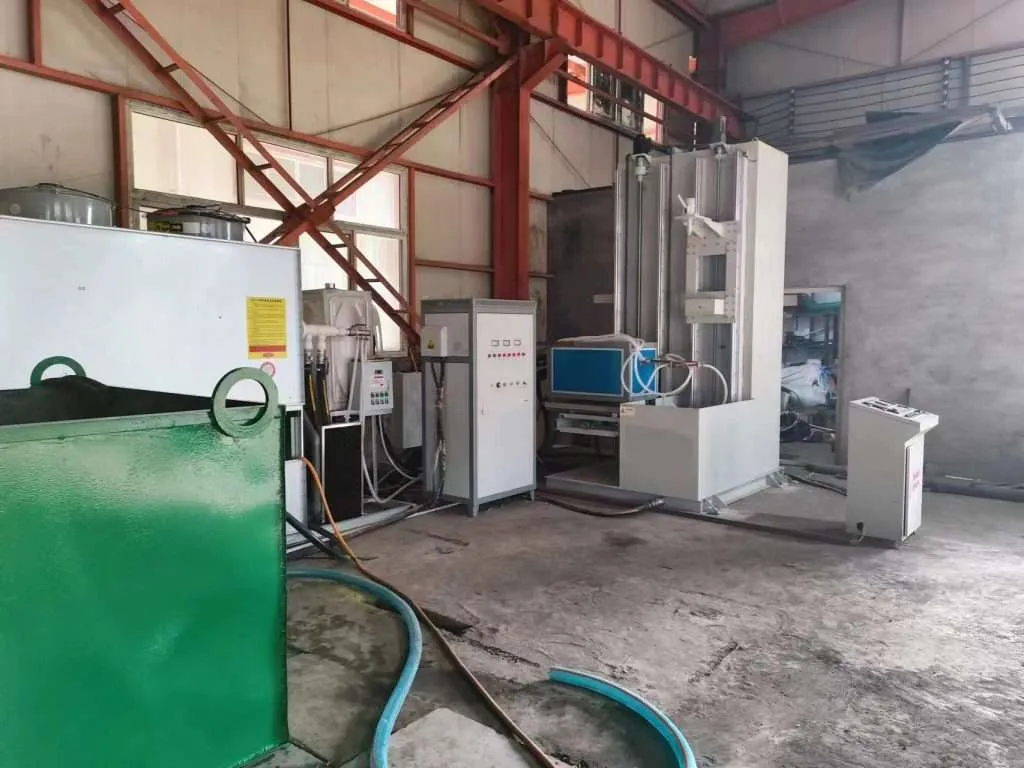
If you are in the manufacturing business, you need to understand how to use this machine to improve the quality of your products. In this article, we will provide you with an ultimate guide to roller shaft induction hardening machines. We will go over everything you need to know about the machine, how it works, its benefits, and how to maintain it so that it lasts longer. Let's dive in and learn more about this powerful tool.
3. Benefits of Using CNC Vertical Induction Hardening Machine
CNC Vertical induction hardening machines have become increasingly popular due to their many benefits. One of the most notable benefits is that they provide a quick and efficient hardening process for roller shafts. With this technology, roller shafts can be hardened in a matter of seconds, which greatly reduces production time and increases efficiency. Additionally, the machines are very versatile and can accommodate a variety of roller shaft sizes. This means that businesses can adapt and customize their production processes to meet their specific needs. Another benefit of using a roller shaft induction hardening machine is that it provides a uniform hardening pattern across the entire roller shaft surface. This ensures that the quality of the hardened surface is consistent and reliable throughout the entire production process. Additionally, the process of induction hardening is environmentally friendly, as it only requires a minimal amount of energy to operate. It also produces less waste and pollution compared to other traditional hardening processes. Furthermore, using a roller shaft induction hardening machine can also help to extend the lifespan of the roller shafts, reducing the need for frequent repairs and replacements. This ultimately saves businesses money and increases their overall productivity. Finally, the machine provides a safe and reliable hardening process, with minimal risk of injury to operators. Overall, the benefits of using a roller shaft induction hardening machine make it a valuable investment for businesses looking to improve their production processes and reduce their environmental impact.
