
Induction hardening steel screw threads

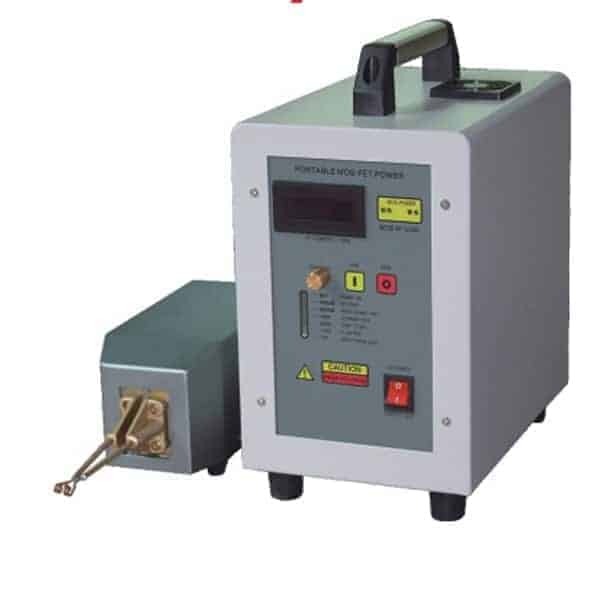

The distillation process plays a crucial role in refining crude oil into valuable products such as gasoline, diesel, and jet fuel. Traditionally, heating crude oil pipes for distillation has been done using conventional methods, which can be time-consuming and energy-inefficient. However, with the advent of induction technology, a more efficient and precise heating method has emerged. In this blog post, we will explore how induction technology is revolutionizing the distillation process by heating crude oil pipes effectively, resulting in improved productivity, energy savings, and overall process efficiency.
1. Understanding the distillation process in oil refining
Understanding the distillation process is crucial in oil refining, especially when it comes to heating crude oil pipes with induction technology. Distillation is a key step in the refining process that separates crude oil into different components based on their boiling points. The process involves heating the crude oil to vaporize it and then condensing the vapor back into liquid form to extract various products such as gasoline, diesel, and jet fuel.
In oil refining, the distillation process typically involves a series of distillation columns or towers, each designed to separate specific fractions of crude oil based on their boiling points. As the crude oil is heated, the lighter components with lower boiling points rise to the top of the column, while the heavier components with higher boiling points sink to the bottom.
Heating crude oil pipes with induction technology offers several advantages in the distillation process, such as precise and efficient heating, reduced energy consumption, and improved safety. Induction heating uses electromagnetic induction to generate heat directly within the material being heated, resulting in faster and more uniform heating compared to traditional methods.
By understanding the distillation process in oil refining and utilizing induction technology for heating crude oil pipes, refineries can optimize their operations, improve product quality, and enhance overall efficiency in the production of valuable petroleum products.
2. Introduction to induction heating technology
Induction heating technology is a cutting-edge method that has revolutionized various industries, including distillation processes in oil refining. This innovative technique utilizes electromagnetic induction to generate heat within a conductive material, such as metal pipes used in the distillation of crude oil. By applying high-frequency alternating current to a coil surrounding the pipe, induction heating induces electrical currents that result in rapid and precise heating of the pipe's surface. This localized heating is highly efficient, as it minimizes heat loss to the surrounding environment and allows for targeted heating of specific sections of the pipe as needed. As a result, induction heating technology offers enhanced control, energy efficiency, and speed in heating crude oil pipes during the distillation process, ultimately leading to increased productivity and cost savings for oil refineries.
3. Benefits of using induction technology in heating crude oil pipes
Using induction technology to heat crude oil pipes offers numerous benefits that can significantly improve the efficiency of the distillation process. One of the key advantages is the ability to achieve precise and uniform heating throughout the pipes, resulting in consistent temperatures and reduced energy consumption. Induction technology also enables rapid heating, which helps to shorten the heating process and increase overall productivity.
