Induction Preheating Before Welding For Stress Relieving Heater
Why use Induction Preheating Before Welding ?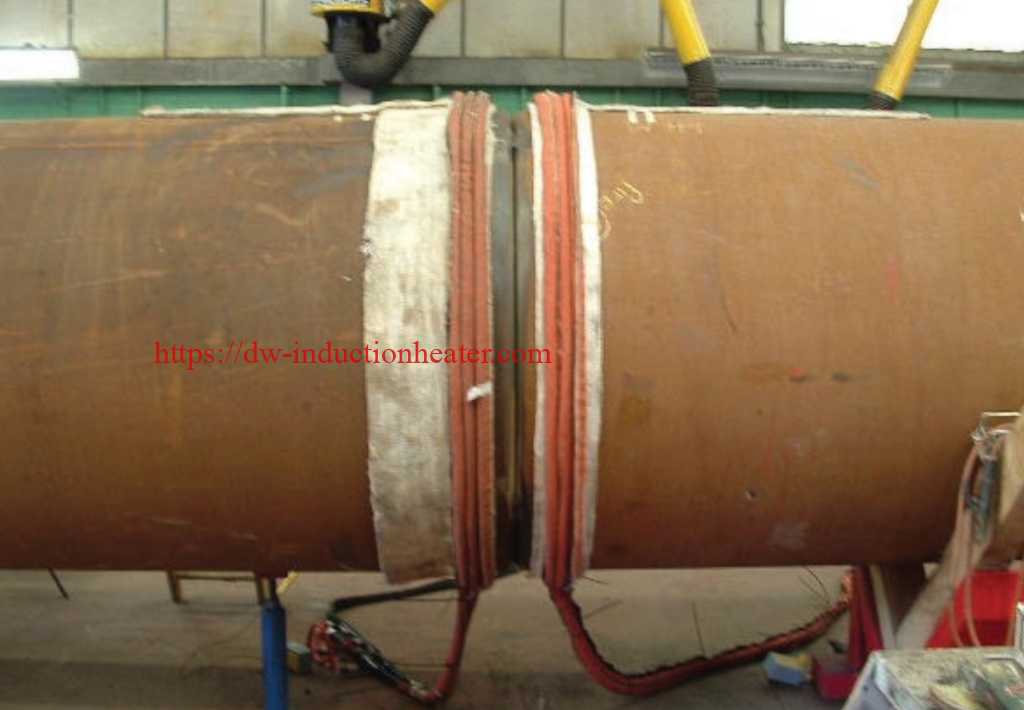
Induction preheating can slow down the cooling rate after welding. It is beneficial to escape the diffused hydrogen in the weld metal and avoid hydrogen-induced cracks. At the same time, It also reduces the welding seal and heat-affected zone hardening level, the welded joint crack resistance is improved.
Induction preheating can reduce welding stress. The temperature difference (also known as temperature gradient) between welders in the welding area can be reduced by uniformly local or whole induction preheating. In this way, on the one hand, the welding stress is reduced, on the other hand, the welding strain rate is reduced, which is beneficial to avoiding welding cracks.
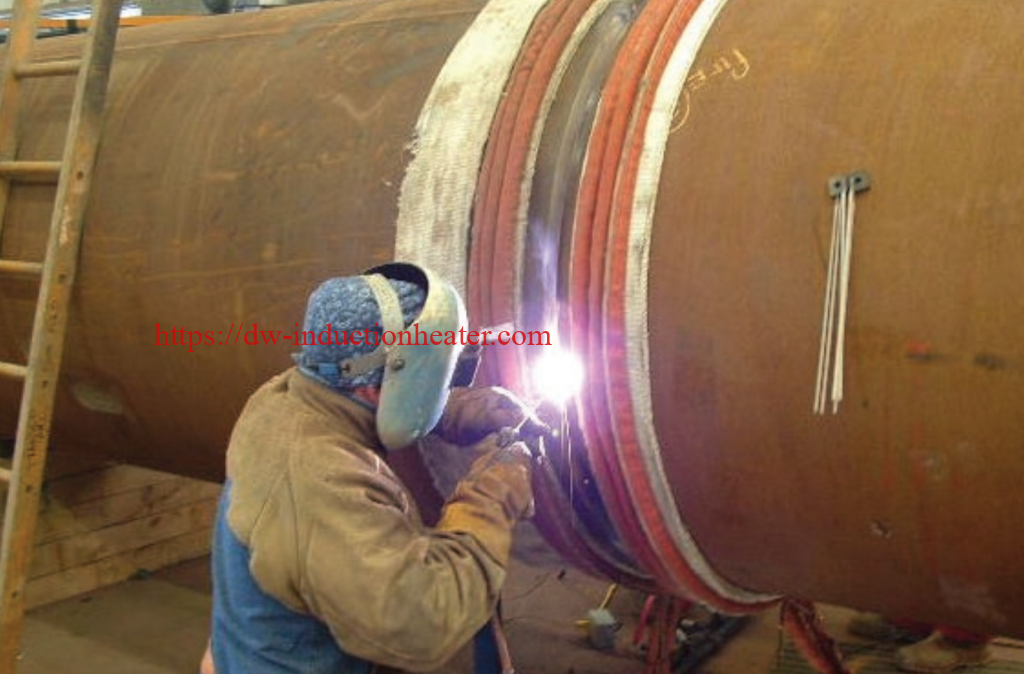
Induction preheating can reduce the welded structures constraint degree, it is especially obvious to reduce the constraint of the Angle joint. With the increase of induction preheating temperature, the crack incidence decreases.
