High Frequency Induction Brazing Brass Tube to Brass Disk Applications
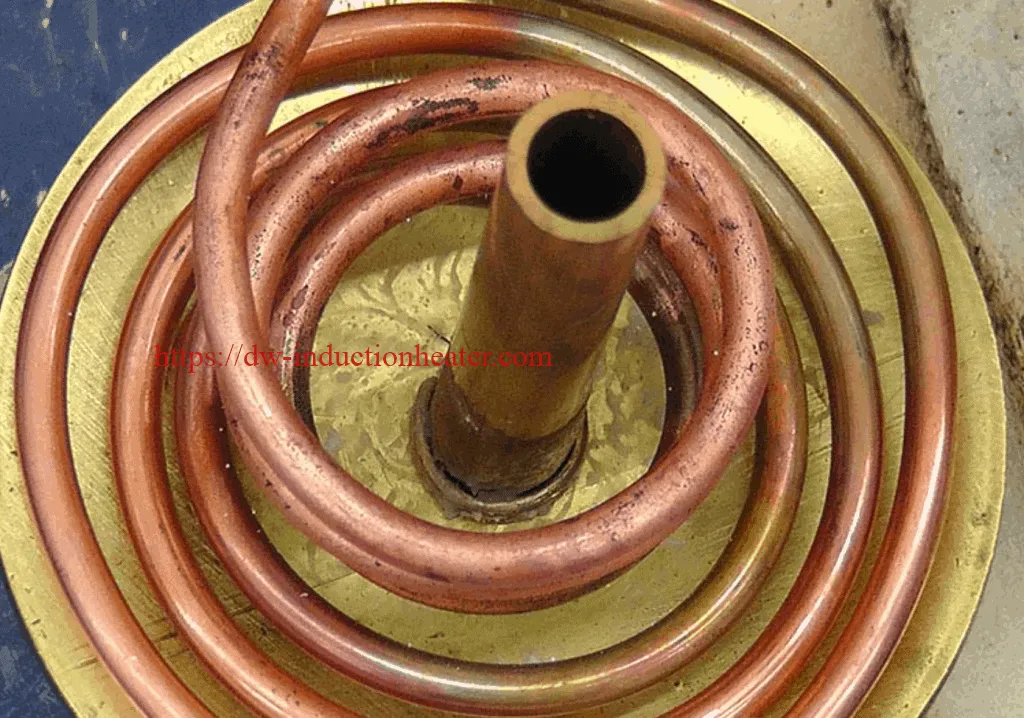
Equipment
DW-HF-15kw induction brazing heater
Materials
• Sample materials are both brass. Center tube – .500” (12.7mm) OD (0.0605” (1.537mm) wall thickness) x 2.9/3” (73.66mm) high
• Marker plate – 3.6” (91.44mm) OD x 0.125” (3.175mm) thick (nominal) slightly concave.
• Alloy – Sil Fos rod- 0.125” (3.175mm) x 0.050” (1.27mm)
• Flux
Key Parameters
Temperature: 1475-1500°F (801-815°C)
Power: 5 kW
Time: 45 seconds
Proces of induction brazing:
Benefits of induction brazing:
- To demonstrate elimination of “hand feeding” the alloy (common practice when torch brazing), we formed the customer’s alloy into a ring to tightly fit over the center post tube. This method affords several benefits in production operations: (a) Alloy in pre-formed rings provides a uniform amount for each cycle, resulting in uniform joints and wetting (b) operator control is replaces with uniform alloy rings – operators need no particular skills as with torch brazing. Pre-form alloy rings can be provided by the alloy supplier to tightly fit the tube OD.
- We fluxed the tube and mating area on the marker plate with the provided Stay Silv whit flux and moved the pre-formed alloy ring to the bottom of the tube to make contact both with the tube and the marker based at their interface position.
- A dual section/diameter coil was designed to uniformly heat the tube and plate to approximately 1500 0F at the interface of the parts – once temperature was to flow the alloy was reached, the pre-formed rings flowed around the tube and marker plated forming a complete braze filet. The apply was permitted to solidify, then the assembly was lowered out of the coil and subjected to a water bath to remove the residual flux residue.

