What is Induction Hardening and How Does it Work?
Induction hardening is a process used to strengthen the surface of metal parts. It involves heating the metal part through electromagnetic induction and then immediately quenching it in water or oil. This process can be used to increase the wear resistance and durability of metal components. The induction hardening process works through the use of an induction hardening machine. This machine generates a high-frequency electromagnetic field that quickly heats the metal part to a desired temperature. The heat generated is concentrated on the surface of the metal part, which allows for a rapid heating and cooling process. This process effectively hardens the outer layer of the metal part, which can improve its strength and durability. One of the primary benefits of using induction hardening machines is that it can save time and money in the manufacturing process. The process is much quicker than traditional methods of hardening, which involves heating the entire part and then cooling it slowly. Induction hardening is also more precise than other methods, as it can be controlled with accuracy, resulting in more consistent product quality. Additionally, induction hardening machines can be used to harden localized areas of a part, which allows for more flexibility in the manufacturing process. This means that manufacturers can focus on specific areas of a part that require hardening rather than hardening the entire part. This can result in significant cost savings, as well as increased efficiency in the production process. In summary, induction hardening is a process that can benefit manufacturing businesses by improving the wear resistance and durability of metal parts. The use of induction hardening machines can save time and money in the manufacturing process, as well as improve product quality and consistency.
Benefits of Induction Hardening Machines for Your Manufacturing Business
Induction hardening machines have become a popular choice for many manufacturing businesses due to their numerous benefits. One of the primary benefits of induction hardening machines is their ability to increase the wear resistance of metal components. This is achieved by rapidly heating and cooling the surface of the metal, which results in a hardened layer. This hardened layer can greatly increase the lifespan of the component and ultimately reduce the need for replacement parts. In addition to increasing wear resistance, induction hardening machines also offer increased accuracy and efficiency. These machines are capable of precisely controlling the amount of heat applied to the metal, which ensures consistent results every time. This level of accuracy can ultimately lead to a reduction in waste and an increase in productivity. Another benefit of induction hardening machines is their ability to work with a wide range of metals, including steel, aluminum, and copper. This versatility allows manufacturers to use the same machine for multiple components, further increasing efficiency and reducing costs. Finally, induction hardening machines are also environmentally friendly. Unlike traditional hardening methods, such as flame hardening, induction hardening does not produce harmful emissions or waste. This makes it a great choice for manufacturers who are looking to reduce their environmental impact. Overall, induction hardening machines offer a wide range of benefits for manufacturing businesses. From increased wear resistance to improved accuracy and efficiency, these machines can help businesses become more productive, reduce waste, and ultimately save money.
An
Induction Hardening Machine is a piece of industrial equipment used to harden metal parts. The process involves heating the metal using an electromagnetic field and then quenching it with water or oil. This results in a surface layer that is harder than the rest of the part, which can improve its durability and performance. Induction hardening machines can be used on a variety of metal parts, including gears, shafts, and bearings. They're commonly used in automotive and aerospace industries, as well as in the manufacturing of industrial machinery and equipment. If you're in need of an induction hardening machine, there are many reputable manufacturers and suppliers that can help you find the right equipment for your needs.
The Ultimate Guide to Roller Shaft Induction Hardening Machine
Roller shaft induction hardening machine is an essential tool in the manufacturing industry that is used to harden roller shafts. The process of induction hardening is the most efficient way to strengthen the surface of metal parts, including roller shafts. It provides improved wear resistance, durability, and better performance of the finished product.