Furthermore, induction heating is a clean and environmentally friendly method that does not involve direct contact between the heating source and the pipes, reducing the risk of contamination and ensuring a safe working environment. Additionally, this technology offers excellent control over the heating process, allowing for adjustments in real-time and minimizing the chances of overheating or uneven heating.
Moreover, induction technology is highly reliable and requires minimal maintenance, leading to cost savings and improved operational efficiency. The overall performance and longevity of the crude oil pipes can also be enhanced by utilizing this advanced heating method. In conclusion, the benefits of using induction technology in heating crude oil pipes make it a valuable asset in achieving an efficient distillation process.
Traditional crude oil distillation methods involve heating the oil in large vertical columns known as distillation towers. As the oil is heated, its components vaporize and rise to different levels within the tower, where they are collected and condensed. However, this process is not without its drawbacks.
One of the major challenges is the uneven heating of the crude oil. Due to the size and shape of the distillation towers, the heat distribution is often inconsistent, leading to inefficiencies in the separation process. This results in lower distillation yields and higher energy consumption, ultimately impacting the overall profitability of oil refineries.
Another challenge is the slow heating and cooling rates associated with traditional distillation methods. The gradual heating and cooling cycles not only prolong the distillation process but also contribute to increased maintenance costs and downtime.
How Induction Heating Improves Distillation Efficiency
Induction heating technology offers several advantages over traditional distillation methods, leading to enhanced distillation efficiency. Firstly, the uniform heating provided by induction heating ensures consistent temperature distribution throughout the crude oil, minimizing the formation of hotspots and cold spots. This promotes better separation of the oil components and improves distillation yields.
Secondly, induction heating enables precise and rapid heating and cooling cycles, significantly reducing the overall distillation time. This not only increases productivity but also minimizes energy consumption and maintenance costs. The ability to achieve higher heating rates also allows for better control over the distillation process, leading to improved product quality.
Additionally, induction heating systems can be easily integrated into existing distillation setups, making it a cost-effective solution for oil refineries. The flexibility of induction heating technology allows for customization based on specific refinery requirements, ensuring optimal performance and efficiency.
Case Studies of Successful Implementation of Induction Heating in Crude Oil Distillation
Several oil refineries have successfully implemented induction heating technology in their crude oil distillation processes, reaping the benefits of improved efficiency and productivity. One such case study involves a refinery in Texas that experienced a significant increase in distillation yields after installing an induction heating system. The refinery reported a 15% increase in product output and a reduction in energy consumption by 20%.
Another case study comes from a refinery in the Middle East, where induction heating was introduced to replace traditional heating methods. The refinery saw a drastic reduction in distillation time, resulting in higher production rates and improved profitability. The installation of the induction heating system also led to a decrease in maintenance costs and a more sustainable refining process.
These success stories highlight the transformative impact of induction heating technology on crude oil distillation, making it a compelling choice for refineries looking to enhance their efficiency and profitability.
Factors to Consider When Choosing Induction Heating for Crude Oil Pipes
When considering the implementation of induction heating in crude oil distillation processes, there are several factors to take into account. Firstly, the size and capacity of the distillation setup should be evaluated to determine the appropriate induction heating system. Factors such as pipe diameter, material composition, and flow rate should be considered to ensure optimal performance.
Secondly, the reliability and durability of the induction heating equipment should be a priority. It is essential to select a reputable manufacturer with a proven track record in the industry. Additionally, the maintenance requirements and availability of spare parts should be taken into consideration to minimize downtime and ensure uninterrupted operation.
Furthermore, safety measures should be carefully assessed when integrating induction heating technology into existing distillation setups. Adequate insulation, grounding, and temperature monitoring systems must be in place to prevent accidents and ensure the well-being of refinery personnel.
Conclusion
Induction heating technology offers a compelling solution to enhance the distillation efficiency of crude oil pipes. By providing uniform heating, faster heating and cooling cycles, and improved control over the distillation process, induction heating systems can significantly improve distillation yields, reduce energy consumption, and increase profitability for oil refineries.
