200kg^3000kg Induction brass melting furnace is widely used for the casing and melting copper,bronze and brass block,brass chip,brass ingot,etc.
Series Connection Mid Frequency induction brass,copper melting furnace for aluminum is designed specifically for the purpose of melting lower density metal, employing exactly the right temperatures and evenly distributing the heat. This is vital in melting such metals as brass,copper,bronze if you want to preserve the expected lifetime of brass,copper and its quality. The ideal melting furnace for brass/copper will offer precise temperature controls in order to achieve this goal.
Advantages of electromagnetic Mid Frequency induction copper/brass Melting furnace:
1, save energy and reduce the environmental temperature
Original diesel furnace workshop on pollution, but also the auxiliary exhaust pipeline, inside and outside the furnace heat has a large number of distribution in the workshop, resulting in high temperature workshop. So is the original furnace condition, most escapes to the air, there is heat conduction loss, the production of large power consumption, increase the cost of production. At the same time, the ambient temperature increases. The electromagnetic induction heating process, the heating element is through magnetic field heating, in order to reduce the loss of heat conduction, fast heating, melting rapidly, thus reducing energy consumption. Reduce electricity consumption. After the comparison of the experimental test and modification, the power saving effect is 20%-40%.
2, Rapid heating, temperature control accurate real-time
Electromagnetic induction heating method is through the magnetic field lines make heating rapid heating, the rapid melting Aluminum Alloy. The temperature control is real-time and accurate, which improves the quality of the product and improves the production efficiency!
3 and long service life, simple maintenance
The traditional electric furnace heating method is to use resistance wire heating, resistance wire in the high temperature environment for a long time in the use of oxidation will result in reducing its service life, high maintenance costs. The electromagnetic heating coil is made of insulating material and high temperature wire, so the service life is long and without any maintenance.
4, power
Electromagnetic induction heating with the development and maturity of the technology, the production process and technology of components, software, such as reliable protection of the current power can be 2-200KW.
5, safe
The utility model adopts the electromagnetic induction heating, which can reduce the surface temperature of the machine, and the human body can be safely touched, so as to avoid the occurrence of burn and scald accidents caused by the traditional heating mode and protect the production safety of the employees.
Features
1 energy saving and environmental protection, Germany’s IGBT power devices, high reliability, stable operation and low maintenance costs.
2) the frequency of the digital phase locked loop tracking, automatic load impedance matching.
3 power closed-loop control, to avoid the temperature change caused by the power down.
4) over voltage, under voltage, lack of phase, over current, over heat protection, real-time display of the parameters, fault diagnosis and alarm; leakage automatic alarm, cut off the power supply and the working state of real-time display.
5) PID heating control system, uniform heating temperature, prevent molten aluminum temperature drift, burning less, homogeneous metal components to improve the product qualification rate.
6 (LED) digital temperature controller, measuring and controlling the temperature accuracy of up to 3 degrees centigrade, the quality of aluminum soup is good, the melting temperature rises quickly, the furnace temperature is easy to control, the production efficiency is high;
7) the integral structure of polycrystalline mullite fibers of furnace, small volume, good insulation property, low energy consumption, high efficiency, temperature above 1200 degrees, long service life;
8. The operation is simple and the power can be adjusted with the work;
9 (100%) load duration, maximum power, to ensure the operation of 24 hours.