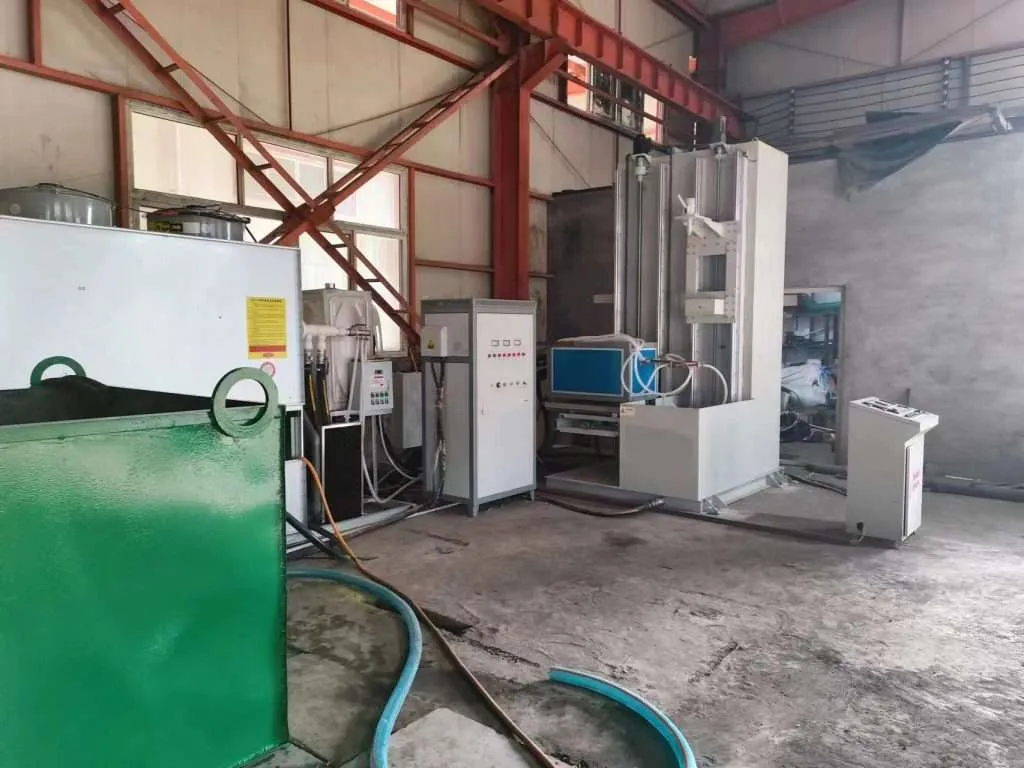
If you are in the manufacturing business, you need to understand how to use this machine to improve the quality of your products. In this article, we will provide you with an ultimate guide to roller shaft induction hardening machines. We will go over everything you need to know about the machine, how it works, its benefits, and how to maintain it so that it lasts longer. Let's dive in and learn more about this powerful tool.
1. What is a Roller Shaft Induction Hardening Machine?
A roller shaft
induction hardening machine is a piece of industrial equipment that is specifically designed to harden the surface of roller shafts. Induction hardening is a process that uses an electromagnetic field to heat the surface of a material, typically steel, to a very high temperature. This heat treatment process is used to create a hard, wear-resistant surface on the material. A roller shaft
induction hardening machine does this by using an induction coil to produce a high frequency electromagnetic field that rapidly heats the surface of the roller shaft. The heat generated by the electromagnetic field causes the surface of the roller shaft to reach a high temperature, which in turn causes the surface to harden. This process is often used in the manufacturing of roller shafts that are used in a variety of industrial applications, such as in conveyor systems or printing presses. A roller shaft induction hardening machine is an essential tool for many industrial manufacturers who require strong and durable roller shafts for their machinery.
2. How Does Roller Shaft Induction Hardening Machine Work?
The roller shaft induction hardening machine is an innovative technology that is used to produce high-quality roller shafts. This machine uses an induction heating process that heats the surface of the roller shaft to a high temperature, hardening the surface of the material while leaving the core of the roller shaft untouched. This process is known as induction hardening, and it is a popular method for producing durable and long-lasting roller shafts. The roller shaft induction hardening machine works by using an electromagnetic field to generate heat, which is applied to the surface of the roller shaft.
