Induction Stress relieving is applied to both ferrous and non-ferrous alloys and is intended to remove internal residual stresses generated by prior manufacturing processes such as machining, cold rolling and welding. Without it, subsequent processing may give rise to unacceptable distortion and/or the material can suffer fromservice problems such as stress corrosion cracking. The treatment is not intended to produce significant changes in material structures or mechanical properties, and is therefore normally restricted to relatively low temperatures.
Carbon steels and alloy steels can be given two forms of stress relief:
1. Treatment at typically 150-200°C relieves peak stresses after hardening without significantly reducing hardness (e.g. case-hardened components, bearings, etc.)
2. Treatment at typically 600-680°C (e.g. after welding, machining etc.) provides virtually complete stress relief.
Objective
Stress relieving flat blanks of carbon steel at a rate of 30 feet/9.1 meters per minute to reduce hardness from the outer 2”/51mm on each side to eliminate cracking issues with the end product
Material: Carbon steel flat blanks (5.7-10.2”/145-259mm wide and 0.07-0.1”/1.8-2.5mm thick)
Temperature: 1200 ºF (649 ºC)
Frequency: 30 kHz
Induction Heating Equipment: HLQ 200kW 10-30 kHz induction heating system equipped with a remote heat station containing eight 10 μF capacitors
-- A multiple turn split induction heating coil designed and developed specifically for this application
Process Carbon steel flat blanks will run through an induction coil at a rate of 30 feet/9.1 meter per minute to temper or stress relieve carbon steel. During this process, the carbon steel will heat to 1200 ºF (649 ºC). This will be sufficient to remove work hardening from 2”/51mm of each side of the width.
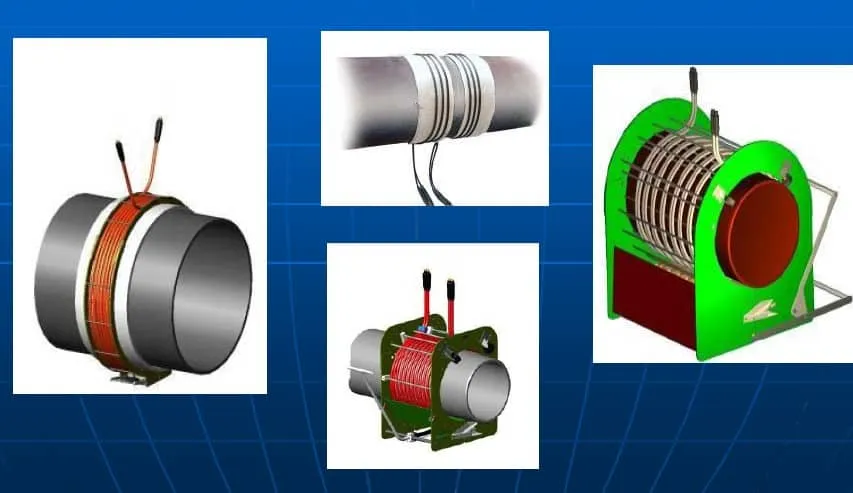
Results/Benefits
Speed: Induction rapidly heats the carbon steel to temperature, which enables a rate of 30 feet per minute
--Efficiency:
Induction heating not only saves production time, it also saves energy costs
--Footprint: Induction takes up a modest footprint, so it can easily be implemented into production processes such as
this one
Treatment at typically 150-200°C relieves peak stresses after hardening without significantly reducing hardness (e.g. case-hardened components, bearings, etc.):
--Treatment at typically 600-680°C (e.g. after welding, machining etc.) provides virtually complete stress relief.
--Non-ferrous alloys are stress relieved at a wide variety of temperatures related to alloy type and condition. Alloys that have been age-hardened are restricted to stress relieving temperatures below the ageing temperature.
Austenitic stainless steels are stress relieved below 480°C or above 900°C, temperatures in between reducing corrosion resistance in grades that are not stabilised or low-carbon. Treatments above 900°C are often full solution anneals.
Normalising Applied to some, but not all, engineering steels, normalising can soften, harden or stress relieve a material, depending on its initial state. The objective of the treatment is to counter the effects of prior processes, such as casting, forging or rolling, by refining the existing non-uniformstructure into one which enhances machinability/formability or, in certain product forms, meets final mechanical property requirements.
A primary purpose is to condition a steel so that, after subsequent shaping, a component responds satisfactorily to a hardening operation (e.g. aiding dimensional stability). Normalising consists of heating a suitable steel to a temperature typically in the range 830-950°C (at or above the hardening temperature of hardening steels, or above the carburising temperature for carburising steels) and then cooling in air. Heating is usually carried out in air, so subsequent machining or surface finishing is required to remove scale or decarburised layers.

Air-hardening steels (e.g. some automotive gear steels) are often "tempered" (subcritically annealed) after normalising to soften the structure and/or promote machinability. Many aircraft specifications also call for this combination of treatments. Steels that are not usually normalised are those which would harden significantly during air cooling (e.g. many tool steels), or those which gain no structural benefit or produce inappropriate structures or mechanical properties (e.g. the stainless steels).
https://dw-inductionheater.com/induction-stress-relieving-flat-blanks.html?feed_id=234250&_unique_id=65d0e8a64a26d