Induction preheating temperature and interlayer temperature (Note: when multi-layer and multi-pass welding is carried out on the weldment, the lowest temperature of the front weld is called interlayer temperature when the post-weld is welded. For materials requiring induction preheating welding, when multilayer welding is required, the interlayer temperature should be equal to or slightly higher than the induction preheating temperature. If the interlayer temperature is lower than the induction preheating temperature, it should be induction preheated again.
In addition, the uniformity of induction preheating temperature in the direction of steel plate thickness and in the weld area has an important effect on reducing welding stress. The width of local induction preheating should be determined according to the constraint of the welder, generally three times the wall thickness around the weld zone, and not less than 150-200 mm. If the induction preheating is not uniform, not only will not reduce the welding stress but will increase the welding stress.
How to Find the Suitable Induction Preheating Solution?
When choosing the appropriate induction preheating equipment mainly consider the following aspects:
The heated workpiece’s shape and size.: Large workpiece, bar material, solid material, should be selected relative power, low-frequency induction heating equipment; If the workpiece is small, pipe, plate, gear, etc., the induction preheating equipment with low relative power and high frequency should be selected.
The depth and area to be heated: Deep heating depth, large area, overall heating, should choose large power, low frequency induction heating equipment; Shallow heating depth, small area, local heating, selection of relatively small power, high frequency induction preheating equipment.
The requried heating speed: If the heating speed is fast, the induction heating equipment with relatively large power and relatively high frequency should be selected.
Equipment continuous working time: Continuous working time is long, relatively select slightly larger power induction preheating equipment.
Distance between the induction heating head and the induction machine: Long connection, even the use of a water-cooled cable connection, should be a relatively large power induction preheating machine.
Induction Heating: How It Works?
Induction heating systems use noncontact heating. They induce heat electromagnetically rather than using a heating element in contact with a part to conduct heat, as does resistance heating. Induction heating acts more like a microwave oven — the appliance remains cool while the food cooks from within.
In an industrial example of
induction heating, heat is induced in the part by placing it in a high-frequency magnetic field. The magnetic field creates eddy currents inside the part, exciting the part's molecules and generating heat. Because heating occurs slightly below the metal surface, no heat is wasted.
Induction heating's similarity to resistance heating is that conduction is required to heat through the section or part. The only difference is the source of heat and the temperatures of the tool. The induction process heats within the part, and the resistance process heats on the surface of the part. The depth of heating depends on the frequency. High-frequency (e.g., 50 kHz) heats close to the surface, while low-frequency (e.g., 60 Hz) penetrates deeper into the part, placing the heating source up to 3 mm deep, which allows heating of thicker parts. The induction coil does not heat up because the conductor is large for the current being carried. In other words, the coil does not need to heat up to heat the workpiece.
Induction Heating System Components
Induction heating systems can be air- or liquid-cooled, depending on application requirements. A key component common to both systems is the induction coil used to generate heat within the part.
Air-cooled System. A typical air-cooled system consists of a power source , induction blanket, and associated cables. The induction blanket consists of an induction coil surrounded by insulation and sewn into a high-temperature, replaceable Kevlar sleeve.
This type of induction system can include a controller to monitor and automatically control temperature. A system not equipped with a controller requires the use of a temperature indicator. The system also could include a remote on-off switch. Air-cooled systems can be used for applications up to 400 degrees F, designating it as a preheat-only system.