The successful implementation of induction heating in crude oil distillation has been demonstrated through various case studies, showcasing the transformative impact of this technology. Factors such as system selection, installation, and maintenance should be carefully considered to ensure optimal performance and reliability.
The cost and energy savings associated with induction heating further contribute to its appeal, along with the potential for future advancements and innovations in the field. As the petroleum industry continues to evolve, induction heating technology will play a crucial role in driving efficiency, sustainability, and profitability in crude oil distillation processes.
https://dw-inductionheater.com/heating-crude-oil-pipes-for-distillation-with-induction.html?feed_id=235260&_unique_id=65dfaf895874eInduction heating can outperform traditional paint-stripping methods. Abrasive blasting or disk grinding are generally more labour intensive and come with other issues such as the cost of enclosure or containment and collection of blast media, plus the filtration or separation of the coating materials for disposal. In many urban projects these are prime considerations and extremely costly to overcome. Whereas, when coatings are removed by induction, the only waste is the coating itself which in most cases can be swept or even vacuumed like any other workshop waste.
Safer working environment: The controlled, localized heat results in significantly reduced fumes and toxic dust.
Easy clean-up: The coating material mainly peels off in flakes rather than being pulverized.
Noiseless operation: Operators can work in public areas without creating a disturbance.
Mobile: The equipment is rugged and reliable but still light-weight and easy to move around worksites.
Reduced energy consumption: Fast, accurate and repeatable heat delivery makes the coating removal process extremely energy efficient.
Method flexibility: Spot heating, scanning, freehand and semi-automatic.
No limitations: The system can be used at flat surfaces, round contours, inside/outside corners, both sides of substrate, round rivets, etc.
Induction coating removal is used in many industries, such as ships/marine, buildings, storage tanks, pipelines, bridges and offshore.
induction heating involves using alternating current and an induction coil to generate a powerful electro-magnetic field. When used properly, this field generates heat below a coating on a steel substrate, resulting in the coating de-bonding quickly and easily from the metal surface. At Alliance, we use this process to remove coatings from steel such as:
The distillation process plays a crucial role in refining crude oil into valuable products such as gasoline, diesel, and jet fuel. Traditionally, heating crude oil pipes for distillation has been done using conventional methods, which can be time-consuming and energy-inefficient. However, with the advent of induction technology, a more efficient and precise heating method has emerged. In this blog post, we will explore how induction technology is revolutionizing the distillation process by heating crude oil pipes effectively, resulting in improved productivity, energy savings, and overall process efficiency.
1. Understanding the distillation process in oil refining
Understanding the distillation process is crucial in oil refining, especially when it comes to heating crude oil pipes with induction technology. Distillation is a key step in the refining process that separates crude oil into different components based on their boiling points. The process involves heating the crude oil to vaporize it and then condensing the vapor back into liquid form to extract various products such as gasoline, diesel, and jet fuel.
In oil refining, the distillation process typically involves a series of distillation columns or towers, each designed to separate specific fractions of crude oil based on their boiling points. As the crude oil is heated, the lighter components with lower boiling points rise to the top of the column, while the heavier components with higher boiling points sink to the bottom.
Heating crude oil pipes with induction technology offers several advantages in the distillation process, such as precise and efficient heating, reduced energy consumption, and improved safety. Induction heating uses electromagnetic induction to generate heat directly within the material being heated, resulting in faster and more uniform heating compared to traditional methods.
By understanding the distillation process in oil refining and utilizing induction technology for heating crude oil pipes, refineries can optimize their operations, improve product quality, and enhance overall efficiency in the production of valuable petroleum products.
2. Introduction to induction heating technology
Induction heating technology is a cutting-edge method that has revolutionized various industries, including distillation processes in oil refining. This innovative technique utilizes electromagnetic induction to generate heat within a conductive material, such as metal pipes used in the distillation of crude oil. By applying high-frequency alternating current to a coil surrounding the pipe, induction heating induces electrical currents that result in rapid and precise heating of the pipe's surface. This localized heating is highly efficient, as it minimizes heat loss to the surrounding environment and allows for targeted heating of specific sections of the pipe as needed. As a result, induction heating technology offers enhanced control, energy efficiency, and speed in heating crude oil pipes during the distillation process, ultimately leading to increased productivity and cost savings for oil refineries.
