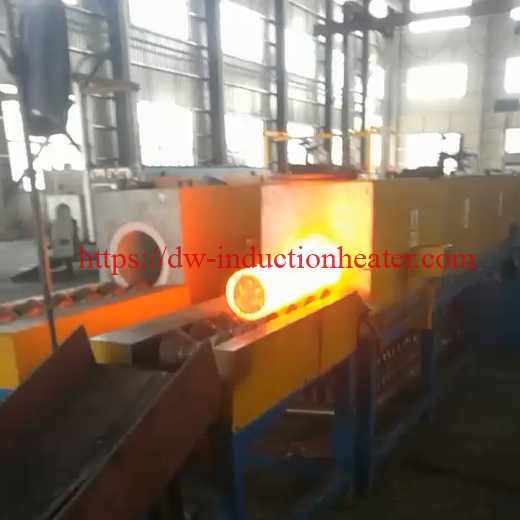
The Induction Billet Heating System: A Comprehensive Overview
In the rapidly advancing field of metal processing, the induction billet heating system stands out as a groundbreaking technology that significantly enhances efficiency, precision, and material quality. This article delves deep into the technical specifications, features, benefits, structure, applications, and advantages of induction billet heating systems, shedding light on why they are increasingly becoming the go-to solution in various industrial sectors.The principle of induction billet heating system
The principle of an induction billet heating system is deeply rooted in the phenomena of electromagnetic induction, discovered by Michael Faraday in the 1830s. This principle allows for the rapid, efficient, and controlled heating of metal billets, without direct contact or the use of combustion-based methods. The system essentially transforms electrical energy into heat energy within the metal billet through the creation of an alternating magnetic field.
Here’s how this process unfolds step by step:
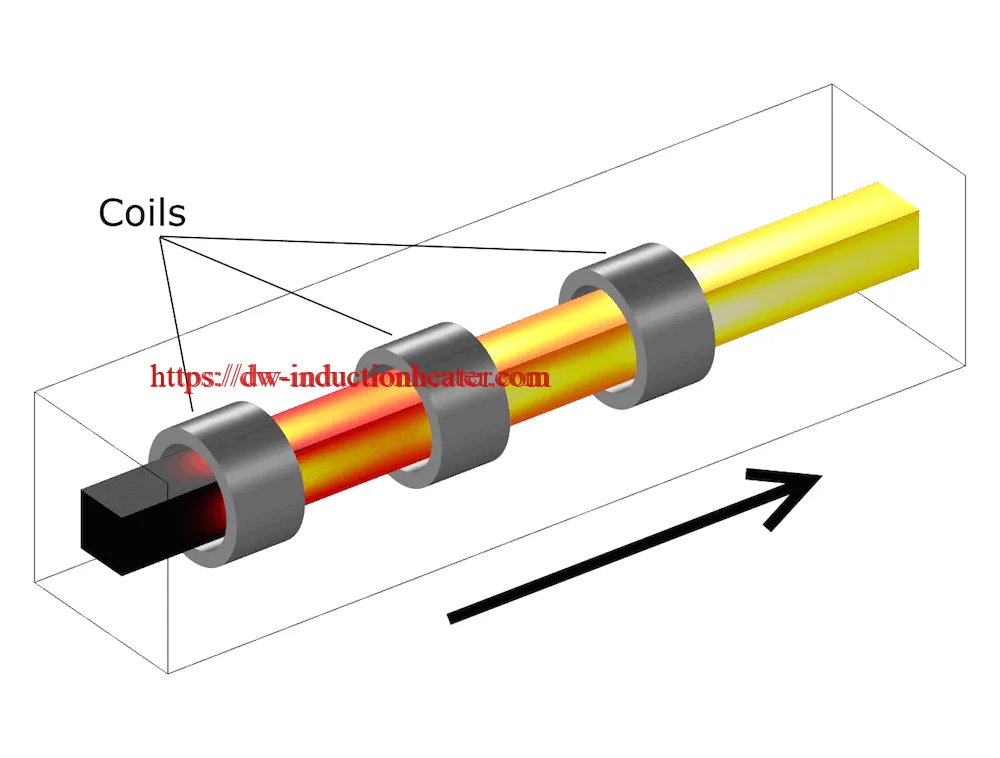
1.
