The Complete Guide to Copper Melting Furnaces: Types, Applications, and Advantages
Copper, a metal prized for its conductivity, durability, and beauty, has been a cornerstone of human civilization for millennia. From ancient tools to modern electronics, its applications are as diverse as they are vital. At the heart of copper's transformation from raw material to finished product lies the
copper melting furnace. This essential piece of equipment provides the intense heat needed to melt and refine copper, enabling its shaping and utilization in countless industries.
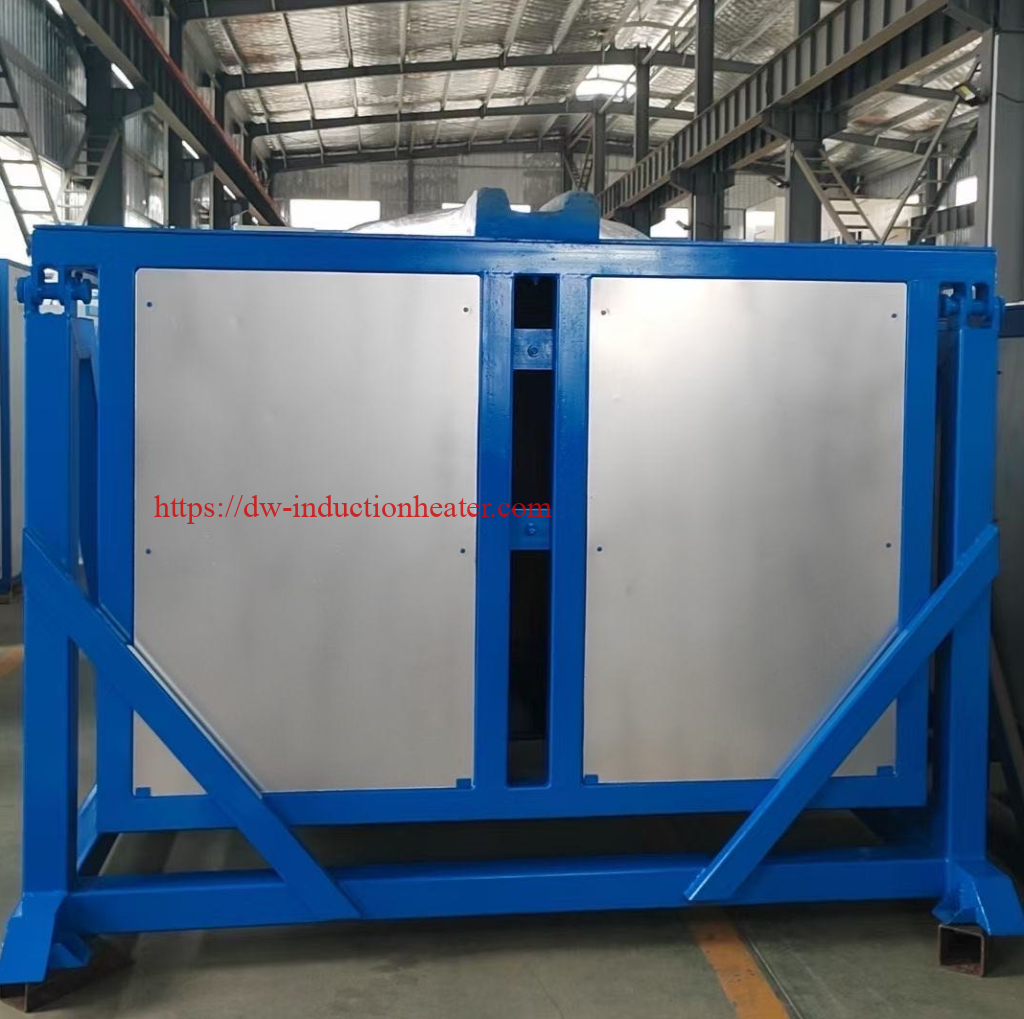
This comprehensive guide delves into the world of copper melting furnaces, exploring their various types, applications, advantages, and key factors to consider when choosing the right one for your needs.
Types of Copper Melting Furnaces
Copper melting furnaces come in a variety of designs, each with its own strengths and weaknesses. Choosing the right type depends on factors like production volume, desired purity level, energy efficiency, and budget.
Here are some of the most common types:
1. Induction Copper Melting Furnaces:
- How they work: Utilize electromagnetic induction to generate heat directly within the copper charge, resulting in rapid melting and excellent energy efficiency.