3. Benefits of using induction technology in heating crude oil pipes
Using induction technology to heat crude oil pipes offers numerous benefits that can significantly improve the efficiency of the distillation process. One of the key advantages is the ability to achieve precise and uniform heating throughout the pipes, resulting in consistent temperatures and reduced energy consumption. Induction technology also enables rapid heating, which helps to shorten the heating process and increase overall productivity.
Furthermore, induction heating is a clean and environmentally friendly method that does not involve direct contact between the heating source and the pipes, reducing the risk of contamination and ensuring a safe working environment. Additionally, this technology offers excellent control over the heating process, allowing for adjustments in real-time and minimizing the chances of overheating or uneven heating.
Moreover, induction technology is highly reliable and requires minimal maintenance, leading to cost savings and improved operational efficiency. The overall performance and longevity of the crude oil pipes can also be enhanced by utilizing this advanced heating method. In conclusion, the benefits of using induction technology in heating crude oil pipes make it a valuable asset in achieving an efficient distillation process.
Traditional crude oil distillation methods involve heating the oil in large vertical columns known as distillation towers. As the oil is heated, its components vaporize and rise to different levels within the tower, where they are collected and condensed. However, this process is not without its drawbacks.
One of the major challenges is the uneven heating of the crude oil. Due to the size and shape of the distillation towers, the heat distribution is often inconsistent, leading to inefficiencies in the separation process. This results in lower distillation yields and higher energy consumption, ultimately impacting the overall profitability of oil refineries.
Another challenge is the slow heating and cooling rates associated with traditional distillation methods. The gradual heating and cooling cycles not only prolong the distillation process but also contribute to increased maintenance costs and downtime.
Induction heating technology offers several advantages over traditional distillation methods, leading to enhanced distillation efficiency. Firstly, the uniform heating provided by induction heating ensures consistent temperature distribution throughout the crude oil, minimizing the formation of hotspots and cold spots. This promotes better separation of the oil components and improves distillation yields.
Secondly, induction heating enables precise and rapid heating and cooling cycles, significantly reducing the overall distillation time. This not only increases productivity but also minimizes energy consumption and maintenance costs. The ability to achieve higher heating rates also allows for better control over the distillation process, leading to improved product quality.
Additionally, induction heating systems can be easily integrated into existing distillation setups, making it a cost-effective solution for oil refineries. The flexibility of induction heating technology allows for customization based on specific refinery requirements, ensuring optimal performance and efficiency.
Several oil refineries have successfully implemented induction heating technology in their crude oil distillation processes, reaping the benefits of improved efficiency and productivity. One such case study involves a refinery in Texas that experienced a significant increase in distillation yields after installing an induction heating system. The refinery reported a 15% increase in product output and a reduction in energy consumption by 20%.
Another case study comes from a refinery in the Middle East, where induction heating was introduced to replace traditional heating methods. The refinery saw a drastic reduction in distillation time, resulting in higher production rates and improved profitability. The installation of the induction heating system also led to a decrease in maintenance costs and a more sustainable refining process.
These success stories highlight the transformative impact of induction heating technology on crude oil distillation, making it a compelling choice for refineries looking to enhance their efficiency and profitability.
When considering the implementation of induction heating in crude oil distillation processes, there are several factors to take into account. Firstly, the size and capacity of the distillation setup should be evaluated to determine the appropriate induction heating system. Factors such as pipe diameter, material composition, and flow rate should be considered to ensure optimal performance.
Secondly, the reliability and durability of the induction heating equipment should be a priority. It is essential to select a reputable manufacturer with a proven track record in the industry. Additionally, the maintenance requirements and availability of spare parts should be taken into consideration to minimize downtime and ensure uninterrupted operation.
