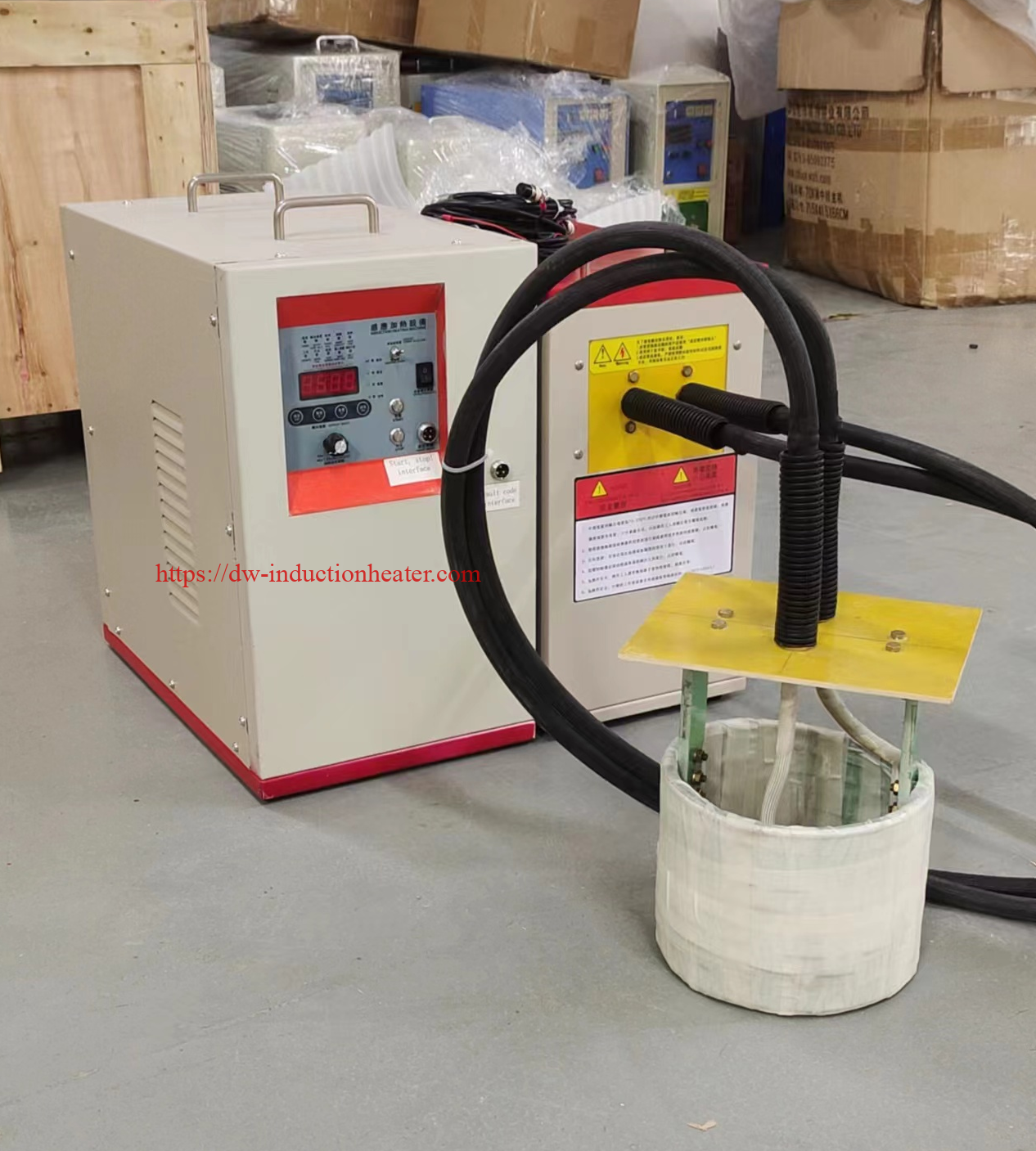
Enhancing Automotive Efficiency: The Role of Induction Heating in Shrink Fitting Aluminum Motor Housings
The automotive industry is constantly seeking methods to improve the performance, efficiency, and sustainability of its products. Shrink fitting using induction heating has emerged as a pivotal technology in the assembly of aluminum motor housings. This article delves into the principles of shrink fitting and induction heating, highlighting their significance in automotive manufacturing. It explores the benefits of using aluminum in motor housings, the process of induction heating for shrink fitting applications, the advantages over traditional methods, and the impact on the automotive industry's future.

Introduction:
In the quest for superior automotive performance and efficiency, the integration of lightweight materials such as aluminum in motor housings has become increasingly prevalent. The assembly of these components often involves the process of shrink fitting, which requires precise thermal expansion to create a tight, secure fit between parts. Induction heating has revolutionized this process, offering a fast, controllable, and energy-efficient method to achieve the desired interference fit. This article examines the application of induction heating in the shrink fitting of automotive aluminum motor housings and its implications for the industry.
The Advantages of Aluminum Motor Housings:
Aluminum, known for its lightweight, high strength-to-weight ratio, and excellent thermal conductivity, makes it an ideal choice for motor housings. These properties lead to reduced vehicle weight, improved fuel efficiency, and better heat dissipation, all critical factors in the performance and longevity of automotive engines.
