Induction Thermal Fluid Pipeline Heater
Conventional heating methods, like boilers and hot press machines that burn coal, fuel or other material, usually come with drawbacks such as low heating efficiency, high cost, complex maintenance procedures, pollution, and hazardous work environment. Induction heating effectively addressed those problems. It has the following advantages:
-High heat efficiency; Save more energy;
-Fast temperature ramp-up;
-Digital software control gives accurate control over the temperature and the whole heating process;
-Highly reliable;
-Easy installation and maintenance;
-Lower operation and maintenance cost.
HLQ Induction Heating Equipment is designed for Pipeline, Vessel, Heat Exchanger, Chemical Reactor and Boiler. The vessels transfers heat to the fluid materials like Industrial Water, Oil, Gas, Food Material and Chemical Raw Materials heating. Heating Power size 2.5KW-100KW is the air cooled ones. Power size 120KW-600KW is the water cooled ones. For some on site chemical material reactor heating, We will supply the heating system with Explosion Proof Configuration and Remote Control System.
This HLQ heating system consists induction heater,
induction coil, temperature control system, thermal couple and insulation materials. Our company provides installation and commissioning scheme. The user can install and debug by yourself. We can also provide on-site installation and commissioning. The key of power selection of fluid heating equipment is the calculation of heat and heat exchange area.
HLQ Induction Heating Equipment 2.5KW-100KW air cooled and 120KW-600KW water cooled.
Energy Efficiency Comparison
Heating method |
Conditions |
Power consumption |
Induction heating |
Heating 10 liters of water up to 50ºC |
0.583kWh |
Resistance heating |
Heating 10 liters of water up to 50ºC |
0.833kWh |
Comparison between Induction Heating and Coal/Gas/Resistance Heating
Items |
Induction heating |
Coal-fired heating |
Gas-fired heating |
Resistance heating |
Heating efficiency |
98% |
30-65% |
80% |
Below 80% |
Pollutant emissions |
No noise, no dust, no exhaust gas, no waste residue |
Coal cinders, smoke, carbon dioxide, sulfur dioxide |
Carbon dioxide, sulfur dioxide |
Non |
Fouling (pipe wall) |
Non-fouling |
Fouling |
Fouling |
Fouling |
Water softener |
Depending on the quality of fluid |
Required |
Required |
Required |
Heating stability |
Constant |
Power is decreased by 8% yearly |
Power is decreased by 8% yearly |
Power is decreased by more than 20% yearly (high power consumption) |
Safety |
Electricity and water separation, no electricity leakage, no radiation |
Risk of carbon monoxide poisoning |
Risk of carbon monoxide poisoning and exposure |
Risk of electricity leakage, electric shock or fire |
Durability |
With core design of heating, 30 years service life |
5 years |
5 to 8 years |
Half to one year |
Diagram
Induction Heating Power Calculation
Required parameters of parts to be heated: specific heat capacity, weight, starting temperature and end temperature, heating time;
Calculation formula: specific heat capacity J/(kg*ºC)×temperature differenceºC×weight KG ÷ time S = power W
For example, to heat thermal oil of 1 ton from 20ºC to 200ºC within an hour, the power calculation is as follows:
Specific heat capacity: 2100J/(kg*ºC)
Temperature difference: 200ºC-20ºC=180ºC
Weight: 1ton=1000kg
Time: 1 hour=3600 seconds
i.e. 2100 J/ (kg*ºC)×(200ºC -20 ºC)×1000kg ÷3600s=105000W=105kW
Conclusion
The theoretical power is 105kW, but the actual power is commonly increased by 20% because of taking the heat loss into consideration, that is, the actual power is 120kW. Two sets of 60kW induction heating system as a combination are required.
Induction Thermal Fluid Pipeline Heater
Advantages of using the
Induction Fluid Pipeline Heater:
Precise control of the working temperature, low maintenance cost and the possibility to heat any type of fluid to any temperature and pressure are some of the advantages presented by the Inductive Electrothermal
Induction Heating Generator (or Inductive Heater for fluids) manufactured by HLQ.
Using the principle of magnetic induction heating, in the Inductive Heater for fluids heat is generated in the walls of a spiral of stainless steel tubes. The fluid that circulates through these tubes removes that heat, which is used in the process.
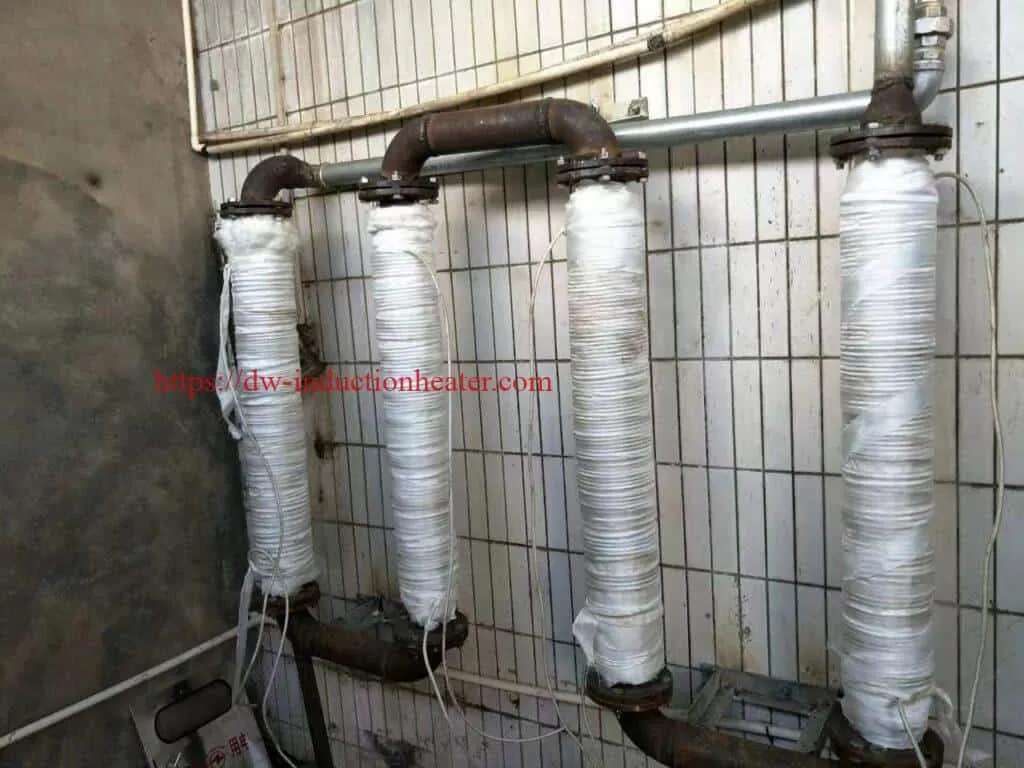
These advantages, combined with a specific design for each customer and the unique durability properties of stainless steel, make the Inductive Heater for fluids practically maintenance-free, with no need to change any heating element during its useful life. . The Inductive Heater for fluids allowed heating projects that were not viable by other electrical means or not, and hundreds of them are already in use.