Furthermore, safety measures should be carefully assessed when integrating induction heating technology into existing distillation setups. Adequate insulation, grounding, and temperature monitoring systems must be in place to prevent accidents and ensure the well-being of refinery personnel.
Induction heating technology offers a compelling solution to enhance the distillation efficiency of crude oil pipes. By providing uniform heating, faster heating and cooling cycles, and improved control over the distillation process, induction heating systems can significantly improve distillation yields, reduce energy consumption, and increase profitability for oil refineries.
The successful implementation of induction heating in crude oil distillation has been demonstrated through various case studies, showcasing the transformative impact of this technology. Factors such as system selection, installation, and maintenance should be carefully considered to ensure optimal performance and reliability.
The cost and energy savings associated with induction heating further contribute to its appeal, along with the potential for future advancements and innovations in the field. As the petroleum industry continues to evolve, induction heating technology will play a crucial role in driving efficiency, sustainability, and profitability in crude oil distillation processes.
https://dw-inductionheater.com/heating-crude-oil-pipes-for-distillation-with-induction.html?feed_id=235182&_unique_id=65df2f6e4dd4dThe distillation process plays a crucial role in refining crude oil into valuable products such as gasoline, diesel, and jet fuel. Traditionally, heating crude oil pipes for distillation has been done using conventional methods, which can be time-consuming and energy-inefficient. However, with the advent of induction technology, a more efficient and precise heating method has emerged. In this blog post, we will explore how induction technology is revolutionizing the distillation process by heating crude oil pipes effectively, resulting in improved productivity, energy savings, and overall process efficiency.
1. Understanding the distillation process in oil refining
Understanding the distillation process is crucial in oil refining, especially when it comes to heating crude oil pipes with induction technology. Distillation is a key step in the refining process that separates crude oil into different components based on their boiling points. The process involves heating the crude oil to vaporize it and then condensing the vapor back into liquid form to extract various products such as gasoline, diesel, and jet fuel.
In oil refining, the distillation process typically involves a series of distillation columns or towers, each designed to separate specific fractions of crude oil based on their boiling points. As the crude oil is heated, the lighter components with lower boiling points rise to the top of the column, while the heavier components with higher boiling points sink to the bottom.
Heating crude oil pipes with induction technology offers several advantages in the distillation process, such as precise and efficient heating, reduced energy consumption, and improved safety. Induction heating uses electromagnetic induction to generate heat directly within the material being heated, resulting in faster and more uniform heating compared to traditional methods.
By understanding the distillation process in oil refining and utilizing induction technology for heating crude oil pipes, refineries can optimize their operations, improve product quality, and enhance overall efficiency in the production of valuable petroleum products.
2. Introduction to induction heating technology
Induction heating technology is a cutting-edge method that has revolutionized various industries, including distillation processes in oil refining. This innovative technique utilizes electromagnetic induction to generate heat within a conductive material, such as metal pipes used in the distillation of crude oil. By applying high-frequency alternating current to a coil surrounding the pipe, induction heating induces electrical currents that result in rapid and precise heating of the pipe's surface. This localized heating is highly efficient, as it minimizes heat loss to the surrounding environment and allows for targeted heating of specific sections of the pipe as needed. As a result, induction heating technology offers enhanced control, energy efficiency, and speed in heating crude oil pipes during the distillation process, ultimately leading to increased productivity and cost savings for oil refineries.
3. Benefits of using induction technology in heating crude oil pipes
Using induction technology to heat crude oil pipes offers numerous benefits that can significantly improve the efficiency of the distillation process. One of the key advantages is the ability to achieve precise and uniform heating throughout the pipes, resulting in consistent temperatures and reduced energy consumption. Induction technology also enables rapid heating, which helps to shorten the heating process and increase overall productivity.
Furthermore, induction heating is a clean and environmentally friendly method that does not involve direct contact between the heating source and the pipes, reducing the risk of contamination and ensuring a safe working environment. Additionally, this technology offers excellent control over the heating process, allowing for adjustments in real-time and minimizing the chances of overheating or uneven heating.