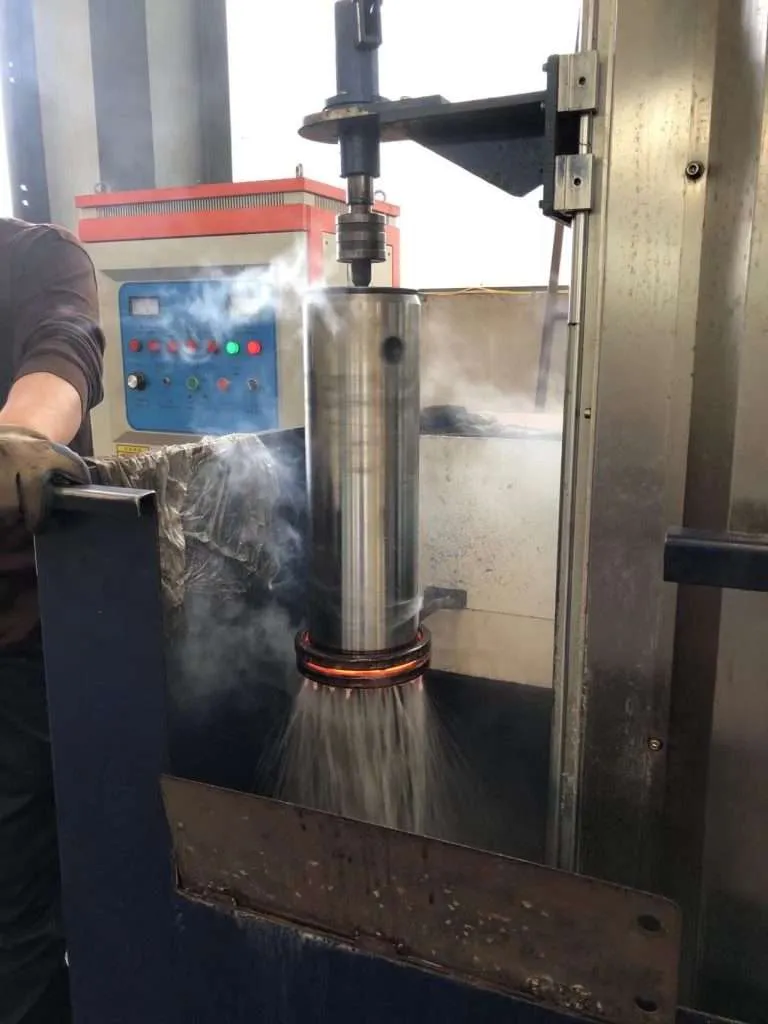
The heat generated causes the surface of the roller shaft to reach a specific temperature, which then hardens the material. This process is achieved through a combination of the electromagnetic field and the material's properties, which allows for precise control over the heating process. The roller shaft induction hardening machine is an efficient and cost-effective way to produce high-quality roller shafts. It is widely used in the manufacturing industry, particularly in the production of conveyor belts, printing presses, and other industrial equipment that requires durable and reliable roller shafts. With the ability to produce roller shafts that can withstand heavy loads and harsh environments, the roller shaft induction hardening machine is a valuable asset for any manufacturing company looking to produce high-quality products.
3. Benefits of Using Roller Shaft Induction Hardening Machine
Roller shaft induction hardening machines have become increasingly popular due to their many benefits. One of the most notable benefits is that they provide a quick and efficient hardening process for roller shafts. With this technology, roller shafts can be hardened in a matter of seconds, which greatly reduces production time and increases efficiency. Additionally, the machines are very versatile and can accommodate a variety of roller shaft sizes. This means that businesses can adapt and customize their production processes to meet their specific needs. Another benefit of using a roller shaft induction hardening machine is that it provides a uniform hardening pattern across the entire roller shaft surface. This ensures that the quality of the hardened surface is consistent and reliable throughout the entire production process. Additionally, the process of induction hardening is environmentally friendly, as it only requires a minimal amount of energy to operate. It also produces less waste and pollution compared to other traditional hardening processes. Furthermore, using a roller shaft induction hardening machine can also help to extend the lifespan of the roller shafts, reducing the need for frequent repairs and replacements. This ultimately saves businesses money and increases their overall productivity. Finally, the machine provides a safe and reliable hardening process, with minimal risk of injury to operators. Overall, the benefits of using a roller shaft induction hardening machine make it a valuable investment for businesses looking to improve their production processes and reduce their environmental impact.