The Induction Pipeline Heater for fluids, in spite of using electrical energy to generate heat, in many applications presented itself as a more advantageous option than operating heating systems with fuel oil or natural gas, mainly due to the inefficiency inherent in the generation systems combustion heat and the need for constant maintenance.
Advantages:
In summary, the Inductive Electrothermal Heater has the following advantages:
- System works dry and is naturally cooled.
- Precise control of the working temperature.
- Almost immediate availability of heat when energizing the Inductive Heater, due to its very low thermal inertia, eliminating the long heating periods necessary for other heating systems to reach the regime temperature.
- High efficiency with consequent energy savings.
- High power factor (0.96 to 0.99).
- Operation with high temperatures and pressures.
- Elimination of heat exchangers.
- Total operational security due to the physical separation between the heater and the electrical network.
- Maintenance cost practically non-existent.
- Modular installation.
- Quick responses to temperature variations (low thermal inertia).
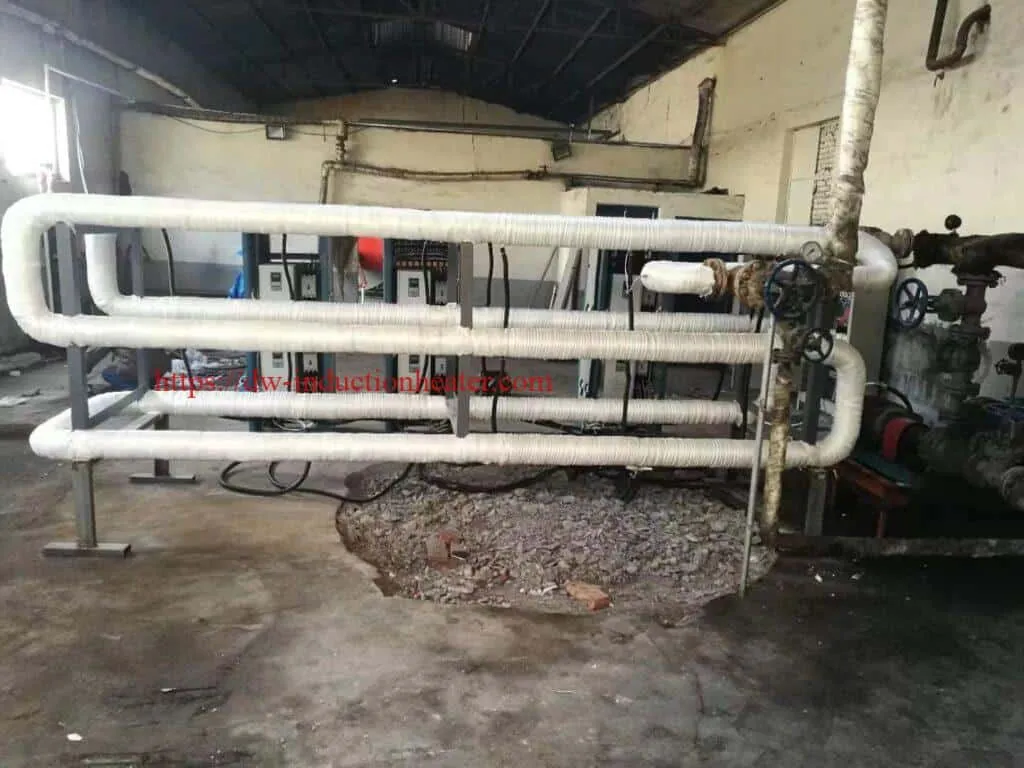
- Wall temperature differential - extremely low fluid, avoiding any kind of cracking or degradation of the fluid.
- Accuracy and temperature uniformity throughout the fluid and quality of the process for maintaining a constant temperature.
- Elimination of all maintenance costs, installations and relative contracts when compared to steam boilers.
- Total security for the operator and the entire process.
- Gain space due to the compact construction of the Inductive Heater.
- Direct heating of the fluid without the use of a heat exchanger.
- Due to the working system, the heater is anti-pollutant.
- Exempt from generating residues in direct heating of the thermal fluid, due to minimal oxidation.
- In operation the inductive heater is completely noise free.
- Ease and low cost of installation.
https://dw-inductionheater.com/induction-fluid-pipe-heater.html?feed_id=233236&_unique_id=65ba0eb8004fd