Moreover, induction technology is highly reliable and requires minimal maintenance, leading to cost savings and improved operational efficiency. The overall performance and longevity of the crude oil pipes can also be enhanced by utilizing this advanced heating method. In conclusion, the benefits of using induction technology in heating crude oil pipes make it a valuable asset in achieving an efficient distillation process.
Traditional crude oil distillation methods involve heating the oil in large vertical columns known as distillation towers. As the oil is heated, its components vaporize and rise to different levels within the tower, where they are collected and condensed. However, this process is not without its drawbacks.
One of the major challenges is the uneven heating of the crude oil. Due to the size and shape of the distillation towers, the heat distribution is often inconsistent, leading to inefficiencies in the separation process. This results in lower distillation yields and higher energy consumption, ultimately impacting the overall profitability of oil refineries.
Another challenge is the slow heating and cooling rates associated with traditional distillation methods. The gradual heating and cooling cycles not only prolong the distillation process but also contribute to increased maintenance costs and downtime.
Induction heating technology offers several advantages over traditional distillation methods, leading to enhanced distillation efficiency. Firstly, the uniform heating provided by induction heating ensures consistent temperature distribution throughout the crude oil, minimizing the formation of hotspots and cold spots. This promotes better separation of the oil components and improves distillation yields.
Secondly, induction heating enables precise and rapid heating and cooling cycles, significantly reducing the overall distillation time. This not only increases productivity but also minimizes energy consumption and maintenance costs. The ability to achieve higher heating rates also allows for better control over the distillation process, leading to improved product quality.
Additionally, induction heating systems can be easily integrated into existing distillation setups, making it a cost-effective solution for oil refineries. The flexibility of induction heating technology allows for customization based on specific refinery requirements, ensuring optimal performance and efficiency.
Several oil refineries have successfully implemented induction heating technology in their crude oil distillation processes, reaping the benefits of improved efficiency and productivity. One such case study involves a refinery in Texas that experienced a significant increase in distillation yields after installing an induction heating system. The refinery reported a 15% increase in product output and a reduction in energy consumption by 20%.
Another case study comes from a refinery in the Middle East, where induction heating was introduced to replace traditional heating methods. The refinery saw a drastic reduction in distillation time, resulting in higher production rates and improved profitability. The installation of the induction heating system also led to a decrease in maintenance costs and a more sustainable refining process.
These success stories highlight the transformative impact of induction heating technology on crude oil distillation, making it a compelling choice for refineries looking to enhance their efficiency and profitability.
When considering the implementation of induction heating in crude oil distillation processes, there are several factors to take into account. Firstly, the size and capacity of the distillation setup should be evaluated to determine the appropriate induction heating system. Factors such as pipe diameter, material composition, and flow rate should be considered to ensure optimal performance.
Secondly, the reliability and durability of the induction heating equipment should be a priority. It is essential to select a reputable manufacturer with a proven track record in the industry. Additionally, the maintenance requirements and availability of spare parts should be taken into consideration to minimize downtime and ensure uninterrupted operation.
Furthermore, safety measures should be carefully assessed when integrating induction heating technology into existing distillation setups. Adequate insulation, grounding, and temperature monitoring systems must be in place to prevent accidents and ensure the well-being of refinery personnel.
Induction heating technology offers a compelling solution to enhance the distillation efficiency of crude oil pipes. By providing uniform heating, faster heating and cooling cycles, and improved control over the distillation process, induction heating systems can significantly improve distillation yields, reduce energy consumption, and increase profitability for oil refineries.
The successful implementation of induction heating in crude oil distillation has been demonstrated through various case studies, showcasing the transformative impact of this technology. Factors such as system selection, installation, and maintenance should be carefully considered to ensure optimal performance and reliability.
