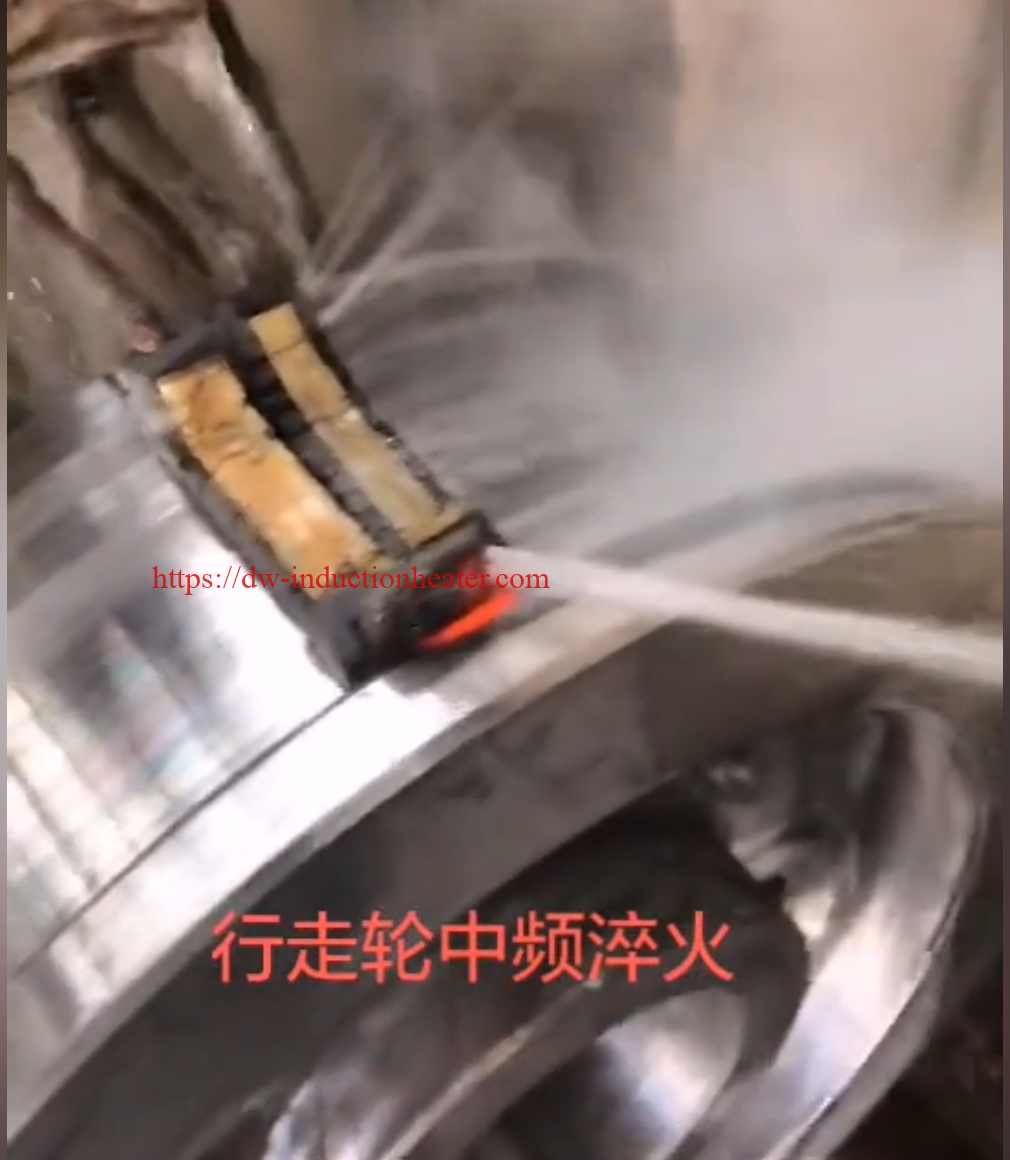
Induction Wheels Surface Hardening: The Ultimate Guide to Boosting Performance and Durability.
Induction wheel surface hardening is a process that has been used for decades to improve the performance and durability of various types of machinery.