4. How to Maintain Your Roller Shaft Induction Hardening Machine?
Maintaining your roller shaft induction hardening machine is crucial to ensure its longevity and continued performance.
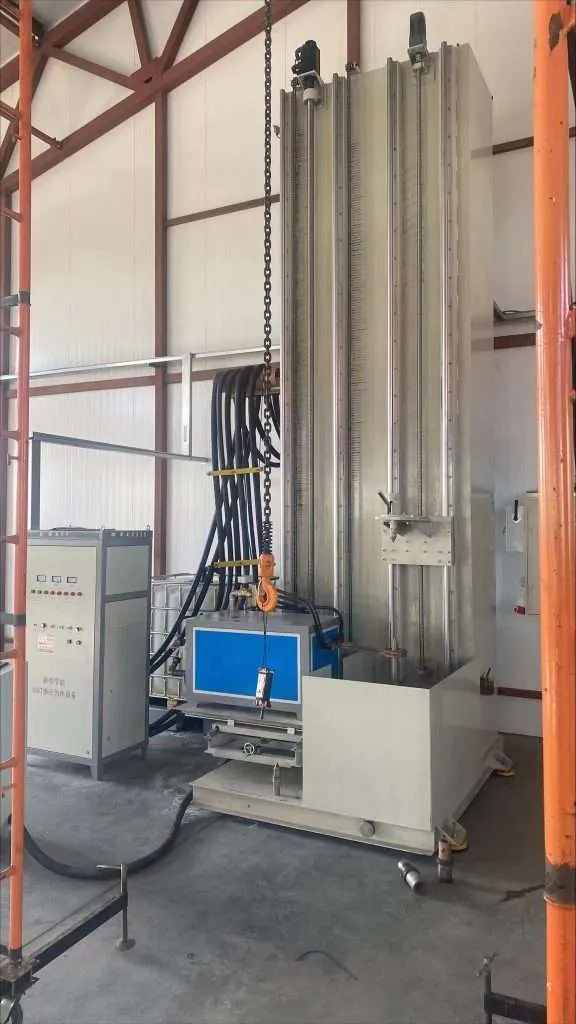
Here are some tips to keep your machine running smoothly:
1. Regular cleaning: Dust and debris can accumulate on your machine, which can cause damage over time. It's essential to clean your machine regularly to prevent any build-up. Use a soft cloth to wipe down the machine and remove any dirt or debris.
2. Lubrication: Proper lubrication is essential to keep your machine functioning correctly. Make sure to use the recommended lubricant and apply it regularly to the appropriate parts of the machine.
3. Regular inspection: Inspecting your machine regularly can help you identify any potential issues before they become bigger problems. Look for signs of wear and tear, such as cracks or deformation in the rollers.
4. Proper storage: When not in use, it's essential to store your machine properly. Keep it in a dry, cool place that is free from any exposure to moisture or extreme temperatures.
5. Professional maintenance: While regular cleaning and inspection can help prevent issues, it's also crucial to have your machine professionally serviced regularly.
A professional technician can identify any potential problems and provide the necessary repairs and maintenance to keep your machine running smoothly. By following these tips, you can ensure that your roller shaft induction hardening machine remains in top condition, providing you with reliable and efficient performance for years to come.
Hardening Machine Tools-Quenching Machine Tools
According to the different of workpiece, there are vertical type, horizontal type,closed type, customized type, etc.
1.Standard SK-500/1000/1200/1500 workpiece moving type For shafts, discs, pins and gears hardening
2.SK-2000/2500/3000/4000 Transformer moving type , Used for heating length more than 1500mm shaft
3.Closed type : Customized for big shaft ,More clean work environment.