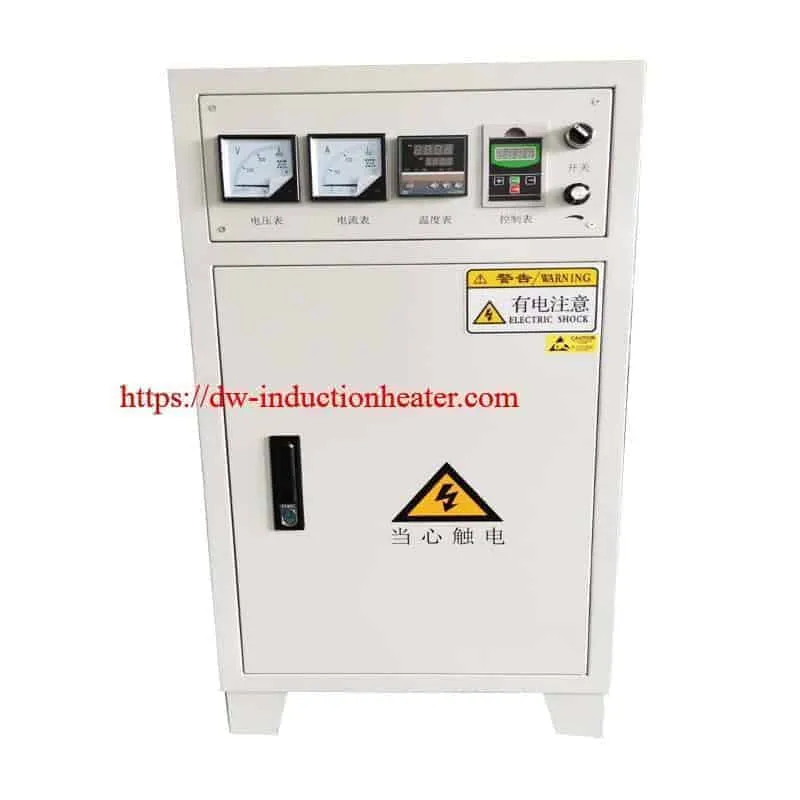
Liquid-cooled System. Because liquid cools more efficiently than air, this type of induction heating system is suitable for applications requiring higher temperatures, such as high-temperature preheating and stress relieving. The principal differences from an air-cooled system are the addition of a water cooler and the use of a flexible, liquid-cooled hose that houses the induction coil. Liquid-cooled systems also generally use a temperature controller and built-in temperature recorder, particularly important components in stress-relieving applications.
The typical stress-relieving procedure requires a step to 600 to 800 degrees F, followed by a ramp or controlled temperature rise to a soak temperature of approximately 1,250 degrees. After a hold time, the part is control-cooled to between 600 and 800 degrees. The temperature recorder collects data on the part's actual temperature profile based on a thermocouple input, a quality assurance requirement for stress-relieving applications. The type of work and the applicable code determine the actual procedure.
Induction Heating's Benefits
Induction heating offers numerous benefits, including good heat uniformity and quality, reduced cycle time, and long-lasting consumables. Induction heating is also safe, reliable, easy to use, power-efficient, and versatile.
Uniformity and Quality. Induction heating is not particularly sensitive to coil placement or spacing. Generally, the coils should be spaced evenly and centered on the weld joint. On systems so equipped, a temperature controller can establish the power requirement in an analog fashion, providing just enough power to maintain the temperature profile. The power source provides power during the entire process.
Cycle Time. The induction method of preheating and stress relieving provides relatively quick time-to-temperature. On thicker applications, such as high-pressure steam lines, induction heating can slash two hours from cycle time. It is possible to reduce cycle time from the control temperature to soak temperature.
Consumables. The insulation used in induction heating is easy to attach to workpieces and can be reused many times. In addition, induction coils are robust and do not require fragile wire or ceramic materials. Also, because the induction coils and connectors do not operate at high temperatures, they are not subject to degradation.
Ease of Use. A major benefit of induction preheating and stress relieving is its simplicity. Insulation and cables are simple to install, usually taking less than 15 minutes. In some cases, how to use the induction equipment can be taught in one day.
Power Efficiency. The inverter power source is 92 percent efficient, a critical advantage in an era of skyrocketing energy costs. Additionally, the induction heating process is more than 80 percent efficient. Regarding power input, the induction process requires only a 40-amp line for 25 kW of power.
Safety. Preheating and stress relieving through the induction method is worker-friendly. Induction heating does not require hot heating elements and connectors. Very little airborne particulate is associated with the insulation blankets, and the insulation itself is not exposed to temperatures higher than 1,800 degrees, which can cause insulation to break down into dust that workers may inhale.