4. How to Maintain CNC Vertical Induction Hardening Machine?
Maintaining your roller shaft induction hardening machine is crucial to ensure its longevity and continued performance.
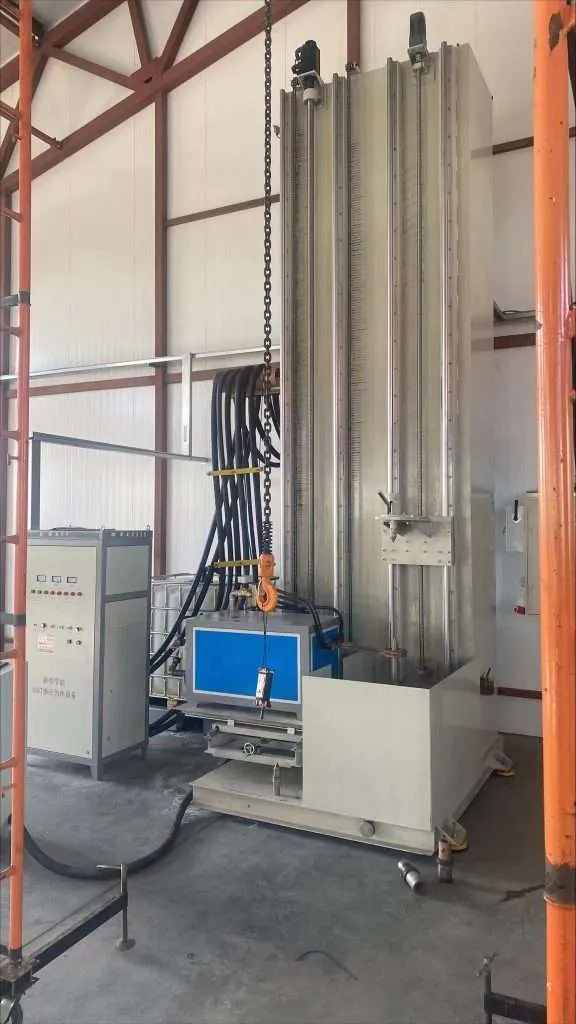
Here are some tips to keep your machine running smoothly:
1. Regular cleaning: Dust and debris can accumulate on your machine, which can cause damage over time. It's essential to clean your machine regularly to prevent any build-up. Use a soft cloth to wipe down the machine and remove any dirt or debris.
2. Lubrication: Proper lubrication is essential to keep your machine functioning correctly. Make sure to use the recommended lubricant and apply it regularly to the appropriate parts of the machine.
3. Regular inspection: Inspecting your machine regularly can help you identify any potential issues before they become bigger problems. Look for signs of wear and tear, such as cracks or deformation in the rollers.
4. Proper storage: When not in use, it's essential to store your machine properly. Keep it in a dry, cool place that is free from any exposure to moisture or extreme temperatures.
5. Professional maintenance: While regular cleaning and inspection can help prevent issues, it's also crucial to have your machine professionally serviced regularly.
A professional technician can identify any potential problems and provide the necessary repairs and maintenance to keep your machine running smoothly. By following these tips, you can ensure that your roller shaft induction hardening machine remains in top condition, providing you with reliable and efficient performance for years to come.
Hardening Machine Tools-Quenching Machine Tools
According to the different of workpiece, there are vertical type, horizontal type,closed type, customized type, etc.
1.Standard SK-500/1000/1200/1500 workpiece moving type For shafts, discs, pins and gears hardening
2.SK-2000/2500/3000/4000 Transformer moving type , Used for heating length more than 1500mm shaft
3.Closed type : Customized for big shaft ,More clean work environment.
