Induction Brazing Copper Lap Joints: A Reliable and Efficient Joining Method
Induction brazing copper lap joints is a highly effective method for joining copper components with precision and strength. The process involves using an
induction heating system to generate heat directly within the copper material, allowing for a localized and controlled heating of the joint area. The brazing filler metal, typically a copper-based alloy, is then introduced to the heated joint, melting and flowing into the gap to create a strong, durable bond. Induction brazing offers several benefits including rapid heating, minimal distortion, and the ability to join dissimilar metals. If you are looking for a reliable and efficient method to braze copper lap joints, induction brazing is the way to go.
1. The Advantages of Induction Brazing Copper Lap Joints
1.1. Precise Heat Control: Induction brazing allows for precise and localized heating, minimizing the risk of thermal damage to the surrounding areas. This is especially important when working with sensitive copper components or assemblies with complex geometries.
1.2. Increased Efficiency: Induction heating is fast and efficient, as it directly heats the workpiece without the need for preheating the entire assembly. This results in reduced energy consumption, shorter cycle times, and increased productivity.
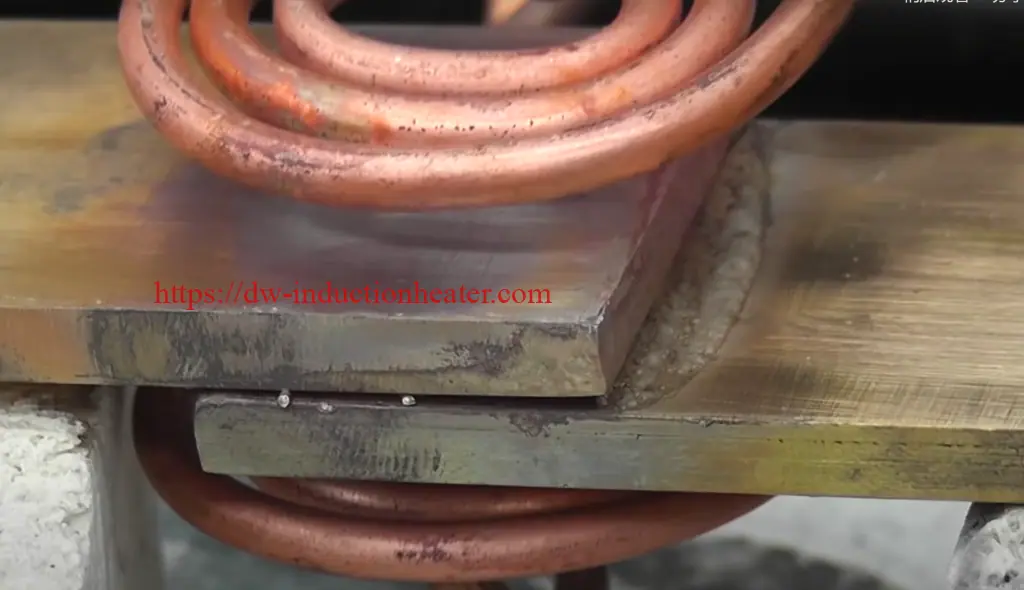
1.3. Stronger Joints: Induction brazing produces high-quality joints with excellent bond strength. The controlled heating process ensures uniform heating and proper filler metal flow, resulting in robust and reliable connections.
1.4. Clean and Environmentally Friendly: Induction brazing eliminates the need for open flames or torches, minimizing the risk of contamination and creating a safer working environment. Additionally, it reduces the generation of harmful fumes and pollutants, making it an eco-friendly choice.
2. The Induction Brazing Process for Copper Lap Joints
2.1. Preparation: Thoroughly clean the copper surfaces to remove any contaminants, such as dirt, grease, or oxide layers. This ensures optimal bonding and prevents defects in the joint.
2.2. Filler Metal Selection: Choose a brazing filler metal that is compatible with copper and suitable for your specific application. Silver-based alloys, such as silver-copper-phosphorus, or copper-phosphorus alloys are commonly used for copper brazing.
2.3. Joint Assembly: Position the copper parts in a lap joint configuration, ensuring a close fit. Fixtures or clamps can be used to secure the parts during the brazing process.