Melting capacity of SMJD series Connection Mid Frequency induction brass melting furnace for copper and bronze:
Type | Input Power | Melting Capacity | Max Temperature |
steel, stainless steel | copper, gold, silver (scrap, Slag) | aluminum, aluminum alloy,
Aluminum scrap, Aluminum slag, pop can | 1800℃ |
SMJD-463 | 60 KW | 200 KG | 500 KG | 200 KG |
SMJD-480 | 60 KW | 150 KG | 500 KG | 150 KG |
SMJD-580 | 80 KW | 200 KG | 600 KG | 200 KG |
SMJD-600 | 60 KW | 230 KG | 560 KG | 230 KG |
SMJD-900 | 120 KW | 300 KG | 900 KG | 300 KG |
SMJD-905 | 80 KW | 300 KG | 900 KG | 300 KG |
SMJD-1250 | 80 KW | 400 KG | 1200 KG | 400 KG |
SMJD-1250 | 120 KW | 450 KG | 1350 KG | 450 KG |
SMJD-1500 | 120 KW | 500 KG | 1500 KG | 500 KG |
SMJD-1550 | 120 KW | 520 KG | 1560 KG | 520 KG |
SMJD-1700 | 160KW | 600 KG | 1700 KG | 600 KG |
SMJD-2300 | 160KW | 800 KG | 2000 KG | 800 KG |
