Induction Curing Epoxy Adhesives: How It Works and Its Benefits.
Epoxy adhesives are an incredibly versatile and widely used type of adhesive, thanks to their strong bonding properties and ability to adhere to a range of materials. However, traditional curing methods for these adhesives can be time-consuming and require high temperatures, which can damage the materials being bonded. This is where induction curing comes in. Induction curing is a fast, efficient, and highly precise method of curing epoxy adhesives that relies on electromagnetic waves to generate heat within the adhesive itself. In this post, we'll explore how induction curing works, its benefits over traditional curing methods, and why it's an ideal solution for a wide range of industrial applications.
What is induction curing of epoxy adhesives?
Induction curing of epoxy adhesives is a process that uses high-frequency electromagnetic waves to cure the adhesive. This method is becoming increasingly popular due to the many benefits it offers. The process involves applying the adhesive to the surface and then exposing it to a high-frequency current that passes through a conductive coil. The current heats the coil, which in turn heats the adhesive through induction. This process causes the adhesive to cure quickly and evenly. One of the main advantages of induction curing is the speed at which the adhesive cures. The process can take as little as 15 seconds, making it significantly faster than other curing methods. Induction curing also has the added benefit of being able to cure epoxy adhesive in hard-to-reach areas. It is a non-contact process, so the adhesive can be cured without touching the surface. Another advantage of induction curing is that it is an energy-efficient method. The process only heats the adhesive and not the entire surface, which saves energy and time. It also creates a stronger bond than other curing methods, as the even heat distribution ensures that the adhesive cures evenly and with minimal stress. Overall, induction curing is an excellent choice for those looking to cure epoxy adhesives quickly and efficiently. The process is energy-efficient, provides a strong bond, and can reach areas that other methods cannot.
How does induction curing of epoxy adhesives work?
Induction curing is a process that is used to cure epoxy adhesives. It works by using an induction coil to create an electromagnetic field that heats up the adhesive. The adhesive is placed inside the coil, and the electromagnetic field causes the adhesive to heat up rapidly. This rapid heating causes the adhesive to cure quickly and efficiently. The process is known for being extremely fast, with curing times ranging from just a few seconds to a few minutes. The speed of induction curing makes it an excellent choice for use in high-volume production environments. Induction curing is also known for being very precise. The electromagnetic field can be precisely controlled, allowing for very accurate curing of the adhesive. This precision ensures that the adhesive is cured evenly, which is important for maintaining the strength and integrity of the bond. Another benefit of induction curing is that it is a non-contact process.
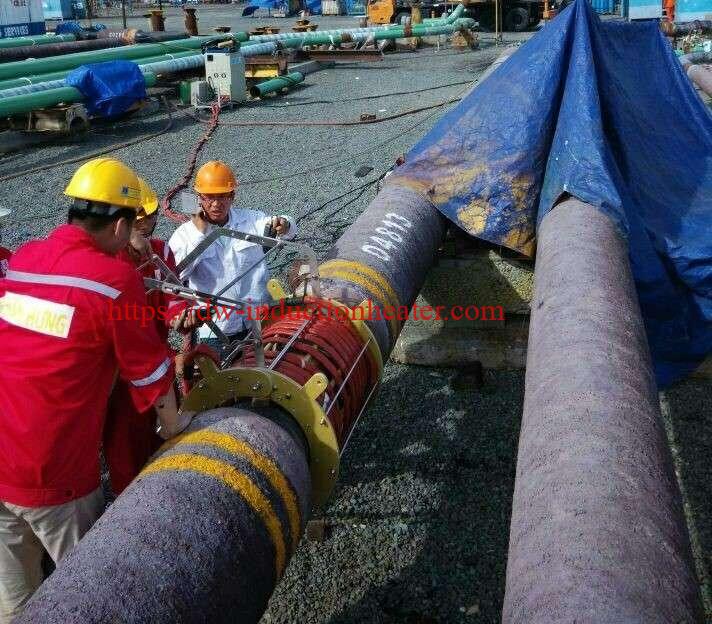
This means that there is no physical contact between the adhesive and the curing equipment, which reduces the risk of contamination. Additionally, induction curing is a very energy-efficient process, which can help to reduce operating costs. Overall, induction curing is a highly effective and efficient method for curing epoxy adhesives, offering many benefits to manufacturers and end-users alike.
Benefits of induction curing for epoxy adhesives over traditional curing methods
Induction curing is a relatively new technique that has been gaining popularity in recent years. One of the main benefits of induction curing over traditional curing methods is the speed of the process.
1) Reduced curing time: One of the most significant advantages of induction curing is its ability to cure adhesives faster than thermal curing. The electromagnetic induction method can cure epoxy adhesives in a matter of seconds, compared to the hours or days it can take using thermal curing. This results in significant time savings in the production process, leading to increased productivity and efficiency.
2) Lower energy consumption: Induction curing also requires much less energy than thermal curing since only the adhesive material is heated, rather than the entire assembly. This results in lower energy costs and reduced carbon emissions.
3) Improved mechanical properties: Researchers have found that induction curing can produce an epoxy adhesive bond with superior mechanical properties, such as adhesion and shear strength, compared to thermal curing. This is attributed to the fact that induction curing produces a more uniform and controlled curing process, resulting in a stronger bond between the adhesive and the substrates.
4) Challenges and Limitations: Despite its benefits, induction curing does have some challenges and limitations that must be addressed. One of the limitations is the need for specialized equipment to generate the electromagnetic field required for curing. This can be expensive, making it difficult for smaller manufacturers to adopt the technology. Additionally, the process is highly dependent on the adhesive and substrate properties and may not be suitable for all types of materials.
Applications of induction curing for epoxy adhesives
The use of induction curing for epoxy adhesives has numerous applications across various industries. One of the primary applications is in the automotive industry, where the quick curing time of induction curing allows for faster production rates. This is particularly useful in the production of vehicle components where epoxy adhesives are used to bond metal parts together. The ability to cure these adhesives quickly and efficiently means that production times are reduced, and vehicles can be manufactured at a lower cost. Induction curing is also used in the electronics industry, where epoxy adhesives are used to bond components together. These adhesives provide excellent protection from moisture and other environmental factors, which is critical in the production of electronic devices.

With induction curing, the curing process is completed quickly, which is vital in the fast-paced electronics industry. Another industry that benefits from induction curing for epoxy adhesives is the aerospace industry. The ability to cure adhesives quickly and efficiently is essential in the production of aircraft components. Induction curing provides a fast and reliable solution for curing epoxy adhesives, ensuring that aircraft components are produced to the highest possible standards. Overall, the applications of induction curing for epoxy adhesives are vast and varied, and it offers numerous benefits across various industries. With faster production times, improved product quality, and reduced costs, it's no wonder that more and more industries are turning to induction curing for their adhesive bonding needs.
Conclusion
Induction curing of epoxy adhesives is an innovative method of curing that has gained popularity in recent years. Unlike traditional methods, which rely on heat or UV light to cure adhesives, induction curing uses electromagnetic waves to generate heat directly within the adhesive. This results in faster, more efficient curing, and reduces the risk of damage to sensitive components. Induction curing is ideal for high-precision applications, such as electronics manufacturing, where precise control of temperature and curing time is critical. If you're looking for a reliable and efficient way to cure epoxy adhesives, induction curing may be the solution you've been searching for.
https://dw-inductionheater.com/induction-curing-epoxy-adhesives-how-it-works-and-its-benefits.html?feed_id=231676&_unique_id=659b59ac5e4e5