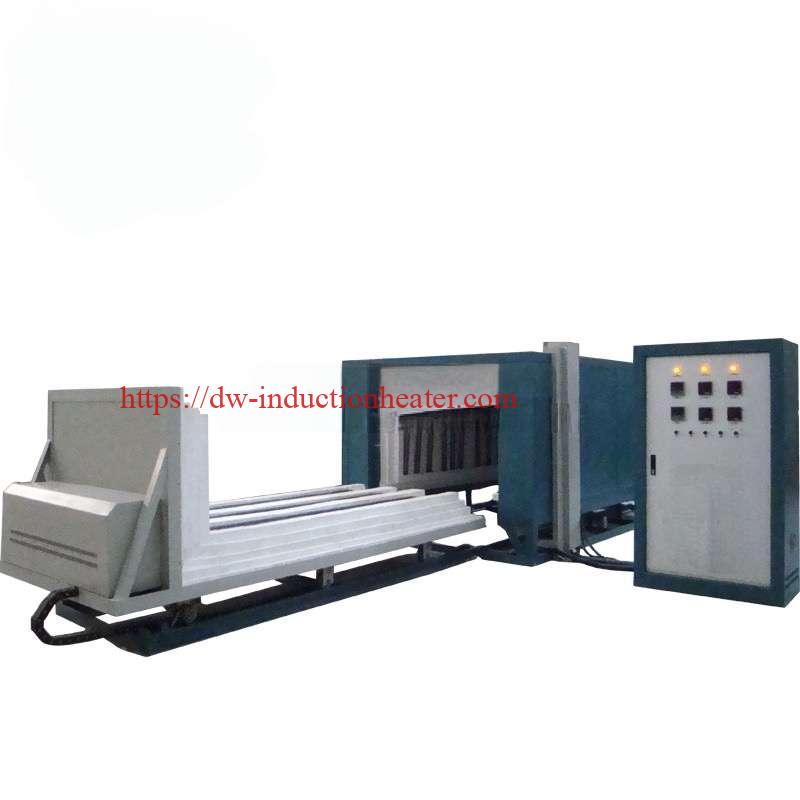
A
Copper Annealing Furnace is a specialized heating device designed for the annealing process of copper components. Annealing is a heat treatment method where a material, in this case, copper, is heated above its recrystallization temperature and then slowly cooled. This process helps relieve stresses, soften the material, and enhance its mechanical properties.
A
heat treatment furnace is an industrial device designed for the controlled application of extreme heating or cooling processes to achieve specific material properties. These furnaces play a crucial role in metallurgy and material science, facilitating various heat treatment processes such as:
- Preheating: Before forging or other manufacturing processes.
- Normalizing: To improve mechanical properties by uniformizing grain structure.
- Annealing: Softening and stress relief by controlled heating and slow cooling.
- Stress Relieving: Reducing internal stresses in materials.
- Tempering: Adjusting hardness and toughness after hardening.
- Hardening: Achieving high hardness by rapid cooling (quenching).
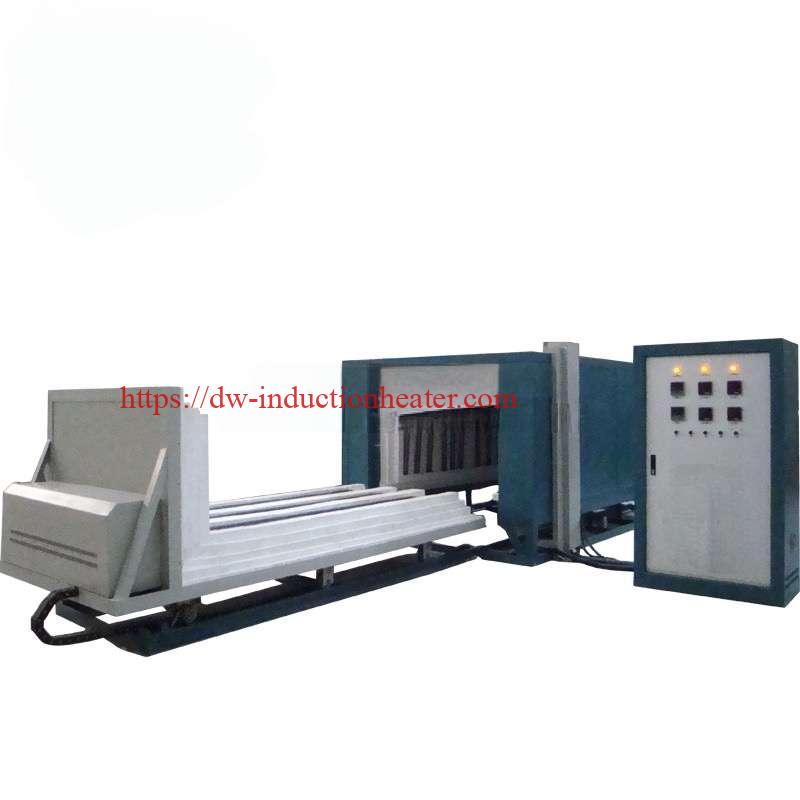
Heat treatment furnaces are vital in industries like metalworking, allowing manufacturers to tailor material characteristics to meet specific requirements. These furnaces come in various types, including those from manufacturers like Lindberg/MPH, Fives Group, and Grieve, each offering solutions for diverse applications.
