What is induction shrink fitting?
Induction shrink fitting is a simple operation involving either contraction or expansion of one component on another to cause interference and the development of pressure, holding the two components together mechanically. Each method of securing parts in an assembly has unique advantages. In the case of shrink fitting, parts made from any metal can be assembled: steel to steel, steel to copper, aluminum to steel, magnesium to steel, etc. Usually, the temperatures involved in heating for expansion are significantly lower to avoid changes in metallurgical structure as in tempering or melting. Due to the possibility of stress concentrations, the influence of shrink fitting should be evaluated in critical assemblies.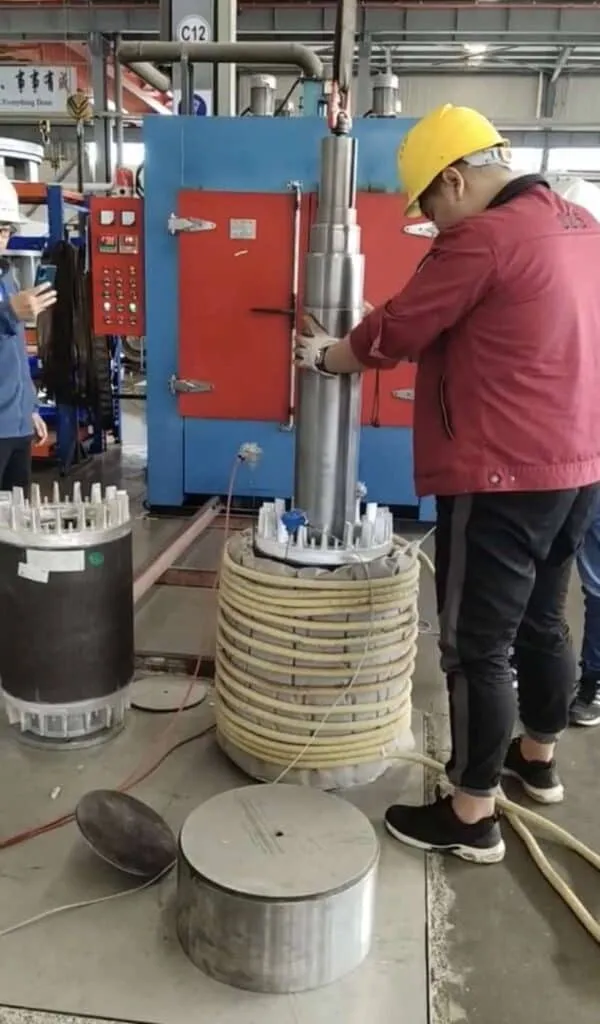

What are the benefits?
Process controllability, consistency, accuracy and speed are key benefits of induction shrink fitting. Induction heat delivery is very accurate. Due to the heat being generated within the component, you only heat the part you want to heat, not the atmosphere around it. As well as reducing the risk of ovality, this is energy efficient. Additionally, since induction produces extremely uniform consistent heat, this often allows less heat to be used. Temperature control is accurate with precise control of ramp-up times and holding temperatures. Unlike traditional heating methods, induction involves no naked flame. This allows induction shrink fitting to be used in a wide variety of applications in volatile environments, in particular in petrochemical applications.
Where is it used?
A wide variety of industries and applications can benefit from induction shrink fitting. Our induction heating systems are used in the automotive industry to shrink fit gears, bearing and rings. They are employed in the mechanical industry as well as in the maintenance of planes and trains. Our mobile systems are used for shrink fitting tasks on ships and offshore platforms and are increasingly used to fit and remove the giant nuts and bolts in the turbines of power stations as well as the bearings and shafts in wind power generators.
The induction shrink fitting technique is commonly used for the following processes:
• Fitting in gear wheels (pinions on shafts, etc.) • Covers for refrigerant compressors • Morse tapers for machine-tools • Rotating parts for turbines.Fives meets the specifications of all types of technologically advanced segments of the aerospace industry with processes that guarantee induction shrink fitting precision and do not contaminate inner surfaces, especially when assembling fragile parts.
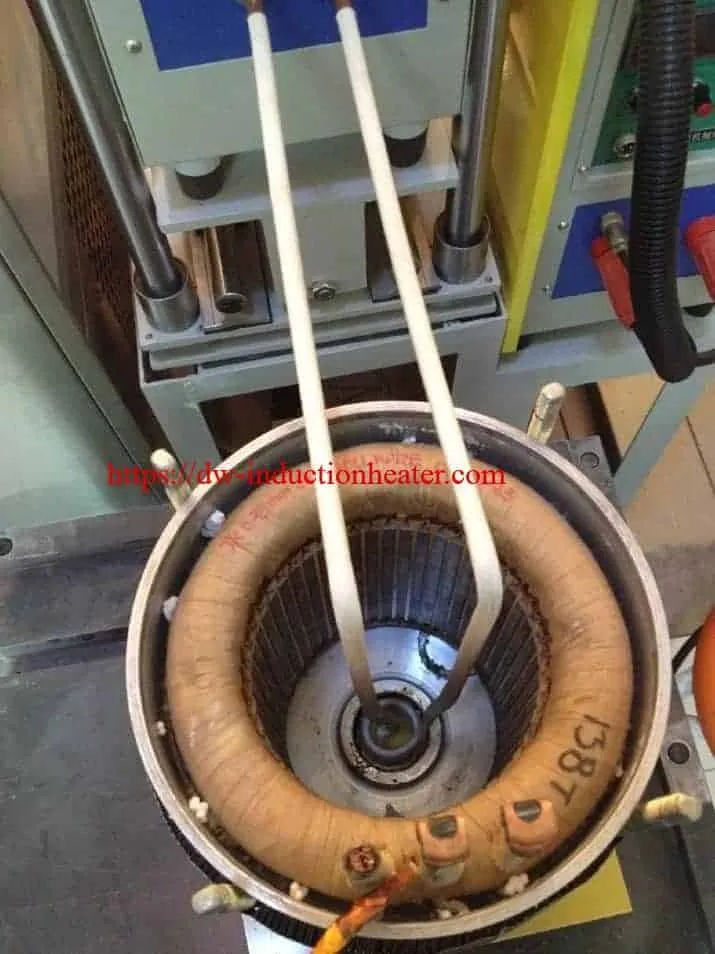