- Advantages: High melting rates, precise temperature control, minimal metal loss, reduced oxidation, environmentally friendly.
- Applications: Ideal for melting and alloying copper for high-purity applications like electrical wiring, electronics manufacturing, and coinage.
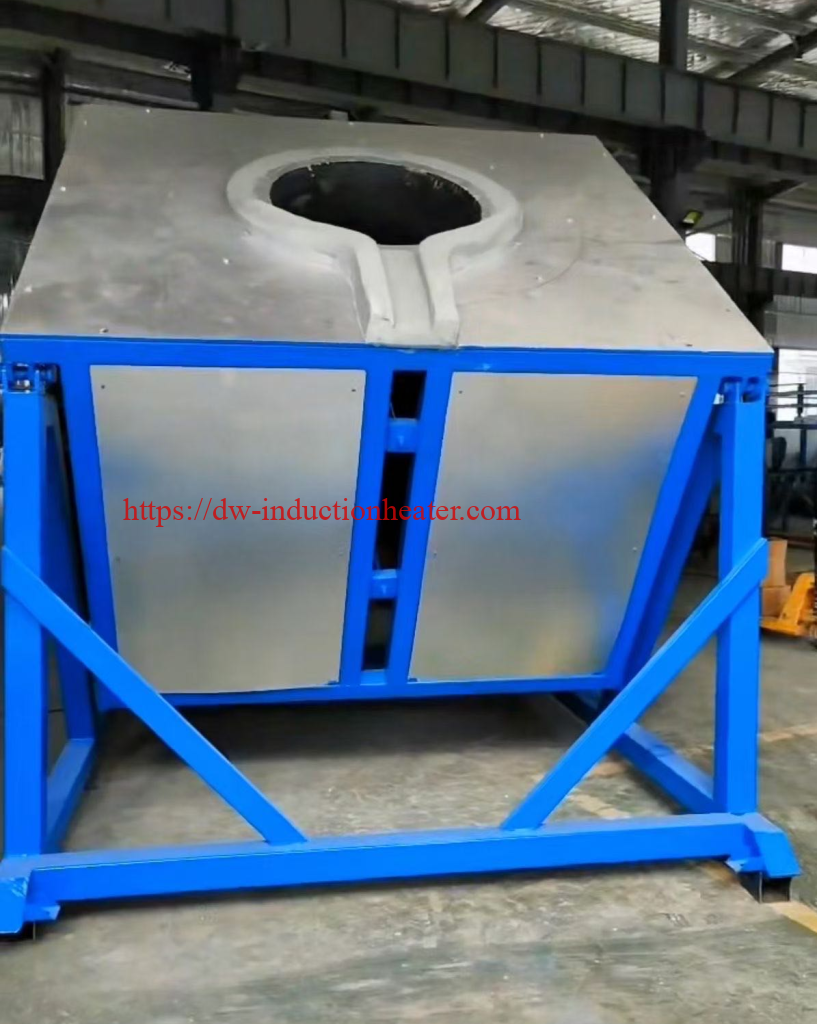
2. Crucible Furnaces:
- How they work: Employ a crucible (a heat-resistant container) made of materials like clay graphite or silicon carbide to hold the copper charge, which is heated externally by fuels like gas, oil, or electricity.
- Advantages: Relatively simple design, lower initial cost compared to induction furnaces, suitable for small to medium-scale operations.
- Applications: Commonly used for melting and casting copper alloys in foundries, art casting, and small-scale manufacturing.
3. Reverberatory Furnaces:
- How they work: Utilize a large, shallow hearth where the copper charge is melted by heat radiated from the furnace roof and walls. Fuel sources include gas, oil, or pulverized coal.
- Advantages: High melting capacity, suitable for processing large quantities of copper scrap and concentrates.
- Applications: Primarily used in large-scale copper production and refining operations.
4. Electric Arc Furnaces:
- How they work: Generate heat through an electric arc formed between electrodes and the copper charge.
- Advantages: High melting temperatures, capable of handling large volumes of scrap metal.
- Applications: Often used in secondary copper production, recycling scrap copper into usable material.
Factors to Consider When Choosing a Copper Melting Furnace
Selecting the right copper melting furnace is crucial for efficient and cost-effective operations. Here are some key factors to consider:
- Production Capacity: Determine the volume of copper you need to melt per hour or day.