Reliability. One of the most important factors impacting productivity in stress relieving is an uninterrupted cycle. In most instances cycle interruption means the heat treat will need to be rerun, which is significant when a thermal cycle can take a day to complete. The induction heating system components make cycle interruptions unlikely. The cabling for induction is simple, making it less likely to fail. Also, no contactors are used to control the heat input to the part.
Versatility. In addition to using
induction heating systems to preheat and stress relieve pipe, users have adapted the process for weldolets, elbows, valves, and other parts. One of the aspects of induction heating that makes it attractive for complex shapes is the ability to adjust the coils during the heating process to accommodate unique parts and heat sinks. The operator can start the process, determine the effects of the heating process in real time, and modify the coil position to change the result. The induction cables can be moved without waiting for air cooling at the end of the cycle.
Induction Heating before Welding Applications
This technology has proved itself on a number of projects, including oil and gas pipelines, heavy equipment construction, and maintenance and repair of mining equipment.
Oil Pipeline. A North American oil pipeline maintenance operation needed to heat pipe before welding encirclement repair sleeves or fittings to the pipeline's 48-in. girth. While workers could make many repairs without having to stop oil flow or drain it from the pipe, the presence of the crude itself hampered welding efficiency because the flowing oil absorbed the heat. Propane torches required constant interruption of welding to maintain heat, and resistance heating — while providing continuous heat — often could not meet required weld temperatures.

The Workers used two 25-kW systems with parallel blankets to obtain a preheat temperature of 125 degrees on encirclement sleeve repairs. As a result, they reduced cycle time from eight to 12 hours to four hours per girth weld.
Preheating for a STOPPLE fitting (a T junction with valve) repair was even more challenging because of the fitting's greater wall thickness. With induction heating, however, the company used four 25-kW systems with a paralleled blanket setup. They used two systems on each side of the T. One system was used on the main line to preheat the oil, and the second was used to preheat the T at the circumferential weld joint. The preheat temperature was 125 degrees. This reduced the weld time from 12 to 18 hours to seven hours per girth weld.
Natural Gas Pipeline. A natural gas pipeline construction project entailed building a 36-in.-diameter, 0.633-in.-thick pipeline from Alberta, Canada, to Chicago. On one stretch of this pipeline, the welding contractor used two 25-kW power sources mounted on a tractor with the induction blankets attached to booms for speed and convenience. The power sources preheated both sides of the pipe joint. Critical to this process were speed and reliable temperature control. As alloy content increases in materials to reduce weight and weld time, and to increase part life, controlling preheat temperatures becomes more critical. This induction heating application it required less than three minutes to obtain the 250-degree preheat temperature.
Heavy Equipment. A heavy equipment manufacturer often welded adapter teeth onto its loader bucket edges. The tack-welded assembly had been moved back and forth to a large furnace, requiring the welding operator to wait while the part was reheated repeatedly. The manufacturer opted to try induction heating to preheat the assembly to prevent movement of the product.
The material was 4 in. thick with a high required preheat temperature because of alloy content. Customized induction blankets were developed to meet the application requirements. The insulation and coil design provided the added benefit of shielding the operator from the part's radiant heat. Overall, operations were considerably more efficient, reducing welding time and maintaining temperature throughout the welding process.
Mining Equipment. A mine had been experiencing cold-cracking problems and preheating inefficiency using propane heaters in its repair operations of mining equipment. Welding operators had to remove a conventional insulating blanket from the thick part frequently to apply heat and keep the part at the correct temperature.
The induction preheat blanket maintains the temperature of the bucket edge during the attachment of teeth.
The mine opted to try induction heating using flat, air-cooled blankets to preheat the parts before welding. The induction process applied heat to the part quickly. It also could be used continuously during the welding process. Weld repair time was reduced by 50 percent. In addition, the power source was equipped with a temperature controller to keep the part at the target temperature. This almost eliminated rework caused by cold cracking.
Power Plant. A power plant builder was constructing a natural gas power facility in California. Boilermakers and pipefitters had been experiencing construction delays due to the preheating and stress-relieving methods they were employing on the plant's steam lines. The company brought in induction heating technology in an attempt to increase efficiency, particularly for work on medium to large steam lines, as these pieces take the most heat-treating time required on a job site.
The simplicity of wrapping the induction blankets around complex shapes, such as at this natural gas power plant, can reduce heat-treating time.
On a typical 16-in. weldolet with a 2-in. wall thickness, induction heating was able to shave two hours off the time-to-temperature (600 degrees) and another hour to reach soak temperature (600 degrees to 1,350 degrees) for stress relieving.
https://dw-inductionheater.com/induction-preheating-before-welding-for-stress-relieving.html?feed_id=208861&_unique_id=6474fd68077cf