Maximizing Efficiency of Induction Heating for Thermal Fluid Pipelines
Induction thermal fluid heating pipeline technology is quickly gaining popularity in the oil and gas industry due to its energy efficiency and lower operating costs compared to traditional heating methods. This technology provides a means to heat fluid in pipelines and tanks without the need for direct heating elements or fuel combustion. In this article, I will explore the benefits of using magnetic induction heating for pipeline heating, the types of induction heaters available, how to select the right one for your pipeline, installation process, maintenance and repair, cost analysis, a case study of successful implementation, and the future of induction heating technology.
Introduction to Induction Heating for Thermal Fluid Pipelines
Induction heating is a process of heating a metallic material by inducing an electric current through it. When a magnetic field is created around the material, eddy currents are produced within the material, causing it to heat up. This technology has been used in various industries, including manufacturing, automotive, and aerospace, for heating and hardening metals.
In the oil and gas industry, induction heating has been applied to pipeline heating for the transportation of thermal fluids such as crude oil, natural gas, and various chemicals. Thermal fluid pipelines require consistent heating to maintain the fluid's viscosity and prevent it from solidifying or becoming too viscous to pump. Traditional heating methods such as steam or hot oil have been used for decades, but their inefficiency and high cost have made them unsustainable. Magnetic induction heating has become a more viable alternative, providing a more efficient and cost-effective solution for pipeline heating.
Understanding the Concept of Magnetic Induction Heating
Magnetic induction heating uses an alternating magnetic field to heat a metallic material. When a metallic material is exposed to a magnetic field, it generates eddy currents, which produce heat. The amount of heat produced is determined by the material's electrical conductivity, magnetic permeability, and the strength of the magnetic field.
In pipeline heating, induction heating is achieved by wrapping a coil around the pipe and passing an alternating current through it. The electrical current produces a magnetic field that induces eddy currents within the pipe, heating it up. The heat is then transferred to the fluid inside the pipe through conduction, maintaining the fluid's temperature.

Benefits of Using Magnetic Induction Heating for Pipeline Heating
Magnetic induction heating offers several advantages over traditional heating methods for pipeline heating. First, it is a more efficient process, with up to 90% of the energy used being converted into heat. In contrast, traditional heating methods such as steam or hot oil have an energy conversion efficiency of 30-50%.
Second, magnetic induction heating provides a more precise and consistent heating process. The heat is generated directly within the pipe, ensuring that the fluid is heated uniformly throughout the pipeline. Traditional heating methods are often affected by heat loss, resulting in uneven heating and temperature fluctuations.
Third, magnetic induction heating is a safer process. There is no need for open flames, hot oil, or pressurized steam, reducing the risk of accidents and injuries. Additionally, the process is environmentally friendly, with no emissions or waste products.
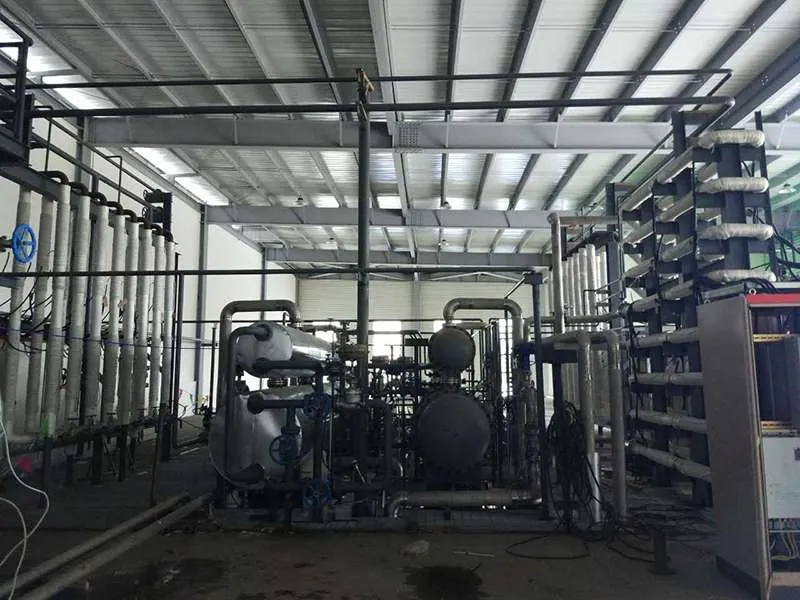
Types of Induction Heaters for Pipeline Heating
There are two types of induction heaters used for pipeline heating: high-frequency induction heaters and low-frequency induction heaters.