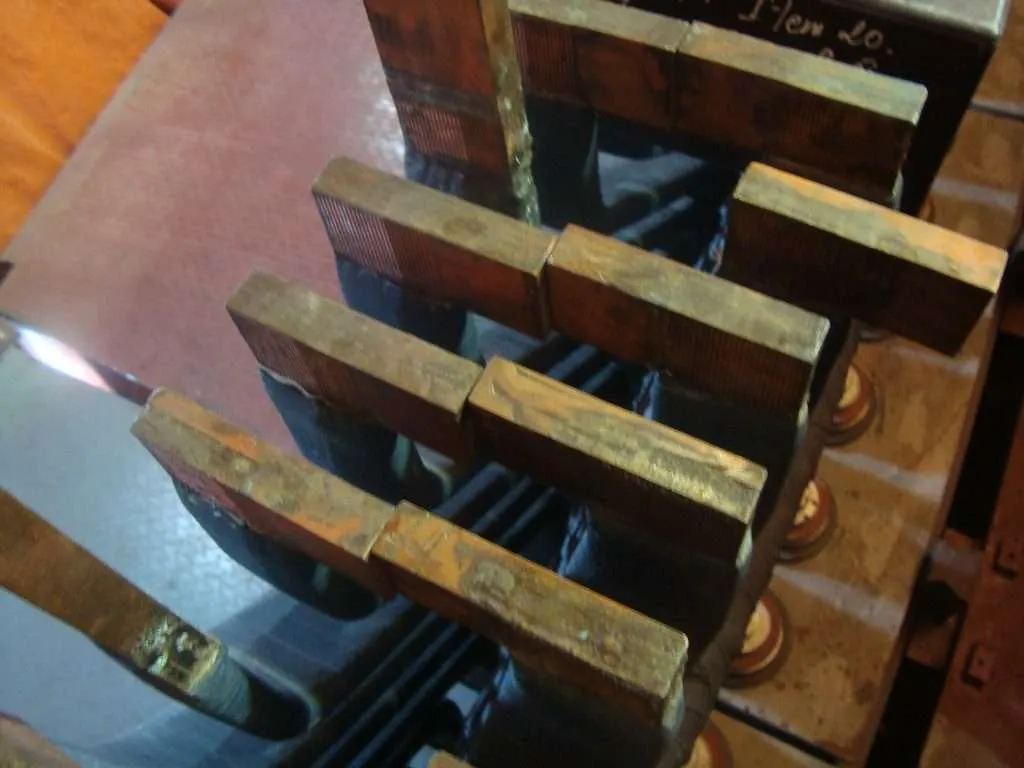
2.4. Flux Application: Apply a suitable flux to the joint area. The flux removes oxide layers, promotes wetting of the filler metal, and prevents oxidation during heating. Select a flux specifically formulated for brazing copper.
2.5. Induction Heating: Position the copper assembly within the induction coil, ensuring the joint area is within the heating zone. Adjust the induction heating system's power, frequency, and parameters based on manufacturer guidelines and the size/thickness of the copper parts.
2.6. Filler Metal Introduction: Once the joint area reaches the brazing temperature, introduce the filler metal. It can be in the form of a pre-placed filler wire or applied directly as a brazing paste or powder. The heat from the induction process melts the filler metal, allowing it to flow into the joint.
2.7. Cooling and Cleaning: After the filler metal has completely filled the joint, switch off the power and allow the joint to cool naturally. Once cooled, remove any residual flux or oxide from the brazed joint using appropriate cleaning methods.
3. Applications of Induction Brazing Copper Lap Joints
3.1. Electrical and Electronics Industry: Induction brazing is widely used in manufacturing electrical connectors, motor windings, transformers, and various electronic components that require reliable electrical conductivity and mechanical strength.

3.2. HVAC and Refrigeration: Copper tube connections in air conditioning, refrigeration, and heat exchanger systems often employ
induction brazing for its efficiency, accuracy, and consistent quality.
3.3. Automotive and Aerospace: Induction brazing is utilized in the production of automotive heat
exchangers, fuel systems, and aerospace components, ensuring reliable performance under demanding conditions.
3.4. Plumbing and Pipe Fittings: Copper plumbing fittings, valves, and pipe joints can be efficiently and effectively brazed using induction, providing leak-free connections and extended service life.
Conclusion
Induction brazing copper lap joints is a highly efficient and effective method of joining two copper pieces together. The process involves using an induction heating system to heat the joint area, melting a filler metal, and creating a strong bond between the copper pieces. This technique offers several advantages, including precise and localized heating, minimal distortion, and faster heating cycles. Induction brazing also ensures a clean and contamination-free joint, resulting in superior quality and strength. Whether you require brazing for plumbing, electronics, or any other copper applications, our skilled technicians are ready to provide reliable and durable solutions. Trust our expertise in induction brazing copper lap joints for a seamless and robust joining process that meets your specific needs.
https://dw-inductionheater.com/induction-brazing-copper-lap-joints-a-reliable-and-efficient-joining-method.html?feed_id=231466&_unique_id=65967e5a9fb68