Generation of Alternating Current (AC):
The system starts with an electrical source that supplies alternating current (AC) to an induction coil. This coil is essentially a copper conductor, carefully shaped and sized to suit the billet that will be heated.2.
Creation of a Magnetic Field:
As the AC flows through the induction coil, it creates a dynamic or alternating magnetic field around the coil. The strength and pattern of this magnetic field can be controlled by varying the current's frequency and amplitude, allowing for precise control over the heating process.3.
Induction of Eddy Currents:
When a metal billet is placed within this alternating magnetic field (without necessarily touching the coil), eddy currents are induced in the billet itself. These are circular electric currents that flow parallel to the billet's cross-section. The phenomenon responsible for the creation of these currents is known as electromagnetic induction.4.
Conversion of Electrical Energy to Heat:
The metal billet inherently resists the flow of the induced eddy currents, and this resistance converts the electrical energy of the eddy currents into heat. This is similar to how a wire becomes warm when it carries an electrical current, though in the case of induction heating, the effect is much more pronounced due to the higher currents involved and the properties of the metal.5.
Controlled Heating of the Billet:
The amount of heat generated depends on several factors: the intensity of the magnetic field (which is related to the current flowing through the coil), the frequency of the AC (which influences the depth of the heat penetration and distribution within the billet), and the electrical and magnetic properties of the billet material. By adjusting these factors, the system can provide precise, uniform heating, tailor-fitted to the billet’s requirements.6.
Cooling of Induction Coil:
Given the high currents and magnetic fields involved, the induction coil itself can become hot. Therefore, a cooling system, usually circulating cool water, is integrated to remove excess heat from the coil, maintaining its efficiency and longevity.Key Considerations:
- Skin Effect: At higher frequencies, the induced current tends to flow on the surface of the billet (known as the skin effect), reducing the effective heating depth. Lower frequencies are used to heat thicker billets more deeply and uniformly.
- Material Properties: The effectiveness of induction heating depends on the material’s electrical and magnetic properties. Metals like iron, which are electrically conductive and magnetically permeable, heat more effectively than non-magnetic metals like aluminum, though the latter can still be efficiently heated with adjustments to the system’s frequency and coil design.
- Efficiency: Induction heating is highly efficient and controllable, allowing for rapid heating cycles and minimal energy waste, as the heat is generated directly within the billet instead of in the surrounding environment.
Technical Specifications:
The technical specifications of an induction billet heating system can vary widely based on its intended use, the variety of materials it needs to heat, the volume of production, and the specific requirements of a manufacturing process. However, there are some key specifications that are crucial to consider when evaluating or designing an induction billet heating system for industrial applications. Here’s a breakdown of these specifications:
1. Power Rating
- Range: Typically ranges from a few kilowatts (kW) for small, specialized applications, to several megawatts (MW) for high-volume, industrial processes.
- Example: 50 kW to 2 MW is common for medium to large-scale operations.
2. Operating Frequency
- Range: Varies from low frequency (1 kHz) to high frequency (10 kHz or more), depending on the depth of heating required and the billet size.
- Example: 1 kHz for deep, uniform heating of large billets; 10 kHz or higher for shallow heating and smaller billets.
3. Temperature Capacity
- Maximum Temperature: Can exceed 1250°C (2282°F), necessary for the heating of steel and other metals to required forging or processing temperatures.
- Control Accuracy: Precise temperature control within a few degrees of the target temperature is typical.
4. Billet Size Capability
- Diameter Range: Systems are capable of handling billets from small diameters (e.g., 25 mm) to large diameters (e.g., 600 mm or more).