High-frequency induction heaters are used for small diameter pipes, typically less than 6 inches in diameter. They operate at a frequency of 10 kHz to 400 kHz, producing a shallow but intense heating effect. They are ideal for heating thin-walled pipes and for applications where precise control is required.
Low-frequency induction heaters are used for larger diameter pipes, typically greater than 6 inches in diameter. They operate at a frequency of 1 kHz to 10 kHz, producing a deeper but less intense heating effect. They are ideal for heating thick-walled pipes and for applications where high power is required.
How to Select the Right Induction Heater for Your Pipeline
Selecting the right
induction heater for your pipeline depends on several factors, including the pipe diameter, wall thickness, and length, the fluid to be transported, the required temperature, and the power source available.
For small diameter pipes, high-frequency induction heaters are ideal, while low-frequency induction heaters are suitable for larger diameter pipes. The heater's power output should be sufficient to meet the required heating demand, and the heating process should be controlled to ensure uniform heating and temperature control.
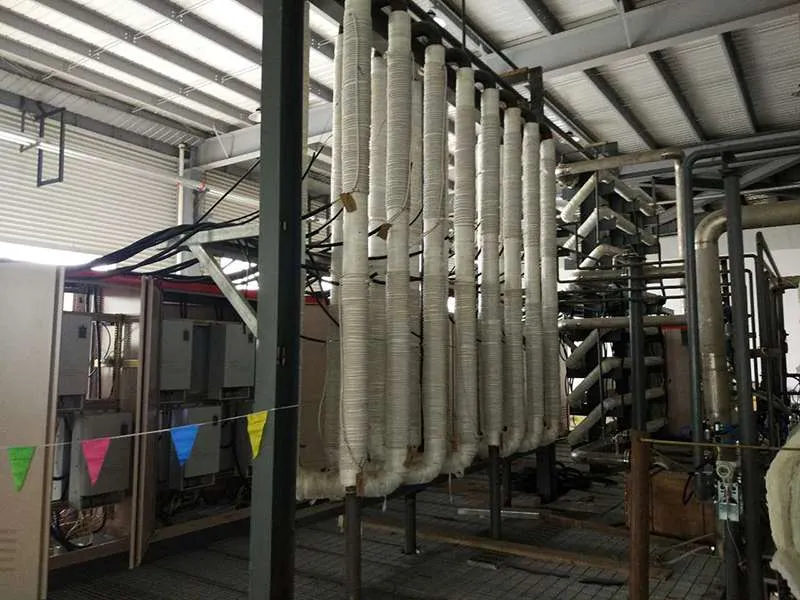
Installation Process for Magnetic Induction Heaters
The installation process for magnetic induction heaters is straightforward. The heater is wrapped around the pipe, and the power supply is connected to the coil. The pipe's insulation is then installed over the heater to prevent heat loss and protect the pipeline from external elements.
The installation process can be completed quickly, with minimal downtime, and the heater can be easily removed and reinstalled if required.
Maintenance and Repair of Induction Heating Systems
Induction heating systems are low maintenance and require minimal repairs. Routine maintenance includes checking the power supply, inspecting the coils for any damage or wear, and ensuring that the insulation is intact. Repairs are rare but may be required if the coil is damaged or the power supply fails.
Cost Analysis of Using Induction Heating for Pipeline Heating
The cost of using
magnetic induction heating for pipeline heating is lower than traditional heating methods. The process is more efficient, reducing energy consumption and costs. Additionally, the installation process is quick and easy, minimizing downtime and labor costs.
The initial investment in an induction heating system may be higher than traditional heating methods, but the long-term cost savings outweigh the initial investment. Induction heating systems have a longer lifespan, require less maintenance, and provide a more consistent and precise heating process.