1. What is induction wheel surface hardening?
Induction wheel surface hardening is a process that involves heating the surface of a wheel using a high-frequency induction process. This process allows the surface of the wheel to be hardened without affecting its core strength. The induction process works by passing a high-frequency electrical current through a coil that surrounds the wheel. This causes the surface of the wheel to heat up rapidly, and then quickly cool down. This rapid heating and cooling process causes the surface of the wheel to harden, resulting in increased durability, strength, and performance. Induction wheel surface hardening is commonly used in the automotive and manufacturing industries to improve the performance and durability of wheels. It can be applied to a variety of different materials, including steel, aluminum, and cast iron. The benefits of induction wheel surface hardening include increased wear resistance, improved fatigue strength, and reduced friction. This process can be customized to meet the specific needs of each application, making it an extremely versatile and effective method for improving wheel performance and durability.
2. Benefits of Induction Wheel Surface Hardening
Induction wheel surface hardening is a process that involves heating the surface of the wheel to a high temperature and then rapidly cooling it using a quenching medium. This process helps to improve the performance and durability of wheels in various industries, including automotive, aerospace, and heavy machinery. There are several benefits of induction wheel surface hardening, including increased wear resistance, improved fatigue strength, and enhanced load-carrying capacity. When the surface of the wheel is hardened using induction, it becomes more resistant to wear and tear, which means that it will last longer and require less maintenance.
3. Methods of Induction Wheel Surface Hardening
There are several methods of induction wheel surface hardening. One of the most common methods is a single-shot surface hardening process. This process involves heating the surface of the wheel to a high temperature, typically between 800 and 1000 degrees Celsius. Once the surface is heated, it is rapidly cooled to create a hard, wear-resistant surface. Another method of induction wheel surface hardening is the progressive surface hardening process. This process involves heating the surface of the wheel in stages, gradually increasing the temperature and depth of the heating as the process continues. This method allows for a more precise and controlled hardening process. A third method of induction wheel surface hardening is the pulse hardening process. This process involves heating the surface of the wheel using a series of short, intense pulses of current. The rapid heating and cooling of the surface create a hard, wear-resistant surface.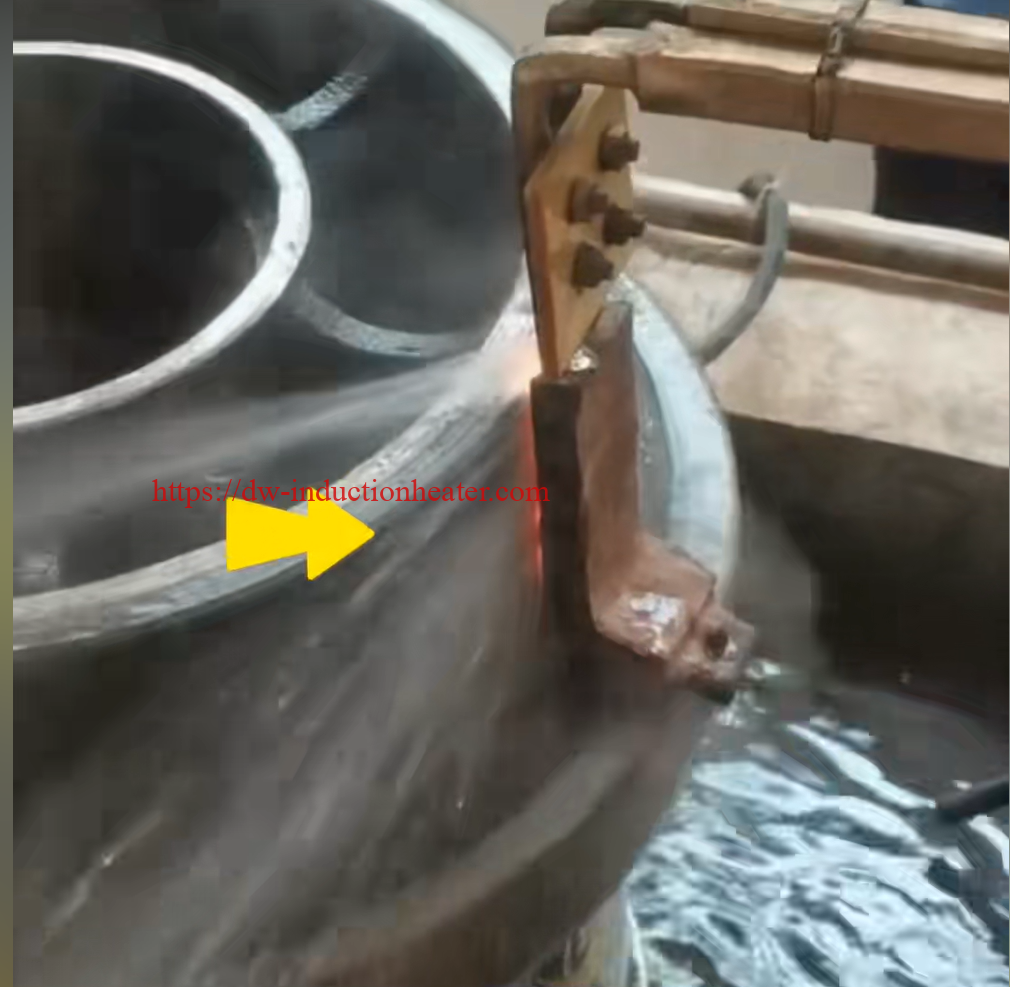
4.The Benefits of Induction Hardening for Wheels
Induction hardening offers several benefits for wheels used in different equipment. The most significant advantage is increased surface hardness, which makes the wheels more resistant to wear and tear. This, in turn, extends the life of the wheels and reduces maintenance costs. Induction hardening also improves the fatigue strength of the wheels, making them more durable and less susceptible to damage from repeated loading.