- Length Range: Flexible to accommodate varying lengths, with systems efficiently heating billets up to 12 meters (39 feet) or more.
5. Efficiency
- Electrical Efficiency: High, often exceeding 85%, due to the direct transfer of electrical energy into heat within the billet, minimizing losses.
- Energy Saving Features: Some systems include features like standby modes and energy recuperation systems to minimize energy consumption.
6. Heating Speed
- Ramp-up Time: Varies based on the power of the system and the material being heated but is typically much faster than traditional furnace heating. Systems can often reach target temperatures in a matter of minutes.
7. Cooling Requirements
- Type: Most systems require a cooling method, often a water cooling system, to regulate the temperature of the induction coils and other system components.
- Cooling Capacity: Should be matched to the system’s power rating to ensure efficient operation and protect components.
8. Control and Automation Features
- Temperature Monitoring and Control: High-precision sensors and controllers are used to closely monitor the billet temperature and adjust the heating process in real-time.
- Material Handling: Automated loading and unloading mechanisms, plus conveyance through the heating area, are often integrated, allowing for continuous operation.
9. Safety Features
- Emergency Stops: Quick-responsive mechanisms to immediately halt operation in case of an emergency.
- Protective Shields: Barriers or shields to protect operators from heat and any electromagnetic fields.
10. Compliance and Standards
- Industry Standards: Compliance with relevant industry standards for electrical safety, electromagnetic emissions, and operational safety is essential.
- Certifications: Systems may need certifications like CE (Conformité Européenne) for European market requirements or UL (Underwriters Laboratories) for the United States.
11. Manufacturer Support
- Warranty: Length and coverage details, which should include parts and labor.
- Technical Support: Availability of technical support services, including installation, troubleshooting, and maintenance.
Features
- Uniform Heating: Achieves uniform temperature distribution within the billet, crucial for maintaining material integrity.
- Rapid Heating Rates: Capable of heating billets to the required temperature in significantly less time than traditional methods.
- Intelligent Temperature Control: Incorporates temperature sensors and closed-loop control for real-time adjustments ensuring consistent heating.
- Automated Material Handling: Equipped with automated loading and unloading systems that minimize manual intervention and ensure continuous operation.
- Energy Saving Modes: Features like standby modes and energy recuperation systems reduce power consumption during downtimes.
Benefits
- Reduced Oxidation and Scale Formation: The absence of direct flame reduces surface oxidation, minimizing material wastage and post-processing requirements.
- Enhanced Material Properties: Uniform heating prevents thermal stresses, improving the billet's microstructure and mechanical properties.
- Lower Operating Costs: High efficiency and reduced energy consumption lead to significant savings in operational expenses.
- Environmentally Friendly: Produces no combustion gases, reducing the environmental footprint of the heating process.
Structure
The induction billet heating system is pivotal in metalworking for the uniform, efficient, and rapid heating of billets before further processing. The intricate structure of such a system integrates advanced technology and engineering principles to achieve optimum performance. Understanding its detailed structure provides insights into how it accomplishes high efficiency and quality in metal processing.
Main Components of an Induction Billet Heating System:
1.
Induction Coils:
- Function: Generate a magnetic field to heat the billets.
- Structure: Made of copper tubing, these coils are designed to match the shape and size of the billets for efficient heating. The coil geometry can vary depending on the specific application, ensuring that the magnetic field is concentrated exactly where needed.
2.
Power Supply:
- Function: Converts AC mains power to a high-frequency alternating current.
- Structure: Consists of components like rectifiers, inverters, capacitors, and inductors. Modern systems use solid-state technology to generate frequencies from a few kHz to several MHz. The power supply's capacity directly correlates to the system's ability to heat billets of various sizes and materials.
3.
Cooling System:
- Function: Dissipates heat generated in the induction coils and power supply.
