Hig Frequency Induction Soldering Brass Corner Joint
Objective
Successfully solder two 45° brass corner joints.
Equipment:
DW-UHF-10kw induction soldering heater
Materials
StayBrite #8 silver solder supplied by customer
Bridgit solder flux supplied by customer
Brass corner joint
Pancake coil
Key Parameters
Power: 5.5 kW
Temperature: Approximately 550° F (288° C)
Time: 20 sec
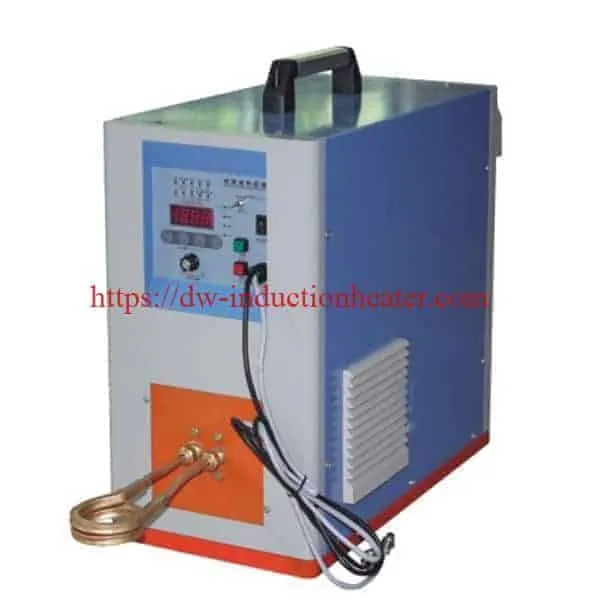

Process:
Results/Benefits:
- Flux is applied at all joints.
- The assembly is positioned into for heating
- Induction heating is applied for 15 sec
- The brazing rod is applied to the joint

- Since the brazing alloy is manually fed, the coil is placed under the joint, facing the visible side of the frame. The visible side of the joint is laying on a flat wooden surface, which does not allow the brazing alloy to leak and spill. This keeps the visible surface nice and clean, while the seam is internally brazed.
- If solder paste is used, then the coil can be placed on top of the joint. If special dual coil is used, then both joints (top and bottom) can be done with one shot.
- No frame flipping is needed in this case. See the video and zoom the pictures attached for more details.
- No special cleaning is needed on either side of the joint. The samples on the pictures have been paper towel wiped only.
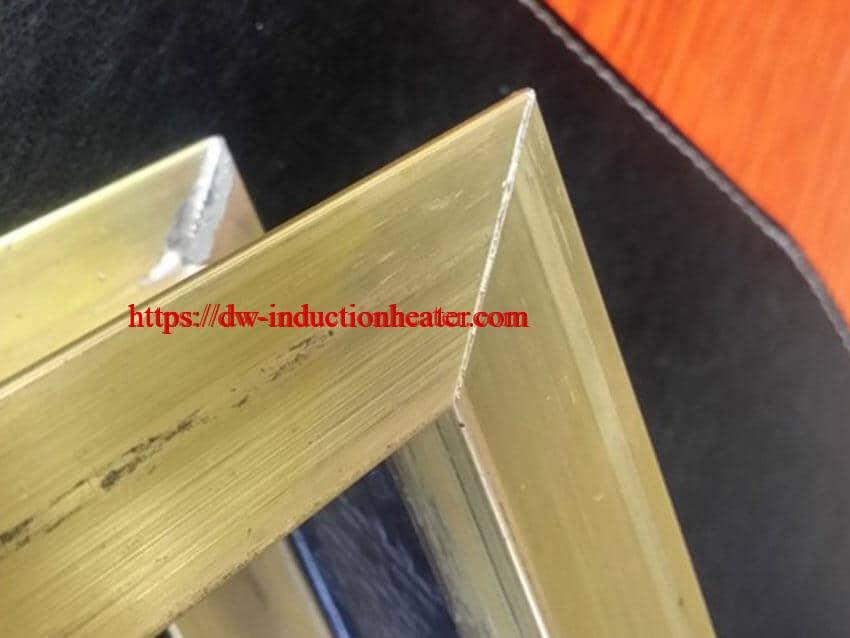