Induction Heating Stress Relieving For metal that has been cold-processed, formed, machined, welded, or cut, it may be necessary to preform a stress relieving operation to reduce stresses created during the fabrication process.
Induction Heating Stress relieving is applied to both ferrous and non-ferrous alloys and is intended to remove internal residual stresses generated by prior manufacturing processes such as machining, cold rolling and welding. Without it, subsequent processing may give rise to unacceptable distortion and/or the material can suffer fromservice problems such as stress corrosion cracking. T

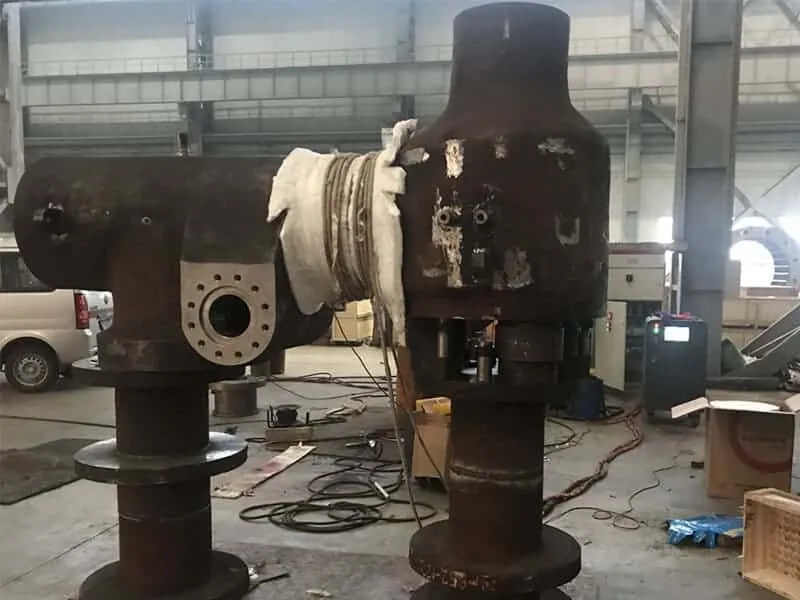
he treatment is not intended to produce significant changes in material structures or mechanical properties, and is therefore normally restricted to relatively low temperatures.
For metal that has been cold-processed, formed, machined, welded, or cut, it may be necessary to preform a stress relieving operation to reduce stresses created during the fabrication process.
Stresses in metal as a result of fabrication operations can cause unwanted dimension changes, distortion, premature failure or stress corrosion cracking of the part when these stresses are released. Parts with tight dimensional requirements may require stress relieved before other production operations can be performed. Welded sections can be made tension-free with a stress relief heating operation.
Induction Stress relieving can be performed in a controlled atmosphere chamber or vacuum to reduce oxidation.
Carbon steels and alloy steels can be given two forms of stress relief:
1. Treatment at typically 150-200°C relieves peak stresses after hardening without significantly reducing hardness (e.g. case-hardened components, bearings, etc.):
2. Treatment at typically 600-680°C (e.g. after welding, machining etc.) provides virtually complete stress relief.
Non-ferrous alloys are stress relieved at a wide variety of temperatures related to alloy type and condition. Alloys that have been age-hardened are restricted to stress relieving temperatures below the ageing temperature.
Austenitic stainless steels are stress relieved below 480°C or above 900°C, temperatures in between reducing corrosion resistance in grades that are not stabilised or low-carbon. Treatments above 900°C are often full solution anneals.
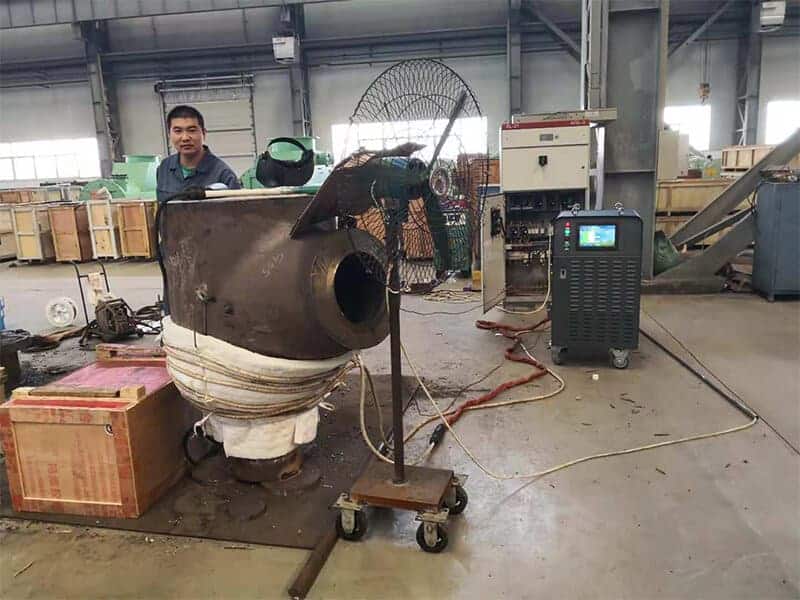
Normalising Applied to some, but not all, engineering steels, normalising can soften, harden or stress relieve a material, depending on its initial state. The objective of the treatment is to counter the effects of prior processes, such as casting, forging or rolling, by refining the existing non-uniformstructure into one which enhances machinability/formability or, in certain product forms, meets final mechanical property requirements.