- Melting Temperature: Copper has a melting point of 1085°C (1984°F). Ensure the furnace can achieve and maintain this temperature.
- Energy Efficiency: Consider the furnace's energy consumption and choose an energy-efficient option to minimize operating costs.
- Metal Purity Requirements: Different furnace types offer varying levels of control over metal purity. Choose a furnace that meets the specific purity requirements of your application.
- Environmental Impact: Assess the furnace's emissions and waste generation. Opt for environmentally friendly options with low emissions and efficient waste management systems.
- Budget: Copper melting furnaces range in price depending on their type, size, and features. Determine your budget and choose a furnace that offers the best value for your investment.
Advantages of Using Copper Melting Furnaces
Copper melting furnaces offer numerous advantages, making them indispensable in various industries:
- High-Quality Melting: Precise temperature control and efficient heating ensure high-quality molten copper with minimal impurities.
- Increased Efficiency: Modern furnaces are designed for optimal energy efficiency, reducing operating costs and environmental impact.
- Versatility: Copper melting furnaces can handle various forms of copper, including ingots, scrap, and concentrates.
- Improved Safety: Advanced safety features and automated controls enhance operator safety and minimize risks associated with high-temperature melting.
- Environmental Benefits: Modern furnaces incorporate pollution control systems to minimize emissions and promote sustainable copper production.
The Future of Copper Melting Furnaces
The copper industry is continuously evolving, driven by technological advancements and the growing demand for sustainable solutions. The future of copper melting furnaces lies in:
- Enhanced Energy Efficiency: Research and development efforts are focused on developing even more energy-efficient furnaces that minimize energy consumption and reduce the carbon footprint of copper production.
- Digitalization and Automation: Integration of digital technologies, sensors, and automation will enable real-time monitoring, process optimization, and predictive maintenance, further improving efficiency and safety.
- Sustainable Practices: The industry is increasingly adopting sustainable practices, including the use of recycled copper, renewable energy sources, and advanced emission control systems, to minimize the environmental impact of copper melting.
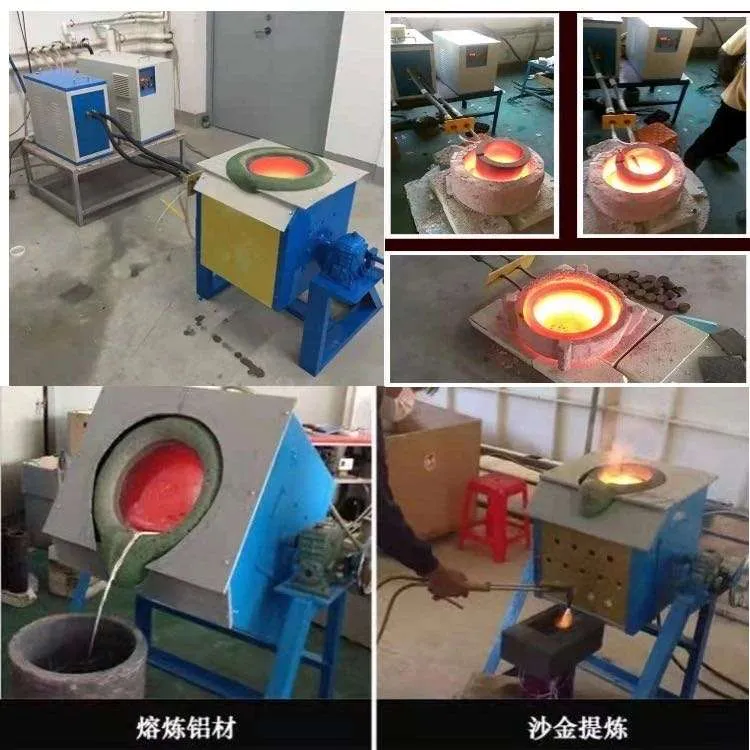
Conclusion
Copper melting furnaces are essential tools that enable the transformation of copper into countless products that shape our world. Choosing the right furnace is crucial for efficient, cost-effective, and sustainable operations. By understanding the different types of furnaces available, their advantages, and key selection factors, businesses can make informed decisions that meet their specific needs and contribute to a more sustainable future for the copper industry.
https://dw-inductionheater.com/industrial-copper-melting-furnaces-types-applications-and-advantages.html?feed_id=247041&_unique_id=6651107291155