- Structure: Typically employs a closed-loop water cooling system. It comprises a pump, cooling tower or chiller, and conduits connecting to induction coils and power components. The system maintains the temperature within operational limits, ensuring component longevity and system reliability.
4.
Load Matching System:
- Function: Optimizes the coupling efficiency between the power supply and the induction coils.
- Structure: Includes capacitors and sometimes inductors that adjust the system's electrical characteristics to match the load impedance. Improved matching increases the electrical efficiency and effectiveness of the heating process.
5.
Material Handling System:
- Function: Transports billets through the induction coil.
- Structure: Composed of conveyors, rollers, or pusher mechanisms. This system is often automated and synchronized with the heating cycle to ensure that billets are heated uniformly as they move through the coil at a controlled speed.
6.
Control System:
- Function: Monitors and adjusts the heating process parameters.
- Structure: Integrates sensors (for temperature, position, and velocity), PLCs (Programmable Logic Controllers), and user interfaces. It allows for precise control over the heating cycle, including ramp-up times, hold times, and cooling rates, ensuring that the billets reach the desired temperature with high uniformity.
7.
Protective Housing and Safety Features:
- Function: Ensures the safety of the operation and protects components from external conditions.
- Structure: Enclosures for electrical components, shielding for the induction coils, emergency stop mechanisms, and isolation systems. These components prevent accidental contact and contain any failures within the system to protect the operators and environment.
8.
Auxiliary Systems:
- Function: Support the main operation of the heating system.
- Structure: This may include systems for billet surface cleaning (to enhance heating efficiency), temperature measurement devices (pyrometers or thermocouples), and data acquisition systems for quality control and process optimization.
Integrated Operation:
The induction billet heating system's components work in concert to heat billets efficiently. The process begins with placing a billet within or near the induction coil. The power supply then drives a high-frequency current through the coil, generating a fluctuating magnetic field. This field induces currents within the billet (eddy currents), heating it through resistance. The control system constantly monitors the billet's temperature, adjusting the power supply accordingly to maintain the required heating profile. Meanwhile, the cooling system keeps the coil and other components at safe operating temperatures, and the material handling system ensures continuous and consistent movement of billets through the heating zone. This comprehensive structure, combining high-powered electromagnetic technology with precise control and handling mechanisms, makes the induction billet heating system a cornerstone in modern metalworking, offering unparalleled efficiency, consistency, and safety in heating processes.Applications Of Induction Billet Heater :
Induction billet heating systems have revolutionized numerous industrial processes by offering efficient, precise, and controlled heating solutions. Their applications span a wide range of sectors, from automotive manufacturing to aerospace, construction, and beyond. Here are some of the key applications of induction billet heating systems:
1.
Forging Industry
In forging processes, metal billets need to be heated to high temperatures to become malleable enough to be deformed into desired shapes. Induction billet heating systems provide uniform and rapid heating, ensuring the metal achieves the necessary ductility without compromising its integrity. This application is critical in the manufacturing of automotive components, aerospace parts, hardware tools, and various machinery elements.
2.
Extrusion Process
Extrusion involves forcing heated billets through a die to create objects with a fixed cross-sectional profile. Induction heating systems are used to bring billets to the precise temperatures required for extrusion, which is essential for producing components for the construction sector, automotive industry, and for creating intricate shapes in aluminum and copper products.3.
Rolling Mill Operations
Before billets are rolled into bars, rods, or sheets, they need to be uniformly heated. Induction systems are adept at quickly bringing billets to target temperatures, reducing surface defects and improving the quality of the rolled products. This application is particularly important in steel mills and aluminum production facilities where efficiency and product quality are paramount.4.
Seamless Pipe Manufacturing
The production of seamless pipes involves heating solid billets before piercing them to create pipes. Induction heating ensures that billets are heated in a uniform manner, reducing the likelihood of material defects and ensuring the integrity of the pipes. This application is crucial in the oil and gas industry, where high-quality seamless pipes are needed for drilling and transport.5.