4.Horizontal hardening machine tool
SK-500/1000/1200/1500/2000/2500/3000/4000 Used for smooth shaft
5.Customized type
Technical Parameter
Model |
SK-500 |
SK-1000 |
SK-1200 |
SK-1500 |
Max heating length(mm) |
500 |
1000 |
1200 |
1500 |
Max heating diameter(mm) |
500 |
500 |
600 |
600 |
Max holding length(mm) |
600 |
1100 |
1300 |
1600 |
Max weight of workpiece(Kg) |
100 |
100 |
100 |
100 |
Workpiece rotation speed(r/min) |
0-300 |
0-300 |
0-300 |
0-300 |
workpiece moving speed(mm/min) |
6-3000 |
6-3000 |
6-3000 |
6-3000 |
Cooling method |
Hydrojet cooling |
Hydrojet cooling |
Hydrojet cooling |
Hydrojet cooling |
Input voltage |
3P 380V 50Hz |
3P 380V 50Hz |
3P 380V 50Hz |
3P 380V 50Hz |
Motor power |
1.1KW |
1.1KW |
1.2KW |
1.5KW |
Dimension LxWxH (mm) |
1600 x800 x2000 |
1600 x800 x2400 |
1900 x900 x2900 |
1900 x900 x3200 |
weight(Kg) |
800 |
900 |
1100 |
1200 |
Model |
SK-2000 |
SK-2500 |
SK-3000 |
SK-4000 |
Max heating length(mm) |
2000 |
2500 |
3000 |
4000 |
Max heating diameter(mm) |
600 |
600 |
600 |
600 |
Max holding length(mm) |
2000 |
2500 |
3000 |
4000 |
Max weight of workpiece(Kg) |
800 |
1000 |
1200 |
1500 |
workpiece rotation speed(r/min) |
0-300 |
0-300 |
0-300 |
0-300 |
workpiece moving speed(mm/min) |
6-3000 |
6-3000 |
6-3000 |
6-3000 |
Cooling method |
Hydrojet cooling |
Hydrojet cooling |
Hydrojet cooling |
Hydrojet cooling |
Input voltage |
3P 380V 50Hz |
3P 380V 50Hz |
3P 380V 50Hz |
3P 380V 50Hz |
Motor power |
2KW |
2.2KW |
2.5KW |
3KW |
Dimension LxWxH (mm) |
1900 x900 x2400 |
1900 x900 x2900 |
1900 x900 x3400 |
1900 x900 x4300 |
weight(Kg) |
1200 |
1300 |
1400 |
1500 |
Induction Heating System for Hardening Surface Process
Specifications
Models |
Rated output power |
Frequency rage |
Input current |
Input voltage |
Duty cycle |
Water flow |
weight |
Dimension |
MFS-100 |
100KW |
0.5-10KHz |
160A |
3phase 380V 50Hz |
100% |
10-20m³/h |
175KG |
800x650x1800mm |
MFS-160 |
160KW |
0.5-10KHz |
250A |
10-20m³/h |
180KG |
800x 650 x 1800mm |
MFS-200 |
200KW |
0.5-10KHz |
310A |
10-20m³/h |
180KG |
800x 650 x 1800mm |
MFS-250 |
250KW |
0.5-10KHz |
380A |
10-20m³/h |
192KG |
800x 650 x 1800mm |
MFS-300 |
300KW |
0.5-8KHz |
460A |
25-35m³/h |
198KG |
800x 650 x 1800mm |
MFS-400 |
400KW |
0.5-8KHz |
610A |
25-35m³/h |
225KG |
800x 650 x 1800mm |
MFS-500 |
500KW |
0.5-8KHz |
760A |
25-35m³/h |
350KG |
1500 x 800 x 2000mm |
MFS-600 |
600KW |
0.5-8KHz |
920A |
25-35m³/h |
360KG |
1500 x 800 x 2000mm |
MFS-750 |
750KW |
0.5-6KHz |
1150A |
50-60m³/h |
380KG |
1500 x 800 x 2000mm |
MFS-800 |
800KW |
0.5-6KHz |
1300A |
50-60m³/h |
390KG |
1500 x 800 x 2000mm |
Applications of CNC Vertical Induction Hardening Machines:
CNC Vertical induction hardening machines are used in various industrial applications, including:
1. Steel mills: Roller shafts are used in steel mills to transport steel coils.
Induction hardening increases the lifespan of these shafts, reducing the need for frequent replacements.
