The Benefits of Induction Quenching Surface Process for Manufacturing.
Manufacturing is an industry that thrives on innovation and efficiency. When it comes to surface treatment processes, induction quenching is quickly becoming the method of choice for a variety of manufacturing applications. Unlike traditional heat treatment methods, induction quenching offers several unique benefits such as high production rates, increased precision, and improved part quality. In this article, we'll look at some of the key benefits of induction quenching surface process and why it's quickly becoming a popular choice for manufacturers across a range of industries. So, if you're looking to improve the efficiency and quality of your manufacturing process, or you're simply interested in the latest surface treatment techniques, keep reading to learn more about the benefits of induction quenching.
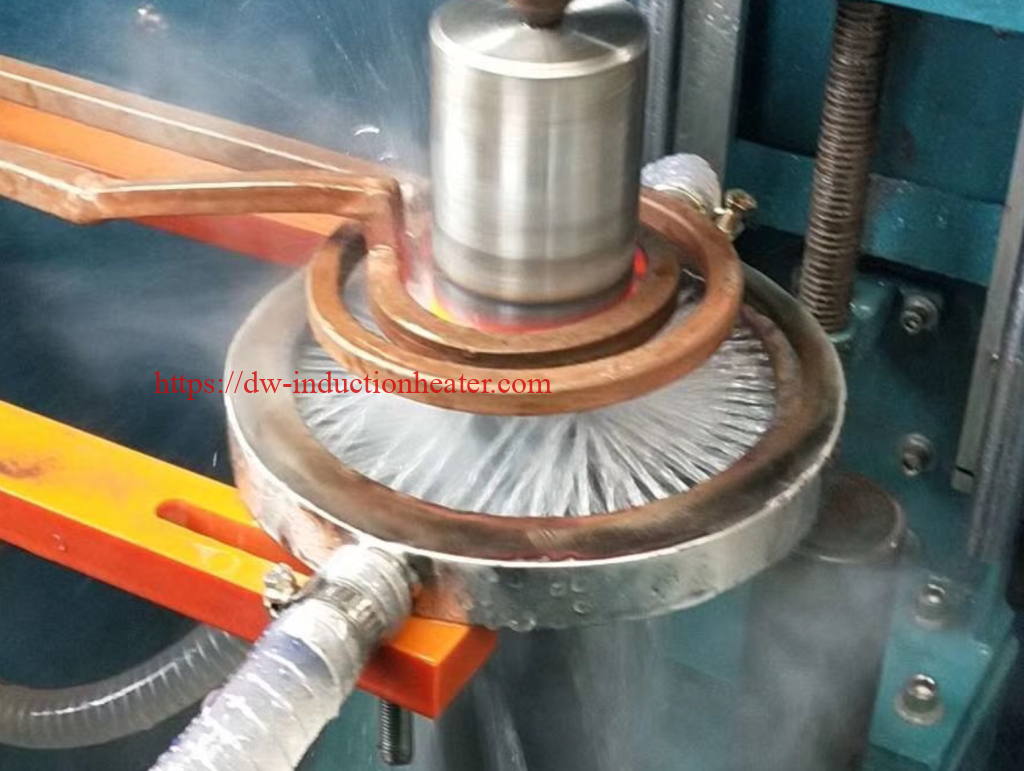
1. What is Induction Quenching Surface Process?
Induction quenching surface process is a type of surface hardening process that uses electrical induction to rapidly heat and cool metal parts. This process is commonly used in manufacturing because it offers a number of benefits over other types of surface hardening processes. In induction quenching, an induction coil is used to generate a high-frequency magnetic field that rapidly heats the metal part. Once the part is heated to the desired temperature, a quenching medium, such as water or oil, is used to rapidly cool the part. This rapid heating and cooling process causes the surface of the metal part to harden, which makes it more wear-resistant and less likely to crack or deform under stress. Induction quenching is also a very precise process that allows for accurate control of the surface hardness of the metal part. This precision makes it an ideal process for manufacturing parts that require high levels of wear resistance, such as gears, shafts, and bearings. Additionally, induction quenching is a very efficient process that can be completed quickly, which makes it ideal for high-volume production environments. Overall, induction quenching is a highly effective surface hardening process that offers many benefits for manufacturers looking to produce high-quality, durable metal parts.
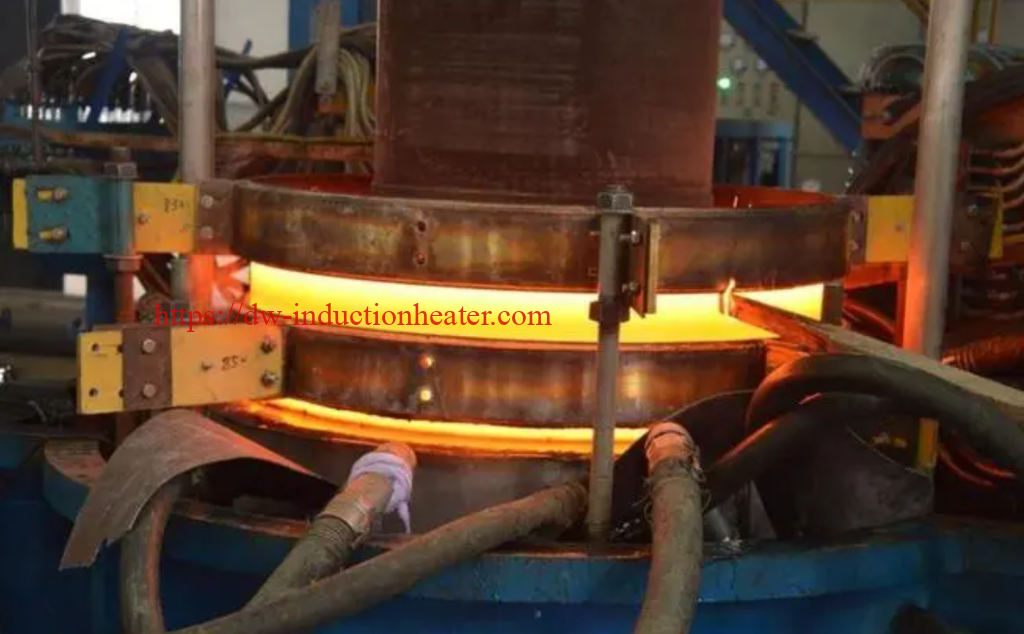
2. Benefits of Induction Quenching Surface Process
Induction quenching surface process is a highly efficient manufacturing technique that offers numerous benefits over traditional surface treatment methods. One of the most significant benefits of this process is that it is incredibly fast and efficient. With the ability to deliver heat at a rate of up to 25,000 degrees per second, induction quenching can heat treat parts in seconds, instead of hours or days, as is the case with other heat treatment methods. This means that manufacturers can produce more parts in less time, without sacrificing quality or reliability. Another significant benefit of induction quenching surface process is that it produces a superior product.