A primary purpose is to condition a steel so that, after subsequent shaping, a component responds satisfactorily to a hardening operation (e.g. aiding dimensional stability). Normalising consists of heating a suitable steel to a temperature typically in the range 830-950°C (at or above the hardening temperature of hardening steels, or above the carburising temperature for carburising steels) and then cooling in air. Heating is usually carried out in air, so subsequent machining or surface finishing is required to remove scale or decarburised layers.
Air-hardening steels (e.g. some automotive gear steels) are often "tempered" (subcritically annealed) after normalising to soften the structure and/or promote machinability. Many aircraft specifications also call for this combination of treatments. Steels that are not usually normalised are those which would harden significantly during air cooling (e.g. many tool steels), or those which gain no structural benefit or produce inappropriate structures or mechanical properties (e.g. the stainless steels).
Induction preheating PWHT machine is widely used for pipe/tube weld peheat and pwht, stress reliving and so on.
Welding is one of the most critical processes in the manufacture of pressure vessels like the boiler of a thermal power plant. The temperature of the molten weld pool during the process is in the range of 2000 deg C. The heat increase is rapid and instantaneous. When this small strip of molten pool cools down the shrinkage results in thermal stresses that are locked up inside the metal. This also can change the macrostructure of the steel.
PWHT eliminates these effects by heating, soaking, and cooling the weld area in a controlled manner to temperatures below the first transformation point, giving the macro structure sufficient time to readjust to its original state and removing the residual stress.
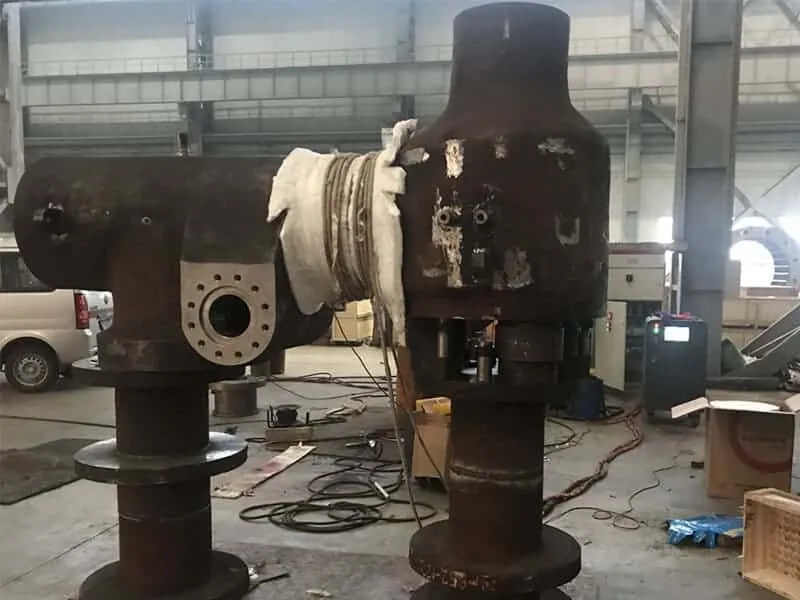
PWHT consists of heating the metal after the welding process in a controlled manner to temperature below the first transformation point, soaking at that temperature for a sufficiently long time, and cooling at controlled rates.
Induction heating is one method that is gaining popularity even though the cost is high. This is a more welder friendly process. Unlike resistance heating only the pipe becomes hot. The temperature gradients are uniform across the thickness.
The heating power is from 10KW ~ 120KW
Model: 10KW, 20KW, 40KW, 60KW, 80KW, 120KW and so on.
Heating temperature: 0 ~ 900 C
Max heating temperature: 900 C
The pipe / tube diameter: 50 ~ 2000 mm
Heating coil: Clamp coil or induction heating blanket
The induction weld preheating machine include:
1. induction heating power source.
2. SOFT Induction Heating Cable
3. Extend cable
4. K type thermocouple
5. Paper / Paperless recorder and so on.

Compare with ceramic heater and frame heater. It has more advantage.
1. Quickly heating speed and unfirom heating temperature
2. Energy saving without any pollution
3. Long working time and more stable
4. Touch screen and PLC control, Easy to operate
5. Can suitable for different welding condition