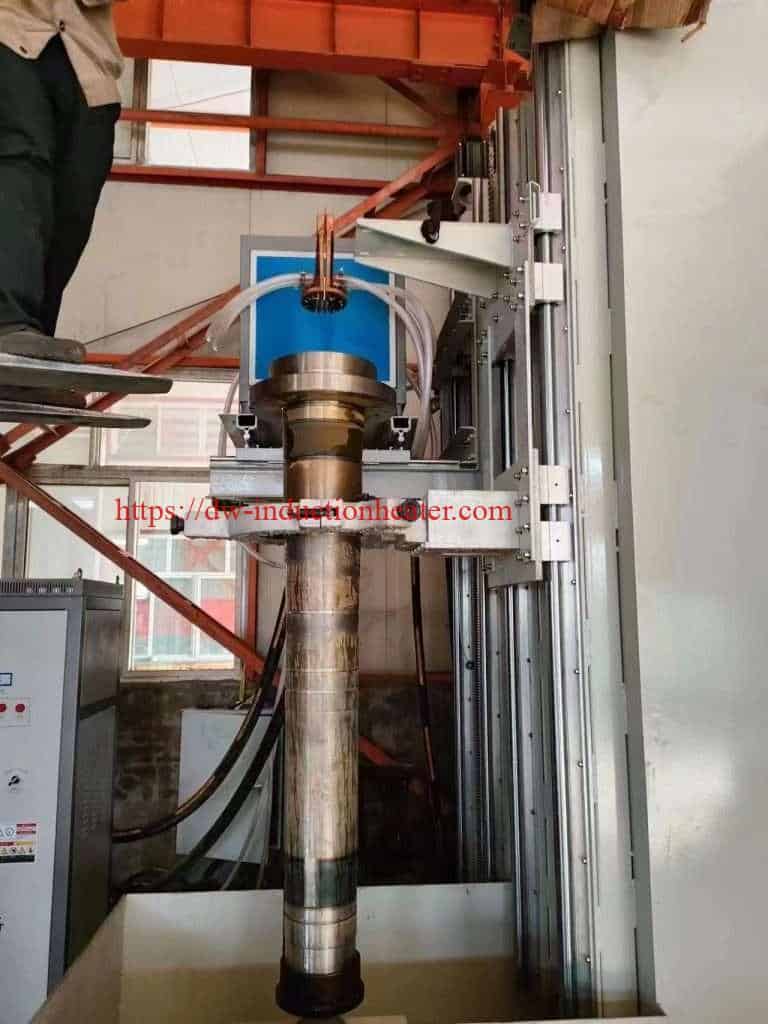
2. Paper mills: Roller shafts are used in paper mills to transport paper rolls. Induction hardening increases the lifespan of these shafts, reducing the need for frequent replacements.
3. Printing presses: Roller shafts are used in printing presses to transport paper. Induction hardening increases the lifespan of these shafts, reducing the need for frequent replacements.
4. Automotive industry: Roller shafts are used in various automotive applications, including engine components and transmission systems. Induction hardening increases the lifespan of these shafts, reducing the need for frequent replacements.
Conclusion:
CNC vertical induction quenching machines are a highly efficient and cost-effective way of heat-treating metal parts. They offer precision control, automated processes, high efficiency, and a compact design, making them an ideal choice for manufacturers who are looking to improve product quality, reduce manufacturing time, and lower operating costs. With their wide range of applications in the automotive, aerospace, and medical industries, CNC vertical induction quenching machines are a valuable addition to any manufacturing facility.
https://dw-inductionheater.com/cnc-vertical-induction-quenching-machines-for-hardening-shafts-rollers-pins-and-gears.html?feed_id=231556&_unique_id=65987e79dc3b7