4.Horizontal hardening machine tool
SK-500/1000/1200/1500/2000/2500/3000/4000 Used for smooth shaft
5.Customized type
Technical Parameter
Model |
SK-500 |
SK-1000 |
SK-1200 |
SK-1500 |
Max heating length(mm) |
500 |
1000 |
1200 |
1500 |
Max heating diameter(mm) |
500 |
500 |
600 |
600 |
Max holding length(mm) |
600 |
1100 |
1300 |
1600 |
Max weight of workpiece(Kg) |
100 |
100 |
100 |
100 |
Workpiece rotation speed(r/min) |
0-300 |
0-300 |
0-300 |
0-300 |
workpiece moving speed(mm/min) |
6-3000 |
6-3000 |
6-3000 |
6-3000 |
Cooling method |
Hydrojet cooling |
Hydrojet cooling |
Hydrojet cooling |
Hydrojet cooling |
Input voltage |
3P 380V 50Hz |
3P 380V 50Hz |
3P 380V 50Hz |
3P 380V 50Hz |
Motor power |
1.1KW |
1.1KW |
1.2KW |
1.5KW |
Dimension LxWxH (mm) |
1600 x800 x2000 |
1600 x800 x2400 |
1900 x900 x2900 |
1900 x900 x3200 |
weight(Kg) |
800 |
900 |
1100 |
1200 |
Model |
SK-2000 |
SK-2500 |
SK-3000 |
SK-4000 |
Max heating length(mm) |
2000 |
2500 |
3000 |
4000 |
Max heating diameter(mm) |
600 |
600 |
600 |
600 |
Max holding length(mm) |
2000 |
2500 |
3000 |
4000 |
Max weight of workpiece(Kg) |
800 |
1000 |
1200 |
1500 |
workpiece rotation speed(r/min) |
0-300 |
0-300 |
0-300 |
0-300 |
workpiece moving speed(mm/min) |
6-3000 |
6-3000 |
6-3000 |
6-3000 |
Cooling method |
Hydrojet cooling |
Hydrojet cooling |
Hydrojet cooling |
Hydrojet cooling |
Input voltage |
3P 380V 50Hz |
3P 380V 50Hz |
3P 380V 50Hz |
3P 380V 50Hz |
Motor power |
2KW |
2.2KW |
2.5KW |
3KW |
Dimension LxWxH (mm) |
1900 x900 x2400 |
1900 x900 x2900 |
1900 x900 x3400 |
1900 x900 x4300 |
weight(Kg) |
1200 |
1300 |
1400 |
1500 |
Induction Heating System for Hardening Surface Process
Specifications
Models |
Rated output power |
Frequency rage |
Input current |
Input voltage |
Duty cycle |
Water flow |
weight |
Dimension |
MFS-100 |
100KW |
0.5-10KHz |
160A |
3phase 380V 50Hz |
100% |
10-20m³/h |
175KG |
800x650x1800mm |
MFS-160 |
160KW |
0.5-10KHz |
250A |
10-20m³/h |
180KG |
800x 650 x 1800mm |
MFS-200 |
200KW |
0.5-10KHz |
310A |
10-20m³/h |
180KG |
800x 650 x 1800mm |
MFS-250 |
250KW |
0.5-10KHz |
380A |
10-20m³/h |
192KG |
800x 650 x 1800mm |
MFS-300 |
300KW |
0.5-8KHz |
460A |
25-35m³/h |
198KG |
800x 650 x 1800mm |
MFS-400 |
400KW |
0.5-8KHz |
610A |
25-35m³/h |
225KG |
800x 650 x 1800mm |
MFS-500 |
500KW |
0.5-8KHz |
760A |
25-35m³/h |
350KG |
1500 x 800 x 2000mm |
MFS-600 |
600KW |
0.5-8KHz |
920A |
25-35m³/h |
360KG |
1500 x 800 x 2000mm |
MFS-750 |
750KW |
0.5-6KHz |
1150A |
50-60m³/h |
380KG |
1500 x 800 x 2000mm |
MFS-800 |
800KW |
0.5-6KHz |
1300A |
50-60m³/h |
390KG |
1500 x 800 x 2000mm |
Applications of Roller Shaft Induction Hardening Machines:
Roller shaft induction hardening machines are used in various industrial applications, including:
1. Steel mills: Roller shafts are used in steel mills to transport steel coils.
Induction hardening increases the lifespan of these shafts, reducing the need for frequent replacements.