SMJD-3100 | 200KW | 1200 KG | 3000 KG | 1200 KG |
Aluminium Scraps Recycling Melting Process
SMJD induction melting furnace parameter
Aluminum,Copper,Iron Induction Melting Furnace manual
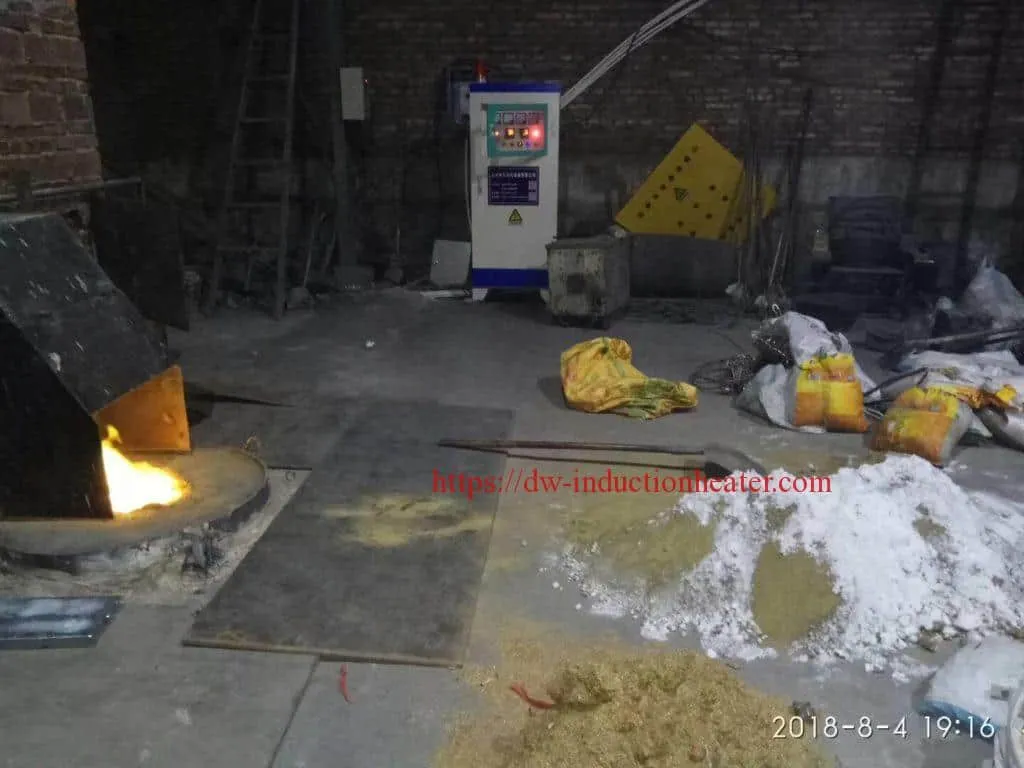
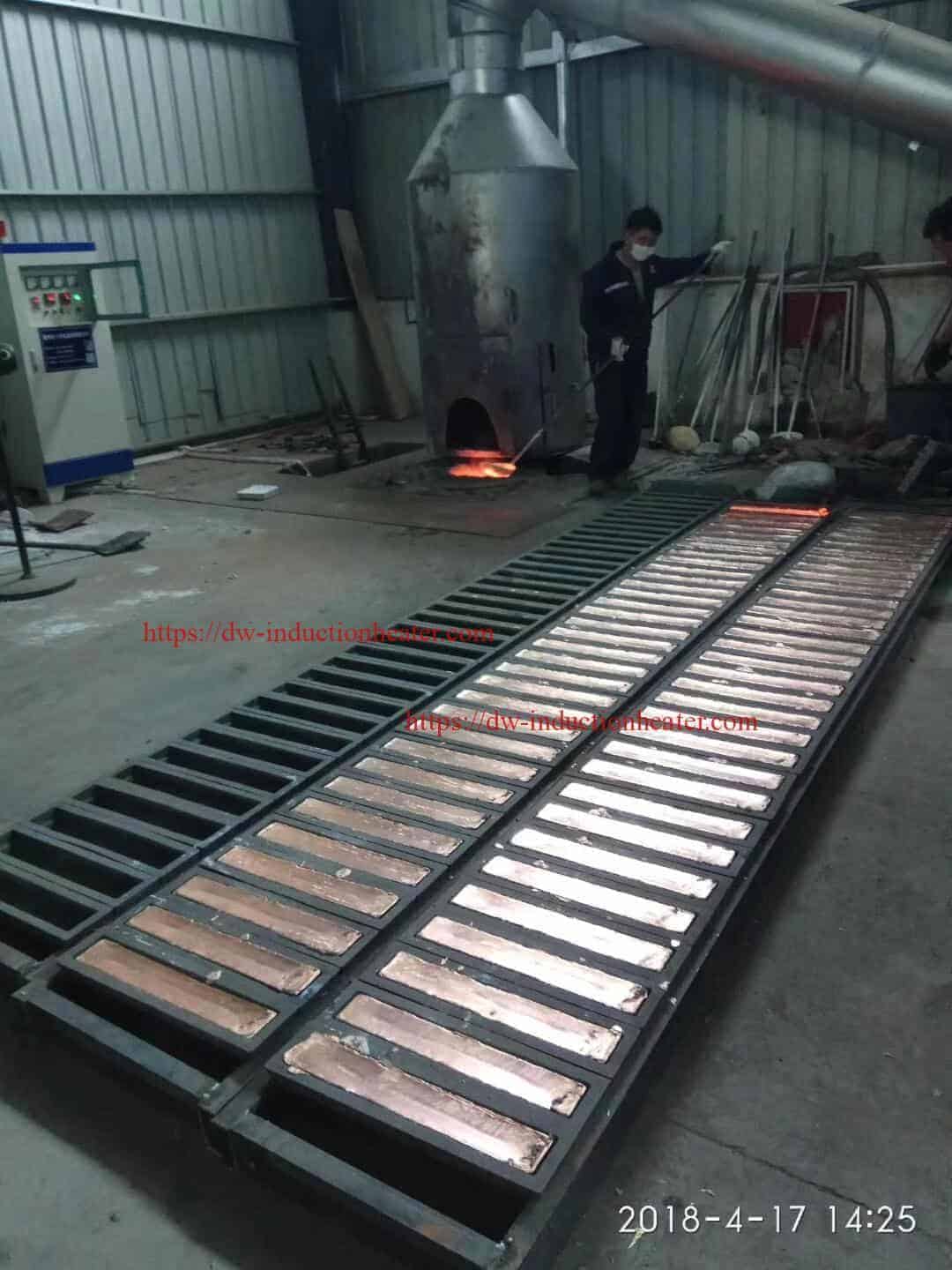
[pdf-embedder url=”https://dw-inductionheater.com/wp-content/uploads/2018/12/AluminumCopperIron-Induction-Melting-Furnace-manual.pdf” title=”Aluminum,Copper,Iron Induction Melting Furnace manual”]

https://dw-inductionheater.com/wp-content/uploads/2018/12/MF-brass-melting-furnace.jpg
https://dw-inductionheater.com/induction-brass-melting-furnace.html
brass melting, brass melting furnace, brass melting furnace manufacturer, induction brass melting, induction brass melting furnace, induction melting brass, melting brass furnace, melting brass induction furnace, MF brass melting furnace