1.>Induction Hardening for Driving Wheels
Driving wheels used in heavy-duty equipment such as excavators and loaders require high traction and stability. Induction hardening improves the surface hardness of the wheel, making it more resistant to wear and tear caused by constant friction. The hardened surface layer also provides better grip and reduces slippage, improving the wheel's traction and stability. Induction hardening can also improve the fatigue strength of the wheel, making it more durable and less susceptible to damage from repeated loading.2.>Induction Hardening for Crane Wheels
Crane wheels used in material handling are subject to wear and tear caused by heavy loads. Induction hardening improves the wheel's resistance to wear and tear, making it more durable and extending its life. The hardened surface layer also reduces the risk of cracking and deformation caused by heavy loads. Induction hardening can also improve the fatigue strength of the wheel, making it more resistant to damage from repeated loading.3.>Induction Hardening for Lead and Guide Wheels
Lead and guide wheels used in rolling mills are subject to deformation caused by the rolling process. Induction hardening improves the wheel's resistance to deformation, making it more durable and extending its life. The hardened surface layer also reduces the risk of cracking and deformation caused by the rolling process. Induction hardening can also improve the fatigue strength of the wheel, making it more resistant to damage from repeated loading.5.Induction Hardening Process and Machines
The induction hardening process requires specialized equipment designed for this purpose. Induction hardening machines consist of an induction coil, a power supply, and a cooling system. The induction coil is designed to generate a magnetic field that induces an electric current in the metal part. The power supply provides the alternating current required to heat the metal, while the cooling system quenches the metal after it reaches the desired temperature. Parameters Data:Models | Rated output power | Frequency rage | Input current | Input voltage | Duty cycle | Water flow | weight | Dimension |
MFS-100 | 100KW | 0.5-10KHz | 160A | 3phase 380V 50Hz | 100% | 10-20m³/h | 175KG | 800x650x1800mm |
MFS-160 | 160KW | 0.5-10KHz | 250A | 10-20m³/h | 180KG | 800x 650 x 1800mm | ||
MFS-200 | 200KW | 0.5-10KHz | 310A | 10-20m³/h | 180KG | 800x 650 x 1800mm | ||
MFS-250 | 250KW | 0.5-10KHz | 380A | 10-20m³/h | 192KG | 800x 650 x 1800mm | ||
MFS-300 | 300KW | 0.5-8KHz | 460A | 25-35m³/h | 198KG | 800x 650 x 1800mm | ||
