Induction Zinc Alloy Melting Furnace: The Efficient Solution for Metalworking
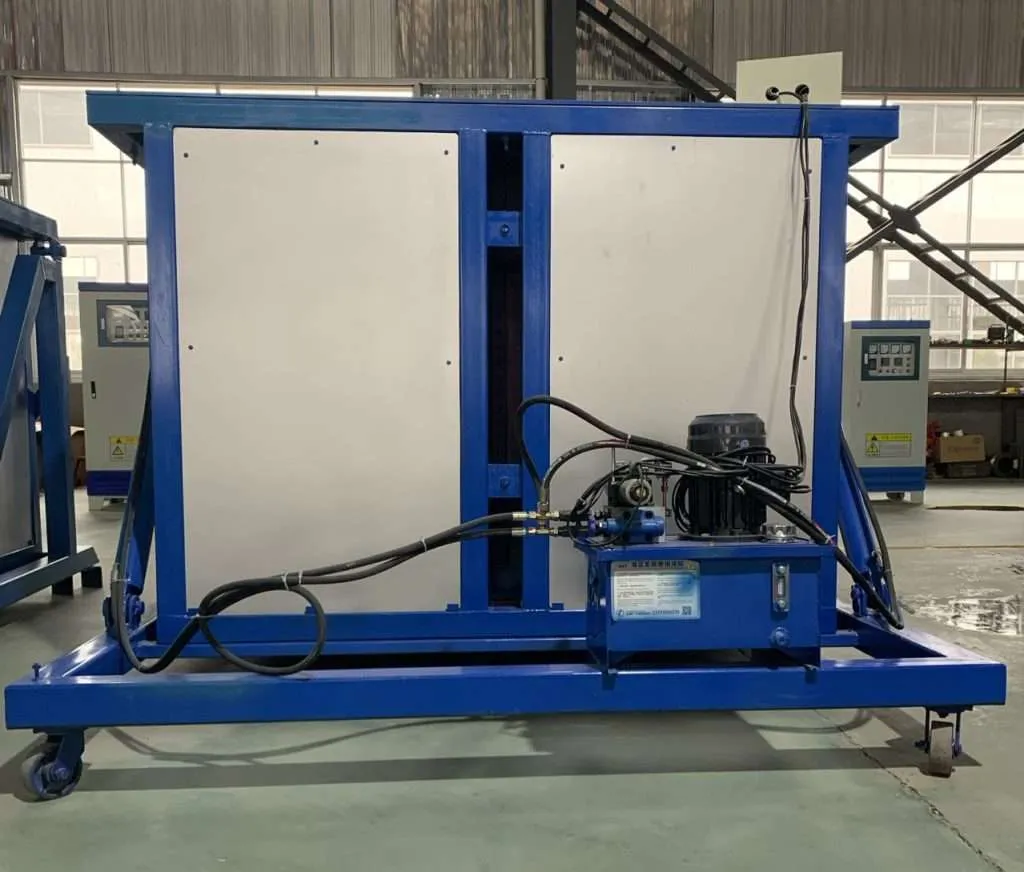
In the ever-evolving world of metalworking, efficiency and precision are paramount. Whether you're a small-scale manufacturer or a large-scale production facility, having the right equipment can make all the difference. One such crucial piece of machinery is the
induction zinc alloy melting furnace. This advanced technology has revolutionized the way zinc alloys are melted, casting, and processed, offering unparalleled benefits that set it apart from traditional melting methods.
What is an Induction Zinc Alloy Melting Furnace?
An
induction zinc alloy melting furnace is a specialized piece of equipment designed to melt and maintain the molten state of zinc alloys using the principle of
electromagnetic induction. Unlike conventional furnaces that rely on direct heat transfer through combustion or resistance heating, induction furnaces generate heat within the metal itself.
How Does an Induction Zinc Alloy Melting Furnace Work?
The process of melting zinc alloys in an induction furnace is based on the principle of
electromagnetic induction. Here's how it works:
- Induction Coil: At the heart of the furnace lies an induction coil, typically made of copper tubing. This coil is connected to a high-frequency alternating current (AC) power supply.
- Alternating Magnetic Field: When the AC current flows through the induction coil, it creates an alternating magnetic field within the furnace chamber.
- Eddy Currents: As the zinc alloy charge is placed inside the furnace chamber, the alternating magnetic field induces eddy currents within the metal itself.
- Joule Heating: These eddy currents encounter resistance as they flow through the metal, resulting in the generation of heat due to the Joule heating effect. The heat is distributed evenly throughout the metal, causing it to melt from within.
- Melting and Holding: The induction furnace can precisely control the temperature and melt rate, ensuring consistent and efficient melting of the zinc alloy. Once melted, the furnace can maintain the molten state of the metal for as long as needed.
Advantages of Induction Zinc Alloy Melting Furnaces
Energy Efficiency: Induction furnaces are highly energy-efficient compared to traditional melting methods. Since the heat is generated within the metal itself, there is minimal energy loss, resulting in significant cost savings and reduced environmental impact.