Heat Treatment Processes
Induction billet heating systems are also used in various heat treatment processes, such as annealing, hardening, and tempering, to alter the physical and mechanical properties of metals. This controlled heating process is essential for enhancing the durability, strength, and performance of metal components used in high-stress applications.6.
Manufacturing of Metal Parts and Components
In the manufacturing of specific parts and components, preheated billets can be directly used in stamping, pressing, or other shaping processes. Induction heating offers the advantage of quick, localized heating, making it suitable for operations that require precise control over the heating zone and duration.7.
Powder Metallurgy
Induction heating plays a role in powder metallurgy, particularly in the sintering process where metal powders are compacted and heated to form solid parts. While not directly heating billets in this case, the principle of induction heating is applied to achieve uniform temperatures necessary for sintering.8.
Automotive Manufacturing
Beyond component forging, induction heating is crucial in the heat treatment of automotive parts like gears, shafts, and fasteners, providing them with the necessary strength and wear resistance. This application directly impacts vehicle performance and safety.9.
Renewable Energy Sector
Components for wind turbines, such as shafts and gearboxes, are often made from large metal billets that require precise and efficient heating. The renewable energy sector benefits from the efficiency and control offered by induction heating, contributing to the sustainability of manufacturing practices.10.
Aerospace and Defense
Critical components, such as landing gear and engine parts, necessitate the high-quality standards that induction billet heating can deliver. The precise control over the properties of metals makes this technology invaluable in sectors where reliability and performance are critical. Induction billet heating systems have become integral to modern industry, influencing not just the quality and efficiency of production but also opening new avenues for manufacturing innovation. By providing precise, controlled, and efficient heating, these systems enable industries to meet high standards of quality and performance in their products.Advantages
Induction billet heating systems offer a multitude of advantages over traditional heating methods such as gas or oil furnaces, particularly in terms of efficiency, control, and environmental impact. Here’s a deeper look into these benefits:
1.
High Energy Efficiency
One of the standout advantages of induction heating is its energy efficiency. Since the heat is generated directly within the billet via electromagnetic induction, rather than being transferred from an external source, there's minimal heat loss to the environment. This direct heating method can significantly reduce energy consumption compared to conventional heating techniques.2.
Rapid Heating Times
Induction billet heating systems can achieve target temperatures much faster than traditional methods. The ability to quickly heat metal billets reduces cycle times, thus enhancing productivity and throughput in manufacturing processes. This rapid heating capability is particularly beneficial in high-volume production settings.3.
Precise and Uniform Heating
The technology allows for precise control over heating parameters, including the ability to target specific areas of a billet if necessary. This precise control ensures uniform temperature distribution within the billet, which is critical for maintaining the quality of the metal and achieving consistent properties across the billet. Uniform heating helps avoid internal stresses, distortions, and weaknesses in the finished product.4.
Reduced Oxidation and Scale Loss
As induction heating occurs in a controlled environment and often under protective atmospheres, there's significantly less oxidation compared to open-flame furnaces. This reduced oxidation means minimal scale formation on the billet surface, preserving material and reducing the need for post-heating surface treatments.5.
Enhanced Worker Safety
The absence of open flames and considerably lower ambient temperatures improve safety within the workplace. Additionally, since the induction process can be automated, the need for manual handling of hot materials is greatly reduced, further enhancing safety.6.
Improved Environmental Impact
Induction heating is a cleaner process that doesn't emit combustion by-products, thereby reducing the environmental footprint of the heating process. This is increasingly important as industries seek to comply with stricter environmental regulations and aim to reduce their carbon footprint.7.
Versatility
Induction billet heating systems can be designed to accommodate a wide range of billet sizes, shapes, and materials. The system can be easily adjusted or reconfigured to meet changing production requirements, making it a flexible solution for different heating applications.8.
Low Maintenance and Operational Costs
Induction systems have fewer mechanical parts than traditional furnaces, translating to lower maintenance requirements and costs. Also, the improved energy efficiency and reduced material loss contribute to lower operational costs over time.9.