Our
heat treatment furnaces designed for pyrolysis, melting, analysis and production ceramics, metallurgy, electronics, machinery,chemical, glass, refractories, for develop new material, special materials, construction materials, the equipment is suitable forinstitutions of higher learning and laboratory of scientific research institute and industrial and mining enterprises.
The control panel equipped with the intelligent adjustment device, power control switch, main working/stop button,voltmeter、 ammeter、 Computer interface、 Observe port /Air inlet port, for convenience to observe the furnace working status, the product using reliable integrated circuit, excellent working environment, anti-interference, the highest temperature of furnace shell temperature is less than 45 can greatly improve the working environment, micro computer program control,programmable setting temperature rise curve, Fully automatic temperature rise / cooling, Temperature control parameters and programs can be modified during operation, which is flexible, convenient and simple in operation.
Temperature Control Accuracy:± 1℃,Temperature Constant Accuracy: ±1℃.Fast Temperature rise rate,Maximum heating rate≤30℃/min. Furnace hearth materials made up by vacuum forming high purity alumina light materials(Will be changing due to the temperature required), High temperature for use, Less heat storage amount,Tolerance the extremely heating and cold、 no crack, No dregs, Excellent thermal insulation performance (the energy saving effect is over 60% of the traditional furnace).Reasonable structure, Double layer furnace cover, Air cooling,Greatly shortening the experimental period.
Model |
GWL-STCS |
Working Temperature |
1200℃ |
1400℃ |
1600℃ |
1700℃ |
1800℃ |
Maximum Temperature |
1250℃ |
1450℃ |
1650℃ |
1750℃ |
1820℃ |
Furnace Door Open method |
Electric control rises to open (Opening status can be modified) |
Temperature Rise Rate |
Temperature Rise Rate Can Be Modify(30℃/min | 1℃/h), Company Suggest 10-20℃/min. |
Refractories |
High purity alumina fiber polymer light material |
Loading Platform Capacity |
100Kg to 10Ton (Can be modify) |
Loading Platform Passes In And Out |
Electric machinery |
Rated Voltage |
220V/380V |
Temperature Uniformity |
±1℃ |
Temperature Control Accuracy |
±1℃ |
|
Heating Elements, Specification Certificate, Heat Insulation Brick, Crucible Pliers, High Temperature Gloves. |
Standard Accessories |
Furnace Hearth Standard Dimension |
Furnace Hearth Dimension |
Power Rating |
Weight |
Appearance Dimension |
800*400*400mm |
35KW |
Around 450Kg |
1500*1000*1400mm |
1000*500*500mm |
45KW |
Around 650Kg |
1700*1100*1500 |
1500*600*600mm |
75KW |
Around 1000Kg |
2200*1200*1600 |
2000*800*700mm |
120KW |
Around 1600Kg |
2700*1300*1700 |
2400*1400*650mm |
190KW |
Around 4200Kg |
3600*2100*1700 |
3500*1600*1200mm |
280KW |
Around 8100Kg |
4700*2300*2300 |
Characteristic: |
Open Model: Bottom Open; |
1. Temperature accuracy:±1℃ ; Constant temperature:±1℃(Base on Heating zone size ) 。 |
2. Simplicity for operation, programmable , PID automatic modify, automatic temperature rise, automatic temperature retaining , automatic cooling,unattended operation |
3. Cooling structure: Double Layer Furnace Shell, Air Cooling. |
4. Furnace surface temperature approach the indoor temperature. |
5. double layer loop protection. (over temperature protection, over pressure protection, over current protection, thermocouple protection, Power supply protection and so on) |
6. Importing refractory,excellent temperature retaining effect,high temperature resistance, Tolerance the extreme heat and cold |
7. Furnace hearth materials: 1200℃:High Purity Alumina Fiber Board; 1400℃:High purity alumina (Contain zirconium) fiberboard; 1600℃:Import High Purity Alumina Fiber Board; 1700℃-1800℃:High Purity alumina polymer fiber board. |
8. Heating Elements: 1200℃: Silicon Carbide Rod or Electric Resistance Wire; 1400℃: Silicon Carbide Rod ; 1600-1800℃: Silicon Molybdenum Rod |
Bogie Hearth Furnace Can Be Customized.More Details Please Contact Us : sales@dw-inductionheater.com |
|
|
|
|
|
|
|
|
|
The Role of Heat Treatment Furnaces in Industry:
Heat treatment furnaces are essential in various industries, including automotive, aerospace, tool making, and any sector requiring enhanced material properties. They enable manufacturers to achieve precise material characteristics, ensuring that components can withstand the stresses of their intended applications.
Advancements in Heat Treatment Technology:
The field of heat treatment is continuously evolving, with recent advancements focusing on energy efficiency, process automation, and improved control systems. Innovations such as AI and IoT are being integrated into furnace operations to achieve smarter, more predictive maintenance and process optimization.
Conclusion:
Heat treatment furnaces-Copper annealing furnaces are the unsung heroes of the material science world, enabling the precise manipulation of materials to attain desired properties and performance. As we continue to push the boundaries of engineering and manufacturing, these furnaces will evolve, incorporating cutting-edge technologies to meet the ever-increasing demands for material excellence. Understanding the intricacies of heat treatment furnaces is not only crucial for professionals in the field but also fascinating for anyone interested in the transformative power of heat on the very building blocks of our engineered world.
https://dw-inductionheater.com/product/copper-annealing-furnace-heat-treatment-furnace-annealing-oven?feed_id=235845&_unique_id=65eb15428661e