Precise Temperature Control: The temperature of the molten metal can be accurately controlled and maintained, ensuring consistent quality and minimizing the risk of overheating or underheating.
Clean Melting Process: Induction furnaces operate in a closed system, minimizing exposure to atmospheric contaminants and reducing the risk of oxidation or other chemical reactions that can affect the quality of the molten metal.
Fast Melting Rates:
Induction furnaces can melt zinc alloys at a much faster rate compared to conventional furnaces, increasing productivity and reducing overall processing times.
Versatility: Induction furnaces can handle a wide range of zinc alloy compositions, making them suitable for various applications in the metalworking industry.
Applications of Induction Zinc Alloy Melting Furnaces
Induction zinc alloy melting furnaces find applications in numerous industries, including:
- Die Casting: Zinc alloys are widely used in the die casting industry for producing intricate and high-precision components for various sectors, such as automotive, electronics, and consumer goods.
- Foundry Operations: Induction furnaces are employed in foundries for melting and casting zinc alloys into various shapes and sizes, catering to diverse industrial needs.
- Galvanizing: Zinc alloys play a crucial role in the galvanizing process, where steel or iron components are coated with a protective zinc layer to prevent corrosion. Induction furnaces ensure consistent and efficient melting of the zinc alloy for this process.
- Alloy Development: The precise temperature control and clean melting environment offered by induction furnaces make them ideal for developing and testing new zinc alloy compositions.
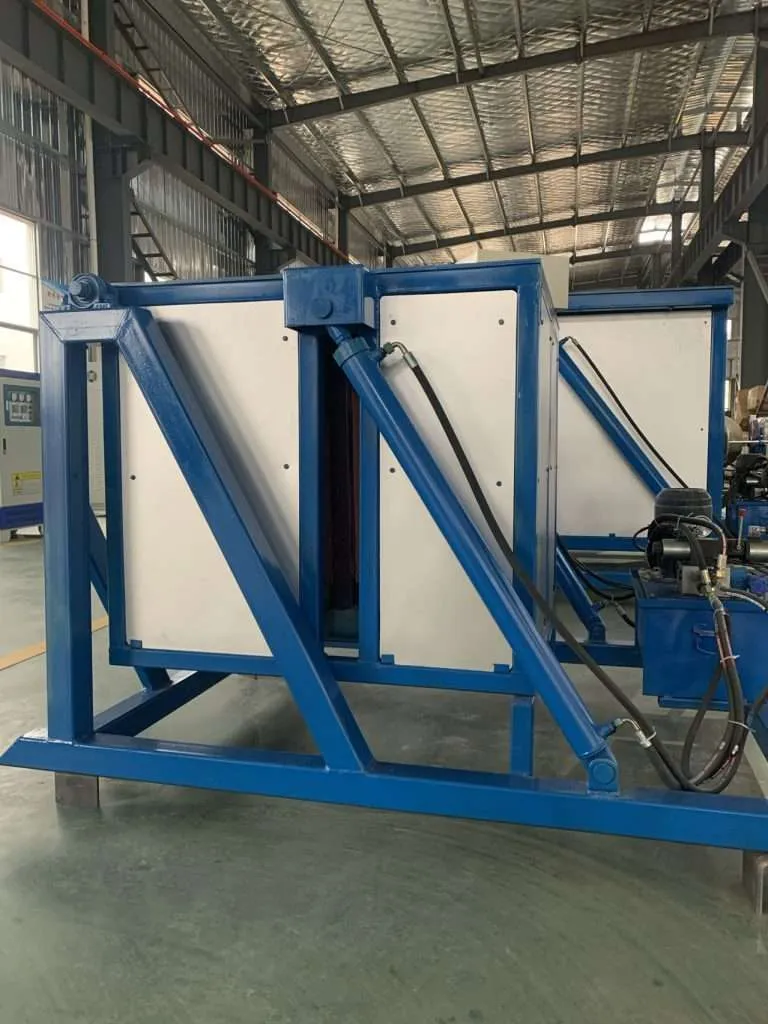
Choosing the Right Induction Zinc Alloy Melting Furnace
When selecting an induction zinc alloy melting furnace, several factors must be considered:
- Capacity: Determine the required melting capacity based on your production needs and the volume of zinc alloy to be processed.
- Power Requirements: Assess the available power supply and choose a furnace that meets your electrical requirements while ensuring efficient operation.
- Temperature Range: Ensure that the furnace can achieve and maintain the desired temperature range for melting and holding the specific zinc alloy composition.
- Automation and Control: Consider the level of automation and control features required for your production process, such as programmable temperature profiles, data logging, and remote monitoring capabilities.
- Safety Features: Prioritize furnaces with robust safety features, including emergency shutdown systems, overheating protection, and proper insulation and shielding.
- Maintenance and Support: Evaluate the manufacturer's reputation, availability of spare parts, and technical support services to ensure reliable and long-term operation.