MFS-400 | 400KW | 0.5-8KHz | 610A | 25-35m³/h | 225KG | 800x 650 x 1800mm | ||
MFS-500 | 500KW | 0.5-8KHz | 760A | 25-35m³/h | 350KG | 1500 x 800 x 2000mm | ||
MFS-600 | 600KW | 0.5-8KHz | 920A | 25-35m³/h | 360KG | 1500 x 800 x 2000mm | ||
MFS-750 | 750KW | 0.5-6KHz | 1150A | 50-60m³/h | 380KG | 1500 x 800 x 2000mm | ||
MFS-800 | 800KW | 0.5-6KHz | 1300A | 50-60m³/h | 390KG | 1500 x 800 x 2000mm |

6. Considerations for Induction Wheel Surface Hardening
Induction wheel surface hardening is an effective way to boost the performance and durability of wheels. When considering induction wheel surface hardening, there are several factors to consider. The first factor is the type of wheels you plan to harden. Different types of wheels will require different types of hardening processes. For example, cast iron wheels will require a different hardening process than steel wheels. The second factor to consider is the depth and type of hardening required. Hardening can be done to various depths, from surface hardening to full hardening. The type of hardening required will depend on the type of wheel and the stresses it will face. The third factor to consider is the cost of the hardening process. Induction wheel surface hardening can be expensive, so you must ensure that the cost of hardening is worth it compared to the cost of replacement. Finally, it is essential to find a reputable company to perform the induction wheel surface hardening. The process requires specialized knowledge and equipment, and it is important to choose a company that has experience and a good reputation for quality work. By considering these factors, you can choose the right induction wheel surface hardening process for your wheels and ensure that you get the best performance and durability from them.Conclusion: The Importance of Induction Wheels Surface Hardening Process
Induction Wheels Surface Hardening is a process that involves heating the surface of a metal wheel using electromagnetic induction. By doing so, the surface of the wheel becomes harder, more durable, and resistant to wear and tear. This process is ideal for industries that rely on machinery with wheels that are constantly in use, such as the automotive or manufacturing industries. By using induction wheels surface hardening, you can extend the life of your machinery and reduce the need for costly repairs and replacements. So if you're looking to improve the efficiency and durability of your machinery, induction wheels surface hardening is a smart choice.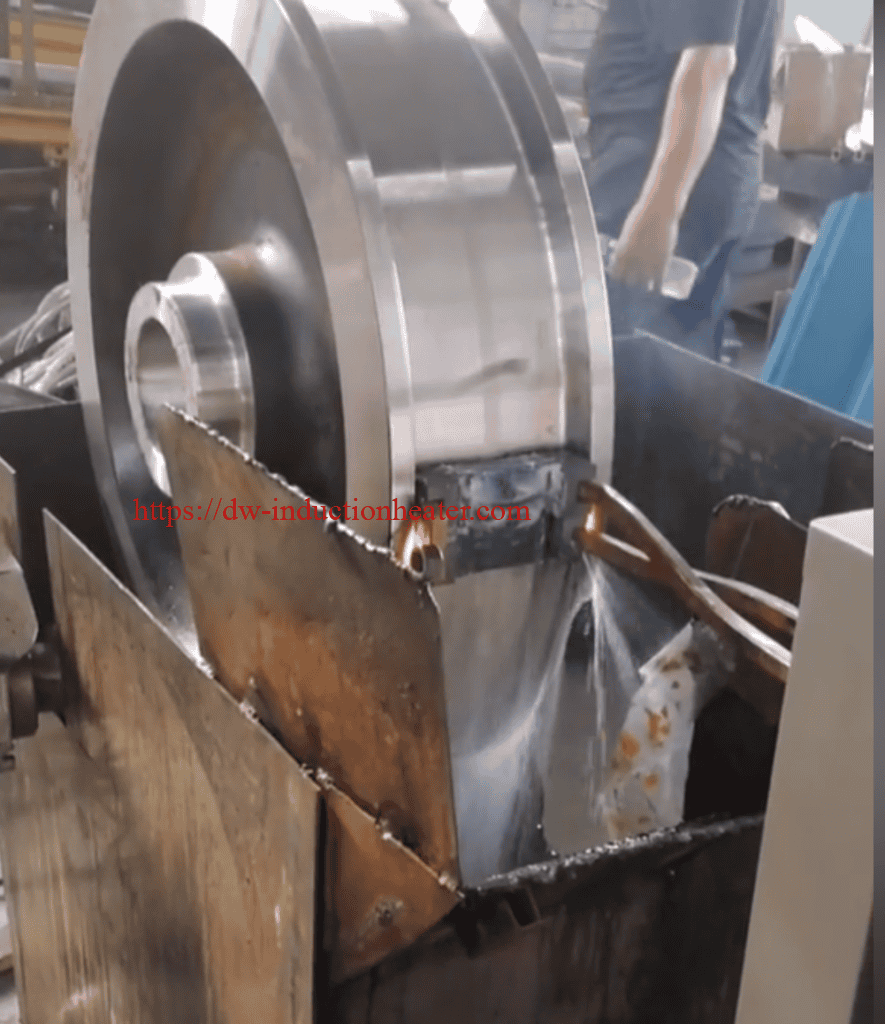