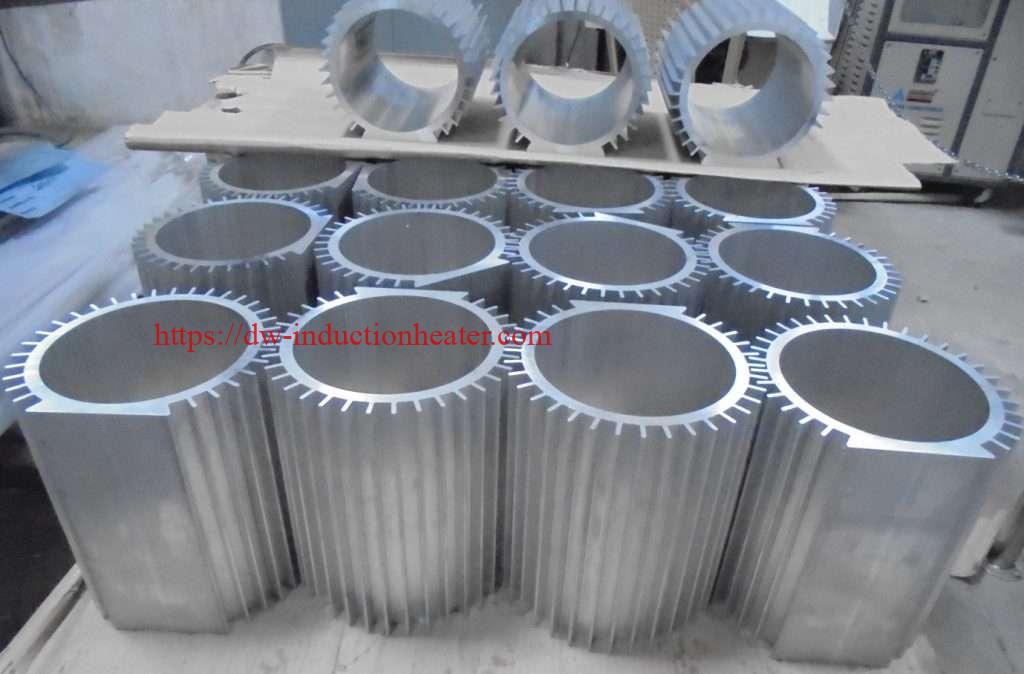
Principles of Shrink Fitting:
Shrink fitting is a mechanical method used to join two components with a high degree of precision. It involves heating the outer component (in this case, the aluminum motor housing) to expand it, allowing the insertion of the inner part (such as a steel shaft). Upon cooling, the outer component contracts to form a tight, seamless joint that can withstand significant mechanical loads without the need for adhesives or mechanical fasteners.
Induction Heating in Shrink Fitting:
Induction heating is a non-contact process that uses electromagnetic fields to heat conductive materials rapidly and selectively. In the context of shrink fitting, induction heating provides several benefits, including:
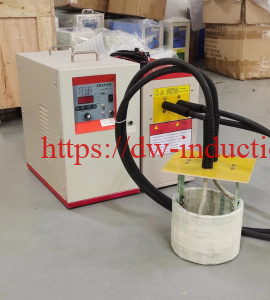
- Speed: Induction heating can rapidly bring the aluminum housing to the required temperature, reducing process times and increasing throughput.
- Control: The process offers precise temperature control, ensuring uniform expansion and preventing damage to the components.
- Energy Efficiency: Induction heating is highly energy-efficient, converting most of the energy into heat within the workpiece, minimizing waste.
- Localized Heating: The ability to localize the heat to specific areas of the housing allows for targeted expansion and protects surrounding materials and components.
- Cleanliness and Safety: Since induction heating does not rely on flame or contact heating, it is a cleaner and safer alternative that fits well within modern manufacturing environments.
The Process of Shrink Fitting with Induction Heating:
The shrink fitting process using induction heating involves several steps:
- Designing an induction coil that conforms to the geometry of the motor housing.
- Setting up the induction heating equipment with the correct power and frequency to achieve the necessary temperature.
- Heating the aluminum motor housing uniformly to the desired temperature to allow for expansion.
- Quickly inserting the inner component before the housing cools and contracts.
- Monitoring the cooling process to ensure a secure fit and prevent thermal stresses.
Advantages Over Traditional Methods:
Compared to conventional heating methods like ovens or torches, induction heating offers superior consistency, repeatability, and efficiency. It reduces the risk of component distortion and eliminates the need for long cool-down periods associated with oven heating.
Impact on the Automotive Industry:
The adoption of induction heating for shrink fitting in the automotive sector has a transformative impact. It enables manufacturers to meet the increasing demand for lightweight, high-performance vehicles while maintaining high production rates and stringent quality standards. This technology supports the industry's shift towards more sustainable manufacturing practices and contributes to the development of electric and hybrid vehicles that require lightweight, high-efficiency components.
Application in the Production of Automotive Aluminum Motor Housings
In the production of automotive aluminum motor housings, induction shrink fitting has proven to be a game-changer. The process begins with the induction heating of the aluminum housing. Once the housing has expanded, the motor is inserted. As the housing cools and contracts, it forms a tight seal around the motor, ensuring a secure fit.

This method not only accelerates the production process but also results in a superior product. The precision of induction shrink fitting ensures that the motor is securely housed, enhancing the overall performance and lifespan of the vehicle.
Conclusion:
The induction shrink fitting of automotive aluminum motor housings is a significant advancement in automotive manufacturing. By offering a combination of speed, precision, safety, and quality, this innovative process is set to become a standard in the industry, propelling the production of high-performance vehicles into the future. As technology continues to evolve, it’s exciting to imagine what other advancements lie ahead in the realm of automotive manufacturing.
https://dw-inductionheater.com/shrink-fitting-of-automotive-aluminum-motor-housings-with-induction-heating.html?feed_id=235122&_unique_id=65dded8f34609