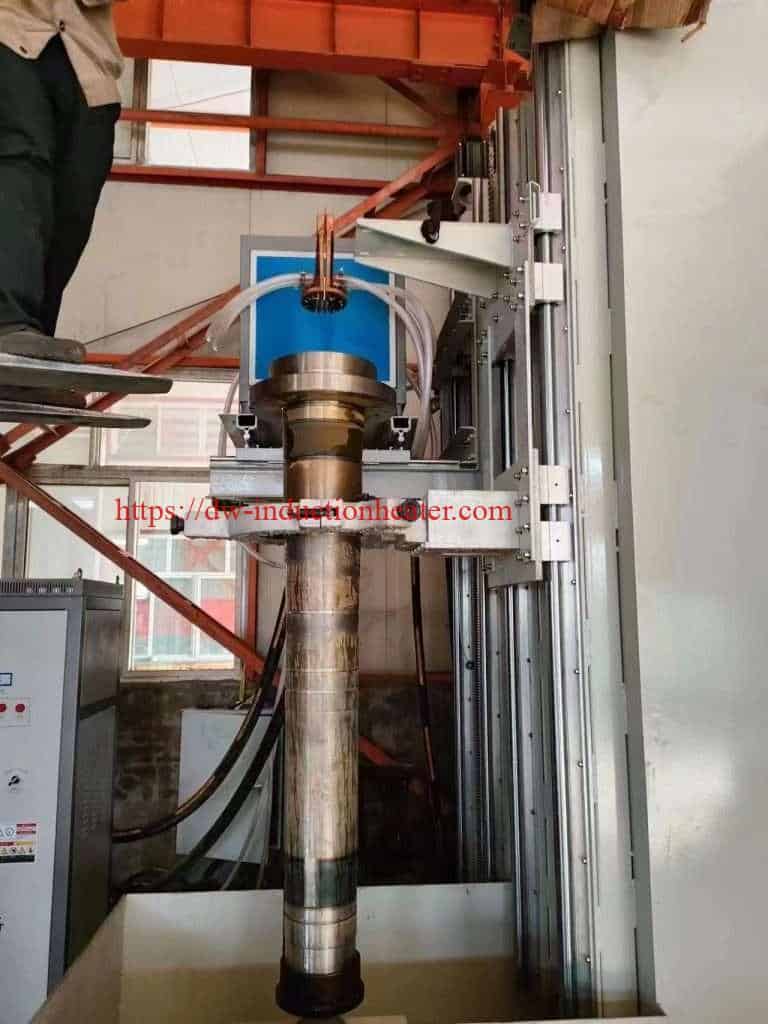
2. Paper mills: Roller shafts are used in paper mills to transport paper rolls. Induction hardening increases the lifespan of these shafts, reducing the need for frequent replacements.
3. Printing presses: Roller shafts are used in printing presses to transport paper.
Induction hardening increases the lifespan of these shafts, reducing the need for frequent replacements.
4. Automotive industry: Roller shafts are used in various automotive applications, including engine components and transmission systems. Induction hardening increases the lifespan of these shafts, reducing the need for frequent replacements.
Conclusion:
An
induction hardening machine is a specialized equipment used in the manufacturing industry for hardening metal parts. It utilizes induction heating technology to heat the surface of a metal part to a high temperature before quickly cooling it off. This process enhances the surface hardness of the metal, making it more durable and resistant to wear and tear. Induction hardening machines come in different sizes, shapes, and power outputs, depending on the specific needs of the application. They can also be customized to suit the unique requirements of a particular manufacturing process.
https://dw-inductionheater.com/how-induction-hardening-machines-can-benefit-your-manufacturing-business.html?feed_id=231586&_unique_id=6599356c087e2