- Precise control of the time and temperature
- Power on demand with rapid heat cycles
- Repeatable process, not operator dependent
- Safe heating with no open flames
- Energy efficient heating

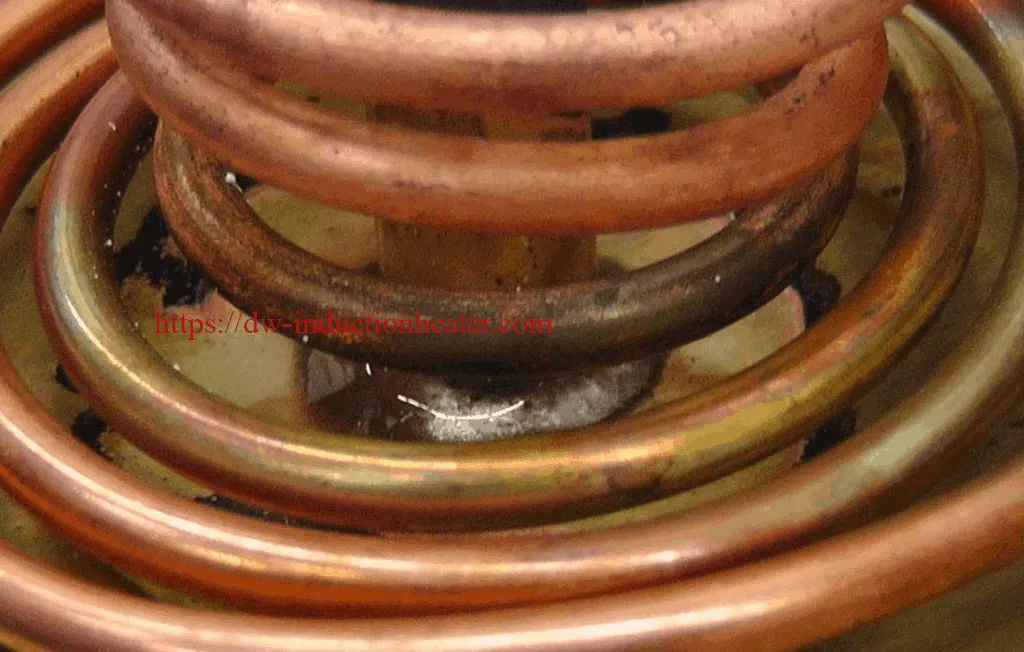
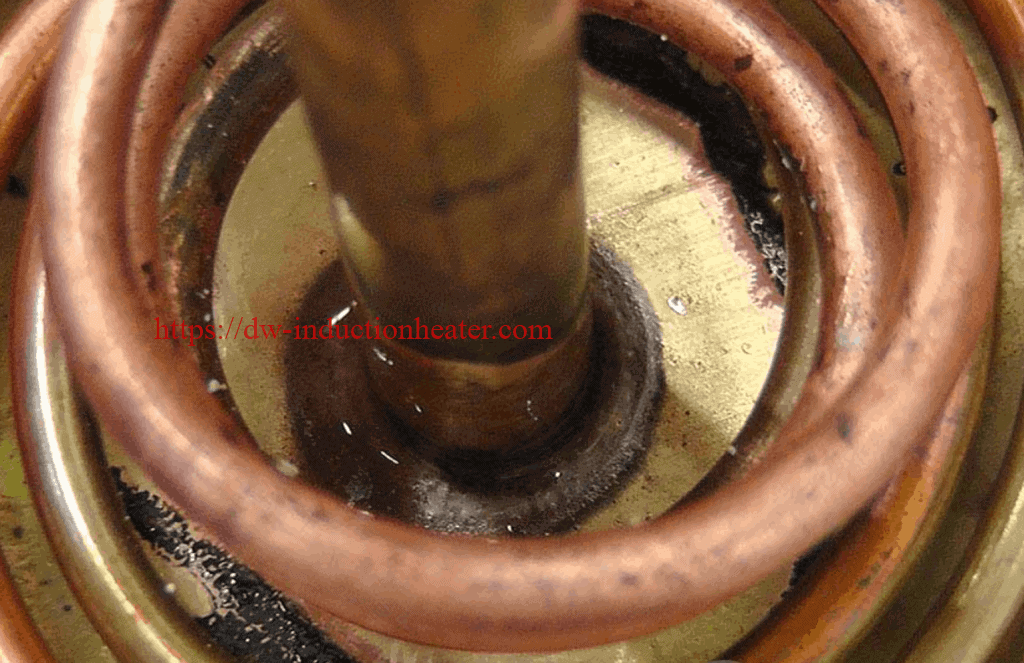