The cost and energy savings associated with induction heating further contribute to its appeal, along with the potential for future advancements and innovations in the field. As the petroleum industry continues to evolve, induction heating technology will play a crucial role in driving efficiency, sustainability, and profitability in crude oil distillation processes.
https://dw-inductionheater.com/heating-crude-oil-pipes-for-distillation-with-induction.html?feed_id=235182&_unique_id=65df2f6e400b2Enhancing Automotive Efficiency: The Role of Induction Heating in Shrink Fitting Aluminum Motor Housings
The automotive industry is constantly seeking methods to improve the performance, efficiency, and sustainability of its products. Shrink fitting using induction heating has emerged as a pivotal technology in the assembly of aluminum motor housings. This article delves into the principles of shrink fitting and induction heating, highlighting their significance in automotive manufacturing. It explores the benefits of using aluminum in motor housings, the process of induction heating for shrink fitting applications, the advantages over traditional methods, and the impact on the automotive industry's future.
Introduction:
In the quest for superior automotive performance and efficiency, the integration of lightweight materials such as aluminum in motor housings has become increasingly prevalent. The assembly of these components often involves the process of shrink fitting, which requires precise thermal expansion to create a tight, secure fit between parts. Induction heating has revolutionized this process, offering a fast, controllable, and energy-efficient method to achieve the desired interference fit. This article examines the application of induction heating in the shrink fitting of automotive aluminum motor housings and its implications for the industry.
The Advantages of Aluminum Motor Housings:
Aluminum, known for its lightweight, high strength-to-weight ratio, and excellent thermal conductivity, makes it an ideal choice for motor housings. These properties lead to reduced vehicle weight, improved fuel efficiency, and better heat dissipation, all critical factors in the performance and longevity of automotive engines.
Principles of Shrink Fitting:
Shrink fitting is a mechanical method used to join two components with a high degree of precision. It involves heating the outer component (in this case, the aluminum motor housing) to expand it, allowing the insertion of the inner part (such as a steel shaft). Upon cooling, the outer component contracts to form a tight, seamless joint that can withstand significant mechanical loads without the need for adhesives or mechanical fasteners.
Induction Heating in Shrink Fitting:
Induction heating is a non-contact process that uses electromagnetic fields to heat conductive materials rapidly and selectively. In the context of shrink fitting, induction heating provides several benefits, including:
The Process of Shrink Fitting with Induction Heating:
The shrink fitting process using induction heating involves several steps:
Advantages Over Traditional Methods:
Compared to conventional heating methods like ovens or torches, induction heating offers superior consistency, repeatability, and efficiency. It reduces the risk of component distortion and eliminates the need for long cool-down periods associated with oven heating.
Impact on the Automotive Industry:
The adoption of induction heating for shrink fitting in the automotive sector has a transformative impact. It enables manufacturers to meet the increasing demand for lightweight, high-performance vehicles while maintaining high production rates and stringent quality standards. This technology supports the industry's shift towards more sustainable manufacturing practices and contributes to the development of electric and hybrid vehicles that require lightweight, high-efficiency components.
Application in the Production of Automotive Aluminum Motor Housings
In the production of automotive aluminum motor housings, induction shrink fitting has proven to be a game-changer. The process begins with the induction heating of the aluminum housing. Once the housing has expanded, the motor is inserted. As the housing cools and contracts, it forms a tight seal around the motor, ensuring a secure fit.
This method not only accelerates the production process but also results in a superior product. The precision of induction shrink fitting ensures that the motor is securely housed, enhancing the overall performance and lifespan of the vehicle.
Conclusion:
The induction shrink fitting of automotive aluminum motor housings is a significant advancement in automotive manufacturing. By offering a combination of speed, precision, safety, and quality, this innovative process is set to become a standard in the industry, propelling the production of high-performance vehicles into the future. As technology continues to evolve, it’s exciting to imagine what other advancements lie ahead in the realm of automotive manufacturing.
https://dw-inductionheater.com/shrink-fitting-of-automotive-aluminum-motor-housings-with-induction-heating.html?feed_id=235122&_unique_id=65dded8f34609