Case Study: Successful Implementation of Magnetic Induction Heating for Pipeline Heating
A major oil and gas company implemented magnetic induction heating for pipeline heating, resulting in significant cost savings and improved efficiency. The company had been using steam heating for pipeline heating, which was expensive and inefficient.
After implementing magnetic induction heating, the company reduced its energy consumption by 50%, resulting in an annual cost savings of $500,000. The heating process was more precise, ensuring consistent heating throughout the pipeline, resulting in improved product quality and reduced downtime.
Future of Induction Heating Technology
The future of induction heating technology is promising, with ongoing research and development focused on improving efficiency and reducing costs. New advancements in technology are focused on improving the power output and heating efficiency of induction heaters, reducing installation costs, and improving the reliability of the heating process.
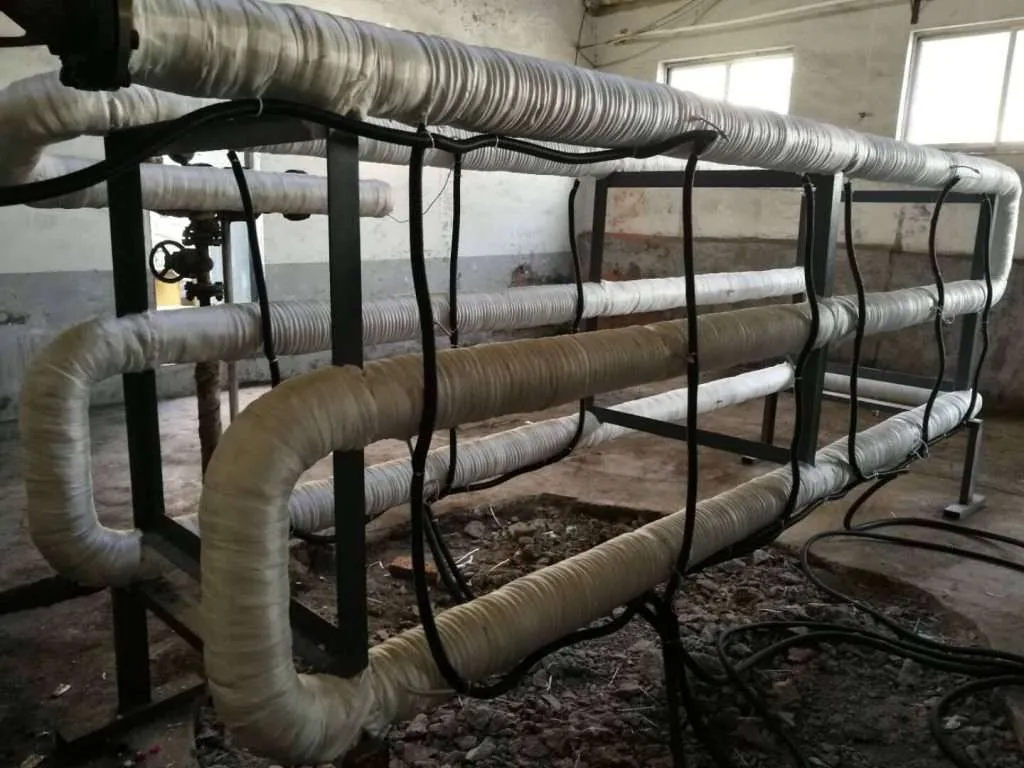
Conclusion
Magnetic induction heating has revolutionized the oil and gas industry by providing a more efficient, cost-effective, and safer solution for pipeline heating. The benefits of using magnetic induction heating are numerous, including improved efficiency, precise and consistent heating, and reduced downtime. The technology is environmentally friendly, and the cost savings outweigh the initial investment. As technology continues to advance, the future of induction heating technology is promising, with ongoing research and development focused on improving efficiency and reducing costs. If you are considering pipeline heating, magnetic induction heating is a viable and efficient solution to consider.
CTA: For more information on magnetic induction heating for pipeline heating, contact us today.
https://dw-inductionheater.com/maximizing-efficiency-of-induction-heating-for-thermal-fluid-pipelines.html?feed_id=232435&_unique_id=65a8eb3883989