The process uses localized heating, which means that the heat is only applied where it is needed, resulting in less distortion, less scrap, and fewer defects. This makes induction quenching a great choice for manufacturers who are looking to produce high-quality parts quickly and efficiently. Induction quenching surface process is also a more environmentally-friendly option than other surface treatment methods. Since the process uses less energy and generates less waste, it is a more sustainable option for manufacturers who are looking to reduce their carbon footprint and be more environmentally responsible. In addition to these benefits, induction quenching surface process also offers a more controlled and precise heat treatment. The process allows manufacturers to control the depth of the heat treatment and the hardness achieved, which is a significant advantage over other surface treatment methods. With this level of control, manufacturers can produce parts that are exact in their specifications and meet the needs of their customers. Overall, the benefits of induction quenching surface process make it an ideal choice for manufacturers who are looking to improve their production processes, reduce waste, and produce high-quality parts quickly and efficiently.
3. Applications of Induction Quenching Surface Process in Manufacturing
Induction quenching is a surface hardening process that uses induction heating to heat the surface of a material to a high temperature and then rapidly cools it down by quenching it with water, oil or a polymer solution. This process creates a surface that is harder, more wear-resistant, and more durable than the original material. Induction quenching has many applications in manufacturing, including the hardening of gears, shafts, and bearings. It is also used in the automotive industry to harden engine components, such as camshafts, rocker arms, and valve lifters. The aerospace industry uses induction quenching to harden turbine components, and the energy industry uses it to harden drilling and mining components. The medical industry also uses induction quenching to harden surgical instruments and dental tools.

The process is also used in the production of cutting tools and molds. Induction quenching can produce a surface that is up to 10 times harder than the original material, making it an ideal choice for manufacturing applications where durability and wear resistance are critical. Additionally, the process is efficient and cost-effective, making it an attractive option for many manufacturers.
4. Conclusion.
Induction quenching surface process is a type of heat treatment process that is used to harden metal parts. The induction process involves passing a high-frequency electrical current through a coil, which creates a magnetic field. The metal part is then placed inside the coil, where the magnetic field induces an electrical current in the metal. This current causes the metal to heat up quickly, which then allows for the surface of the metal to be rapidly quenched by an appropriate cooling medium. This process creates a hardened surface that is more resistant to wear and tear, making it ideal for use in a wide variety of industrial applications.

https://dw-inductionheater.com/the-benefits-of-induction-quenching-surface-process-for-manufacturing.html?feed_id=206011&_unique_id=6466b2b7743b9