- What types of zinc alloys can be melted in an induction furnace? Induction furnaces are versatile and can be used to melt a wide variety of zinc alloys including die-casting alloys like Zamak, as well as other specialized zinc-based alloys used in different industries. The high frequency used in induction furnaces is suitable for achieving the melting points of these various alloys without contaminating the metal, unlike some other furnaces that may use contact methods of heating.
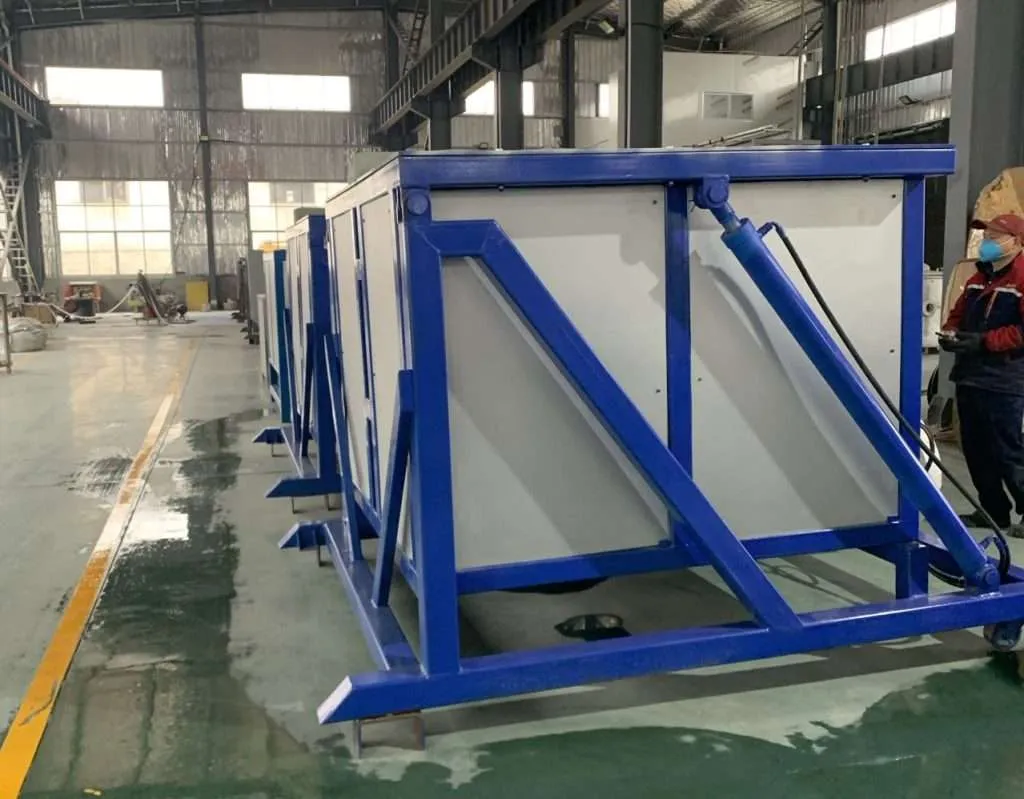
- How do you maintain an induction zinc alloy melting furnace? Regular maintenance is crucial for ensuring the furnace operates efficiently and has a long service life. Maintenance tasks may include:
- Checking and Tightening Connections: Regularly inspecting and ensuring that electrical connections are tight to avoid power losses and potential dangers.
- Cooling System Maintenance: Keeping the cooling system in good working order, which often involves checking for leaks and ensuring that the coolant is at the correct level and condition.
- Coil Inspection: The induction coil should be inspected for cracks or wear since it is a critical component of the furnace.
- Cleaning: Regularly remove any accumulated debris or metal spillage to prevent damage and inefficiency.
- Professional Inspections: Have qualified technicians perform periodic inspections and calibrations to ensure everything is working correctly and to troubleshoot any potential issues.
- What safety measures should be observed when operating an induction zinc alloy melting furnace?
- Proper Training: Only trained personnel should operate the furnace.
- Personal Protective Equipment (PPE): Operators should wear appropriate PPE, such as heat-resistant gloves, safety goggles, and protective clothing.
- Emergency Procedures: Establish and practice clear emergency procedures for dealing with incidents such as molten metal spillage or electrical faults.
- Regular Checks: Implement regular checks of the furnace's safety features, such as emergency stop buttons, safety interlocks, and temperature controls.
- Ventilation: Ensure the facility is well-ventilated to prevent the buildup of fumes that can be hazardous when metals are melted.
Conclusion
The
induction zinc alloy melting furnace has emerged as a game-changer in the metalworking industry, offering unparalleled efficiency, precision, and versatility. With its energy-saving capabilities, clean melting process, and precise temperature control, this technology has become an indispensable tool for manufacturers seeking to optimize their production processes and meet the highest quality standards. Whether you're involved in die casting, foundry operations, galvanizing, or alloy development, investing in a reliable induction zinc alloy melting furnace can provide a significant competitive edge and ensure consistent, high-quality results.
https://dw-inductionheater.com/product/induction-zinc-alloy-melting-furnace-zinc-smelting-oven-manufacturer?feed_id=239290&_unique_id=66081162e7fa7