Integration with Production Lines
These systems can be fully integrated into automated production lines, improving efficiency and reducing handling times. Integration facilitates seamless processing, from heating through to subsequent manufacturing steps, without needing to move billets between separate pieces of equipment.10.
Scalability
Induction heating setups can be scaled to match production needs, from single, small-scale units to multiple, networked systems for large operations. This scalability allows businesses to expand their capacity in line with growth without significant re-investment in new heating technology.How to Choose an Induction Billet Heating System?
Choosing an induction billet heating system requires careful consideration of several factors to ensure you get a system that not only meets your immediate needs but also offers scalability for future requirements. Here’s a comprehensive guide on how to select the right induction billet heating system for your metalworking processes:
1. Assess Your Material Specifications
- Type of Material: Different metals (e.g., steel, aluminum, copper) have varying electrical and thermal properties affecting their heating requirements. Ensure the system is compatible with the types of billets you intend to heat.
- Size and Shape: Consider the range of billet sizes and shapes you'll be working with. The system's capacity to accommodate these dimensions will impact its effectiveness and efficiency.
- Temperature Requirements: Different applications require billets to be heated to specific temperatures. Assess the maximum and minimum temperature requirements for your processes.
2. Consider Production Volume and Throughput
- Volume Requirements: High-volume environments need a system with a fast heating cycle to maintain productivity. Calculate your desired throughput to match the system’s capacity.
- Batch vs. Continuous Operation: Decide whether a batch or continuous heating system suits your operation better. Continuous systems are typically preferred for higher volumes due to their efficiency.
3. Evaluate System Efficiency and Power Consumption
- Energy Efficiency: Look for systems with high electrical efficiency ratings to minimize operational costs. Modern induction heating systems are typically designed with energy-saving features.
- Power Supply: Ensure the system's power requirements are compatible with your facility's existing power supply infrastructure or assess what upgrades will be necessary.
4. Look Into Control and Flexibility
- Temperature Control: Precise temperature control is crucial for ensuring the quality of the billets. Opt for systems with advanced temperature monitoring and control features.
- Process Flexibility: Consider systems that allow easy adjustments to heating parameters to accommodate different billet types and process changes.
5. Investigate System Durability and Maintenance
- Build Quality: Choose a system known for durability to withstand the demanding conditions of industrial environments.
- Maintenance Requirements: Understand the maintenance needs of the system and the availability of maintenance services, especially if your operations run continuously.
6. Assess Installation and Operational Space
- Footprint: Evaluate the space available in your facility and compare it against the dimensions of the induction billet heating systems you're considering.
- Integration With Existing Processes: It's beneficial if the new system can be seamlessly integrated into your existing production line with minimal disruption.
7. Consider Safety Features
- Safety Mechanisms: Safety should be a priority. Look for systems that include built-in safety features such as emergency stop buttons, alarms, and protective barriers.
- Compliance: Ensure the system complies with relevant industrial safety standards pertinent to your region or sector.
8. Research the Manufacturer and Support Services
- Reputation and Experience: Choose a manufacturer with a proven track record in the industry. Experience in delivering systems for similar applications to yours can be invaluable.
- Technical Support and Warranty: Consider the level of technical support provided, including training for your staff on system operation and maintenance. Also, evaluate the warranty terms.
9. Evaluate Total Cost of Ownership
- Initial Investment vs. Operating Costs: Besides the purchase price, consider the total cost of ownership, which includes installation, operating costs, maintenance, and potential downtime.
- ROI Calculation: Estimate the return on investment (ROI) by considering productivity gains, energy savings, and potential increases in product quality.
10. Request Demonstrations and References
- Live Demonstrations: If possible, arrange for a live demonstration of the system to assess its operation firsthand.
- Customer References: Ask for and follow up on customer references to get real-world feedback on the system's performance and reliability.